Get a Free WorkTrek Demo
Let's show you how WorkTrek can help you optimize your maintenance operation.
Try for freeKey Takeaways:
- CMMS solutions help streamline and improve entire maintenance operations
- A typical industrial business loses $125,000 an hour due to unplanned downtime
- Due to labor shortages, maintenance personnel struggle to perform their tasks properly.
The manufacturing industry relies heavily on a wide range of machinery and equipment, making maintenance an essential component of its operations.
Safety, efficiency, and bottom lines take a significant hit when this is neglected.
And yet, maintenance often doesn’t receive the attention it deserves, whether due to competing priorities or a lack of knowledge.
This article aims to address the latter.
On this page, you’ll find a detailed overview of everything you need to know about manufacturing maintenance: from the basics of different maintenance types to the latest technologies shaping the field.
Let’s get started.
How Manufacturing Maintenance Changed Through Times
In its early stages, maintenance was primarily corrective—focused on fixing problems as they arose.
This worked well for a time.
But then, significant historical events like the Industrial Revolution and World War II brought about new developments and inventions, changing our maintenance needs as well.
At that point, a more proactive approach was needed to prevent serious equipment damage before it impacted operations. This forever changed the way maintenance is perceived and performed.
In the 1980s, digitalization began to reshape manufacturing maintenance even further.
Many new technologies were introduced, and Computerized Maintenance Management Systems (CMMS) started gaining more traction.
Fast forward to today, and we can access technological solutions that our predecessors could never have imagined.
With sensors, data analytics, and the Internet of Things (IoT), we can create smart systems that can predict equipment failures before they even happen.
The timeline below illustrates the history of manufacturing maintenance from its inception to the present day.
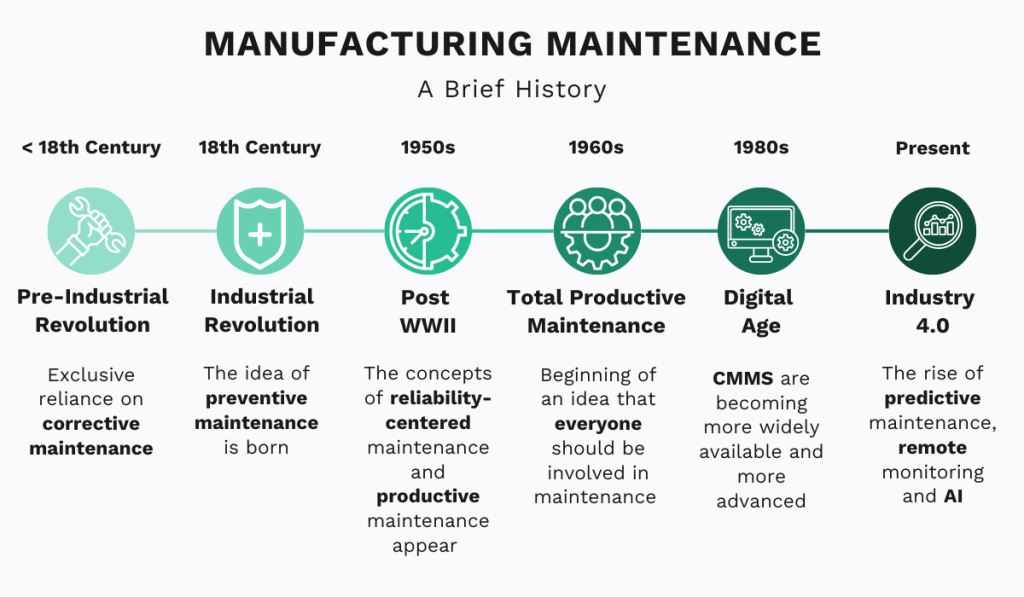
So, in just a few short decades, manufacturing maintenance has grown from a simple “fix it when it breaks” mindset to a high-tech, data-driven field.
It’ll be exciting to see what else the future has in store.
Key Objectives of Maintenance in Manufacturing
Of course, the ultimate objective of maintenance is to save money in the long run.
However, this can be achieved by focusing on several specific goals.
First and foremost, maintenance aims to prevent costly, unplanned downtime.
When a key piece of equipment suddenly stops working, it costs you differently, from lost production time and increased labor costs to missed delivery deadlines.
A 2023 ABB survey revealed that an hour of unscheduled downtime costs a typical industrial business a shocking $125,000.
And even more shocking is that 69% of plants experience this problem at least once a month.
This is where well-planned upkeep comes into play.
If routine tasks like lubrication, calibration, and inspection are performed regularly, minor problems will likely be caught and fixed before they snowball into severe operational disruptions.
Similarly, maintenance ensures that production capacities stay at optimal levels.
This is important because a decrease in production capacity can lead to unnecessary expenses, bottlenecks in productivity, and reduced profitability.
Fabio Camargo de Oliveira, Technical Assistance and Services Manager at Wenger, an industrial equipment supplier, illustrates the impact of this issue with an example:
For example, if an extruder in good condition that usually produces 10 tons per hour—consuming approximately 25 kw per ton, [suddenly starts to produce] 7 tons per hour—consuming 32 kw per ton—it will spend more electricity, water, and steam due to wear and difficulty in stabilization, ultimately producing less and decreasing the manufacturer’s profit.
The problem is that, unlike downtime, you may not immediately notice a slow decline in production capacity, but only when it’s already started to harm your bottom line.
However, with proper maintenance, this issue can be avoided entirely.
Beyond just keeping things running, maintenance also plays a role in ensuring a safe work environment. After all, properly maintained equipment is far less likely to malfunction and injure your employees.
This directly translates to fewer accidents and decreased costs associated with workers’ compensation, insurance premiums, legal liabilities, and productivity losses.
Did you know that, in the manufacturing industry, an average of 67 days are lost per injury?
That’s more than two months of missed work—no small matter.
When you add potential lawsuits, reputational damage, and lowered worker morale, the costs of neglecting equipment safety quickly increase.
Overall, the role of maintenance is very multifaceted. Many people aren’t even aware of just how impactful it can be.
It isn’t only about fixing broken assets—far from it—but about building a solid foundation for safe, profitable, and efficient operations.
Types of Manufacturing Maintenance (And When to Use Each)
There are many different types of maintenance used in manufacturing, each with its advantages, disadvantages, and ideal use cases.
Corrective or reactive maintenance, as the name implies, focuses on fixing problems after they have already occurred.
It often gets criticized for being ineffective in the long term, but there is a time and place for it—especially with non-critical assets.
Preventive maintenance, on the other hand, is a more proactive strategy.
It prioritizes frequent cleaning, parts replacement, and similar tasks to prevent unexpected failures and keep operational disruptions minimal.
According to the 2024 MaintainX survey, this is currently the most popular approach to asset upkeep, with 87% of respondents reporting its active use.
And why wouldn’t they?
It’s proven to minimize unplanned downtime, extend equipment lifespan, and keep operations running smoothly.
Condition-based maintenance is also proactive, but its implementation differs from a preventive strategy.
Preventive maintenance schedules tasks based on regular time intervals or usage (e.g., every three months, or after a certain number of operating hours).
On the other hand, condition-based focuses on servicing when particular indicators show signs of decreasing performance or potential failure.
This way, you’re only maintaining equipment when it’s actually needed and not just because the calendar says you should.
Another maintenance type that’s been gaining traction in manufacturing is predictive maintenance.
You can consider it the more advanced version of a condition-based method.
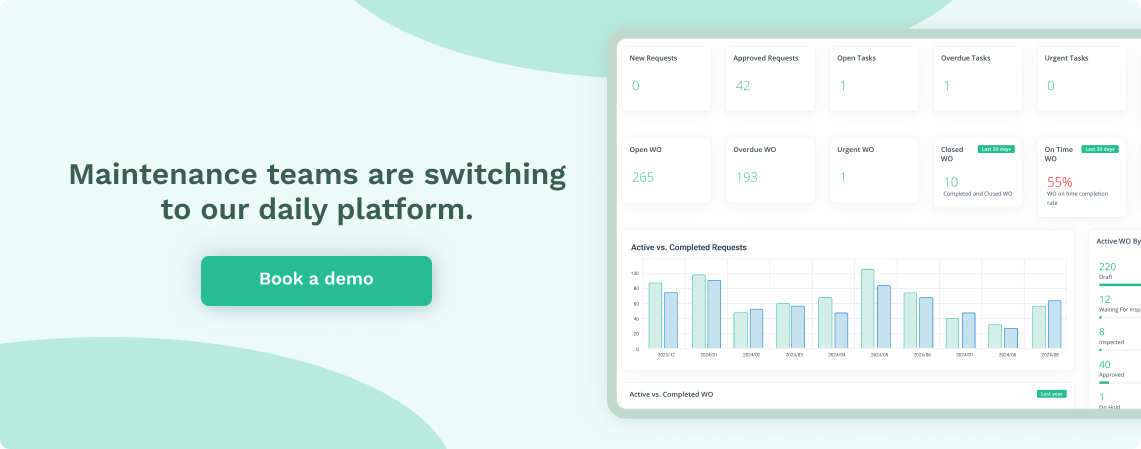
It uses data, various sensors, and analytical tools like machine learning to identify, detect, and predict equipment issues before they even occur.
Kevin Tucker, Advisory Practice Lead at the IT services and consulting company Info-Tech Research Group, explains why this is such a valuable addition to any upkeep plan.
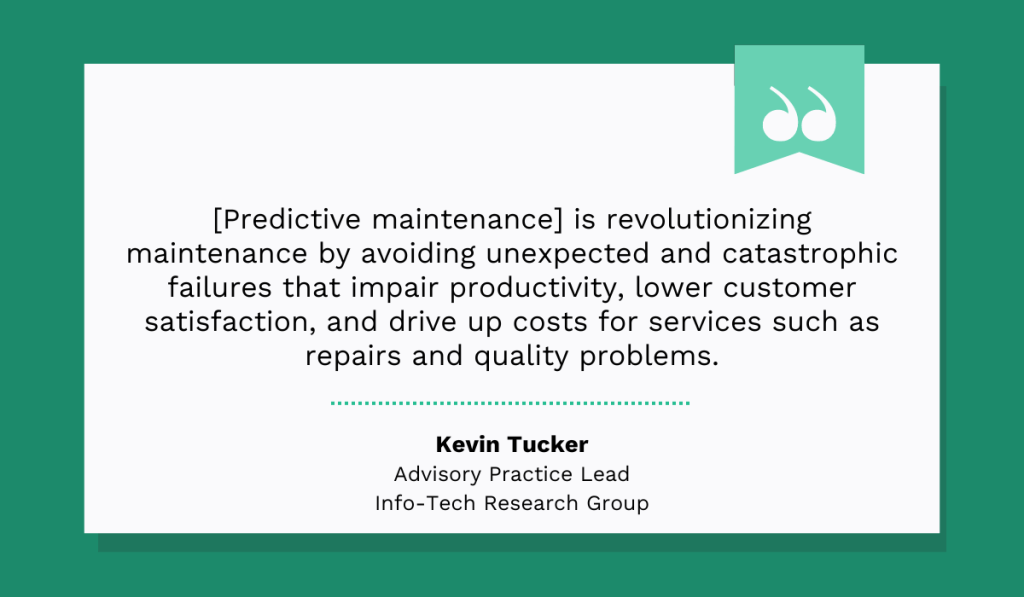
Lastly, Total Productive Maintenance (TPM) is the all-hands-on-deck approach that blends corrective, preventive, and predictive methods into one strategy.
The idea here is that everyone within the operations should take responsibility for daily service tasks, which helps detect problems earlier and reduces the likelihood of unplanned downtime.
Here’s a quick overview of all these types of maintenance:
Type | Pros | Cons | When to use |
Corrective | No upfront maintenance costs and minimal planning | If certain issues are overlooked, it can lead to unplanned downtime and more long-term costs | For non-critical assets and when replacement parts are easily accessible and repairs can be made quickly |
Preventive | Reduces the likelihood of unexpected equipment failure and increases equipment lifespan | Can lead to unnecessary maintenance and requires more manpower and resources for routine checks. | For critical equipment that would cause significant downtime if it failed |
Condition-based | Helps in planning upkeep activities without disrupting production and avoiding unnecessary maintenance | High initial costs for equipment and sensors, as well as challenging data management | When equipment has fluctuating loads and operating conditions |
Predictive | Reduces unnecessary maintenance by only performing maintenance when needed | High initial setup costs for sensors, monitoring equipment, and software.
Requires skilled personnel to analyze data and manage systems |
For critical equipment where downtime is very costly and when the needed technology is readily available and feasible to implement |
Total Productive Maintenance | Engages all employees, increasing accountability and leading to a culture of continuous improvement | Requires significant effort for training and a high level of commitment from all employees and management | Where the highest manufacturing standards and employee accountability are a priority |
So, which strategy should you implement? Which one’s the best?
The truth is, there is no one-size-fits-all solution.
Your choice of maintenance activities should be tailored to your organization’s and equipment’s specific needs.
In most cases, this means mixing and matching all of these approaches to create a maintenance plan that works for you.
Why Is Maintenance in the Manufacturing Industry So Challenging?
Any experienced manufacturing maintenance professional will tell you their job isn’t always easy.
In addition to being a complex process, maintenance is often faced with various outside challenges that make it even more difficult.
For starters, there’s a significant shortage of skilled workers.
According to an UpKeep survey, 72% of companies anticipate maintenance staff shortages and related issues in 2024.
The problem is that seasoned professionals are all retiring, but new talent is tough to come by.
At the same time, technology is evolving at lightning speed, and not everybody can keep up.
This leaves maintenance teams spread too thin, often without the expertise needed to maintain equipment properly.
But the problems don’t stop there.
It’s more than just people we’re running short on; it’s the tools, spare parts, and materials, too.
A Limble study shows that 34.1% of manufacturing and facility maintenance professionals consider supply chain issues one of their biggest challenges.
This issue leads to delays in the delivery of spare parts, increased costs for specific items, and difficulties in accurately forecasting resource needs and managing inventory.
Consequently, organizations either face understocking, which causes delays, or overstocking, which ties up their cash flow and storage space.
Either way, the machinery doesn’t get the care it needs when needed, and productivity takes a hit.
And then there’s the budget—or lack thereof.
Many maintenance teams operate with minimal budgets, preventing them from doing their jobs properly.
This is because, for too many executives, strategic upkeep is an afterthought, overshadowed by short-term cost-cutting.
John Sedgwick, Director of Engineering and Maintenance at the chemical manufacturing company HEXPOL Compounding, experienced this first-hand.
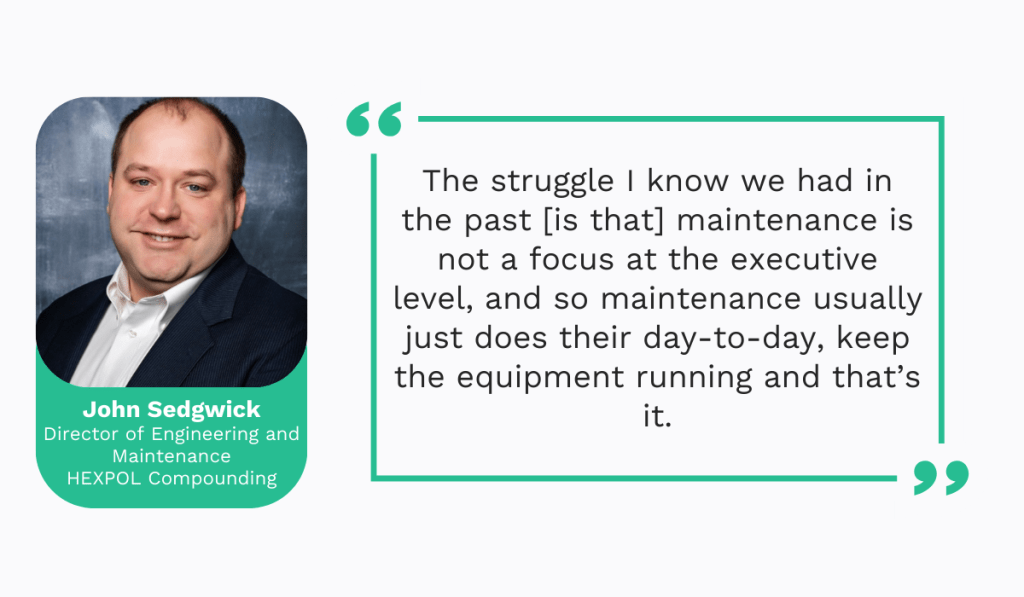
His team initially had issues with productivity and unplanned downtime.
However, the situation improved once the company prioritized proper upkeep and invested more in maintenance software.
And it makes sense. Without adequate financial backing, maintenance always suffers.
Aging equipment isn’t replaced or upgraded, training or tech investments fall by the wayside, and teams are forced to rely solely on reactive maintenance.
Put simply, short-term savings lead to long-term problems.
All in all, with all these issues and more, it’s clear why maintenance in manufacturing is so challenging.
But what’s the solution?
How to Ensure Effective Manufacturing Maintenance
The answer to these challenges is clear: start prioritizing effective manufacturing maintenance.
Let’s dive a bit deeper into what that means, exactly.
It all begins with maintenance planning and then regularly updating the plan to reflect your changing needs.
This plan should clearly outline which assets need maintenance, the type of maintenance they require, how often, and who’s responsible for it.
Vivre Viitanen, Head of Global Service Line at ABB Motion Services, a technology leader in electrification and automation, outlines the benefits of having a well-structured plan:
When strategies are planned, you can ensure that the right capabilities and skilled people are in the right place at the right time and you have the necessary materials. That means the plan can be rolled-out in a more efficient and effective way than if you’re reacting to a situation which has come as a surprise or a shock.
In other words, a solid maintenance plan is the backbone of successful operations.
It prioritizes more strategic resource allocation and scheduling, boosting your processes’ effectiveness.
To take it up a notch, create Standard Operating Procedures (SOPs) that go hand-in-hand with your plan.
SOPs are more granular, step-by-step instructions on executing specific tasks, in what order, and with which resources.
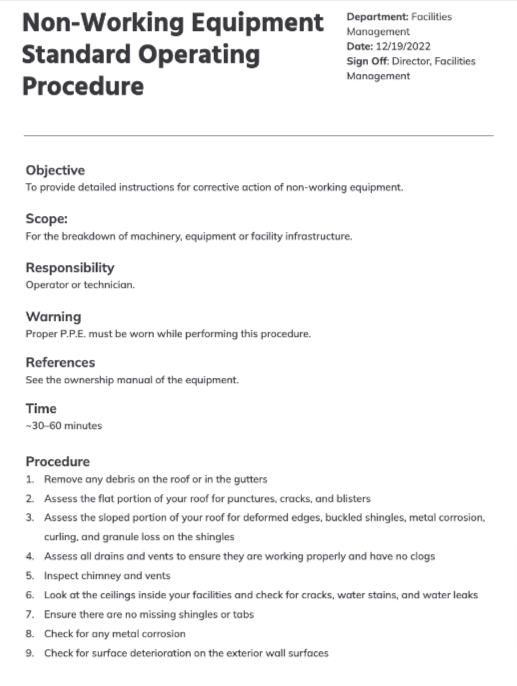
This ensures more consistency in your practices, eliminating mistakes and confusion.
When everyone knows exactly how to fulfill their responsibilities, everything gets done on time, safely, and efficiently—every single time.
However, it’s not enough to simply tell your team what to do and how to do it.
You should also monitor performance to ensure your plans and procedures are effective and realistic.
For example, if you’re still struggling with high downtime rates despite careful planning, it’s a sign that something is off.
Maybe your instructions regarding a particular activity aren’t clear enough, or perhaps some equipment needs specialized maintenance that you didn’t account for.
Tracking relevant KPIs is the best way to gauge your performance.
These metrics provide clear, data-driven insights into the effectiveness of your upkeep efforts, without any biases or relying on guesswork.
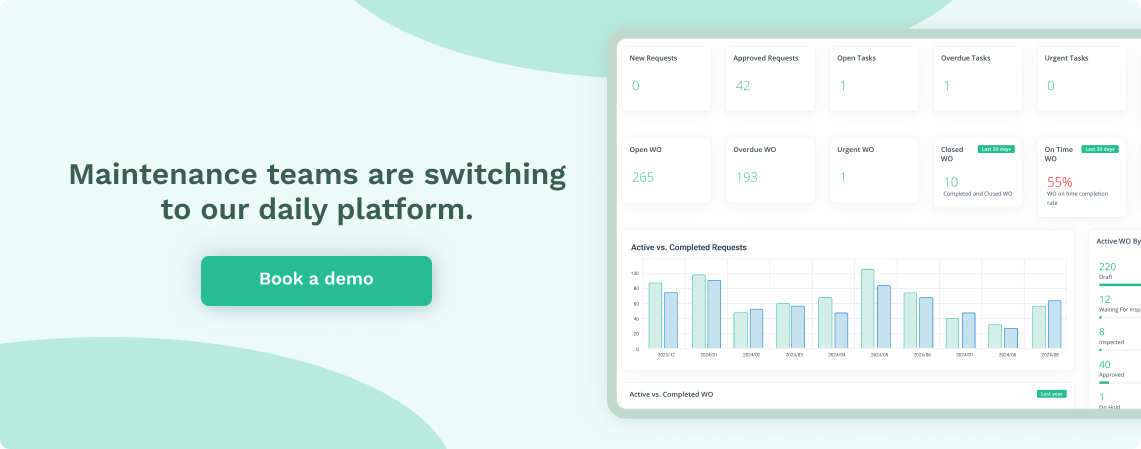
After all, the numbers never lie.
Here are some KPIs worth considering:
- Mean Time to Repair (MTTR)
- Mean Time Between Failures (MTBF)
- Overall Equipment Effectiveness (OEE)
- Planned Maintenance Percentage (PMP)
And if you’d like to explore these metrics in more detail, check out our guide on the top 5 maintenance metrics you should always have in mind.
Overall, these practices are a solid starting point for more efficient maintenance operations.
Still, given the complexity of the process and the challenges involved, they may not be enough on their own.
Luckily, there are many digital tools available that can help further streamline and improve your maintenance efforts.
Modern Tech Used For Factory Maintenance
From advanced robots to augmented reality, a wave of exciting new technologies is transforming manufacturing maintenance.
One technology that has been in the spotlight for some time now is AI.
AI is a key component in predictive maintenance, where machine learning models analyze historical and real-time data to predict future equipment failures.
The technology becomes even more powerful when combined with IoT sensors.
Rakesh Prasad, Senior Vice President of Digital Business at Innover Digital, a technology and process digitization company, explains how this integration works:
For PdM, IoT sensors are fitted in machines and equipment to monitor their health and surroundings, gathering data on factors such as vibration, temperature, and humidity. This data is then relayed to a central system that employs AI/ML algorithms to examine the data and give insights into the equipment or machinery’s well-being.
With countless data points to draw from, AI-driven predictive maintenance can deliver precise forecasts.
This allows its users to schedule upkeep accurately and keep equipment in peak condition without over-maintenance.
Remote monitoring is another technology that is making significant strides in manufacturing maintenance.
It uses various sensors, software, and tools to detect and diagnose issues without requiring maintenance personnel to be physically present.
Robots and drones are increasingly being used for this purpose, too.
Jeff Burnstein, President of the Association for Advancing Automation, predicts we’ll see even more robots used in this space.
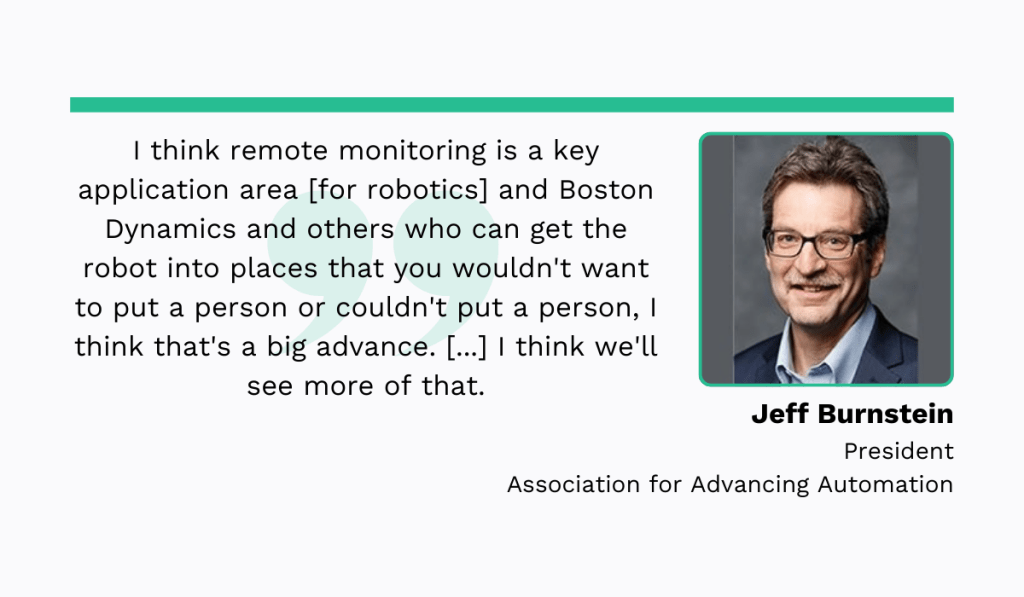
With remote monitoring, you can access hard-to-reach areas and capture high-resolution images and videos.
This gives you a full 360-degree view of your equipment’s health.
In other words, you get more data but fewer safety risks—a true win-win scenario.
The last type of tech on our list is a Computerized Maintenance Management System (CMMS), like our own WorkTrek.
You can think of this tool as your ultimate command center for the entire maintenance operation.
For those routine tasks, you can use WorkTrek’s task management feature to create and assign tasks, keep track of completed work, and see how much time your team spends on certain activities.
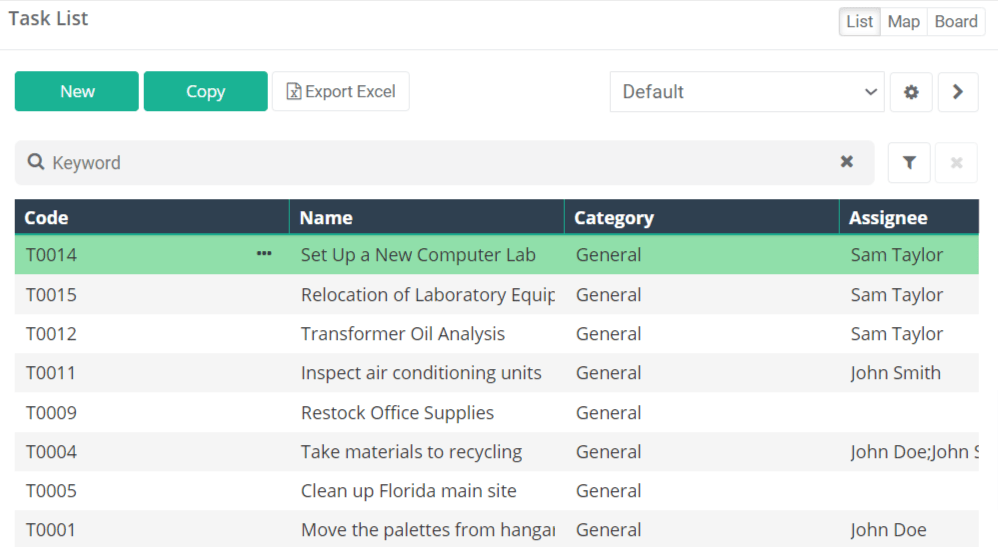
Plus, your staff can report problems and generate work requests by going through our web and mobile apps or via the WorkTrek Request portal.
You can create new work orders as soon as those requests come in and assign them to the right technician or team.
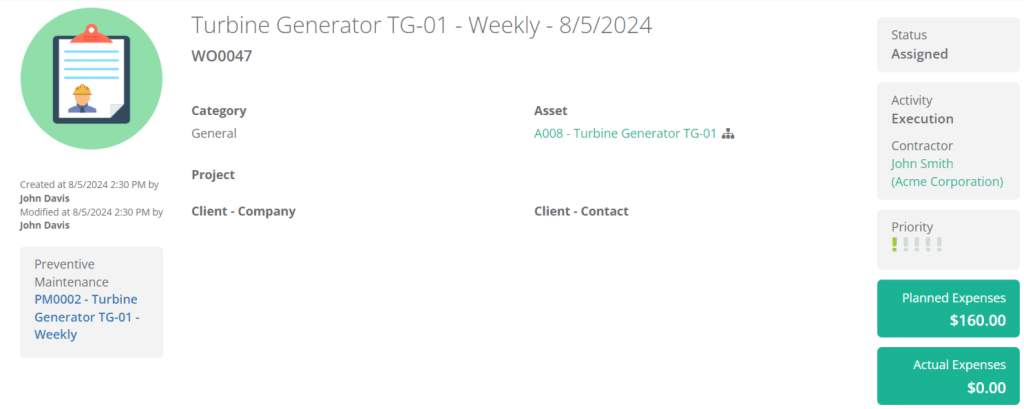
Each work order comes with all the details—priority level, needed resources, and more—so your team can get the job done right and on time.
But that’s not all.
With WorkTrek, you can keep a close eye on your inventory, tracking quantities, locations, and costs of your spare parts and materials.
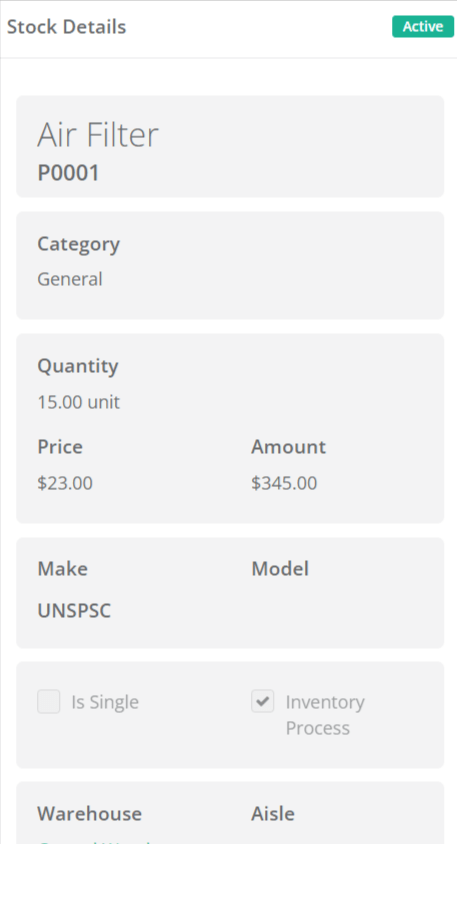
The system enables you to specify minimum quantities for products and then alerts you when your inventory falls below a safe level so that you can restock on time.
It’s really easy to see why maintenance professionals love CMMS so much.
Thanks to this technology, you can manage your whole maintenance operation from a single, intuitive dashboard and, in turn, improve overall efficiency and save money.
Conclusion
Hopefully, you now see manufacturing maintenance for the vital process it truly is.
When done right, it can transform entire operations beyond recognition, boosting profitability, safety, and efficiency.
Plus, being a manufacturing maintenance professional has never been more exciting.
The field is full of new technologies that help simplify the complexities and tackle the challenges that usually come as a part of the job.
We can now predict equipment problems, automate repetitive tasks, and eliminate errors, all from our computers.
So don’t let anyone tell you maintenance is just another routine task when, in reality, it’s the backbone of any successful operation.