Get a Free WorkTrek Demo
Let's show you how WorkTrek can help you optimize your maintenance operation.
Try for freePreventative maintenance benefits any mechanical equipment, whether your personal car or critical equipment in factories. It is essential to increasing productivity.
This article offers a comprehensive approach to implementing preventive maintenance strategies that can help prevent equipment failure and minimize maintenance costs.
By following the straightforward, actionable steps outlined in this blog, you can improve your operation’s reliability while extending the lifespan of your equipment downtime.
Preventive vs Predictive Maintenance: Understanding the Differences
While both preventive and predictive maintenance are proactive strategies designed to enhance equipment reliability and longevity, they differ significantly in their approach and execution. Preventive maintenance is a schedule-driven process that relies on regular, calendar-based checks and servicing to prevent potential equipment failures.
On the other hand, predictive maintenance leverages real-time data and advanced analytics to forecast when maintenance should be performed, aiming to predict equipment issues before they occur. This comparison highlights the distinction between maintaining equipment based on a set timetable versus using technology-driven insights to inform maintenance actions.
Preventive maintenance is a predictive approach to maintaining equipment efficiency and reliability. It helps reduce downtime, unplanned maintenance, and repair costs and improves safety and productivity through regular checks and scheduled servicing based on usage or time. An effective preventive maintenance program relies on a well-organized schedule, meticulous documentation and record-keeping, and a skilled maintenance team trained in current technologies and best practices.
Implementing a preventive maintenance plan involves identifying critical assets, setting SMART goals and KPIs, creating and adhering to a maintenance schedule, assigning team responsibilities, and continuously monitoring and adjusting the plan for effectiveness.
Understanding Preventive Maintenance
Preventative maintenance is a systematic strategy for maintaining and improving equipment conditions. It can be performed on a scheduled basis based on either usage or time-based triggers. It constitutes regular preventive maintenance tasks designed to reduce the likelihood of equipment failures and bolster long-term efficiency.
Consider these tasks for medical check-ups for machinery. They aim at identifying potential issues early on before they escalate into cost-intensive malfunctions.
Some key benefits that stem from practicing preventative maintenance include:
- Boosted reliability and operational availability of equipment
- Improve customer satisfaction
- Reduced downtime and ensure equipment items are functioning properly
- Reduced costs related to repairs and decreased periods of downtime
- Increasing the lifespan of machinery
- Improve safety measures for those operating or utilizing the machines
- Increase productivity
- Reduce unplanned downtime
- Reduce reactive maintenance
- Reduce instances of unexpected equipment failures
- Reduce random failures and costly downtime
- Improving regular maintenance upfront costs
- Reduce mechanical failures
How to Reduce Unplanned Downtime
Adopting a program centered around preventive maintenance allows proactive intervention in addressing mechanical concerns and securing seamless operation.
There are two types of preventive maintenance: calendar-based procedures carried out periodically (e.g., monthly inspections) and usage-based interventions triggered by how much an item is used—like servicing vehicles after reaching specified mileage thresholds.
Improve Preventive Maintenance Tasks
Regular preventive maintenance promotes safety while reducing costly repairs. This can significantly reduce reactive remedies post-failure incidents. It also creates a more resilient infrastructure for your business where you can mitigate risks before they escalate.
This proactive approach ensures the smooth operation of facilities and instills a culture of safety and responsibility among maintenance teams. Regular maintenance checks become routine, enabling teams to identify potential hazards and inefficiencies early.
This approach allows for swift and cost-effective resolutions that maintain the integrity and reliability of the equipment. By preemptively addressing potential issues, it reduces the time and resources needed for repairs after a failure has occurred.
This proactive stance preserves the equipment’s operational capabilities and ensures that maintenance efforts are less disruptive and more predictable. Furthermore, it contributes to a safer working environment by decreasing the likelihood of emergencies arising from equipment breakdowns.
Adopting such a strategy is a testament to an organization’s foresight and commitment to upholding high standards of operational excellence and equipment care.
From thorough cleanings and lubrications to parts replacements, activities are grouped under preventative measures to maintain order in HVAC and electrical systems and optimize functionality in industrial environments.
Critical Components of a Preventive Maintenance Program
A successful preventive maintenance program is more than simply conducting routine checks and executing repairs. It includes a thoughtful integration of multiple elements, all critical to improved product functioning.
Key to its success are defined schedules, thorough record-keeping, employing maintenance systems, and the expertise of the maintenance team that has received proper training.
Examining these components in detail reveals their collective impact on crafting an effective preventive maintenance strategy.
Scheduling Maintenance Tasks
Establishing a schedule is crucial in preventive maintenance. It includes outlining maintenance tasks and inspections that should be performed at predetermined times or based on specific triggers, such as usage-based maintenance related to usage intervals or environmental factors.
Maintenance can be triggered by a predefined schedule, at regular periods, or depending on how much an asset has been used. For example, while an industrial machine may require servicing after a set number of hours operated, quarterly check-ups might be sufficient for an HVAC system.
Experts create these schedules to reduce production interruptions and consider various elements, including technician availability and inventory levels for parts and tools required to complete these jobs within expected timeframes.
Following planned maintenance routines helps companies reduce unexpected downtime issues and backlog accumulation in maintenance work orders, which can lead to potential miscommunication risks or accidents. Consequently, this approach can lower the overall costs related to maintaining assets.
Modern preventive maintenance extends beyond following a fixed schedule. It leverages innovative technological tools like Enterprise Asset Management software to automate the scheduling of maintenance tasks. This integration streamlines the management of work orders and enhances the standardization of documentation processes for equipment care tasks.
Source: WorkTrek
Documentation and Record-Keeping
Maintaining detailed records is an essential aspect of proactive maintenance strategies. Equipment maintenance history should also be readily available to technicians. Having this history can improve repair times and reduce unnecessary or duplicate repairs.
Suppose you can centralize these documents and serve them in an existing Work order for maintenance tasks. In that case, they provide essential structure, describing the extent of work, expectations, timeframes, authorization details, and specific responsibilities.
They guide technicians by clarifying the necessary actions to be taken along with their timing and methods.
Documentation’s importance extends beyond mere work order management. By keeping accurate and comprehensive logs of all maintenance activities, businesses can analyze spending trends and improve overall asset management efficiency.
Conversely, a lack of documentation can result in irregular maintenance histories, complicating the establishment of an ideal routine for upkeep activities.
Therefore, it’s clear that meticulous documentation is more than just keeping records; it plays a pivotal role in enhancing the accuracy and effectiveness of preventive maintenance programs.
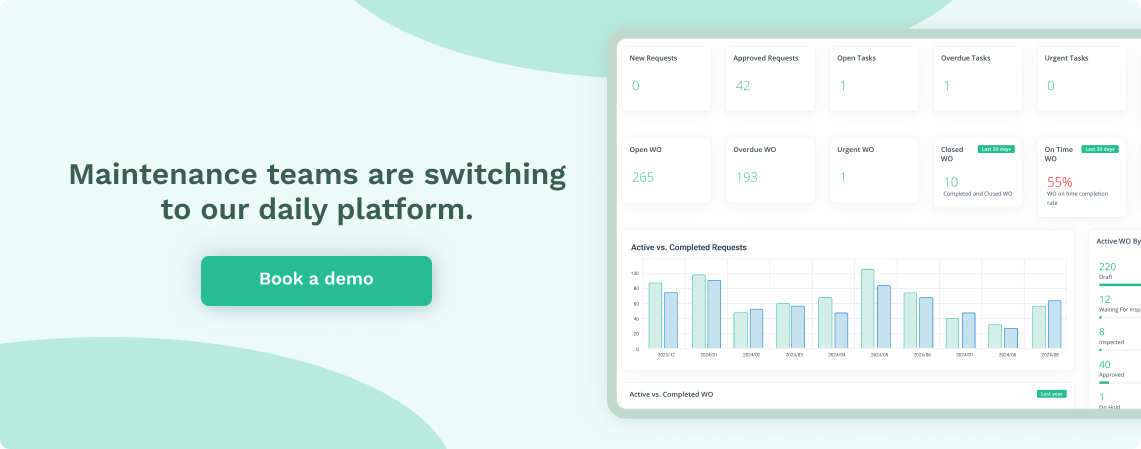
Training and Skill Development
Source: ita group
The successful implementation of a preventive maintenance plan is heavily dependent on the expertise and training of the maintenance crew. The ability to carry out maintenance tasks effectively depends significantly upon their competencies, especially as technologies evolve and best practices in equipment maintenance progress.
It is essential to carefully select technicians with the right skills for specific preventive maintenance tasks. Maintenance activities can present environmental or safety hazards, necessitating compliance with rigorous industry standards and thorough risk assessments to safeguard the health and safety of personnel and the integrity of the equipment. Focus on continuous training of the team.
A successful preventive maintenance system depends on providing clear, comprehensive instructions that enable maintenance professionals to conduct tasks with precision and efficiency.
Implementing a Preventative Maintenance Plan
Let’s dive into integrating a preventive maintenance plan, having unpacked its essential elements. Enacting this process requires multiple phases, such as:
- Pinpointing assets in need of preventive maintenance
- Establishing objectives for your preventative maintenance scheme
- Devising a timetable for carrying out maintenance tasks
- Allocating duties and training team members
- Supervising progress and fine-tuning when necessary
Adherence to these steps while executing preventive maintenance tasks allows you to successfully apply a preventive maintenance strategy within your establishment.
We will now explore each phase in more detail.
Identifying Assets
Initiating a preventive maintenance plan begins by identifying the assets subject to preventative care. This is achieved through developing an inventory of assets, which includes comprehensive details such as their make, model, serial number, specific features, situated location, and tracking mechanisms like QR codes or barcodes. While this process can be cumbersome, it is critical to the success of having well-maintained equipment.
This detailed registry is critical for efficiently monitoring and maintaining each asset under the preventive maintenance program.
Nevertheless, it’s important to recognize that not every asset is equally important. Assessing each asset’s criticality depends on evaluating how its failure could affect operations, such as production downtime, safety risks, or environmental hazards.
By performing these assessments, you can prioritize preventive maintenance activities for assets whose malfunction would profoundly impact your operations.
It is essential to manage the process continuously to maximize efficiency in preventing equipment failures and stay aligned with evolving operational conditions or strategies. Regular reviews of the inventory list and reassessments of asset criticality are crucial for maintaining high-priority assets within any operation.
Source: WorkTrek
Setting Goals and KPIs
Setting clear and quantifiable objectives is essential to the effectiveness of a preventive maintenance strategy, mirroring the principles of any strategic planning. To track progress accurately, objectives should align with SMART criteria—Specific, Measurable, Achievable, Relevant, and Time-bound. An example objective might be aiming for a 20% reduction in equipment downtime over the next six months.
You must employ Key Performance Indicators (KPIs) to evaluate your preventive maintenance plan’s performance. A balanced selection of leading indicators forecasting future performance and lagging indicators verifying past patterns gives a rounded picture of maintenance effectiveness. Among common KPIs utilized for this purpose are:
- Percent critical scheduled maintenance
- Planned maintenance ratio
- Compliance with preventive measures
- The overall efficiency of the equipment
- The average time between failures
It is essential to apply a consistent approach to measuring these KPIs to reliably ascertain whether your preventive maintenance plan is hitting its targets.
Source: WorkTrek
Monitoring Progress and Adjusting as Needed
A preventive maintenance program must be adaptable and continually refined through data analysis to improve its success. It ought to incorporate a performance evaluation method with the flexibility to tweak procedures over time to sustain its effectiveness.
Embracing this philosophy of ongoing enhancement helps tailor scheduled maintenance activities more closely to actual equipment usage trends, thereby reducing unplanned downtime and boosting the overall efficiency of the preventive maintenance strategy.
Yet, no matter how thorough a preventive maintenance plan may be, it cannot completely rule out unforeseen equipment breakdowns.
For such eventualities, having backup plans ready—like arrangements for unplanned repair work—is crucial, as is consistently assessing how well preventive measures work.
These emergency protocols ensure quick responses when unexpected failures occur and help keep operations running smoothly without major interruptions.
Source: eLearning Industry
The Role of Technology in Preventive Maintenance
As with many other industries, technology has revolutionized preventive maintenance, significantly enhancing the efficiency of its processes.
A computerized maintenance management system (CMMS) can improve operations by enabling efficient scheduling, execution, and monitoring of work orders related to preventive maintenance tasks.
Predictive maintenance takes advantage of real-time data analysis to anticipate when equipment might need servicing—proactively issuing work orders ahead of potential failures. Capturing and analyzing maintenance data can significantly improve predictive maintenance.
Intelligent sensors and sophisticated data analysis allow for the precise timing of inspections, minimizing the resources traditionally spent on asset maintenance.
Proactive maintenance harnesses predictive insights to improve equipment reliability and ensure timely responses to potential issues. By proactively addressing these concerns, operations can avoid downtime.
Routine checks and real-time system monitoring contribute to this by consistently implementing preventive actions across all operational platforms.
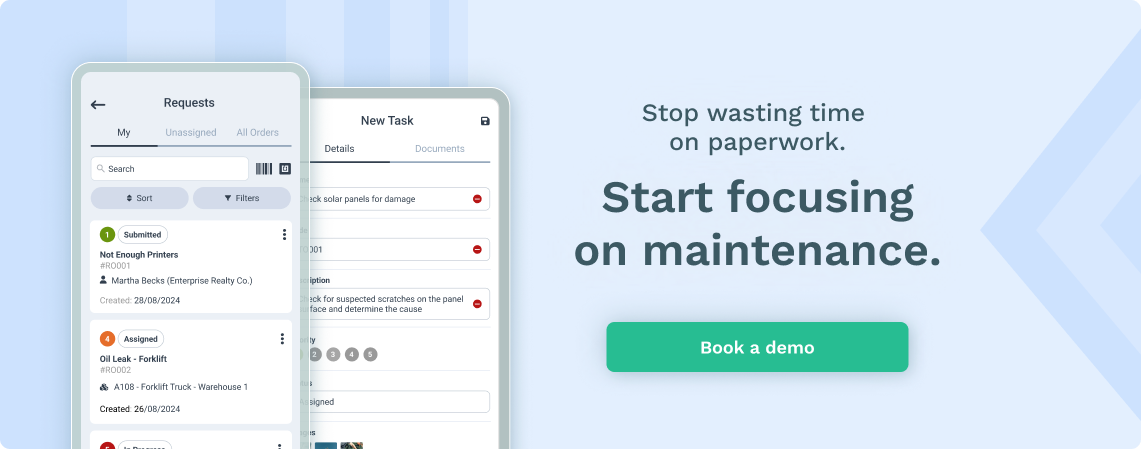
Integrating new technological solutions designed to optimize these workflows is essential for maintaining seamless operations and setting the stage for future advancements in the field.
Overcoming Common Challenges in Preventive Maintenance
Source: WorkTrek
Implementing a preventive maintenance strategy can significantly enhance the longevity and reliability of assets, though it also presents some hurdles.
One primary obstacle is the initial investment in establishing a proactive maintenance program, as an immediate rise in costs could discourage organizations from adopting it.
Transitioning to a preventive maintenance approach might necessitate additional resources, including new personnel, an expanded spare parts inventory, and more time dedicated to the program’s execution. Risk assessment is integral to this framework.
Challenges associated with emergency interruptions are minimized by preemptively addressing potential asset failures through strategic planning and resource allocation.
Over 60% of routine activities in leading-edge programs consist of proactive maintenance measures. By prioritizing preventative strategies over reactive ones, enterprises experience fewer unforeseen disturbances, resulting in stable and streamlined operations.
The Impact of Preventive Maintenance on Overall Business Performance
Proactive maintenance practices don’t just preserve the integrity of equipment. They also provide significant savings. By adopting preventative measures, organizations can achieve:
- A reduction in urgent service calls that typically exceed proactive maintenance expenses
- A decrease in unscheduled shutdowns and catastrophic malfunctions
- Diminished urgency for express parts procurement
These reductions translate into increased savings for companies.
Preventive maintenance delivers a suite of additional advantages, including:
- Enhanced operational efficiency
- Elevated safety standards within the workplace
- Better adherence to regulatory requirements such as those set by OSHA
- Fewer asset failures leading to less downtime
- Saved time for the maintenance team thanks to fewer unexpected issues
- Boosted dependability of assets, ensuring smoother operations with minimal interruptions
- Improved functionality of machinery and equipment
- Implement usage-based maintenance for critical equipment items
Simplifying routine tasks related to maintenance can lead to an uptick in overall productivity.
Real-World Examples of Successful Preventive Maintenance Programs
Source: Click Maint
Let’s look at some real-world examples to understand preventive maintenance’s impact fully. Preventive property maintenance is a great example involving routine inspections and repairs to avoid costly system failures and keep maintenance expenses low.
Seasonal and quarterly tasks such as winterizing pipes, cleaning gutters, and HVAC servicing are examples of time-based preventive maintenance.
On the other hand, different types of preventive maintenance can be employed for various assets. These include:
- Usage-based preventive maintenance: This is used for vehicles and elevators, where servicing is scheduled based on the hours used.
- Risk management preventive maintenance involves frequent inspections of high-value assets to prevent failures. For example, checking access control systems and conducting electrical inspections to avoid fires.
- Augmentation maintenance: This involves making improvements and renovations to keep the building up-to-date with technological advancements. For example, installing smart lighting or keyless entry systems.
Implementing a preventive maintenance checklist can help determine which preventive actions are necessary and aid in budgeting and planning maintenance schedules.
Summary
In conclusion, preventive maintenance is an integral part of any successful operation. It involves systematically scheduling, documenting, and performing maintenance tasks to prevent equipment failures, improve safety, and save costs.
Implementing a preventive maintenance plan involves identifying and prioritizing assets, setting measurable goals, and monitoring progress. Leveraging technology can significantly enhance the efficiency and effectiveness of preventive maintenance.
While challenges exist, they can be effectively overcome, leading to significant benefits, including cost savings, improved safety, and increased productivity.
Source: Skilled Group