Get a Free WorkTrek Demo
Let's show you how WorkTrek can help you optimize your maintenance operation.
Try for freeA maintenance excellence team can ensure efficient and effective operations for the organization. A successful maintenance team starts with clear goals, effective maintenance practices, and competent, well-trained, and motivated individuals. Setting SMART goals can guide your team toward achieving maintenance excellence.
Engaging key stakeholders in the planning process is crucial. They help identify and address inconsistencies or missed opportunities. This holistic approach ensures the team is aligned and understands the project’s scope and objectives.
Motivating your team with recognition and other strategies can foster an environment of engagement and dedication.
Implement core maintenance processes to build a solid foundation. This groundwork allows for further improvements and refined strategies.
Learning from established practices of high-performing teams can provide valuable insights into achieving excellence in maintenance.
Source: WorkTrek
Understanding Maintenance Excellence
Maintenance excellence is about creating a well-oiled machine of people, processes, and technology to ensure optimal equipment performance and reliability.
A centralized maintenance department is crucial in achieving maintenance excellence by improving efficiency, resource allocation, communication, and equipment integrity and reliability.
Source: WorkTrek
Defining Maintenance Excellence
Maintenance excellence involves a strategic approach to maintaining and improving equipment reliability and efficiency. It requires a blend of best practices, continuous improvement, and proactive measures to minimize downtime and extend the life of equipment.
Key components include:
- Preventive Maintenance: Routine inspections and services to prevent equipment failures.
- Predictive Maintenance: Using data and analytics to predict when equipment might fail.
- Reactive Maintenance: Quickly addressing issues as they arise to reduce downtime.
By integrating these strategies, you can build a robust system that keeps operations running smoothly and efficiently.
Source: WorkTrek
Importance of Maintenance Excellence
Implementing maintenance excellence can significantly boost your organization’s performance. High equipment reliability and efficiency lead to fewer breakdowns, less downtime, and better productivity.
Benefits include:
- Improved Reliability: Consistent performance of machinery reduces interruptions in production.
- Cost Savings: Fewer breakdowns mean less money on emergency repairs and parts.
- Enhanced Safety: Well-maintained equipment lowers the risk of accidents and injuries.
- Operational Efficiency: Streamlined operations result in better use of resources and time.
Fostering a culture of maintenance excellence ensures your team is always equipped to handle challenges and keep equipment running at peak efficiency.
Source: WorkTrek
Building the Foundation of Maintenance Excellence
Establishing a solid foundation for maintenance excellence involves creating reliable leadership and clear standards. Both are crucial in driving an effective team towards common goals.
The Role of Leadership
Leadership is critical in forming a solid maintenance foundation. Leaders should inspire and guide their teams by setting clear visions and objectives. They must encourage a culture of continuous improvement and motivate their staff through recognition and reward.
Influential leaders also ensure that communication flows smoothly across all levels. This helps address any issues quickly and keeps everyone aligned toward common goals.
Consistent training and development programs for maintenance personnel play a significant role in maintaining high performance levels, as they equip team members with the necessary skills.
Moreover, leadership must foster an environment where each team member feels valued. This can be achieved by regularly engaging with the team and showing genuine interest in their work.
Transparency in decision-making and feedback openness are vital components of successful leadership.
Source: WorkTrek
Setting Standards and Expectations
Setting clear standards and expectations is crucial to building maintenance excellence. Start by defining SMART (Specific, Measurable, Achievable, Relevant, Time-bound) goals for the team. These goals act as a roadmap and provide clear direction.
Well-documented maintenance procedures and protocols ensure everyone follows best practices, reducing errors and enhancing efficiency. Regular audits and reviews help maintain these standards and identify areas for improvement.
Source: WorkTrek
Maintenance Tasks Metrics
Performance metrics should be established and communicated clearly.
These metrics keep everyone focused on a systematic approach to achieving goals and help track progress. Providing feedback based on these metrics fosters an environment of accountability.
Enforcing standards consistently is key. The maintenance process becomes more streamlined and effective when everyone understands what is expected and follows the same guidelines.
This consistency ultimately contributes to achieving maintenance excellence for the maintenance staff.
Source: WorkTrek
Developing a Comprehensive Maintenance Plan
Creating a thorough maintenance plan helps ensure that the maintenance personnel are operating and that your facility’s assets operate efficiently, reducing unexpected breakdowns and planning maintenance activities effectively.
It would help if you had well-defined strategies, including preventive and predictive maintenance, and a keen understanding of maintenance planning factors.
Designing a Preventive Maintenance Program
A preventive maintenance program involves routine checks and servicing to prevent equipment failures. List all equipment and systems that need regular maintenance.
Identify critical assets that can significantly impact operations if they fail.
Set a schedule for routine inspections and tasks. Use tools like checklists and software to track maintenance activities.
Develop standardized procedures for each type of equipment, detailing specific tasks, tools required, and safety precautions.
Train your team in these procedures to ensure consistency and effectiveness. Keep detailed records of completed tasks to monitor performance and make necessary adjustments.
Source: WorkTrek
Incorporating Predictive Maintenance Strategies
Predictive maintenance uses data from sensors and machine learning algorithms to anticipate equipment failures before they occur. This strategy enhances predictability, leading to fewer unexpected outages.
Install sensors on critical equipment to monitor temperature, vibration, and pressure.
Data collected from these sensors can be analyzed to predict potential failures.
Implementing this technology requires an initial investment in hardware and software, but the long-term maintenance costs and downtime savings can be substantial. Regularly review the data trends and adjust maintenance schedules accordingly.
Source: WorkTrek
Factors Impacting Maintenance Planning
Several factors influence the effectiveness of a maintenance plan. Equipment age and condition play significant roles; older machinery might require more frequent attention.
Environmental conditions like humidity, temperature, and dust can affect equipment performance and lifespan.
The availability of maintenance resources, including spare parts and skilled technicians, is crucial. Ensure you have a reliable supply chain for parts and invest in ongoing training for your staff. Budget constraints are another consideration. Allocate funds wisely to balance immediate needs and long-term asset management.
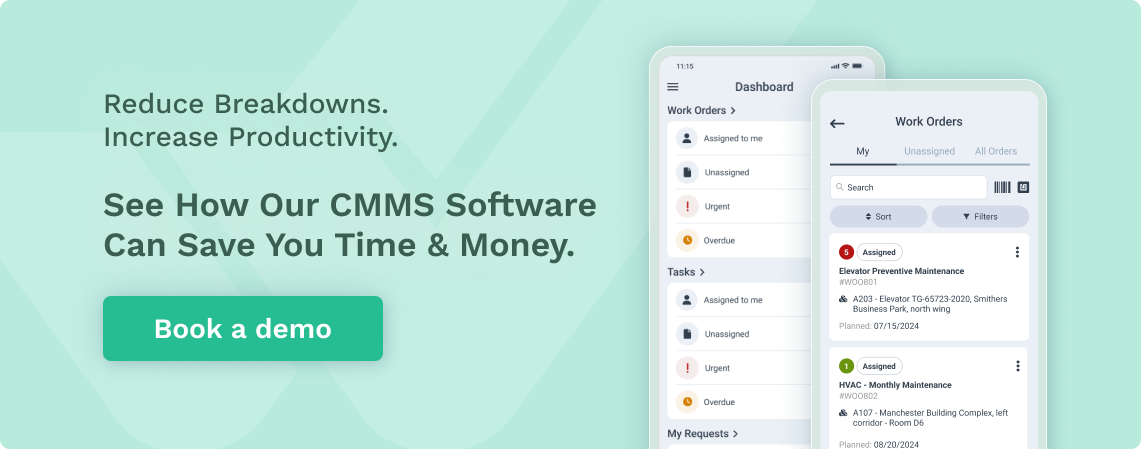
Fostering a culture of continuous improvement is also essential. Review your maintenance processes regularly, gather feedback from your team, and make necessary adjustments to optimize efficiency and effectiveness.
Source: WorkTrek
Structure and Roles in a Maintenance Team
Creating a solid maintenance team requires careful planning of roles and responsibilities. A cross-functional approach can enhance teamwork and efficiency.
Maintenance teams are crucial in implementing maintenance strategies and plans and fostering a culture of operational excellence.
Defining Team Roles and Responsibilities
It’s crucial to define roles within the maintenance team clearly. Each team member should know their tasks and responsibilities. The main roles typically include:
- Maintenance Manager: Oversees the team, sets goals, and ensures tasks are completed on time.
- Technicians: Technicians handle daily maintenance tasks and repairs. Based on skills and experience, technicians might be classified into levels, such as tech 1, tech 2, and tech 3.
- Planners and Schedulers: Develop and maintain maintenance schedules. They ensure tasks are done systematically.
- Safety Officers: Make sure all safety protocols are followed.
Defined roles help prevent confusion and ensure everyone knows what is expected of them. This structure supports efficiency and accountability within the team.
Source: WorkTrek
The Importance of Cross-Functional Teams
Cross-functional teams bring together people with different skills. This means combining technical skills, planning abilities, and safety knowledge in a maintenance team.
- Enhanced Problem-Solving: When people with different specialties work together, they can solve problems more effectively.
- Skill Development: Working in a diverse team helps members learn new skills from each other. This can be especially important for ongoing training and growth.
- Flexibility: Cross-functional teams can adapt to different challenges. If a technician understands planning, they can step in if the planner is unavailable.
Building a cross-functional team helps create a more resilient and capable maintenance team. It ensures that all aspects of maintenance are covered, from technical tasks to safety measures.
Source: WorkTrek
Effective Maintenance Operations Management
Effective maintenance operations management is crucial for ensuring your equipment’s optimal performance and maximizing uptime. This involves careful planning, resource allocation, and scheduling.
Ensuring Equipment Performance
Maintaining high equipment performance starts with regular inspections and preventive maintenance. By identifying potential issues before they become serious problems, unexpected downtime can be reduced.
Use condition monitoring tools to track the health of your machines. Technologies like vibration analysis and thermal imaging can detect early signs of wear or damage. Regularly update maintenance logs to spot trends and address recurring issues.
Training your team on proper equipment use and maintenance procedures is also key. Create standard operating procedures (SOPs) to ensure everyone follows the same practices. This consistency helps maintain performance and extend the equipment’s lifespan.
Source: WorkTrek
Optimizing Scheduling and Resources
Efficient scheduling ensures that maintenance tasks are completed without disrupting production. Implement computerized maintenance management systems (CMMS) to streamline scheduling and manage resources effectively.
Classify tasks based on their urgency and importance. Emergency repairs should be prioritized, while routine checks and minor repairs can be scheduled during low production periods.
This strategy minimizes downtime and maximizes productivity.
Additionally, allocate resources wisely by keeping an inventory of spare parts and tools.
Having suitable materials on hand reduces delays and keeps operations running smoothly. Assign roles and responsibilities clearly so that everyone knows their tasks, ensuring coordinated efforts and efficient use of manpower.
Source: WorkTrek
Maintenance Tools and Technology
Staying updated with the latest tools and technologies is crucial for a high-performing maintenance team. These innovations improve efficiency, safety, and predictive capabilities.
Leveraging a Computerized Maintenance Management System
A Computerized Maintenance Management System (CMMS) is essential for organizing and streamlining maintenance tasks.
A CMMS helps you schedule preventive maintenance, track work orders, and manage inventory. By centralizing information, a CMMS ensures you never miss critical maintenance due dates, reducing downtime and unexpected failures. For example, setting SMART goals can be facilitated by tracking progress and identifying trends using CMMS tools like Fiix or MaintWiz.
Source: WorkTrek
Benefits of CMMS:
- Improved Scheduling: Automate maintenance schedules.
- Inventory Management: Track parts and supplies efficiently.
- Data Analysis: Leverage data to make informed decisions.
A CMMS tool can optimize workflows, making your maintenance team more responsive and efficient.
Source: WorkTrek
The Impact of Emerging Technologies
Emerging technologies are transforming maintenance practices, making them more proactive and less reactive.
Artificial Intelligence (AI) and Machine Learning (ML) can analyze data patterns to predict equipment failures before they occur.
Virtual Reality (VR) and Augmented Reality (AR) offer immersive training experiences, helping your team learn complex tasks in a controlled environment. Tools like AI and VR are becoming integral, providing real-time diagnostics and remote support.
Key Technologies:
- AI & ML: For predictive maintenance.
- VR & AR: For interactive training.
- IoT Devices: These are used for real-time monitoring of equipment.
Embracing these technologies enables your maintenance team to avoid potential issues, ensuring smoother operations and reducing downtime.
Source: WorkTrek
Ensuring Quality and Compliance
Quality and compliance in maintenance programs are essential to ensure safety and effectiveness. By adhering to standards and continuously improving processes, you can maintain high performance levels and avoid costly errors.
Adhering to Safety Protocols and Standards
Maintaining safety is critical in any maintenance operation. You must ensure all staff are trained in safety protocols and adhere to industry standards. This includes using proper personal protective equipment (PPE) and following guidelines for equipment use.
Safety protocols minimize accidents and downtime. Regular safety training sessions keep safety practices fresh in employees’ minds.
Utilizing tools like thermographic cameras for inspections can also enhance safety by detecting issues early. Strict documentation practices help track compliance and manage potential hazards efficiently.
Source: Safety in Maintenance: An Improvement Framework
Maintenance Audits and Continuous Improvement
Conduct regular maintenance audits to evaluate the effectiveness of your procedures.
These audits should identify inefficiencies and areas needing improvement. Implementing the findings can lead to a more efficient and safer maintenance process.
Continuous improvement involves regularly updating maintenance techniques and tools. Structured problem-solving methods, such as Pareto and Ishikawa, can be used to analyze data and address root causes.
Source: AlisQI
Encouraging a culture of openness and regular feedback ensures that improvements are sustained over time.
Focusing on these areas ensures that quality and compliance are upheld in your maintenance operations, leading to sustained success and safety.
Maximizing Maintenance Budget Efficiency
Effective maintenance budget efficiency involves meticulous planning and controls, as well as strategic cost-cutting measures that do not compromise the quality of maintenance operations.
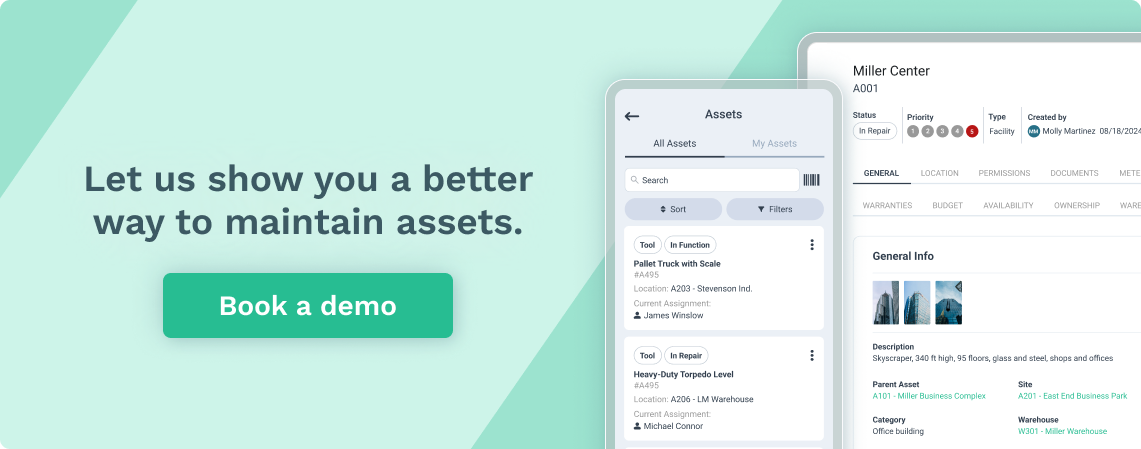
Budget Planning and Control
Start by setting realistic and achievable goals for your maintenance budget. Identify critical equipment and prioritize spending accordingly. Use historical data to forecast future maintenance costs accurately.
For instance, comparing maintenance cost (MC) to your equipment’s replacement asset value (RAV), as noted in a Baker Hughes study, can help you keep MC between 2% and 5% of RAV.
Source: WorkTrek
Create a detailed budget that includes all potential costs, from labor to equipment replacement. Regularly monitor and update your budget based on actual performance to ensure you stay within limits. Software tools can help automate tracking and reporting, making budget control more effective.
Cutting Costs Without Compromising Quality
To reduce costs, consider implementing a proactive maintenance strategy, which includes preventive and predictive maintenance. Educating your team on best practices such as root cause analysis can prevent recurring issues, saving time and money. Additionally, using in-house training can cut costs further than outsourced services.
Source: WorkTrek
Another strategy is to invest in efficient, high-quality tools and materials. This may have a higher upfront cost but reduces long-term maintenance expenses. You should also regularly review your supply chain and negotiate with vendors for better rates. Applying these strategies ensures cost efficiency without sacrificing the quality of your maintenance operations.
Communication and Problem-Solving Skills
Strong communication and effective problem-solving skills are crucial in building a maintenance excellence team. Clear communication enables team members to understand tasks and expectations, while efficient problem-solving helps resolve issues swiftly.
Fostering Clear Communication
Clear communication is key to ensuring all team members are on the same page. To achieve this, use simple and direct language and avoid jargon that may confuse some team members.
Regular meetings, such as daily standups, are also essential. These meetings allow team members to share updates, ask questions, and discuss issues.
Using digital communication tools can also help. Tools like Slack or Microsoft Teams enable quick and efficient communication. They ensure everyone can be reached, regardless of where they are.
Encourage an open-door policy. This approach makes team members feel comfortable seeking guidance and sharing ideas, creating an environment where everyone feels valued and heard.
Source: WorkTrek
Effective Maintenance Troubleshooting
A structured approach is essential for maintenance troubleshooting. Start by training your team in problem-solving techniques. Methods like Pareto analysis and Ishikawa diagrams help identify root causes.
Invest in continuous technical training for your team. Keeping up-to-date with the latest maintenance techniques, tools, and technologies ensures your team can handle any issue.
Having a step-by-step troubleshooting guide can also be beneficial. This guide should outline procedures for diagnosing and fixing common problems.
Encourage teamwork during troubleshooting. Team members can pool their knowledge and skills to find solutions faster when collaborating.
Effective troubleshooting resolves issues and prevents recurring problems, ensuring smoother operations.
Maintenance Team Development and Growth
Effective maintenance team development involves continuous training and initiatives to keep the team motivated and recognized. Fostering both personal and professional growth is crucial for building a high-performing team.
Training and Professional Development
Regular training sessions ensure your team stays updated with the latest maintenance techniques, tools, and technologies. Providing opportunities for professional development, like obtaining industry-specific certifications, helps keep skills sharp and relevant.
Encouraging cross-training among team members boosts versatility and helps the team adapt to various tasks. Establishing mentorship programs allows experienced members to pass on valuable knowledge, building a more confident and well-rounded team. Regular updates and new training programs can significantly enhance technical and soft skills, like communication and problem-solving.
Recognition and Motivation
Motivating your team through recognition of their efforts plays a key role in maintaining a high-performing maintenance team. Implementing an appreciation system where achievements are acknowledged boosts morale and fosters a sense of camaraderie among team members.
Provide regular feedback and celebrate milestones. Set up formal rewards, such as bonuses or promotions, and informal ones, like team outings or shout-outs during meetings. Ensuring that your team feels valued and appreciated helps maintain high motivation and dedication towards their work.
Source: WorkTrek
Measuring Maintenance Success
Measuring the success of your maintenance team is essential to ensure ongoing efficiency and improvement. Focus on using key performance indicators (KPIs) and regular performance reviews to track and enhance your team’s effectiveness.
Understanding Key Performance Indicators (KPIs)
Key performance indicators (KPIs) are vital metrics that help you evaluate your maintenance team’s performance. KPIs provide quantitative data that reveals how well the team meets its goals.
Common KPIs include:
- Equipment uptime,
- Maintenance backlog,
- Mean time to repair (MTTR)
- Preventive maintenance compliance. By tracking these metrics, you can identify areas where your team excels and where improvements are needed.
For example, a low MTTR indicates efficient repair processes, while high preventive maintenance compliance ensures scheduled tasks are completed on time. Using KPIs allows you to make data-driven decisions to improve your maintenance strategy.
Source: WorkTrek
Maintenance Metrics and Performance Reviews
Maintenance metrics involve the data collected from various KPIs, providing a comprehensive view of your team’s performance. Regular performance reviews using these metrics are critical.
During performance reviews, focus on metrics like work order completion rates, technician productivity, and the overall cost of maintenance activities. These reviews facilitate constructive feedback and help set goals for improvement.
Create a feedback loop where team members can discuss challenges and successes. This promotes a culture of continuous improvement.
By evaluating key metrics regularly, you ensure that your maintenance operations align with your business goals and achieve maximum efficiency. For more on building a high-performance team, visit maintenance team creation.
You build a framework that continuously drives operational success by emphasizing KPIs and maintenance metrics.
Leveraging Feedback and Insights
Understanding and utilizing feedback from all levels of the maintenance team is critical. By acting on user and equipment feedback, you can significantly improve your maintenance operations and achieve excellence.
From Upper Management to Technicians
Communication between upper management and technicians is key. Upper management must be open to receiving feedback from technicians on the frontline who perform daily maintenance tasks.
This feedback allows upper management to provide valuable resources and set priorities.
Regular meetings encourage the exchange of ideas. Surveys and suggestion boxes can also be helpful for anonymous feedback. Clearly define goals so everyone works towards the same targets.
Technicians should feel comfortable sharing their insights on maintenance issues and troubleshooting. This creates a culture of continuous improvement.
By valuing the feedback from technicians, you ensure they stay engaged and motivated, contributing to maintenance excellence.
Source: WorkTrek
Acting on User and Equipment Feedback
Using data from equipment is essential. Condition monitoring tools can provide real-time feedback on machinery health. This data helps in predictive maintenance, allowing you to fix issues before they escalate.
User feedback, especially from operators, provides insights into how equipment performs in actual use. Listening and acting on this feedback can prevent future breakdowns. Analyze the data collected from both users and equipment to identify patterns.
After gathering feedback, create an action plan. Prioritize issues based on their impact and implement solutions. Regularly review the input and update your maintenance practices. Ensuring timely responses to feedback builds trust and enhances maintenance efficiency.
Source: WorkTrek