Get a Free WorkTrek Demo
Let's show you how WorkTrek can help you optimize your maintenance operation.
Try for freeManufacturers today face major challenges when trying to address failures caused by a lack of clear reactive, preventive, and predictive maintenance processes. Outdated protocols, such as using paper to maintain facilities, setting up schedule reminders, and using multiple decentralized tools to perform routine maintenance, prevent manufacturers from becoming more efficient. Additionally, inefficient maintenance and asset management lead to increased unplanned manufacturing costs, overtime, extended downtime, and the inability to meet production deadlines. It’s time to involve the CMMS to maximize production.
What Is A Computerized Maintenance Management System (CMMS)?
A computer-aided maintenance management system or CMMS is software that centralizes maintenance-related information and facilitates maintenance operations processes. It helps to optimize the utilization and availability of physical equipment such as vehicles, machines, communications, plant infrastructure, and other assets. CMMS systems are found in manufacturing, oil and gas production, power generation, construction, transportation, and other industries where physical infrastructure is critical.
The heart of a CMMS system is its database. It has a data model that organizes information about the assets that a maintenance organization is responsible for maintaining, as well as the equipment, materials, and other resources needed to do so.
What Is CMMS Used For?
CMMS works by tracking and managing data related to maintenance activities. This data can be used to improve the quality of an organization’s services.
Using a CMMS has many benefits in manufacturing for maximizing production, including:
Improving the quality of service
By monitoring and managing data relating to maintenance activities, CMMS can help organizations improve the quality of their services. This improvement in service quality can lead to greater customer satisfaction.
Reduced downtime
By streamlining and optimizing an organization’s maintenance operations, CMMS can help reduce downtime. This reduction in downtime can lead to increased productivity and lower costs.
Increased productivity
By reducing downtime and improving the quality of a company’s services, CMMS can help increase productivity. This increased productivity can lead to increased profits.
Reduced maintenance costs
By streamlining and optimizing an organization’s maintenance operations, CMMS can help reduce maintenance costs. This reduction in costs can lead to increased profits.
Accurate Industrial Maintenance Tracking
CMMS can help organizations accurately track their maintenance activities. This accurate tracking can help improve decision-making and enable better planning.
Asset Visibility
Centralized information in the CMMS database allows managers and maintenance teams to almost instantly call up an asset’s purchase date, maintenance run date, frequency of failures, parts used, efficiency rates, etc.
Workflow Visibility
Dashboards and visualizations can be tailored for technicians and other roles to assess status and progress in near real-time. Maintenance teams can quickly find out where an asset is, what it needs, who needs to work on it, and when.
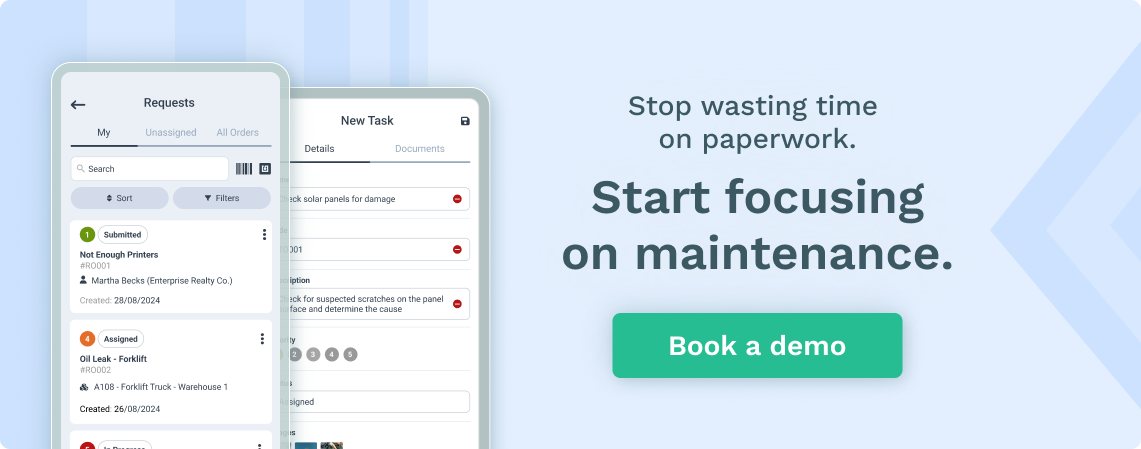
Which Sectors Of Activity Use CMMS Tools?
The use of CMMS is not limited to any particular industry. Any organization that performs maintenance activities can benefit from using a CMMS.
Some of the industries that use CMMS include manufacturing, transportation, and utilities. In these industries, CMMS is used to manage maintenance tasks such as repairing equipment, tracking inventory, and scheduling preventive maintenance.
CMMS is used in many other sectors. For example, town halls use technical service management software to optimize technical operations at the municipal level and improve their efficiency.
CMMS In Manufacturing
In manufacturing, the CMMS not only makes it possible to ensure the maintenance management of all the active equipment in your production chain but also to monitor the maintenance of buildings and networks. The specificity of your industrial site is taken into account by our solutions designed for optimal comfort in the management of your equipment and to constantly improve your industrial performance.
What Are The Expected Benefits?
The benefits expected from the integration of a CMMS in manufacturing are multiple, although difficult to quantify because they are often indirect. We can thus cite:
- Optimization of maintenance and operating costs (labor, spare parts, administrative processing, etc.).
- Improving equipment reliability and availability.
- Purchasing optimization (help with calls for tenders, management of contracts with external service providers, etc.).
- Improved quality of experience feedback thanks in particular to the history of maintenance work.
- Improving intervention planning.
- The reduction of corrective operations in favor of prevention.
- Better control of the activity of subcontractors and external service providers.
- Optimization of inventory management (better output control, help with inventories, optimization of the rotation rate, etc.).
- Traceability of equipment, sometimes to meet regulatory constraints.
- Decision support thanks to the provision of more objective indicators, in particular decisions to renew equipment.
- Etc.
CMMS Is Essential In The Manufacturing
The CMMS plays a preponderant role in manufacturing. An example of the food industry turns out to be relevant. The agri-food sector brings together all the industrial activities aimed at transforming raw materials from livestock, fishing, or agriculture into industrial foods.
Governed by several strict regulations, the sector is managed by severe standards imposed by the Government. A very small mistake can be devastating to consumer health. A tiny imperfection can thus damage the reputation of the manufacturer and also engage its long-term liability.
It is, therefore, necessary to handle the equipment with caution in order to avoid infecting all the production (food). Each maintenance procedure is unique and very specific, but also, the devices admit complex maintenance. It is mandatory that cleanliness and hygiene be exemplary and must in no way cause wear and damage to the devices. They must not be harmful to the staff. To avoid these inconveniences, the plant must set up a maintenance system that continually responds to the environmental conditions in force, to new production constraints, and to changes in standards. This standardization is part of a process that reassures consumers about their fear of intoxication.
In order to comply with this regulation imposed by the Government and to meet its challenges, CMMS software is essential.
Role Of CMMS In Manufacturing
Computer-assisted maintenance management or CMMS is an effective and essential tool for closely monitoring the condition of installations and equipment. It supports all maintenance personnel to maintain production assets in optimal and operational condition.
Thus, computer-assisted maintenance management is inevitable for any industrial company. It allows professionals and production agents and technical services, but also the manager of the company to:
- Discover and be aware of the materials and equipment to be maintained.
- Benefit from an up-to-date maintenance log for each piece of equipment and allows you to trace their history and costs in relation to their maintenance (preventive, curative, etc.).
- Concentrate on all administrative, technical, or even financial documentation of equipment and interventions.
- Schedule periodic maintenance to be carried out on devices and equipment: regulatory checks, quality checks, checks, cleaning, and lubrication.
- Collect and process requests for intervention from operators: improvements, fixes, repairs, etc.
- Organize the activities of external maintenance service providers (control offices, manufacturers, subcontractors, etc.) and internal (maintenance technicians).
- Manage the stock of accessories and spare parts and initiate refueling alarms to prevent stocks from running out.
- Calculate, examine, and optimize maintenance work: lifespan of devices and equipment, availability, reliability, the responsiveness of the team, savings generated by the maintenance service, costs, and working hours.
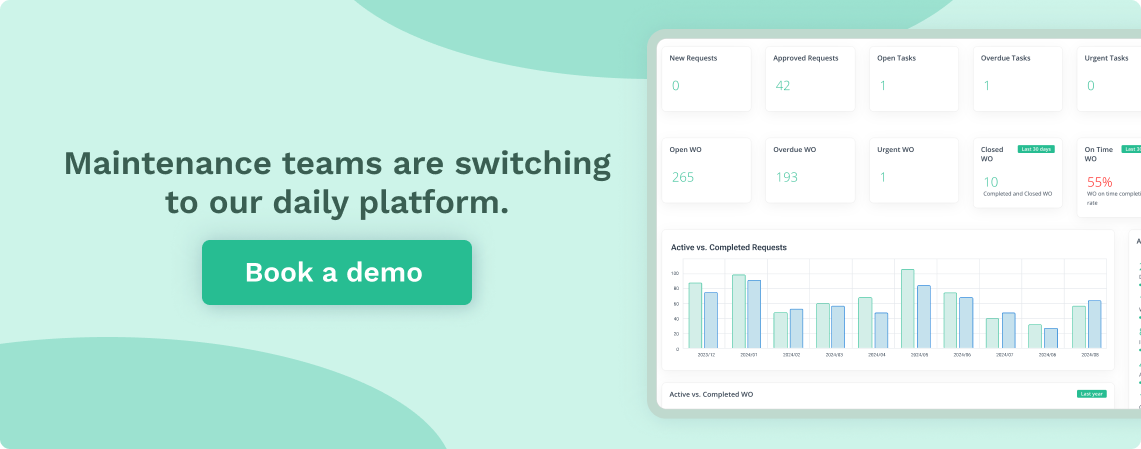
Deploy A CMMS To Meet The Challenges
Maintenance management software not only allows field teams to better organize themselves but also the entire plant to better understand its needs and obtain reliable feedback on the maintenance operations carried out and the costs involved. This is then an opportunity for managers to rethink their strategy. The teams generally apply corrective maintenance (i.e. a maintenance operation on equipment only after it has suffered a malfunction), which nevertheless requires more emergency interventions and interactions between operators. To better deal with the various challenges, it is, therefore, wiser to move towards preventive maintenance, which is easy to set up thanks to a CMMS.
A maintenance management solution improves the traceability of operations and spare parts needs. It allows better monitoring of the various procedures and technicians, who gain autonomy: the creation of tasks and activities, maintenance plans, real-time notifications, calendars, and checklists are all features that simplify all processes. The technicians fill in the tool with all the details of the interventions on the machines, which improves the overall knowledge of the breakdowns and gives precise indications of their frequency. Since the teams take a step back from the operations, it is easier to plan them and therefore to prepare them in advance (make an inventory of the necessary tools, for example).
What Is Total Productive Maintenance?
Equipment failures aren’t just inefficient for a production schedule. They are energy-intensive for each of the interdependent members of all the installations within the plant and are a brake on working properly as a team. Therefore, if there is any problem with the equipment fleet, it leads to delays in deliveries, quality problems, financial losses, and, ultimately, it impacts the overall quality of work.
Fortunately, digital manufacturing has created unprecedented ways to improve long-standing processes in the industry. There are practices, methods, and tools that empower organizations to reduce such equipment losses while maximizing the efficiency of the production system. Total Productive Maintenance (TPM) is one of them.
Initially, Total Productive Maintenance (TPM) was developed and formalized in Japan before World War II. More specifically, it is a so-called “Lean” approach (the “Lean” approach consists of a strategy aimed at pursuing performance through continuous improvement and the elimination of waste) to improve the manufacturing process by combining the traditional practice of preventive maintenance with total quality by control and total employee involvement.
TPM is therefore an organization-wide equipment improvement strategy, which is based on a philosophy comprising 8 pillars, which allows it to achieve a high level of industrial performance. It also differs from preventive maintenance in its participatory approach. Indeed, each member of the organization has a proactive role to play in contributing effectively to this quest for efficiency and quality.
Goal of TPM
The goal of the TPM is to achieve a zero number of equipment failures. Even if this objective may seem utopias or unattainable, it is above all a question of identifying and eliminating the causes of breakdowns. Finally, to promote the development of an evolutionary state of mind, a corporate and work culture in order to constantly and sustainably improve productivity within production.
Total Productive Maintenance engages every member of your organization to minimize all types of losses as it focuses on different targets: failures, incidents, slowdowns, energies, environmental pollution…
This strategy helps you detect, expose, and eliminate minor equipment faults, establish and maintain baseline equipment conditions, identify and establish optimal operating conditions, and correct each identified failure.