Get a Free WorkTrek Demo
Let's show you how WorkTrek can help you optimize your maintenance operation.
Try for freeKey Takeaways:
- A CMMS with mobile access can eliminate unnecessary and cumbersome tasks.
- Many facility managers find work order tracking too time-consuming.
- Spreadsheets and similar tools can’t keep up with modern maintenance needs.
With equipment becoming more complex daily and skilled upkeep workers in short supply, optimizing maintenance can no longer be put off.
Unplanned downtime, delays, and budget overruns are a constant threat for those who don’t take control of their assets and upkeep.
That’s where a CMMS comes in.
This powerful tool helps businesses streamline operations, slash downtime, and extend the life of critical assets.
So, keep reading to discover what a CMMS is, its must-have features, and tips for successful implementation.
Whether you’re looking to cut costs, prevent unexpected breakdowns, or boost efficiency, a CMMS is exactly what you need.
What Is a CMMS?
A Computerized Maintenance Management System (CMMS) is a significant game-changer in the maintenance world.
It’s specifically designed to centralize maintenance information, streamline upkeep processes, and improve asset management within an organization.
It serves maintenance professionals across various industries, helping manage tools, equipment, fleets, systems, and facilities.
In short, a CMMS can benefit operations that rely on large or small assets.
Many companies seem to be already well aware of those benefits.
According to a 2024 report from the Institution of Mechanical Engineers, 62% now use a CMMS.

The primary advantage of a CMMS is its ability to replace inefficient, manual maintenance processes, which are often tedious and prone to human error.
William Matthews, Regional Asset and Lifecycle Manager at Kerry, an Ireland-based public food company, agrees.
He maintains that tools like Excel can’t keep up with modern needs.

Put simply, a CMMS unlocks unparalleled efficiency, accuracy, and accessibility across entire maintenance operations.
With this technology, you can finally say goodbye to lost work orders, forgotten repairs, and guesswork.
Key Features of a CMMS
Of course, a CMMS’s benefits stem from its features, which improve various aspects of your upkeep operations.
Let’s explore the most significant ones.
Work Order Management
This feature allows maintenance personnel to easily create, assign, prioritize, and track work orders in real time.
As a result, tasks get completed more efficiently, while delays, confusion, and miscommunication are minimized.
This feature enables you to set up templates with required fields, ensuring that no critical data is overlooked.
Typically, there are fields for priority levels, assigned workers, planned materials and costs, signatures, and more, just like in the example below.

Additionally, you can attach photos, documents, and comments, ensuring technicians have all the information they need to complete their tasks correctly.
Checking WO status is equally easy.
From the moment a work order is created to its completion, all stakeholders can quickly look it up from anywhere and anytime.
A 2024 JLL Technologies report hints at how game-changing automated WO management can be, particularly in facilities management.
As it turns out, FMs are drowning in work orders, with tracking their progress and status ranked as the most time-consuming part of their job.

A CMMS fixes that.
Everyone involved can access and update vital information anytime, accelerating task completion.
With automated work order management, operations simply run much more smoothly.
Preventive Maintenance
A CMMS makes proactive maintenance easier than ever by automating the planning and scheduling of recurring tasks.
That way, you reduce the risk of unexpected breakdowns, lowering repair costs and downtime.
WorkTrek, our CMMS, supports this function too.
For instance, you can schedule service and inspections based on time triggers, which means you can decide whether you want the task to repeat daily, weekly, monthly, or yearly:

You can also specify the planned duration and end rule for maximum efficiency.
Alternatively, you can set schedules based on meter readings, ensuring maintenance occurs after specific usage hours, mileage, temperature, pressure, or other factors:

In any case, with WorkTrek, you ensure each asset gets the care it needs, exactly when it needs it.
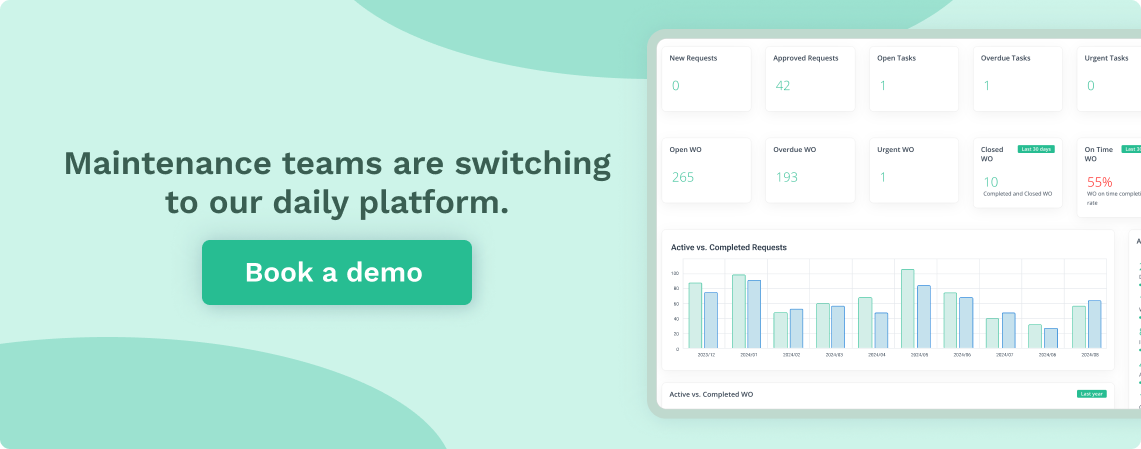
This improves your upkeep planning and scheduling and saves you money in the long run.
Terri Ghio, former President of the manufacturing optimization solution FactoryEye North America, illustrates this point with an example:

That’s where a CMMS like WorkTrek comes in. It helps you track every asset’s needs and keeps your entire team proactive.
Inventory Management
The inventory management feature lets you manage and track spare parts, their locations, stock levels, and supplier details from one centralized platform.
You can see what that might look like in the image below:

Everything is right at your fingertips, from make and model to quantity and user manuals.
Some systems even send real-time alerts when stock levels are low, allowing you to restock on time and avoid costly operational disruptions.
Given just these elements, this feature makes it significantly easier to prevent stockouts or overstocking, optimizing spare parts usage and cost control.
As such, it transforms your inventory from a necessary expense into a strategic asset.
According to a 2024 Veruson report, 71% of organizations believe MRO management should be treated as a strategic initiative rather than just an operational necessity.
However, only 54% report having full visibility into their MRO materials, including consumption patterns, utilization, maintenance schedules, and personnel involved in upkeep.
This is a problem because, without that kind of visibility, unlocking the full potential of your inventory is practically impossible.
Luckily, with a CMMS, that all changes.
These solutions show you precisely what you have, how much, where, and how it’s being used, enabling you to allocate resources more strategically.
Reporting and Analytics
The analytics and reporting feature delivers valuable insights into your maintenance efforts by automating the collection, analysis, and visualization of relevant upkeep data.
As such, it helps you track key performance indicators, uncover hidden inefficiencies, and, ultimately, optimize maintenance processes.
Typically, interactive dashboards give you a consolidated view of your operations’ activities.
For example, here, you can quickly look up WO status, active requests, and more:

However, if you want to dig a bit deeper, you can also use pre-built KPIs and reports for a more detailed performance and cost analysis.
Some solutions even enable you to schedule these reports to be automatically delivered via email at specified intervals.
That way, keeping everyone in the loop becomes so much easier.
These insights aren’t just numbers on paper but can be leveraged to improve various aspects of your operations, such as costs, downtime, or spare parts usage.
For instance, Tim Newman, Maintenance Manager at Simmons Feed Ingredients, a supplier of poultry, pet, and ingredient products, uses this information for better planning and scheduling:

Put simply, with this feature, you no longer have to rely on gut instinct when making decisions.
Instead, you can trust reliable, data-backed insights to guide you, giving you the confidence to make informed choices every time.
Mobile Access
Mobile access allows technicians to use all CMMS features on their smartphones and tablets.
This significantly boosts their overall flexibility, allowing them to update and access crucial data easily while on the go.
They can create requests, look up information, take photos of assets or completed work on-site, and attach them to the work order—all with just a couple of taps on their mobile device:

Some solutions offer offline functionality, enabling workers to work without cellular or Wi-Fi connections.
Danielle Rivers, Director of Business Services at Camden Property Trust, a multifamily real estate company, shares that mobile apps have boosted productivity within her upkeep team:
She explains that technicians no longer need to visit the office to print work orders or pick up keys, complete tasks, fill out forms, and return to close the job.
Now, they can view their assignments, track progress, report complications, and close out tasks—from the palm of their hand.
For a typical field worker, that’s a huge difference in terms of productivity.
Tips for Successful Implementation
To unlock a CMMS’s advantages, you need to implement and integrate it effectively into your processes.
Here are some tips on how to do this.
Define Clear Goals
Before evaluating potential CMMS solutions, it’s important to identify the key challenges you need to address and establish relevant KPIs.
If you skip this step, assessing whether the system is solving your problems will be very difficult, leading to wasted time and resources.
A 2023 Microsoft study found that 98% of leaders use some form of goal-setting framework, demonstrating that goal clarity is essential for any project.
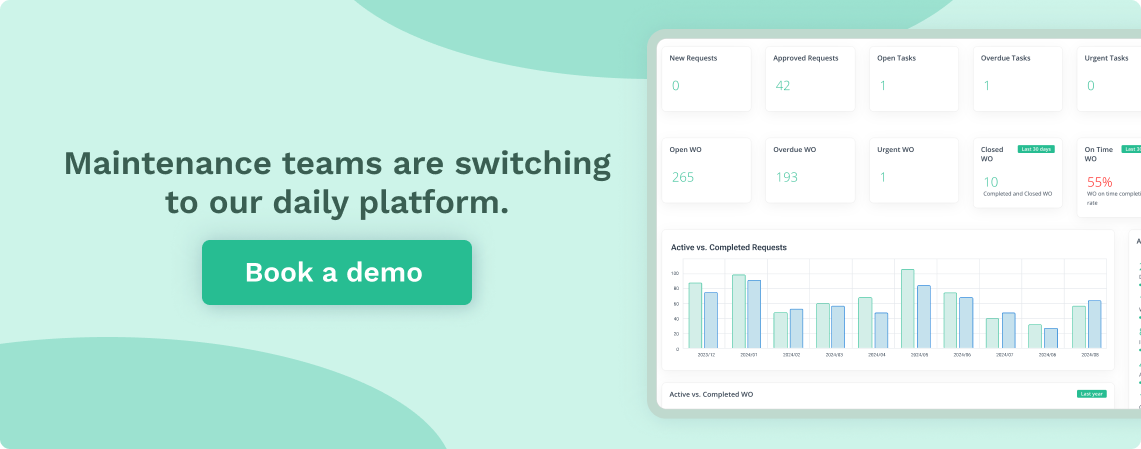
One effective framework to consider is the SMART criteria, which helps ensure your goals are realistic and achievable.
Here’s a breakdown of SMART:
Specific | Define exactly what you want to achieve (e.g., “Reduce unplanned equipment downtime”) |
Measurable | Identify clear metrics (e.g., “Reduce unplanned equipment downtime by 20%“) |
Achievable | Ensure the goal is realistic, considering the resources and time available (Given your current maintenance team size and existing tools, is this reduction feasible?) |
Relevant | Make sure the goal supports broader business objectives (e.g., if your company’s goal is to increase production efficiency and minimize costs, then reducing downtime would align with those objectives) |
Time-bound | Set a specific deadline for achieving the goal (e.g., “Reduce unplanned equipment downtime by 20% within the next 12 months) |
Once these goals are defined, you can establish KPIs to track progress toward meeting them.
For example, if your goal is to reduce unplanned downtime, relevant KPIs could include metrics such as:
- Mean Time Between Failures (MTBF)
- equipment availability
- the ratio of planned vs. unplanned work orders
When you implement your CMMS solution, you can revisit these goals and metrics to evaluate whether your targets are being met.
This way, you ensure that your efforts align with your desired outcomes.
Choose The Right Software
Your chosen software should be user-friendly and tailored to your company’s needs and workflows.
If you select the wrong one, you could end up with a system that’s either too complex or lacks essential features, hindering adoption and overall performance.
This problem is more common than you might think.
According to Capterra’s 2024 survey, 58% of U.S. buyers regret at least one software purchase.
These wrong decisions often lead to severe consequences, such as reduced competitiveness, excessive costs, and employee dissatisfaction.
To avoid making the same mistake with your CMMS, conducting thorough research is crucial.
Carefully evaluate each candidate’s features and pricing, keeping your goals in mind.
But don’t stop there.
Look at online reviews—like the one below—to gauge the user-friendliness, customer support quality, and overall experience of other users.

Such insights can provide a clearer picture of the software’s true performance.
For solutions that meet your requirements, fit your budget, and have positive reviews, check if they offer a free trial or demo.
There’s no better way to assess a solution than by trying it out yourself.
This will allow you to evaluate its ease of use, gather feedback from your team, and make a fully informed decision before committing to the purchase.
Monitor Progress
Even after the software has been purchased and implemented, the work doesn’t end.
At this stage, it’s best to monitor system usage and analyze user feedback to improve workflows where necessary.
If this isn’t done, inefficiencies may persist, and employees might eventually abandon the system altogether.
According to a Userlane 2023 survey, the average employee loses 2.33 hours per week due to software-related challenges, resulting in hundreds of thousands of hours wasted yearly.
If you don’t track post-implementation performance, you risk facing similar inefficiencies.
In fact, you might end up like the company described by this Reddit user.
From their post, it seems their upkeep management solution isn’t working as intended, yet no one is paying attention or addressing the issue:

Don’t let things get to this level of chaos.
Instead, revisit the KPIs and goals you set earlier and see if they are being met.
If not, this could be a sign that the software is underperforming.
In that case, contact your team for feedback on software usability, work order processes, and any bottlenecks.
After all, it’s better if they talk to you directly than vent on social media.
Together, you can address the problems and ensure you get the most out of your CMMS.
Often, you need simple fixes, such as providing additional training on using certain features or tweaking system settings to match your workflows better.
Conclusion
All things considered, CMMS solutions are undoubtedly the future of maintenance.
They can streamline nearly every aspect of asset upkeep, boosting efficiency, reducing errors, and keeping your equipment and facilities in peak condition.
Once you see what a CMMS can do for your operations, you’ll never be able to imagine being without it—nor will your maintenance team.