Get a Free WorkTrek Demo
Let's show you how WorkTrek can help you optimize your maintenance operation.
Try for freeAre you wondering how to digitalize your maintenance for improved efficiency? This article will guide you through practical steps to transition to digital maintenance. You’ll find tips on choosing tools, using real-time data, and enhancing team skills.
We will discuss using a CMMS system to reduce human error and allow for live data access. Additionally, this article will discuss the benefits of implementing Preventive Maintenance Checklists, which can improve the organization’s efficiency.
Transition to Digital Maintenance Procedures
Traditional maintenance methods are inefficient and generally paper-based. Manual data collection and poor history tracking can lead to delays, errors, and missed maintenance tasks.
This hampers productivity, increasing the risk of equipment failure and unplanned downtime. The need for digitization has never been more pressing.
Maintenance organizations face significant challenges related to equipment availability, emphasizing the importance of preventive maintenance strategies.
Digitization of maintenance procedures can enhance operational efficiency and productivity, allowing companies to avoid reliance on outdated paper-based systems and instead utilize real-time data for informed decision-making.
Benefits of Digital Maintenance
Digitization of maintenance procedures can enhance operational efficiency and productivity, allowing companies to avoid reliance on outdated paper-based systems and instead utilize real-time data for informed decision-making.
Improve Efficiency by Ditching Paper-Based Processes
Digital maintenance management offers a solution that improves efficiency and reduces that improves efficiency and reduces human error. Automating maintenance procedures and delivering real-time data access enables technicians to make swift, informed decisions, enhancing maintenance operations.
Transitioning from paper-based processes to digital systems guarantees accurate tracking and timely completion of all maintenance tasks.
Source: WorkTrek
Real-Time Data
One key benefit of digital maintenance is the ability to provide frontline workers with real-time data. This access to up-to-date information allows them to perform maintenance tasks more effectively, reducing the likelihood of errors and improving overall safety.
A well-prepared transition strategy is essential. Implementing the right digital tools and specialized technical teams ensures successful adaptation to digital maintenance.
Selecting the Right Tools for Digital Maintenance
It all starts with selecting the right tools. This process is essential to using Computerized Maintenance Management Systems (CMMS), which significantly streamline maintenance tasks, diminish equipment downtime, and boost scheduling efficacy.
CMMS offers a centralized management platform that helps keep all maintenance activities accounted for without oversights.
Illustration: WorkTrek / Quote: Forbes
Customized Maintenance Procedures
It all starts with selecting the right tools. The first step is choosing a suitable Computerized Maintenance Management System (CMMS) that significantly streamlines maintenance tasks, diminishes equipment downtime, and boosts scheduling efficacy.
CMMS offers a centralized management platform that helps keep all maintenance activities accounted for without oversights.
Fine Tune Maintenance Procedures
Individual machines have unique maintenance-related requirements that must be addressed through digitized preventive maintenance procedures. This includes the need for real-time data access and digital checklists to ensure efficient operational management.
Integrating IoT devices into operations is invaluable in monitoring equipment conditions live. These devices gather continuous data streams that support preventive maintenance measures and reduce the chances of unexpected equipment failure.
Augmented Reality and Smart Glasses
Employing smart glasses can reshape how technical teams accomplish their work. They provide augmented reality guidance by superimposing critical digital information onto real-world scenarios within technicians’ field of view.
The combination of CMMS, IoT gadgets, and smart eyewear proves indispensable in propelling productivity levels and quality outcomes when effectively maintaining operational assets.
By integrating these innovative tools, your maintenance team will be well-equipped for current efficiency and future adaptability.
Source: EDAG
Implement Customized PM Checklists
The introduction of PM checklists has transformed maintenance operations. Maintenance managers can use a CMMS system, like WorkTrek, to create customized preventive maintenance checklists with detailed instructions.
These checklists assist operators in navigating through legal mandates and procedural steps, reducing mistakes while elevating safety standards.
Preventive maintenance checklists are vital for maintaining consistency in maintenance tasks. They offer detailed, step-by-step instructions, health and safety guidelines, control measure checkpoints, and visual aids to help technicians execute procedures precisely.
Source: WorkTrek
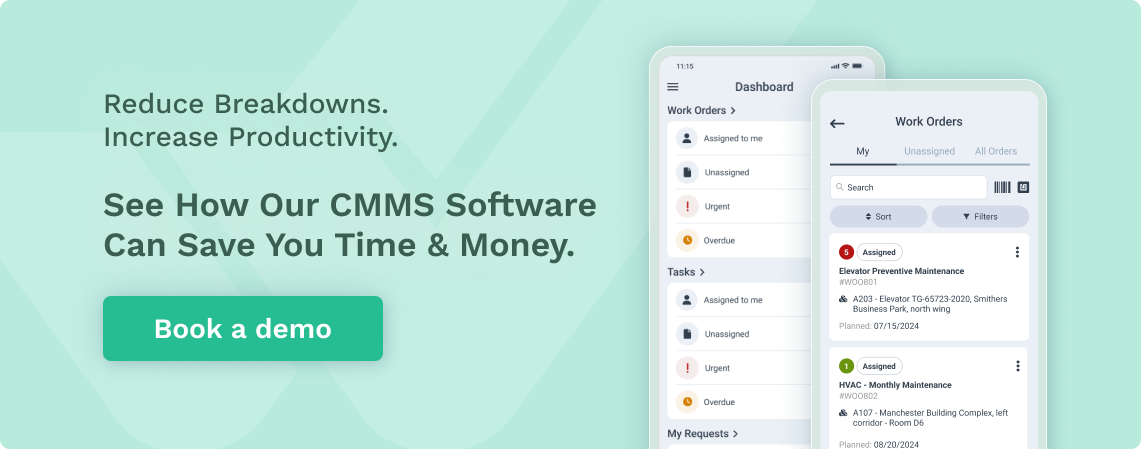
Live Tracking
Moreover, integrating case status tracking within these tools guarantees that tasks are monitored.
Maintenance checklists are designed with safety considerations in mind. They are equipped with intelligent offline modes so that technicians can carry out their duties even when network connectivity is compromised or absent altogether, thereby ensuring continuous operation of maintenance activities without any interruptions.
Integrating digital checklists into routine practices significantly enhances the accuracy and efficiency of executing maintenance tasks and overall operational security.
This technological strategy ensures compliance with all critical checkpoints, substantially diminishing the likelihood of equipment failures leading to unexpected halts in production or service delivery (unplanned downtime).
Enhancing Preventive Maintenance with Real-Time Data
Data acquisition in real-time is essential for executing effective preventive maintenance operations. IoT sensors facilitate monitoring equipment conditions, giving maintenance managers a detailed view of all equipment.
Such measures contribute considerably to prolonging the service life span of the machinery.
Access to archived production data plays can help maintenance technicians perform preventive maintenance. This type of analysis of historical information can help organizations identify and discern patterns, enabling maintenance teams to improve overall maintenance procedures.
Source: Estuary
Preventive Maintenance
Preventive maintenance can help organizations reduce student and expensive interruptions.
By anticipating potential equipment failures early enough, businesses can organize their resources and schedule maintenance to reduce production disruptions.
By anticipating potential equipment failures early enough, businesses can organize their schedule around necessary maintenance, minimizing disturbances in ongoing production processes.
Incorporating real-time data into routine preventive maintenance practices enables swift responses to emerging issues, reducing unplanned downtime and significantly enhancing system performance.
This proactive approach strengthens safety measures and increases productivity while lowering maintenance-related costs.
Source: WorkTrek
Training Your Maintenance Team on New Technologies
Training your team in emerging technologies can improve the success of any digital transformation initiative.
An additional approach is promoting cross-training. By doing so, you empower your maintenance teams with the capability to handle intricate software systems and cooperate effectively across different departments.
Customized training modules catering to individual career ambitions should be part of structured educational plans, providing each member with the skills necessary for professional advancement.
Knowledge Sharing
Establishing knowledge-sharing practices like mentoring encourages informal learning within a supportive environment and increases overall efficiency among team members.
A cross-training matrix can reveal areas where expertise is lacking within the group, guiding developmental efforts appropriately.
Employing varied instructional techniques such as simulations or role-play exercises reinforces abilities by allowing workers to hone their skills without real-world consequences.
Source: Helpjuice
Feedback
Ongoing reviews and updates based on strategic insights from employee feedback are fundamental in continuously enhancing operational performance through education programs.
Investing in thorough training regimens equips your maintenance staff to use innovative technologies adeptly, ensuring they meaningfully contribute to refining digital strategies related to upkeep activities.
Integrating CMMS
As you undertake digital transformation, you must link maintenance systems with established infrastructures.
Ensuring that Computerized Maintenance Management Systems (CMMS) can seamlessly interact with existing data systems is key to maintaining a consistent flow of digital information. This integration enhances collaboration between departments and boosts overall operational efficiency.
Connect with ERP and MES Systems
Integrating CMMS with other systems, such as Enterprise Resource Planning (ERP), accounting software, and Manufacturing Execution Systems (MES), enhances operational productivity through task automation and simplification.
Leveraging a cloud-based approach for incorporating CMMS may streamline this process while ensuring these management solutions stay updated.
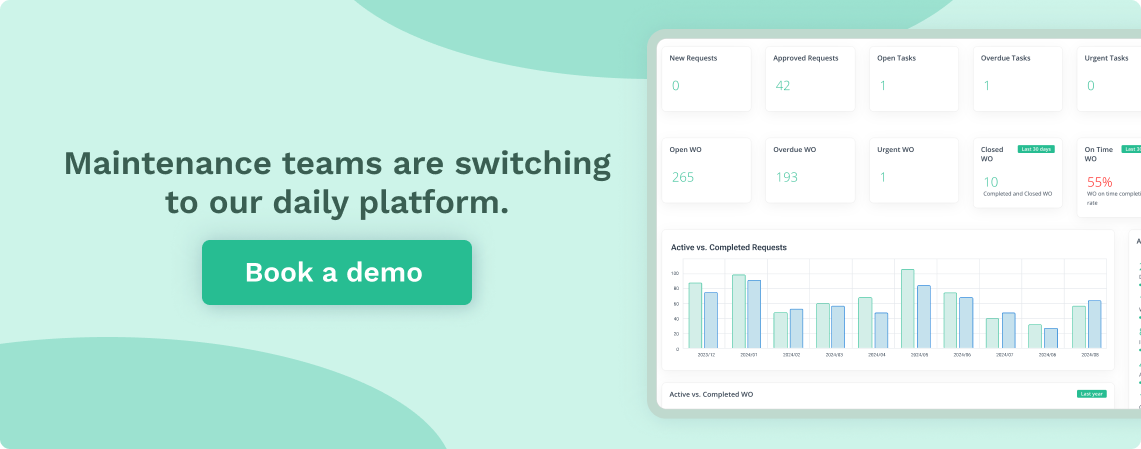
Setting distinct goals when merging CMMS into business operations helps align efforts with overarching organizational objectives. This can lead to a more strategic allocation of resources.
Source: L2L
Continuous Assessment
Regular assessments of data accuracy uphold the quality of information within integrated systems while preventing redundancies during this fusion stage.
Implementing advanced dashboards within Enterprise Asset Management or CMMS provides robust visualization tools that support informed decision-making based upon real-time maintenance insights.
Real-Time Monitoring
Finally, integrating digitized checklists into automated systems allows for real-time monitoring of ongoing maintenance tasks and their outcomes.
This approach streamlines processes, encourages continuous communication among components, and enhances overall efficiency in maintaining system health.
Source: WorkTrek
Monitoring and Analyzing Maintenance Performance
Monitoring and analyzing maintenance performance can optimize equipment operation and boost efficiency. Integrating CMMS with other systems can enhance reporting capabilities, making tracking Key Performance Indicators (KPIs) easier.
These reports offer valuable insights into maintenance activities, helping pinpoint areas needing improvement.
A Connected Worker platform aids in tracking job completion by digitally storing completed job information for management insights. Monitoring work order cycle time, which measures the duration from initiation to completion, provides valuable insights into maintenance efficiency.
Key Performance Indicators (KPIs)
Key performance metrics such as operating hours, equipment availability, and task completion rates are essential for making data-driven decisions to enhance maintenance performance. Analyzing these metrics helps organizations identify trends and patterns, optimize maintenance operations, and improve overall quality.
Regular monitoring and analysis ensure efficient equipment operation and improve maintenance operations’ overall safety and reliability. This data-driven approach supports continuous improvement and helps organizations achieve their maintenance goals.
Free Demo and Trial
A free demo of digital maintenance solutions lets users experience the software’s features and understand how it can enhance their maintenance operations. Experiencing the software through a demo provides insights into its practical application and benefits.
A demo allows users to ask questions and address any concerns regarding implementing digital maintenance solutions. This hands-on experience can help users understand how to integrate digital solutions effectively into their maintenance practices.
By experiencing the software firsthand, potential customers can make informed decisions about adopting these technologies.
Source: WorkTrek
Summary
Implementing digital maintenance procedures offers numerous benefits, including enhanced effectiveness, reduced human error, and improved safety protocols. By adopting these digital solutions, organizations can overcome the constraints of traditional maintenance methods, resulting in more efficient and effective execution of maintenance tasks.
Choosing the appropriate tools—including CMMS (Computerized Maintenance Management Systems), IoT devices, and smart glasses—is essential for organizations as they are key to improving productivity and quality in maintenance operations.
Using digitized checklists and comprehensive step-by-step instructions increases precision and ensures that every maintenance task is performed methodically and according to safety standards.
For preventive maintenance strategies to succeed, they must integrate real-time data capture capabilities, enabling continuous monitoring and analysis of system performance.
Offering comprehensive training programs to equip your team with the necessary skills, alongside smoothly integrating new technological advancements into existing infrastructures, ensures your organization is ready for a successful digital transformation journey.