Get a Free WorkTrek Demo
Let's show you how WorkTrek can help you optimize your maintenance operation.
Try for freeSpare parts management may not be the glamorous part of running a business, but it’s one of the most critical. Every industry that relies on machinery—manufacturing, transportation, energy, or construction—needs a smooth and efficient way to manage its spare parts inventory.
Illustration: WorkTrek / Data: MARK-PILOT
Imagine your business grinding to a halt because you couldn’t find a small yet crucial part in time. It’s a scenario no one wants to face, yet without proper spare parts inventory management, this is a daily risk.
In this blog, we’ll discuss why having a solid system to manage your spare parts can be a game changer. By the end, you’ll understand how it can reduce downtime, save money, and improve efficiency and customer satisfaction.
Understanding the Basics of Spare Parts Management
Spare parts management involves overseeing, tracking, and controlling an organization’s inventory of spare components needed for equipment repair and maintenance. This should be part of any inventory control process for critical spare parts.
It’s about more than just keeping parts on a shelf. You need the right parts at the right time without overstocking or understocking.
Many organizations fail here. They don’t give enough thought to managing their spare parts until something breaks down. Then, they’re left scrambling to find what they need, which costs them dearly.
So, why is spare parts management critical? Let’s break it down.
Downtime Costs More Than You Think
We’ve all been there: A critical piece of equipment breaks down, and the whole operation comes to a standstill. This downtime doesn’t just affect productivity. It hits your bottom line in more ways than one.
Let’s take a manufacturing example. If a production line stops for even one hour, you can expect significant financial losses.
Illustration: WorkTrek / Data: Sparrow
According to The International Society of Automation, equipment downtime in the manufacturing industry can cost between $20,000 and $30,000 per hour. It can be even higher for sectors like oil and gas, reaching up to $88,000 per hour!
The scary part? Much of this downtime could be avoided if spare parts were appropriately managed. A well-organized system can significantly reduce the time needed to get equipment back up and running.
The Ripple Effect of Downtime
When you experience downtime, it doesn’t just impact the immediate area where the failure occurred. Think of it as a ripple effect. Here’s what can happen:
1. Production Halts:
Equipment breakdowns can cause a bottleneck in your production process. As a result, you may miss deadlines, disappoint customers, and potentially lose contracts.
ff2. Labor Inefficiencies:
While your machines are down, employees may be left waiting for repairs to be completed. You’re paying for that time without getting any work done.
3. Customer Dissatisfaction:
Your reputation will suffer if you can’t deliver products or services on time due to equipment failure. Customers will not only get frustrated but also take their business elsewhere.
4. Unplanned Overtime:
When equipment is finally repaired, your team might need to work overtime to compensate for lost production time, adding additional costs to your budget.
Implementing a robust spare parts management system minimizes these costly ripple effects. Downtime is reduced, and your entire operation can continue functioning smoothly.
Avoiding the Overstocking and Understocking Dilemma
Effective spare parts management is about finding the perfect balance between having enough parts to meet demand and not having so many that you’re wasting money on excess inventory. This is known as avoiding the overstocking and understocking dilemma.
When you overstock, you’re tying up valuable capital in parts that may sit on the shelf for months—or even years—without use. Worse, they might become obsolete as newer machinery models come into play.
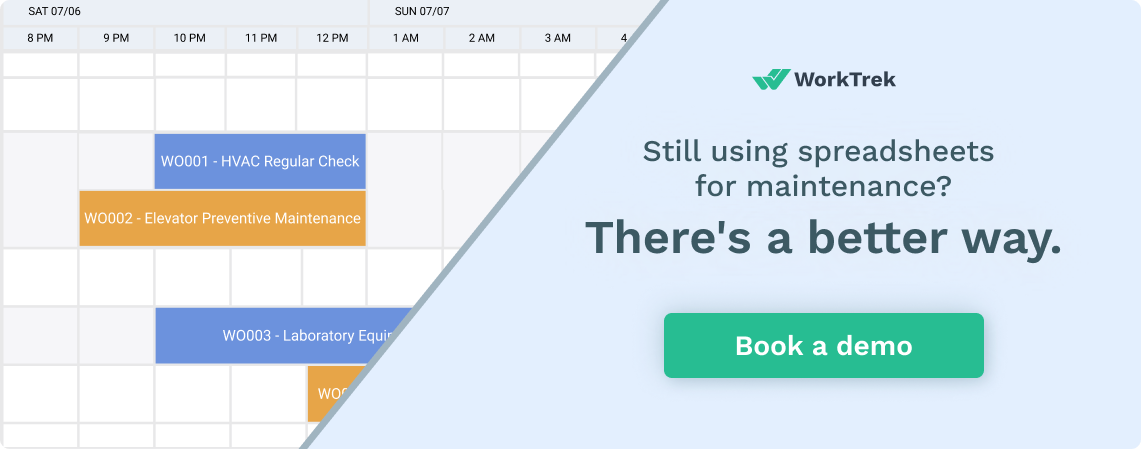
Illustration: WorkTrek / Data: Fin Models Lab
On the flip side, understocking leaves you vulnerable when critical equipment breaks down. If you don’t have the part available, you’re forced to scramble for an emergency procurement, which leads to rush fees, shipping costs, and inflated prices from suppliers who know you’re in a pinch.
So, how do you avoid both scenarios? Technology plays a huge role.
Using Technology to Optimize Inventory
Modern technology allows companies to manage their spare parts inventory without relying on manual processes or gut feelings. Today, advanced systems can track usage patterns, monitor stock levels in real-time, and even predict when certain parts are likely to fail based on historical data.
Here are some of the top tools to help you manage spare parts effectively:
1. CMMS (Computerized Maintenance Management Systems):
A CMMS system like WorkTrek tracks maintenance tasks and schedules. It also allows you to manage spare parts by keeping a record of your inventory, flagging low stock levels, and automating reordering processes.
Illustration: WorkTrek / Data: SM Global
2. ERP (Enterprise Resource Planning):
ERP systems go a step further by integrating spare parts management with other areas of your business, like finance, procurement, and logistics. This gives you a complete view of how spare parts inventory impacts other parts of the business.
3. Barcoding and RFID:
You can track each part’s movement through your warehouse or facility by tagging each part with a barcode or RFID tag. This eliminates the guesswork and human error involved in manual inventory tracking. Scanning technology helps you instantly update stock levels, ensuring accuracy at all times.
4. Predictive Analytics:
With the help of data analytics, businesses can forecast the demand for specific spare parts. This means you can anticipate when a part will be needed based on factors like machine age, usage patterns, and past breakdowns.
These technologies save time, increase efficiency, and reduce the risk of running out of critical parts.
Preventive Maintenance: Your Secret Weapon
One of the biggest benefits of having an organized spare parts management system is that it allows you to stay ahead of the game regarding preventive maintenance.
Instead of waiting for something to break, preventive maintenance allows you to service your equipment regularly before issues arise. This reduces the chances of major equipment failure, which can be far more expensive.
Illustration: WorkTrek / Data: Milliken
Preventive maintenance depends heavily on having the right spare parts available when needed. If you’re missing a part, the whole plan can fall apart. A well-managed spare parts inventory ensures you’re always ready for scheduled maintenance, which keeps your equipment in peak condition and prevents unexpected downtime.
Financial Impact of Effective Spare Parts Management
Beyond reducing downtime, efficient spare parts management directly impacts your financial performance.
Let’s break it down:
1. Reduced Holding Costs:
Excess inventory ties up capital that could be used elsewhere. By managing your inventory more effectively, you can reduce holding costs and free up funds for other investments.
2. Lower Procurement Costs:
With a reliable system, you can avoid last-minute, emergency purchases, which are typically much more expensive. Planning allows you to purchase parts in bulk, take advantage of discounts, and negotiate better deals with suppliers.
3. Fewer Production Delays:
The production runs smoothly when equipment is maintained correctly, and spare parts are readily available. This means you can meet customer demand, increase output, and improve profitability.
4. Improved Cash Flow:
You improve your company’s cash flow by not overstocking and tying up cash in unnecessary parts. This allows you to reinvest in growth, innovation, or other critical business areas.
Building Strong Relationships with Suppliers
Another overlooked benefit of good spare parts management is building strong, long-term supplier relationships.
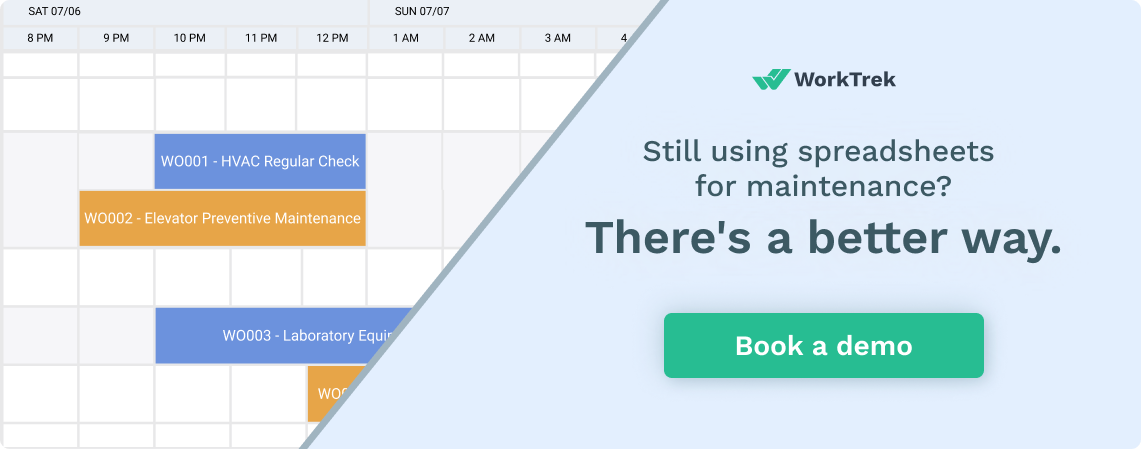
When you clearly understand your spare parts needs, you can work more closely with suppliers to ensure timely deliveries, negotiate better pricing, and even secure priority service in case of emergencies.
Source: WorkTrek
A good supplier relationship isn’t just about getting parts on time—it’s about being proactive. Communicating your needs ahead of time helps suppliers better anticipate demand, avoiding shortages and delays.
Plus, if you’re seen as a reliable, long-term partner, you’re more likely to get preferential treatment, like discounted rates or access to new technologies.
Enhancing Operational Efficiency
A streamlined spare parts management system doesn’t just save money—it improves operational efficiency across the board. When parts are readily available, and maintenance processes are efficient, your employees can focus on their primary tasks instead of wasting time searching for parts or waiting for repairs.
This is particularly important for industries that rely on continuous operations, such as manufacturing, utilities, or healthcare. Even minor delays can have major consequences in these sectors.
Automating parts management reduces human error, speeds up repair times, and ensures that your machinery is always running at its best. This boosts productivity and reduces the stress on your maintenance teams, allowing them to focus on preventing problems rather than reacting to them.
The Role of Security in Spare Parts Management
You might not think of spare parts as a high-security item, but they can be a target for theft or mismanagement. High-value parts are especially vulnerable; losing just one critical component can be costly.
That’s why it’s so important to incorporate security measures into spare parts management. Surveillance cameras, restricted access areas, and inventory audits are just a few ways to secure your parts.
Ensuring that only authorized personnel can access your parts inventory reduces the theft risk and improves accountability.
Extending the Lifespan of Your Equipment
Ultimately, proper spare parts management contributes to the longer lifespan of your equipment. When you have the parts needed to perform maintenance promptly, you’re extending the usable life of your machinery.
Illustration: WorkTrek / Quote: SCMDOJO
Regular maintenance and timely repairs prevent minor issues from turning into major problems. This reduces wear and tear on your equipment and helps you get more value from your investment.
And it’s not just about keeping things running for the sake of it. Extending the life of your equipment also means you can delay costly replacements and avoid unnecessary capital expenditures. This is a win for your bottom line.
Conclusion: The Real Value of Spare Parts Management
At its core, effective spare parts management is about being prepared. When you’re prepared, you avoid unnecessary downtime, save money, improve efficiency, and keep your team and customers happy.
It’s a simple concept, but its impact is far-reaching. By investing in a robust spare parts management system, you can ensure the smooth operation of your business, enhance your financial performance, and maintain a competitive edge.
So, if you haven’t already, now’s the time to examine your spare parts management. Implementing the right strategies today can set you up for long-term success tomorrow.