Search results for: work
Category
Announcements
CMMS
Compliance & Control
Enterprise Asset Management
Facility Management
Fleet
Operations & Maintenance
Product Updates
Uncategorized
Operations & Maintenance
How to Optimize Maintenance Workflow Using CMMS
Are you looking to enhance your maintenance workflow by using a CMMS? This piece explores how employing a CMMS can streamline and reduce mistakes in your maintenance operations. It offers methods for a CMMS to systematize tasks, automate processes, judiciously distribute resources, and underpin decisions with solid data—revolutionizing your entire suite of maintenance processes. Source: […]
Make your work easier.
Try for free.
Book a demo
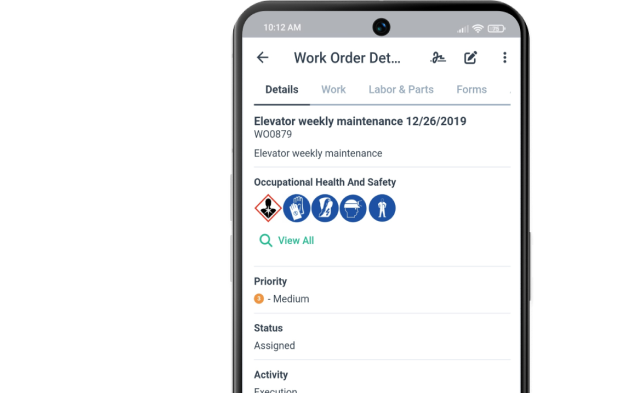