Get a Free WorkTrek Demo
Let's show you how WorkTrek can help you optimize your maintenance operation.
Try for freeIn facility management, most maintenance tasks are categorized as ‘reactive’ or ‘preventive’. Knowing the difference between the two is important because the most successful facilities sectors maintain a healthy balance between reactive and preventive maintenance. Too much reactive maintenance can stress and overwhelm your team. Therefore, it is important to create a program that emphasizes preventive maintenance and minimizes the possibility of reactive maintenance.
In this blog, we explain the difference between reactive and preventive maintenance and their long-term cost-effectiveness.
Reactive vs. Preventive Maintenance
Maintenance is an important part of keeping equipment running efficiently for as long as possible. Maintenance inevitably involves downtime and expense, so maintenance is sometimes postponed in hopes of maximizing production and profits. This avoidance can be detrimental in the long run, so it is important to distinguish between preventative and reactive maintenance.
Preventive maintenance addresses potential problems before they occur and reduces the likelihood of unexpected equipment failures. Preventive maintenance involves cleaning, replacing parts, and inspecting equipment properly to identify problems and then fix them before they become bigger problems. Preventative measures are proactive and can improve equipment longevity and safety outcomes.
Reactive maintenance occurs after an equipment failure, often unexpectedly. Unexpected equipment failures can lead to increased costs such as more expensive repairs, overtime payments to repair equipment, and unplanned downtime.
Preventive Maintenance
Preventive maintenance software is a strategy that teams and managers employ before a failure or outage actually occurs.
The main goal is to reduce the likelihood of failure or deterioration of equipment, components, or spare parts. To perform this type of maintenance, the team must consider the history of the equipment and track its previous failures. This paves the way for determining how often equipment is likely to fail and require repair/maintenance.
Preventive maintenance is a planning strategy for maintenance operations as it is based on well-established maintenance facts, reports, equipment history, and needs of the organization working as efficient equipment maintenance software.
With preventive maintenance as part of the CMMS functionality, companies can easily organize their maintenance tasks and ensure continuous productivity.
There is no doubt that preventive maintenance is one of the most popular and effective maintenance methods. However, this may not always be the right choice, as each organization has its own idiosyncrasies. Sometimes the cost of preventive maintenance is much higher compared to other possible methods.
What Are The Different Types Of Preventive Maintenance?
There are 3 types of preventive maintenance:
Systematic Preventive Maintenance
Preventive maintenance is carried out according to a schedule established according to the time or the number of units of use (produced). Even if time is the most common unit, other units can be used such as the number of products manufactured, the length of products manufactured, the distance traveled, the mass of products manufactured, the number of cycles carried out, etc.
This frequency of an intervention is determined by commissioning or after a complete or partial overhaul.
Condition-Based Preventive Maintenance
Preventive maintenance is subject to a type of predetermined event (self-diagnosis, sensor information, wear measurement, etc.). Condition-based maintenance is therefore maintenance that depends on experience and involves information gathered in real-time. It is also called predictive maintenance (non-standard term).
Conditional preventive maintenance is characterized by the highlighting of weak points. Depending on the case, it is desirable to put them under surveillance and, from there, to decide on an intervention when a certain threshold is reached. But the controls remain systematic and are part of the non-destructive control methods.
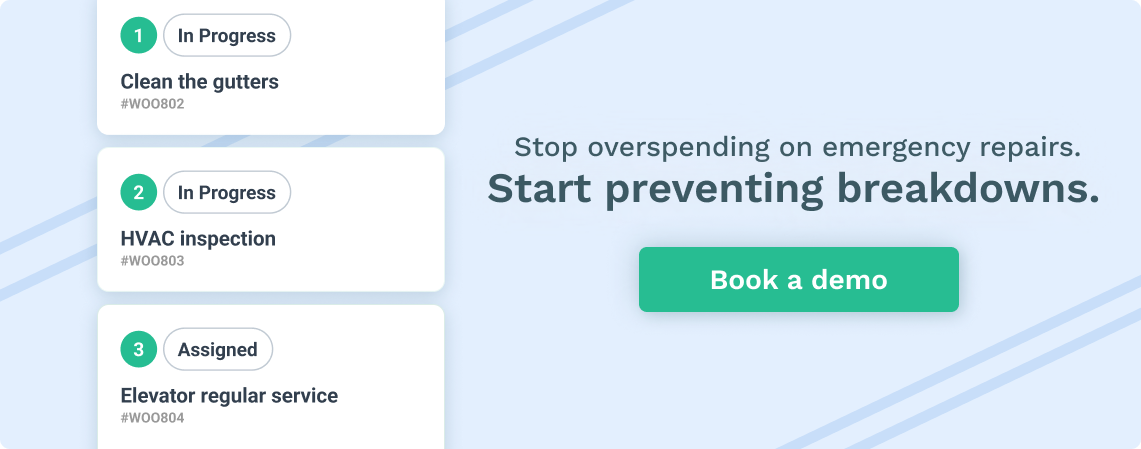
All materials are affected. This conditional preventive maintenance is done by relevant measurements of the equipment in operation.
Predictive maintenance
Predictive maintenance consists of anticipating future failures on equipment, an object, a system, etc. Concretely, it is a question of anticipating a breakdown or a malfunction thanks to the accumulation of a set of data. Booming in recent years, predictive maintenance has had several advantages. It avoids, for example, the immobilization of a broken-down production system (with the resulting financial repercussions).
Predictive maintenance makes it possible above all to anticipate breakdowns and offers the possibility of intervening while avoiding a much more expensive repair. With predictive technology, maintenance costs are reduced by 10 to 40% and the number of breakdowns is halved.
Is Preventive Maintenance Cost Effective?
Preventive maintenance has long been the most popular maintenance strategy for manufacturers. In industrial maintenance, 60% of companies associate preventive maintenance with increased productivity and over 60% associate preventive maintenance with reduced downtime and increased safety. It has long been believed to provide better cost savings than reactive maintenance.
While preventive maintenance still involves machine downtime, it is scheduled for a more convenient time and preferred over unplanned reactive maintenance, where the cost and time until the problem is diagnosed and repaired is unknown.
Benefits of Properly Implementing a Preventive Maintenance Program:
-
Reduce maintenance costs
Depending on the type and complexity of the company’s equipment, maintenance costs can be one of the largest financial drains. Preventive maintenance can help avoid this problem by reducing the likelihood of catastrophic failure or equipment degradation. Additionally, companies can now benefit from predictive maintenance software. These systems create regular maintenance checklists and help coordinate company-wide maintenance schedules.
-
Early detection of faults
One of the most basic preventive maintenance tasks is dismantling and thorough inspection of equipment and plant installations. While this is the most effective way to clean and polish your equipment from the inside out, it can also help identify some hidden flaws that surface diagnostics might miss. Production lines can benefit from early detection of problems as they are the cause of prolonged downtime. Regularly replacing dirty or partially damaged parts can eliminate many major defects in the long run. Managers can upgrade or install new functional software to realize automatic diagnosis and error detection. Additionally, some CMMS products can perform maintenance checks of an entire facility in a single cycle. Some systems are even building IoT infrastructure to incorporate device performance data. A single administrator can spot vulnerabilities before they cause significant damage.
-
Reduce downtime
For maintenance operations, both static systems and running machines must be partially or completely shut down. Preventive maintenance is almost always faster and uses fewer resources than other maintenance methods. Most modern operating systems, such as production lines and electrical equipment, include performance management sensors that identify specific problem areas. In this case, instead of shutting down the entire system, these problems can be isolated and fixed. With predictive maintenance, you can schedule maintenance work at convenient times, such as when employees leave the building or when the day’s operations are over, reducing disruptions to production and efficiency.
-
Longer asset life
Every piece of equipment has a finite useful life after which it needs to be repaired or replaced to varying degrees. Companies typically purchase such assets after determining their potential operation and potential production. Most companies already factor in repair or replacement costs. Still, preventative maintenance can provide an extra layer of protection to prolong the life of your equipment. A preventive maintenance program ensures equipment is performing according to the manufacturer and consumer specifications.
Challenges of Preventive Maintenance:
-
May exceed expectations
With preventive maintenance, there is still a risk of over-maintenance. Some failures are less dangerous to your operation than others. If you dedicate resources to avoiding every single problem, you’re probably wasting resources on PMs. Finding a balance between proactive error prevention and reactive remediation efforts is critical. If a preventative maintenance program is too extensive, it can lead to serious financial waste. In some cases, you should test components, parts, or even entire machines for possible failures.
-
Unexpected failure
Certain components and parts may fail randomly such that preventive maintenance cannot permanently prevent the failure. In such cases, it may make more sense to think about effective ways to deal with the consequences. You should not base the frequency of preventive maintenance calls on the usual metric of mean time between failures. Instead, the lifespan of the component should be considered when making this decision.
-
Continuous training for technicians
Another downside of some preventative maintenance systems is that field technicians don’t always keep their knowledge and training up to date. The bottom line is, if your maintenance professionals don’t understand the need for preventive maintenance, or aren’t adequately trained to perform it, they won’t be able to do it properly.
-
High upfront costs
When you first implement a preventive maintenance program, it can cost more to service equipment and assets on a regular basis than to wait for a power outage. Small businesses may find the initial cost of deploying a CMMS for preventive maintenance prohibitive if they have a limited budget for asset management and equipment maintenance.
Since facilities are regularly inspected for maintenance, you may need to invest in the latest tools and equipment to properly carry out the repair work, which will undoubtedly add to your overall business expenses.
Reactive Maintenance
Reactive maintenance is the strategy of returning equipment to normal operating conditions only when it fails. This means there is no regular maintenance or repair schedule to reduce downtime. Also known as breakdown repair or repair.
Under the right circumstances, reactive maintenance can be a good strategic approach. For example, you might have a facility that has low maintenance costs and is not essential to its operation. Or you may have planned to replace the machine after a failure, eliminating the need for proactive maintenance.
Reactive maintenance is a cost-effective approach as it requires minimal maintenance personnel and less budgeted repair costs. But it shouldn’t be used as your long-term strategy. This can lead to increased repair costs, unplanned downtime, production delays and lost revenue. It is recommended to allocate only 10% of the total asset inventory to reactive maintenance.
Don't let equipment failures add to your costs!
Stay competitive with WorkTrek CMMS software!
Try for freeWhat Are The Different Types Of Reactive Maintenance?
In addition to various maintenance strategies, asset-intensive companies can also choose a strategic approach within this strategy. For example, preventive maintenance (PM) and condition-based maintenance (CBM) are forms of proactive maintenance strategies.
Reactive maintenance is an umbrella term that includes the following types of maintenance:
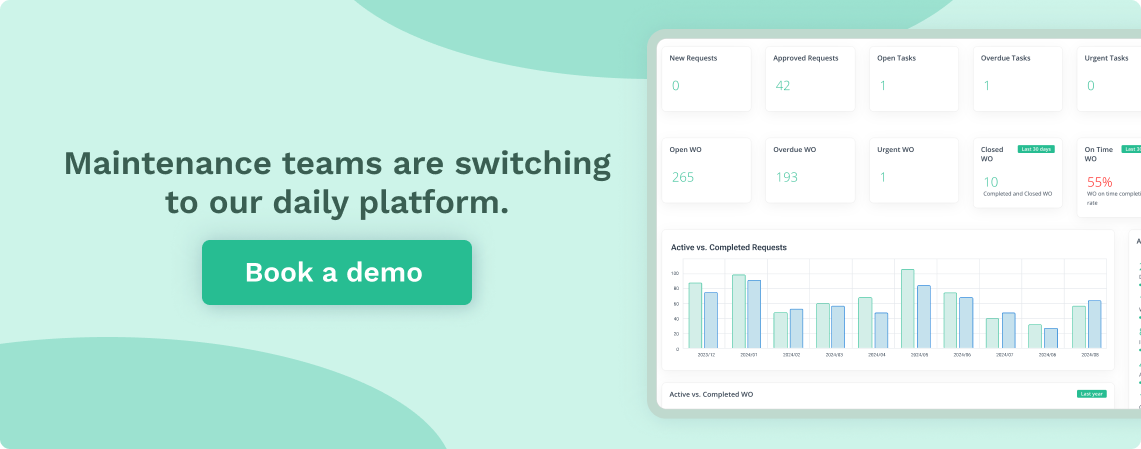
Emergency Maintenance
Emergency maintenance is performed on equipment or machinery that plays an important role in your production. This type of reactive maintenance is never planned and is usually a last-minute response to an immediate outage. Emergency maintenance also takes precedence over other business processes, which can cause unplanned delays.
Breakdown Maintenance
Similar to contingency strategies, breakdown repairs are unplanned events. It refers to an asset that fails suddenly and requires extensive repair work. This can lead to high repair and technician costs, as well as costly unplanned downtime. Running equipment to failure can cost organizations 10 times more than routine maintenance.
Corrective Maintenance
Corrective maintenance is a form of maintenance performed on an asset before it fails completely. For example, machine defects can be noticed during production. Rather than waiting for the inevitable machine failure, this part will be fixed immediately. Corrective maintenance is the closest thing to preventive maintenance in a reactive strategy by responding to problems before they escalate.
Run-to-Failure
Unlike the unplanned outage maintenance approach, run-to-failure maintenance is a planned strategy. This is done when the asset is consciously instructed to run until it fails. This allows a plan to be made to repair equipment without unduly delaying production. Or, in some cases, spare parts have been purchased to replace aging equipment should it fail.
Is Reactive Maintenance Cost Effective?
Reactive maintenance can be a fundamental part of any maintenance strategy, but when used alone it is only cost-effective for selected assets, such as:
- Short-term assets.
- Available assets.
- Long-lived or unmaintainable assets.
- Small capital assets.
- Non-critical assets.
For most machines and systems, purely reactive maintenance is much more costly and the least efficient type of maintenance in the long run. That’s because reactive maintenance can lead to unplanned inefficiencies and disruptions that often occur even at the most inconvenient times. Reactive maintenance is best used as a small part of a maintenance strategy once more efficient types of maintenance have been implemented.
Benefits of Reactive Maintenance:
-
Reduce investment cost
Reactive maintenance saves you money that would normally be spent upfront on preventive maintenance and labor costs. However, relying solely on reactive maintenance and completely ignoring preventive maintenance could be bad for your business in the long run.
-
Fewer staff required
With reactive maintenance, your main concern is to fix problems as soon as they arise. This way you don’t need a huge team of technicians to manage the device all the time. For preventive maintenance, you must have at least two technicians in the facility to conduct timely inspections to catch problems early. This also translates into extra salaries, increased team size, and labor costs.
-
No planning required
Preventive maintenance requires planned machine downtime for inspections, parts replacement, and other maintenance activities. There is no planned or planned equipment downtime and reactive maintenance. However, this may lead to unpredictable equipment failures in the future.
Reactive Maintenance Challenges:
-
Overtime is more expensive
Late orders, damaged reputation, and lost sales are common consequences of unexpected delays in manufacturing runs. Additionally, the equipment can break down at inconvenient times when personnel and parts are scarce. In such cases, businesses may have to pay extra for after-hours assistance, commuting, and emergency parts.
-
Unexpected shutdown of equipment
Plant downtime is a major disadvantage of reactive maintenance, which can lead to plant shutdowns or production interruptions lasting several days. Downtime is especially problematic in manufacturing because it can lead to layoffs or even entire plant closures for an unknown period of time.
-
Employees work overtime
In addition to the initial financial loss that reactive repairs typically entail, you may also need to pay overtime for those responsible for the associated equipment. For example, if one or two employees use down machines more than others, they may need extensive knowledge of the broken machine when investigating repairs.
Reactive vs. Preventive Maintenance – Conclusion
In maintenance management, reactive maintenance and preventive maintenance are usually opposites. Choosing a plan for your business that fits your functions and needs can be a difficult choice.
Maintenance costs make up a significant portion of operating costs. Many unpredictable and uncontrollable situations arise, resulting in additional costs that are difficult to predict in advance but are closely related to maintenance.
But your equipment is the heart of your business. Neglecting to maintain your equipment can cost you a lot of time, money, and sometimes even your business. Maintenance management today is very different from that of spreadsheets, notebooks, pens, and paper. Businesses want to keep their existing equipment for as long as possible, they want to stay ahead of the competition, and of course, they don’t want to suffer injury, equipment failure, or failure.
Is maintenance management important? If you consider your business important, maintaining your equipment and assets is equally important. You can’t do it without equipment.