Get a Free WorkTrek Demo
Let's show you how WorkTrek can help you optimize your maintenance operation.
Try for freeAs a maintenance manager, you work hard to keep your facility in top shape, constantly monitoring and doing the necessary work to fix problems before they arise.
A smarter approach is to prevent issues before they happen. This is where proactive maintenance comes in.
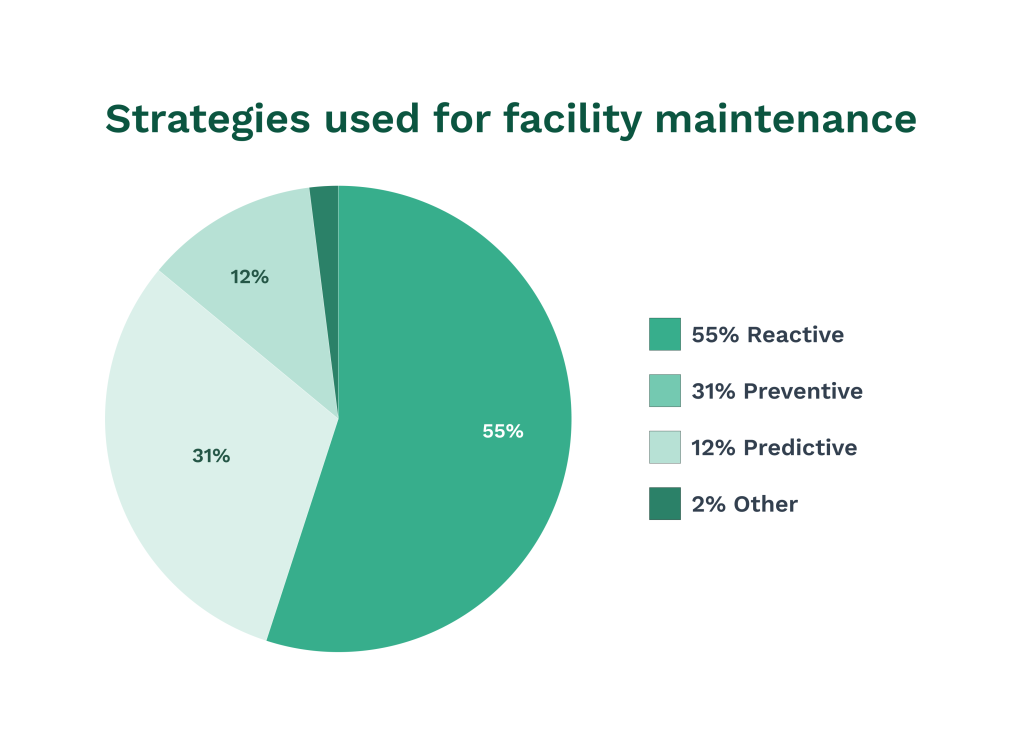
Proactive maintenance involves regular checks and upkeep to stop equipment breakdowns before they occur.
It’s about avoiding potential problems rather than just reacting to them. This method can save money, time, and stress in the long run.
Setting up a proactive maintenance plan may seem like a big task, but it’s worth the effort. You can create a system that keeps your facility running smoothly with the right steps. Let’s explore how to put this helpful strategy into action.
Key Takeaways
- Regular equipment checks prevent costly breakdowns
- Data analysis helps predict and avoid maintenance issues
- Using the right tech tools makes proactive maintenance easier
Understanding Proactive Maintenance
Proactive maintenance is a key strategy for keeping facilities running smoothly and planning future maintenance needs better.
It focuses on preventing problems before they occur.
Proactive maintenance practices can save money, reduce downtime, and ensure equipment reliability and operational efficiency.
Definition and Importance
Proactive maintenance is a method that aims to prevent equipment failures before they happen so you can minimize downtime. It is a strategy best reserved for the most critical assets.
It involves regular checks and upkeep of machinery and systems.
This type of preventive maintenance is crucial for facilities because it helps avoid costly breakdowns and equipment failures.
Proactive maintenance includes several key activities:
- Regular inspections
- Cleaning and lubricating parts
- Replacing worn components
- Monitoring equipment performance
- Performing routine maintenance
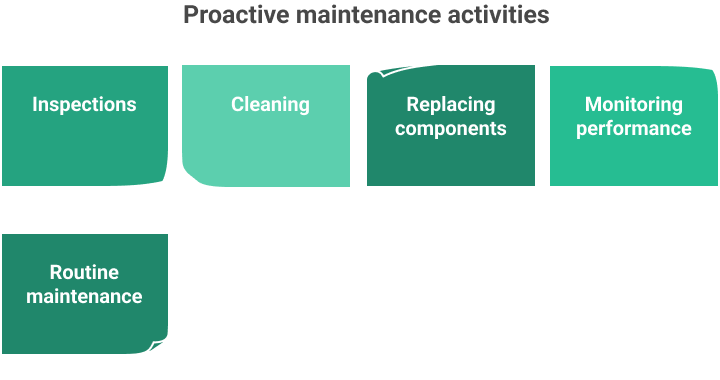
By doing these tasks, facilities can spot potential issues early. This allows them to fix problems when they’re small and cheap to address.
Comparing Proactive vs. Reactive Maintenance
Proactive and reactive maintenance are two different approaches to keeping equipment running.
Proactive maintenance:
- Prevents problems before they occur
- Reduces unexpected downtime
- Unlike reactive maintenance, it can extend equipment life
- Lowers overall maintenance costs
Reactive maintenance:
- Fixes problems after they happen
- This can lead to more downtime
- May shorten equipment life
- Often costs more in the long run and can lead to more machine failure
Proactive strategies help facilities avoid the pitfalls of reactive maintenance and optimize operational efficiency.
They also allow for better planning and more efficient resource use.
Benefits of Proactive Maintenance for Facilities
Proactive maintenance offers many advantages for facility managers. It can lead to significant improvements in a building’s operation.
Key benefits include:
- Lower repair costs: Fixing small issues is cheaper than major repairs.
- Less downtime: Equipment breaks down less often, so work isn’t interrupted.
- Longer equipment life: Regular care helps machines last longer, reducing potential equipment failures.
- Better safety: Well-maintained equipment is less likely to cause accidents.
- Improved efficiency: Equipment that works well uses less energy.
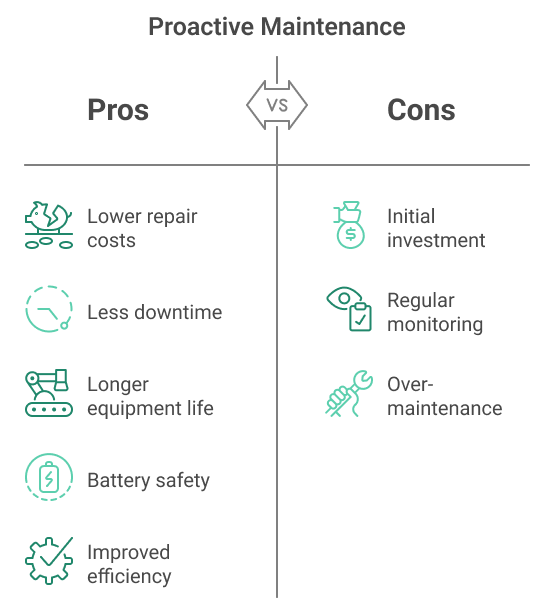
Proactive maintenance also helps facilities plan better. They can schedule work at convenient times and avoid rush jobs.
Planning for Proactive Maintenance
Good planning is key to a successful proactive maintenance strategy. It sets the foundation for smoother operations and helps prevent costly breakdowns.
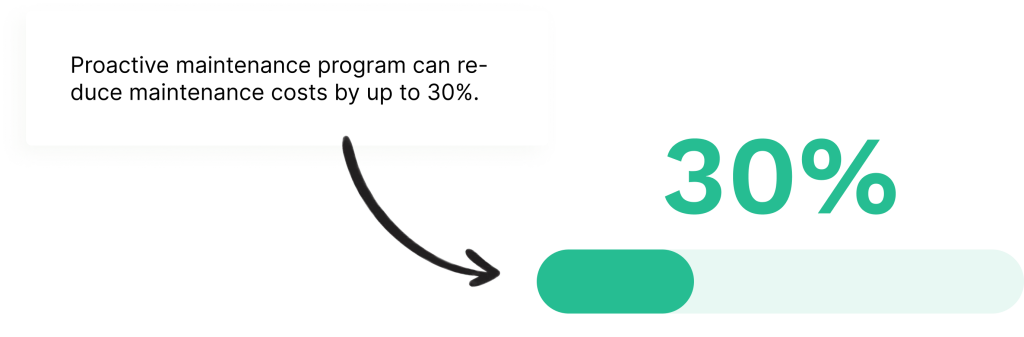
Setting Objectives
Start by defining clear goals for your proactive maintenance program. These might include:
- Reducing equipment downtime
- Extending asset lifespans
- Cutting maintenance costs
- Improving safety standards
Make sure your objectives are specific and measurable. For example, aim to “reduce unplanned downtime by 25% within 6 months.”
Set both short-term and long-term targets. This helps track progress and keeps the team motivated.
Assessing Current Maintenance Practices
Take a close look at your existing maintenance routines. This step is crucial for identifying areas for improvement.
Review maintenance logs and equipment histories. Look for patterns in breakdowns or recurring issues.
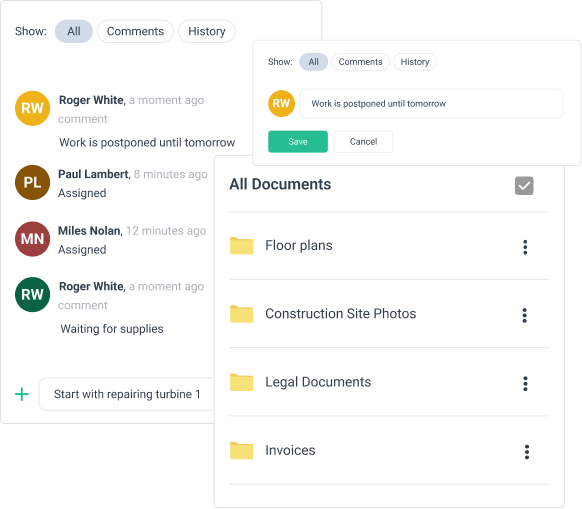
Talk to technicians and operators. They often have valuable insights into equipment problems and maintenance needs.
Consider using tools like:
• Root cause analysis • Failure mode and effects analysis (FMEA) • Equipment criticality assessments
These methods can help pinpoint where proactive maintenance will have the biggest impact.
Resource Allocation for Implementation
Implementing proactive maintenance requires careful resource planning. Start by creating a diverse team to oversee the implementation.
Assess your current resources:
- Staff skills and availability
- Budget for new tools or training
- Time needed for planning and execution
You may need to invest in:
- Predictive maintenance technologies
- Staff training programs
- Upgraded maintenance management software
Prioritize your spending based on potential return on investment. Focus first on critical equipment and high-impact improvements.
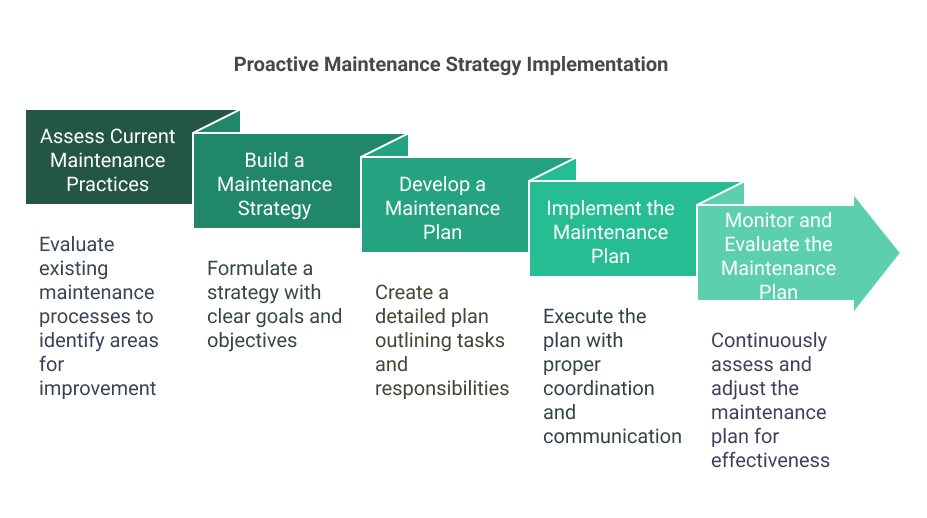
Remember, shifting to proactive maintenance is a gradual process. Plan for a phased implementation to manage resources effectively.
Execution of Proactive Maintenance Strategies
Putting proactive maintenance into action requires careful planning and systematic implementation. Key elements include assessing equipment needs, creating schedules, training staff, monitoring conditions, and using predictive tools.
Identifying Equipment Needs
A thorough equipment assessment is crucial for proactive maintenance. Start by making a list of all machinery and assets in the facility. Rank each item based on its importance to operations and potential impact if it fails.
For critical equipment, gather detailed information:
- Age
- Maintenance history
- Expected lifespan
- Replacement costs
This data helps prioritize maintenance efforts. Focus on items vital to operations or have a history of breakdowns.
Use key performance indicators to help you identify equipment that is more likely to fail.
Regular inspections are key. Set up a system for staff to report unusual sounds, vibrations, or performance issues. Early detection of problems can prevent major failures.
Implement a Computerized Maintenance Management System
Consider using computerized maintenance management systems (CMMS) like WorkTrek to track equipment data and maintenance needs.
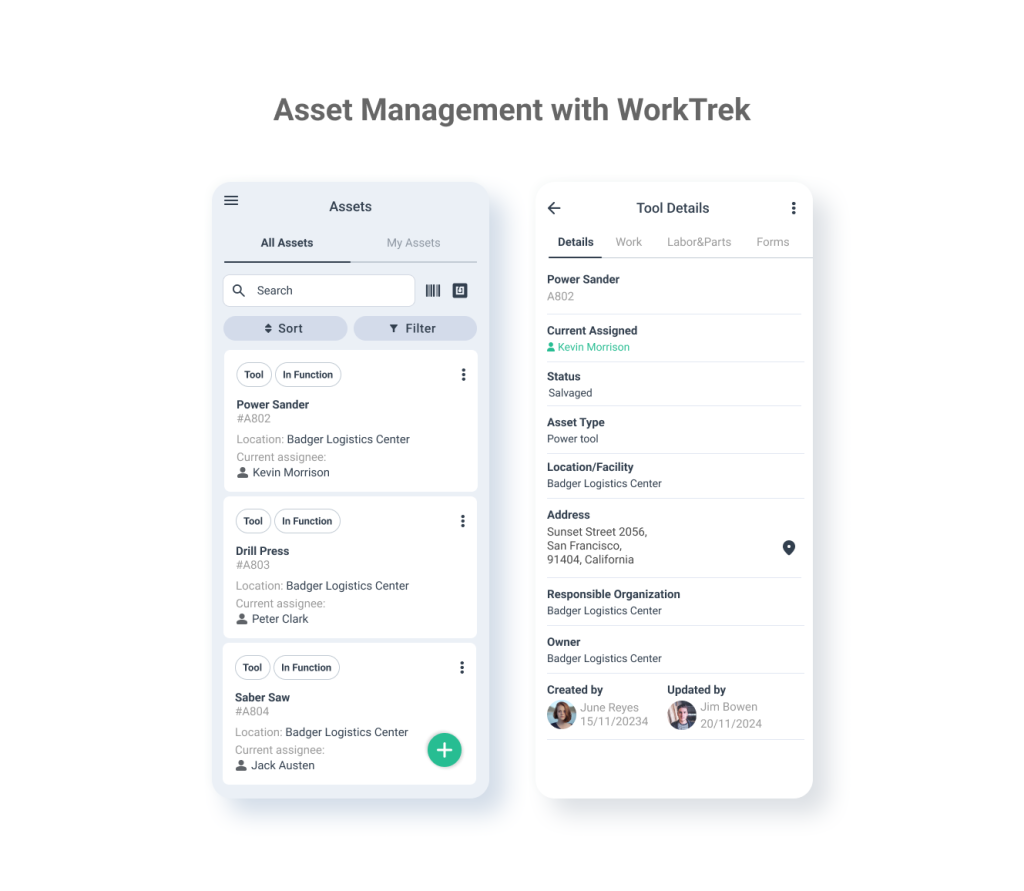
These tools can provide valuable insights for decision-making.
Developing Maintenance Schedules
Create a detailed maintenance calendar for each piece of equipment.
Base schedules on manufacturer recommendations, equipment age, and past performance.
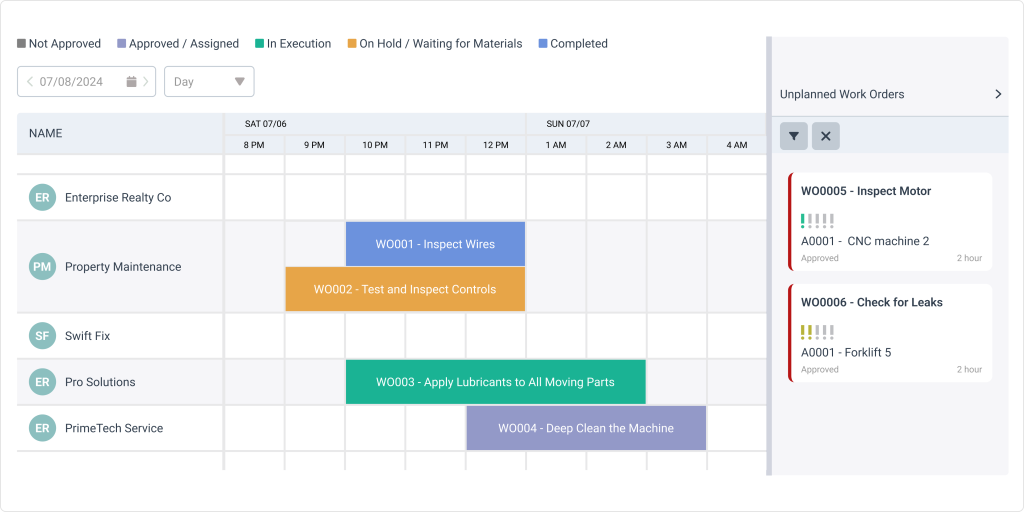
Include tasks like:
- Regular inspections
- Lubrication
- Parts replacement
- Cleaning
- Routine Inspections
- Performance metrics
Adjust schedules as needed based on equipment performance and feedback from maintenance staff.
Be flexible but consistent in following the plan.
Use digital tools to manage schedules and send automatic reminders for upcoming tasks. This helps ensure nothing falls through the cracks.
Balance the workload across days and weeks to avoid overwhelming maintenance staff.
When possible, group similar tasks together for efficiency.
Training Maintenance Personnel
Invest in ongoing training for maintenance staff. This keeps their skills up-to-date and improves job performance.
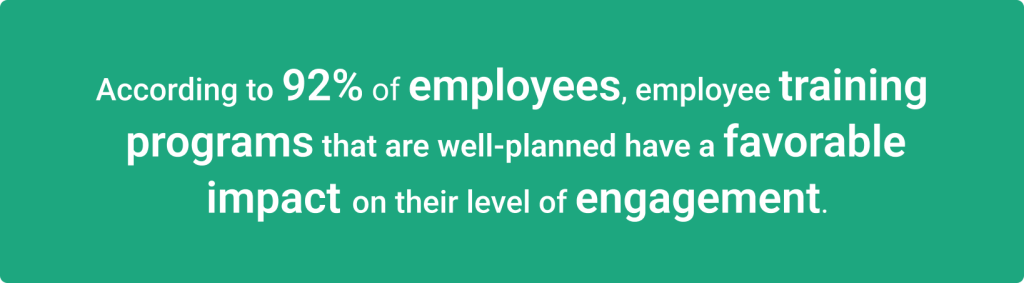
Key training areas include:
- Equipment-specific maintenance procedures
- Safety protocols
- Troubleshooting techniques
- Use of maintenance software and tools
Encourage staff to earn relevant certifications. This boosts their expertise and the overall quality of maintenance work.
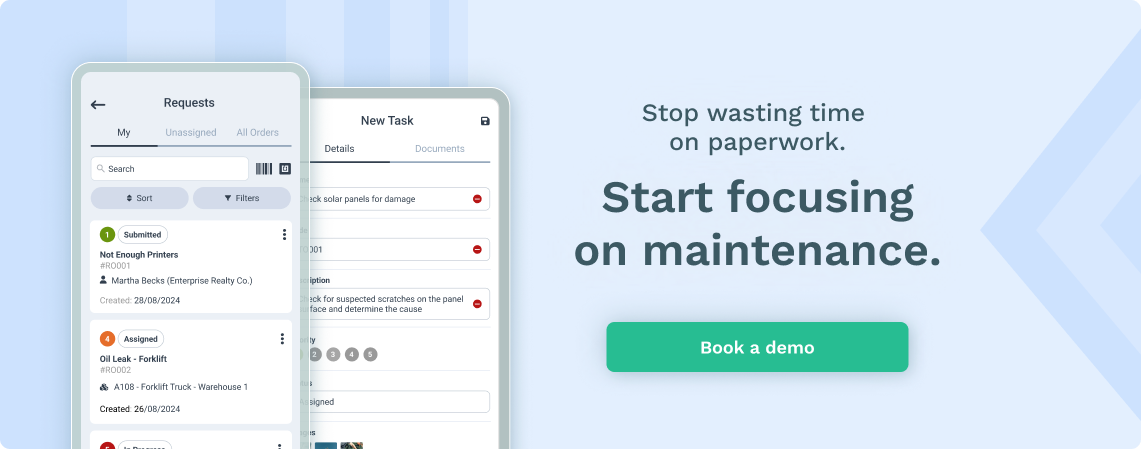
Create detailed maintenance manuals for each piece of equipment.
The manuals should include step-by-step procedures, safety guidelines, and troubleshooting tips.
Foster a culture of continuous learning. Encourage staff to share knowledge and best practices.
Consider implementing a mentorship program for new hires.
Implementing Condition-Based Monitoring
Condition based maintenance continuously monitors equipment performance.
Use sensors to track factors like:
- Temperature
- Vibration
- Pressure
- Oil quality
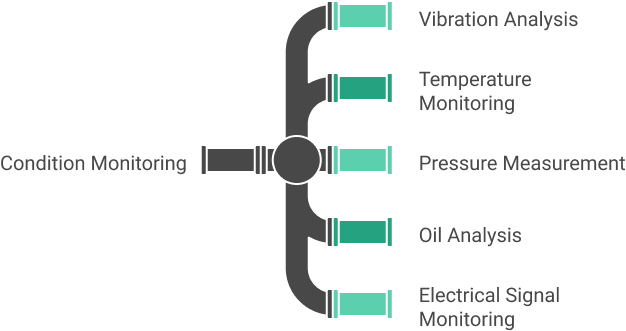
Establish normal operating ranges for each parameter.
Configure alerts to notify staff when readings fall outside these ranges.
Regularly analyze collected data to spot trends and potential issues. This allows for timely interventions before failures occur.
Integrate monitoring systems with maintenance software for streamlined data management and analysis. This helps identify potential equipment failures early on, reducing costly repairs.
Train the maintenance technicians to interpret monitoring and performance data and take appropriate action when issues that help reduce expensive repairs are detected.
Regular reviews of monitoring data can reveal opportunities for process improvements.
Utilizing Predictive Maintenance Tools
Implement advanced tools to forecast maintenance needs. These may include:
- Vibration analysis equipment
- Infrared cameras for thermal imaging
- Oil analysis kits
- Ultrasonic detectors
Use these tools to detect subtle changes in equipment conditions that might signal future problems. This allows for planned repairs before breakdowns occur.
Integrate predictive maintenance data with your overall maintenance strategy. Use insights to refine maintenance schedules and prioritize tasks.
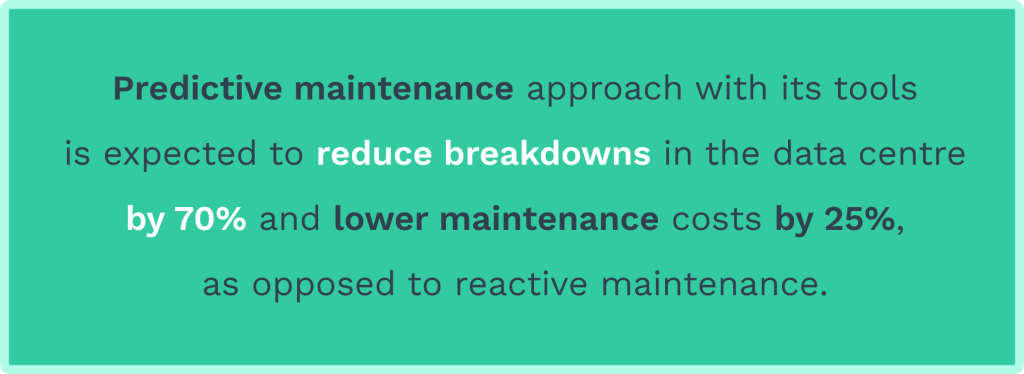
Consider machine learning algorithms to analyze maintenance data and predict future equipment behavior. This can help optimize maintenance timing and resource allocation.
Regularly evaluate the effectiveness of predictive tools. Adjust your approach based on real-world results and emerging technologies.
Data Analysis and Continuous Improvement
Data analysis and improvement are key to effective proactive maintenance. These processes help facilities spot trends, fix issues early, and improve over time.
Collecting and Managing Maintenance Data
To start, gather data from many sources. Use sensors, IoT devices, and other tools to track equipment health. Log all maintenance tasks, repairs, and part replacements.
Store this info in a central system.
A good computerized maintenance management system (CMMS) like WorkTrek can help. It keeps data organized and easy to access.
Make sure staff enter data correctly and regularly. Set clear rules for data entry. This helps keep the info accurate and valuable.
Analyzing Maintenance Metrics
Look at key metrics to spot trends. Common ones include:
- Equipment downtime
- Mean time between failures
- Repair costs
- Energy use
Use charts and graphs to see patterns. Compare current data to past performance.
Find failure patterns in equipment using historical data.
This helps predict when machines might break down and extend equipment lifespan.
Check which maintenance tasks work best. See if some methods save more money or time than others.
Applying Insights to Improve Processes
Use data insights to make smart changes. If a machine often breaks, adjust its maintenance schedule. This can prevent future issues.
Update staff training based on common problems found. This helps workers spot and fix issues faster.
Optimize preventive maintenance by focusing on high-risk equipment. This saves time and resources.
Try new maintenance methods and track results. Keep what works and change what doesn’t. This leads to steady improvement over time.
Share findings with the whole team. This helps everyone understand goals and progress and can give your organization a competitive advantage.
Technology in Proactive Maintenance
Modern technology plays a key role in effective proactive maintenance. The right tools can help predict issues, streamline workflows, and boost efficiency.
Exploring Advanced Maintenance Technologies
Computerized Maintenance Management Systems (CMMS) are central to proactive maintenance. These systems track equipment data, schedule tasks, and generate reports.
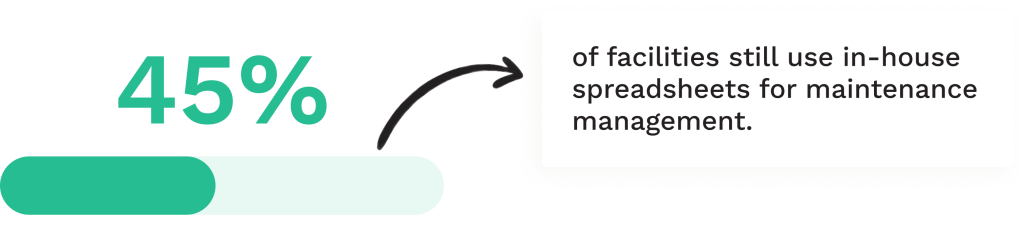
Sensors and Internet of Things (IoT) devices monitor equipment in real time.
They can detect changes in temperature, vibration, or other metrics that may signal potential issues.
Artificial Intelligence (AI) and Machine Learning (ML) analyze data from sensors and CMMS.
These technologies can predict when equipment will likely fail, allowing for timely maintenance.
Augmented Reality (AR) helps technicians visualize complex repairs.
It can overlay schematics onto physical equipment, guiding maintenance work.
Integration with Existing Systems
Integrating new tech with existing systems is crucial for success. This process starts with a thorough assessment of current infrastructure and needs.
API connections allow different software systems to communicate, enabling seamless data flow between maintenance tools and other business systems.
Cloud-based solutions offer flexibility and scalability. They can be accessed from anywhere, making it easier to manage maintenance across multiple locations.
Training staff on new systems is essential.
Regular workshops and hands-on practice sessions help ensure the smooth adoption of new technologies.
Investing in the Right Tools and Software
Choosing the right tools requires careful consideration. Factors to weigh include:
- Scalability
- User-friendliness
- Integration capabilities
- Cost-effectiveness
- Vendor support
Mobile maintenance apps allow technicians to access information and log data on the go, improving efficiency and data accuracy.
Data analytics tools help make sense of collected information. They can identify trends and provide insights for better decision-making.
Automation software can handle routine tasks like creating work orders and ordering parts, freeing staff time for more complex maintenance activities.
Maintaining Safety and Compliance
Proactive maintenance plays a key role in keeping facilities safe and compliant. It helps prevent accidents, meet regulations, and avoid costly fines. Let’s explore how to maintain safety and stay compliant through proactive strategies.
Adhering to Safety Regulations
Safety should be the top priority in any facility.
Implementing proactive maintenance strategies can help reduce unexpected failures and ensure safety rules are followed.
Here are some key steps:
- Train staff on proper equipment use and safety protocols
- Regularly inspect and maintain safety equipment
- Post clear safety signs and instructions
- Provide proper personal protective equipment (PPE)
- Document all safety procedures and incident reports
Creating a safety-first culture is crucial. To prevent accidents, encourage employees to report potential hazards and address safety concerns promptly.
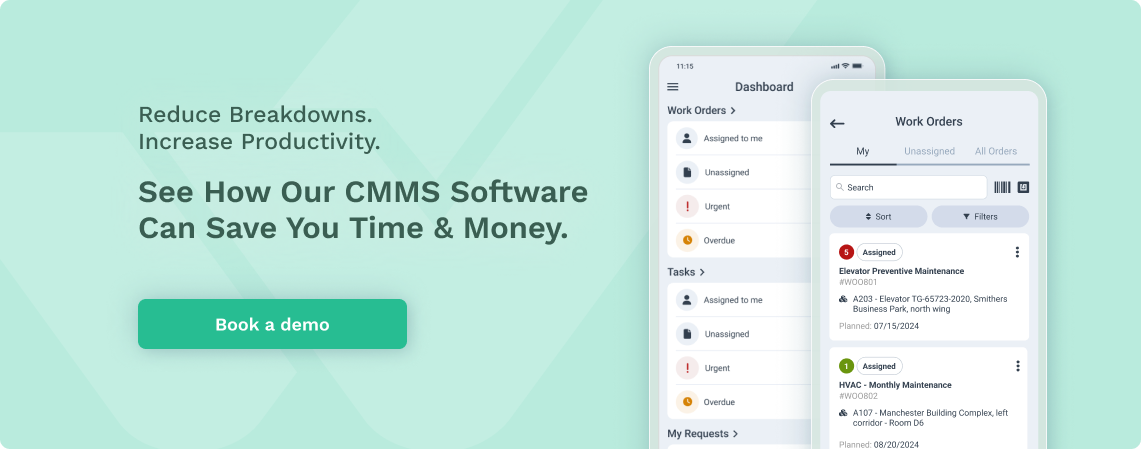
Regular safety meetings keep everyone informed and engaged. These meetings can cover new regulations, review incident reports, and share best practices.
Ensuring Compliance with Industry Standards
Staying compliant with industry standards protects your facility from legal issues and fines. Proactive maintenance supports compliance by catching problems early. Follow these steps:
- Stay updated on current regulations
- Create a compliance checklist
- Schedule regular equipment inspections
- Keep detailed maintenance records
- Use software to track compliance tasks
Assign team members to oversee specific compliance areas. This ensures nothing falls through the cracks.
Work with regulatory bodies to understand requirements fully. They can often provide guidance on best practices for compliance.
Regular Audits and Adjustments
Audits help identify gaps in safety and compliance efforts and show areas for improvement.
Schedule regular safety audits to stay on track.
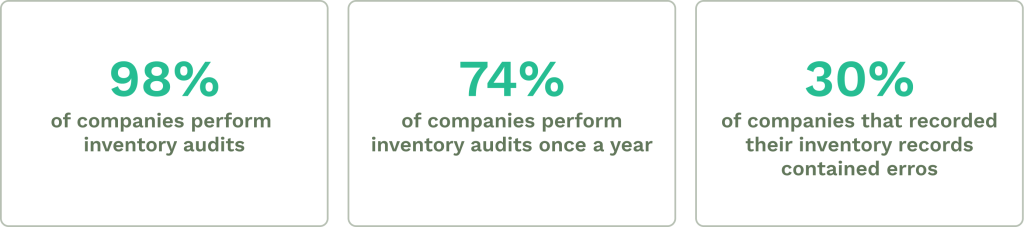
During audits:
- Review maintenance logs
- Check equipment performance
- Assess employee knowledge of procedures
- Inspect safety equipment and signage
Use audit results to make needed adjustments. Update procedures, retrain staff, or upgrade equipment as needed.
Consider hiring external auditors for an unbiased view. They can spot issues you might miss and suggest improvements.
Track audit findings over time to measure progress. Celebrate improvements to boost morale and encourage ongoing vigilance.
Challenges and Solutions in Proactive Maintenance
Implementing proactive maintenance brings unique hurdles and challenges. Facility maintenance managers face common obstacles, staff resistance, and cost concerns.
Smart strategies can address these issues and maximize benefits.
Addressing Common Roadblocks
Limited resources often hinder proactive maintenance efforts. Many facilities lack the proper tools or staff to carry out regular checks. Automated analytics can help predict issues before they become costly. This tech collects data from sensors to create predictive models.
Training gaps pose another challenge. Staff may not know how to use new systems or perform advanced maintenance tasks. Regular training sessions can bridge this knowledge gap, and hands-on workshops work well for teaching practical skills.
Data management can overwhelm teams. Too much information makes it hard to spot key trends. With a a CMMS (Computerized Maintenance Management System) helps organize data. These systems track equipment history and schedule tasks efficiently.
Strategies for Overcoming Resistance to Change
Staff often resist new maintenance approaches. Clear communication is key to gaining buy-in. Explain the benefits of proactive maintenance for both the facility and employees.
Create a transition plan with small, achievable steps. This makes the shift less daunting. Set realistic goals and celebrate small wins to build momentum.
Involve team members in planning and ask for their input on new procedures. This builds ownership and reduces pushback.
Provide ongoing support during the transition. Assign mentors to help staff adapt to new methods. Regular check-ins can address concerns quickly.
Balancing Costs and Benefits
Upfront costs for proactive maintenance can seem high. New equipment and training require investment. But long-term savings often outweigh initial expenses.
Track key metrics to show value. Monitor equipment downtime, repair costs, and energy use. Compare these to past reactive maintenance data.
Start with critical assets to prove the concept. Focus on equipment that most impacts safety or production. Early wins here can justify wider implementation.
Consider phased implementation to spread costs. Upgrade systems and train staff in stages. This approach makes budgeting more manageable and allows for adjustments.
Regular inspections and monitoring help prevent unexpected breakdowns. This reduces costly emergency repairs and production losses.
Case Studies and Best Practices
Real-world examples offer valuable insights into proactive maintenance strategies. These cases highlight successful approaches, common pitfalls, and industry-specific considerations.
Worthington Industries
In 2017, they set out to improve machine reliability. They selected the approach of implementing company-wide proactive maintenance practices.
They started implementing their plan across 17 plants and 650+ pieces of equipment. They also implemented many sensors, leading to 8 million data points, which they used for their analysis.
What was the result of all this?
- They realized $16M in savings across the enterprise
- Greatly reduced equipment downtime
- Improved overall customer experience and deliveries
Wood County Facility Management
Wood County is located in central Wisconsin. The maintenance team manages several county buildings, including the local jail and hospital.
By implementing a CMMS and a proactive maintenance program, Wood County improved its maintenance outcomes and reduced system downtime.
Conclusion and Future Outlook
Proactive maintenance is changing how facilities operate. It helps prevent problems before they happen.
This approach saves money and time in the long run.
By 2025, more facilities will use smart technology for maintenance. Sensors and data analysis will spot issues early, allowing teams to fix things quickly and avoid big breakdowns.
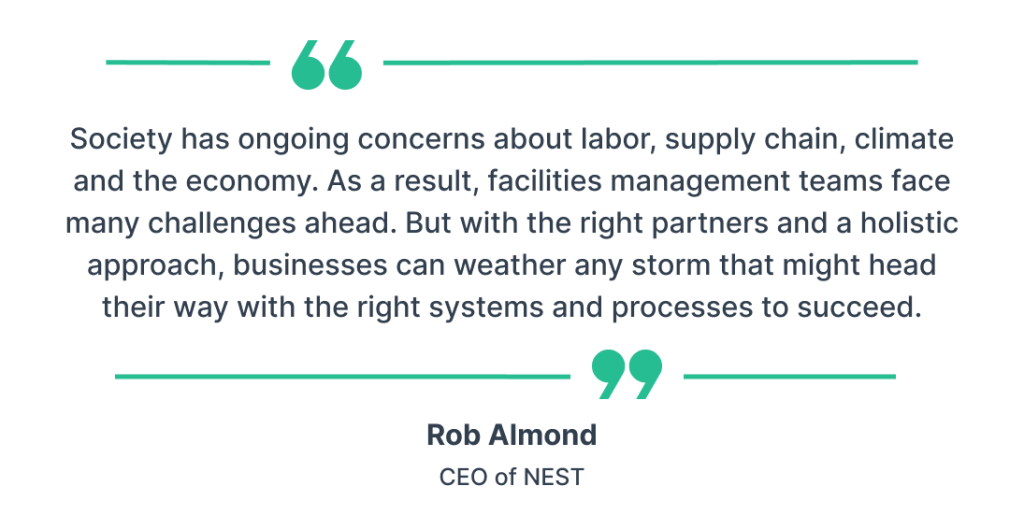
Facilities that use proactive maintenance can expect:
- Longer-lasting equipment
- Lower repair costs
- Less downtime
- Happier employees and customers
The future of facility management looks bright with proactive maintenance.
It turns guesswork into planned action. Managers can make better choices about when to fix or replace things.
Training is key for this new approach. Teams need to learn how to use new tools and read data.
This knowledge helps them make smart decisions about maintenance.
As more facilities adopt proactive maintenance, the industry will change. As practices improve, costs may decrease, and buildings will run smoother and be more eco-friendly.
Proactive maintenance is not just a trend. It’s becoming the new standard for well-run facilities. Those who embrace it now will be ahead of the game in future years.