Get a Free WorkTrek Demo
Let's show you how WorkTrek can help you optimize your maintenance operation.
Try for freeMany businesses face unplanned and unscheduled maintenance. Unplanned maintenance happens when equipment breaks down unexpectedly, disrupting normal operations.
Unscheduled maintenance, or corrective maintenance, is reactive maintenance performed to address unforeseen equipment issues and restore assets to their optimal functioning state.
While it is costly and time-consuming for most organizations, this type of maintenance cannot always be avoided.
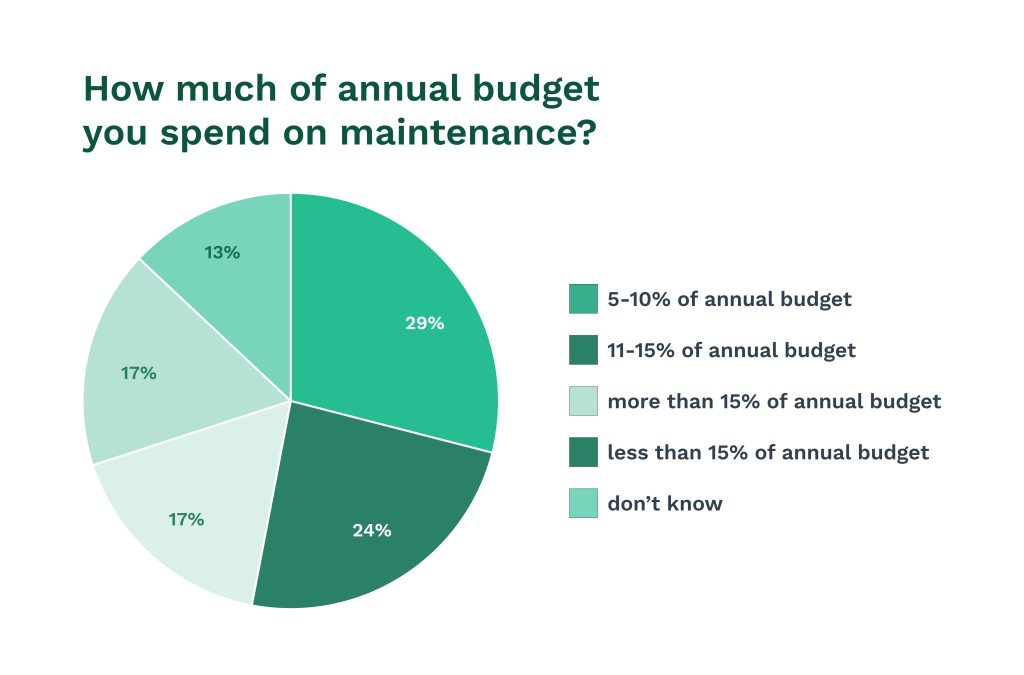
Illustration: WorkTrek / Data: Infraspeak Blog
It often delays production and can impact a company’s bottom line. While preventing all unexpected breakdowns is impossible, there are ways to reduce their frequency and impact.
Businesses can take steps to minimize unplanned maintenance. Regular inspections, preventive maintenance, and modern technology can help predict and prevent equipment failures. By being proactive, companies can save money and keep their operations running smoothly.
Key Takeaways
- Unplanned maintenance occurs when equipment unexpectedly breaks down
- It can lead to costly downtime and production delays
- Proactive strategies can help reduce the frequency of unplanned maintenance
Understanding Unplanned Maintenance
Unplanned maintenance, sometimes called reactive maintenance, is part of a broader maintenance strategy that addresses unexpected equipment failures.
It involves quick responses to breakdowns and emergency repairs to minimize downtime. Examples of unplanned maintenance include when a belt breaks or a motor breaks.
Definition and Characteristics
Unplanned maintenance, also called breakdown maintenance, is a reactive approach to fixing equipment failures that occur without warning. It’s often called corrective or emergency maintenance.
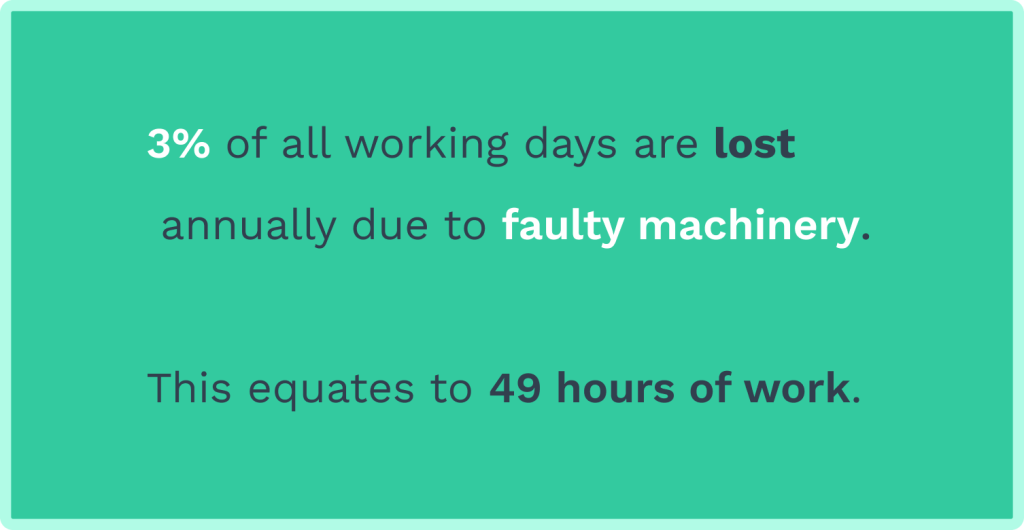
Illustration: WorkTrek / Data: Fingent
This type of maintenance happens when something breaks suddenly or stops working correctly.
Key characteristics include:
- Unexpected nature
- Urgent response required
- Potential for increased costs
- Disruption to normal operations
Unplanned maintenance can lead to more extended downtimes and higher repair costs than planned maintenance activities.
Comparison with Planned Maintenance
Planned maintenance involves plans and structured documents detailing preventive maintenance schedules based on regular intervals and equipment history. It aims to prevent breakdowns before they happen.
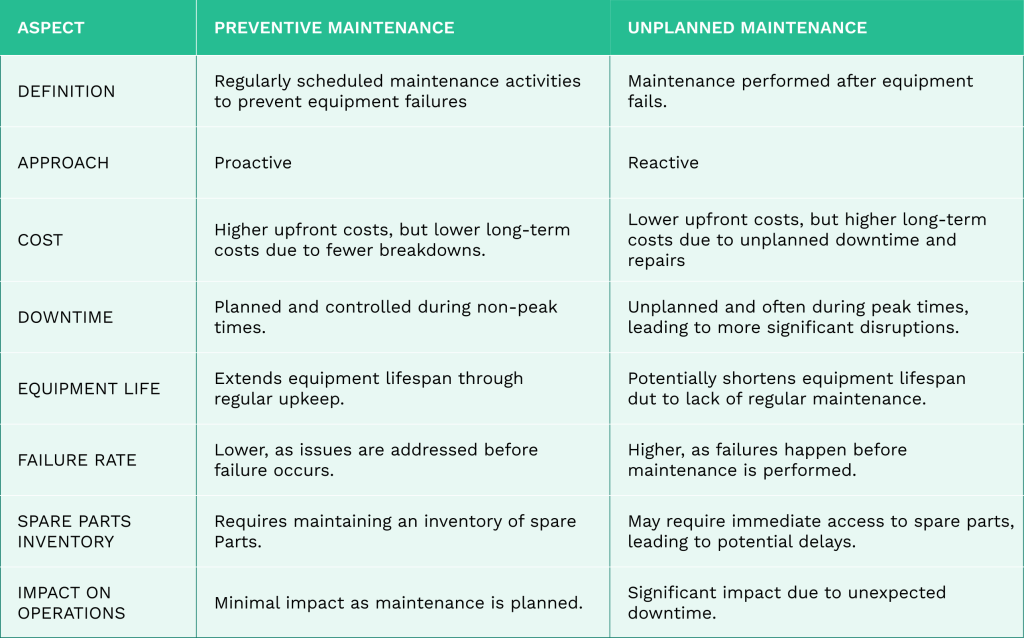
Source: WorkTrek
Differences between planned and unplanned maintenance:
- Timing: Planned is scheduled, unplanned is reactive
- Cost: Planned is often more cost-effective long-term
- Efficiency: Planned allows for better resource allocation
- Downtime: Unplanned typically results in longer, unexpected downtimes
Planned maintenance helps extend equipment life and improve overall reliability.
Types of Maintenance
Several types of maintenance can be employed to ensure the optimal functioning of equipment and assets. These types of maintenance can be broadly categorized into two main groups: planned and unplanned maintenance.
Unexpected Failures and Emergency Repairs
Unexpected failures leading to unplanned corrective maintenance can occur due to various reasons, such as:
- Wear and tear
- Improper use of equipment
- Lack of regular inspections
- Environmental factors
Emergency repairs are a key part of unplanned maintenance. They require quick action to fix critical issues and restore operations.
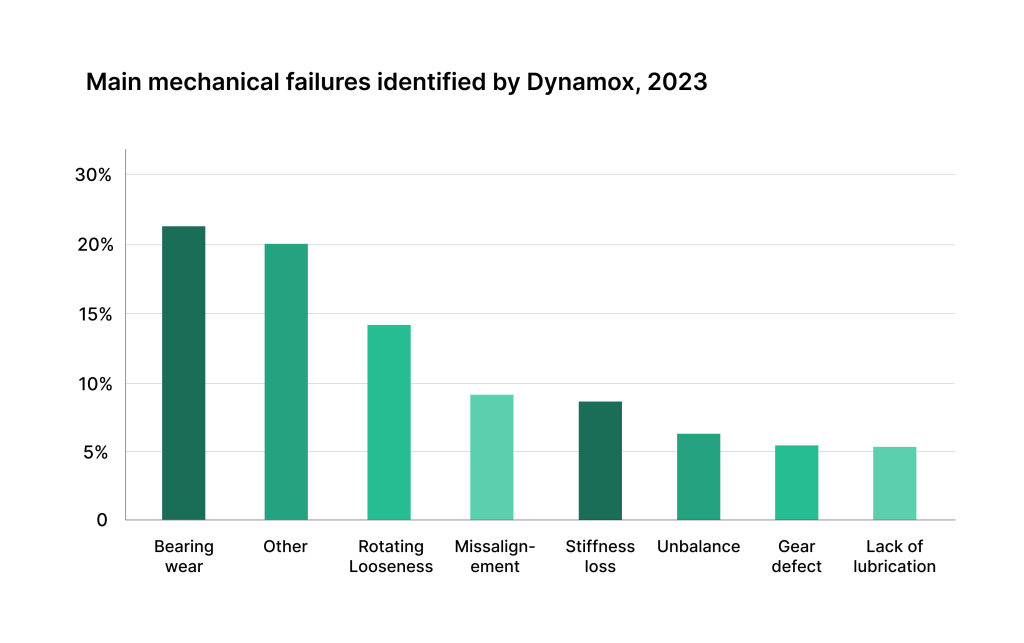
Illustration: WorkTrek / Data: Dynamox
Steps in the emergency repair process include:
- Identify the problem
- Assess the situation
- Gather necessary tools and parts
- Perform repairs quickly
- Test and return equipment to service
Proper training and preparation can help teams respond more effectively to these situations.
Examples of Unplanned Maintenance
Manufacturing Equipment Breakdown
Consider a manufacturing facility that uses a high-speed packaging machine. During a routine production run, the machine suddenly starts making unusual noises and stops operating.
Upon inspection, technicians discover that a critical bearing has failed due to unexpected wear. This situation requires immediate unplanned maintenance because:
- Production has completely halted
- The issue wasn’t detected during routine inspections
- The part wasn’t scheduled for replacement for another six months
In this case, the maintenance team needs to quickly source the bearing, disassemble the machine, replace the component, and verify proper operation before resuming production.
This type of unexpected failure often results in longer downtime than planned maintenance would have required.
HVAC System Emergency
Picture a commercial building during peak summer where the central air conditioning system suddenly stops working. An investigation revealed that the compressor had burned out due to an electrical surge. This represents unplanned maintenance because:
- The failure occurred without warning
- The building’s temperature is rapidly rising
- Occupant comfort and safety are at risk
- Business operations could be affected
The maintenance team must respond by assessing the damage, determining if the compressor can be repaired or needs replacement, and coordinating with HVAC specialists for emergency service. This scenario often increases costs due to emergency service rates and potential business disruption.
Industrial Pump Failure
Consider a chemical processing plant where a crucial transfer pump develops a severe leak due to an unexpected seal failure. This unplanned maintenance scenario is particularly challenging because:
- The leak poses potential safety and environmental risks
- Production processes dependent on the pump must be suspended
- Other connected systems might need to be shut down
- Specialized cleanup procedures may be required
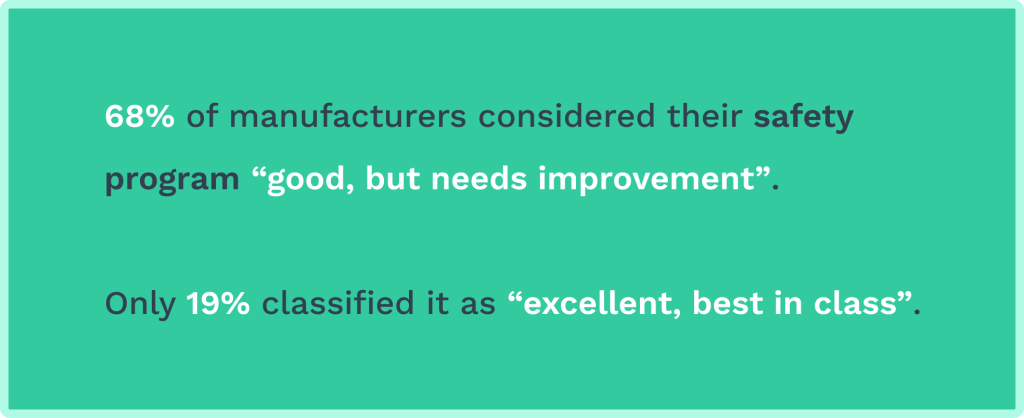
Illustration: WorkTrek / Data: ATS
The maintenance response involves securing the area, implementing proper safety protocols, diagnosing the exact cause of the seal failure, and performing necessary repairs or replacement. This type of unplanned maintenance often reveals opportunities to improve preventive maintenance procedures.
Each of these examples demonstrates key characteristics of unplanned maintenance:
- The failures occur unexpectedly and often at inopportune times
- They typically result in more significant disruption than planned maintenance
- The repairs often cost more due to emergency response requirements
- They frequently reveal opportunities to improve preventive maintenance programs
- They can lead to cascading effects on related systems or processes
Organizations can learn from these unplanned maintenance events by:
- Analyzing the root causes of the failures
- Updating preventive maintenance schedules and procedures
- Implementing better condition monitoring systems
- Improving spare parts inventory management
- Developing more robust emergency response procedures
Understanding these real-world examples helps maintenance teams better prepare for unexpected failures and continuously improve their maintenance strategies to reduce the frequency and impact of unplanned maintenance events.
The Impact of Unplanned Maintenance
Unplanned maintenance events are inevitable in equipment operations and facilities management. They disrupt operations, increase costs, and affect equipment reliability.
Operational Efficiency and Downtime
Unplanned maintenance often leads to unexpected downtime. This disrupts production schedules and can cause missed deadlines. Maintenance teams must address these sudden issues, causing workers to sit idle and wait for repairs to finish.
Efficiency drops as resources are diverted to fix sudden issues. Regular tasks get delayed, creating a backlog of work.
This can lead to a domino effect, impacting other departments and processes and potentially increasing unplanned failure.
If orders are delayed, customer satisfaction may suffer. In some cases, businesses might lose clients due to repeated disruptions.
Maintenance Costs and Downtime Costs
Unplanned maintenance costs are often higher than planned maintenance. Emergency repairs may require rush orders for parts at premium prices, and technician overtime pay can add up quickly.
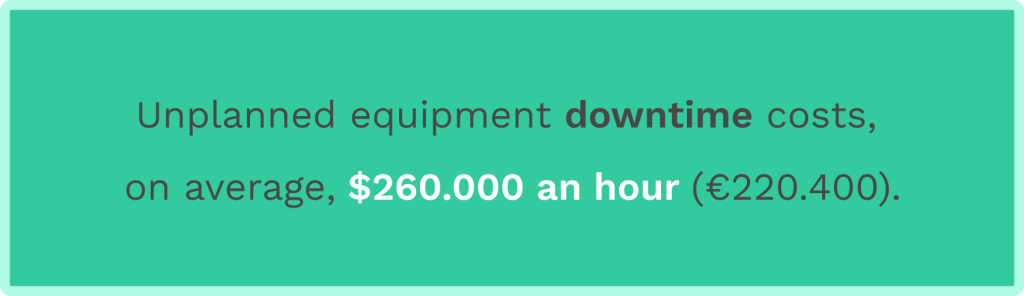
Illustration: WorkTrek / Data: Aberdeen
The true cost goes beyond repairs. Lost production time means lost revenue; even short downtimes can result in significant financial losses for some industries.
Indirect costs can include:
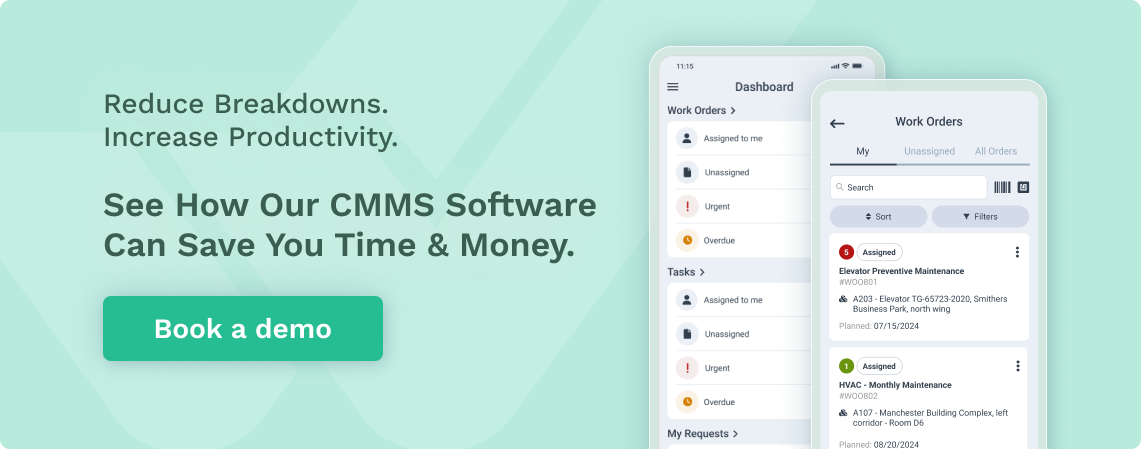
- Wasted materials
- Spoiled products
- Penalties for missed deadlines
- Damage to company reputation
Equipment Operation and Reliability
Frequent unplanned repairs can shorten equipment lifespan. Parts may wear out faster due to sudden stresses from breakdowns.
Equipment reliability suffers when maintenance is reactive rather than proactive. Small issues may go unnoticed until they cause major failures.
Inconsistent equipment performance can lead to:
- Quality control problems
- Safety risks for operators
- Increased energy consumption
Regular operation becomes unpredictable, making it hard to plan production schedules effectively.
Strategies to Minimize Unplanned Maintenance
Companies can take several steps to reduce unexpected equipment failures and downtime. These strategies focus on planning, using advanced tools, and regularly checking equipment health.
Preventive Maintenance Planning
Performing preventive maintenance aims to stop problems before they happen. Companies should make a clear schedule for upkeep tasks. This plan lists what needs to be done and when.
Regular checks and part replacements keep machines running well. A good plan tracks past issues to spot patterns and help fix equipment weaknesses.
Teams should update the plan as they learn more. They can add new tasks or change how often they do specific jobs. A solid preventive plan can reduce surprise breakdowns.
Proactive and Predictive Approaches
Proactive maintenance looks for minor issues before they grow. Workers fix these problems early to avoid more considerable trouble later.
Predictive maintenance uses data and analytics to guess when things might break.In addition, using modern IoT devices can significantly improve predictive maintenance. Some of those tools include:
- Vibration levels
- Temperature
- Oil quality
- Noise levels
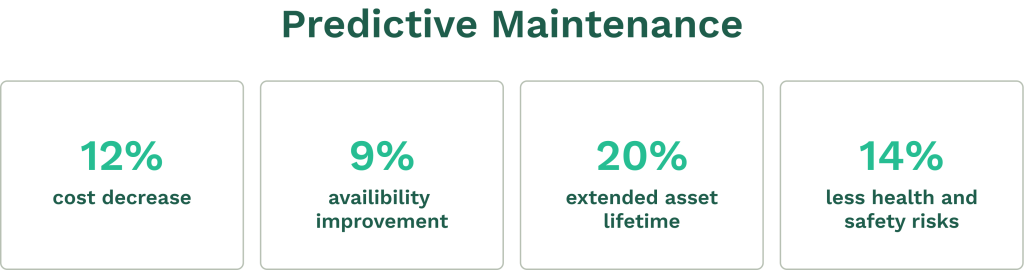
Illustration: WorkTrek / Data: pwc
This info helps teams know when to fix things before they break. It’s smarter than just waiting for something to go wrong.
Adopting these methods can save money and keep machines running longer.
Utilizing CMMS for Maintenance Management
A Computerized Maintenance Management System (CMMS) is a powerful tool for tracking all aspects of maintenance work.
Key features of a good CMMS include:
- Scheduling maintenance tasks
- Tracking inventory
- Managing work orders
- Storing equipment history
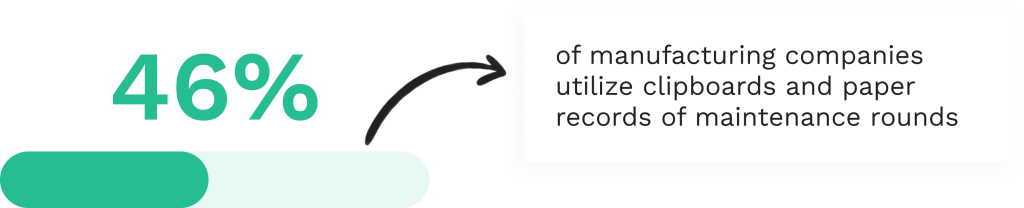
Illustration: WorkTrek / Data: Plant Engineering
CMMS software makes it easier to plan and perform maintenance work. It keeps all information in one place, allowing teams to make better choices.
Using a CMMS can improve maintenance. It helps catch problems early and keeps everything running smoothly.
Regular Maintenance Audits and Equipment Reviews
Regular checks on equipment and maintenance work are crucial. These audits assess how well current plans are working.
During a review, teams should:
- Check equipment condition
- Look at maintenance records
- Talk to operators about any issues
- Test safety systems
These checks help find gaps in the maintenance plan. They also show which machines might need more care.
Teams should update their plans after each audit. This keeps the maintenance strategy fresh and effective, and regular reviews ensure that maintenance efforts stay on track.
Developing a Comprehensive Maintenance Plan
A well-structured maintenance plan helps prevent unplanned downtime and extends asset life. Understanding the types of unplanned maintenance, which include reactive, corrective, and opportunistic maintenance, is essential to being prepared for unexpected events in equipment operations and facilities management.
The plan combines different maintenance strategies and optimizes schedules to keep equipment running smoothly.
Incorporating Opportunistic Maintenance
Opportunistic maintenance takes advantage of planned downtime to perform extra tasks. This approach saves time and reduces overall maintenance costs.
Key benefits include:
- Fewer equipment shutdowns
- Improved efficiency
- Better use of maintenance resources
To implement opportunistic maintenance:
- List potential tasks for each asset
- Train staff to spot maintenance opportunities
- Create flexible work orders
- Track and analyze results
This strategy helps catch small issues before they become big problems.
Maintenance Schedule Optimization
A good maintenance schedule balances preventive and corrective actions. It aims to minimize downtime while maximizing equipment life.
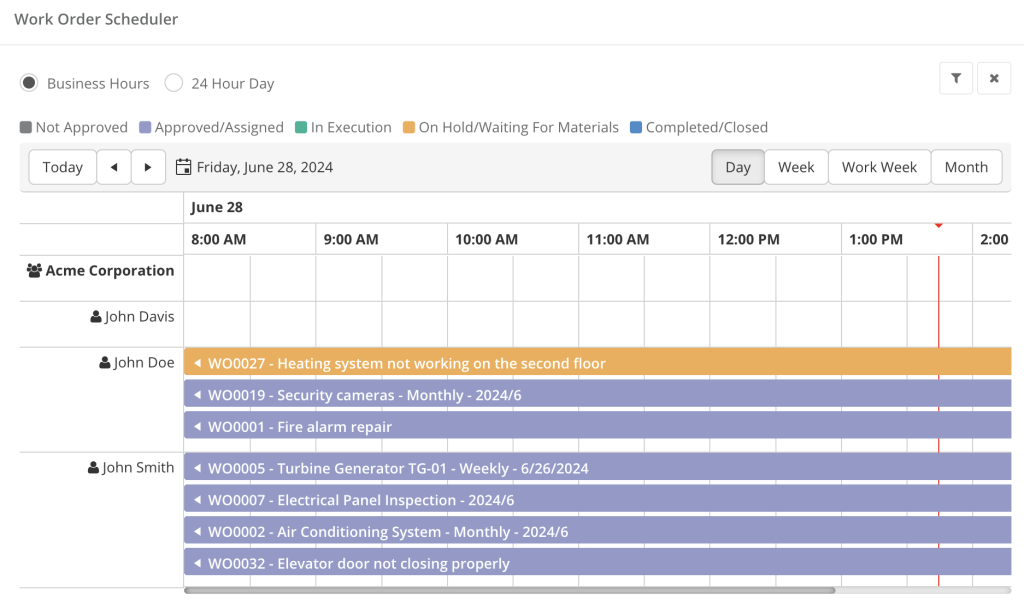
Source: WorkTrek
Steps to optimize schedules:
- Gather equipment data
- Analyze failure patterns
- Set maintenance intervals
- Use software to track and adjust plans
Regular reviews help fine-tune the schedule, ensuring maintenance happens at the right time, not too early or too late.
Teams should be ready to adjust plans as needed. Flexibility is key to handling unexpected issues while sticking to the overall schedule.
Asset Life Extension Strategies
Extending asset life reduces replacement costs and improves return on investment. It requires a mix of proactive maintenance and smart operational practices.
Effective strategies include:
- Regular inspections and cleaning
- Proper lubrication and calibration
- Monitoring equipment performance
- Replacing worn parts before failure
Developing a comprehensive maintenance plan is crucial for asset longevity. It should cover all equipment lifecycles, from installation to retirement.
Training operators on proper equipment use also helps extend asset life. This reduces wear and tear from misuse or poor practices.
Role of Maintenance Team and Training
A skilled maintenance team is vital for plan success. They need the right knowledge and tools to carry out tasks effectively.
Key aspects of team development:
- Ongoing technical training
- Cross-training for flexibility
- Safety and compliance education
- Soft skills development
Teams should understand both unplanned and planned maintenance. This helps them respond to unexpected outages and prevent future issues by scheduling and expecting maintenance tasks.
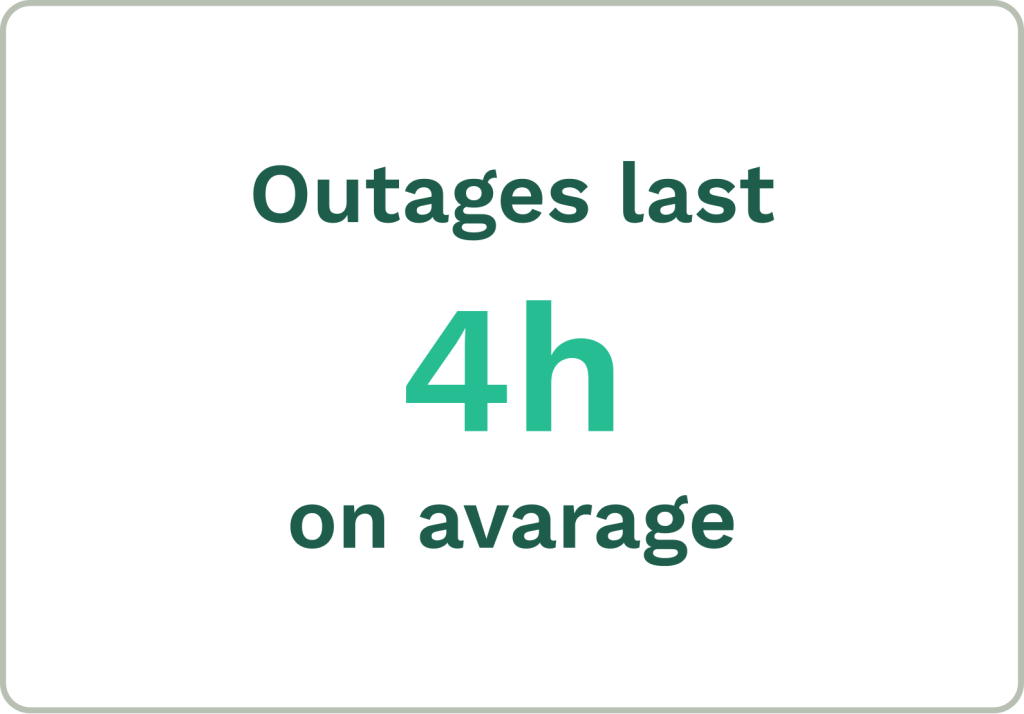
Illustration: WorkTrek / Data: Machine Metrics
Good communication is essential. Teams need to share information about equipment status and maintenance needs.
Regular meetings help keep everyone aligned with maintenance goals and provide a chance to discuss challenges and improvements.
Technological Advancements in Maintenance
Modern technology has transformed how businesses approach maintenance. New tools and systems help companies prevent breakdowns, save money, and keep equipment running smoothly.
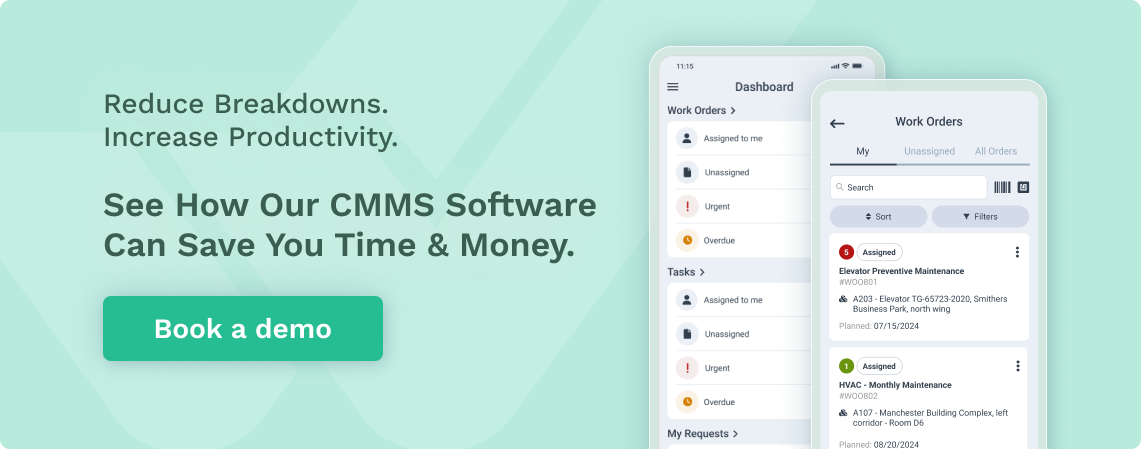
The Role of CMMS in Maintenance Processes
A Computerized Maintenance Management System (CMMS) like WorkTrek is key for effective maintenance. It helps track equipment, schedule work, and manage inventory.
With a CMMS, teams can easily see what needs fixing and when. This helps prevent small issues from becoming big problems. The system also records all repairs, making it easier to spot patterns.
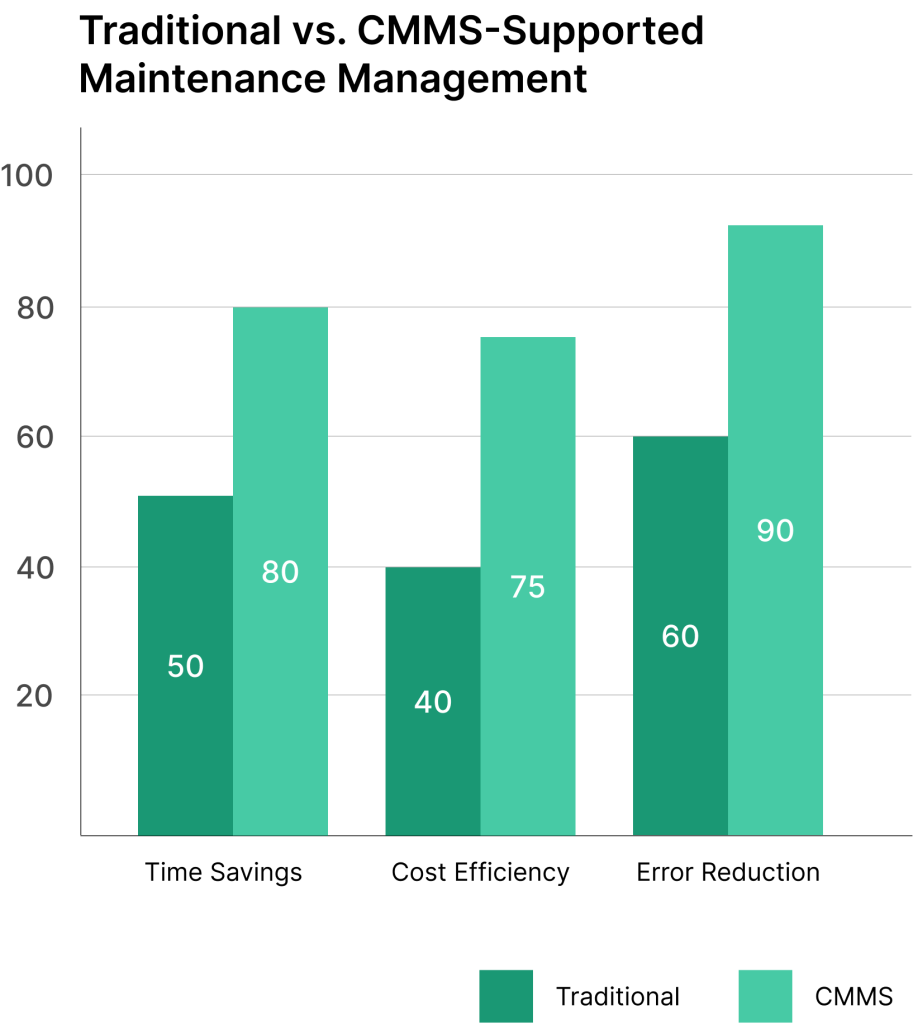
Illustration: WorkTrek / Data: Camcode
Many CMMS tools can now be accessed on mobile devices. This means technicians can update information immediately, no matter where they work.
CMMS software also helps with planning. It can show which parts are running low and need to be ordered, keeping maintenance work moving forward without delays.
Automation in Maintenance Tasks
Automation is changing how maintenance tasks get done. Robots and smart machines can now do some of the work people used to do.
For example, drones can inspect tall buildings or hard-to-reach places. This is safer and faster than sending someone to climb up and look. Some factories use robots to clean and oil machines automatically.
AI-powered systems can also help. They can monitor machine performance and alert technicians if something seems off. This helps catch problems early before they cause breakdowns.
Automated systems can also handle routine tasks like ordering supplies and freeing maintenance staff to focus on more complex work.
Data Analytics for Predictive Maintenance
Data analytics is a powerful tool for predicting when equipment might fail. By analyzing data patterns, companies can fix problems before they occur.
Sensors on machines collect information constantly. This data shows how the equipment is working. Computer programs then look for signs that something might go wrong soon.
This approach, called predictive maintenance, can save a lot of money. It helps avoid surprise breakdowns that stop work and cost time and money to fix.
Companies can also use this data to decide when to replace old equipment. They can see which machines break down most often and plan to buy new ones.
Best Practices for Maintenance Management
Good maintenance management helps reduce downtime and costs. It keeps equipment running smoothly and prevents unexpected breakdowns. These practices focus on planning, organizing, and improving maintenance activities.
Effective Work Order Management
Work orders are key to good maintenance. They track tasks, assign staff, and set priorities. A clear work order system helps teams finish jobs faster.
Digital work order systems make things easier. They let staff see job details on phones or tablets, reducing paperwork and saving time.
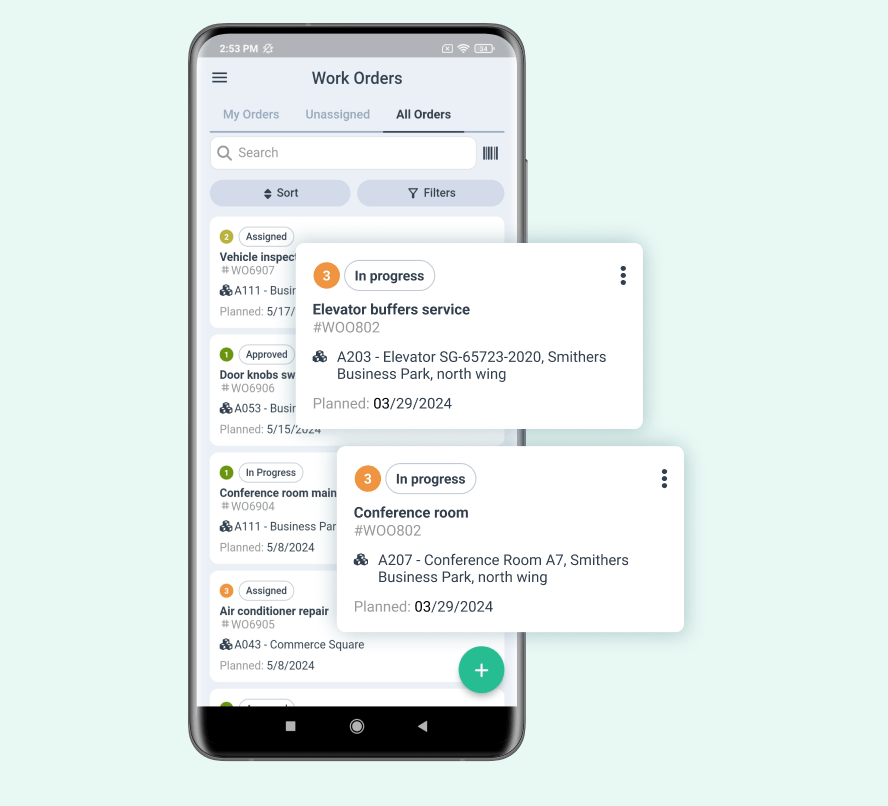
Source: WorkTrek
Regular reviews of work orders show what’s working well and point out areas for improvement. Tracking metrics like completion time helps measure success.
Training staff on work order procedures is important. It ensures everyone follows the same steps. This leads to more consistent results.
Asset Management and Inventory Control
Keeping track of assets and parts is crucial. It helps prevent repair delays. A good system shows what’s in stock and what needs ordering.
Regular audits of inventory keep records accurate. This prevents overstocking or running out of parts and helps control costs.
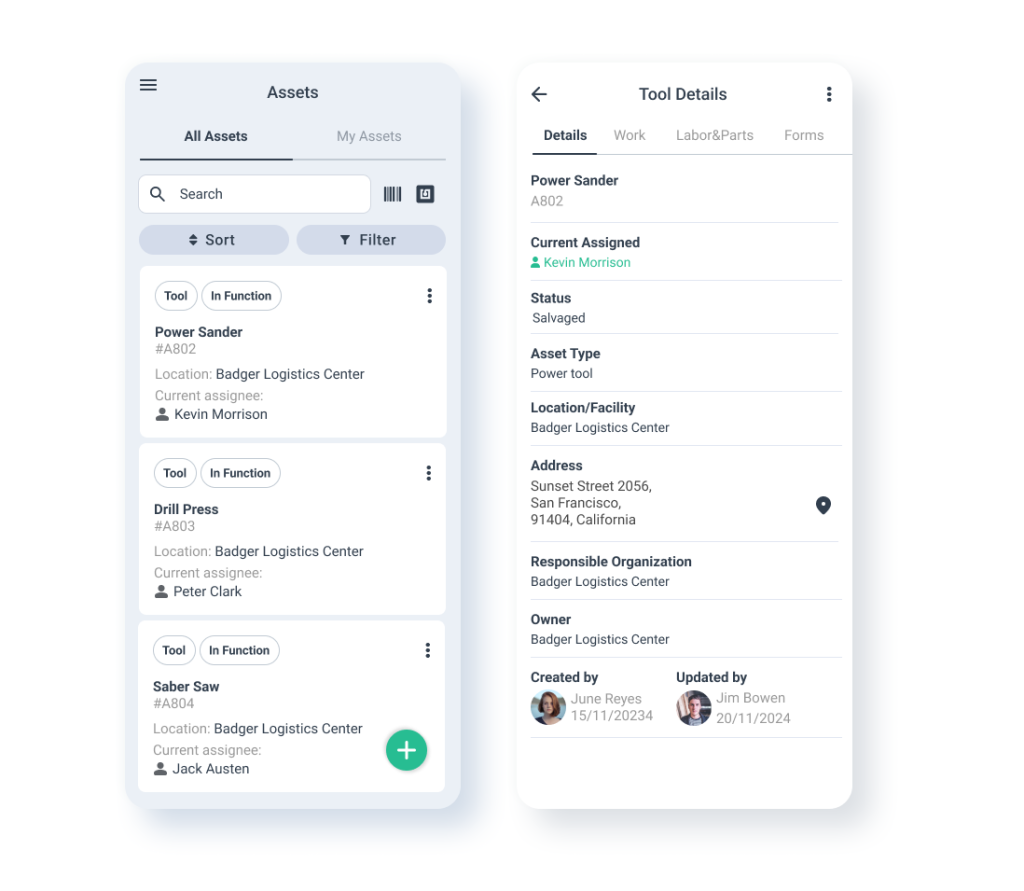
Source: WorkTrek
Asset management software can make this easier. It tracks equipment life cycles and maintenance history, which helps plan for replacements and upgrades.
Setting reorder points for critical parts is smart. It ensures you always have what you need on hand. This cuts down on emergency orders and rush fees.
Cultivating a Culture of Maintenance Excellence
Creating a culture that values maintenance is vital. It starts with leadership showing its importance. Regular training keeps skills sharp and demonstrates a commitment to improvement.
Encouraging staff to report issues early helps catch problems. This can prevent minor issues from becoming big breakdowns. Reward programs for sound maintenance practices can boost motivation.
Clear communication between maintenance and other teams is key. It helps everyone understand how maintenance impacts the whole operation. Regular meetings to share updates and concerns can improve teamwork.
Safety should always be a top priority in maintenance work. Proper safety training and equipment protect workers and assets and help build trust and respect within the team.
Conclusion
Unplanned maintenance poses challenges for businesses. It disrupts operations and can be costly. Companies need to take steps to reduce unexpected breakdowns.
Developing a good maintenance strategy is key to reducing unplanned maintenance. This includes regular inspections and preventive care. It helps catch issues before they become big problems.
Training maintenance staff can help improve maintenance operations. They need to know how to spot potential issues early, and quick response times can minimize downtime when breakdowns occur.
Using technology can improve maintenance operations. Sensors and monitoring systems help track equipment health. This data allows for better planning and fewer surprises.
By focusing on these areas, companies can reduce unplanned maintenance. This leads to smoother operations and better overall performance.