What is Zero-Based Maintenance?
Zero-based maintenance (ZBM) is a strategic method that starts with zero assumptions about existing maintenance activities and rebuilds the maintenance program from scratch, focusing only on what’s truly needed to keep equipment running efficiently.
Unlike traditional maintenance approaches that carry forward previous practices, ZBM requires justifying every maintenance task based on current equipment needs and conditions. This approach helps companies eliminate unnecessary maintenance tasks and introduce cost savings while ensuring critical equipment receives proper care.
By restoring equipment to like-new condition, ZBM improves efficiency, extends machinery life, and reduces operational costs.
Similar to zero-based budgeting in finance, this method demands that maintenance activities prove their value before being included in the program.
Understanding Zero-Based Maintenance
Zero-based maintenance represents a fundamental shift in how organizations approach maintenance planning and execution. This methodology challenges traditional assumptions by starting from scratch rather than building upon existing processes.
Principles of Zero-Based Maintenance
The core principles of ZBM include:
- Clean-slate approach: Every maintenance activity must prove its value
- Resource optimization: Allocating resources based on current needs, not historical patterns
- Data-driven decisions: Using real-time information rather than assumptions
- Continuous evaluation: Regularly reassessing maintenance requirements
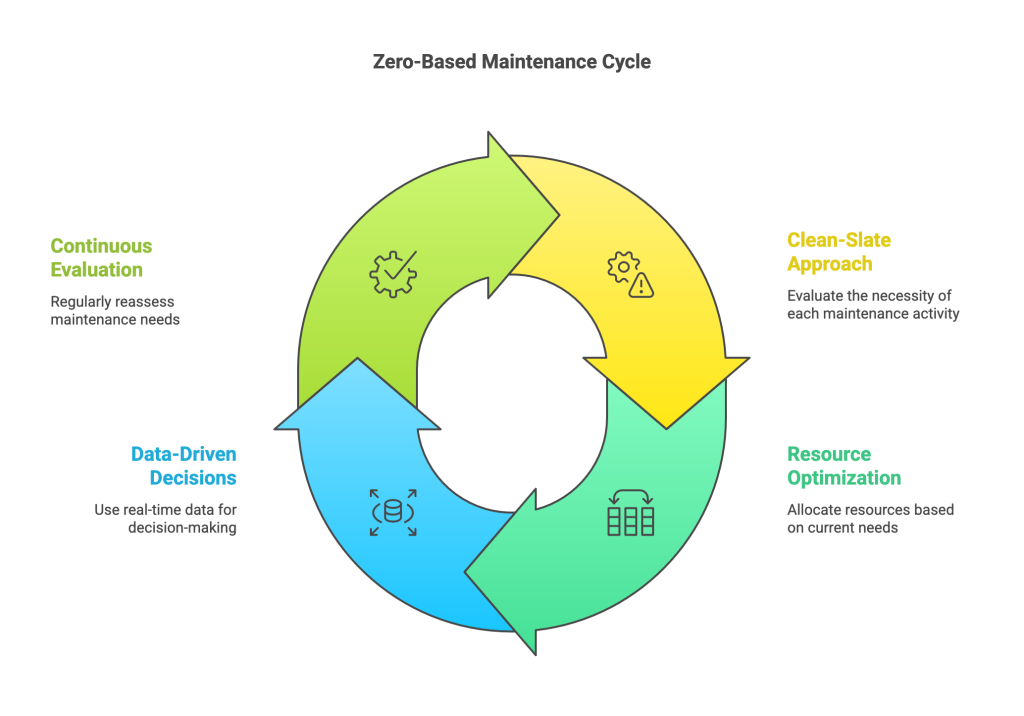
Source: Worktrek.com
ZBM develops maintenance tasks and schedules from scratch, focusing on what is needed rather than what has always been done. This approach eliminates redundant or unnecessary maintenance activities that consume resources without adding value.
Comparison to Traditional Maintenance Approaches
Traditional maintenance typically relies on historical schedules and budgets, often carrying forward previous plans with incremental adjustments. This can perpetuate inefficiencies and outdated practices.
Key differences include:
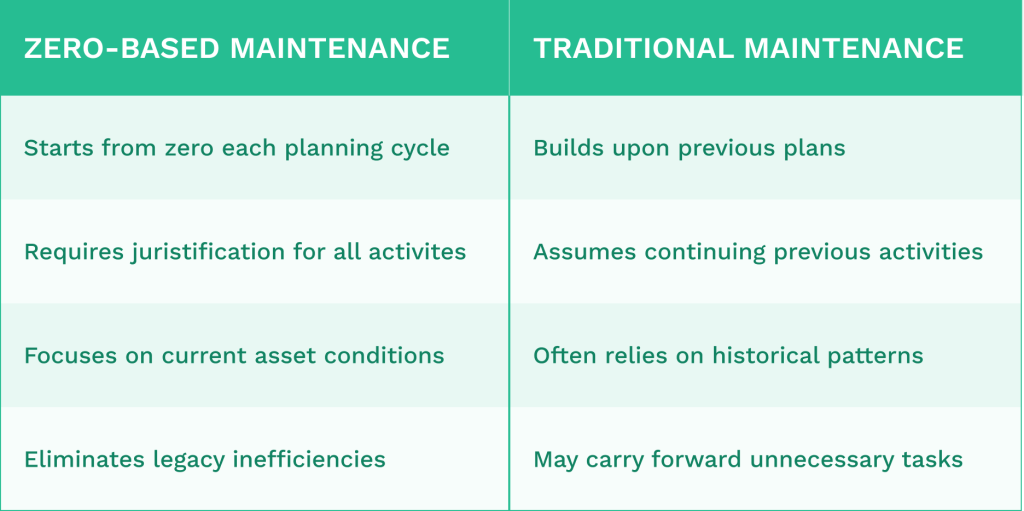
ZBM shares similarities with zero-based budgeting (ZBB), where expenses must be justified for each new period. This is a different approach to the budgeting process. However, it does have the potential benefit of enhancing equipment reliability and improving asset performance.
ZBB breaks down the maintenance demands into specific assets or areas, creating a more targeted approach. One of the first steps in the process is identifying critical assets and updating existing maintenance programs.
This reassessment helps organizations identify redundancies and focus resources where they deliver the most value, which can reduce unnecessary expenses and enhance operational efficiency.
Implementation of Zero-Based Maintenance
Implementing Zero-Based Maintenance (ZBM) requires systematic planning and execution. The process involves careful assessment, strategic development, and disciplined execution to optimize maintenance resources and improve operational efficiency.
Assessment of Assets and Needs
The first step in implementing Zero-Based Maintenance is conducting a comprehensive assessment of all assets. This involves creating a detailed inventory of equipment and facilities requiring maintenance.
Teams should evaluate each asset’s criticality, condition, and historical performance data. Critical factors to consider include:
- Equipment age and condition
- Failure history and patterns
- Operational importance
- Safety implications
This assessment helps identify maintenance priorities and needs from the ground up. Unlike traditional approaches, ZBM doesn’t rely on previous maintenance schedules or budgets.
Maintenance professionals must gather input from operators, technicians, and engineers to understand real maintenance requirements. This collaborative approach ensures that all perspectives are considered when building the maintenance framework.
Developing a Zero-Based Maintenance Strategy
After assessment, the next phase involves developing a comprehensive maintenance strategy starting from scratch. This strategy should align with business objectives while optimizing resource allocation.
The strategy development process includes:
- Setting clear maintenance objectives
- Determining appropriate maintenance types (preventive, predictive, corrective)
- Establishing performance metrics and KPIs
- Allocating resources based on justified needs
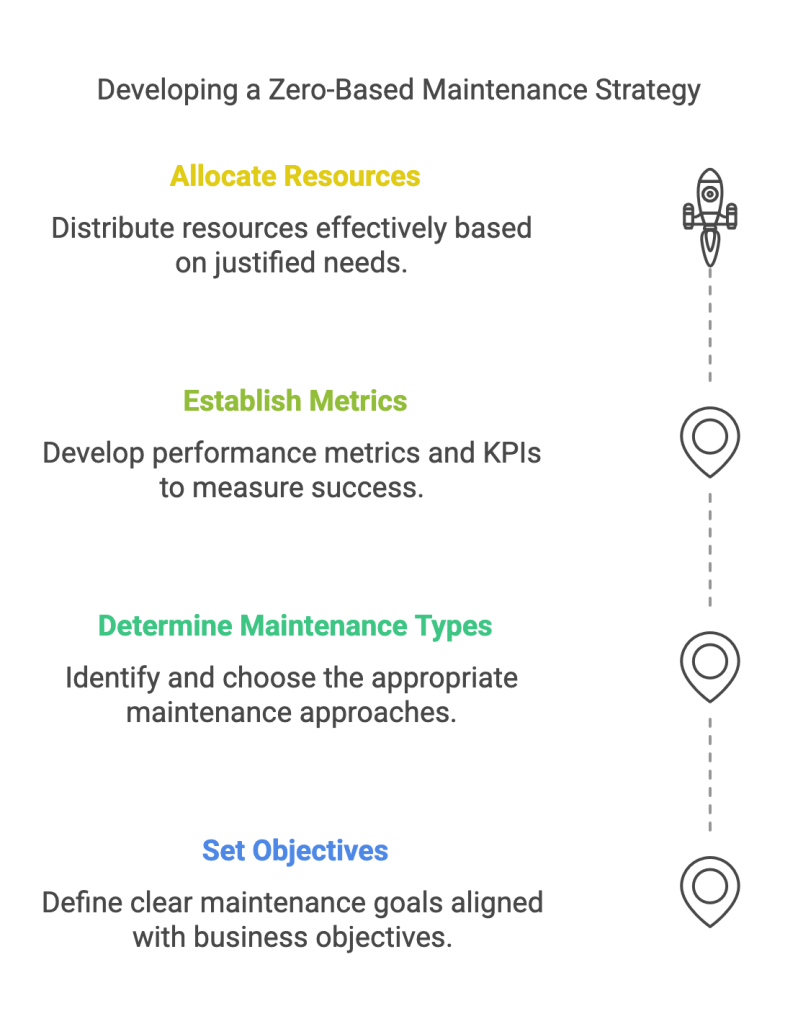
Like zero-based budgeting, each maintenance activity must be justified based on current needs rather than historical practices. This eliminates unnecessary tasks and focuses resources where they deliver the most value.
Resource requirements should be calculated for each asset or group of similar assets. This includes labor hours, parts, tools, and specialized services needed to maintain equipment properly.
Execution of Maintenance Plan
The execution phase transforms the zero-based strategy into actionable maintenance activities. This requires careful scheduling, clear communication, and proper documentation.
Implementation typically follows these steps:
- Create detailed work procedures for each maintenance task
- Develop scheduling systems that prioritize critical work
- Train maintenance personnel on new procedures
- Implement tracking mechanisms to monitor performance
Effective execution depends on strong leadership and clear communication. Maintenance teams must understand the rationale behind the new approach and their role in its success.
Regular review meetings help identify obstacles and make necessary adjustments. Breaking maintenance demands into constituent parts allows teams to focus on specific assets or areas, improving overall efficiency.
Technology solutions like CMMS (Computerized Maintenance Management Systems) can support implementation by tracking work orders, managing inventory, and providing data for ongoing analysis.
Benefits of Zero-Based Maintenance
Zero-based maintenance offers significant advantages for organizations looking to improve their maintenance operations. It creates measurable improvements in financial resources, operational performance, and equipment longevity.
Cost Optimization
Zero-based maintenance enables organizations to allocate resources more effectively by identifying and eliminating unnecessary maintenance costs.
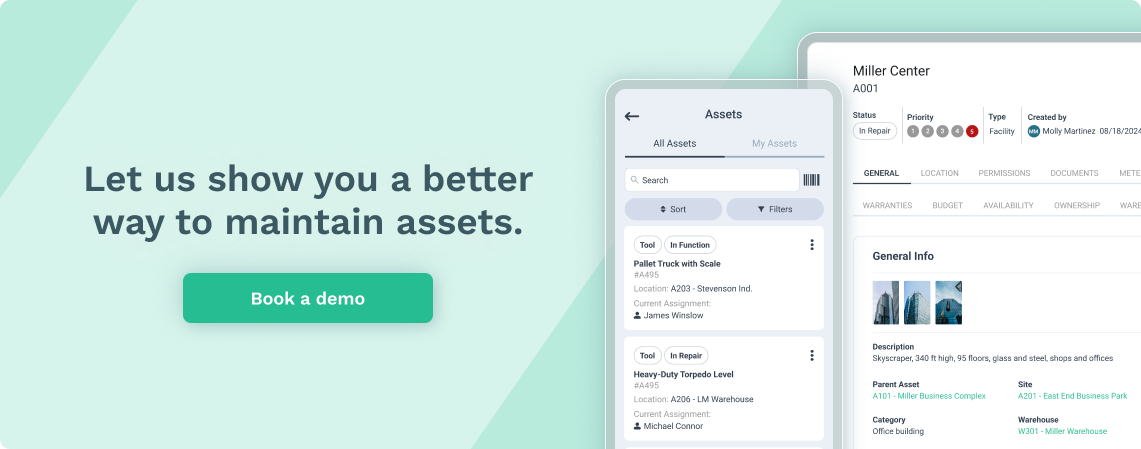
Instead of using previous budgets as a starting point, maintenance managers evaluate each maintenance activity from zero to justify expenses.
This approach helps prevent budget waste by focusing resources on critical equipment needs rather than continuing historical spending patterns. Companies can redirect saved resources to other strategic initiatives or investments.
The zero-based budgeting process requires maintenance teams to provide detailed justification for each maintenance task, creating greater accountability and transparency in spending.
This detailed analysis often reveals hidden costs or inefficiencies that would otherwise go unnoticed.
Organizations implementing zero-based maintenance typically see a 10-20% reduction in maintenance costs within the first year.
Improved Efficiency and Equipment Reliability
Zero-based maintenance significantly improves operational efficiency, equipment performance, and overall operation efficiency by prioritizing maintenance activities based on equipment criticality and business impact. This approach eliminates unnecessary maintenance while ensuring critical assets receive proper attention.
Maintenance teams become more focused and productive as they concentrate on value-adding activities rather than routine tasks that provide minimal benefit.
The systematic evaluation process helps identify bottlenecks and inefficiencies in maintenance workflows.
Zero-based maintenance reduces unexpected breakdowns and emergency repairs by restoring equipment to like-new condition. This predictability allows for better planning and scheduling of maintenance activities.
Organizations can also optimize their maintenance staff levels and skill requirements based on actual needs rather than historical precedent. This right-sizing ensures the maintenance team has the right capabilities to support business goals.
Improved Asset Lifespan
Equipment maintained through zero-based principles typically lasts longer and performs more reliably. By focusing maintenance efforts on critical components and failure modes, organizations can address issues before they cause significant damage.
The approach encourages developing detailed equipment maintenance plans (EMPs) that outline specific maintenance requirements for each asset. These plans ensure consistent application of maintenance best practices.
Zero-based maintenance often incorporates condition monitoring and predictive technologies that detect potential failures early. This early detection allows for timely interventions that extend equipment life.
Studies show that properly maintained equipment can achieve 20-40% longer useful life compared to equipment subject to reactive maintenance approaches. This extended lifespan translates to significant capital savings by delaying replacement costs.
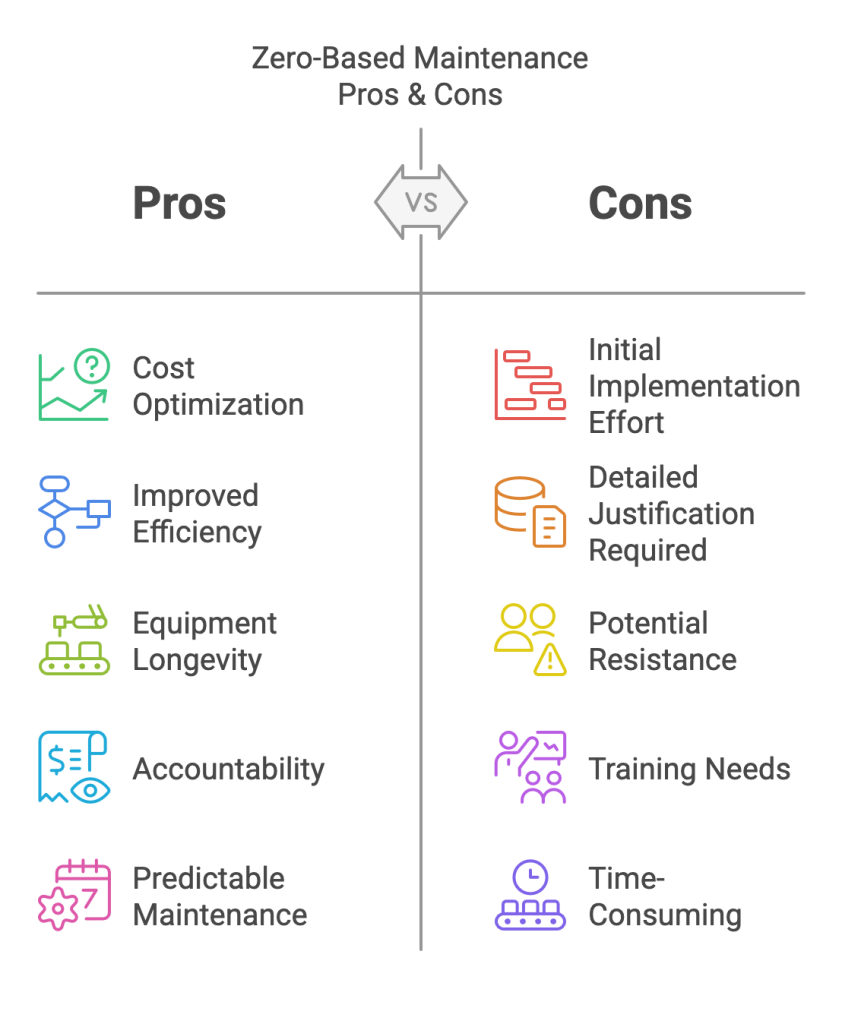
Source: WorkTrek.com
Challenges and Considerations
Implementing zero-based maintenance involves several significant hurdles organizations must overcome to succeed.
These include workforce adaptation, balancing competing priorities, and managing the substantial data requirements.
Cultural Change and Workforce Training
Transitioning to zero-based maintenance requires a fundamental shift in organizational culture. Maintenance teams accustomed to reactive or scheduled maintenance may resist the more rigorous approach.
Staff must develop new skills to implement condition assessments, new maintenance practices, and data-driven decisions effectively. This training demands significant time, investment, and resources. However, it can improve overall operational efficiency.
Management must lead by example and communicate the benefits to gain buy-in from all levels. Without proper support, implementation efforts often fail.
Resistance typically stems from comfort with established routines and fear of increased accountability. Organizations should create comprehensive training programs and provide ongoing support during transition.
Balancing Short-term and Long-term Goals
Zero-based maintenance creates tension between immediate costs and future benefits. The initial implementation requires substantial investment in equipment analysis, training, and possibly new monitoring technologies.
Decision-makers often struggle to justify these upfront expenses despite the long-term efficiency gains and cost reductions. Budget constraints may limit the scope of implementation.
Organizations must develop frameworks to evaluate maintenance decisions based on:
- Total cost of ownership
- Risk assessment
- Equipment criticality
- Production impact
Phased implementation approaches can help balance immediate budget concerns with strategic maintenance goals.
Starting with critical equipment creates early wins that build momentum for wider adoption.
Data Management and Analytics
Zero-based maintenance generates enormous amounts of data that must be collected, stored, and analyzed effectively. Many organizations lack the necessary infrastructure to handle this volume of information.
Selecting appropriate metrics and key performance indicators proves challenging. Teams struggle to translate data into actionable maintenance decisions without proper analytical frameworks.
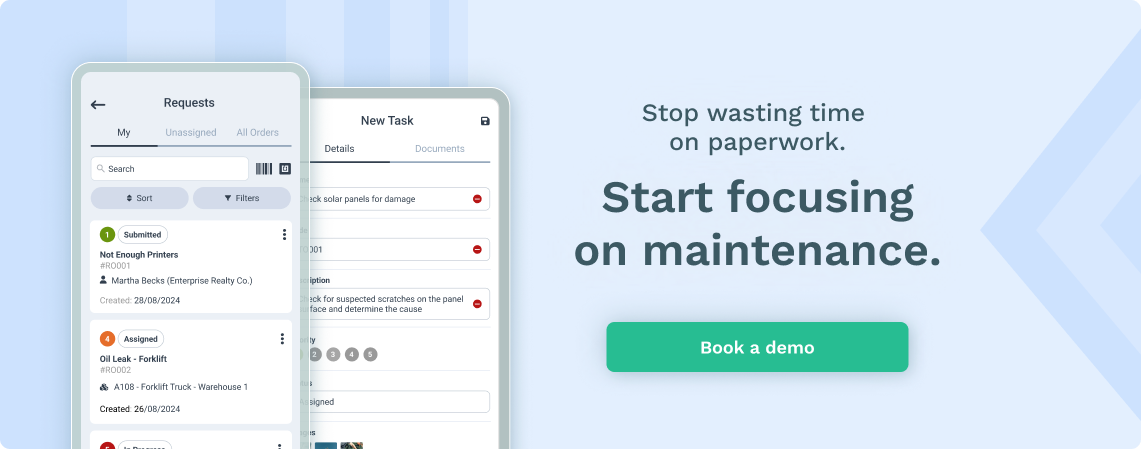
Integration with existing systems often creates technical hurdles. Legacy maintenance management software may not support the detailed tracking required.
Data quality issues frequently undermine analysis efforts. Incomplete or inaccurate information leads to poor decision-making and reduces confidence in the system.
Organizations should invest in robust data governance practices and appropriate analytics tools before full implementation. Starting with standardized data collection methods establishes a foundation for future success.
Tools and Technologies in Zero-Based Maintenance
Modern Zero-Based Maintenance (ZBM) relies on several key technologies to restore equipment to optimal condition. These tools help maintenance teams track, analyze, and optimize maintenance activities.
Computerized Maintenance Management Systems (CMMS) like WorkTrekare the backbone of ZBM programs. These systems track equipment history, schedule maintenance tasks, and store documentation for all assets.
Condition Monitoring Tools like vibration sensors, thermal cameras, and oil analysis equipment help detect potential failures before they occur. This technology supports ZBM’s predictive maintenance aspect.
Enterprise Asset Management (EAM) Software integrates with financial systems to provide the detailed cost tracking necessary for zero-based budgeting in maintenance operations. This integration ensures every maintenance dollar is justified.
Mobile applications enable technicians to access repair procedures, equipment histories, and parts inventories anywhere in the facility. This improves efficiency and data collection accuracy.
Common ZBM Technology Tools:
- Ultrasonic testing equipment
- Infrared thermography devices
- Machine learning algorithms for failure prediction
- Digital twins for equipment simulation
- IoT sensors for real-time monitoring
Data analytics tools process the vast amounts of information generated by these systems. They identify patterns and opportunities to reduce costs and optimize resources through better maintenance scheduling and resource allocation.
Measuring Success and Continuous Improvement
Tracking the right metrics is essential to evaluating the success of zero-based maintenance efforts. Organizations must establish key performance indicators (KPIs) that align with their maintenance goals.
Standard metrics to track include:
- Equipment Effectiveness: OEE (Overall Equipment Effectiveness)
- Maintenance Costs: Before and after implementation
- Downtime Reduction: Frequency and duration
- Mean Time Between Failures: Improved reliability measurements
- Energy Efficiency: Reduced consumption due to optimized equipment
Regular audits help organizations identify areas for improvement in maintenance practices. These audits should compare current performance against the “zero-loss” baseline established during implementation.
Zero-loss thinking encourages teams to view any deviation from perfect performance as an opportunity for improvement. This mindset drives continuous refinement of maintenance processes.
Successful organizations implement feedback loops where maintenance technicians can share insights directly from the field. This hands-on knowledge is invaluable for refining procedures.
Technology plays a crucial role in measurement. Modern CMMS (Computerized Maintenance Management Systems) can automatically track KPIs and generate reports showing progress over time.
Like zero-based budgeting requires justification of expenses, zero-based maintenance requires justification of current practices. Teams should regularly question existing procedures and look for better alternatives.
Get a Free WorkTrek Demo
Let's show you how WorkTrek can help you optimize your maintenance operation.
Try for free