Get a Free WorkTrek Demo
Let's show you how WorkTrek can help you optimize your maintenance operation.
Try for freeThis article will cover the concept of the planned maintenance system (PMS). This is a strategic method for the systematic scheduling and execution of regular maintenance tasks to boost equipment reliability and extend asset longevity.
Implementing a maintenance plan can reduce downtime and maintenance costs, shifting from reactive to preventive maintenance. Such systems are designed to minimize operational downtime, simplify maintenance activity, and reduce maintenance costs.
We’ll examine the components, advantages, and steps necessary for integrating a PMS within your organization, emphasizing its importance in proactive facility management.
A Planned Maintenance System (PMS) centralizes and schedules maintenance tasks to ensure efficient and proactive maintenance management, reducing the risk of unscheduled repairs and operational disruptions.
PMS offers substantial benefits, including reduced maintenance costs, prolonged equipment lifespan, and enhanced workplace safety by preventing unexpected equipment failures and minimizing urgent corrective measures.
Source: WorkTrek
Understanding Planned Maintenance Systems
Every successful organization or manufacturing facility relies on a robust Planned Maintenance (PM) system, which acts as a stabilizing force amidst operations’ complexities.
This PM’s primary purpose is to identify what needs to be done and how to do it and to bring all those activities together in one place.
The Benefits of Planned Maintenance System
A robust planned maintenance (PM) system is the foundation of every efficiently functioning facility. It acts as a reliable, proactive mechanism despite operations’ unpredictable demands.
The primary purpose of this PM strategy is to determine ‘what’ maintenance tasks are required and ‘how’ they should be carried out, unifying them within a cohesive and comprehensive structure. This helps improve asset management and reduce unplanned equipment downtime.
Maintenance Planning
This coordinated approach to maintenance work and scheduled maintenance tasks—which can include procedures such as condition-based monitoring and regular meter readings—creates an environment where maintenance outcomes are dependable and foreseeable.
Implementing planned preventive maintenance can improve equipment maintenance, give visibility to the condition of all the resources, and clearly define maintenance tasks.
This method guarantees that resources are efficiently allocated, timelines are strictly followed, and unexpected downtime is reduced.
Reviewing different examples of planned maintenance underscores the importance of creating a practical PM strategy based on routine inspections and strategic interventions grounded in a comprehensive preventive approach.
Key Features of a Planned Maintenance System
Planned maintenance software technology is a guiding system for maintenance teams, synchronizing each element to work seamlessly.
It provides essential features like precise scheduling, detailed inventory management, and comprehensive reporting, guiding maintenance teams through the complexities of their tasks.
This type of software is distinguished by its capacity to:
- Forecast future requirements for upkeep
- Initiate actions at opportune moments
- Supervise inventory with precision
- Administer work orders with both effectiveness and efficiency.
Maintenance software dedicated to planned activities empowers teams by furnishing them with advanced tools that predict upcoming needs, facilitate prompt interventions when necessary, ensure tight control over parts and supplies inventories, and seamlessly manage various work assignments.
Types of Planned Maintenance
Exploring the intricate realm of PMS, a variety of maintenance strategies emerge.
Preventive maintenance can help reduce potential breakdowns.
The approach involves more than simple tasks like oil changes or fan belt replacements. It’s about ensuring that operations continue seamlessly without interruption.
Conversely, planned unscheduled maintenance adopts an approach where less critical assets are monitored until they show subtle signs of wear or concern rather than being routinely serviced.
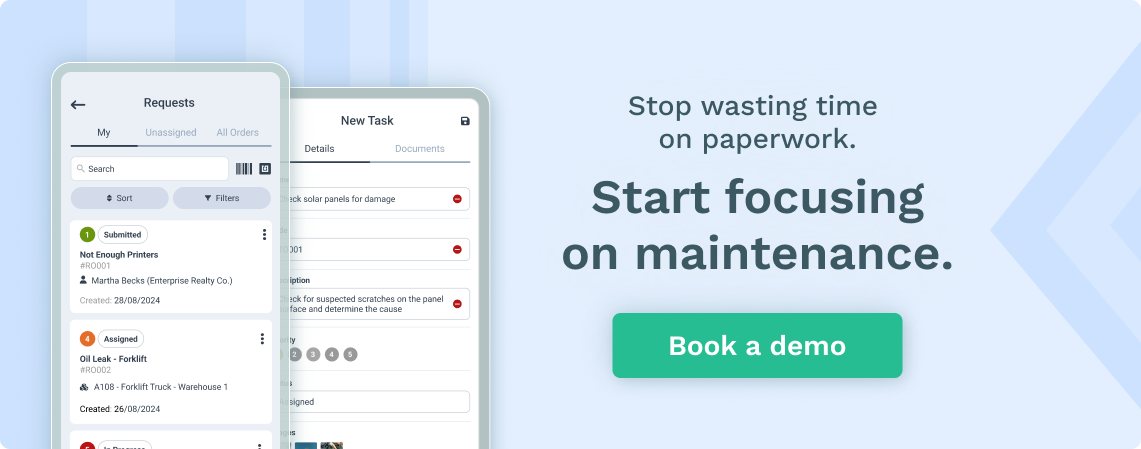
This method accepts measured risks, enables prompt action in response to sudden equipment malfunctions, and keeps necessary resources available for reactive maintenance.
Benefits of Implementing a Planned Maintenance System
Incorporating a Planned Maintenance System (PMS) into an organization offers many advantages.
Key among these are the significant cost savings, reduced unplanned downtime, better asset maintenance, enhanced durability, and improved safety that make adopting such a proactive maintenance system highly attractive.
This approach leads to notable financial efficiencies and smoother operations by preemptively tackling maintenance concerns and curtailing unexpected repairs.
Implementing planned maintenance involves a systematic approach to setting up and using planned maintenance software, emphasizing the importance of technology and organization in planning maintenance activities.
Reduced Maintenance Costs
From a financial standpoint, investing in preventive maintenance can reap significant benefits. By identifying and addressing minor issues early on, companies can circumvent the steep expenses associated with reactive fixes.
Planned maintenance usually costs just a tiny portion of what emergency repairs would, highlighting the economic intelligence behind proactive maintenance planning.
Increased Equipment Lifespan
Regular maintenance of equipment ensures years of dependable service in return. A correctly implemented Preventive Maintenance System (PMS) guarantees the preservation and optimal condition of machinery, thereby delaying any early replacement and maximizing asset life.
Enhanced Workplace Safety
Adhering to a planned maintenance program signifies a dedication to ensuring safety. Such a maintenance strategy diminishes the chances of unforeseen equipment breakdowns, thereby fostering a workspace that prioritizes the well-being of all personnel and strives for maximum risk reduction every working day.
Steps to Implement a Planned Maintenance System
Adopting a Property Management System (PMS) necessitates implementing planned maintenance with a detailed and comprehensive plan.
This journey starts with an in-depth evaluation of asset significance, progresses to carefully crafting a maintenance schedule, and ends with comprehensive training for maintenance teams.
Conduct a Criticality Analysis
Criticality analysis is the pivotal point at which it is decided which assets are of paramount importance and require preferential focus.
This vital examination forms the foundation for a successful Preventive Maintenance Strategy (PMS), guaranteeing that critical pieces of equipment always receive due attention rather than being left to random fate.
Develop a Maintenance Schedule
Develop a planned maintenance schedule customized for the organization’s requirements using the information gathered from a criticality analysis.
By integrating manufacturer guidelines with the needs of daily operations, this schedule evolves into an effective instrument that guarantees all maintenance activities are performed at optimal times.
Train Your Maintenance Team
The final phase requires equipping the maintenance team with the essential training and resources to carry out the Planned Maintenance System (PMS) effectively. Thorough education about innovative procedures and technologies is crucial to facilitate a smooth and triumphant shift toward a planned maintenance strategy.
Using Planned Maintenance Software
Planned maintenance software, such as WorkTrek CMMS, has revolutionized maintenance management during the digital transformation. This cutting-edge tool streamlines the coordination, implementation, and tracking of all maintenance tasks, heralding a new period of enhanced operational effectiveness.
Source: WorkTrek
Choosing the Right Maintenance Software
Choosing the right maintenance software is not a universal solution, as it must be tailored to meet an organization’s requirements. These can vary based on organizational scale, sector of operation, and particular needs.
Essential factors like growth potential, ease of merging with existing systems, and the level of support vendors provide should be considered when deciding on such software.
Integrating CMMS with Existing Systems
Incorporating a Computerized Maintenance Management System (CMMS) into current systems is crucial for establishing an integrated maintenance environment. By allowing smooth data exchange and cooperative workflows, such integration significantly improves the efficiency of maintenance management operations.
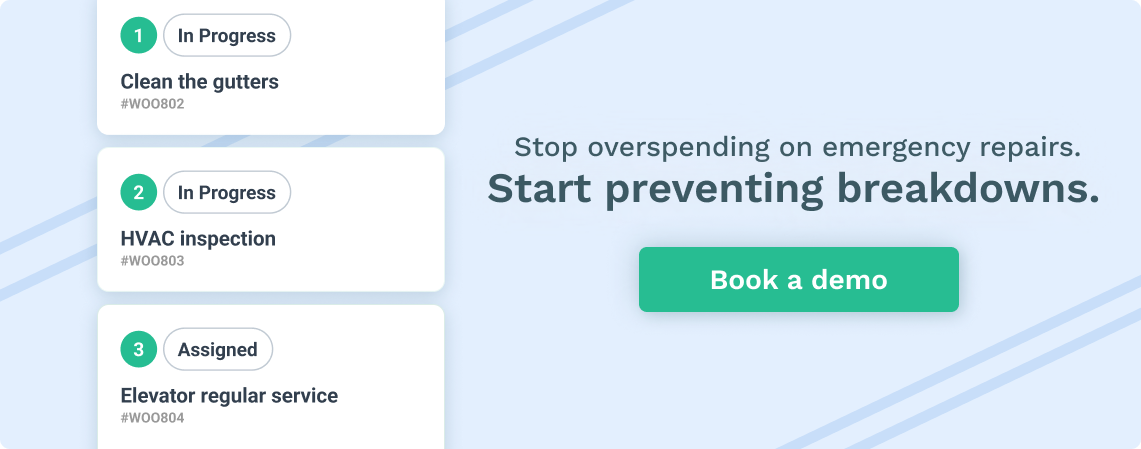
Tracking and Analyzing Maintenance Data
The robustness of the process hinges on the underlying data. To traverse the maintenance terrain successfully, organizations must:
- Monitor and scrutinize maintenance-related data
- Leverage such data to discern emerging patterns
- Execute decisions based on this insight, which consistently refine their approaches to maintenance.
Common Challenges and Solutions in Planned Maintenance
Every effort towards planned maintenance excellence can face obstacles, including labor shortages and miscommunication. Despite these challenges, solutions exist for every problem encountered along the way.
A successful Planned Maintenance System (PMS) hinges on foreseeing and countering these difficulties with thoughtful strategic planning.
Managing Scheduling Conflicts
Significant hurdles often arise in maintenance planning due to scheduling conflicts. Overcoming these challenges necessitates proficient communication, utilization of resource calendars, and an adaptable approach to shift patterns to guarantee that maintenance tasks are carried out seamlessly.
Ensuring Compliance with Safety Standards
Adhering to safety protocols is mandatory in a PMS. Implementing a compliance management system that monitors safety rules and confirms the provision of essential personal protective equipment for maintenance staff represents the solution.
By implementing a CMMS you can easily include safety information related to each work order.
Balancing Preventive and Corrective Maintenance
Striking the right balance between preventive and corrective maintenance is akin to walking a tightrope, where any miscalculation can lead to inefficiency and higher expenses.
The primary strategy involves ranking maintenance tasks by urgency and relevance according to criticality assessments and performance analytics, aiming for a symphony of proactive strategies complemented by essential reactive responses.
Source: WorkTrek
Case Studies: Successful Implementation of Planned Maintenance Systems
Case studies, such as Raytheon’s adoption of lean manufacturing principles and BMW’s successes in achieving remarkable uptime, serve to illuminate the way for organizations contemplating the implementation of a PMS. These real-world success narratives provide insights into how a properly implemented Performance Management System can revolutionize businesses across diverse sectors.
Summary
Implementing a Planned Maintenance System goes beyond a simple strategic move. It is a driving force for lasting operational excellence.
By integrating preventive maintenance principles and utilizing advanced technologies, organizations can realize cost savings, extend the lifespan of their equipment, and enhance workplace safety. This journey demands commitment, but the ultimate aim is to achieve optimized, reliable, and secure operations.