Get a Free WorkTrek Demo
Let's show you how WorkTrek can help you optimize your maintenance operation.
Try for freeThis article will provide a comprehensive guide to developing an effective preventive maintenance schedule. The schedule details regular inspections and actions that ensure machinery remains in excellent working order.
By adopting this proactive approach, you can avert sudden malfunctions, reduce equipment failure, eliminate unplanned downtime, and prolong the lifespan of your assets while understanding the advantages of such a plan.
There are two types of preventive maintenance scheduling: fixed scheduling, which follows set intervals, and floating scheduling, which adjusts based on actual usage patterns.
Successful implementation of a preventive maintenance schedule involves clear asset inventory, criticality analysis, setting ideal maintenance intervals, utilizing preventive maintenance software, and continuous monitoring and adjustments.
Introduction
The lifeblood of any business is its consistent and reliable assets. A machine that runs smoothly, literally and figuratively, is critical to winning in today’s competitive world. Here, an effective maintenance schedule rules—a systematic way of automating maintenance, increasing asset performance, and enhancing your workforce.
Now, let’s explore how to develop a robust and transformative strategy for establishing a reliable preventive maintenance routine within your organization.
Understanding Preventive Maintenance Schedules
Starting a preventive maintenance program involves recognizing that these schedules go beyond mere to-do lists. They form the foundation for operational excellence.
A detailed and robust preventive maintenance schedule is vital. It guarantees that crucial maintenance tasks are carried out automatically, reduces downtime to an absolute minimum, and maximizes resource efficiency.
This approach emphasizes proactive actions over reactive maintenance. It addresses potential problems before they occur and enables your team to boost productivity and reduce critical equipment downtime. It also reduces unplanned downtime, equipment downtime, and equipment failure.
What is a Preventive Maintenance Schedule?
A preventive maintenance schedule is like a roadmap for critical assets, guiding them through scheduled inspections and tasks based on time or usage. This covers all the maintenance activities you need to keep your equipment running at its best:
- Air filter replacement
- Regular engine oil changes
- Electrical connections inspection and cleaning
- Moving parts lubrication
- Belts and hoses checks with necessary adjustments
- Safety feature examinations
- Calibration of instruments
Doing this ensures that your machinery is maintained in excellent condition while significantly reducing the potential for unforeseen malfunctions or steep repair bills.
Commitment to this approach allows you to promptly address minor issues, preventing them from escalating into more significant and costly complications—a true embodiment of the proactive ‘earlier rather than later’ approach to upkeep activities.
Benefits of a Preventive Maintenance Schedule
A preventative maintenance schedule, sometimes referred to PM schedule, carries significant advantages, underscoring why having such a plan is essential for any enterprise. It safeguards your business activities, providing returns by preventing extensive repairs and diminishing operational downtime.
An effective preventive management strategy is crucial for reducing the likelihood of abrupt equipment failures, clearly defining maintenance tasks, and reducing failures while enhancing the efficiency and consistency of operations.
Taking this proactive step also conveys several benefits:
- Minimizes expenditures through reduced urgency in shipping and unplanned overtime expenses
- Prolongs the service life of company assets
- Augments asset performance and dependability
- Clearly define a successful preventive maintenance schedule
- Simplify regular maintenance
- Outline each maintenance task for technicians
- Reduce reactive maintenance
- Curbs instances of surprise malfunctions along with steep repair fees, thus decreasing overall replacement costs
Types of Preventive Maintenance Schedules
Having covered the fundamental concepts, let us explore the primary variants of preventive maintenance scheduling: fixed and floating. These models each bring distinct advantages that can be customized according to your operation’s requirements.
The predictability inherent in a fixed schedule contrasts sharply with the flexibility a floating schedule offers. Choosing the best fit for your strategy depends on various factors, including asset characteristics, maintenance needs, and desired maintenance outcomes.
The following sections will outline the different types of preventive maintenance.
Fixed Preventive Maintenance Scheduling
Preventive maintenance scheduling is the cornerstone of organized maintenance planning, providing a predictable and manageable framework.
Routine and schedule maintenance is executed at predetermined intervals, independent of when the last task was performed. For example, commercial vehicles typically receive preventive maintenance every 3 to 5 thousand miles, depending on the type of usage, to maintain optimal performance.
This fixed preventive maintenance schedule can also be used with regular maintenance based on maintenance tasks.
This is ideal for assets where reliability is vital, and conditions don’t change. It also allows for long-term maintenance scheduling so the maintenance technicians and managers can see ahead.
Floating Preventive Maintenance Scheduling
Conversely, adaptive preventive maintenance scheduling is tailored to your assets’ utilization patterns. This flexible strategy, sometimes called usage-based maintenance, considers when previous maintenance tasks were performed and modifies future schedules accordingly.
For instance, should a vehicle undergo maintenance interval at 3,250 miles rather than the prescribed 3,000-mile mark, subsequent preventive maintenance would be arranged for 6,250 miles. This ensures that the asset receives upkeep in harmony with its real-world use instead of following an inflexible schedule.
This method is particularly effective for assets experiencing fluctuating usage levels as it offers a personalized approach to maintenance plans and needs.
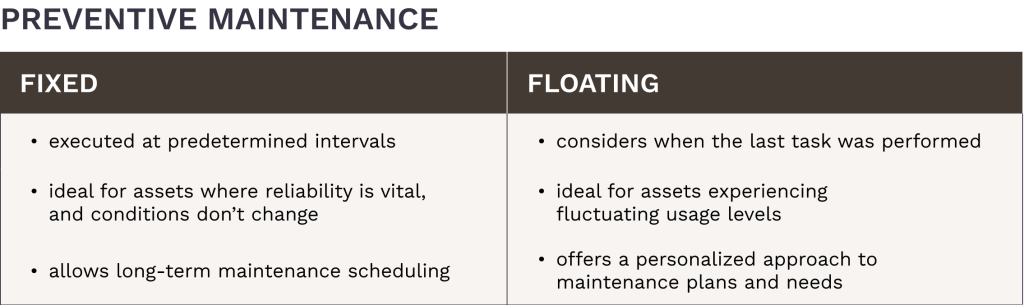
Source: WorkTrek
Steps to Create a Preventive Maintenance Schedule
Creating an effective preventive maintenance program is a multi-step process, with each phase building on the previous one. These steps include:
- Compiling a comprehensive list of your assets
- Pinpointing which ones are essential to operations
- Figuring out the optimal intervals for their upkeep
- Implementing recurring tasks into the schedule
- Regularly reviewing and tweaking as needed
Following these guidelines helps you develop a maintenance timetable, a preventive maintenance schedule, and an approach that ensures efficient asset management while enhancing performance and supporting broader business objectives.
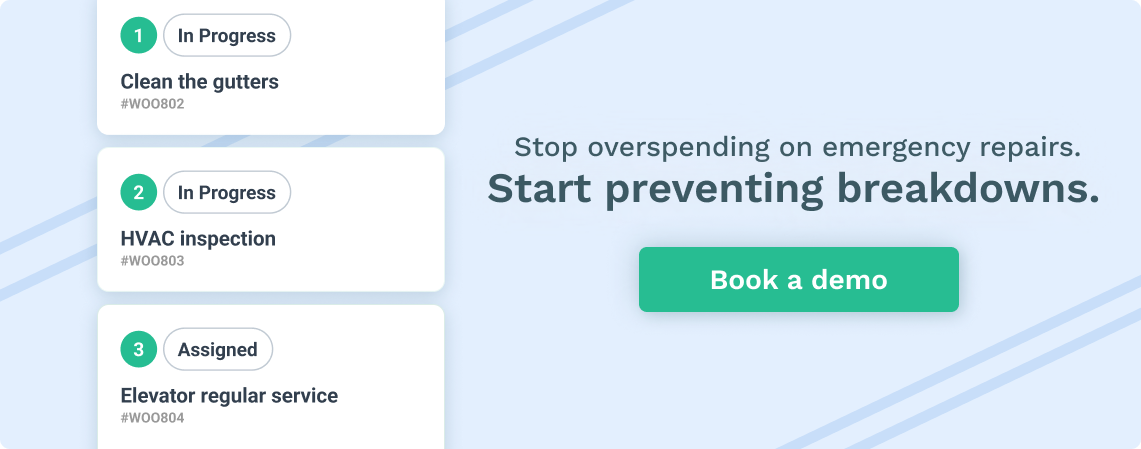
Once you’ve defined your maintenance schedules, it is time to start getting an overview and inventory of your critical assets.
Inventory Your Assets
Embarking on developing your preventive maintenance strategy begins with a comprehensive cataloging of your assets. This asset inventory must encompass critical information, including:
- Manufacturer
- Model designation
- Unique serial number
- Current Placement
- Historical records of upkeep
Consider this as compiling a detailed dossier for every equipment item that will serve as the foundation for making educated decisions about their maintenance.
This procedure ensures awareness of the available range of instruments and helps organize them systematically based on maintenance priority.
Determine Critical Assets
Possessing a detailed inventory allows for the subsequent identification of assets essential to your business functions. A criticality analysis will help pinpoint which pieces of equipment require heightened focus because they significantly affect operations, finances, or safety.
By prioritizing these high-impact assets, you can efficiently distribute maintenance resources to keep vital equipment in optimal working order.
This process involves making informed decisions to secure the highest possible return on investment from your asset management efforts.
Identify Ideal Maintenance Intervals
Consider the manufacturer’s suggested timelines and historical maintenance data to determine the optimal maintenance intervals for your prioritized assets. This will allow you to develop a tailored schedule that avoids excessive or insufficient upkeep.
This approach is critical in providing each asset with an appropriate level of care at the most suitable times to enhance its durability and operational efficiency.
Schedule Recurring Maintenance Tasks
Once you’ve defined the maintenance intervals, the focus shifts to implementing a recurring maintenance schedule and tasks. Preventive maintenance software can significantly simplify this phase, offering features that enable you to establish maintenance intervals, add instructions, and create checklists for your technicians.
This software is critical for coordinating preventive maintenance operations, enhancing efficiency, and elevating productivity.
Monitor and Adjust the Schedule
Continually tracking and modifying your preventive maintenance plan is crucial for its success. This allows it to stay in sync with your objectives and performance metrics while adjusting for any fluctuations in how assets are utilized or performed.
By conducting periodic evaluations and examining data closely, you can enhance the precision of your maintenance timetable, ensuring it remains robust and tailored to meet the demands of your operations.
Regularly updating your preventive maintenance schedule based on these evaluations helps identify patterns and trends that may not be immediately apparent. This continuous improvement loop ensures that your maintenance activities are always aligned with the current operational realities and emerging needs, thereby maximizing the efficiency and lifespan of your assets.
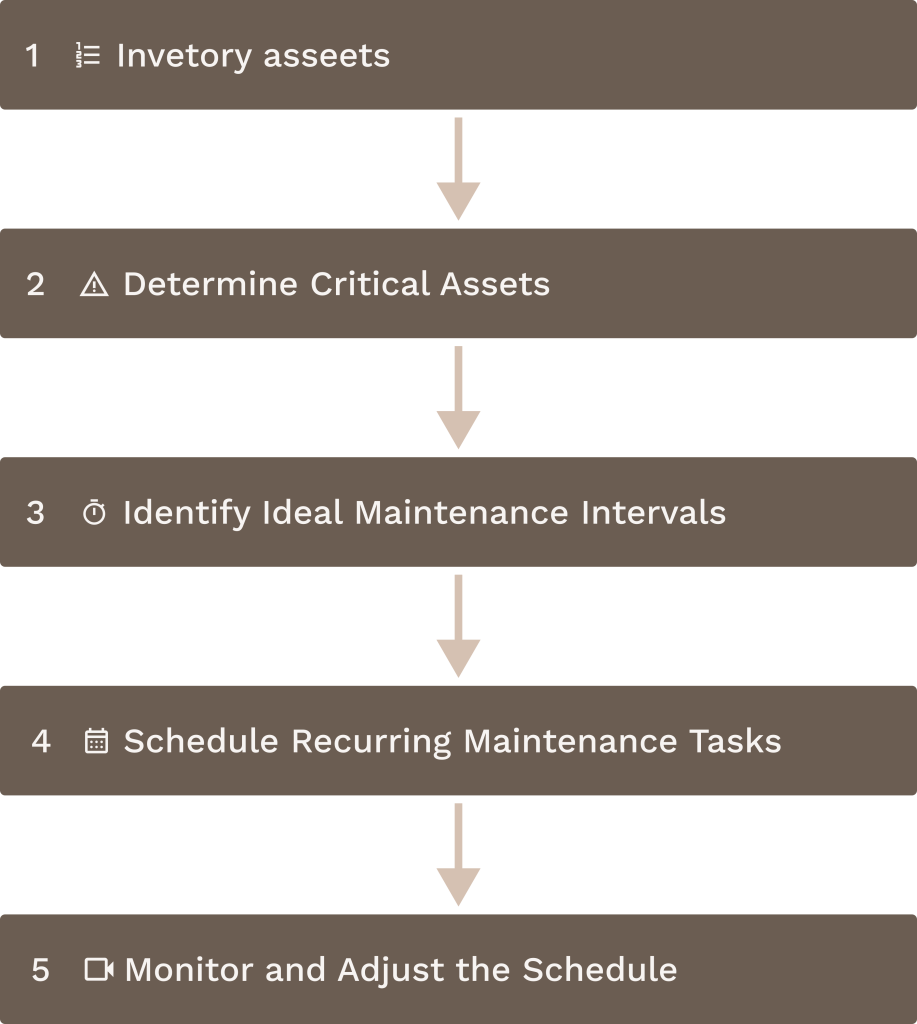
Source: WorkTrek
Implementing Your Preventive Maintenance Schedule
After establishing your preventive maintenance schedule, the next crucial step is to implement it. This process includes several key elements:
- Effectively communicating with your team
- Delegating tasks and defining roles
- Selecting appropriate tools for the job, like WorkTrek CMMS
- Offering essential training to those involved, including the maintenance department
- Fine-tuning PM Schedule
If executed well, your conceptual preventive maintenance strategy can become a practical daily practice that substantially rewards your company.
We will explore strategies to operationalize your schedule effectively, ensuring it becomes a core component of your organization’s maintenance activities instead of simply remaining an idea on paper.
Assign Responsibilities
The key to successful implementation lies in the art of targeted delegation. Allocating particular maintenance tasks among your team members provides ownership and optimizes task execution. The focus is on matching each job with the appropriate person, guaranteeing that every assignment receives attention without being overlooked.
Designating clear-cut roles and responsibilities, whether for supervisors, planners, or specific schedulers, is critical in ensuring a smooth operation of your preventive maintenance schedule. This clarity helps avoid confusion and facilitates an orderly progression of maintenance activities.
Use CMMS for Preventive Maintenance Software
Leveraging preventive maintenance software is a crucial guide to adequate asset upkeep. This software streamlines the planning phase, tracks the progress of scheduled tasks, and provides instant access to vital historical data—essential for making well-informed decisions.
Software such as a Computerized Maintenance Management System (CMMS) has the potential to transform how you handle your maintenance activities. They guarantee that adherence to your preventive maintenance schedule isn’t merely consistent and enhanced for peak performance and efficiency.
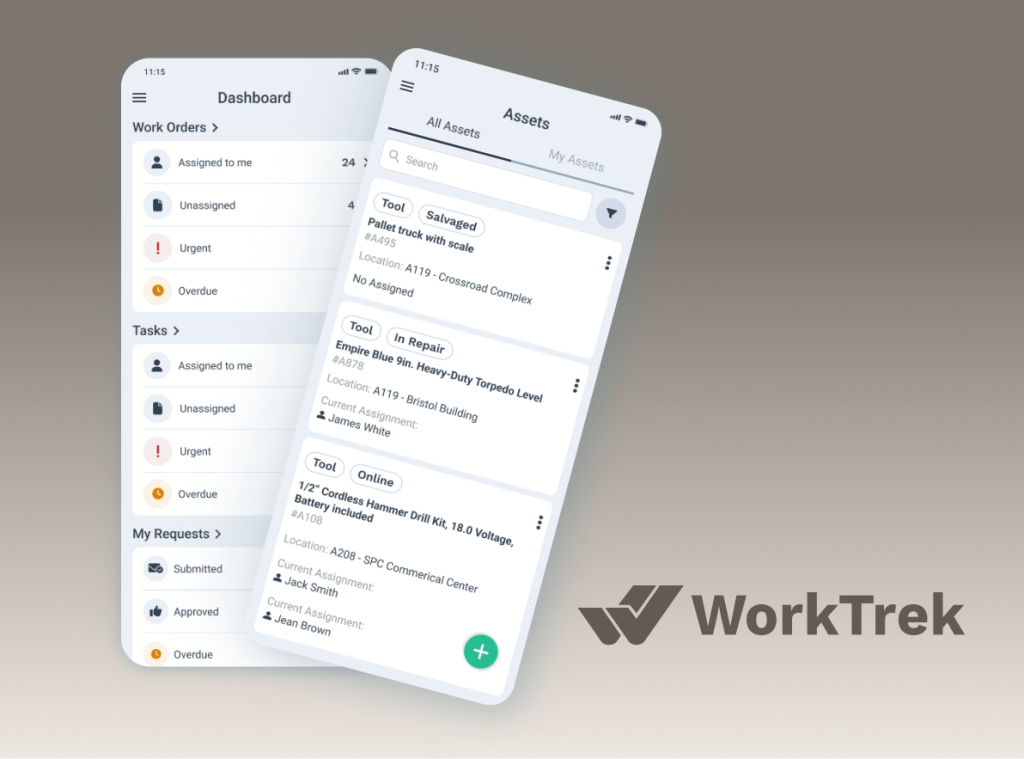
Source: WorkTrek
Training and Communication
Instructing your employees in preventive maintenance protocols is essential for adequate adherence to regulations. Consistent training will enhance your team’s expertise and guarantee they grasp the significance of their responsibilities.
Implementing well-defined communication pathways within your maintenance crew facilitates quick issue resolution, dissemination of new information, and improved collective teamwork.
Enhancing Preventive Maintenance Compliance
A top maintenance schedule works only if you stick to it. To make it work, all tasks must be done on time and tracked centrally for technicians and maintenance managers to review. That means tracking, updating, and recognizing your team members.
We should explore methods for keeping your preventive maintenance timetable on course while ensuring your team remains engaged and driven.
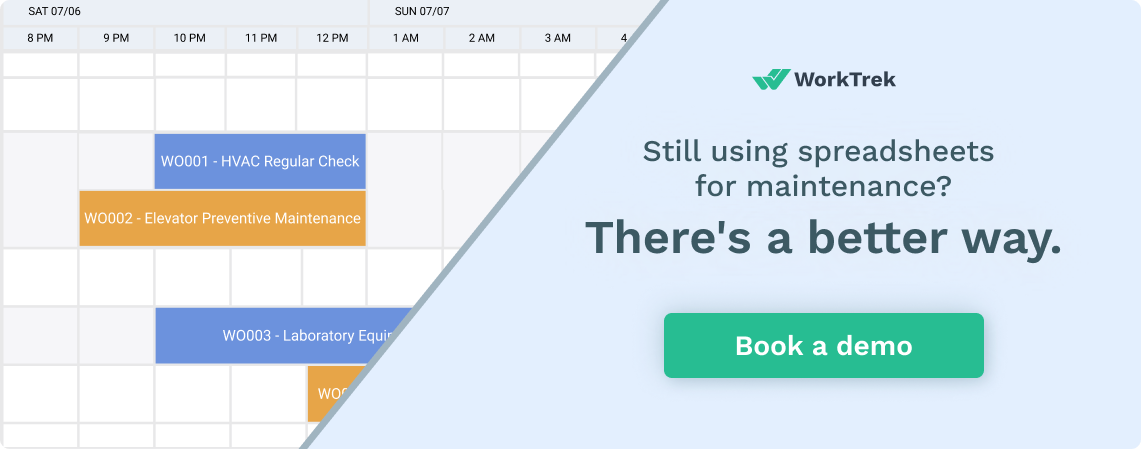
Tracking and Reporting
Monitoring and documenting the adherence to your preventive maintenance schedule is crucial for evaluating its success. Analyzing performance indicators like Mean Time Between Failures (MTBF) and Overall Equipment Effectiveness (OEE), along with finalized work orders, can help determine how practical your maintenance activities are.
Leveraging this information enables you to refine your tactics to achieve exceptional PM compliance, possibly exceeding 90%.
Incentives and Penalties
Motivating your team is critical to keeping compliance high. Rewarding them for completing tasks on time will boost morale and encourage effort, while sanctions for missed or late tasks will remind them to stick to the schedule.
Establishing a connection between performance measures and incentives or consequences fosters an environment committed to accountability and superior quality workmanship.
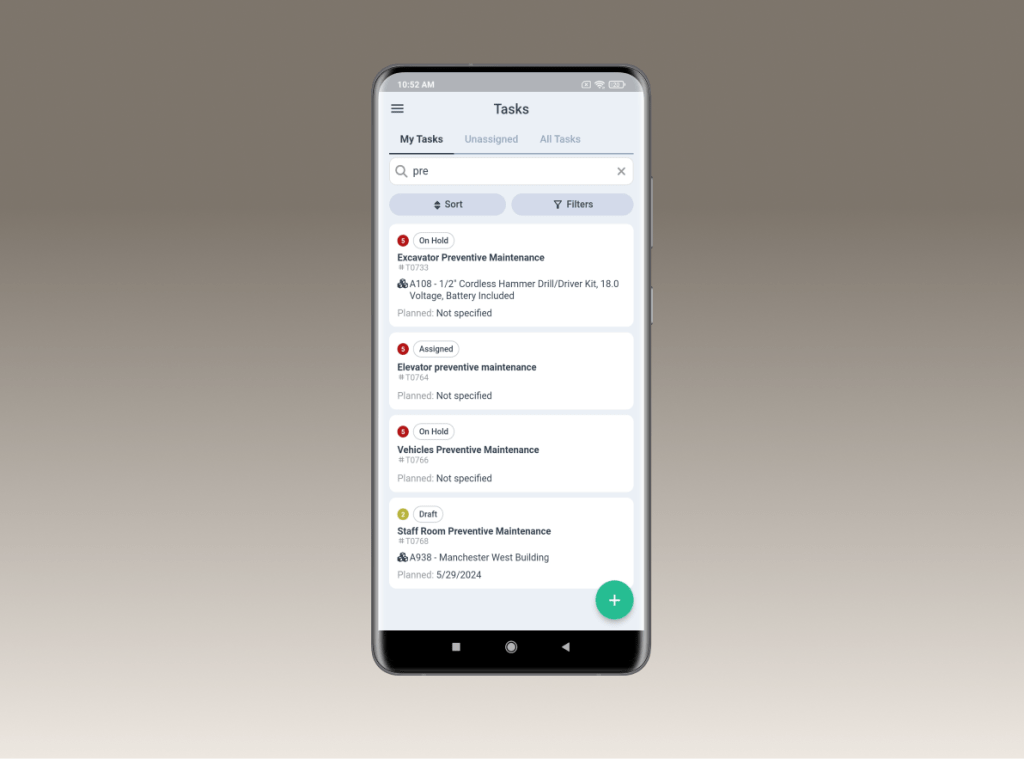
Source: WorkTrek
Common Challenges and Solutions in Preventive Maintenance Scheduling
Even with the most careful and detailed planning, obstacles to scheduling preventive maintenance inevitably occur. Resource limitations, unforeseen breakdowns, and opposition to change can present considerable difficulties.
Nevertheless, these obstacles can be overcome through effective strategies and a proactive mindset, ensuring your maintenance schedule remains robust and efficient.
Let’s explore some common challenges that may arise during this process and discuss strategies for effectively addressing them.
Overcoming Resource Constraints
Resource limitations are common across most organizations and can pose a considerable challenge. However, through strategic prioritization and staged execution, your resources can be efficiently managed. Initiate a trial project targeting the key critical assets and incrementally expand your preventive maintenance initiatives as more resources become available.
Adopting this strategy can maximize your limited resources while laying a solid foundation for your maintenance processes.
Handling Unexpected Failures
Unforeseen equipment breakdowns can disrupt your preventive maintenance routine, resulting in more extended downtimes and higher expenses, and can stretch your resources. Leveraging live data from a Computerized Maintenance Management System (CMMS) enables you to adjust swiftly, reducing the effects on scheduled maintenance tasks.
Additionally, integrating predictive maintenance techniques can help mitigate the impact of unexpected failures. By using advanced analytics and machine learning algorithms, you can anticipate potential breakdowns before they occur. This proactive approach allows you to schedule maintenance activities more effectively, minimizing disruptions and ensuring smoother operations.
Having an adaptive response plan ready for unexpected scenarios helps maintain the integrity of your preventive maintenance program despite unforeseen interruptions.
Summary
To summarize, crafting an effective preventive maintenance schedule is a multi-faceted process that requires attention to detail, strategic planning, and ongoing management. From understanding the importance of preventive maintenance to implementing and adjusting your schedule, each step is critical to ensuring your assets’ operational efficiency and longevity.
By taking a proactive approach, prioritizing tasks based on asset criticality, and leveraging technology, you can create a schedule that minimizes downtime and maximizes productivity and cost savings. Embrace the shift from reactive to proactive maintenance, and watch as it becomes a cornerstone of your operational success.