Get a Free WorkTrek Demo
Let's show you how WorkTrek can help you optimize your maintenance operation.
Try for freeKey Takeaways:
- OSHA fines can reach up to $16,550 per violation.
- Companies save hundreds of thousands of dollars annually by using a CMMS.
- Experts say proactive maintenance is about three times more cost-effective than reactive maintenance.
Unplanned breakdowns aren’t just inconveniences.
In manufacturing, every minute of downtime costs money, delays production, and disrupts efficiency, harming the overall profitability and even the reputation of your plant.
Fortunately, a Computerized Maintenance Management System (CMMS) can help minimize these disruptions.
A CMMS digitizes and automates maintenance processes, bringing order to chaos, boosting data accuracy, and maximizing uptime.
Read on to learn how to use CMMS software effectively and keep your plant running at peak performance.
Work Order Management
CMMS software optimizes creating, tracking, and completing work orders within your plant, boosting the entire team’s efficiency.
Supervisors can easily assign work and monitor progress in real-time, while technicians gain access to all the crucial information they need to complete their tasks properly.
One key advantage of CMMS software is its customizable work order templates with required fields.
They significantly reduce the risk of incomplete information and errors.
For example, with our own CMMS, WorkTrek, you can capture essential work order data such as required labor, parts, expenses, signatures, and more, as shown below:
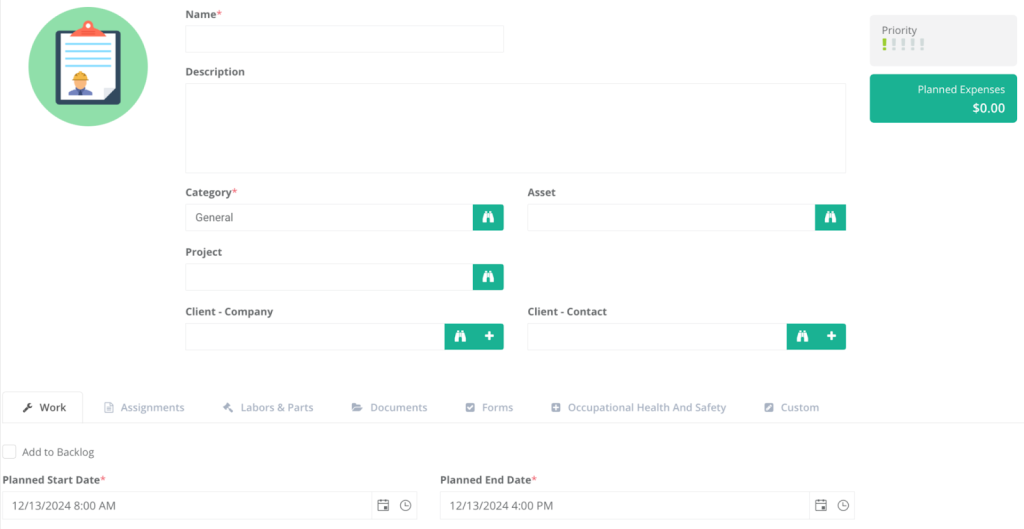
Step-by-step instructions, photos, and other important documents can also be attached to expedite problem resolution further.
Once the work is complete, you can access reports on WO costs, efficiency, and more.
This enables you to quickly identify areas for improvement and plan future maintenance more effectively.
Below, you can see WorkTrek’s dashboard with crucial WO insights:
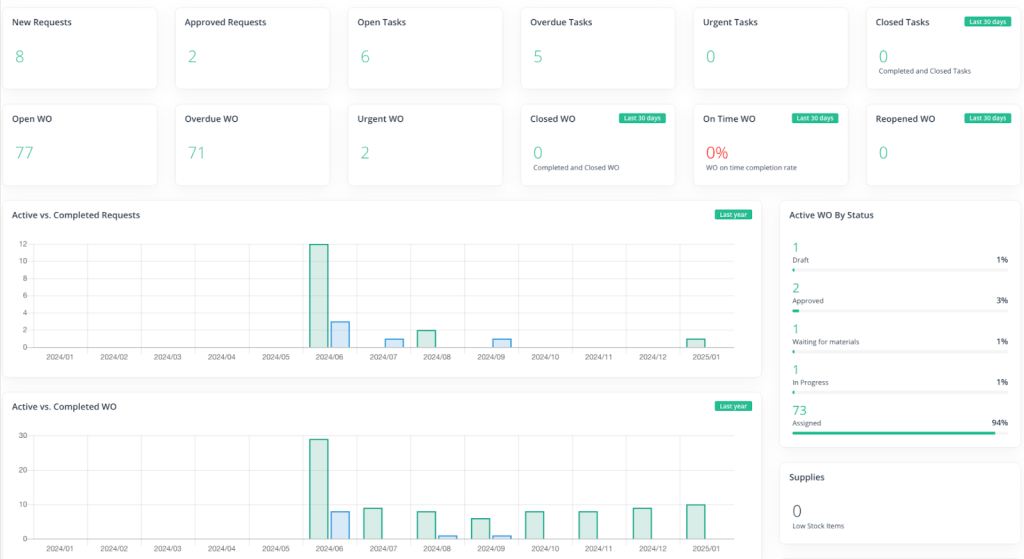
Imagine the alternative: stacks of paperwork, constant trips between the office and the job site, and confusion over who’s responsible for what.
That’s time wasted, and money lost.
With WorkTrek, however, everything is digital and accessible on the go.
Miller Milling, which produces flour for consumers and food service customers, has experienced the struggle of paper-based work orders.
Due to this inefficient system, their daily lives were riddled with issues like lost information, difficulties monitoring task completion, and delays.
With CMMS, all that finally changed, says Alisha Bibriesca, Facility & System Administrator at Miller Milling Company:
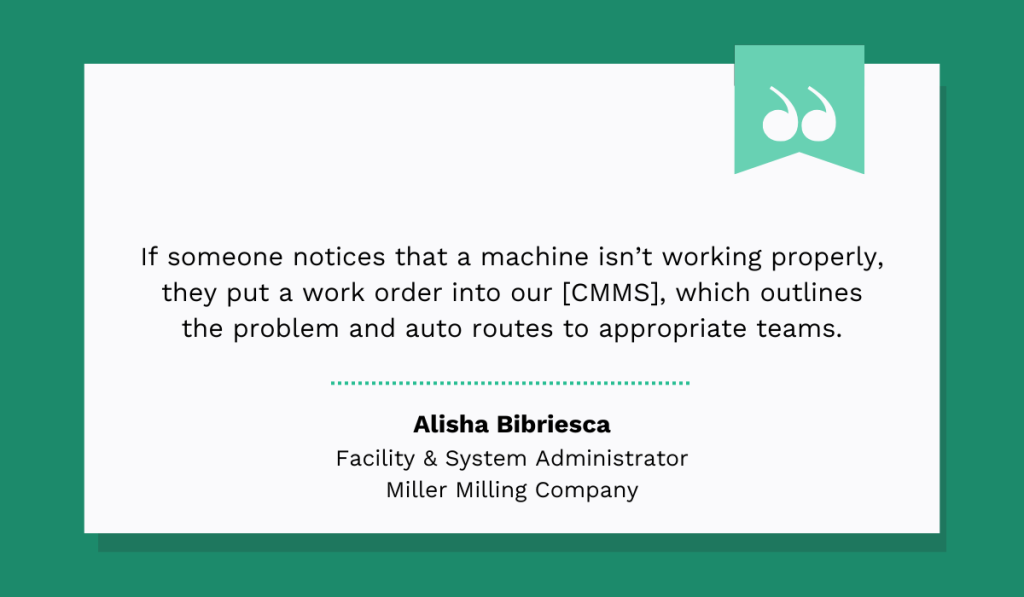
Now, Miller Milling can prioritize tasks more effectively, capture vital data, and ensure work is completed on time.
Examples like this show how CMMS, with its automated work order management, brings more order, accountability, and efficiency to plant maintenance.
It makes it easier to know what needs to be done, when, by whom, and how, leaving no room for error.
Preventive Maintenance Scheduling
If you’ve been struggling to shift from reactive maintenance to a more proactive approach, a CMMS could be the solution you’ve been looking for.
This kind of software automatically schedules tasks based on various triggers, sends alerts for upcoming maintenance, and makes overall planning much easier.
As a result, you’ll see fewer unexpected failures and less downtime.
You can schedule maintenance based on time triggers, ensuring tasks repeat daily, weekly, monthly, or annually, depending on your needs:
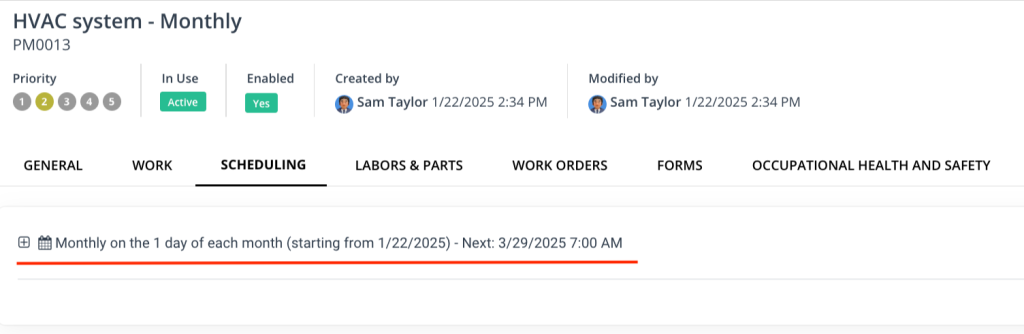
CMMS gives you full control here.
You can set start dates, define end rules (by a specific date or number of occurrences), determine how far in advance WOs should be created, and more.
Leading maintenance scheduling CMMS platforms also support meter-based triggers.
You can schedule inspections or services based on specific usage metrics such as operating hours, mileage, temperature, or pressure.
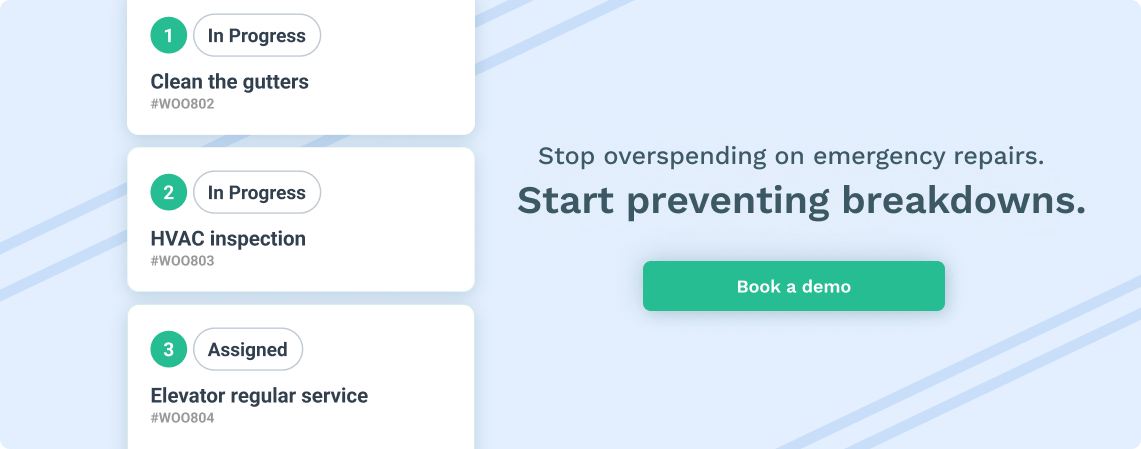
Reading thresholds, conditions, planned durations, and end rules can all be defined, just like in the example below:
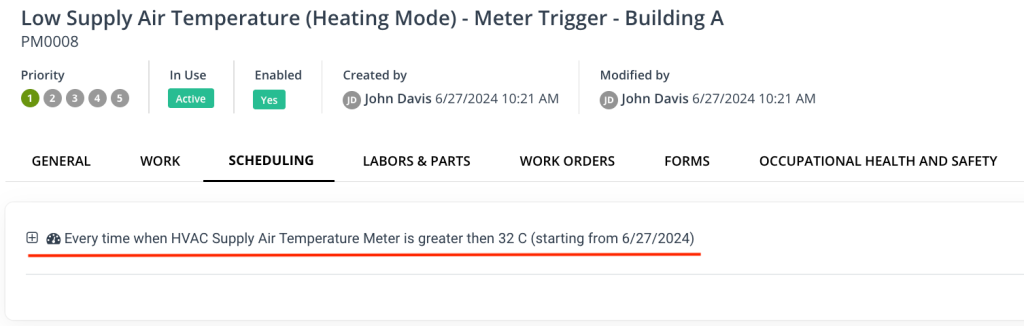
Consequently, each asset receives the specific care it requires, staying in good condition longer and minimizing unexpected breakdowns that could disrupt production.
Zach Williams, Engineering Manager at Kito Crosby Australia, an industrial equipment supplier specializing in custom hoists and lifting solutions, agrees:
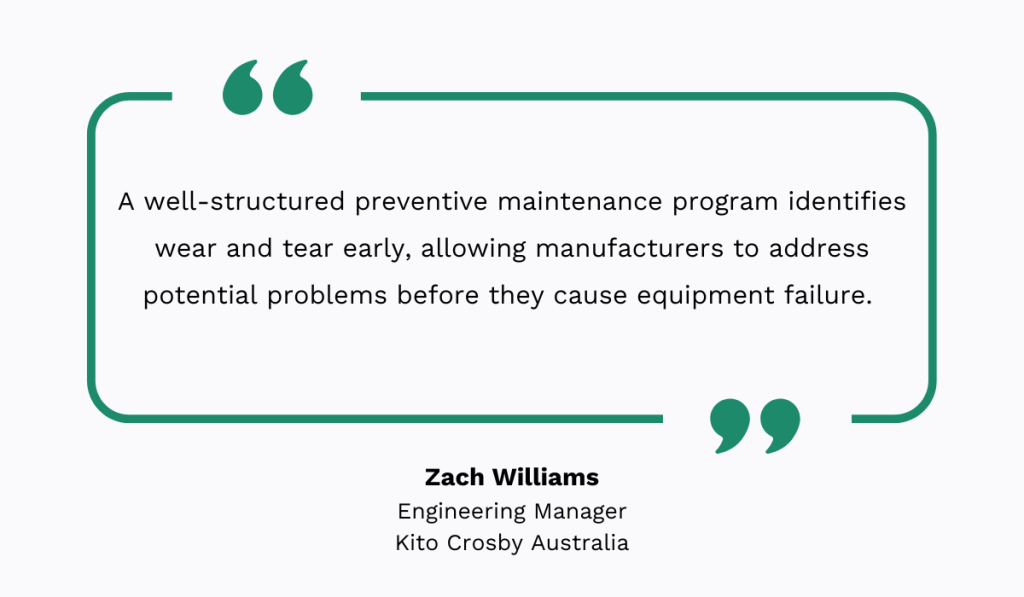
This not only boosts the efficiency of a plant’s operations but also has a direct impact on the bottom line, Williams adds:
“Proactive maintenance is nearly three times more cost-effective than reactive maintenance.”
In other words, preventive maintenance pays off—but only if you have the right system to manage it.
That’s where a CMMS comes in, automating scheduling, sending reminders, and ensuring no task is overlooked.
Regulatory Audits
The core function of any CMMS software is to document maintenance activities and centralize all crucial information in one place, keeping the records complete, accurate, and up-to-date.
As shown below, you can quickly check when an asset was last serviced, what was done, and who performed the task:
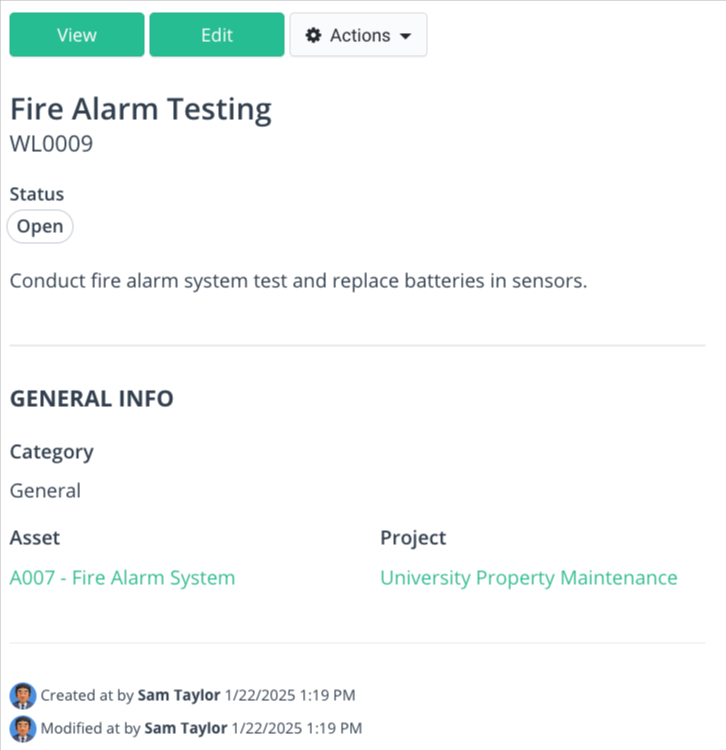
For manufacturing plants operating under strict regulations, this is extremely valuable.
It allows them to easily and quickly demonstrate compliance during regulatory or internal audits, helping avoid hefty fines, penalties, and reputational damage.
Whether you’re preparing for an SQF, EPA, or OSHA inspection, a CMMS will eliminate the need to sift through files for hours or scramble to find missing paperwork.
Instead, all audit-related documents and reports are neatly organized, easily accessible, and ready at a moment’s notice.
Troy Design & Manufacturing, a manufacturer of high-quality automotive prototypes and stamping, leverages a CMMS for this exact purpose.
Bill G., their Facilities Manager, explains how the platform provides unparalleled visibility, significantly simplifying audits:
Audits are stressful enough without adding extra complications.
A CMMS ensures you have everything at your fingertips, eliminating the chaos, guesswork, and headaches.
Since OSHA fines can reach up to $16,550 per violation, having such a well-organized system is helpful and an absolute must-have.
Asset Management
A CMMS tracks the entire asset lifecycle—from procurement to disposal—providing insights into your tools and equipment’s performance, health, utilization, and depreciation.
With this information, you can optimize asset usage, improve resource allocation, and maximize ROI.
Think of a CMMS as your plant’s central command center for asset data.
Everything from physical locations and warranty details to complete maintenance history and expenses can be accessed anytime and anywhere:
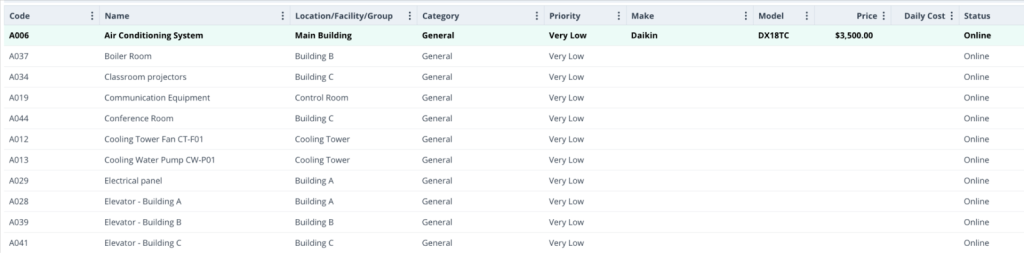
This allows your technicians to check an asset’s availability, whereabouts, or inspection status at a glance.
Moreover, you gain deeper insights into asset performance with CMMS’s built-in reporting and analytics.
For example, you can access reports on warranty expirations, utilization, downtime, production losses, and more, all in mere moments.
Below, you can see one such report:
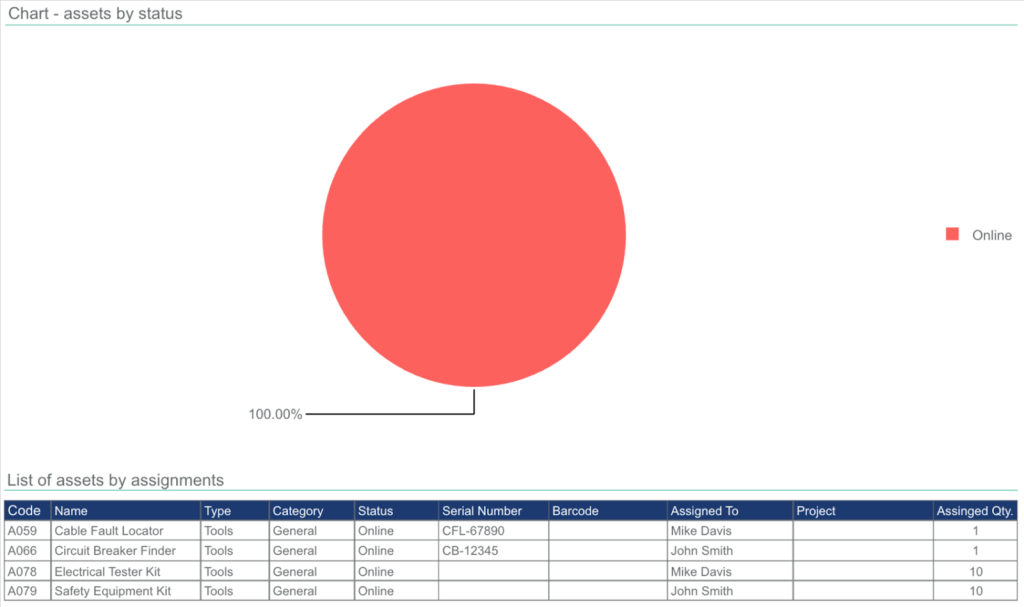
At Cloeren Inc., a global leader in plastics manufacturing, they understand how valuable data-driven decisions can be.
Their Maintenance Administrator, Holly Tullos, explains:
She adds that, with a recent influx of new machinery, each with its unique data, the CMMS helped them finally “catch up with what they have,” organizing all that information in one place.
In fact, the system has even helped justify new equipment purchases—which are often delayed due to cost concerns.
At the end of the day, asset management isn’t about hunches but about hard data.
With a CMMS, every decision is rooted in reality, driving efficiency, cost savings, and long-term success for the entire plant.
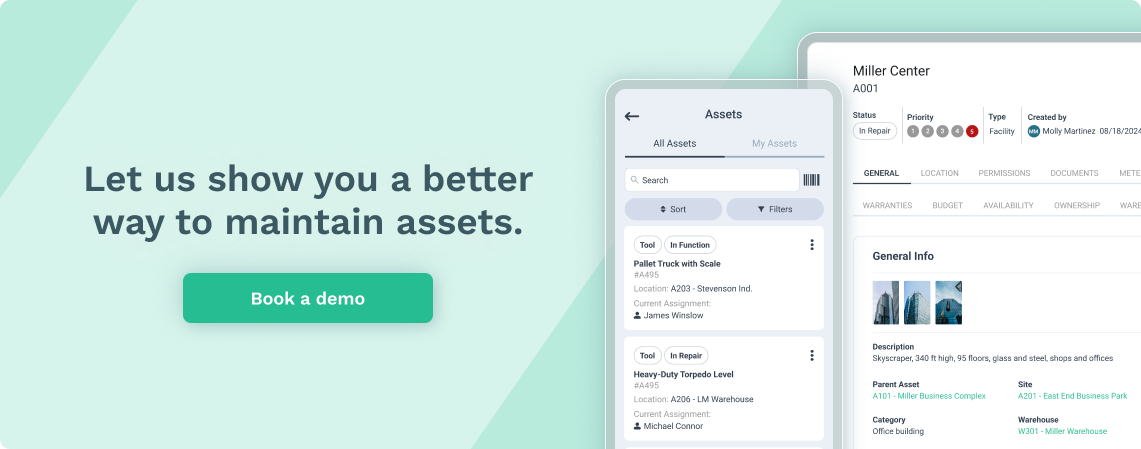
Spare Parts Tracking
In addition to your assets, CMMS software helps manage the inventory needed to perform maintenance on those assets.
More specifically, it does the following:
- Automatically monitors spare part levels.
- Lets you set reorder points.
- Sends alerts when stock is running low.
This ensures continuous parts availability while simultaneously reducing costs by preventing over-purchasing.
Just like with fixed assets, a CMMS keeps a detailed record of spare parts, including their make, model, location, quantity, user manuals, and more, as shown below:
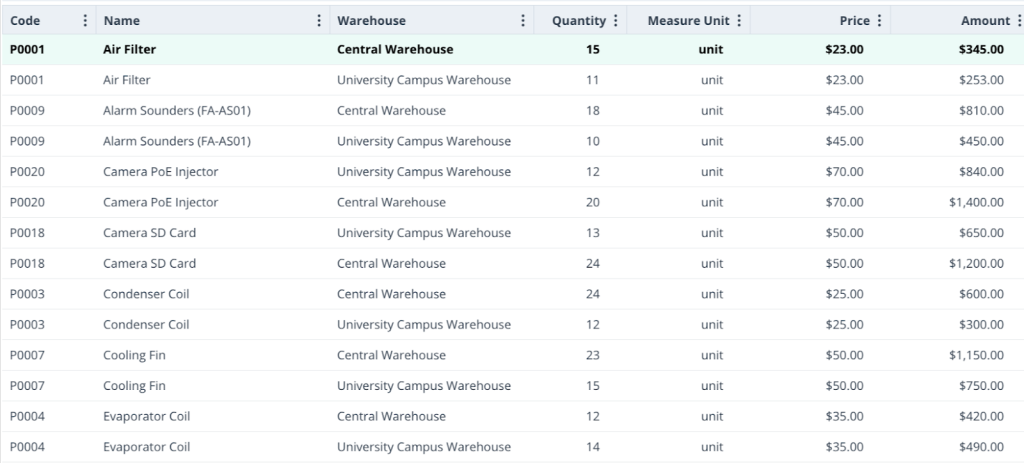
This allows you and your team to easily access all relevant information, update stock levels, and transfer inventory between warehouses on the go.
Additionally, the software provides thorough reports on low-stock items, parts consumption per asset, and other key metrics, helping you identify trends and inefficiencies driving up costs.
A 2025 RS & CIPS report shows a growing need for systems with such capabilities, with 62% of companies across all industries reporting inflation as their biggest challenge.
At the same time, 60% have reduced their operational budgets, while 40% report the need to cut inventory costs.
In other words, modern businesses must find ways to do more with less.
With rising costs and pressure to reduce expenses while maintaining high-quality work, the challenge has never been greater.
Fortunately, a CMMS with automated inventory tracking ensures that every material and spare part is used efficiently.
It helps maintain just the right amount of stock—not too much, not too little—keeping production running smoothly and cost-effectively.
As a maintenance professional, you’re aware that inventory expenses are unavoidable.
But with a CMMS, you can ensure every dollar spent is justified and strategically allocated.
Maintenance Cost Analysis
With its powerful reporting and analytics features, a CMMS can track labor, parts, and other maintenance costs, helping you identify inefficiencies and cost-saving opportunities.
For example, a report like the one below could reveal high-maintenance assets that are more cost-effective to replace than repair or highlight over-purchasing of spare parts that go unused.
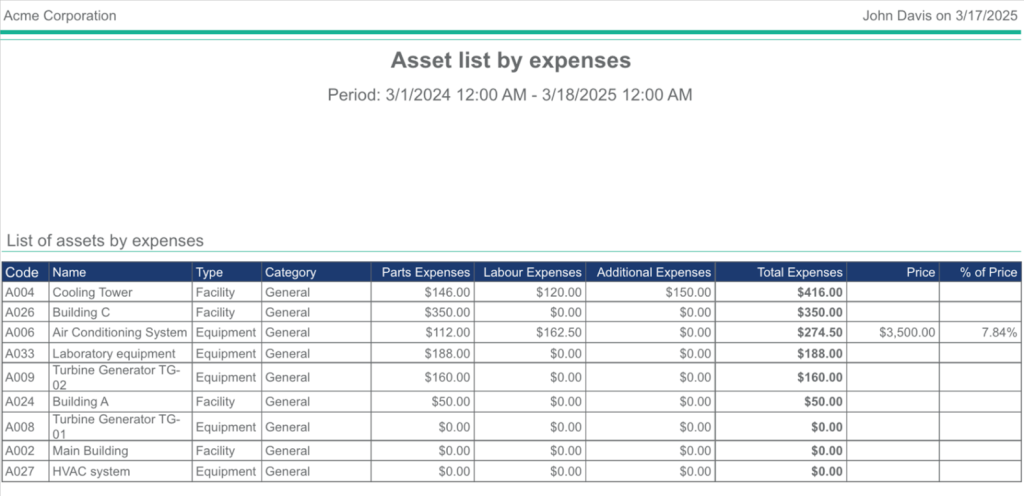
These inefficiencies can quietly drain your budget without a transparent system to gather and analyze maintenance data.
Robert Peffen, Director of Asset Performance Excellence at Implementation Engineers, puts it best:
“One of the most effective ways to control the maintenance budget is to identify and eliminate recurring reliability and maintenance problems. To accomplish this, the data on maintenance work performed must be collected and analyzed.”
In other words, you can’t fix what you don’t track—and you need a CMMS for effective tracking.
Take Johnson & Johnson’s Centocor/Global Biologics Supply Group, a manufacturer of a key biopharmaceutical ingredient used in the drug Remicade.
Their CMMS collects and monitors various data, such as instrument calibration, maintenance schedules, costs, and spare parts usage.
Those insights enable them to make quick, data-driven improvements, leading to significant cost savings:
- The initial CMMS investment was paid back in under two years.
- Increased equipment reliability led to $1.3 million in savings in Year 1 and $1.1 million in Year 2.
- Productivity at the facility rose by 30%, leading to ongoing annual savings of $300,000.
Yes, all of these improvements were driven by one thing: reliable, actionable data.
With an efficient CMMS and data-driven cost analysis, you too can unlock such benefits.
Conclusion
CMMS software improves every aspect of maintenance operations.
Whether you want to streamline work order processes, centralize inventory data, or reduce costs, this system can make a significant difference in your manufacturing plant.
It delivers unmatched transparency, data accuracy, and process efficiency, taking the guesswork out of maintenance—so you can keep your assets performing at their best.