Get a Free WorkTrek Demo
Let's show you how WorkTrek can help you optimize your maintenance operation.
Try for freeThe Future of CMMS as we know it will continue to change and improve as more and more companies continually strive to achieve better resource allocation, greater customer satisfaction, optimized production, and improved safety performance.
Development Of Different Generations Of CMMS
CMMSs have been around since early computers. In the 1960s, the first generation of maintenance solutions used punched cards running on IBM mainframes. Earlier versions of the app were limited in terms of usage and the expertise required to execute basic work orders. The system has attracted large corporations and government organizations to manage its service operations.
Punched cards were replaced by computer terminals in the late 1960s. The development of mainframe computers made the solution available to many organizations, but it remained limited to large corporations and government organizations that could afford the tool.
After the introduction of minicomputers in the late 1970s, service management continued to evolve with advanced features that enabled medium and large industries to take advantage of CMMS. Technological advances in personal computers from the late 1980s to the early 2000s paved the way for the platform.
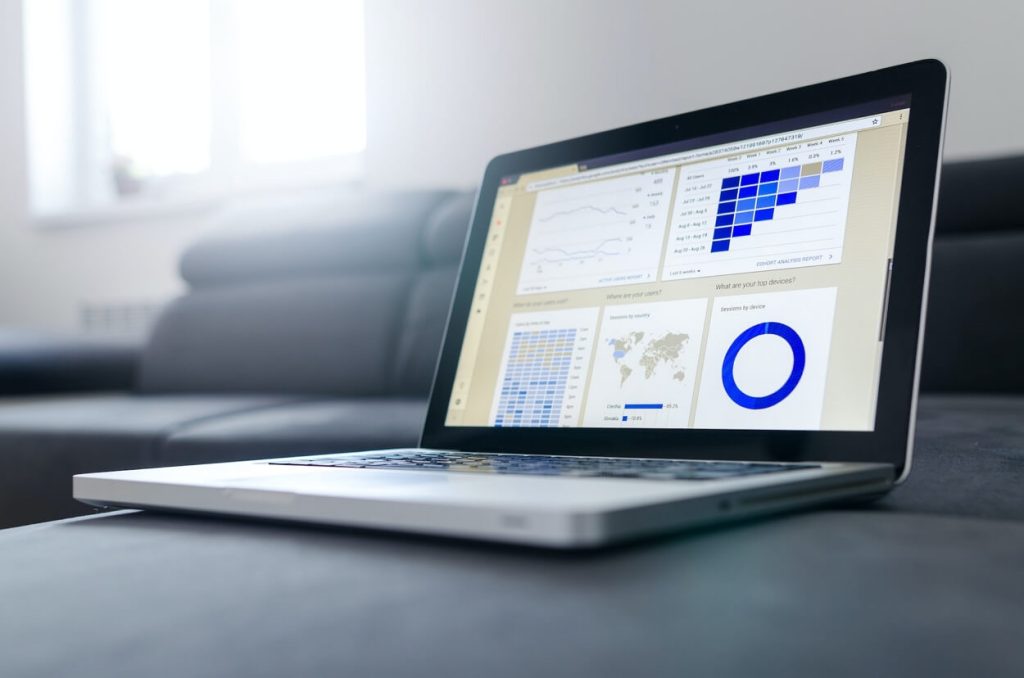
CMMS and Internet Access
The possibility to connect a PC to a local network expands the range of use of the tool’s functions. After the 1990s, and more precisely from 2000 onwards, we saw a huge growth in maintenance driven by the internet and the cloud. This is the story of how CMMS evolved and achieved its biggest breakthrough, which can be used anywhere in the world with Internet access.
This solution emerged through service operations in various industries and evolved from a buy or support model to a SaaS model. After the outbreak of the Fourth Industrial Revolution in 2010, computer networking capabilities emerged. With the advent of wireless and cellular technologies, cloud-based solutions are adopted. Here, the on-premises application model is replaced by a cloud-based model. With the development of Industry 4.0 technology, mobile service solutions have become common, and the Internet of Things and artificial intelligence have made important contributions. This makes it easier for users to remotely place work orders, track progress, and order parts.
The Evolution Of CMMS
The development of CMMS is relatively new, around 50 years ago.
From on-premises CMMS to cloud CMMS.
Initially, there was no wireless or cellular access, so the use of CMMS was limited to large punched card computers. For the most part, these early systems were only attractive to very large companies, given the cost of the equipment and the expertise required to operate them.
With the advent of computer networking capabilities, CMMSs have evolved. They are then available on the institutional network and can be accessed from a desktop computer. With the advent of wireless and mobile technology, the cloud-based CMMS format made its debut. Another new feature of the software is mobile access, allowing system users to remotely place work orders, order parts and track progress.
Finally, the introduction of predictive maintenance programming represents a quantum leap forward for facility management, allowing regular maintenance checks to be performed while equipment is still operating and with minimal disruption to the manufacturer’s production cycle. All of these developments make the latest CMMS releases more attractive to companies of all sizes and industries.
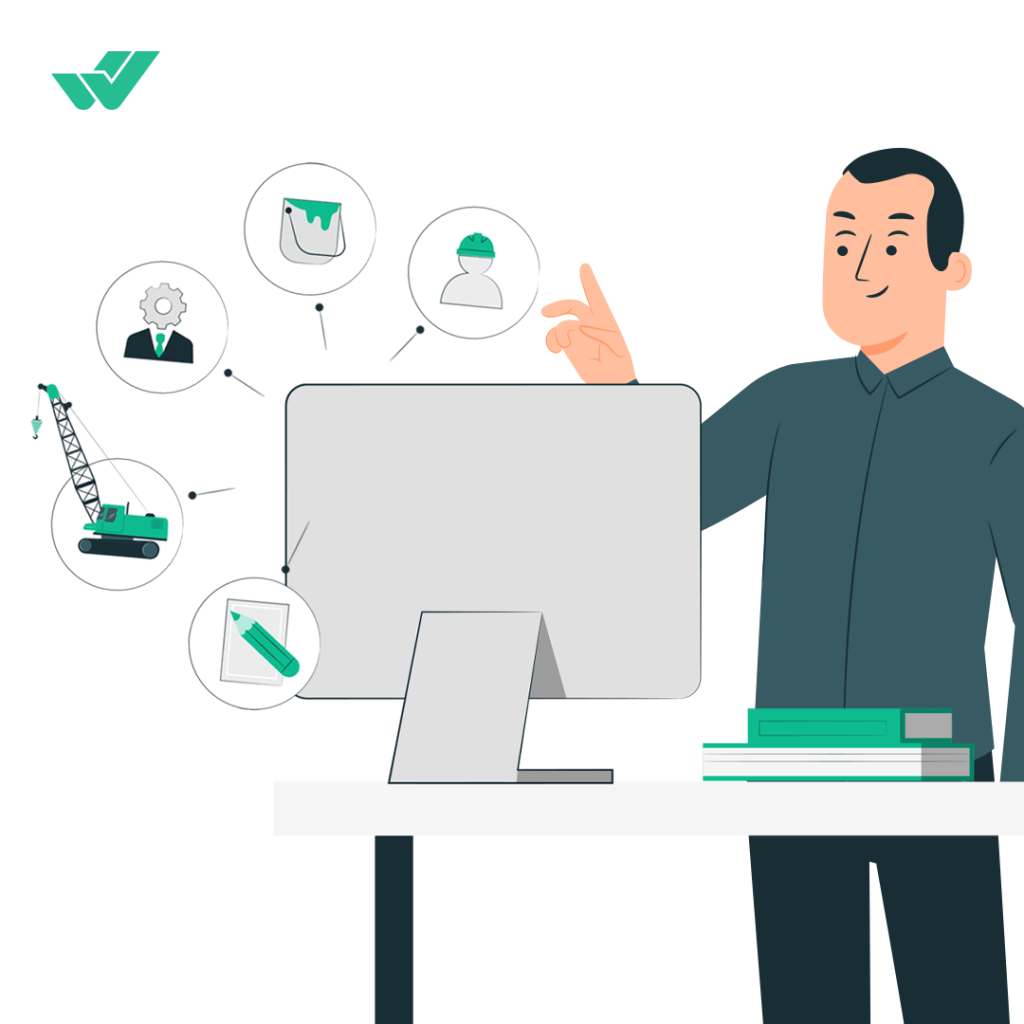
Maintenance management today.
Today’s maintenance management experience is very different from that of a spreadsheet user or earlier CMMS versions.
Automation. Once implemented, these systems perform all maintenance management tasks automatically and often require little more effort from the user than a click or touch of the equipment being used. Maintenance technicians no longer need to be burdened with paperwork as all labor and parts orders, job tracking, and other communications are done electronically.
Mobile access. Mobile access with camera and barcode scanning enables technicians to work from anywhere while saving time and reducing errors.
Customizability. Finally, one of the greatest benefits of today’s CMMS is that they adapt to the organization, rather than requiring the organization to adapt to the system. This means they can meet the unique needs of large and small businesses with varying numbers of assets, users, locations, and preventative maintenance needs. Most importantly, they are also able to adapt to the changing needs of the organization as it grows and restructures.
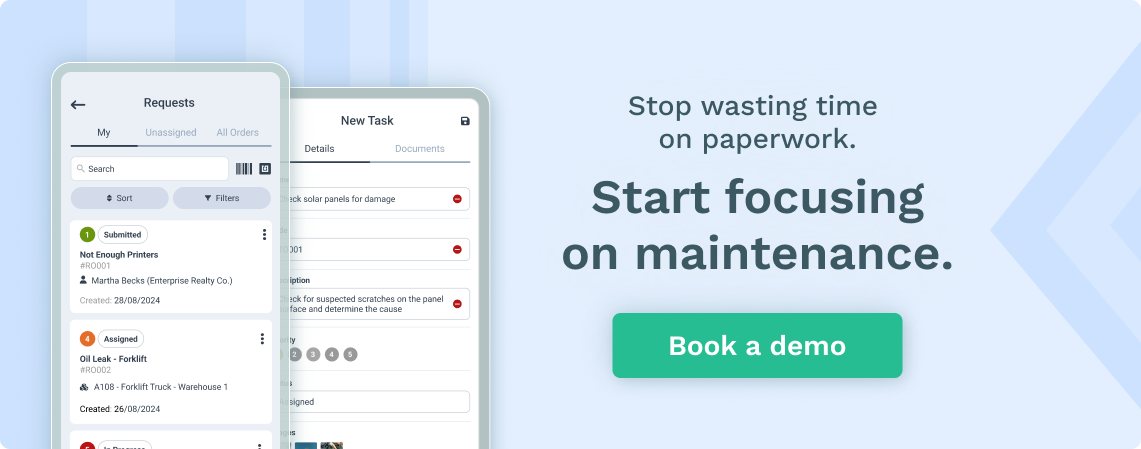
Changes in technology, the market, and the business environment have all led to the development of CMMS as the solution of choice for maintenance management. By comparing pre- and post-implementation approaches to maintenance management, one can see how these software systems have helped thousands of manufacturing companies keep up with tighter profit margins and growing economic and industrial demands.
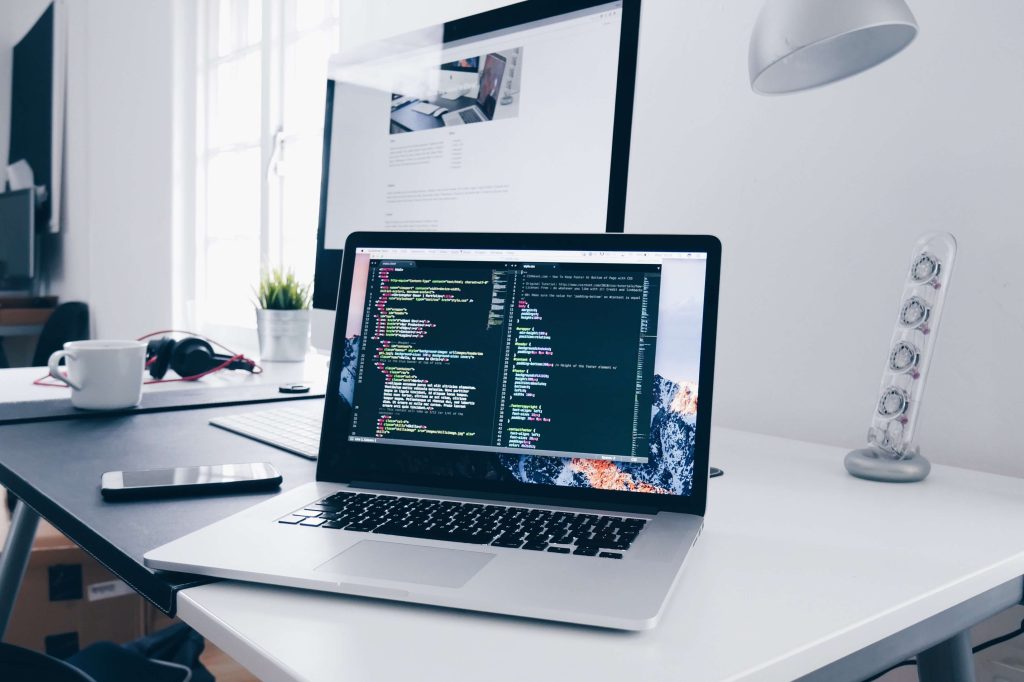
CMMS Top Trends And Predictions
The CMMS market is expected to grow at a compound annual growth rate (CAGR) of 9.1% from 2023 to 2033, reaching USD 42.15 billion. As CMMS software grows and becomes more widely used, predicting the future of CMMS industry trends can be challenging. However, we have identified some emerging trends that are likely to impact this market in the future of CMMS.
Gain better maintenance insights through big data
Almost every industry is leveraging big data to gain insight into its processes, predict problems before they occur, and then use that information to drive continuous improvement. From healthcare to aerospace, education, and manufacturing, these changes are happening primarily on Industrial Internet of Things (IIoT) platforms and wireless sensor networks.
We expect that within the next few decades, the maintenance process will completely shift from paper-based or manual management to real-time monitoring based on machine-provided information. The future of CMMS will be largely digitized and automated, with most of their decisions based on real-time machine data.
The overall result of this massive data analysis will be higher device reliability than ever before.
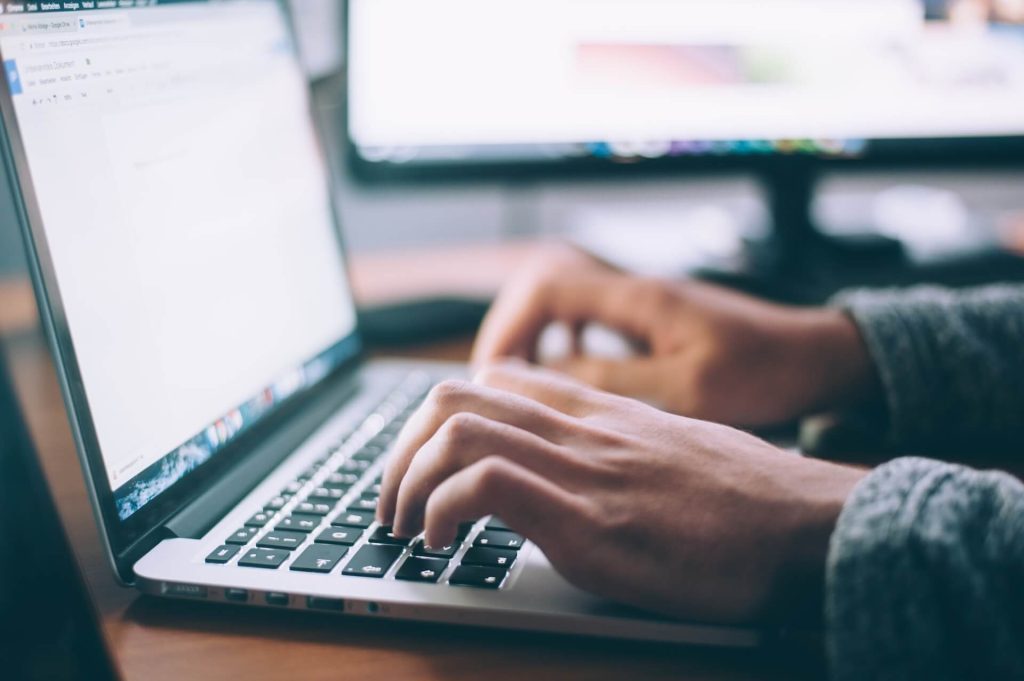
Cloud maintenance
The use of cloud computing solutions by businesses and individuals has increased significantly in recent years.
For maintenance professionals, the main benefit is that cloud-based maintenance support or maintenance-as-a-service offers comprehensive functionality accessible from anywhere in the world. The most popular of these tools are cloud-based computerized maintenance management systems (CMMS) because they offer customizable capabilities, can be deployed faster than on-premises CMMSs, and have traditionally provided more mobile, flexible, and customizable Enterprise Maintenance Solutions. Plus, it gives you all the benefits of a pay-as-you-go enterprise maintenance solution.
Prescriptive maintenance
Yes, predictive maintenance (PdM) is cutting-edge technology. But what about prescriptive maintenance? Prescriptive Maintenance (RxM) is a technique that analyzes machine data and uses that information to recommend actions to correct any anomalies and reduce operational risk.
Basically, RxM is higher than PdM. PdM tells us when something might go wrong, while RxM tells you what steps need to be taken to fix the problem.
While prescriptive maintenance clearly has the potential to fundamentally change maintenance, research is still ongoing.
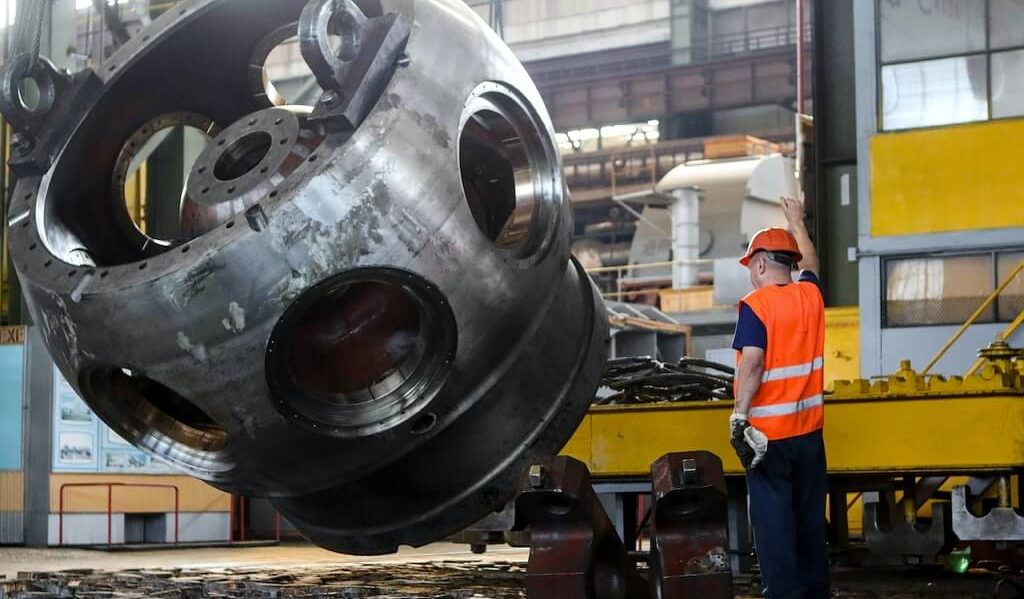
Increasing Predictive Maintenance (PdM) Strategies
Advances in machine learning (ML), artificial intelligence (AI), and the Internet of Things (IoT) enable the collection of data from machine-level sensors and ML algorithms to predict machinery failure modes before they cause costly downtime. This process helps companies plan maintenance proactively, streamline maintenance operations and reduce operating costs.
The latest research reveals that the global predictive maintenance market was valued at USD 5.6 billion in 2021 and is expected to grow to USD 64.25 billion by 2030, at a CAGR of 27.4% from 2022 to 2030.
As the benefits of predictive maintenance are increasingly recognized, this maintenance strategy is expected to gain popularity and impact the CMMS market in the coming years.
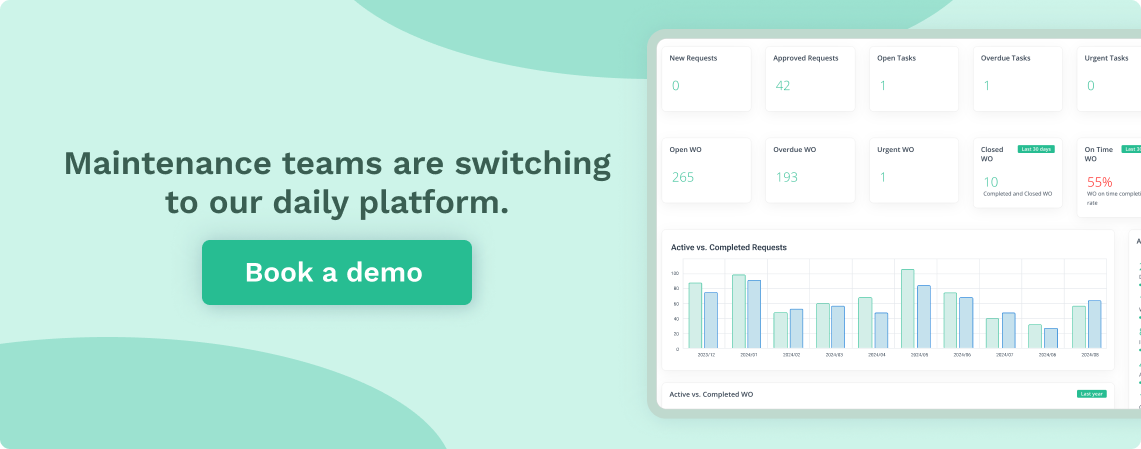
Supercharge your business with WorkTrek CMMS
Book a WorkTrek demo to see how a CMMS can help your asset management.
Try for freeInternet 4.0, Internet of Things, and Artificial Intelligence
The use of modern tools such as Internet 4.0, artificial intelligence, and the Internet of Things is bringing the future of CMMS to industrial maintenance automation. Artificial intelligence or the ability of machines to self-regulate to maintain the human element, the CMMS must be able to integrate with these autonomous machine parts.
A computer can communicate with another computer through Internet 4.0 without human intervention. Smart devices can monitor themselves; no technician is required to do this. Maintenance managers have access to real-time data, which they can then take appropriate action to prevent unforeseen issues.
Companies use IoT data to manage asset maintenance. Predictive maintenance is used to make real-time asset management decisions. The maintenance function will be transformed from a cost center to a profit center. Using data collected through IoT, you can make decisions that align with your long-term goals. People are moving to data-based intuitive maintenance. Maintenance audits can be performed faster using IoT.
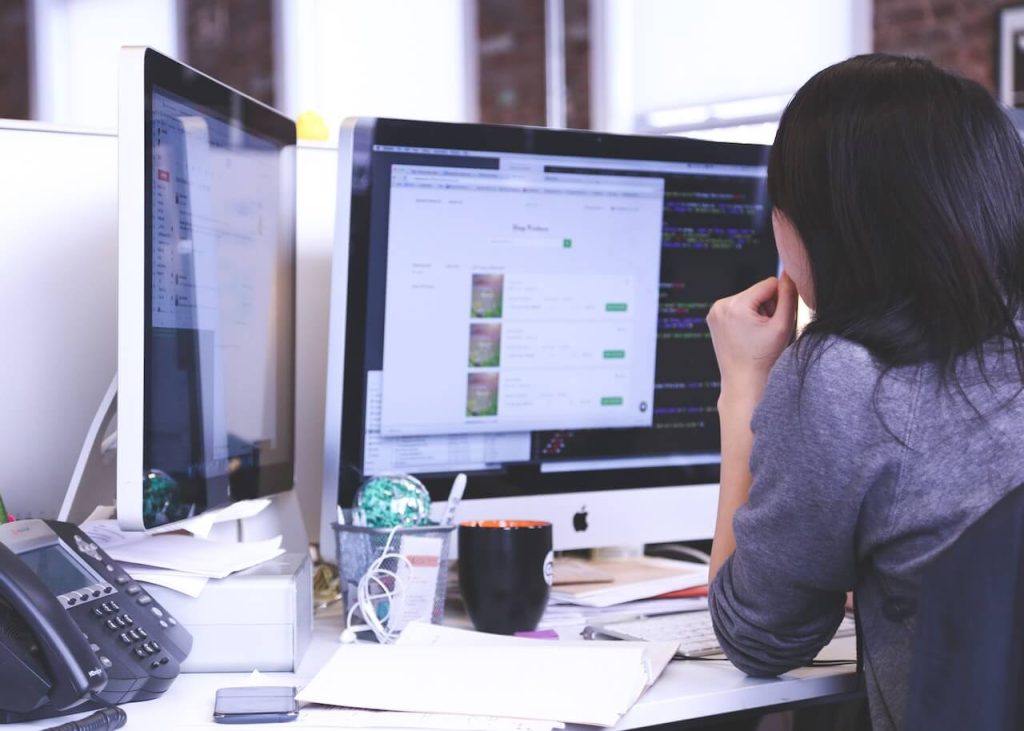
Inventory management
Additionally, to prevent unplanned downtime and loss of production, maintenance managers must ensure that spare parts and components are readily available. Therefore, one of the latest developments in maintenance management is the improvement of inventory management.
Modern CMMS systems make inventory and spare parts management easier than ever. With a reliable CMMS software solution, maintenance managers and technicians can determine which equipment requires which spare parts, provide an estimated time frame for when components on a machine will need to be replaced and more.
A data-driven approach to inventory control can eliminate waste, speed up item delivery, increase prices, and ultimately improve maintenance control.
High demand for integration with other business applications
In the past, CMMS software was seen as a tool that only benefited the maintenance department. These benefits are short-sighted and primarily seen as a tool for tracking preventive maintenance and spare parts. However, companies today are realizing how a CMMS fits into an organization’s overall strategy. Obviously, if production machinery or critical equipment is unavailable, production will slow down or customer service will be disrupted. This ultimately affects the company’s ability to compete and provide value to customers.
Since CMMS software is now considered a critical tool for achieving business goals, there is a strong need for integration with other business-critical applications. Many companies integrate CMMS with enterprise resource planning (ERP), customer relationship management (CRM), human resource information systems (HRIS), and other tools. CMMS users will demand integration capabilities with other business applications, and CMMS vendors are addressing these needs.
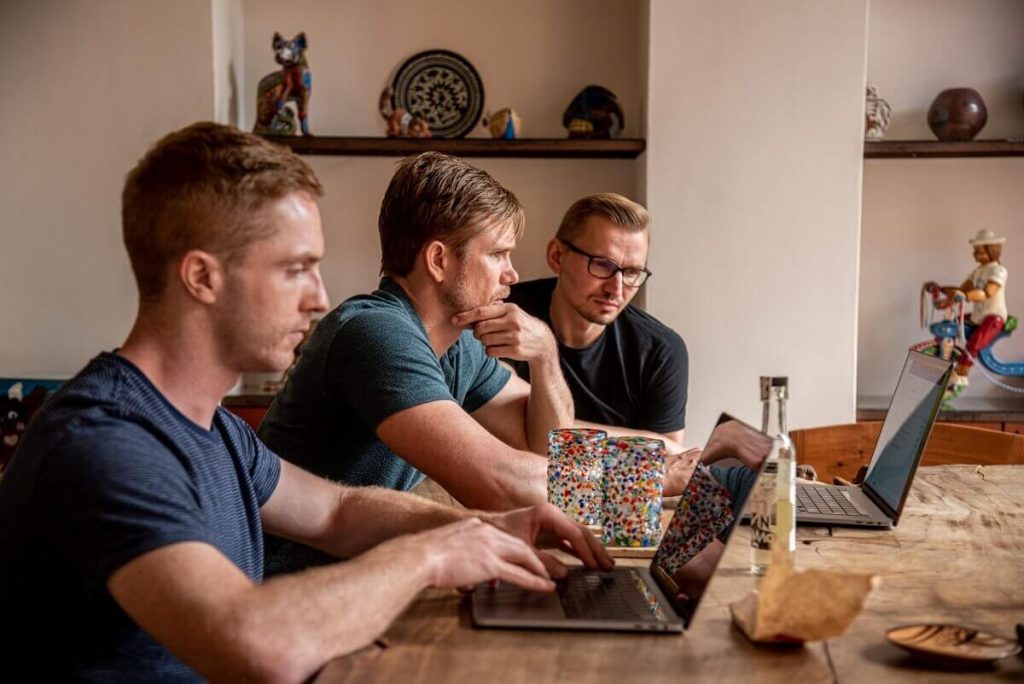
Automation and robotics are revolutionizing maintenance work
Automation technologies, including robotics, will play a vital role in the future of CMMS maintenance management. Robotic and autonomous systems will perform routine tasks, inspections, and repairs in hazardous or hard-to-reach areas, keeping maintenance personnel safe. These AI-powered bots will be able to analyze complex data patterns, detect anomalies and perform advanced diagnostics. Collaboration between humans and robots will simplify maintenance operations and allow technicians to focus on complex problem-solving and decision-making.
Using robots in maintenance management brings several advantages. They can operate in harsh environments without the need for personal protective equipment, minimizing risk to human workers. In addition, robots can work continuously without getting tired, thereby increasing productivity and reducing maintenance costs. By taking on repetitive and mundane tasks, robots free human technicians to engage in more strategic and value-added activities.
Robotic process automation (RPA) will also play an important role in maintenance management. RPA uses software robots to automate manual and repetitive tasks, such as data entry and report generation. By automating these administrative processes, organizations can increase efficiency, reduce errors, and free up resources for more important maintenance activities.
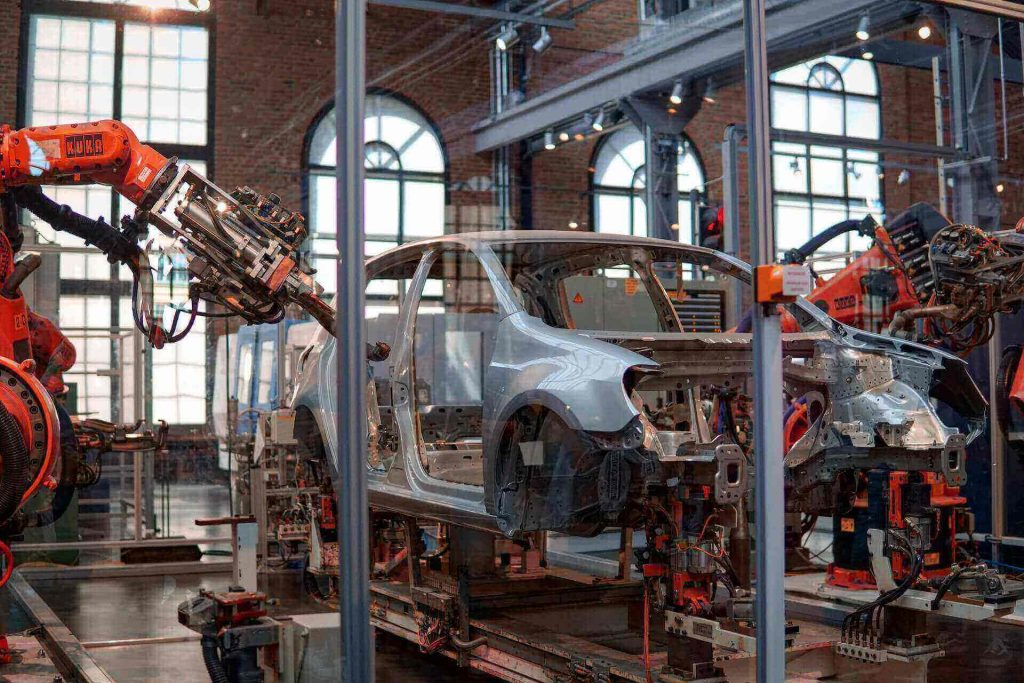
The CMMS Market Continues To Grow
The CMMS market is expected to continue growing through 2023 as more companies realize the benefits of using these systems to manage their maintenance processes. CMMS systems support businesses to increase efficiency, reduce downtime and increase equipment reliability, resulting in cost savings and improved profitability. The continued development of new technologies, including predictive maintenance and advanced analytics, will help drive further expansion in 2023.
According to a new study by Grand View Research, Inc., the global computerized maintenance management system market is expected to reach USD 2.41 billion by 2030, growing at a CAGR of 10.9% from 2023 to 2030.
The future of CMMS maintenance management promises exciting advancements driven by technology and sustainability. AI, IoT, automation, AR/VR, and data-driven decisions will revolutionize maintenance practices, increase efficiency, reduce costs, and increase equipment reliability. Companies that start using these technologies and invest in upskilling their employees will gain a competitive advantage in the future of maintenance. By integrating sustainable practices and circular economy principles, companies can contribute to a greener future while simplifying maintenance operations. The journey to the future of maintenance management and CMMS have already begun.