Get a Free WorkTrek Demo
Let's show you how WorkTrek can help you optimize your maintenance operation.
Try for freeWhat does it take to keep a facility running smoothly, and why is regular maintenance essential? This comprehensive guide to facility maintenance will guide you through the steps you need to take to manage facilities efficiently. Do you spend a lot of time manually tracking your property maintenance tasks? As a facility manager or owner, are you looking for ways to improve building maintenance and manage work being performed by maintenance technicians?
This article outlines the critical elements for adequate facilities management that prevent costly downtime, ensure safety compliance, improve tenant experience, and sustain a productive environment.
Facility maintenance includes routine upkeep, repairs, and safety protocols in physical commercial spaces. It focuses on proactive and predictive approaches to minimize failures and optimize equipment longevity. It also depends heavily on the coordination of facility managers, maintenance technicians, and supporting staff.
These staff members utilize specialized skills and technology to meet the unique needs of different building types. This group can include internal employees, outside firms, or independent contractors.
Additionally, facility management software can improve health and safety standards by directly incorporating health and safety guides in the mobile app.
Exploring the Scope of Facility Maintenance
The facility maintenance process is designed to improve efficiency and extend a building’s lifespan by caring for its capital assets, equipment, and exterior spaces. It focuses on achieving peak functionality while preserving asset longevity.
These maintenance tasks include regular servicing and repairs of machinery, equipment, furniture, and structural elements of buildings, as well as ensuring that spaces are secure, aesthetically pleasing, and operational.
Such facilities typically denote commercial structures where various activities are tailored to specific objectives. Examples include office complexes, medical centers, educational institutions, and storage warehouses.
Maintenance Strategies
Maintenance within these premises encompasses several strategies such as reactive (corrective), preventive (planned), risk-driven (risk-based), and based on actual conditions encountered (condition-based).
It serves an essential function in organizations’ operations management frameworks, allowing them to establish performance benchmarks for continuous evaluation regarding components’ health status and grounds care.
Maintaining fire safety systems forms part of this crucial activity spectrum alongside instituting security protocols that collectively uphold mandated health & safety regulations—strategizing against hazards stemming from neglected assets, thus bolstering uninterrupted facility workflows.
Source: Limble
The Role of Preventive Maintenance
Scheduled inspections, adjustments, and repairs constitute the core of preventive maintenance, an essential aspect of successful facility management. This systematic approach is designed to prevent breakdowns and prolong the life expectancy of equipment.
It bolsters asset longevity while ensuring adherence to legal requirements and minimizing operational interruptions.
Regular servicing and corrective actions taken on malfunctioning equipment significantly diminish disruptions. Such measures elevate staff morale by reducing incidents related to faulty machinery.
They clearly define team duties and accountabilities, promoting an organization’s efficient distribution of resources.
Some of those activities include:
- Testing fire safety systems
- Check Pest control
- Test security cameras and recording devices
- Evaluate electrical systems
- Check office equipment
Corrective Actions to Combat Equipment Failure
Source: Machinery Lubrication
Corrective or reactive maintenance falls at the opposite end of the maintenance continuum and addresses issues once they arise. Its primary objective is to return equipment to its normal operating state. The corrective approach is proactive maintenance.
This element of maintenance plays a vital role in business operations. It tackles breakdowns and malfunctions head-on, offering remedies that restore equipment functionality, thereby preserving uninterrupted business activities.
Embracing Automation in Facility Maintenance
Automation and technology have evolved across industries, and several tools can also help with facility management. Maintenance teams increasingly rely on sophisticated management systems that offer an organized and efficient method of overseeing facility upkeep to function effectively. These technological solutions simplify procedures while simultaneously minimizing human mistakes.
Take WorkTrek CMMS software, for example—it plays a crucial role in automating the scheduling of preventive maintenance tasks and monitoring the status of equipment repairs.
Incorporating such tools into pre-existing organizational systems promotes greater process efficiency and data precision for maintenance management operations.
Source: WorkTrek
Exploring Facility Management Teams
In every efficiently operated building, there are the unseen but crucial efforts of a committed collective responsible for its upkeep. This team consists of facility management professionals, including managers and maintenance workers, who are instrumental in maintaining the seamless function of the premises.
The roles within this group are distinct yet complementary. Facility managers contribute and focus on strategic aspects in orchestrating teams, formulating preventive maintenance programs, allocating work priorities, and communicating with higher-level executives.
On the operational side, facility managers handle various maintenance demands, such as equipment maintenance, cleaning schedules, building-specific equipment, and even parking lots, while upholding uniform quality standards through established protocols.
Facility Managers: The Strategists Behind Efficient Operations
Source: Eptura
Facility managers are commonly recognized as the masterminds who streamline operational efficiency within an organization’s physical premises. They are the nerve center of the operation and orchestrate the various requests related to facility maintenance.
Part of a facility manager’s job is property maintenance for commercial and residential buildings. They manage a diverse maintenance team that includes employees and outside contractors. They are also responsible for ensuring that building systems run smoothly and repair requests are routed efficiently to various technicians.
Their duties also encompass maintaining a safe and healthy environment for staff members and guests. This is achieved through regular inspections, evaluating potential risks, and consistently training employees.
In addition to safeguarding individuals on-site, these professionals leverage advanced space planning techniques to improve space use while supporting adaptable working arrangements.
Facility managers also must comply with municipal ordinances, construction regulations, warranty stipulations, and permit requirements to uphold standards in commercial upkeep.
Maintenance Technicians: The Frontline of Upkeep
Source: Get Reskilled
A maintenance technician is crucial for ensuring the smooth operation of a facility by engaging in preventive maintenance. This entails regular inspections and upkeep to keep HVAC systems and other capital assets functioning properly.
To carry out these preventative measures, their responsibilities extend to addressing particular problems that arise, such as repairing leaks, swapping out electrical outlets, or painting corridors.
The daily efforts of these technicians are essential not only for uninterrupted functionality but also to help sustain an agreeable work atmosphere within the building.
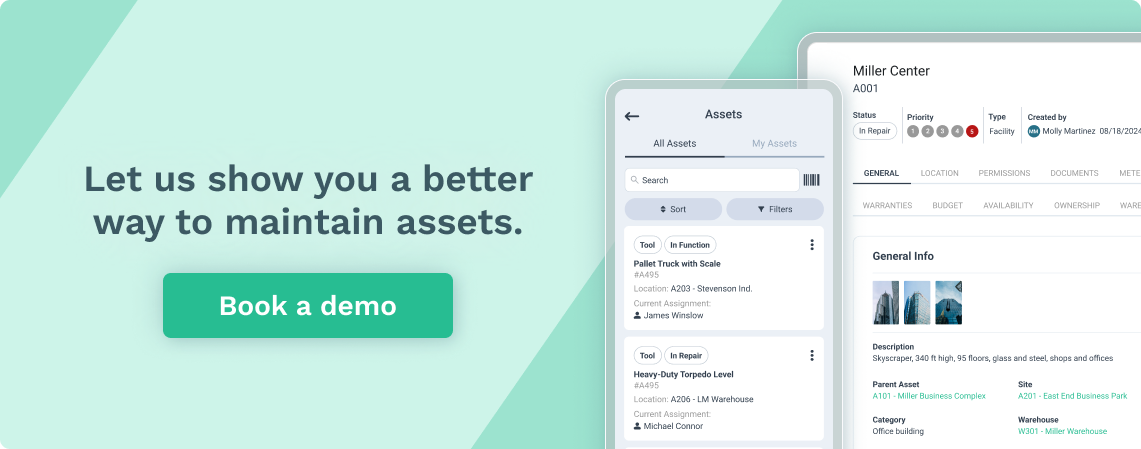
Supporting Roles: Security Personnel and Cleaning Staff
A facility management team is bolstered by including security staff and janitorial workers. The security officers safeguard the premises through regular patrols and keeping a vigilant eye on surveillance cameras.
Meanwhile, custodial employees are tasked with upkeeping the internal environment of buildings by dusting, scrubbing, and waxing floors, sterilizing restrooms, refilling supplies for occupants, and cleaning surfaces that are frequently handled.
Together, these groups play an essential role in fortifying safety measures within the facility. Their collective work guarantees a secure atmosphere conducive to safe operations for everyone present.
Source: WorkTrek
Specialized Maintenance for Different Building Types
Various types of buildings, each designed for specific uses, require tailored maintenance strategies. Hospitals, restaurants, schools, warehouses, gyms, hotels, office buildings, and manufacturing plants require different upkeep approaches.
Facility managers tailor their strategies accordingly and may employ building information modeling technology to manage maintenance needs better while optimizing space usage and energy efficiency.
This is a common practice among members of the International Facility Management Association.
Maintenance activities can be categorized in several ways:
- For residential spaces: Homeowners or landlords typically fund tasks that include carpentry work, plumbing services, home renovations, and fixing household appliances.
- For commercial buildings: There’s an emphasis on maintaining critical office equipment and HVAC systems to uphold a professional environment within structures like hotels or museums.
- Property upkeep: It’s about merging residential with commercial maintenance services according to the requisites of property owners or facility managers.
- For industrial facilities: The focus is preserving capital assets essential for production processes in manufacturing, mining, or packaging operations.
Commercial Buildings: Maintaining a Professional Atmosphere
The practice of building maintenance encompasses more than basic functions like lighting and air conditioning in commercial structures. It involves diligent preservation activities that create and maintain a professional atmosphere.
This requires maintaining internal components such as HVAC systems and elevators and conducting repairs on items such as drywall and electrical installations.
Additionally, it involves attention to the building’s aesthetics, ensuring that spaces are functional, presentable, and conducive to the activities they host. Regular checks and maintenance of plumbing systems, lighting fixtures, and security infrastructure are also part of the comprehensive care that commercial buildings require. These efforts create a safe, reliable, and pleasant environment for occupants and visitors alike.
In commercial facilities, maintenance activities are prioritized based on their urgency. Critical emergency repairs are prioritized to ensure continuous operations, while less critical maintenance can be scheduled later. This prioritization is crucial for maintaining the facility’s seamless functioning.
For complex maintenance chores, specialized contractors with proficiency in construction and building management are called upon.
Industrial Maintenance: Keeping Production Lines Running
Maintenance in industrial environments involves complex demands, necessitating the upkeep of various components such as:
- Essential capital assets
- Industrial machinery
- HVAC systems
- Various other infrastructural systems
Ongoing maintenance, proactive preventive measures, and forward-looking predictive strategies should be employed to address these needs. The goal here is to avoid poorly maintained assets and keep everything running.
The overarching objective is more than just operational functionality. It aims at achieving peak performance through:
- Minimizing periods when equipment is non-functional
- Streamlining production workflows
- Enhancing productivity rates within manufacturing operations
- Reducing expenses tied to running facility assets
- Upholding stringent safety standards for workforce welfare
- Improving the lifespan of capital assets
Adopting appropriate maintenance methodologies enables industrial plants to meet these ambitious targets successfully.
Healthcare Facilities: Precision in Upkeep for Medical Equipment
Source: Intellis
Within healthcare, facility maintenance has elevated importance due to the need for meticulous upkeep of medical equipment.
This is crucial not only for safeguarding patient health but also for adhering to strict regulatory standards. Preventive maintenance becomes imperative to reduce periods when equipment is out of service and avert potential functional failures that could endanger patients.
Maintaining medical equipment can be complex and requires those responsible for maintaining this sophisticated equipment to have specific training and qualifications. Some advanced machinery requiring skilled attention are:
- MRI scanners
- CT scanners
- X-ray machines
- Ultrasound machines
- Dialysis units
- Respiratory ventilators
- Certain office equipment
To ensure these instruments function with the highest precision—a crucial element in patient diagnosis and treatment—they must be subject to consistent, meticulous calibration and regular performance evaluations to uphold their operational excellence.
This rigorous process is vital in healthcare, where even the slightest deviation or malfunction could have significant consequences. Regular maintenance checks conducted by certified technicians ensure that these sophisticated devices operate within their specified parameters.
These procedures often involve mechanical adjustments, software updates, and checks against the latest medical standards to ensure ongoing accuracy and reliability. The goal is to maintain the integrity of these medical devices so that healthcare professionals can rely on them to deliver accurate information, which is the cornerstone of quality patient care.
Facility Management Software: A Tool for Efficiency
Incorporating facility maintenance software in facility management has become pivotal. There are several advantages:
- Automating preventive maintenance schedules
- Monitoring the status and repair history of equipment
- Optimizing maintenance operations for better workflow
- Enhancing overall efficiency
- Minimizing manual mistakes
- Outlining safety protocols for maintenance technicians
- Improving building maintenance
- Seamlessly communicating with facility maintenance professionals
Adopting this type of software enables a methodical and productive strategy for managing asset lifecycles and preparing financial plans for preventive upkeep.
Organizations that integrate such maintenance software into their current systems can refine their processes even more while guaranteeing data precision.
Features of Facility Maintenance Software
Various functionalities that enhance and simplify maintenance operations are encompassed within facility maintenance software, a specialized branch of facility management software. Its capabilities cover:
- Efficient tracking and administration of assets
- Streamlined scheduling and oversight of maintenance activities
- Improvement in the utilization of space
- Strengthening adherence to safety standards and regulatory compliance
Contemporary maintenance software brings several advantages into play:
- Employing data analytics alongside machine learning techniques to automate routine tasks
- Sharpening the management strategies for asset performance
- Informing decisions about repairs or replacements with robust data insights
- Extending the operational lifespan of assets
- Enabling technicians to use mobile devices to track their requests
By integrating communication tools, facility maintenance software bolsters productive exchanges between team members and other involved parties, thereby increasing the productivity of the entire spectrum of maintenance processes.
Choosing the Right Maintenance Software
Source:WorkTrek
With so many options on the market, selecting the most suitable maintenance management software can be overwhelming. Organizations can streamline this process by identifying their unique needs and examining choices such as Integrated Workplace Management Systems (IWMS), Computerized Maintenance Management Systems (CMMS), or Enterprise Asset Management (EAM) software that provides functionalities tailored to their operational demands.
When choosing a maintenance management system, it’s essential that it:
- Supports scaling in line with organizational growth
- Offers customizability to align with specific facility procedures
- Is intuitive for staff use to ensure widespread uptake
Critical steps in selecting vendors include checking their credibility, looking for reviews from current users, and understanding the entire cost of ownership, including initial purchase price, ongoing maintenance fees, and any necessary training expenses. Taking advantage of trial offers is beneficial when making an educated choice.
The Impact of Regular Facility Maintenance
Adherence to maintenance schedules for regular facility upkeep is crucial. Such maintenance ensures a reduction in the risk of equipment failures and system downtimes, thereby facilitating:
- Consistent business operations
- Enhanced production efficiency
- Lower operational expenses
- Optimum performance of production facilities
- Smooth functioning of machinery.
Maintaining rigorous schedules for routine facility maintenance is critical to compliance with safety systems and guarantees dependable business operations during unexpected incidents.
Setting up benchmarks for equipment performance is instrumental in managing its efficiency and contributes to extending asset longevity through planned maintenance measures.
Extending Asset Longevity Through Proper Upkeep
Consistent upkeep and care of facilities through preventive maintenance significantly contribute to the prolonged use of equipment. Ensuring regular cleanliness, proper lubrication, and timely replacement of worn-out components helps prevent machinery malfunctions and promotes increased asset longevity.
This enhancement in an asset’s life is crucial for supporting operational effectiveness and achieving cost savings across different sectors.
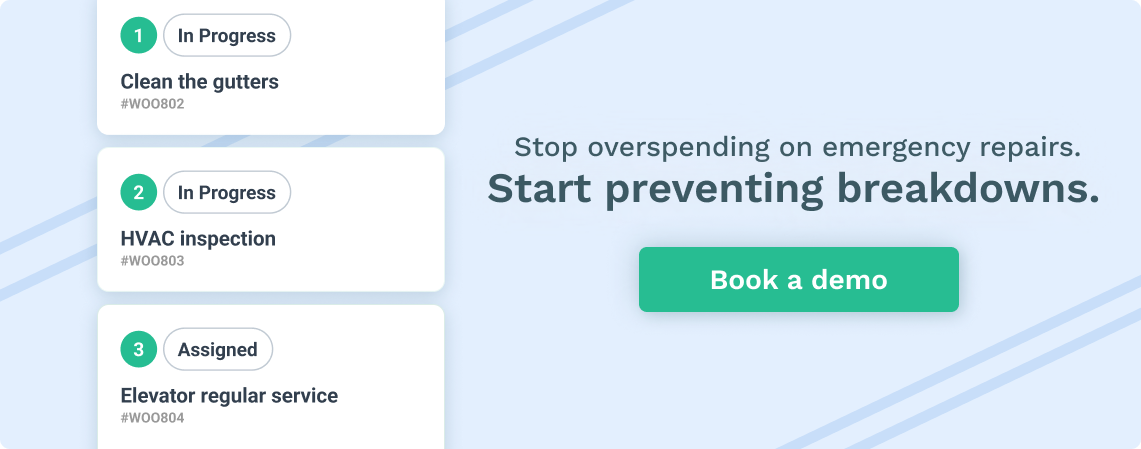
Companies can reap several advantages by prioritizing proper maintenance, leading to extended asset service life.
- Continuous and dependable business operations
- Maximization of operational productivity
- Reduction in expenses associated with both maintaining existing assets and acquiring new ones
- Elimination of downtime due to breakdowns
Implementing a systematic approach to regular maintenance and preemptive attention to asset care is vital in attaining these advantageous outcomes.
Mitigating Risks with Fire Safety and Security Measures
Ensuring a facility’s safety and security is an expansive task beyond keeping day-to-day operations running smoothly. It’s about creating a secure and protected environment for all occupants.
Facility managers are responsible for rigorously testing and inspecting fire safety systems to ensure they function correctly and meet safety standards while maintaining records demonstrating compliance with safety regulations.
Regular maintenance is crucial to prevent accidents and avoid the need for expensive emergency repairs in commercial properties.
Adhering strictly to building regulations and safety codes is fundamental to maintaining these structures, ultimately securing a protected setting for everyone inside.
Source: Team Safety Services
Business Continuity Planning: Preparing for the Unexpected
Business continuity planning is an indispensable aspect of facility maintenance, designed to ensure that a company’s operations can persist through unforeseen disruptions such as emergencies, natural disasters, or significant equipment breakdowns.
As a critical component of this contingency strategy, the facility management team is responsible for ensuring the seamless transfer of business functions to a designated alternative location for operations.
A thorough and multifaceted approach encompasses various elements that prepare a company to maintain its operational functions during challenging situations.
Innovations and Trends in Facility Maintenance
In the dynamic world of facility management, there’s a noticeable shift as cutting-edge trends and technological innovations shape its future. Embracing green practices in facility operations is becoming more common, reflecting a dedication to environmental stewardship and a push toward sustainable practices.
Facility maintenance software is being enhanced with analytics and reporting features that enable detailed operation monitoring and informed strategic planning.
Emerging applications of virtual reality (VR) and augmented reality (AR) are revolutionizing how facility data can be interacted with—improving collaboration during meetings, increasing safety through hazard simulation, and enriching the visualization of spatial information.
Sustainability Initiatives in Facilities
Source: Resonai
A significant trend in facility management is the shift towards embracing sustainability. Smart buildings, now enhanced with Internet of Things (IoT) technologies, allow for real-time, adaptive management of environmental factors and system operations. This approach improves operational efficiency and reduces energy consumption, marking a step forward in sustainable facility management practices.
Facility management teams are progressively adopting IoT-powered HVAC systems that promote energy-efficient temperature regulation—key to their commitment to sustainable practices.
These systems enable precise control and oversight of energy use, ensuring compliance with environmental best practices and adherence to green regulatory requirements.
Energy Efficiency: Optimizing HVAC Systems and Lighting
Source: Perth Air & Power Solutions
Advanced HVAC systems embrace energy efficiency by integrating IoT technologies to decrease environmental impact and operational costs. This move towards smarter energy use is key to achieving cost-effective and environmentally conscious solutions for heating, ventilation, and air conditioning.
Predictive maintenance uses large data sets, monitoring, machine learning, and data analysis to anticipate system breakdowns before they happen. This optimizes energy utilization and plays an essential role in reducing expenses associated with unexpected repairs or downtime.
Summary
In summary, the complex field of facility maintenance is essential in maintaining a building’s safety, operability, and visual appeal. It encompasses everything from routine daily care to strategic planning critical for business continuity, underpinning operational effectiveness.
With the advancement into an increasingly digital era, groundbreaking developments like IoT (Internet of Things), AI (Artificial Intelligence), and efforts towards sustainability are continually transforming facility maintenance into a progressive and changing domain.
Frequently Asked Questions
What is facility maintenance?
Facility maintenance involves diligently caring for and managing a building’s physical assets, systems, and outdoor areas to optimize the facility’s functionality, safety, and efficiency. This encompasses routine maintenance regimen, urgent corrective actions, and the strategic organization of maintenance operations.
What roles do facility managers and maintenance technicians play?
Facility managers oversee strategic tasks and management teams, while maintenance technicians perform preventive and corrective tasks to maintain continuous facility operation.
How does facility maintenance software help in managing maintenance tasks?
Maintenance software designed for facilities assists in organizing maintenance duties by automating task scheduling, monitoring equipment state, and optimizing operational processes. This results in enhanced productivity and a decrease in human errors.
What is the importance of regular facility maintenance?
Maintaining facilities regularly is crucial to minimizing the chances of equipment breakdowns, ensuring seamless operations, enhancing production efficiency, and lowering operational expenses.
What are some of the latest trends in facility maintenance?
Current movements in facility management are steering towards integrating eco-conscious methodologies, implementing HVAC systems enabled by IoT for enhanced energy conservation, and applying analytical tools and reporting functions within maintenance software to monitor performance metrics and aid in informed strategic planning.
Such trends underscore an increasing focus on environmentally sustainable options and reliance on empirical evidence for facility management decisions.