Get a Free WorkTrek Demo
Let's show you how WorkTrek can help you optimize your maintenance operation.
Try for freeEffective maintenance planning for a facility is essential to keep industrial or agricultural facilities in good condition. In particular, it makes it possible to avoid breakdowns, while minimizing downtime. The latter generally generate high additional costs due to the decrease in productivity of the installations, but also of the employees. However, while beneficial to businesses of all sizes, the facility maintenance plan can produce the opposite effect to that intended when it has not been established effectively. On the one hand, maintaining more than necessary equipment wastes time that could have been devoted to other tasks. On the other hand, not maintaining equipment sufficiently increases the risk of failure. Having a plan in place that takes into account the following factors will ensure that you find the right measure.
Inventory Of All Assets At the Facility To Be Maintained
To set up an optimal plan for the facility, it is first necessary to carry out an inventory of all the tools on which maintenance must be carried out in order to not omit any asset essential to the proper functioning of the production chain. Depending on the size of the industrial or agricultural company and the number of installations in its possession, the complexity of the maintenance plan can vary greatly. In the most complex cases, it is strongly recommended to segment this inventory by sector or production unit in order to be able to manage sets of acceptable complexity.
Definition And Prioritization Of Facility Maintenance Tasks
It is essential to define all the facility maintenance tasks to be carried out on each asset, as well as their frequency and the skills required. These will allow tasks to be assigned to technicians with the right skills. In addition, a prioritization of tasks can be useful in the most complex cases. You need to determine the tasks to be carried out and those to be postponed in the event of a lack of resources. The purpose of this prioritization is to better organize the maintenance work. That leads to better efficiency, reduction of stress in the teams, and easier management of unforeseen events.
Setting Up A Facility Maintenance Schedule In the Maintenance Plan
To be effective in business and optimize your time, you have to know how to be organized. There are precise maintenance schedules provided for this purpose! Before understanding why and how to deploy this tool in your facility, let’s find out what this type of planning consists of and its difference from a maintenance plan.
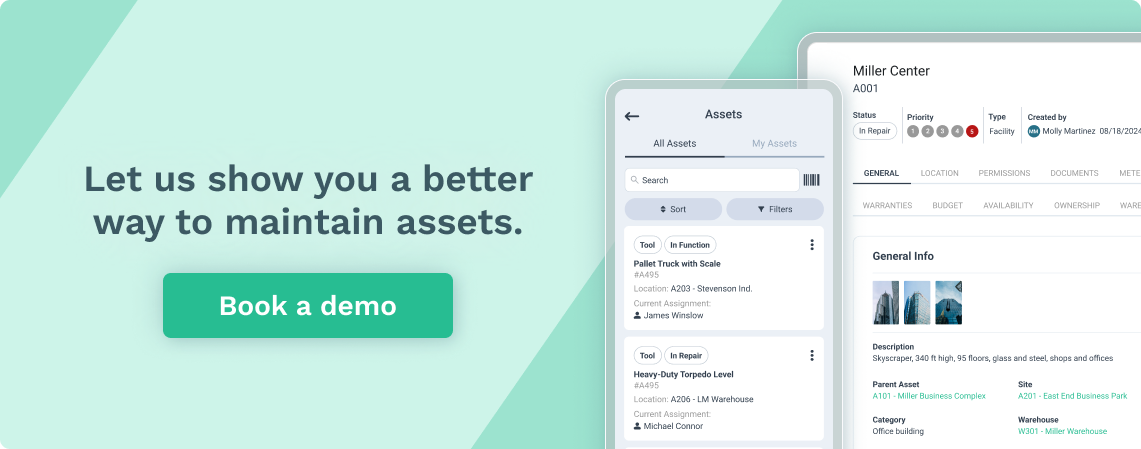
What is a maintenance schedule?
We call the maintenance schedule the document which makes it possible to organize the assignment of technicians to the maintenance tasks of the various equipment. This assignment can be done on a daily, weekly, or monthly basis depending on the equipment concerned. Some of them require daily maintenance while for others, monthly or even annual maintenance is sufficient. A maintenance schedule usually takes the form of a calendar or a table, hence its name schedule. This name is often mistakenly confused with the maintenance plan. However, these two documents do not have the same objective at all, but the maintenance schedule is part of maintenance planning – they complement each other.
The maintenance plan does not have the calendar function that the schedule has. Rather, it is a program that lists resources, procedures, and recommendations for maintenance tasks. This plan will specify, for example, the equipment concerned with maintenance, at what period it will have to be maintained, the equipment required for the intervention, and the budget to be provided. In other words, the maintenance plan indicates the procedure to be followed while the schedule represents the timetable for visualizing recurring or urgent interventions.
Why set up a maintenance schedule in a facility maintenance plan?
Maintenance is a crucial stake in the proper functioning of the facility, its planning is a precious tool with multiple advantages. Thanks to a good maintenance schedule, the team in charge of it (or the management of service providers) can organize itself correctly, better anticipate unforeseen events, respect everyone’s working time and be more reactive in the event of a technical emergency. The advantages of a rigorously established maintenance schedule in a facility maintenance plan are therefore the following:
- Prioritization of all maintenance activities to be able to intervene where and when necessary.
- The provision of room for maneuvering, additional safety for the technician, and the equipment being maintained.
- An extension of the life of equipment thanks to regular checks and adjustments.
- A better distribution of the workload of each technician. The maintenance schedule allows you to see at a glance who is assigned to each task. So you can see if there are particularly large variations in workload from one technician to another.
- Better management of tasks in the event of personal unforeseen events. If one of your technicians or service providers is unavailable, you can easily identify the person who can replace this person for the planned intervention(s).
More advantages:
- Optimization of maintenance rounds, geographically. By knowing that such a technician will intervene at such a place on such a day, you group several interventions and avoid unnecessary back and forth. This optimization saves time, and energy and reduces intervention costs.
- Improved customer satisfaction by preventing your equipment from breaking down and therefore slowing down production or causing poor workmanship.
- Better working conditions for your employees thanks to controlled, functional, and secure equipment.
- Better working conditions also for your technicians and your subcontractors, thanks to a better organization of their schedule and a good distribution of tasks. Your maintenance staff will benefit from real-time visibility. However, communication is one of the keys to efficiency and professional well-being!
How to set up a facility maintenance schedule?
Providing an effective maintenance schedule requires following several major steps. First, be sure to schedule all recurring transactions, those that occur on a regular basis. To do this, provide yourself with maintenance plans indicating precisely the deadlines to be respected for each piece of equipment, choose the interventions, and identify the technician(s) to be assigned. Second, make sure you have a safety margin. This will translate concretely into available slots “just in case”. Equipment may experience a breakdown or malfunction, and being able to have a time slot for urgent intervention is therefore more than reassuring to be able to be reactive. Then plan those famous emergency interventions. To do this, you will need to clearly identify the problem to indicate its level of priority, order any spare parts, and inspect the place of the intervention to inform the technician who will proceed with it.
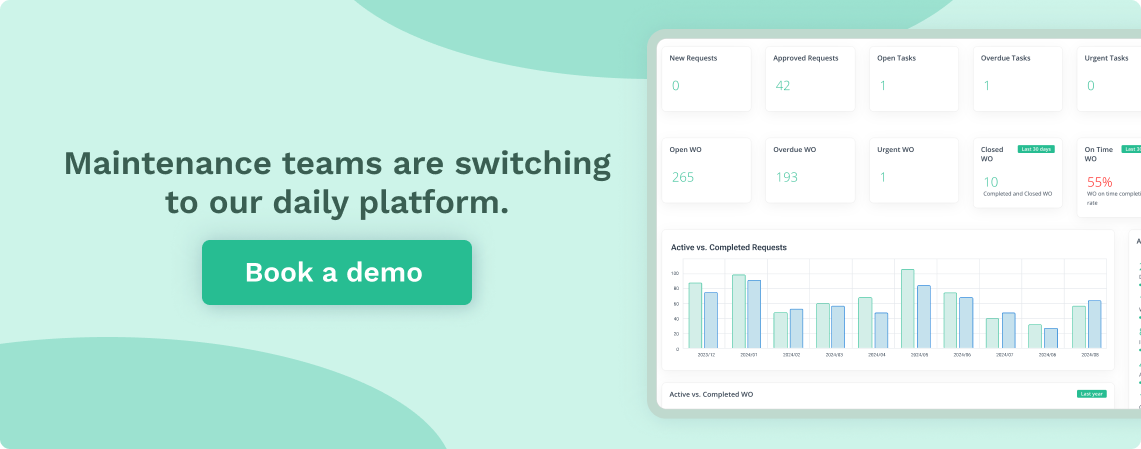
Finally, do not forget, a posteriori, to analyze what will have been done. Performance indicators such as the expenses incurred or the downtime of the equipment concerned will allow you to have an overall follow-up and better optimize your maintenance schedule over time. This will allow you to know, for example, the actual number of hours to be expected for the repair of such or such equipment.
Definition Of Facility Maintenance Procedures And Instructions
To guarantee the quality and efficiency of maintenance work, it is essential that technicians carry out all the prescribed operations correctly, regardless of who is involved. The establishment of standard operating procedures (SOPs) makes it possible to achieve this objective. The way to accomplish each task and the quality criteria to be met must be explicitly defined in this document. In this way, you guarantee the proper functioning of each installation and avoid too frequent stoppages of your production tool.
A Qualified Workforce And Formalized Skills
The equipment of industrial or agricultural facilities, whether small or large, can be affected by mechanical, electrical, or electronic problems. In addition, some installations require skills that can only be acquired through dedicated training. It is therefore essential that the various maintenance tasks be entrusted to technicians with these specific skills. The integration into the facility maintenance plan of the skills required for each task as well as for each technician makes it possible to plan interventions appropriately and to anticipate the recruitment of future technicians or their training. Indeed, you will easily find that you need an additional mechanic if the resources are systematically lacking in the mechanical tasks.
Spare Parts Management
The immobilization of your production tool because of an unavailable spare part is a real risk. With this in mind, maintenance planning makes it possible to anticipate the parts to have in stock for the various maintenance interventions. The objective is to have permanent availability of worn parts and sensitive components. A well-established maintenance plan, therefore, contributes to the effective management of the stock of spare parts.
Use Of Maintenance Management Software
The use of computer-aided maintenance management software (CMMS), such as WorkTrek, facilitates the planning of your maintenance. They generally make it possible to manage interventions, workers, equipment, stocks, and purchases and even have indicators and statistics to optimize your management. Excel remains an adequate solution for small structures, although it is less complete and less automated than dedicated software.