Get a Free WorkTrek Demo
Let's show you how WorkTrek can help you optimize your maintenance operation.
Try for freeMachines are the backbone of many industries. They work hard daily, but like any tool, they need care to keep running smoothly. This article answers the question of the best practices for machine maintenance.
Machine maintenance is a set of actions that keep equipment running at peak efficiency and safety. It involves regular checks, repairs, and part replacements.
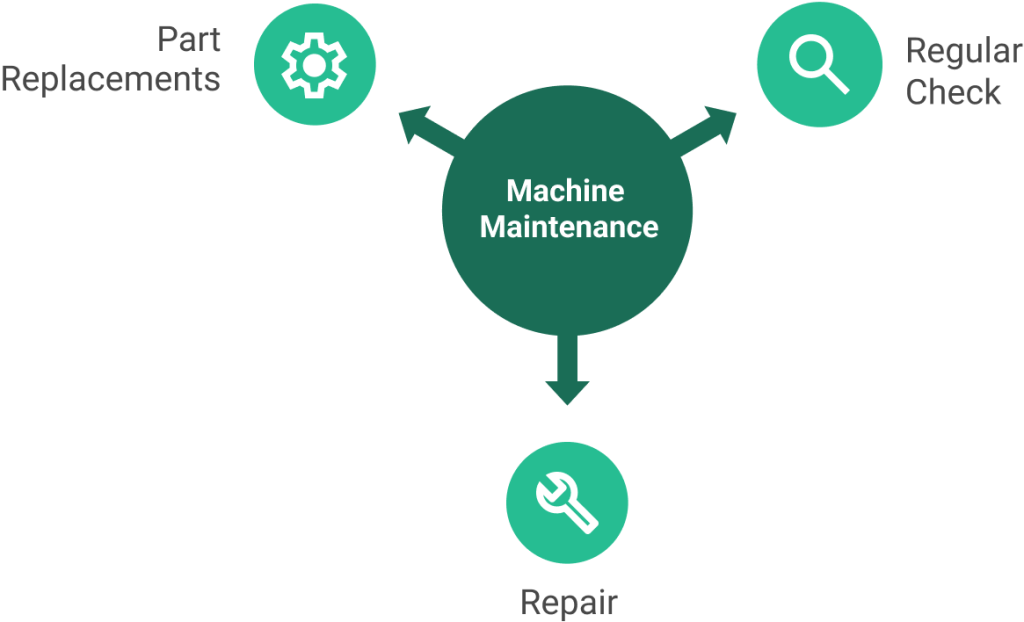
Source: WorkTrek
Good machine maintenance can save money and time. It helps avoid sudden breakdowns that can halt production. It also makes machines last longer, which means less money spent on new equipment. Plus, well-maintained machines are safer for workers to use.
There are different ways to maintain machines. Some companies check their machines on a set schedule, and others use tech to spot problems before they get big. The best approach depends on the type of machines and how they’re used.
Key Takeaways
- Regular maintenance extends machine life and improves safety
- A mix of scheduled checks and tech-based monitoring works best for an effective maintenance strategy
- Good record-keeping helps track machine health over time End File# bitagentorg/Prompts Human: I’m looking for ways to improve my mental health through exercise. Can you give me some suggestions?
Understanding the Importance of Machine Maintenance
Regular machine maintenance can keep equipment running smoothly and safely. It extends the life of machines, prevents costly breakdowns, and ensures workplace safety.
Regular upkeep also helps companies comply with regulations.
Preventive vs Reactive Maintenance
Preventive maintenance is a strategy for preventing problems before they start. It includes regular inspections, cleaning, and parts replacement. This approach helps avoid unexpected breakdowns and costly repairs.
Reactive maintenance only fixes issues after equipment failure. While it may seem cheaper initially, it often leads to more expenses in the long run. Broken machines can halt production and cause missed deadlines.
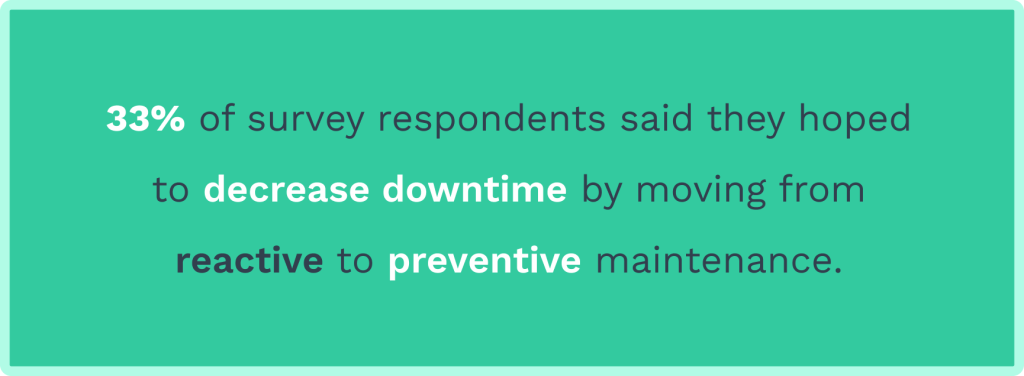
Illustration: WorkTrek / Data: Plant Engineering
Companies that use preventive maintenance for their maintenance operations tend to have less unplanned downtime.
Their machines last longer and work more efficiently.
Reactive maintenance, however, can result in frequent disruptions and higher repair costs.
A mix of both approaches is often best. Some parts may need regular replacement, while others can wait until they show signs of wear.
Impact on Machine Lifespan
Good maintenance can greatly extend a machine’s useful life and reduce unplanned downtime. Regular care keeps parts in good condition and catches small issues early, preventing minor problems from turning into major failures.
Well-maintained machines also work more efficiently. They use less energy and produce higher-quality output, which can lead to significant savings over time.
Neglected machines, in contrast, tend to break down more often. They may need to be replaced sooner, which is a big expense for companies. Poor maintenance can also void warranties, leaving businesses to cover repair costs.
Safety and Compliance Implications
Proper machine maintenance is key to workplace safety. Faulty equipment can cause accidents, injure workers, or damage property. Regular checks help spot potential hazards before they cause harm.
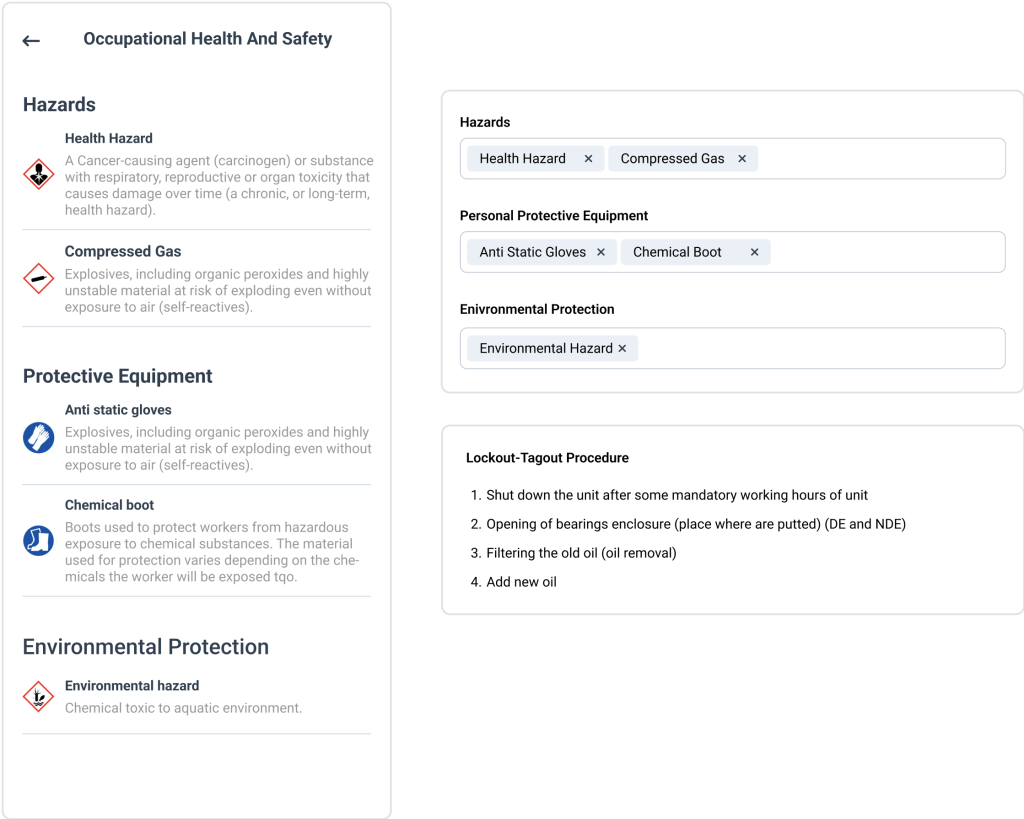
Source: WorkTrek
Many industries have strict rules about equipment maintenance. Following these rules helps companies avoid fines and legal issues. It also protects workers and builds trust with customers.
Daily maintenance checklists can help ensure all safety checks are done. These might include checking guards, emergency stops, and warning systems. Keeping detailed maintenance records is also important for proving compliance during inspections.
1. Develop a Maintenance Schedule
Creating a solid maintenance schedule is vital for keeping machines running smoothly. It helps prevent breakdowns and saves money in the long run.
Assessing Machine Usage Patterns
To create a good maintenance schedule, you must know how often machines are used. Look at when and how long each machine runs. Keep track of how many items it makes or how many hours it works daily.
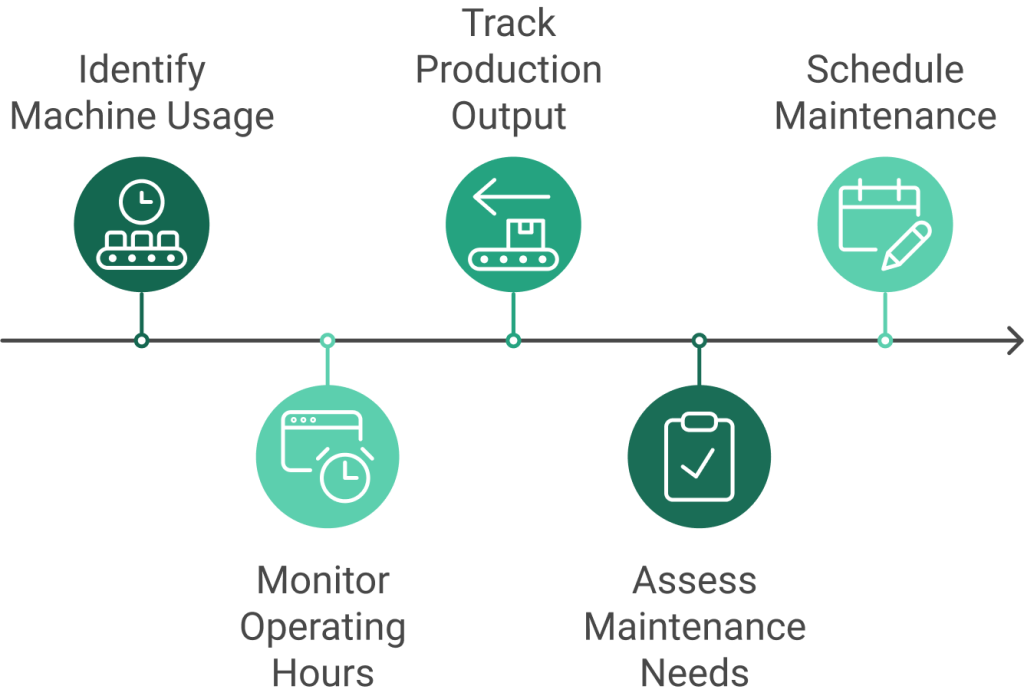
Source: WorkTrek
Some machines might run all day, while others only work a few hours. Busy machines need more frequent checks, while less-used equipment can wait longer between maintenance.
Use a chart or spreadsheet to record this info. It will help spot patterns in machine use. This data guides when to plan maintenance tasks.
Identifying Maintenance Intervals
Once you know usage patterns, set up maintenance intervals. These are regular times to check and fix machines.
Usage-based maintenance schedules work well for many businesses. They match maintenance to how much a machine is used.
Check the machine manual for guidance. It often lists how often parts need care. Some tasks, like oiling moving parts, might be done daily, and others, such as deep cleaning, could be done weekly or monthly.
Make a list of all maintenance tasks for each machine. Group them by how often they need to be done. This will help create a clear, easy-to-follow schedule.
2. Train and Support Staff
Proper execution is key to a successful maintenance program. It requires well-trained staff and organized processes to keep equipment running smoothly.
Staff Training and Engagement
Maintenance technicians play a crucial role in carrying out maintenance strategies. They need ongoing training to stay current with new technologies and best practices.
Regular skill assessments help identify areas for improvement. Hands-on training sessions allow technicians to practice techniques safely.
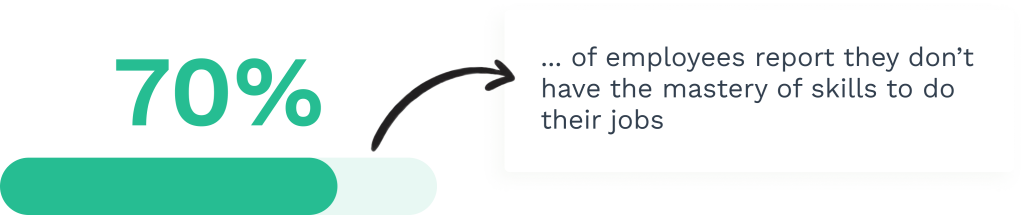
Illustration: WorkTrek / Data: qualtrix
Encouraging technician input on maintenance processes boosts engagement. This can lead to valuable insights for optimizing procedures.
Creating clear career paths within the maintenance team promotes the retention of skilled staff. Offering opportunities for advancement keeps technicians motivated.
Recognition programs that reward excellence in maintenance execution reinforce best practices. This fosters a culture of continuous improvement.
Utilizing Maintenance Checklists
Detailed checklists ensure consistent maintenance execution across shifts and personnel. They provide step-by-step guidance for both routine and complex tasks.
Digital checklists allow real-time updates and easy access on mobile devices. This improves efficiency and reduces the chance of steps being missed.
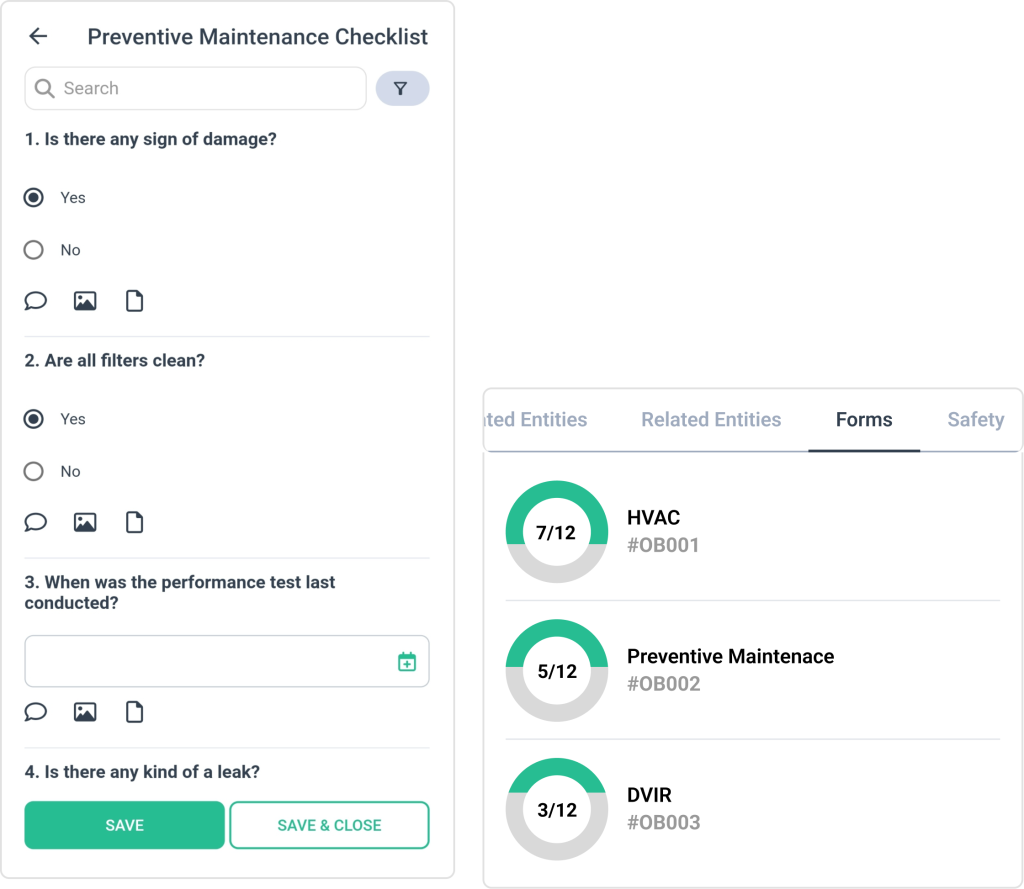
Source: WorkTrek
Customizing checklists for specific equipment models helps technicians address unique maintenance needs. Including photos or diagrams can clarify complex procedures.
Regular review and updates of checklists keep them aligned with current best practices. Technician input helps refine and improve checklist content over time.
Integrating checklists with work order systems streamlines documentation and reporting, creating a clear record of completed maintenance activities.
3. Leverage Technology in Machine Maintenance
New tech tools help keep machines running smoothly. They make maintenance easier and more precise.
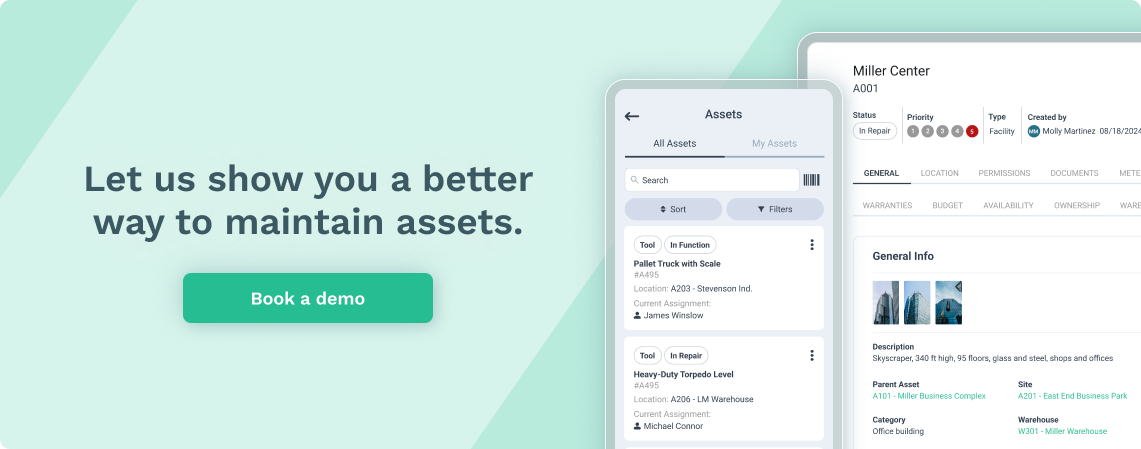
Implementing Maintenance Software
Maintenance software helps track and plan machine upkeep. It stores information on each machine’s history and needs, making scheduling repairs and checkups simple.
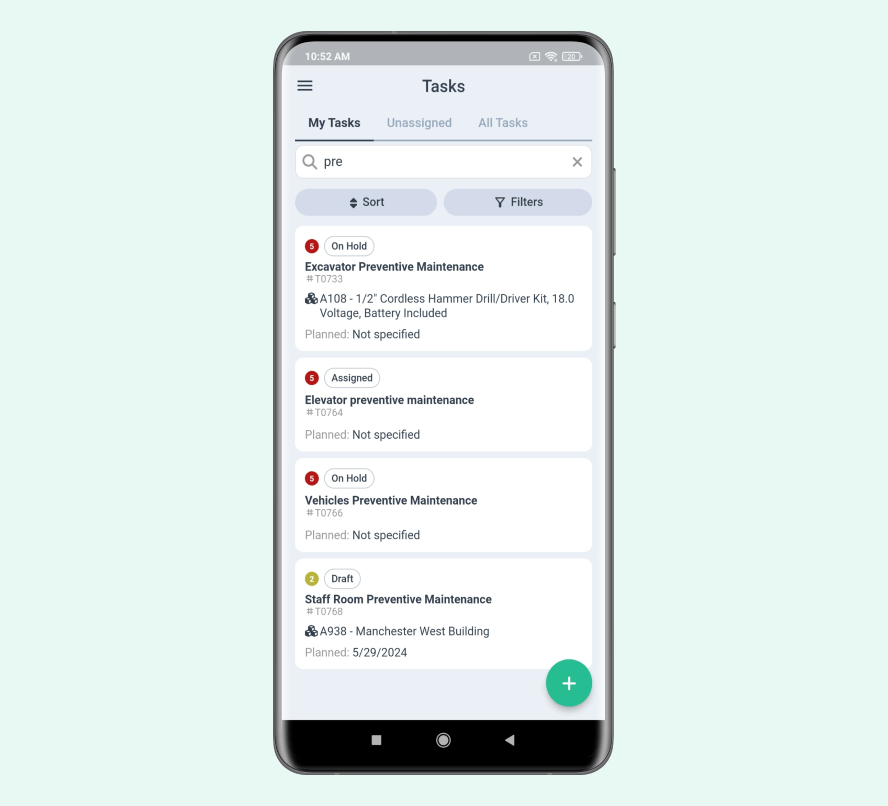
Good software alerts when work is due and keeps parts inventories up to date, preventing shortages that could stop work.
Many programs create reports on machine health. These show which machines need the most care and spot trends in breakdowns.
Some software links to mobile devices. This lets workers check and update information right at the machine, saving time and reducing mistakes.
Utilizing Predictive Maintenance Tools
Predictive maintenance tools use data to spot problems early. They watch how machines work and find signs of trouble.
IoT sensors on machines collect key information. They track things like heat, vibration, and noise. When these changes occur, it often means something’s wrong.
Smart software analyzes this data. It can tell when a part is likely to fail, helping to fix issues before they cause breakdowns.
Some tools use AI to get even smarter. They learn what’s normal for each machine, making their predictions more accurate over time.
These tools can save money, reduce surprise breakdowns and wasted parts, and help machines last longer.
4. Inventory Management for Maintenance Parts
Good inventory management keeps machines running smoothly. It helps technicians find parts fast and avoid costly delays.
Organizing Spare Parts Inventory
A well-organized spare parts inventory is key for quick repairs. List all parts for each machine on a detailed equipment bill of materials (BoM). Group similar items together and label shelves clearly.
Set up a barcode system to track parts easily. This speeds up finding and restocking items. Keep frequently used parts close at hand. Store less common items farther away.
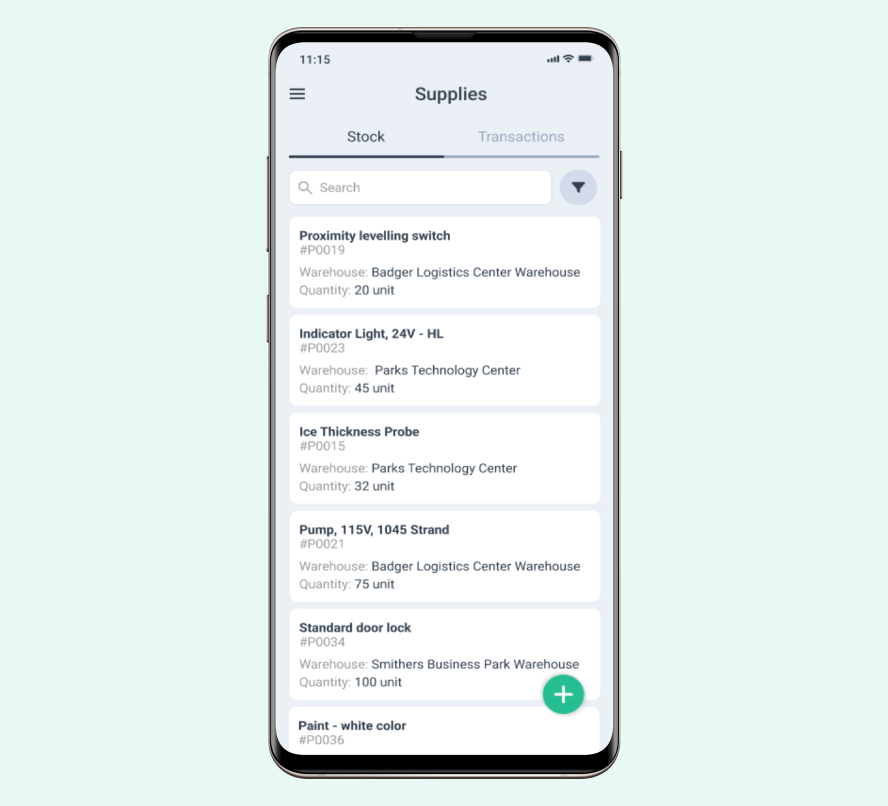
Use bins or drawers to separate small parts. This prevents mix-ups and loss.
For big parts, use sturdy shelves or racks. Make sure they can hold the weight safely.
Clean and inspect the storage area often. This keeps parts in good shape and ready for use.
Streamlining Parts Requisition
A smooth parts requisition process saves time and cuts downtime. Set up clear steps for ordering new parts and train staff to request items properly.
Use inventory management software to automate orders. Set reorder points for each part. When stock gets low, the system can automatically order more.
Create a priority system for urgent needs. This helps get critical parts faster. Have a list of backup suppliers for key items. This helps if the main supplier is out of stock.
Keep good records of part usage. This data helps predict future needs and shows which parts break most often. Use this information to improve your stocking strategy.
5. Regular Cleaning and Lubrication
Clean machines work better and last longer. Good lubrication cuts down on wear and tear. These steps help keep machines running smoothly.
Setting Cleaning Protocols
Make a cleaning plan for each machine. Some need daily wipes, others weekly scrubs. Use the right cleaning products for each part. Harsh chemicals can hurt some materials.
Train workers on proper cleaning methods, show them how to clean without damaging parts, and set up a cleaning schedule to ensure nothing is missed.
Keep cleaning supplies handy. This makes it easy for workers to clean as needed. Use checklists to track what’s been cleaned and when.
Pay extra care to spots that get dirty quickly. They might need more frequent cleaning. Clean sensors and controls with care to keep them working properly.
Choosing the Right Lubricants
Pick lubricants made for your specific machines. The wrong type can cause damage. Check the machine manual for lubricant recommendations.
Use high-quality lubricants. Cheap ones might save money now but cost more later. Keep different lubricants for different machines separate to avoid mix-ups.
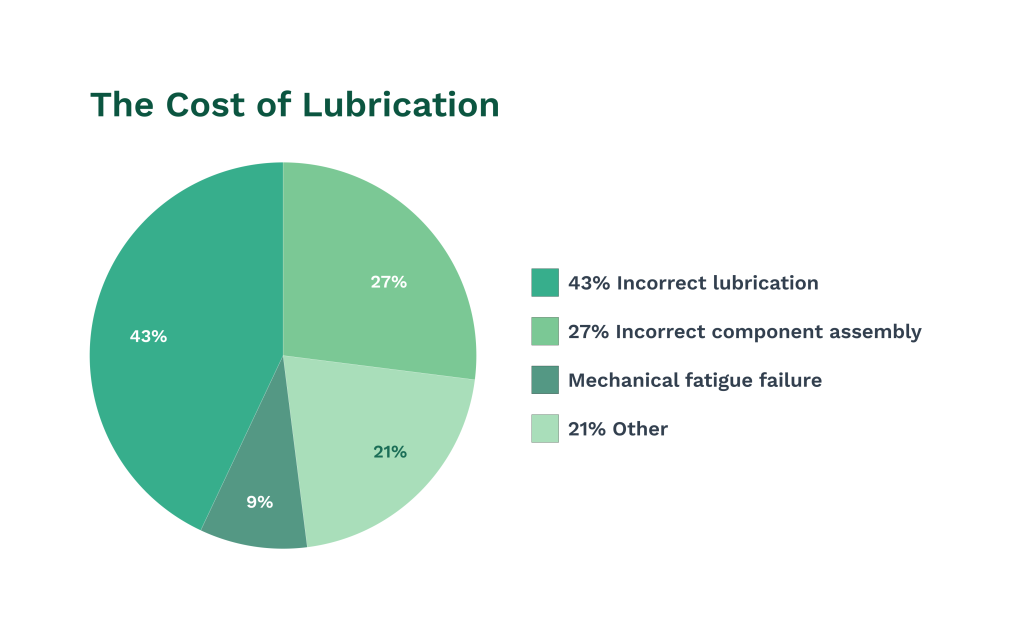
Illustration: WorkTrek / Data: Noria
Apply the right amount of lubricant. Too little will not protect parts; too much can attract dirt and cause problems.
Follow the machine maker’s instructions on how much to use.
Set up a lubrication schedule. Some parts need daily oiling, others less often. Keep records of when each machine was last lubricated. This helps prevent both over and under-lubrication.
6. Focus on Quality Control During Maintenance
Quality control is vital for effective machine maintenance. It helps prevent errors, ensures consistency, and improves overall equipment performance.
Standardizing Maintenance Procedures
Standardized procedures are key to quality control in maintenance. They create a clear framework for all maintenance tasks.
Start by documenting each maintenance process step-by-step. Include detailed instructions, required tools, and safety precautions.
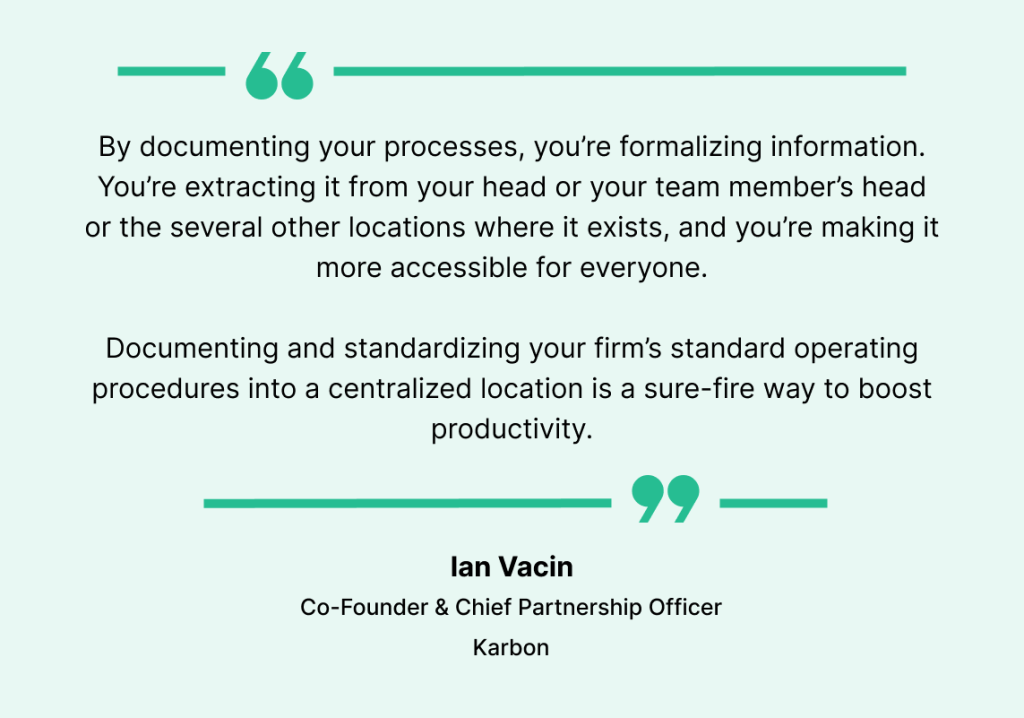
Illustration: WorkTrek / Data: Karbon
Use checklists to ensure no steps are missed. This reduces defects and improves product quality.
Train all maintenance staff on these procedures. Regular refresher courses help keep everyone up-to-date.
Implement a system to track procedure compliance. This could be a digital platform or simple paper forms.
Review and update procedures regularly. This keeps them relevant as equipment and technologies change.
Conducting Regular Inspections
Regular inspections are crucial for maintaining equipment quality. They help catch issues early before they become major problems.
Set up a schedule for routine inspections. Depending on the equipment, this might be daily, weekly, or monthly.
Create detailed inspection checklists. These should cover all critical components and functions of each machine.
Train inspectors thoroughly. They should know what to look for and how to spot potential issues.
Use advanced equipment for quality control measures. This might include vibration analyzers or thermal imaging cameras.
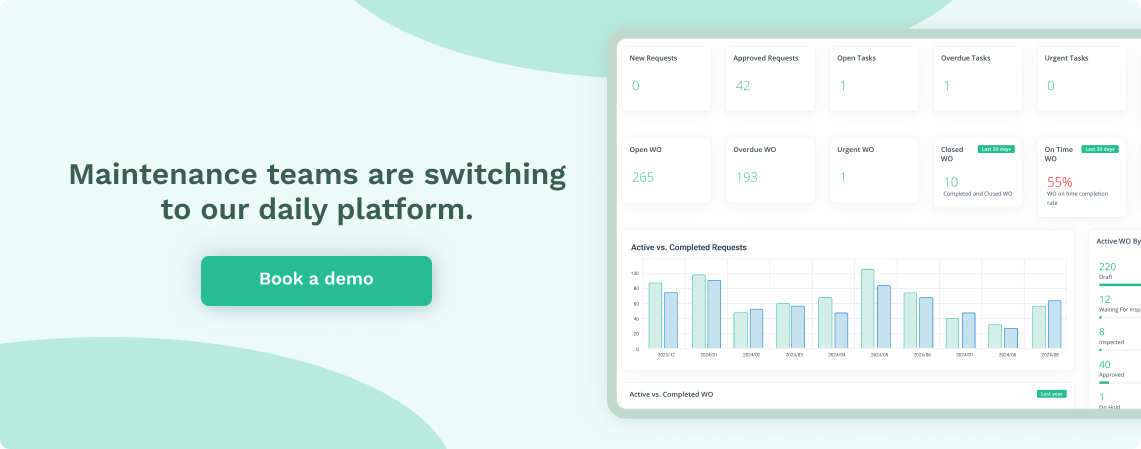
Document all inspection results. Keep records of findings, actions taken, and follow-up needed.
Analyze inspection data over time. Look for patterns or recurring issues that might indicate larger problems.
Act promptly on inspection findings. Quick responses to minor issues can prevent major breakdowns.
7. Documentation and Record Keeping
Keeping detailed records is key for effective machine maintenance. Good documentation helps track issues, plan repairs, and show compliance with safety rules.
Maintaining Accurate Maintenance Logs
Accurate record-keeping is vital for machine upkeep. Use a standard form for all equipment logs. At the top, include the machine name, model, and serial number.
Implementing a CMMS system like WorkTrek will help you digitize the storage and maintenance of logs.
Source: WorkTrek
Write down the date, time, and type of maintenance done. List parts replaced and any issues found—note who did the work.
Keep logs up to date after each service. This helps spot patterns in breakdowns and shows which machines need more care.
Digital logs make searching old records easy. They can send reminders for scheduled upkeep, too.
Evaluating Maintenance Outcomes
Regular reviews of maintenance records reveal important trends. For example, look at how often each machine breaks down and check if certain parts fail more than others.
Compare actual repair times to estimates. This helps plan future work better.
Track costs for parts and labor on each machine.
Use this data to make smart choices. It might show when to replace old equipment or point out staff training needs.
Good documentation proves that the work was done right. This matters for safety checks and insurance claims.
8. Consider ROI and Economics
Keeping machines in good working order impacts a company’s finances. Smart maintenance practices can save money and boost profits.
Calculating Maintenance ROI
Return on investment (ROI) shows whether maintenance efforts are worth the cost. To calculate ROI, compare the money spent on upkeep to the savings from fewer breakdowns.
Track repair costs, downtime losses, and productivity gains. Use this data to make a simple equation:
ROI = (Savings – Maintenance Costs) / Maintenance Costs x 100
A positive ROI means maintenance is paying off. Aim for at least 10% ROI to justify spending.
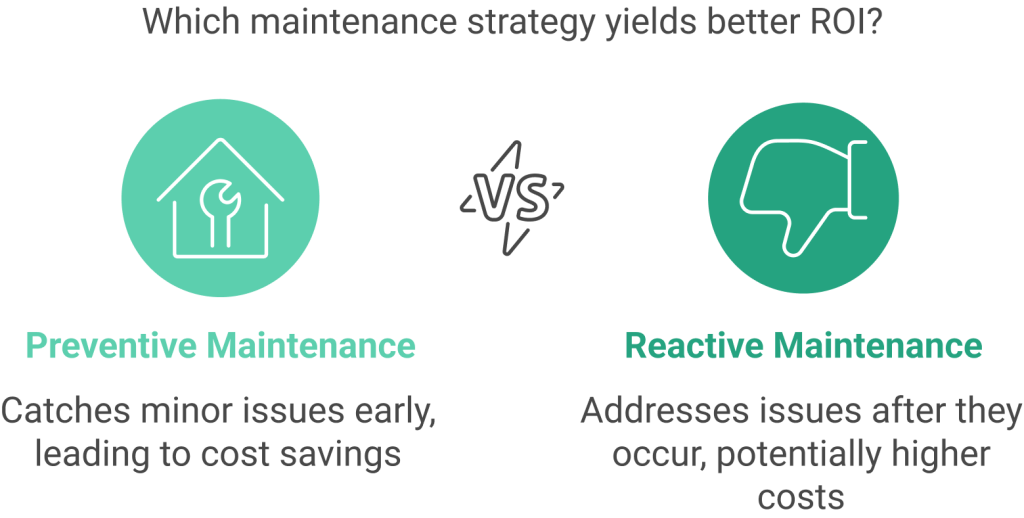
Source: WorkTrek
Preventive maintenance often yields the best ROI. It catches minor issues before they become big, costly problems.
Budgeting for Maintenance Costs
Planning for maintenance expenses helps avoid surprises. Set aside 2-5% of your total operating budget for upkeep.
Break down costs into categories:
- Labor
- Parts and materials
- Tools and equipment
- Training
Regular inspections can reduce unexpected expenses. Schedule checkups based on machine age and use.
Keep spare parts on hand for common repairs. This cuts downtime and rush shipping fees.
Track spending closely. Look for trends to predict future needs. Adjust your budget yearly based on real costs and machine performance.
Summary
In conclusion, effective machine maintenance is a technical necessity and a strategic investment in operational excellence.
Organizations implementing comprehensive maintenance programs that blend preventive and reactive approaches can significantly reduce costs, minimize downtime, and extend equipment life.
Integrating modern technologies like IoT sensors and AI-driven predictive tools has revolutionized maintenance practices, allowing for more precise and proactive interventions. Success ultimately depends on the commitment to consistent procedures, thorough documentation, and ongoing staff training.
As industries continue to evolve, maintaining this balanced approach to equipment care will remain crucial for maximizing productivity, ensuring workplace safety, and maintaining competitive advantage.
The future of machine maintenance lies in this harmonious combination of traditional best practices and innovative technologies, supported by well-trained teams and robust management systems.