Get a Free WorkTrek Demo
Let's show you how WorkTrek can help you optimize your maintenance operation.
Try for freeWhat are the costly consequences of deferred maintenance?
Deferred maintenance can have serious financial and operational consequences for facilities and organizations. When routine upkeep is postponed, minor issues often snowball into major problems, leading to increased repair costs and potential safety hazards.
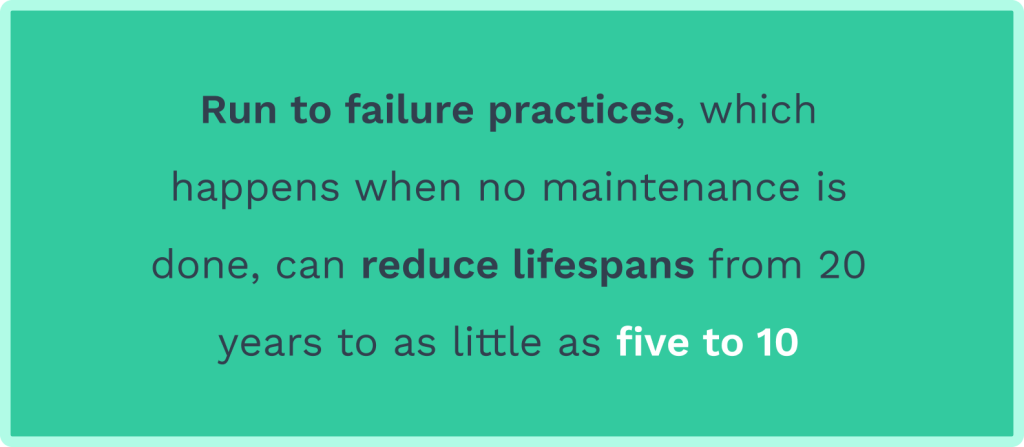
Neglecting maintenance can compound costs at a rate of 7% per year, making it crucial for facility managers to address issues promptly. Ignoring maintenance needs can impact various aspects of a building or infrastructure. From compromised safety and security to decreased operational efficiency, the effects of deferred maintenance are far-reaching.
Faulty, unrepaired wiring may increase fire risks, while neglected flooring could lead to slip-and-fall accidents. These issues pose dangers to occupants and expose organizations to potential legal liabilities.
Key Takeaways
- Deferred maintenance can lead to exponential cost increases and safety risks over time.
- Regular inspections and prompt repairs are essential for maintaining operational efficiency and asset value.
- Implementing proactive maintenance strategies helps prevent emergencies and ensures long-term facility sustainability.
Understanding Deferred Maintenance
Deferred maintenance is a critical concept in facility management with significant financial implications. It involves postponing necessary repairs and upkeep, often increasing costs and risks over time.
Definition and Scope of Deferred Maintenance
Deferred maintenance refers to delaying repairs or maintenance activities on physical assets. This postponement can affect various systems and structures, including buildings, equipment, and infrastructure.
Deferred maintenance encompasses various tasks, from minor repairs to major overhauls. It often results from budget constraints, limited resources, or competing organizational priorities.
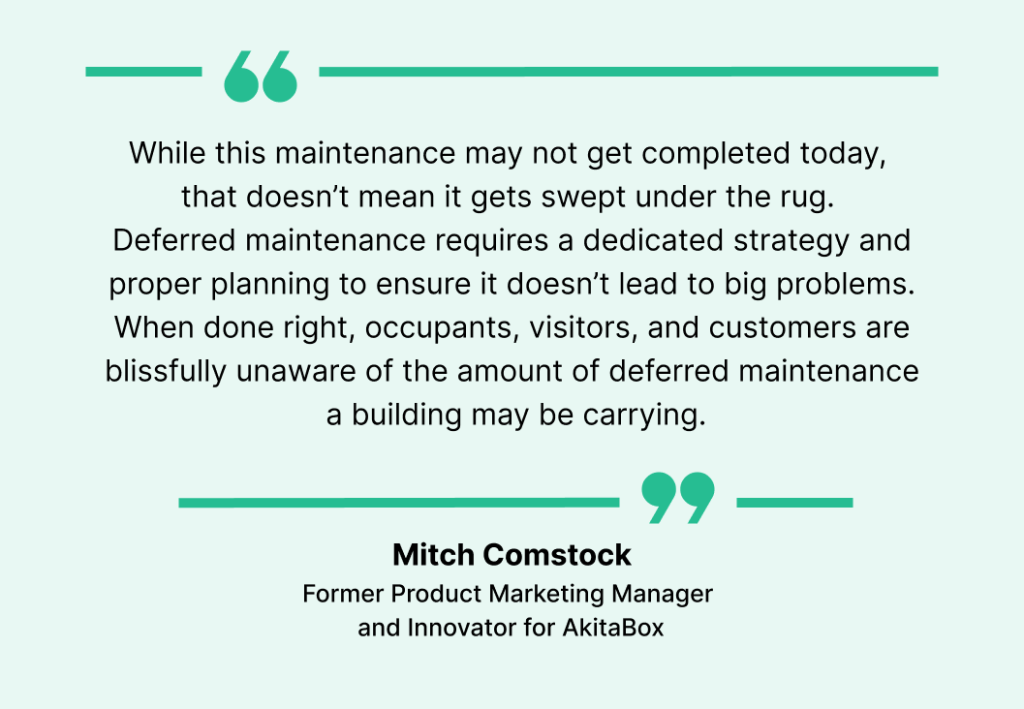
Addressing a deferred maintenance backlog is crucial for facility managers to ensure the longevity and safety of assets.
Neglecting maintenance can compromise the safety, security, and functionality of facilities. For instance, failing to repair faulty wiring increases fire risks, while ignoring damaged flooring may lead to accidents.
Deferred Maintenance Will:
- Increase maintenance costs and operational expenses
- It can lead to entire system failure
- Delaying maintenance can increase environmental damage
- While reducing short-term costs, it can increase future costs
Differences Between Deferred and Preventive Maintenance
Deferred maintenance and preventive maintenance represent contrasting approaches to facility upkeep.
Preventive maintenance involves regular, scheduled activities to maintain assets and prevent breakdowns.
Unlike deferred maintenance, preventive maintenance aims to address issues before they escalate. It typically includes routine inspections, cleaning, and minor repairs to keep systems running efficiently.
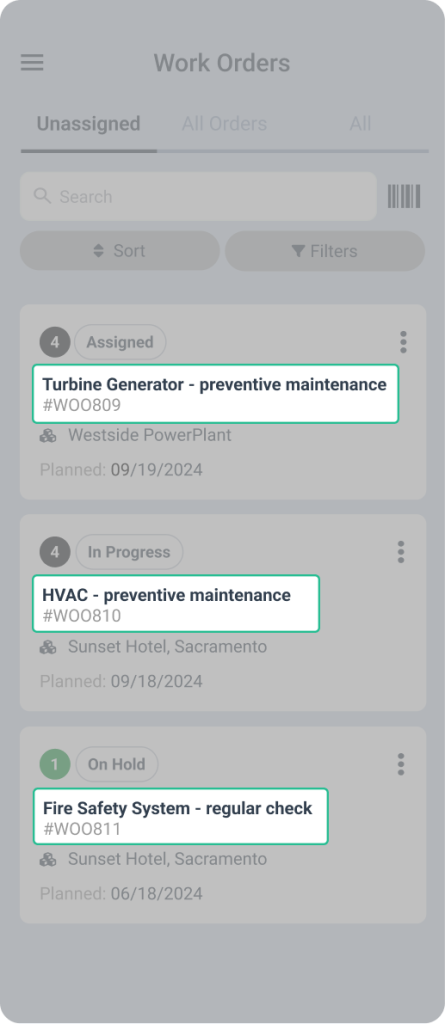
Preventive maintenance often proves more cost-effective in the long run. It helps extend asset lifespan, reduce unexpected breakdowns, and minimize operational disruptions.
Deferring maintenance can lead to higher future costs. Research suggests that every $1 deferred in maintenance may result in $4 of capital renewal needs later. It can also have severe consequences and lead to faulty equipment.
Real-world Examples of Deferred Maintenance Consequences
Several organizations have faced severe consequences due to deferred maintenance. Here are some notable case studies:
- Arecibo Observatory Telescope Collapse
In December 2020, the iconic Arecibo Observatory telescope in Puerto Rico collapsed after 57 years of operation. The collapse was primarily due to deferred maintenance, resulting in a $500 million disaster. This incident had significant financial implications and created a major safety risk for over 180,000 people in the surrounding area.
- Denver International Airport’s Growing Maintenance Backlog
Denver International Airport (DEN), the fifth-busiest airport in the United States, has struggled with a growing deferred maintenance backlog. The airport, which generates $33.5 billion annually and serves over 69 million passengers, has faced out-of-order escalators, broken bathroom fixtures, and other maintenance problems. The backlog includes routine inspections and preventive work on over 7,000 items, including building systems, parking lots, and large equipment11. - U.S. General Services Administration (GSA) Deferred Maintenance
As of 2022, the GSA faced a staggering $3.1 billion backlog in deferred maintenance and repairs. This includes persistent issues such as water leaks and outdated safety systems. During a House hearing, the GSA admitted that it is “suffering from the consequences of significant deferred maintenance, driven by inadequate investment”8. - U.S. Forest Service, Fish and Wildlife Service, and National Park Service
These agencies, along with the Bureau of Indian Education, have reported tens of billions of dollars in deferred maintenance. The backlog has accumulated over decades, resulting in diminished asset quality, shortened asset life, and significantly higher maintenance and repair costs.
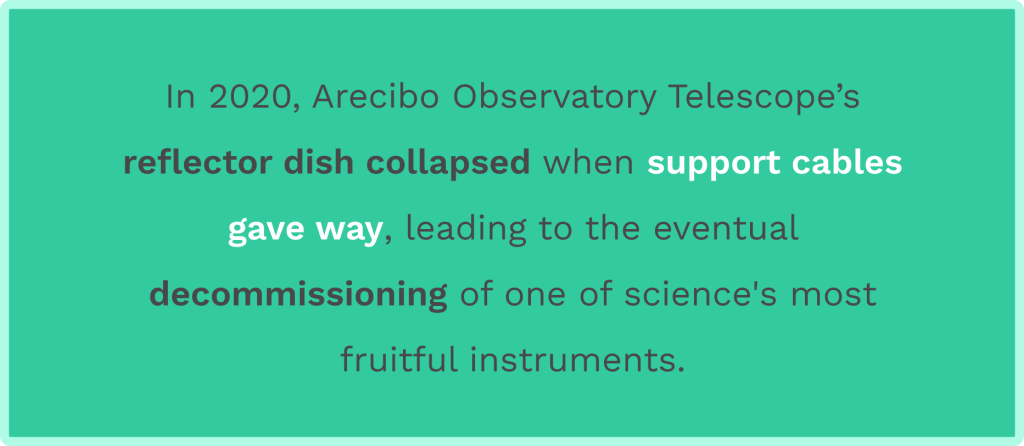
Such incidents underscore the need for comprehensive maintenance strategies to prevent costly emergencies and ensure the longevity of facilities.
Below are a few interesting statistics about deferred maintenance:
- Every $1 deferred in maintenance costs $4 of capital renewal needs in the future.
- On average, deferred maintenance can lead to future expenses equal to or greater than the part cost squared or 15 times the total repair cost.
- Deferred maintenance compounds at a rate of 7% per year7.
- According to some studies, delaying maintenance can increase future costs for the same work by as much as 600%.
These case studies and statistics highlight the significant financial, safety, and operational risks of deferring maintenance across various sectors and organizations.
Financial Repercussions
Deferred maintenance leads to significant financial consequences for organizations. These impacts ripple through budgets, operational costs, and long-term financial planning.
Budget Constraints and Funding Issues
Budget constraints often drive decisions to defer maintenance. Facility managers face challenges balancing immediate needs with long-term maintenance requirements within a limited maintenance budget.
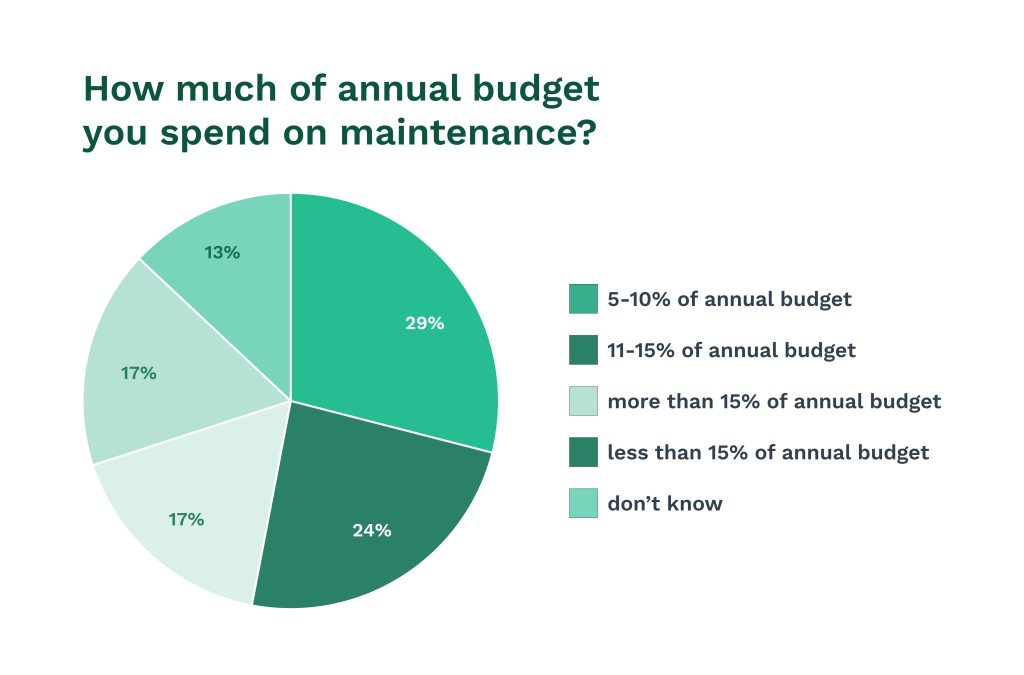
Limited funding forces difficult choices between crucial repairs and routine maintenance.
Organizations may struggle to allocate sufficient resources for maintenance.
This creates a cycle where deferred tasks accumulate, leading to more extensive and costly repairs in the future.
Due to a lack of maintenance, capital renewal costs increase as systems and structures deteriorate faster. This puts additional strain on already tight budgets.
The Hidden Costs of Deferring Maintenance
Deferred maintenance carries numerous hidden costs that may not be immediately apparent. As equipment performance declines, energy efficiency decreases, resulting in higher utility bills.
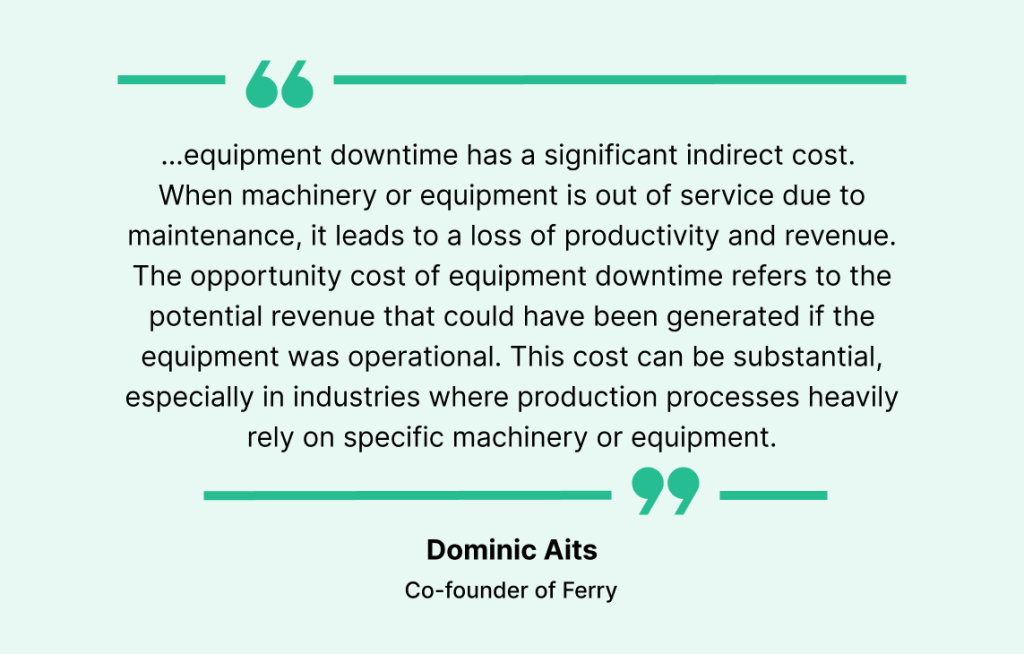
Property values may decrease due to visible deterioration and outdated systems. This can impact an organization’s overall financial health and borrowing capacity.
Neglected maintenance can compromise safety, potentially leading to liability issues and increased insurance premiums.
Lost productivity from equipment downtime or facility closures adds to the hidden financial toll of deferred maintenance.
Increased Operational and Emergency Repair Costs
Delaying routine maintenance often results in more frequent breakdowns and emergency repairs. An understaffed maintenance team can exacerbate this issue, leading to a backlog of essential maintenance tasks and higher operational costs.
Emergency repair costs can quickly deplete maintenance budgets, forcing the reallocation of funds from other areas. This creates a domino effect on overall operational costs.
Equipment lifespan and effectiveness shortens when regular maintenance is neglected, necessitating premature replacements. This accelerates capital expenditure cycles and strains financial resources.
Operational disruptions due to unexpected failures lead to lost revenue and decreased efficiency, further impacting an organization’s bottom line.
Impact on Property and Assets
Deferred maintenance significantly affects property values and asset conditions. Neglecting upkeep leads to deterioration and financial consequences for owners.
Devaluation of Property and Assets
Postponing repairs and upkeep can substantially reduce a property’s market value. Potential buyers often perceive neglected maintenance as a liability requiring additional investment.
Visible signs of wear, such as peeling paint or cracked pavements, create negative first impressions.
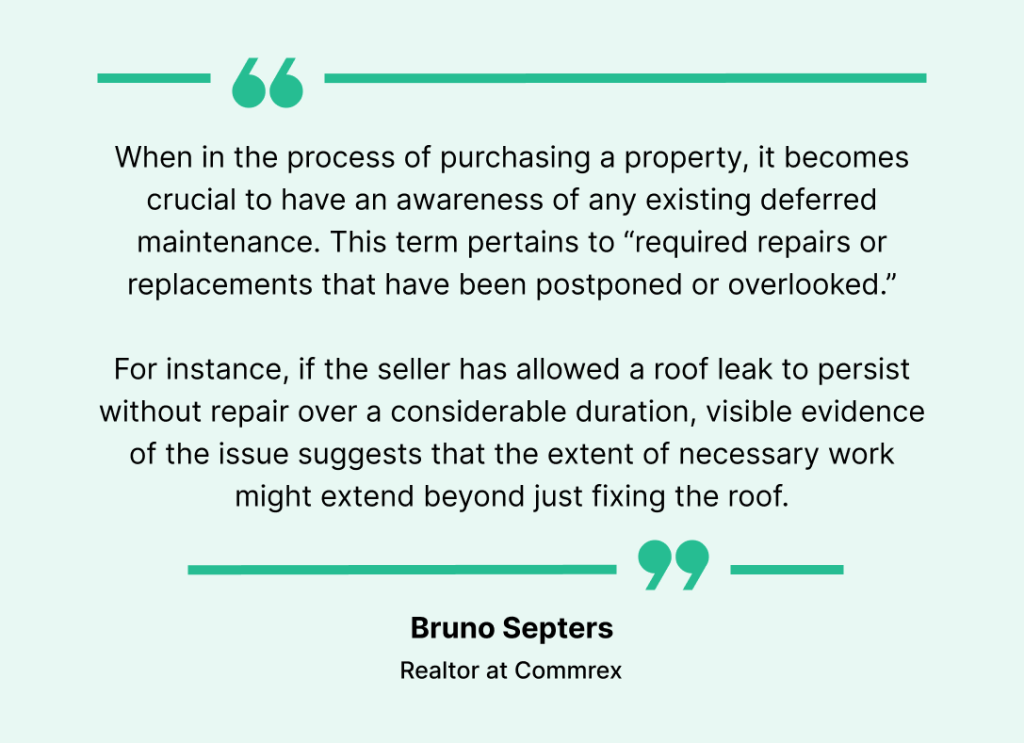
These issues can deter prospective buyers or tenants, leading to extended vacancy periods and reduced rental income.
Outdated or malfunctioning systems like HVAC or plumbing further diminish property appeal. Inefficient equipment increases operating costs, making the property less attractive to cost-conscious investors.
Asset Degradation and Maintenance Backlog
Deferred maintenance accelerates asset degradation, leading to a growing backlog of necessary repairs. As minor issues worsen, they often cascade into more serious problems, requiring costlier interventions.
Equipment and infrastructure deteriorate faster without regular upkeep. This shortened lifespan means more frequent replacements, increasing long-term capital expenditures.
The maintenance backlog can quickly become overwhelming. Prioritizing urgent repairs may leave less critical issues unaddressed, compounding the problem over time.
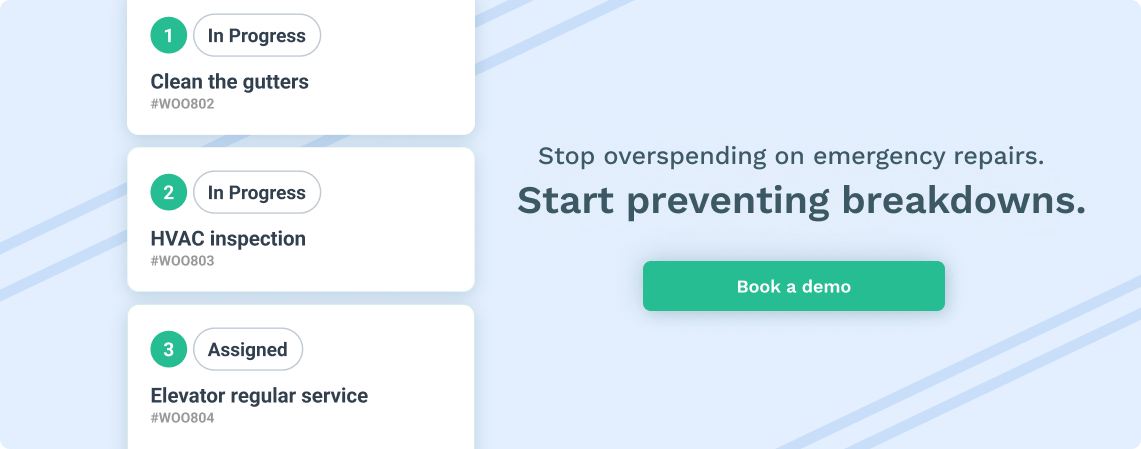
Neglected assets pose increased safety risks. Faulty wiring, damaged flooring, or compromised structural elements can lead to accidents, potentially resulting in legal liabilities and reputational damage.
Operational Efficiency and System Reliability
Deferred maintenance directly impacts equipment performance and system stability. Neglecting upkeep leads to decreased efficiency and heightened failure risks.
Effects on Equipment Efficiency
Postponing necessary maintenance and ignoring routine maintenance tasks cause equipment to operate below optimal levels.
Machinery and systems gradually deteriorate, consuming more energy to perform the same tasks. This reduction in efficiency translates to higher operational costs and decreased productivity.
Wear and tear accumulates on components, leading to increased friction and reduced output. HVAC systems, for example, may struggle to maintain desired temperatures, working harder and using more electricity. Production lines slow down as machines require more frequent adjustments and repairs.
Regular maintenance, such as lubrication, cleaning, and calibration, becomes less effective when delayed. This has a compounding effect on efficiency losses over time.
Risks of System Failure
Neglecting maintenance increases the likelihood of catastrophic breakdowns. Critical systems may fail unexpectedly, causing operational disruptions and safety hazards.
These failures often occur inopportune times, leading to costly emergency repairs and extended downtime.
Interdependent systems can create a domino effect when one component fails. For instance, a malfunctioning cooling system might cause overheating in electronic equipment, potentially leading to data loss or fire hazards.
Unaddressed minor issues can escalate into major problems. For example, a small leak in a pipe, if left unchecked, may result in extensive water damage and mold growth.
Regular inspections and timely repairs are crucial for preventing such cascading failures.
Safety and Compliance Implications
Deferred maintenance poses significant threats to safety and legal compliance. Neglecting repairs and upkeep can create dangerous environments and expose organizations to regulatory violations.
Heightened Safety Risks and Hazards
Postponing necessary maintenance can lead to unsafe conditions for building occupants and employees. Faulty electrical systems increase fire risks, and damaged flooring creates trip hazards.
Deteriorating structures may become unstable over time. Neglected HVAC systems can cause poor air quality and health issues.
Malfunctioning safety equipment like fire alarms or sprinklers leaves facilities vulnerable.
Regular inspections and repairs are crucial for identifying and addressing potential dangers before incidents occur. Proactive maintenance helps prevent accidents, injuries, and property damage.
Legal and Compliance Complications
Proper facility maintenance often violates building codes and safety regulations, resulting in fines, penalties, and legal liabilities for property owners and managers.
Non-compliance with accessibility standards may lead to discrimination lawsuits. Ignoring environmental regulations can trigger investigations and sanctions from government agencies.
Insurance companies may deny claims for damages caused by neglect. Workplace safety violations can prompt investigations by OSHA or other regulators.
Proper documentation of maintenance activities is essential for demonstrating due diligence. Regular audits help ensure ongoing compliance with relevant laws and standards.
Maintenance Strategies to Mitigate Costs
Effective maintenance strategies can significantly reduce the long-term costs associated with deferred maintenance. These approaches focus on proactive measures and leveraging technology to optimize facility upkeep.
Developing a Comprehensive Maintenance Plan
A well-crafted maintenance plan serves as the foundation for cost-effective facility management. It should outline all maintenance activities’ clear goals, responsibilities, and timelines.
Key components of a comprehensive plan include:
- Asset inventory and condition assessment
- Prioritization of maintenance tasks
- Budget allocation for routine and preventive maintenance
- Emergency response procedures
- Preventive maintenance tasks
- Routine inspections
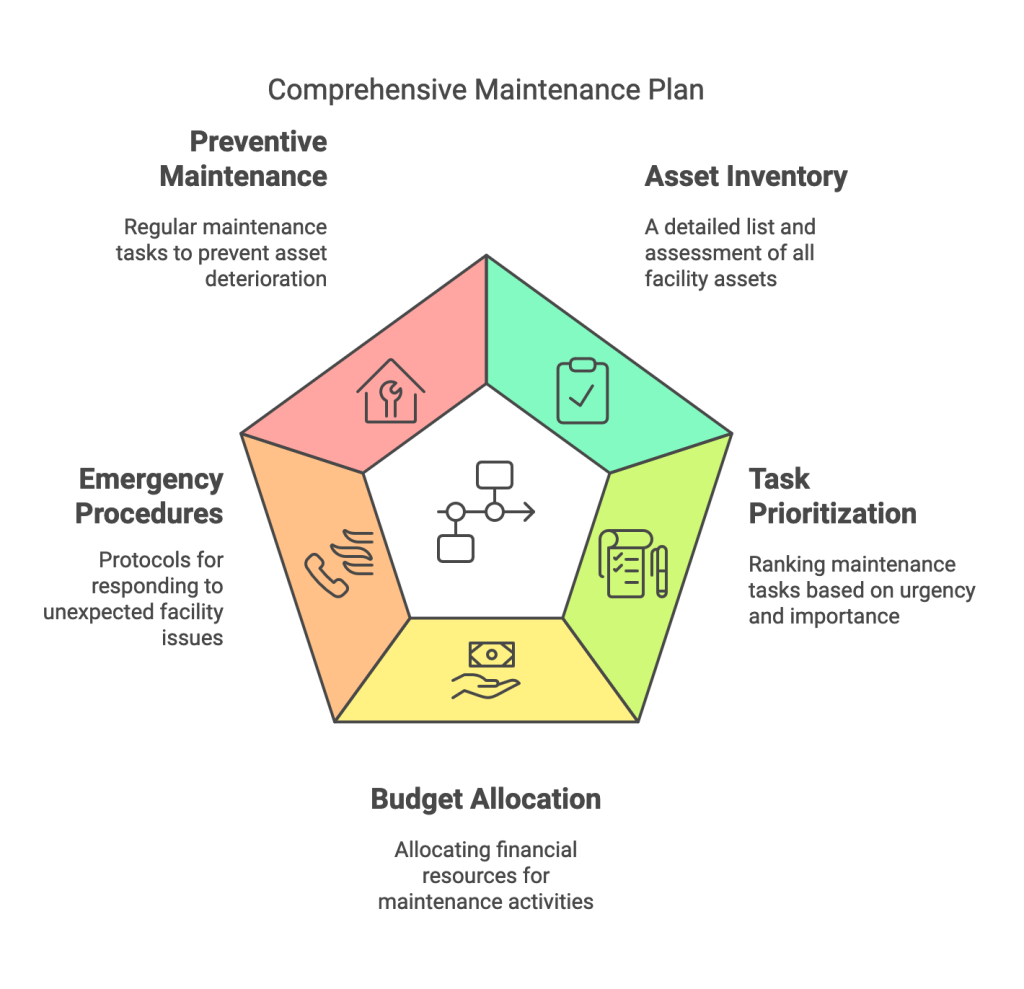
Organizations should regularly review and update their maintenance plans to align with current needs and resources. This proactive approach helps prevent minor issues from escalating into costly repairs.
Effective maintenance planning can significantly reduce safety risks and improve facility functionality. By addressing potential problems early, companies can avoid the high costs of emergency repairs and equipment failures.
Implementing Predictive and Preventative Maintenance Programs
Predictive and preventative maintenance programs minimize unexpected breakdowns and extend asset lifespans. These programs utilize data-driven insights and regular inspections to anticipate and address potential issues before they become critical.
Predictive maintenance techniques include:
- Vibration analysis
- Thermal imaging
- Oil analysis
- Ultrasonic testing
Preventative maintenance involves scheduled inspections, lubrication, cleaning, and minor repairs. Preventive maintenance helps maintain equipment efficiency and reduces the likelihood of sudden failures.
Proactive maintenance strategies can lead to significant cost savings over time. By identifying and addressing issues early, organizations can avoid the high costs of emergency repairs and equipment replacements.
Role of CMMS in Maintenance Management
Computerized Maintenance Management Systems (CMMS) are vital in modern maintenance strategies. These software solutions help organizations streamline maintenance operations, track assets, and make data-driven decisions.
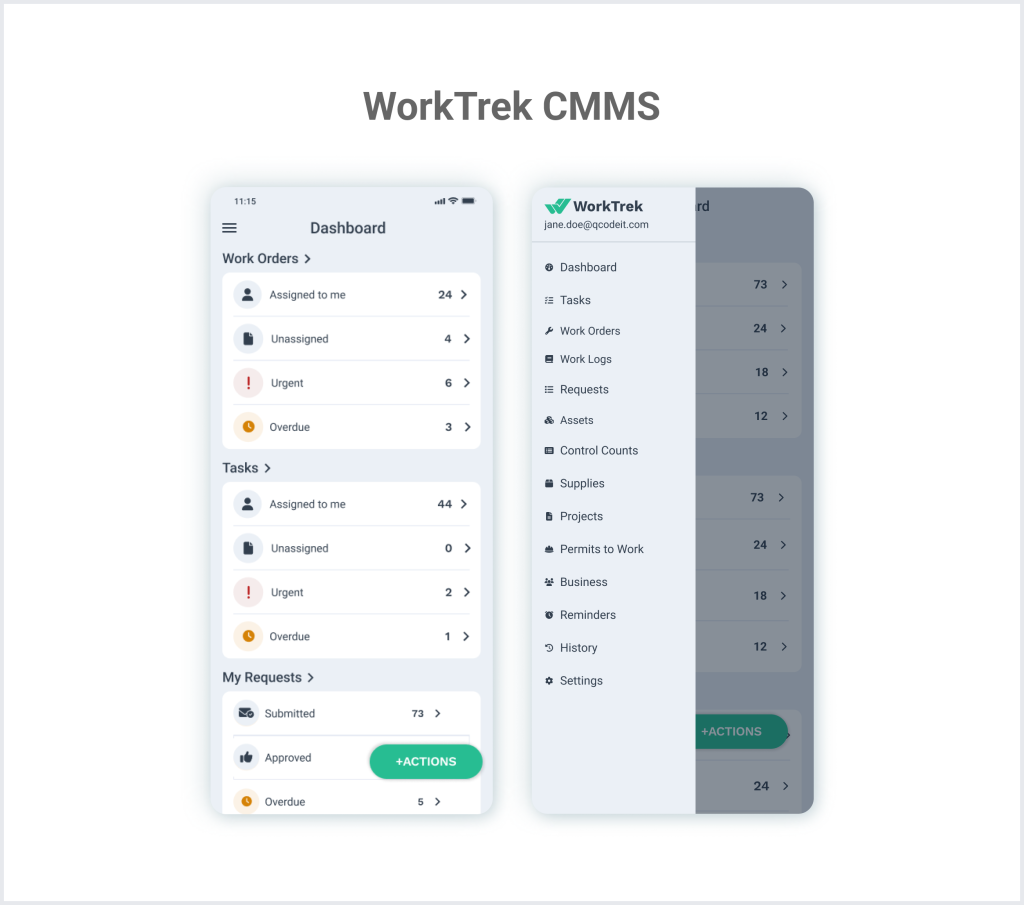
Key benefits of a computerized maintenance management system include:
- Automated work order generation and tracking
- Real-time asset performance monitoring
- Inventory management for spare parts
- Detailed maintenance history and reporting
CMMS solutions enable maintenance teams to prioritize tasks effectively and allocate resources efficiently. By providing a centralized platform for maintenance data, these systems support better decision-making and long-term planning.
Implementing a CMMS can help organizations identify patterns in equipment failures and maintenance needs. This insight allows for more accurate budgeting and resource allocation, ultimately reducing the overall cost of maintenance.
The Role of Regular Inspections and Facility Management
Regular inspections and effective facility management are crucial for preventing costly maintenance issues. These practices allow for early problem detection and optimal resource allocation to address potential concerns before they escalate.
Conducting Regular Inspections for Early Detection
Regular inspections are vital in identifying maintenance needs before they become significant problems. Facility managers should establish comprehensive inspection schedules covering all building systems and components.
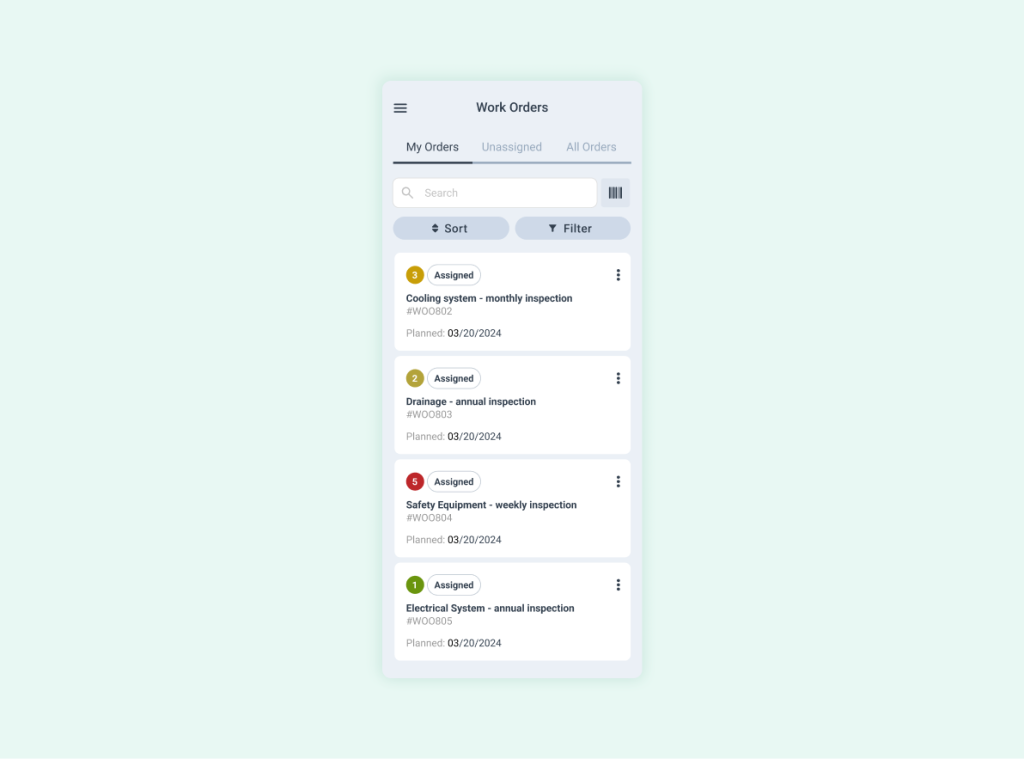
These inspections help detect issues such as:
- Structural damage
- Plumbing leaks
- Electrical faults
- HVAC inefficiencies
Early detection through inspections can significantly reduce repair costs and prevent safety hazards. For example, identifying a small roof leak during an inspection can prevent extensive water damage and mold growth.
Inspections also provide valuable data for planning future maintenance activities and budgeting. This information helps facility managers prioritize tasks and allocate resources effectively.
Facilities Management and Resource Allocation
Effective facilities management involves strategic resource allocation to maintain building systems and infrastructure. Managers must balance immediate needs with long-term preservation goals.
Key aspects of resource allocation in facilities management include:
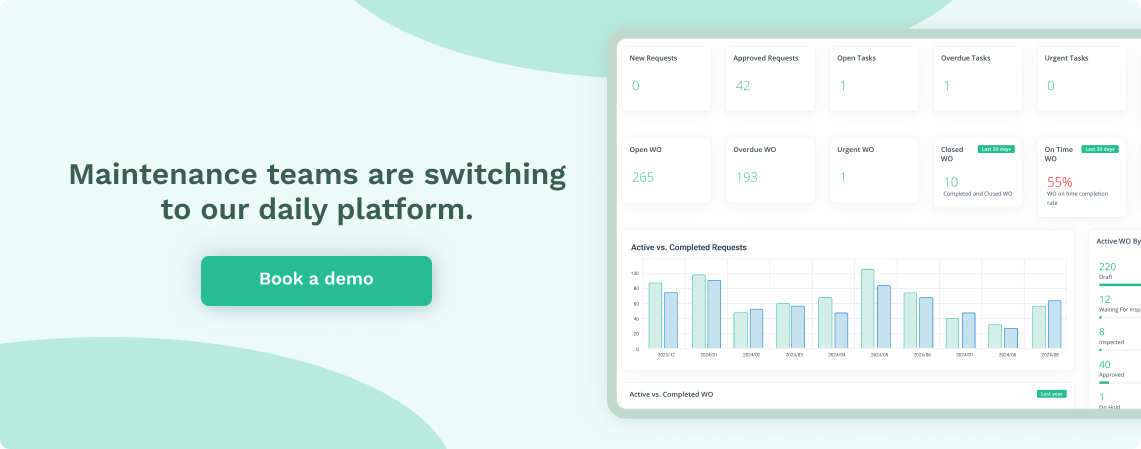
- Prioritizing maintenance tasks based on urgency and impact
- Budgeting for routine maintenance and unexpected repairs
- Staffing and training maintenance personnel
- Investing in preventive maintenance technologies
Proper resource allocation can lead to significant cost savings by addressing maintenance needs promptly and efficiently. It helps prevent the escalation of repair costs associated with deferred maintenance.
Facilities managers should also consider implementing computerized maintenance management systems (CMMS) like WorkTrek to track assets, schedule maintenance, and analyze performance data. These tools can improve decision-making and resource allocation.
Long-Term Considerations
To ensure building longevity and operational efficiency, addressing deferred maintenance requires careful planning and strategic investments. Proper funding allocation and system maintenance are crucial elements for sustainable facility management.
Planning for Capital Renewal and Maintenance Funding
Capital renewal planning is essential for preventing deferred maintenance. Facility managers must develop comprehensive strategies to secure adequate funding for ongoing repairs and upgrades.
This involves creating detailed asset inventories and condition assessments.
Budget allocation should prioritize critical systems and high-impact areas.
Implementing a capital renewal fund can help organizations set aside resources for future major repairs and replacements. Regular financial reviews ensure maintenance budgets align with facility needs.
Proactive funding approaches may include:
- Multi-year budgeting cycles
- Dedicated maintenance reserve accounts
- Exploring alternative funding sources like grants or public-private partnerships
Maintaining Building Systems for Operational Longevity
Effective building system maintenance is crucial for extending operational life and minimizing costly breakdowns. Facility managers should implement robust planned maintenance schedules for all critical systems.
Key focus areas include:
- HVAC systems
- Electrical infrastructure
- Plumbing and water management
- Roofing and building envelope
Regular inspections and preventive maintenance can identify potential issues before they escalate. Computerized maintenance management systems (CMMS) like WorkTrek can help track maintenance history, schedule tasks, and analyze system performance trends.
Investing in energy-efficient upgrades and modern building automation systems can reduce operational costs and improve system reliability. Training staff on proper maintenance procedures ensures consistent care and early problem detection.
Environmental and Health Effects
Deferred maintenance can significantly impact indoor air quality and energy efficiency in buildings, directly affecting occupant health and operational costs.
Impact on Indoor Air Quality
Neglecting HVAC system maintenance leads to poor indoor air quality, increasing health risks for occupants. Dirty air filters and ductwork accumulate allergens, dust, and mold spores. This buildup can trigger allergies, respiratory issues, and other health problems.
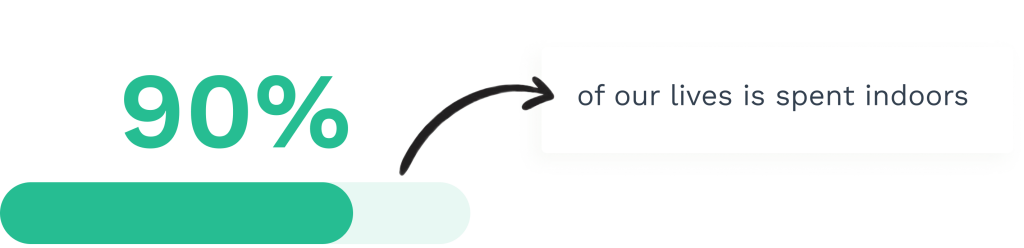
Poorly maintained ventilation systems fail to remove indoor pollutants effectively.
Carbon dioxide levels may rise, causing headaches and decreased cognitive function.
Leaky ductwork can introduce outdoor contaminants, further compromising air quality.
Regular HVAC cleaning and filter replacements are crucial. These tasks remove harmful particles and ensure proper air circulation. Neglecting them allows pollutants to accumulate, creating an unhealthy indoor environment.
Energy Efficiency and Cost Savings
Deferred maintenance on HVAC systems leads to increased energy costs. Dirty coils, clogged filters, and worn components force the system to work harder, consuming more energy.
This inefficiency can significantly raise utility bills.
Leaky ductwork wastes conditioned air, further increasing energy consumption. Poorly maintained equipment operates less efficiently, increasing energy usage and costs.
Regular maintenance keeps HVAC systems running at peak efficiency, reducing energy consumption and costs.
Timely repairs and upgrades can lead to substantial energy savings. Replacing outdated equipment with energy-efficient models can dramatically reduce operating costs.
Proper insulation and sealing prevent energy waste, improving overall building efficiency.
Summary
The consequences of deferred maintenance extend beyond immediate cost savings, creating a complex web of financial, operational, and safety challenges for organizations.
As demonstrated by notable cases like the Arecibo Observatory collapse and Denver International Airport’s maintenance backlog, postponing essential upkeep can lead to catastrophic failures and exponentially higher costs—with every dollar deferred potentially resulting in four dollars of future capital renewal needs.
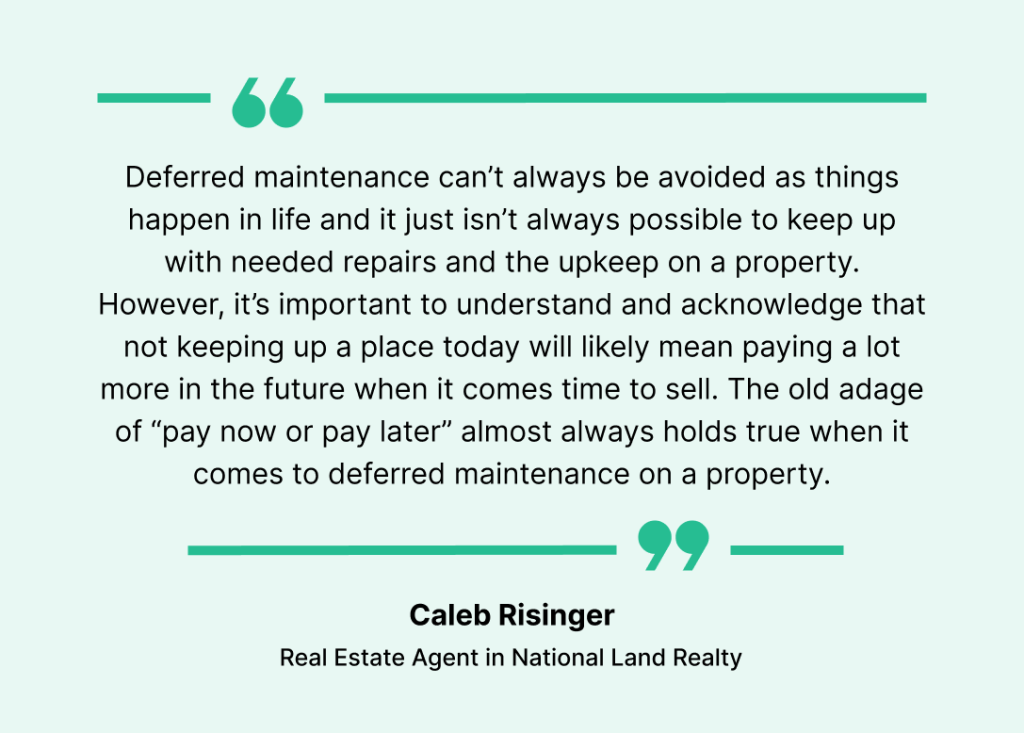
The solution is implementing comprehensive maintenance strategies prioritizing regular inspections, preventive care, and proper resource allocation.
Organizations can better manage their assets, ensure regulatory compliance, and maintain optimal operational efficiency by leveraging modern tools like CMMS systems and adopting proactive maintenance approaches.
The choice between addressing maintenance needs promptly or deferring them often determines not just the longevity of physical assets but also the safety of occupants, environmental impact, and long-term financial health of the organization.