Get a Free WorkTrek Demo
Let's show you how WorkTrek can help you optimize your maintenance operation.
Try for freeWhat is Plant Operations Management?
Plant Operations Management involves overseeing and optimizing the daily operations of a manufacturing facility or industrial plant to ensure efficiency, productivity, and safety.
It encompasses various tasks such as production planning, scheduling, resource allocation, quality control, maintenance, and workforce management. Plant operations managers are responsible for coordinating and supervising these activities to meet production targets, maintain quality standards, minimize downtime, and maximize profitability.
They also play a crucial role in implementing process improvements, implementing new technologies, and ensuring compliance with regulatory requirements and safety protocols. Overall, plant operations management is essential for the smooth and cost-effective functioning of manufacturing plants and plays a vital role in achieving organizational goals.
Almost all businesses have two basic ways to increase their profits. Increase their revenue by selling more products or services and reduce their operating costs. While finding ways to generate sales is often seen as the most appealing aspect of running a business. Reducing costs through the strategic management of operations can be just as important. Given that companies can lose 20-30% of their annual revenue due to organizational inefficiency, there’s something to be said for running a tight ship and finding ways to save money as much as possible. It is precisely for this reason that plant operations management is essential for any business to remain profitable.
What Is Operations Management?
Operations management (OM) is the administration of business practices to create the highest possible level of efficiency within an organization. It is about converting materials and labor into goods and services as efficiently as possible to maximize an organization’s profits. Operations management teams attempt to balance costs with revenue to achieve the highest possible net operating profit.
Key points to remember:
- Operations management is the administration of business practices to create the highest possible level of efficiency within an organization.
- Operations management aims to convert materials and labor into goods and services as efficiently as possible.
- Business operations management professionals try to balance costs with revenue to maximize net operating income.
Understanding Operations Management
Operations management involves the use of personnel resources, materials, equipment, and technology. Managers acquire, develop, and deliver recommended products to customers based on customer needs and company capabilities.
Operations management deals with a variety of strategic issues. Some of them are: determining the size of manufacturing plants and project management methods and implementing the structure of computer networks. Other operational issues include managing inventory levels, including work-in-progress levels and raw material acquisition, quality control, material handling, and maintenance policies.
Operations management consists of studying the use of raw materials and guaranteeing a minimum of waste. Therefore, operations managers use many formulas. For example, the economic order quantity formula determines when and what size of an inventory order to fulfill and how much inventory to hold.
The combination of understanding and coordinating the work of a business is essential to becoming an effective operations manager.
Fundamentals of Operations Management
Although there is no single accepted method of operations management, most schools of thought will agree that its definition rests on the following foundations.
Planning and design
A large part of operations and project management is the forecasting, planning, and design of processes based on current and future conditions.
Processes
Repeatable processes are at the heart of the production and manufacture of goods and services.
Cost management
Product development costs such as materials, labor, and equipment make up a significant portion of a company’s operating expenses. The management professional must monitor these costs carefully.
Efficiency
At some point, every organization will suffer from bottlenecks in production and unoptimized processes. Operations managers need to address these inefficiencies and work to improve them.
Quality control
Ongoing quality assurance is integral to maintaining high levels of customer satisfaction. Without it, the business will lose customer demand for its products and services.
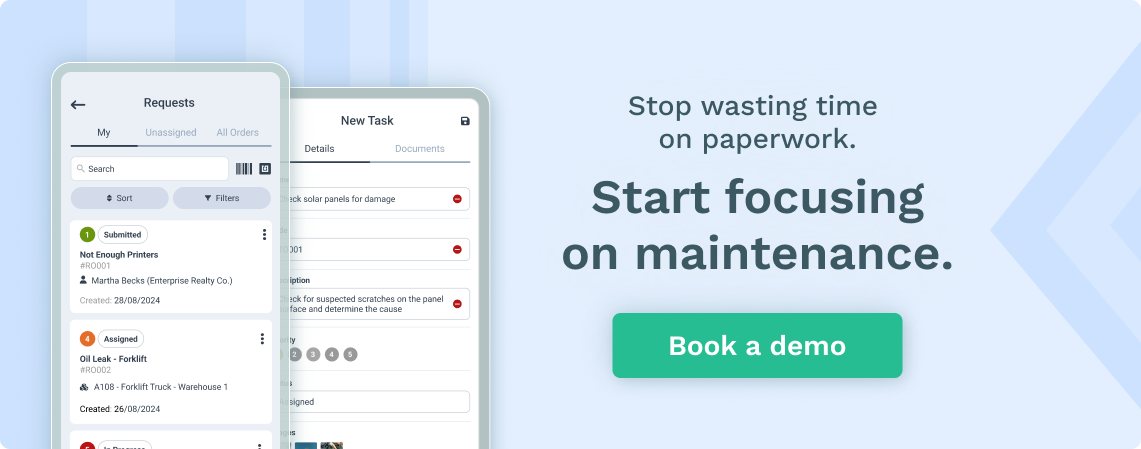
Technology
Research and development are at the heart of these foundations. Therefore leveraging technology allows companies to beat their competitors to the punch.
Continuous improvement
Organizations must constantly work to improve their processes. They need to find new and more efficient ways of doing things. It can be hiring new people, using updated technologies, creating new product lines, and phasing out poorly performing items.
Profitability
Bringing these foundations together leads to a strong bottom line, better cash flow, and better margins.
Implementation Phases
The implementation of an operations management strategy generally follows a three-step sequence which proceeds as follows:
Phase 1: Planning the Operating Systems
The first phase consists of planning the five aspects of the enterprise operating systems:
Outputs
Planning company products or services requires conducting market research to determine the market fit of products, competitors, and optimal pricing strategies.
Capacity
After determining what products or services to produce, operations managers need to specify how many of those outputs will be produced and how often.
Facilities
Next, operations managers need to plan for the facilities needed to support their production and manufacturing activities.
Job descriptions and workforce
Operations managers also need to determine the size of their production workforce. They also need to decide what skills to look for in employees and what their responsibilities and roles will be.
Workflow
The final step in planning operating systems is to create a system of tasks, processes, and a chain of accountability necessary to produce the outputs of the business.
Phase 2: Production Planning
The second phase focuses on planning the precise details of production, supply chain management, and quality control:
Production
Converting inputs (materials and labor) into outputs (products and services) requires the operations manager to determine the equipment, materials, and tasks needed to expedite production.
Scheduling
Scheduling is a critical activity that ensures that enterprise operating systems have the right resources, people, and facilities at all times.
Supply chain and inventory management
As mentioned earlier, supply chain activities are an important component of a company’s operations. A related operational function is inventory management, which requires striking a balance between maintaining a sufficient number of products in stock and avoiding unnecessary costs associated with warehousing and wasted inventory.
Quality control
Operations managers must have a clear system for maintaining optimum levels of inputs and outputs to ensure that products and services meet high-quality standards.
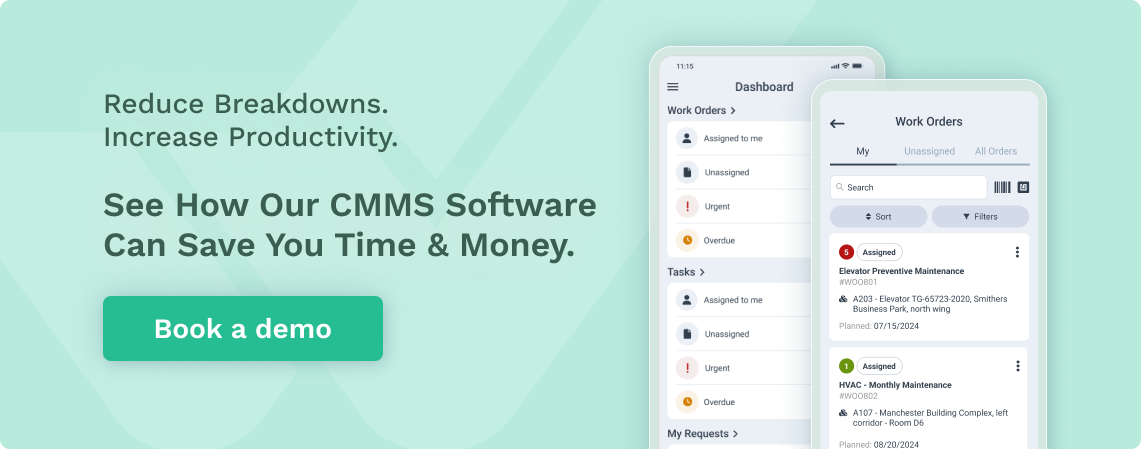
Phase 3: Productivity Management
The final step in implementing an operations management strategy focuses on managing productivity within the organization. In the context of operations management, productivity is defined as the ratio of output volume to input volume. Simply put, productivity refers to the efficiency with which resources like capital and labor are used to produce products and services.
For example, many manufacturing companies measure productivity using the output metric per hour. It looks at the number of units produced per hour. This figure is calculated by dividing the number of units produced by the total number of hours worked by employees over a certain period of time.
Benefits of Implementing an Operations Management System (OMS)
As it grows in size and complexity, any organization begins to become more difficult to manage. Therefore the complexity of managing an organization increases when the number of things to manage increases. For example the number of employees, departments, programs, or business processes. A company’s ability to turn its assets into profits, its inventory into goods, and its supply chains into cash flow is enhanced by the use of an operations management system.
Here are the advantages of implementing such a system in the organization:
Removes complexity from operations
Business complexity has an effect on organizational performance. With an established operations management system, organizations will be able to streamline any processes that may be causing additional costs or wasted time and labor. It minimizes wasted time and helps reduce unnecessary expenses that might arise due to the use of slow and inefficient business processes.
It reduces costs and increases the profit margin
A reduction in production cycle time allows more products to be produced in less time, which increases profit margins for the organization. One of the ways to effectively reduce cycle time is to embed lean production into your organization’s processes and perform analysis at every step of the process, which helps reduce costs. This results in greater profitability and lower product prices, which leads to increased sales.
Increase worker productivity
Operations management systems ensure your production process is running efficiently and improve your existing workflow by seeing what works and what doesn’t. Operational management systems help organizations effectively manage labor resources during the manufacturing and distribution process to maximize revenue.
Promotes collaboration between different departments
Operations management systems allow the different departments of an organization to work together to achieve business objectives and improve management systems to achieve better results. A management information system (MIS) brings together the collection of past data, processes, customer expectations, and requirements for the successful and holistic management of a business.
Minimizes waste
Organizations can better understand what is needed and what isn’t in their business processes by implementing a system. It is also an opportunity to analyze the costs of the organization and to carry out an internal audit to identify opportunities for improvement.