Get a Free WorkTrek Demo
Let's show you how WorkTrek can help you optimize your maintenance operation.
Try for freeA preventive maintenance checklist is a structured list of tasks and inspections designed to be performed on equipment or assets to prevent potential issues, maintain optimal performance, and extend operational lifespan.
It typically includes scheduled maintenance activities such as lubrication, cleaning, visual inspections, component replacements, and other necessary actions to identify and address potential problems before they escalate into costly breakdowns or failures.
The checklist ensures that maintenance tasks are systematically carried out according to a predetermined schedule, reducing the likelihood of unexpected downtime and maximizing equipment reliability and efficiency.
If you’re a facility manager, you’ve probably heard a variation of the phrase, “If it ain’t broke, don’t fix it.” This mentality may work in the short term, but ongoing reactive maintenance may fail due to a lack of consistency, and proactive repairs cost thousands of euros each year.
Unplanned equipment failures are stressful and time-consuming for facility teams to fix. If your team is still taking a reactive approach to maintenance, it’s time to make a change. A solid preventive maintenance program is critical to keeping equipment safe and functioning correctly.
What Is Preventive Maintenance?
Preventive maintenance is a systematic approach to building operations designed to predict and prevent catastrophic equipment failures before they occur. To achieve this, facility personnel routinely inspect, maintain, and repair equipment to ensure that it performs as expected by the manufacturer.
As a general rule, it is better to prevent problems than to react to them. A preventive maintenance plan can help maintenance managers better predict costs and improve key performance indicators.
Preventive maintenance reduces the likelihood of unexpected issues by optimizing equipment performance. The following list outlines a few ways maintenance teams can stay on top of preventive maintenance in their departments:
- Schedule and perform regular equipment inspections.
- Regularly clean buildings, grounds, and property.
- Lubricate moving parts to reduce wear.
- Amplified controls for optimal performance and energy efficiency.
- Repair and replace any defective piece of equipment.
- Develop clear PM Checklists.
- Define maintenance processes
This article will introduce you to the ultimate equipment preventive maintenance checklist that will ensure your equipment’s seamless and efficient operation.
Importance of Preventive Maintenance
Preventive maintenance (PM) involves regular, planned maintenance tasks designed to prevent equipment failure before it occurs. Unlike reactive maintenance, which addresses problems after they arise, preventive maintenance proactively addresses potential issues, ensuring equipment operates smoothly and efficiently.
Benefits of Preventive Maintenance
- Reduced Equipment Downtime: Routine maintenance tasks help identify and fix issues before they escalate into significant problems, reducing unplanned equipment downtime.
- Extended Equipment Lifespan: Regular inspections and maintenance activities can significantly extend the lifespan of equipment, ensuring it remains operational for more extended periods.
- Cost Savings: Preventive maintenance reduces the need for costly repairs and replacements, ultimately saving the organization money.
- Improved Safety: Routine checks and maintenance of safety-critical systems, such as fire alarm systems and carbon monoxide detectors, ensure the safety of personnel and infrastructure.
- Enhanced Efficiency: Well-maintained equipment operates more efficiently, improving productivity and reducing energy consumption.
Source: WorkTrek
Preventive Maintenance Checklist
Equipment/Asset Name: [Insert Equipment/Asset Name]
Date of Inspection: [Insert Date]
Inspector: [Insert Name]
Item Description: [Describe the equipment or asset being inspected]
Preventive Maintenance Checklist Tasks:
- Visual Inspection:
- Check for any signs of abnormal wear or damage.
- Inspect for leaks, cracks, or corrosion.
- Verify proper alignment and positioning.
- Lubrication:
- Lubricate moving parts as per the manufacturer’s recommendations.
- Ensure proper grease or oil levels.
- Replace lubricants if necessary.
- Cleaning:
- Remove any debris, dirt, or buildup.
- Clean filters, vents, and cooling systems.
- Ensure equipment surfaces are free from dust and grime.
- Functional Checks:
- Test equipment functionality according to its operational specifications.
- Verify safety features such as emergency stops and alarms.
- Conduct performance tests if applicable.
- Electrical Components:
- Inspect electrical connections for signs of wear or damage.
- Check for loose connections and tighten if necessary.
- Test electrical systems for proper functioning.
- Fluid Levels:
- Check fluid levels such as oil, coolant, hydraulic fluid, etc.
- Top up fluids as needed.
- Inspect for any leaks or abnormalities in fluid condition.
- Parts Replacement:
- Replace worn or damaged components identified during inspection.
- Follow the manufacturer’s guidelines for part replacement intervals.
- Keep a record of replaced parts for future reference.
- Calibration:
- Verify equipment calibration if applicable.
- Perform calibration adjustments as needed.
- Ensure accuracy and precision of measurements.
- Documentation:
- Record inspection findings, maintenance tasks performed, and any issues identified.
- Maintain a log of maintenance activities for tracking and reference purposes.
Source: WorkTrek
Utilizing CMMS Software for Preventive Maintenance Checklists
Implementing Computerized Maintenance Management Systems (CMMS) software can simplify and automate the creation and management of preventive maintenance checklists. This digital tool allows maintenance managers to automate the scheduling of regular inspections and maintenance tasks, ensuring that nothing falls through the cracks.
With CMMS, you can automate the creation of preventive maintenance checklists, generate task lists for specific equipment and assign them to technicians, set up recurring work orders, and track the completion of each item on your checklist.
This level of organization and automation increases equipment reliability and streamlines the workflow, allowing technicians to focus on their work without worrying about administrative tasks.
Moreover, CMMS software provides a centralized database for all maintenance records, making it easy to access historical data and track the frequency of maintenance activities. This data can be invaluable for refining your preventive maintenance checklists over time, as it reveals patterns and trends that may necessitate adjustments in maintenance frequency or procedures.
Additionally, CMMS can alert managers to upcoming maintenance tasks, help prioritize work based on criticality, and ensure that the necessary parts and tools are available when needed, thus further enhancing the efficiency and effectiveness of preventive maintenance programs.
What Are The Different Types Of Preventive Maintenance?
There are seven types of preventive maintenance:
- Preventive Maintenance
- Predictive Maintenance
- Corrective Maintenance
- Condition Based Maintenance
- Planned Maintenance
- Reactive or Emergency Maintenance
- Deferred Maintenance
Preventive Maintenance
Preventive maintenance is carried out at predetermined intervals or according to prescribed criteria to reduce the likelihood of failure or the degradation of the functioning of an item. This strategy is based on performing maintenance at scheduled intervals, regardless of whether the equipment has shown signs of deterioration. The goal is to prevent unexpected breakdowns and extend the lifespan of the machinery.
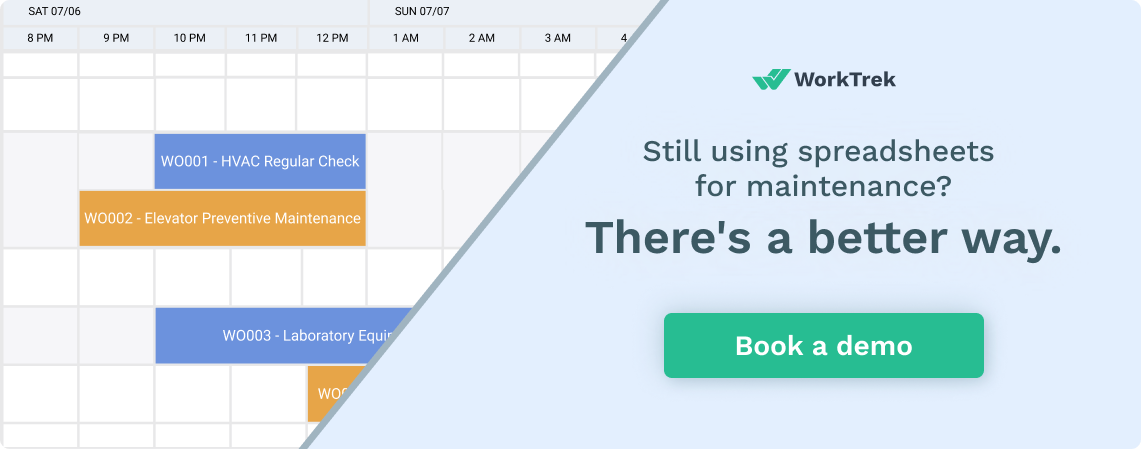
Benefits:
- Reduces the likelihood of unexpected breakdowns.
- Extends equipment lifespan.
- Enhances operational efficiency by minimizing downtime.
- Helps in planning and budgeting for maintenance activities.
Predictive Maintenance
Predictive maintenance is a more sophisticated approach that relies on condition-monitoring equipment and techniques to assess real-time machinery performance. By analyzing sensor data and statistical methods, maintenance can be more accurately scheduled to address issues before they fail, thus reducing unnecessary maintenance tasks and costs.
Benefits:
- Minimizes unplanned downtime by predicting failures.
- Reduces maintenance costs by addressing issues before they escalate.
- Improves equipment performance and reliability.
- Enables better planning and resource allocation.
Corrective Maintenance
Corrective maintenance is performed to rectify identified faults, and restore the equipment to an acceptable condition. Unlike reactive maintenance, which occurs after a breakdown, corrective maintenance is often the result of inspections or monitoring that detect issues before they lead to failure.
Benefits:
- Addresses issues that were not anticipated, ensuring equipment can be repaired promptly.
- It can be more cost-effective for non-critical equipment with lower failure impact.
- It helps identify underlying issues that might not have been apparent during routine checks.
Planned Maintenance
Planned maintenance is carried out at predetermined intervals or according to prescribed criteria to reduce the likelihood of failure or the degradation of the functioning of an item. This strategy is based on performing maintenance at scheduled intervals, regardless of whether the equipment has shown signs of deterioration. The goal is to prevent unexpected breakdowns and extend the lifespan of the machinery.
Benefits:
- Allows for efficient use of maintenance resources.
- Minimizes disruption to operations by scheduling maintenance during non-peak times.
- Ensures systematic and comprehensive equipment care.
- Helps in long-term maintenance planning and budgeting.
Emergency Maintenance
Reactive or emergency maintenance, sometimes called breakdown maintenance, is the most basic form. It involves repairs only after a machine has failed or broken down. While this approach may seem cost-effective in the short term, it can lead to increased downtime and higher repair costs due to the unpredictability of equipment failures. Reducing the volume of emergency maintenance is best to improve equipment reliability and reduce maintenance costs.
Benefits:
- Addresses critical failures promptly to minimize operational impact.
- Enhances safety by quickly mitigating hazardous conditions.
- Reduces the duration of unplanned downtime.
- Essential for maintaining business continuity during emergencies.
Deferred Maintenance
Deferred maintenance refers to postponing maintenance activities on buildings, equipment, and machinery due to budget constraints, prioritization, or resource allocation decisions. While this may offer short-term financial relief, it can increase long-term costs, safety risks, and potential system failures.
Benefits:
- Allows for prioritization of critical maintenance tasks when resources are limited.
- It can be used as a temporary measure to manage budget constraints.
- Provides flexibility in maintenance scheduling.
Condition-based maintenance
Condition-based maintenance is similar to predictive maintenance but specifically focuses on the equipment’s physical condition. It involves monitoring specific variables, such as vibration, temperature, or lubrication properties, to determine when maintenance should be performed. This approach ensures that maintenance is only done when warranted by the equipment’s condition, thus avoiding unnecessary interventions.
Benefits:
- Optimizes maintenance activities by focusing on actual equipment conditions.
- Reduces unnecessary maintenance tasks and associated costs.
- Enhances equipment availability and reliability.
- Increases the accuracy of maintenance interventions.
Source: WorkTrek
What Are The Four Key Preventive Maintenance Actions?
Preventive maintenance adopts the active maintenance method, which mainly includes four significant actions: inspection, detection, correction, and prevention. Let’s examine each concept in more detail to see how it can be the foundation of a successful preventive maintenance program and help the maintenance team.
Inspections
Inspections are necessary for preventive maintenance and help the organization in two ways. First, facility inspections ensure that equipment is safe to use. Regular inspections help avoid workplace accidents and provide the company with more liability protection. The second is to inspect and protect assets regularly. Check to make sure the equipment is operating as intended by the manufacturer.
Detection
Running in a “run-to-fail” fashion ultimately incurs facility service costs, which is why many facility managers opt for a preventive maintenance approach. Predictive maintenance allows facility managers to identify problems early, which are relatively easy and inexpensive to fix.
Correction
Preventive maintenance encourages facility managers to maintain equipment proactively and fix problems before they occur. When a problem (or potential problem) is identified, facility managers take action to resolve it before it escalates or disrupts operations quickly.
Prevention
Facility managers can combine inspection records and maintenance alerts to learn from past mistakes and resolve recurring equipment issues. Preventing equipment downtime reduces stress and increases facility team productivity. When equipment is performed according to inspections, personnel can focus on proactive (rather than reactive) maintenance tasks.
What Are The Benefits Of Preventive Maintenance?
The most obvious benefit of implementing preventive maintenance is to get ahead of problems before equipment failure. Some of the benefits include:
- Preventive maintenance reduces downtime and business shutdowns due to unexpected equipment failures.
- Using preventive maintenance checklists can improve overall efficiency
- Preventive maintenance will increase equipment life, saving you money in the long run.
- Preventive maintenance ensures that all equipment and employees work only during scheduled hours, eliminating the need for overtime pay due to unplanned machinery breakdowns, etc.
- Preventive maintenance will significantly reduce safety risks for employees and customers, reducing the risk of costly lawsuits and workers’ compensation.
- Preventive maintenance helps reduce the energy consumption of your assets and equipment through high levels of operational efficiency, which will lower your utility bills.
- Preventive maintenance can help maintenance teams reduce urgent repairs
- Preventive maintenance can give maintenance technicians a well-defined maintenance strategy
These are just a few of the specific benefits of regular preventive maintenance. Preventive maintenance can reduce accidents and costly damage even if you own a small retail store or food stand and don’t work with heavy machinery or equipment.
What Are Repairs?
Repairs are actions taken to restore an asset to normal function. It’s about restoring a broken thing to its optimal working condition. The extent of repairs required depends on the nature of the equipment failure. There are two main types of errors:
Complete failure
This refers to an outage that causes the asset to become unusable. The asset cannot perform its function until someone takes care of it. For example, an engine failure can stall your car and make it undrivable until you take it to a mechanic. Equipment failure often results in unplanned downtime, which is often costly and requires urgent maintenance.
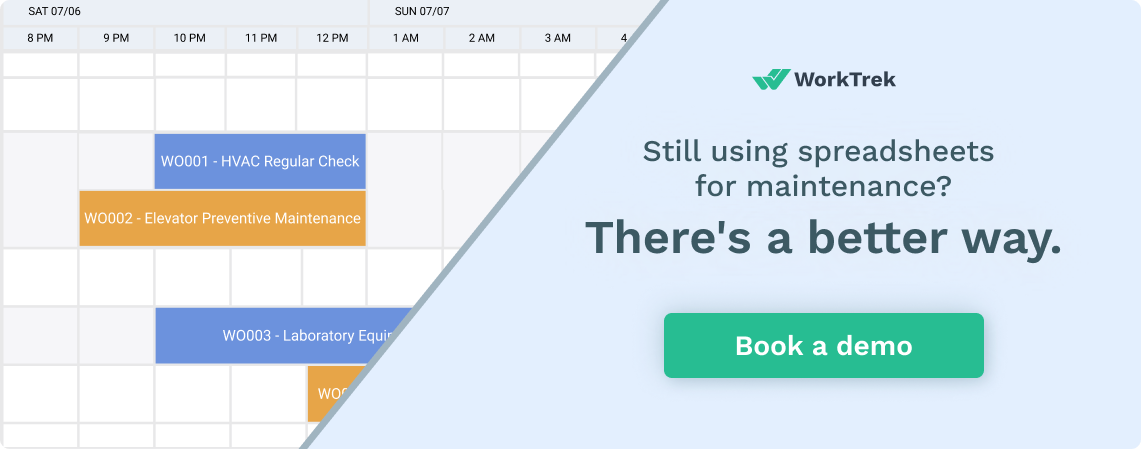
Partial failure
In this case, the asset works to some extent despite the error. You can still use the gear, but it’s either unsafe or extremely ineffective. For example, a driver might drive a vehicle with a dirty air filter. But he might notice that the air conditioner isn’t as cold as it used to be, or he might sneeze because of the poor air quality. Often, you want to fix partial failures as quickly as possible before they lead to complete failures at the wrong time.
Some repairs are more expensive than others. How much you spend on repairs depends on the root cause of the failure.
While failures are inevitable, most equipment failures are avoidable. This is where maintenance comes into play. Proactive maintenance can help you avoid major and expensive repairs.
Source: Huston Dynamic Service, Inc.
Conclusion
A comprehensive preventive maintenance program ensures equipment and assets’ longevity, efficiency, and reliability and reduces maintenance costs. Organizations can significantly reduce the risk of unexpected breakdowns, minimize production downtime, and improve key performance indicators by creating preventative maintenance checklists and following good preventive maintenance processes.
Following a structured preventive maintenance checklist, which includes regular inspections, condition monitoring, predictive maintenance techniques, and timely corrective actions, can also reduce costly repairs.
The benefits of preventive maintenance extend beyond just minimizing downtime; it also enhances overall operational efficiency, improves safety, lowers energy consumption, and ultimately leads to substantial cost savings in the long run.
By embracing a proactive approach to maintenance and leveraging tools like CMMS software, facility managers can streamline their maintenance workflows, make data-driven decisions, and foster a culture of continuous improvement within their organizations.
Frequently Asked Questions (FAQ)
What is a Preventive Maintenance Checklist?
A preventive maintenance checklist is a structured list of tasks and inspections designed to be regularly performed on equipment or assets. It includes scheduled maintenance activities like lubrication, cleaning, visual inspections, and component replacements to identify and address potential problems before they escalate into costly breakdowns or failures.
What are the Different Types of Preventive Maintenance?
The three main types of preventive maintenance are:
- Preventive Maintenance
- Predictive Maintenance
- Corrective Maintenance
- Condition Based Maintenance
- Planned Maintenance
- Reactive or Emergency Maintenance
- Deferred Maintenance
What are the Four Key Preventive Maintenance Actions?
The four critical preventive maintenance actions are:
- Inspections: Regularly inspecting equipment for safety and proper operation.
- Detection: Identifying problems early through predictive maintenance techniques.
- Correction: Proactively fix identified issues before they escalate.
- Prevention: Learning from past issues to prevent recurring equipment problems.
What are the Benefits of Preventive Maintenance?
Some key benefits of preventive maintenance include:
- Reduced downtime and business shutdowns due to unexpected failures
- Improved overall efficiency and equipment life
- Cost savings from avoiding expensive repairs and replacements
- Reduced safety risks and potential legal liabilities
- Lower energy consumption and utility costs
What is the Difference Between Repairs and Maintenance?
Repairs are actions taken to restore an asset to normal function after a failure. Maintenance, on the other hand, refers to proactive actions like inspections, adjustments, and replacements performed to prevent failures from happening in the first place. Proper maintenance can help avoid major and expensive repairs.