Get a Free WorkTrek Demo
Let's show you how WorkTrek can help you optimize your maintenance operation.
Try for freeKey Takeaways:
- CMMS can minimize unplanned failures, which cost companies about $125,000 per hour.
- Over 44% of facility managers say tracking work orders is time-consuming.
- Research found that companies using a CMMS can lower costs and downtime by 20%.
As a maintenance manager in manufacturing, you understand that minimizing downtime and maximizing efficiency are both essential and challenging.
Likewise, if your organization fails to appreciate the power of good maintenance fully, you’re not alone.
The good news?
A proactive approach with a Computerized Maintenance Management System (CMMS) can change that.
This powerful tool brings a range of benefits to your operations.
Are you curious about these benefits and how CMMS helps achieve them?
Read on to find out.
Reduces Equipment Downtime
It’s no secret that preventing unexpected equipment failures and minimizing downtime is the ultimate goal of effective maintenance in any manufacturing facility.
These priorities stem from the need for operational efficiency and safety and compliance requirements.
To tackle this challenge, many companies are adopting predictive maintenance (PdM) as an extension of their preventive maintenance (PM) strategies.
The goal behind this shift—and the technologies enabling it—is to avoid the extremely high costs of unplanned failures.
A 2023 survey by ABB Motion Services, a global leader in motors and drives, examined the impact of equipment outages on 3,215 maintenance leaders worldwide.
As Virve Viitanen, Head of Global Customer Care and Support at ABB, explains:
Moreover, the survey found that 69% of facilities experience unplanned outages of critical equipment at least once a month, with 8% facing them daily.
These alarming statistics underscore the urgent need for predictive maintenance solutions.
However, implementing fully integrated AI-powered PdM systems with real-time sensor monitoring can be costly and complex.
A CMMS provides a cost-effective alternative using historical data and automated alerts to predict and prevent unexpected failures.
Since all maintenance activities are recorded in the CMMS, you can track equipment performance over time.
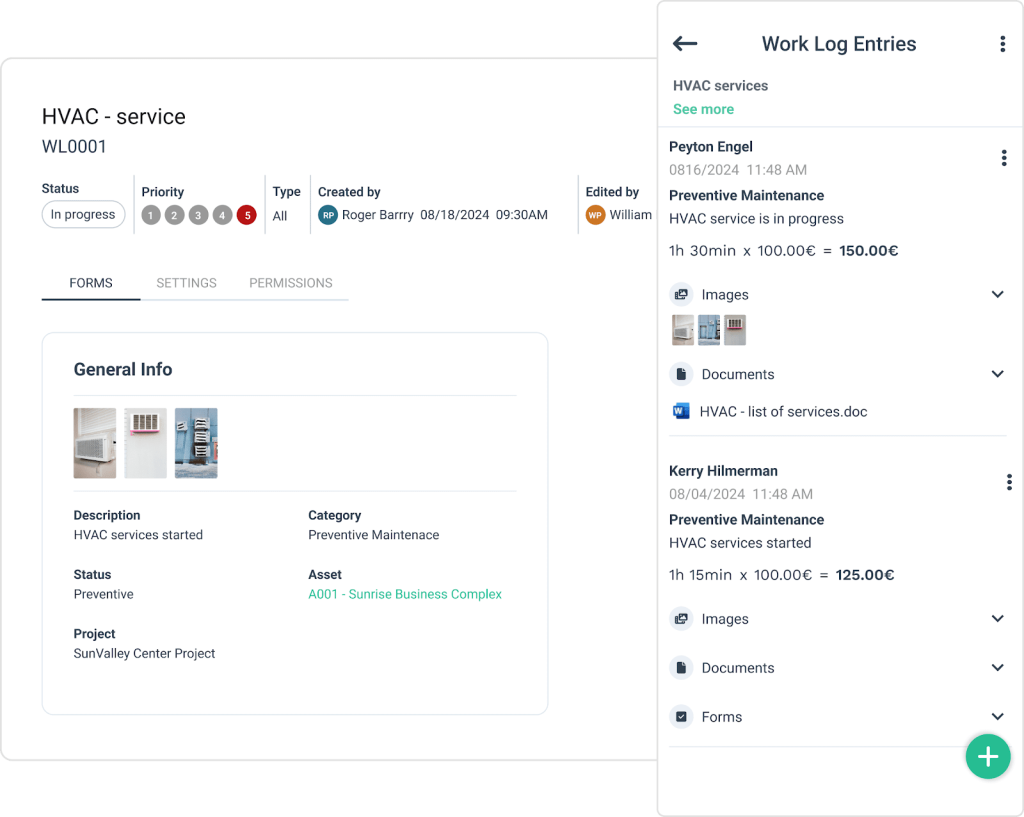
By analyzing maintenance logs and past failure patterns, your team can identify when certain components are likely to fail, allowing for timely interventions and reducing downtime as a result.
Automated alerts further support this by notifying managers when specific machinery needs maintenance.
How?
Monitoring meter readings—such as mileage, operating hours, or oil levels—regularly entered into the CMMS.
Once a predefined threshold is reached, the system can automatically generate a preventive maintenance work order, ensuring issues are addressed before they lead to costly breakdowns.
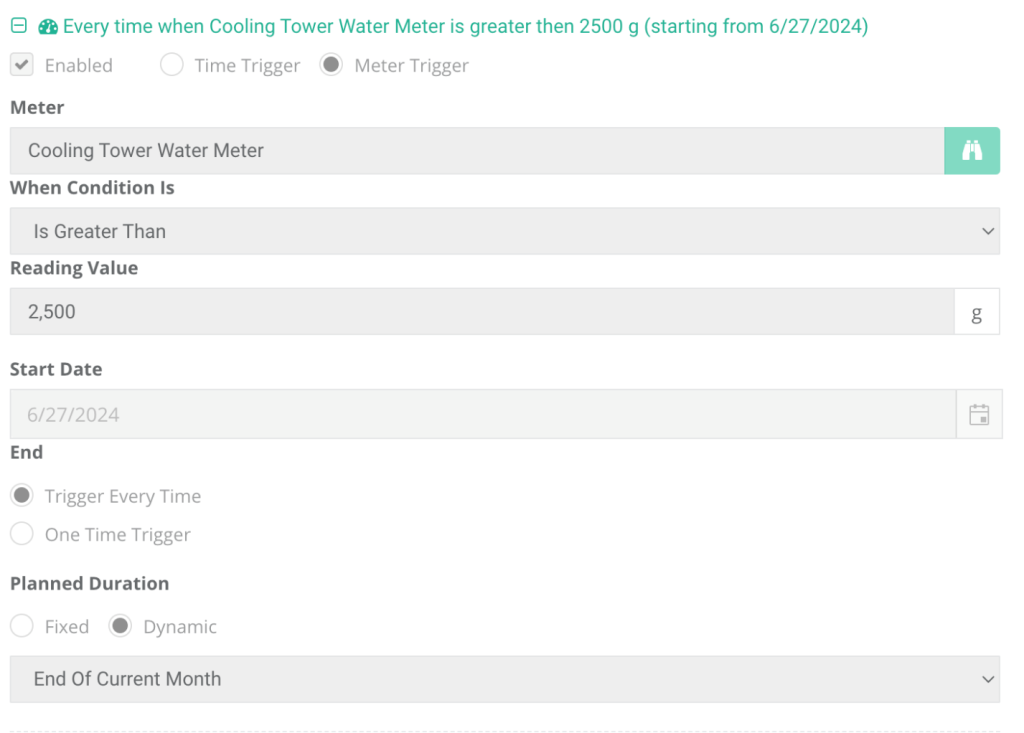
These capabilities also make CMMS solutions a solid foundation for gradually building a more advanced, sensor-based system.
In real-time, various sensors—built-in or external—can continuously monitor equipment conditions such as temperature, vibration, and operational loads.
When integrated with a CMMS, they provide real-time condition data, enabling even more accurate failure predictions and proactive maintenance scheduling.
To recap, CMMS software reduces equipment downtime by leveraging historical maintenance data, automated alerts, and real-time monitoring that can be enhanced with sensors.
Streamlines Work Order Management
Simplified work order management is another way CMMS benefits your manufacturing operations.
It automates task scheduling, tracks maintenance requests, and ensures work is completed on time.
Since everything is digitized and accessible from any device, paperwork is minimized, and maintenance operations run more efficiently.
This efficiency is especially crucial as the demand for maintenance continues to rise.
In 2024, over 55% of facility managers surveyed by JLL Technologies reported an increase in work orders compared to the previous year.
More than 44% cited work order progress tracking as their most time-consuming task.
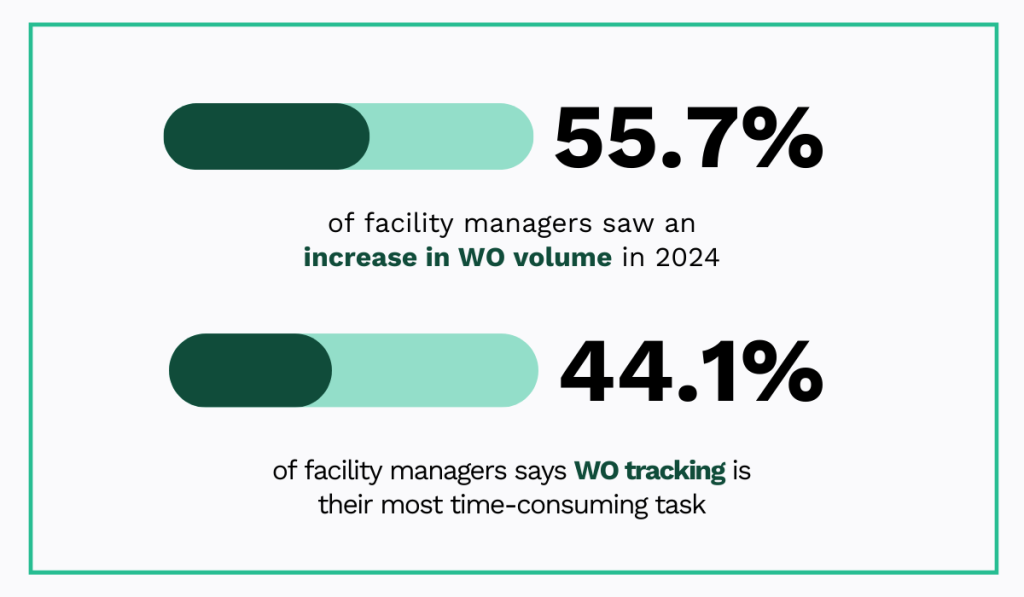
Let’s explore how CMMS streamlines work order management in light of this.
Simply put, it automates and simplifies the entire work order process—from submitting maintenance requests to ensuring timely completion.
For example, when facility workers notice an issue, they no longer need to rely on paper forms or back-and-forth emails.
Instead, they can report it instantly through a CMMS app.
The manager is immediately notified and can use the app to check technicians’ schedules, assess workload, and assign work orders to the right team members.
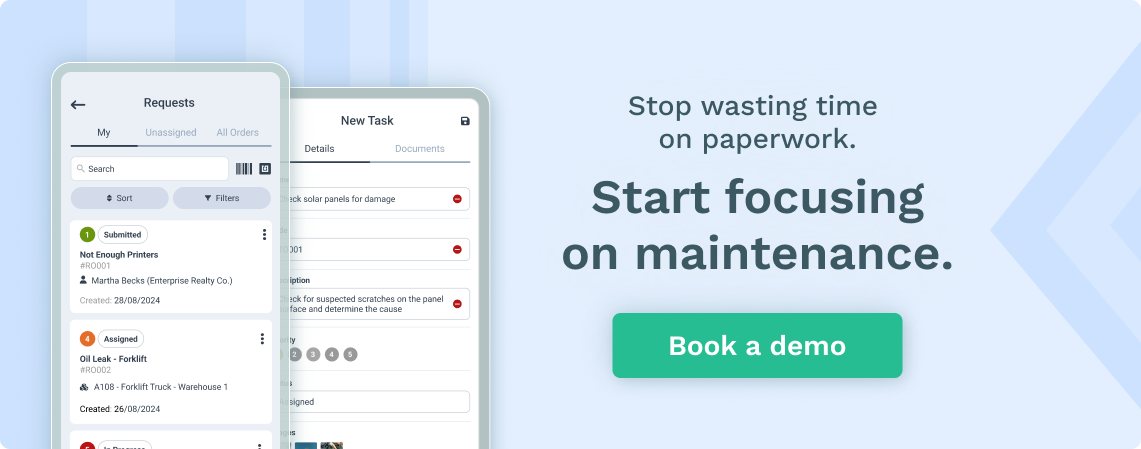
From there, managers can track the status of all work orders in one place, gaining real-time visibility into their progress.
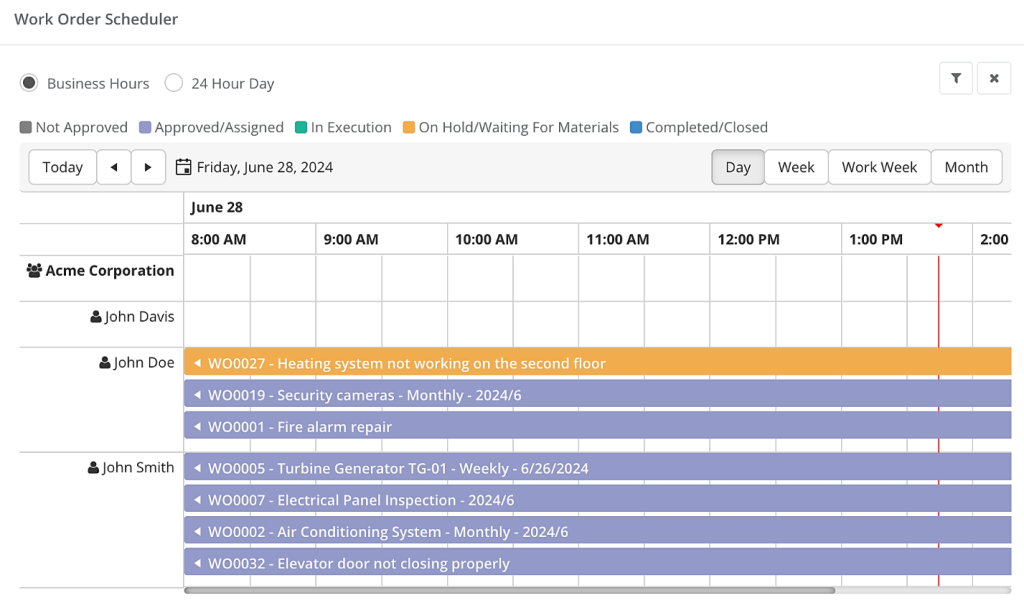
On the technicians’ side, the CMMS app instantly notifies them of new work orders assigned to them and automatically adds the tasks to their dashboard.
Additionally, work orders are prioritized based on urgency—either by the manager or a dedicated prioritization team—ensuring technicians always know which tasks to tackle first.
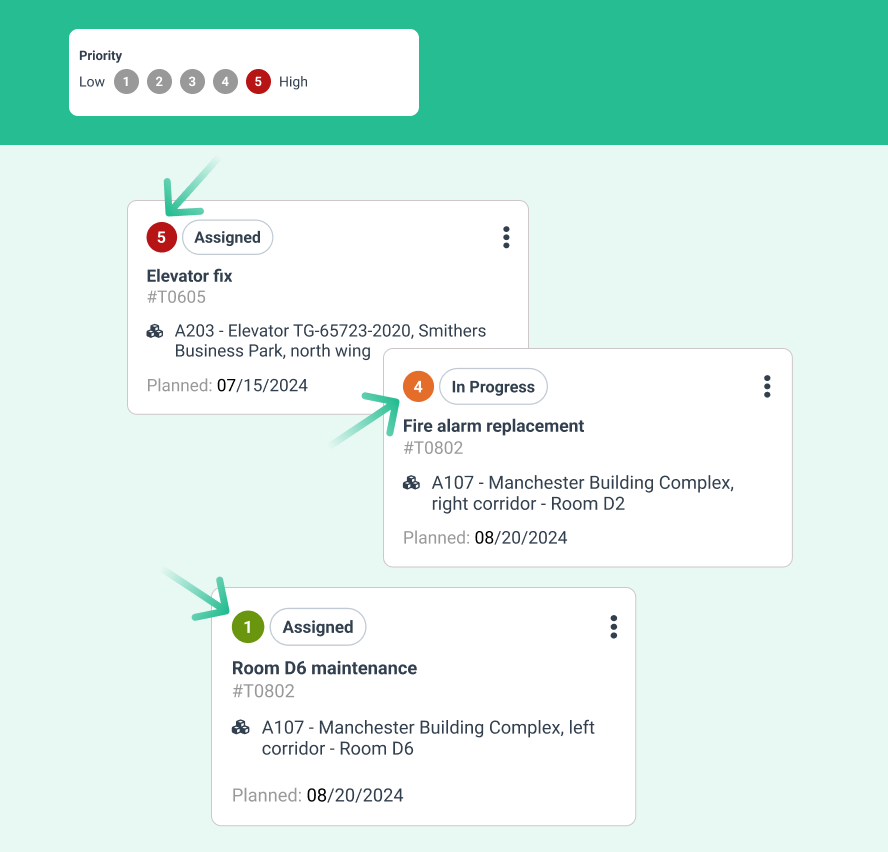
Meanwhile, managers can monitor the status and progress of all work orders on a single screen, eliminating the need for multiple spreadsheets or paper forms.
This digital tracking doesn’t just streamline work order management, though.
It also enhances accountability and ensures critical maintenance tasks are completed without delay.
Overall, a cloud-based CMMS eliminates error-prone, time-consuming paperwork and spreadsheets, fully digitizing and optimizing the entire work order management process.
Extends Asset Lifespan
Guided by a CMMS like WorkTrek, regular maintenance extends the life of machines by enabling proactive maintenance and reducing unexpected breakdowns.
More precisely, the system tracks asset usage and maintenance history, helping maintenance teams identify wear patterns and schedule interventions before failures occur.
By automating maintenance reminders and optimizing service schedules, CMMS enables your team to:
- Minimize excessive wear and tear
- Prevent premature replacements
- Maximize equipment performance
According to OxMaint, continuous asset health monitoring and targeted interventions can extend their useful life by 20-40%.
How is this significant extension of an asset’s useful life achieved?
One key factor is leveraging real-time data and historical maintenance records stored in the CMMS.
These data points help your team track asset performance and detect signs of wear or inefficiencies.
This allows them to make informed, data-driven decisions on when to service equipment, thus preventing minor issues from escalating into costly failures.
Centralizing all this information in your CMMS dashboard further streamlines maintenance planning and enhances asset longevity.
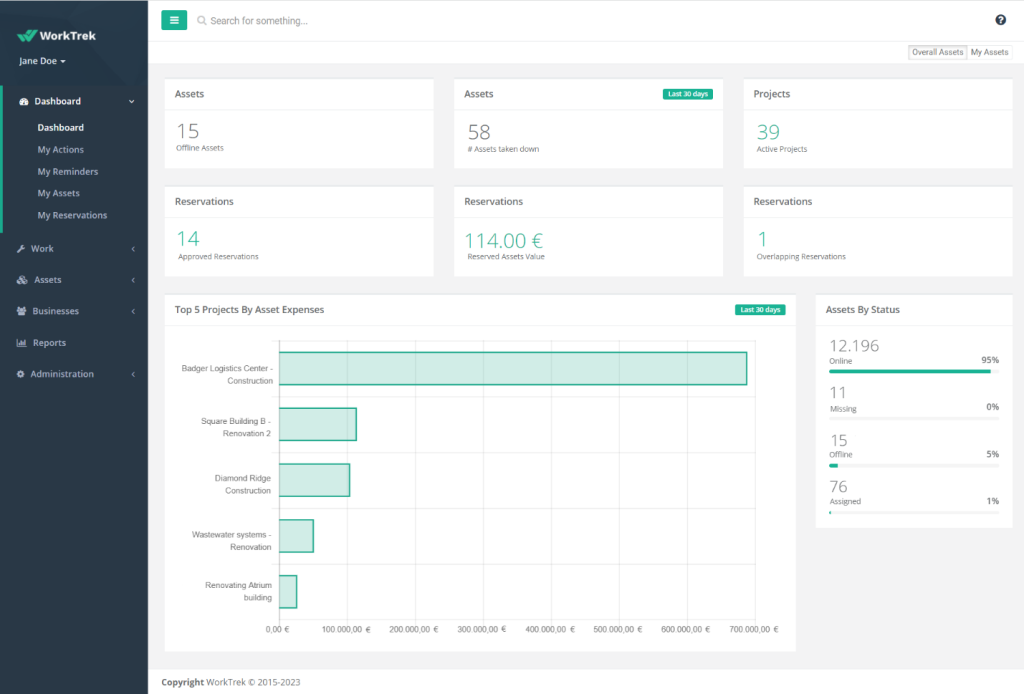
As mentioned, CMMS also offers predictive analytics capabilities even without real-time monitoring sensors.
For example, meter readings entered into the system allow maintenance schedules to be optimized and triggered alerts to be set based on actual usage patterns rather than fixed intervals.
This ensures servicing is done precisely when needed—neither too soon nor too late—helping to extend asset lifespan while optimizing maintenance costs.
Next, CMMS also helps standardize maintenance procedures, ensuring servicing aligns with manufacturer recommendations and industry best practices.
Additionally, automated reminders keep service teams on top of critical tasks, reducing the risk of overlooked maintenance.
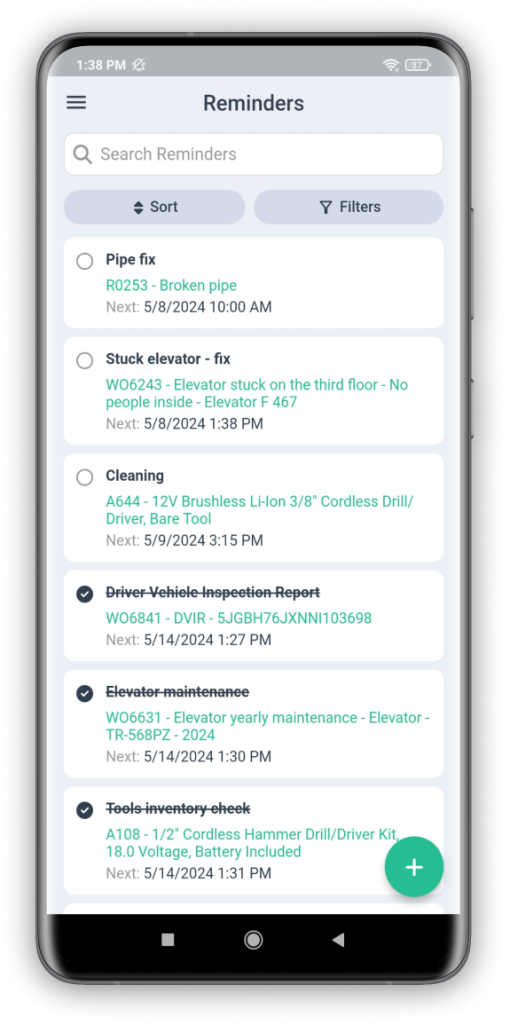
By combining these features, CMMS enables your team to optimize maintenance efforts, ultimately extending equipment lifespan and maximizing the value of your investments.
Enhances Regulatory Compliance
Compliance is a top priority for manufacturers, as failing to meet industry regulations and safety standards can lead to hefty fines, operational shutdowns, and safety risks.
A CMMS simplifies compliance by automating record-keeping and ensuring all maintenance activities align with regulatory requirements.
One way it achieves this is by standardizing maintenance procedures with digital checklists.
These checklists ensure that technicians follow step-by-step procedures, helping prevent human error and ensuring all necessary inspections and servicing tasks are completed correctly.
Here’s an example of an electrical panel inspection checklist.

Additionally, CMMS software streamlines audit preparation by storing maintenance logs, safety inspections, and training records.
Rather than sifting through paper forms or spreadsheets, managers can easily generate reports demonstrating adherence to safety protocols and equipment maintenance schedules.
Another compliance-enhancing feature of CMMS solutions is the ability to establish and track workplace safety requirements, such as wearing proper PPE.
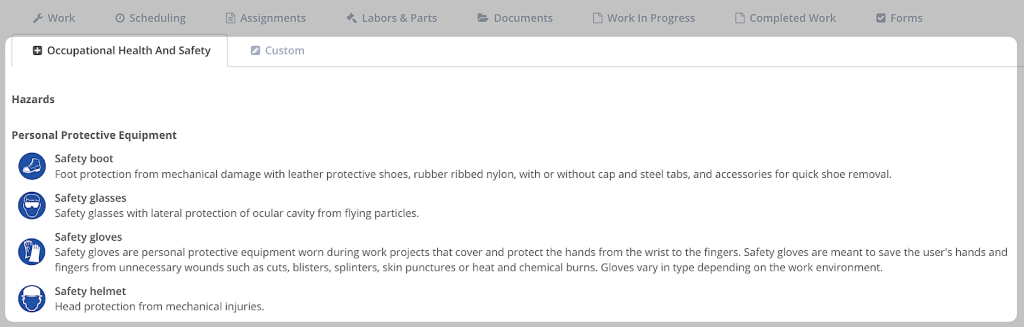
These digital PPE requirements, hazard lists, and safety checklists ensure technicians are properly equipped for maintenance tasks.
This not only reduces workplace hazards but also provides a clear record of adherence to safety measures set by OSHA, ISO, and other industry standards.
Finally, CMMS provides real-time proof of maintenance activities, reducing compliance risks.
If an inspector requests records, you can instantly retrieve a complete history of maintenance logs, technician actions, and completed work orders—it’s all just a few clicks away.
To recap, CMMS software helps manufacturers maintain regulatory compliance, avoid penalties, and uphold high safety standards.
Optimizes Inventory Management
Another key advantage that manufacturing companies gain from a CMMS is automated and streamlined inventory management.
More specifically, CMMS helps you manage the inventory of tools, spare parts, and other supplies.
This helps prevent unnecessary stockpiling and reduces the odds of production delays caused by shortages of key components.
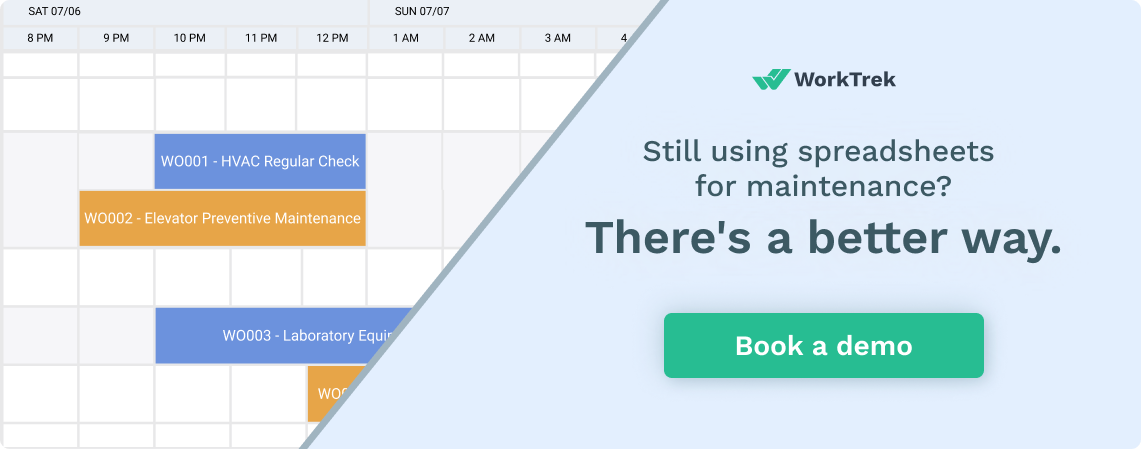
For starters, both the manager and the technician assigned to a task can use a CMMS app to check the availability of tools, spare parts, and materials they need.
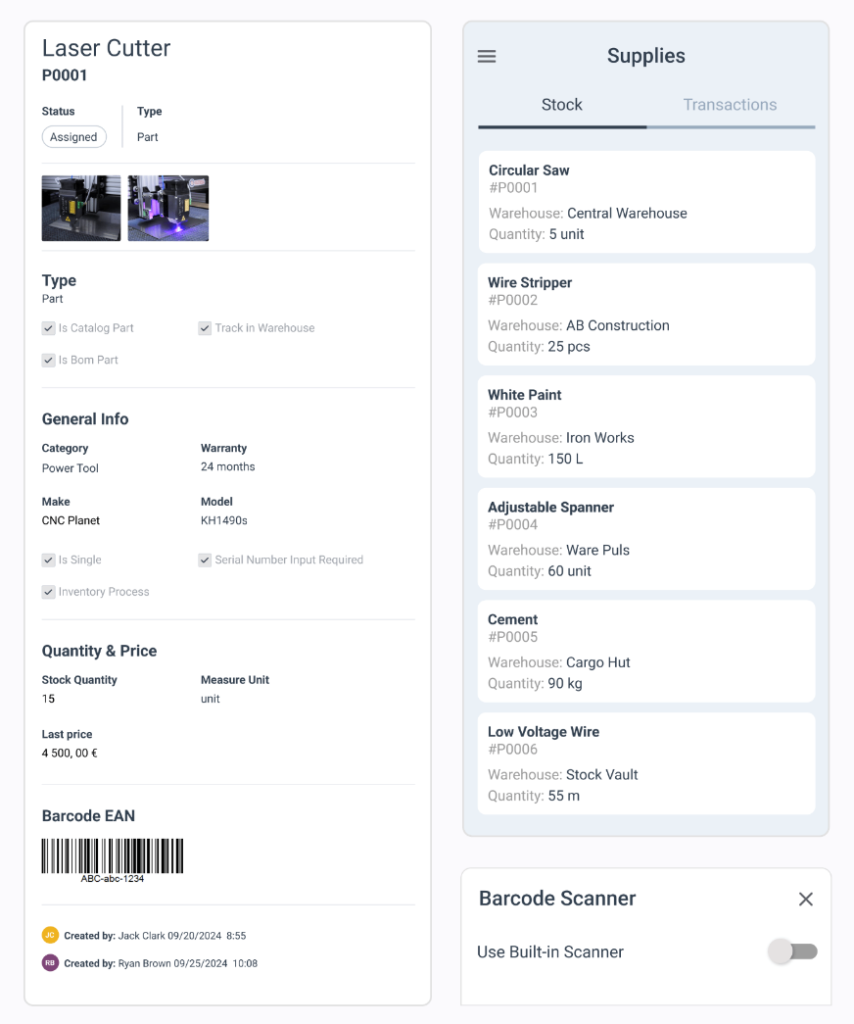
These instant, real-time insights into stock levels are invaluable for service efficiency and directly contribute to reducing downtime when a failure occurs.
As Jeff Shiver, CEO of People and Processes Inc., explains:
“Studies have shown as much as 32% of downtime was related to not having the right parts and materials in the storeroom.”
In other words, if a machine fails and parts are not immediately available, downtime can be extended by nearly a third.
That’s where another CMMS feature—automated low-inventory alerts—comes into play.
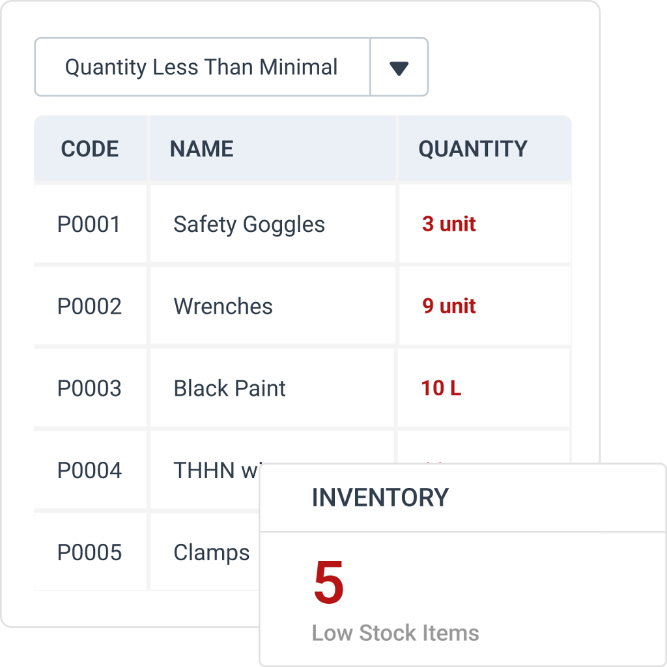
This feature involves setting minimum quantity thresholds for all or just critical inventory items.
As technicians check out the inventory, they record what they took in the CMMS app.
When the system detects that the quantity has fallen below the predefined level, it automatically triggers a low-inventory alert sent to the manager or other authorized personnel.
Additionally, most CMMS software can be easily integrated with your company’s other inventory management systems and business platforms.
Such integrations enable you to align maintenance activities, inventory needs, and procurement planning.
Ultimately, all the above CMMS features allow you to monitor inventory levels, optimize procurement, and ensure that tools, parts, and materials are available at the right time.
Lowers Operational Costs
A CMMS solution helps manufacturers cut operating costs by streamlining maintenance, reducing emergency repairs, and improving resource efficiency.
One major cost-saving advantage comes from proactive maintenance.
Rather than reacting to sudden breakdowns, a CMMS facilitates preventive and predictive maintenance, reducing unexpected failures and unplanned downtime.
As mentioned earlier, downtime can be costly, estimated at $125,000 per hour.
We also just described how CMMS software allows you to proactively manage inventory, which prevents costly stockouts and last-minute purchases, resulting in lower material costs.
These combined benefits translate into significant cost savings.
In fact, BusinessWire research found that companies that implemented a CMMS enjoyed an average 20% reduction in both equipment downtime and material costs.
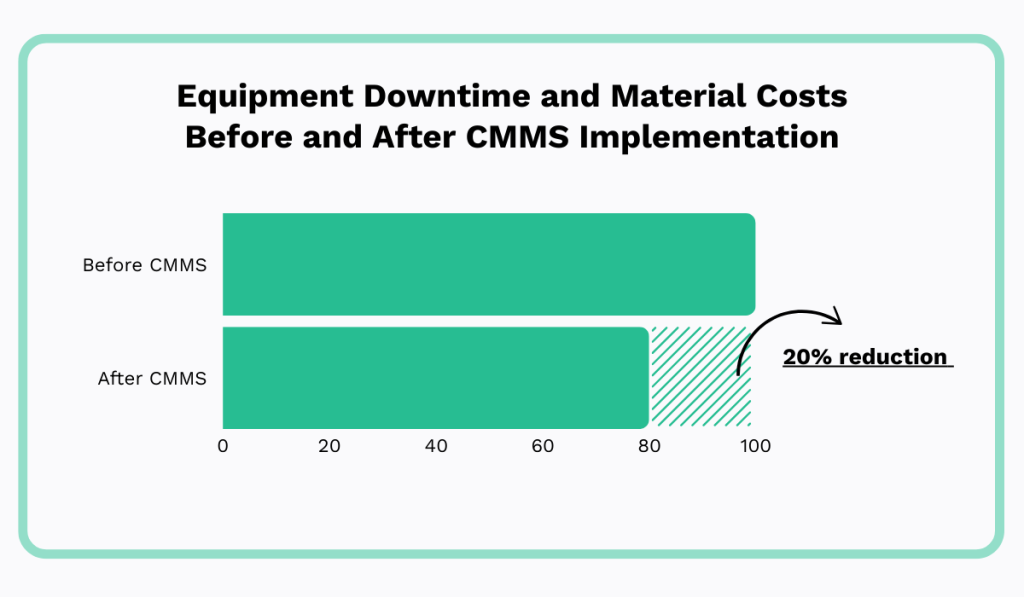
Along with reducing downtime and streamlining inventory, other CMMS features contribute to lower operational costs.
For instance, properly maintained equipment operates more efficiently, reducing energy consumption and minimizing wear and tear.
This leads to lower utility costs and extends asset lifespan, further cutting down on capital expenditures.
Another way CMMS reduces costs is through centralized work order scheduling.
With a single view of all work orders and access to real-time scheduling, managers can efficiently assign tasks, balance workloads, and reduce unnecessary labor costs.
Additionally, some CMMS solutions, like our WorkTrek, allow you to track work hours and task duration, ensuring that labor costs align with actual maintenance needs.
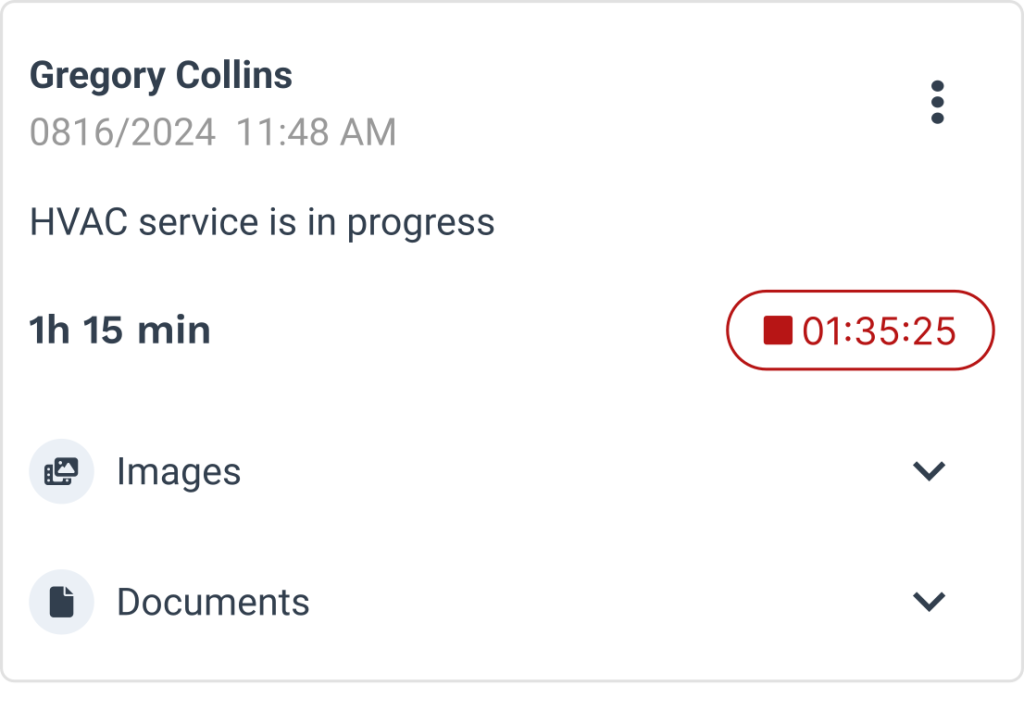
By using the WorkTrek app to clock in and out, technicians create a real-time log of work hours, providing greater transparency and opportunities for cost optimization.
Furthermore, WorkTrek’s features go beyond time tracking, enabling your team to monitor labor, parts, and material expenses—all in one place.
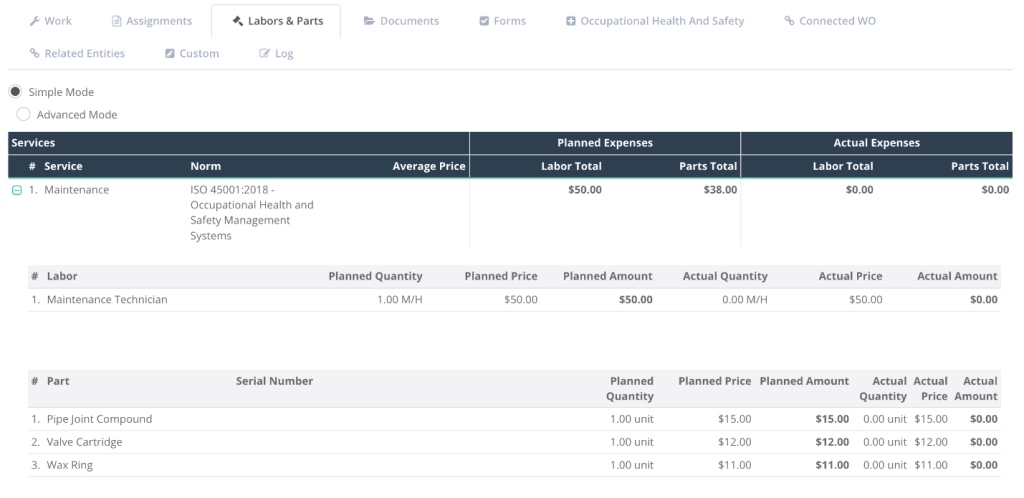
Analyzing these cost breakdowns across different work orders helps identify inefficiencies that can be eliminated or optimized to drive cost savings.
Moreover, a clear view of expected costs helps managers approve work orders strategically, ensuring maintenance stays within budget.
In summary, CMMS software provides the visibility and control you need to reduce operational costs—by preventing equipment failures, streamlining maintenance, and optimizing resource allocation.
Conclusion
After exploring these six key benefits, it’s clear that a CMMS is a powerful tool for enhancing maintenance efficiency, minimizing downtime, and optimizing costs.
It streamlines work order management, improves inventory tracking, ensures compliance, and provides valuable data insights, helping manufacturing operations run smoothly.
By offering real-time visibility and control, CMMS solutions allow manufacturing companies to shift from reactive to proactive maintenance.
So, investing in a CMMS can provide a quick return by improving overall productivity, extending equipment lifespan, and reducing expenses.