Get a Free WorkTrek Demo
Let's show you how WorkTrek can help you optimize your maintenance operation.
Try for freeInvesting in CMMS software is a long process. It’s not uncommon to spend months or even years comparing vendors, pricing, features, and usability until a clear winner emerges. Once you choose the right option, it can feel like a huge weight has been lifted off your shoulders. Time to sit down and watch the results, right? Well, not exactly. The fact is that around 74% of all IT projects fail. It is not a small number! Additionally, there are many factors that can derail a successful CMMS implementation. Whether it is improper training, poor data entered into the system, misconfiguration of the system, employees not taking responsibility for the implementation process, or engineers taking responsibility for themselves. They refuse to use the new technology.
So how can you make sure you are among the 26% of organizations that successfully launch new technologies, such as a CMMS? Or better yet, how can we collectively reduce the total number of failed CMMS implementations? Well, as they say, if you don’t plan, you plan to fail. It is important to know the steps involved in a CMMS implementation so that you can be sure that you plan and execute the implementation correctly.
Define your goals
Before we get into the steps that lead to success, let’s take a moment to define what “success” actually means in the context of a CMMS implementation. The ultimate successful implementation is when the organization maximizes the value of the new system. What does it mean?
Well, it means a lot of things. First, it means that your CMMS is configured correctly for your specific use. It also means that PMs are capitalized when they are hired (and capitalized for the right assets), costs are added to the right assets, you have an accurate picture of your inventory levels, and everyone who should be using the CMMS is using it on a daily basis. Finally, one of the main signs that you have set up your CMMS to maximize value is when real and accurate data can be extracted from the CMMS to form KPIs and reports. These can be used to identify trends and make business decisions such as repair or replacement. Now that we know what you need to work on, let’s get into planning mode.
Create the right culture
To put it bluntly, without the right workplace culture, the implementation will fail. There are a number of guiding principles you should put in place before implementation to ensure your organization can support it. Ensure work requirements documentation is enforced, perform proper root cause failure analysis, and identify and classify equipment by criticality. These tasks, performed consistently, set an accountability-driven precedent that is essential for working with a CMMS.
Once these guiding principles are established and followed, the real work can begin.
Implementation Steps
Step 1: Get management support
With any organizational change, support must come from above. Fully integrating a CMMS into your organization takes time and resources. It will be an uphill battle to keep things running smoothly if management is not committed to providing or allowing these resources.
It is important to manage expectations with management right from the start. Implementing a CMMS is not immediately a panacea. It is a tool that, with the right resources and inputs, will lead to smarter, more efficient and cost-effective maintenance. Make sure your management team is aware that it can take some time to see these returns.
Step 2: get to know your key stakeholders (and give them a voice)
It is important to remember that a CMMS is not a standalone solution. For it to work in your organization, it needs to be integrated into your existing facility workflow. For this reason, it is absolutely essential to define which teams and individuals will work or be affected by a CMMS.
Of course, everyone who creates or completes work orders regularly enters the system. But who else gets hit? It is a good idea to allow CMMS access to machine operators, inventory managers, health and safety officers, and reliability engineers. Each of these roles will be significantly impacted by the introduction of a CMMS, and each of them can use the output of a CMMS to do their jobs better. It is a great idea to set up a steering committee with a representative from each of these groups so that they can ensure that their team’s needs are met during the implementation process.
Above all, it is important to designate a CMMS sample. This is someone who will work closely with your CMMS provider to create a realistic implementation plan that takes into account your organization’s structure and goals. They will be the primary link between your business and the CMMS provider to ensure that key milestones are reached and that nodes are resolved as they occur.
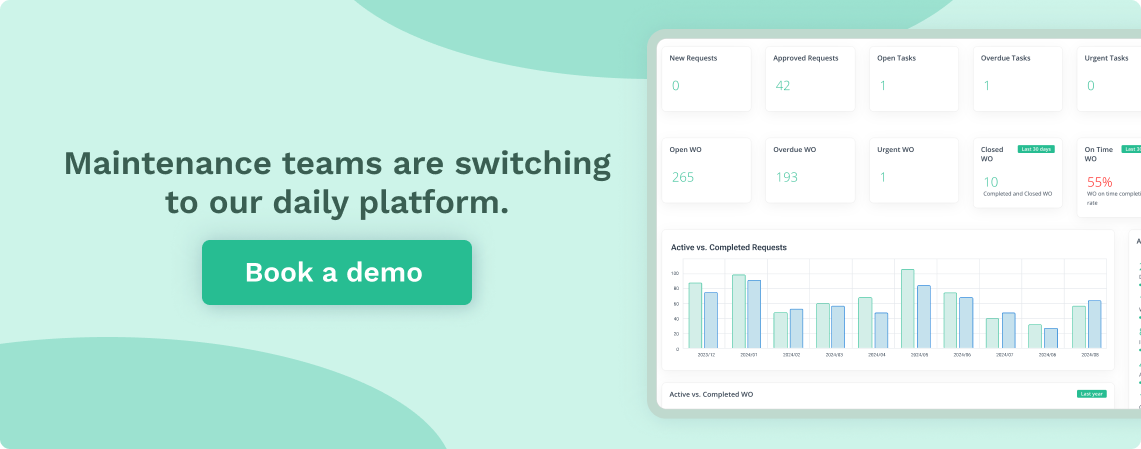
Step 3: Develop a detailed project plan
Now that management is on board and you have identified and consulted everyone who should be involved in your implementation, it’s time to create a project plan with the help of your CMMS provider. This plan should be as detailed as possible and can range from six months to a year or more.
The project plan should include key dates for achieving milestones, such as identifying customization needs, cleaning and entering data, completing user training, and conducting CMMS audits. The more detail you can get with this plan, the better. Having explicit and achievable goals to work on will reduce ambiguity and increase the accountability of everyone involved.
Step 4: Start and check-in
Once you’ve established a solid project plan that has controlled both your organization and your CMMS provider, it’s time to get started. This includes preparing the team for change, collecting and cleaning data, properly configuring the system, training end users, and finally activating the system.
During the kick-off, it’s important to have a CMMS vendor you can check in regularly with. Who can provide on-site training and technical support as you navigate a new system? Trying to do it yourself can lead to poor data entry, improper training, and processes that aren’t as optimized as they could be. At the end of the implementation project plan, it is important to contact the CMMS vendor and discuss issues such as reporting, user adoption, and anything else learned during implementation.
Step 5: Expand, Expand, Expand
In today’s technology landscape, nothing stays the same for long. As the possibilities expand and the tools evolve, it’s important that your business evolves too. Once you’ve successfully set up your CMMS, you keep wondering what else you could do with it. Have you collected enough data to start optimizing your PM strategy? Are there any features you’re not using that you could benefit from? Are there any integrations with other business systems that you can take advantage of?
Remember, a CMMS is a database of information about your assets. You can use this data to make better decisions at all levels of your organization and change the way you work for the better.
Step 6: Use a dedicated migration teams
The ease or difficulty of migration hinges on the upfront effort invested. Take, for instance, a facility anticipating a seamless transition without the meticulous examination and cleanup of their data, as well as efficient asset management prior to implementation; they might face unexpected challenges on the actual migration day. Having a dedicated team for asset migration is invaluable, and for those daunted by the task, specialized services exist to provide assistance.
Step 7: Schedule regular meetings
Establish a practical kickoff date and ensure that all relevant teams are informed of this timeline. Throughout the implementation phase, conduct regular meetings with key stakeholders to ensure their departments receive the necessary attention. These check-ins are essential for maintaining a constant awareness of the CMMS’s status. Regular communication with the best CMMS provider is equally crucial. Your account manager can play a pivotal role in keeping you on course toward a successful implementation.
Step 8: Training
Common mistakes in CMMS implementation
Organizations find adopting new software easily, so they forgo the critical planning and pre-implementation strategies that make CMMS adoption a success.
There are four huge ways to mess up a CMMS implementation, and most failed projects suffer from them.
Lack of planning
Planning is an essential and often missed step in the process. A CMMS alone does not solve the maintenance problems that plague a facility. In order to properly implement a CMMS (or even choose the right software), a facility should create an action plan that includes:
- What types of data they want to track
- What kind of functionality they need
- what budget do you have
- Stakeholder approvals and buy-in
Investing immediately in a CMMS without a plan is a serious mistake that can kill a project when it arrives.
Implementation issues
The stage with the most diverse sources of error is probably the implementation stage. This involves more than installing software and starting work orders. Implementation involves many critical factors:
- How is data migrated from previous systems? Is a PM plan designed and ready to be programmed?
- Was the software field tested before being rolled out to the entire facility?
- Does everyone communicate when things go on?
- At this stage, communication, testing and planning are still extremely important parts of the CMMS implementation process.
Little or no CMMS training
When new equipment enters a facility, maintenance personnel must be trained in its use and maintenance tasks. The same goes for a CMMS, but institutions continue to monitor this step. Training shouldn’t be a one-time thing either. Ongoing training is extremely important, especially when a CMMS receives updates for new features. When an organization skimps on training, maintenance personnel don’t know how to use the system designed to make their jobs easier. Plus, training is proven to increase adoption — don’t let implementation ruin it.
Entering poor-quality data into the CMMS
Finally, the data collection process can easily kill a CMMS – if you put garbage in, you get garbage. Maintenance teams need to understand the types of data they need to capture. Hands-on training can help – when technicians learn to populate work orders with quality, useful information, the data they receive will be actionable. Maintenance teams need to understand the types of data they need to capture. Hands-on training can help with this: show technicians how to fill work orders with useful and quality information, the data you extract will be useful. Trust the CMMS provider to help you throughout the entire CMMS implementation process. Invite them to perform product demonstrations for the entire team during pre-deployment to ensure the product is suitable for everyone. During implementation, ask for their help with data migration. And during post-distribution, ask them how to use the data you’ve collected. By following these steps and avoiding the most common implementation mistakes, you will be among the 30% of organizations that successfully implement an IPS.