Get a Free WorkTrek Demo
Let's show you how WorkTrek can help you optimize your maintenance operation.
Try for freeIn this article, we’re exploring ten statistics about the state of manufacturing maintenance, uncovering the trends they point to and what they could mean for the overall efficiency of plant operations.
Understanding these insights can make all the difference in your decision-making, potentially helping you streamline processes and even unlock significant cost savings.
So, let’s get started and go over some compelling data about this critical process.
In 2018, 57% of Manufacturing Facilities Used a Run-To-Failure Maintenance Method
A Maintenance Report from Plant Engineering and ATS offers an insightful snapshot of how equipment upkeep was handled just a few years ago.
One particularly interesting data point is that over half (57%) of manufacturing businesses relied on run-to-failure (RTF) maintenance at the time.
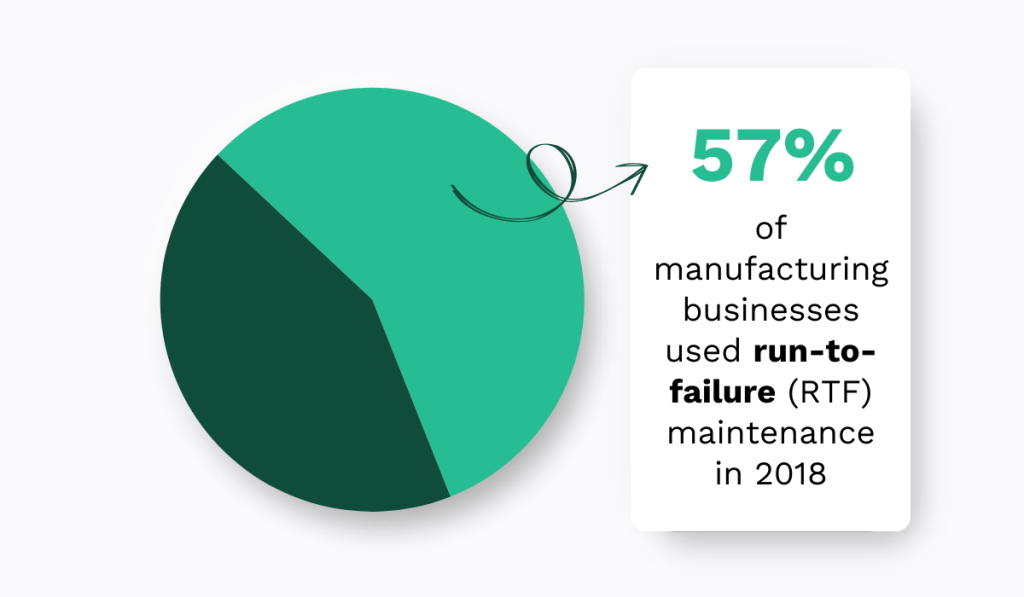
Essentially, it means they didn’t have any maintenance strategy but used assets until they failed and needed repair.
Companies often choose this reactive approach because it requires minimal to no planning and has lower initial costs, making it the easiest to implement.
Plus, maintenance only happens when necessary, so it tends to interrupt production less frequently and reduces planned downtime.
However, the irony is that this approach is often cited as a major contributor to unplanned downtime.
This is because it overlooks proactive asset care, allowing smaller issues to escalate unexpectedly and disrupt operations.
But is that really the case?
Is run-to-failure maintenance truly the leading cause of unscheduled downtime?
The next statistic may offer some insight.
At 44%, Aging Equipment Was the Leading Cause of Unscheduled Downtime in Manufacturing Facilities In 2018
According to the same survey, aging equipment is the leading cause of unplanned downtime, surpassing issues like operator errors, lack of time for maintenance, and neglect of upkeep.
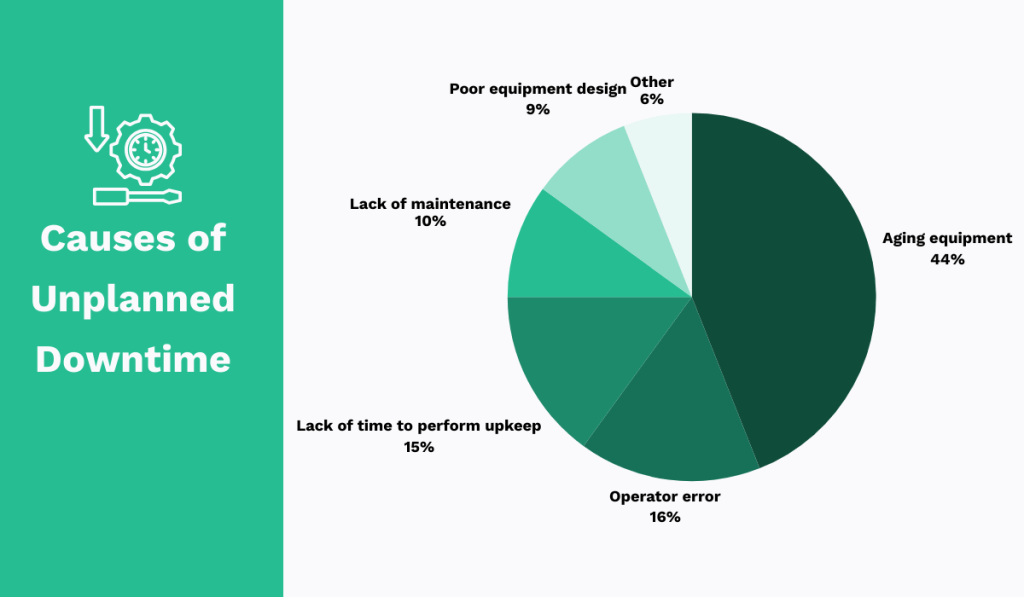
Does reactive maintenance play a role in this?
To some extent.
After all, older assets tend to break down more frequently. If you rely solely on run-to-failure maintenance, you will inevitably face more frequent production stoppages for unexpected repairs.
However, we can’t place all the blame on RTF.
The truth is aging equipment is a big problem itself. Even with a preventive approach, it can still cause disruptions.
Older machines might require no longer manufactured parts, be difficult to handle for younger operators or those that haven’t gotten used to their quirks, or simply be nearing the end of their lifespan.
No asset is built to last forever, no matter how effective the maintenance strategy.
That’s why upgrading machinery was the number one solution survey respondents chose for addressing unscheduled downtime, with proactive upkeep coming in third.
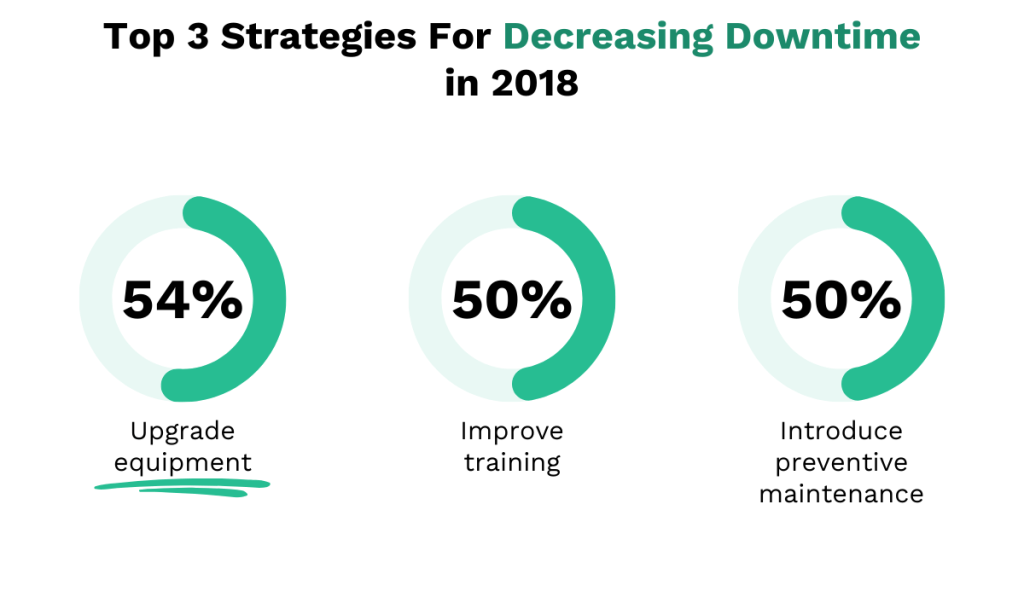
Here’s the bottom line: if you want to minimize downtime, you need reliable machinery running at its best.
Aging equipment doesn’t really meet that standard, especially if you only use reactive maintenance for its upkeep.
So, to improve reliability across operations, invest in preventive upkeep strategies or get new machines, depending on what your budget allows for.
The next statistic shows us that the former option is more realistic.
For 69% of Maintenance Teams, Proactive Maintenance Is the Solution to Aging Infrastructure
The new 2024 Limble report highlights an interesting shift in how we tackle the challenges of aging assets.
Back in 2018, we saw that the focus was primarily on upgrading equipment, but now proactive maintenance has taken center stage.
That’s because, although it’s completely natural for equipment to degrade over time, preventive upkeep can still significantly slow this process down.
And, by addressing minor issues such as leaks, rust, and weakening components through regular checkups and repairs, we can at least postpone those costly replacements.
This is why proactive maintenance is the number one strategy for older infrastructure care, while replacements and upgrades are seen as last resort.
They are reserved for when there are truly no other options.
After all, who wouldn’t prefer to just keep fixing their old, trusted assets rather than having to shell out money for new purchases constantly?
A Manufacturing Facility Allocates Approximately 9.7% of Its Annual Operating Budget to Maintenance Processes
On average, manufacturing facilities allocated 9.7% of their annual operating budgets to upkeep in 2018.
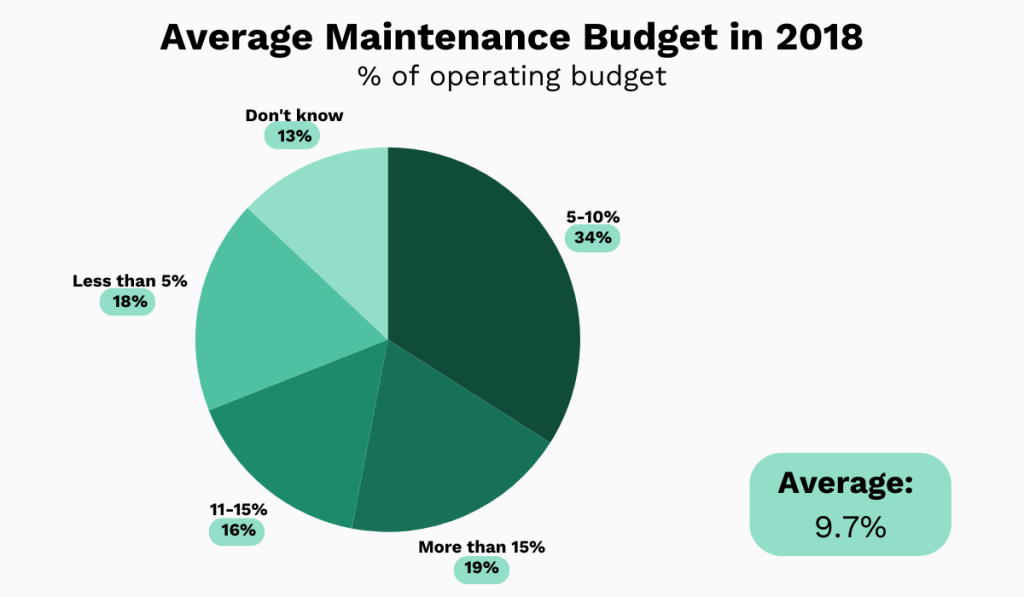
This is definitely a significant amount, but is it a surprising one?
Not really. Maintenance is a costly endeavor.
Keeping equipment in top shape demands real investment, from labor and spare parts to tools and downtime costs.
What’s fascinating, though, is how little this has changed over time.
Fast forward to 2024, and a new MaintainX survey shows that most manufacturers spend 5-10% of their annual budgets on upkeep.
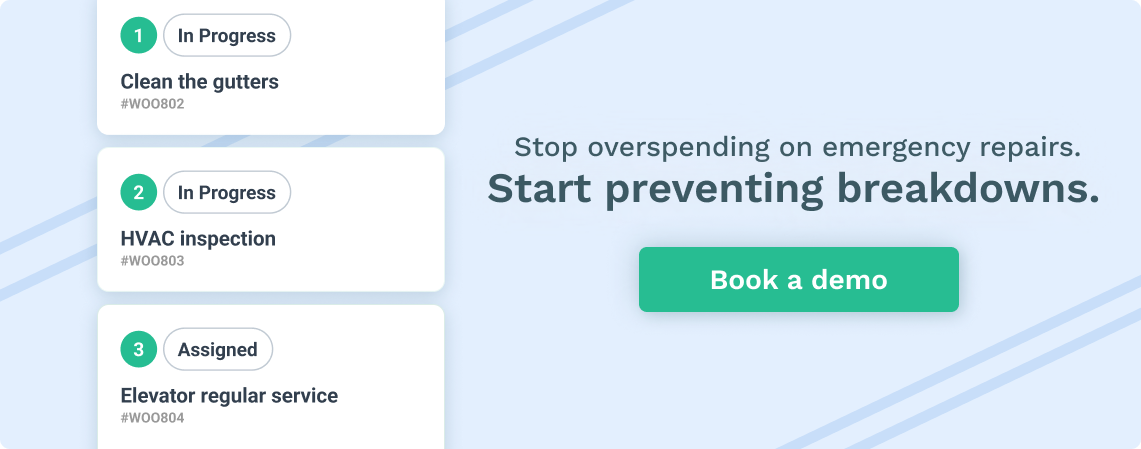
This is close to the 2018 figures.
But with inflation and ongoing material and labor shortages, how have plants stuck to these percentages?
Have innovations in technology and process efficiency allowed us to achieve more with less, or have companies simply had to raise their overall budgets to keep up with rising costs?
The truth is: a bit of both.
While technological advances help streamline operations, maintenance still requires a serious financial investment.
That much is unlikely to change any time soon.
But it’s not just about money—allocating enough time to this vital process is also a must.
31% of Facilities Spend 30 Hours or More Each Week on Scheduled Maintenance
The Engineering Plant and ATS survey reveals that nearly a third of plants spend thirty or more hours per week on maintenance.
For a factory operating two 8-hour shifts daily, five days a week, that’s a significant chunk of total working hours.
In fact, according to the survey, it’s 11 hours longer than the industry average at the time, which is 19 hours.
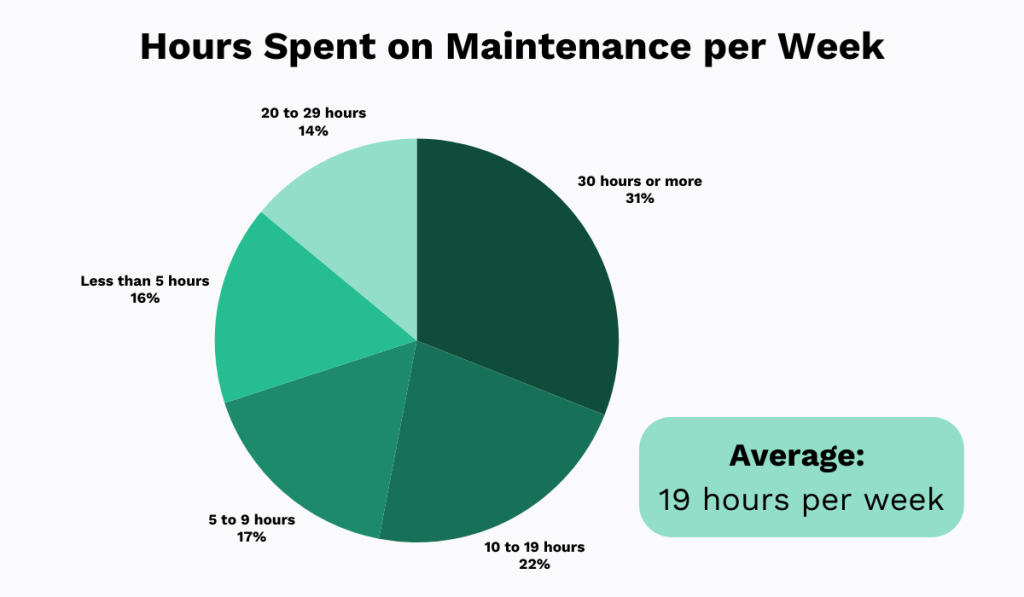
While maintenance is undoubtedly important, you don’t want to spend too much time on it.
Yes, although that may not necessarily be the case with these survey respondents, there is such a thing as too much maintenance—which can spell trouble.
It can lead to delays in production, labor cost increases, and even premature wear of certain components.
It’s an easy way to lose time and money without realizing it.
So, if you are also allocating more hours to maintenance than the industry standard, ask yourself if this maintenance level is necessary for your operations or if you could be missing out on more efficient practices.
Use these maintenance calculators to determine whether you’re spending adequate time on planned maintenance.
In 2024, 67% of Manufacturing Companies Are Using Preventive Maintenance to Address Machine Downtime
A 2024 Limble report on maintenance in manufacturing and facilities highlights that, for many manufacturing companies (67%), preventive maintenance is the top strategy for preventing downtime.
It’s easy to see why.
Preventive maintenance focuses on performing regular checkups and smaller repairs to prevent minor issues from escalating into larger, more detrimental ones.
As a result, equipment becomes more reliable, longer-lasting, and safer, directly translating to fewer operational disruptions.
Previously, one of the main criticisms of this method was its complexity in scheduling and planning, especially when compared to reactive strategies.
However, that is no longer the case thanks to advanced CMMS solutions like WorkTrek.
These solutions simplify various plant upkeep tasks, making the process more well-timed, efficient, and cost-effective.
WorkTrek, for example, enables you to schedule service using predetermined intervals, assign tasks to specific workers, generate detailed work orders, and set up alerts for upcoming or overdue maintenance.
As depicted below, the software also documents all these activities, allowing you to see the whole upkeep history at a glance.
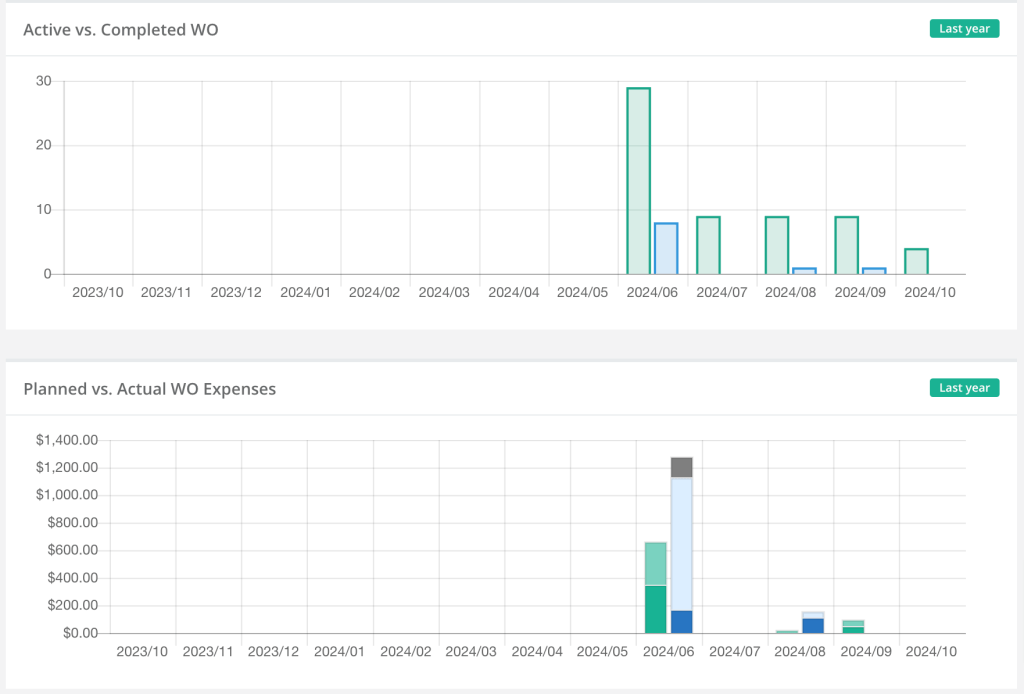
In other words, preventive maintenance is highly effective and has become much easier to implement.
It’s no surprise that so many organizations choose precisely this approach to avoid that dreaded unscheduled downtime.
51% of Maintenance Professionals Say That Machine Downtime and Breakdowns Are One of Their Top Challenges
Equipment uptime is one of the most valuable assets for manufacturing companies but, according to the 2024 Limble survey, they seem to have a hard time increasing it.
As it turns out, 51% of maintenance professionals agree that downtime is one of their top three biggest challenges.
But why is downtime such a big issue?
Because it can seriously impact every facet of business operations.
It causes production lines to grind to a halt, crippling productivity and cutting into profits, all while damaging the company’s reputation due to delays.
On top of that, operational costs soar, particularly as overtime becomes a necessity to compensate for lost time.
In an attempt to catch up, manufacturers may even rush production, inviting a host of quality issues into the mix as well.
No matter how you look at it, downtime spells all kinds of trouble, which explains why so many plants highlight it as a critical concern in their facilities.
But just how often do they have to deal with it?
The Average Manufacturing Facility Suffers 20 Downtime Incidents a Month
The 2022 Siemens survey titled The True Cost of Downtime offers more detailed insights into this persistent problem, revealing that, on average, unplanned downtime occurs about 20 times a month.
The silver lining, the study emphasizes, is that this figure represents six fewer instances than two years prior.
So, does this mean that things are looking better for manufacturing maintenance?
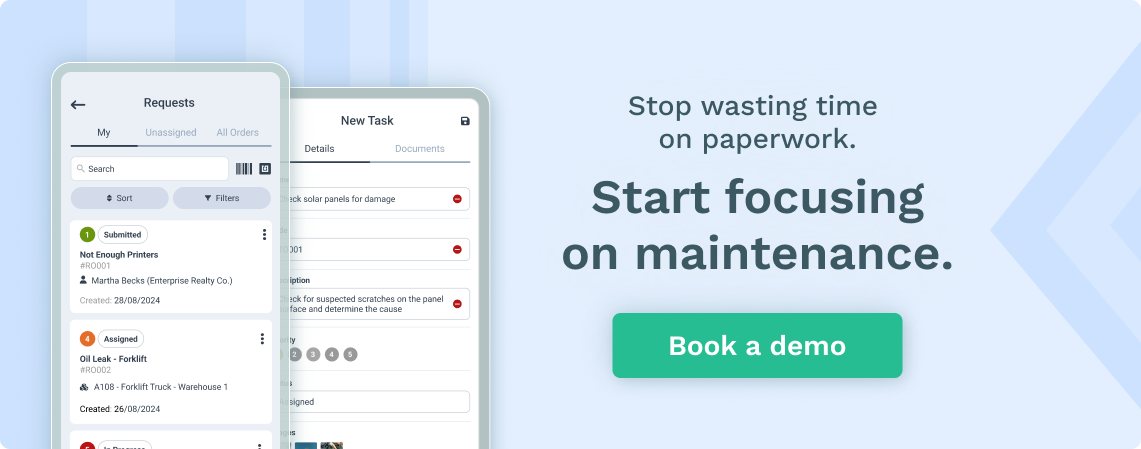
Not exactly.
Although the number of incidents has decreased, the same research shows that recovery times are still alarmingly high.
Namely, the average plant loses more than a full day of production—25 hours to be exact—each month due to unplanned downtime.
According to the study, this issue persists because, while dedicated maintenance technology is improving, supply chains face serious challenges.
As a result, emergency repairs are often put on hold because it’s impossible to procure critical parts amidst all the material and component shortages.
To make matters worse, the industry is grappling with labor shortages, too. There simply aren’t enough skilled workers available to handle these repairs.
When you put it all together, downtime costs too much, and our next statistic reveals how much.
The Cost of an Hour’s Downtime in an Automotive Manufacturing Plant Was More Than $2M In 2021-2022
In the automotive industry, for example, just one hour of downtime costs a shocking $2 million.
In other sectors, such as oil and gas, the figure is around $500,000 per hour.
These expenses are reflected in lost revenue, the cost of emergency spare parts, increased labor costs, and other unnecessary costs.
But, what’s even more alarming is that, across all industries, the cost of downtime increased by 50% from 2020 to 2022 due to inflation and production lines running at higher capacity.
That means today, the cost of downtime could be even higher.
It’s no surprise that more and more companies are adopting proactive maintenance strategies and advanced technologies to avoid these costly disruptions.
With profits at stake, there’s just no room for error.
91% of Manufacturing Maintenance Professionals Are Prioritizing the Improvement of Their Data Collection and Analysis Capabilities
With 91% of manufacturing companies working towards improving their data collection and analysis, it’s quite clear that data truly is king, even within the realm of maintenance.
We have already mentioned that today, so many different technological and process innovations are emerging, all with the goal of making our maintenance efforts more efficient.
But guess what?
None of these innovations are effective without accurate data.
Take predictive maintenance, for example.
Its main objective is to forecast asset failures and schedule maintenance to address potential problems without the risk of over-maintaining proactively.
It achieves that through data.
Predictive maintenance leverages real-time data gathered from a network of sensors on your machines.
This data is then fed into software armed with advanced analytical capabilities that identify patterns and provide users with actionable insights.
Many experts, such as Ankush Malhotra, Group CEO at Element Logic, a company providing warehouse optimization tech, believe that this type of maintenance will soon become the norm:
Predictive maintenance is becoming a need, not a want, especially as skilled labor is hard to come by and retain. AI offers a clear pathway, and there is a strong belief within the industry that manufacturers who don’t adapt to the benefits are likely to be left behind.
Rather than relying on guesswork or ineffective schedules, it focuses exclusively on data to develop better maintenance strategies and plans.
It’s natural that manufacturing facilities want to implement these predictive capabilities in their operations, which is why we see so many of them boosting their data collection and analysis efforts.
Conclusion
Overall, these statistics reveal a significant shift toward proactive, data-driven maintenance.
More than ever, companies prioritize upkeep based on real-time asset conditions, moving away from the outdated approaches of simply reacting to breakdowns or sticking to rigid time-based schedules.
This is because the consequences of both under- and over-maintenance can be steep, often leading to costly downtime.
Looking ahead, we’re likely to see an even greater push toward predictive—and even prescriptive—maintenance models, which will help maintenance professionals ensure assets get exactly the care they need, when they need it.