Get a Free WorkTrek Demo
Let's show you how WorkTrek can help you optimize your maintenance operation.
Try for freeWhat is facility maintenance? Facility maintenance keeps buildings and equipment running smoothly.
It covers many tasks to ensure safe, clean, and functional spaces. These tasks include fixing broken items, cleaning, and ensuring systems work correctly.
Facility maintenance is crucial for the longevity and efficiency of buildings and equipment. It helps prevent costly breakdowns and extends the life of assets. Regular upkeep also creates a better environment for people who use the facilities.
Good maintenance involves planning and quick responses to problems. It requires skilled workers who can handle various issues. From changing light bulbs to managing complex HVAC systems, facility maintenance keeps everything in shape.
Listen to an Audio Version of this Article
Understanding Facility Maintenance
Facility maintenance keeps buildings safe, functional, and comfortable. It involves regular upkeep, repairs, and improvements to extend a property’s lifespan and value.
Definition and Importance of Facility Maintenance
Facility maintenance is keeping buildings and equipment in good working order. It includes tasks like fixing broken items, cleaning, and updating systems. This is when maintenance technicians perform preventive maintenance or a facility manager fixes malfunctioning equipment.
Illustration: WorkTrek / Data: University of South Alabama
This work is important for several reasons:
- Safety: Well-maintained facilities are safer for users.
- Efficiency: Properly working systems use less energy and resources.
- Cost savings: Regular upkeep prevents costly emergency repairs.
- Compliance: Maintenance helps meet legal and regulatory requirements.
Facility maintenance also boosts property value, reduces maintenance costs, and improves user satisfaction. It covers many activities, from daily cleaning to major renovations, aiming to reduce costly downtime.
Roles and Responsibilities of a Facility Manager
Facility managers play a key role in maintaining buildings. Their primary duties include:
• Planning maintenance schedules
• Managing budgets for repairs and upgrades
• Overseeing staff or contractors
• Ensuring compliance with laws and regulations
• Responding to emergencies
Facility managers also handle the following:
- Energy management
- Space planning
- Security coordination
- Waste management
- HVAC Units
- Cleaning schedules
They need strong problem-solving skills and knowledge of building systems. Good communication is vital for working with staff, tenants, and service providers.
Facility Maintenance vs. Property Maintenance
Facility maintenance and property maintenance are related but different:
Source: WorkTrek
Facility maintenance is typically more extensive. It often includes property maintenance tasks plus additional responsibilities. Both aim to keep spaces functional and appealing, but facility maintenance deals with complex issues and systems.
Maintenance Strategies
Effective maintenance strategies help keep facilities running smoothly and safely. They prevent breakdowns, cut costs, and extend equipment life. Different approaches suit various needs and budgets.
Types of Maintenance
Facilities use several maintenance types. Reactive maintenance fixes issues after they happen. Preventive maintenance aims to stop problems before they start. Predictive maintenance uses data to forecast when repairs are needed. Corrective maintenance addresses faults found during inspections.
Reliability-centered maintenance focuses on keeping critical systems working. It looks at how equipment fails and finds ways to prevent those failures. This method often combines other maintenance types for the best results.
Preventive Maintenance Explained
Preventive maintenance is like regular health check-ups for buildings and equipment. It includes routine inspections, cleaning, and part replacements. This approach helps catch small issues before they become big problems.
Illustration: WorkTrek / Data: FMX
Tasks might include changing filters, lubricating parts, or tightening bolts. These jobs are done on a set schedule based on time, usage, or both.
Preventive maintenance can save money by avoiding costly breakdowns and extending equipment life.
Predictive versus Reactive Maintenance
Predictive maintenance uses technology to spot problems early. It relies on sensors and data analysis to tell when a machine is likely to fail. This method allows repairs at the right time, not too early or too late.
Reactive maintenance waits until something breaks to fix it. It’s simple but can lead to unexpected downtime and higher costs. Emergencies often mean rushed repairs and extra expenses.
Predictive maintenance usually costs less in the long run. It helps avoid surprise breakdowns and keeps operations running smoothly.
Implementing a Maintenance Plan
A good maintenance plan starts with clear goals. These might include cutting costs, improving safety, or extending equipment life. The plan should fit the facility’s needs and budget.
Steps to create a plan:
- List all equipment and systems
- Rank items by importance
- Choose the best maintenance type for each item
- Set up schedules and procedures
- Train staff on the new plan
- Use software to track work and results
Source: WorkTrek
Regular reviews help improve the plan over time. Tracking data shows what’s working and what needs to change. A well-run maintenance strategy keeps facilities in top shape and saves money.
Planning and Scheduling
Good planning and scheduling are key to successful facility maintenance. They help keep buildings running smoothly and prevent costly breakdowns.
Creating a Maintenance Schedule
Source: WorkTrek
A maintenance schedule lists all tasks needed to keep a facility in top shape. It includes daily, weekly, monthly, and yearly jobs and should cover all equipment and systems in the building.
Regular HVAC, plumbing, and electrical system checks are often part of the plan. Cleaning tasks and safety inspections also go on the list. A good schedule balances routine upkeep with long-term projects.
Managers should review and update the schedule often. This helps catch any missed tasks or changes in the facility’s needs.
Resource Allocation and Management
Resource allocation means giving out people, tools, and money for maintenance work. It’s about using what you have in the best way possible.
Managers need to know their team’s skills and the tools they have. They should match the right person for each job. Sometimes, they may need to hire outside help for particular tasks.
Good resource management also means tracking supplies. Running out of parts can delay important repairs, and a well-stocked inventory helps avoid this problem.
Using CMMS for Efficient Scheduling
CMMS stands for Computerized Maintenance Management System. It’s a tool that makes scheduling and tracking maintenance work easier.
A CMMS can:
- Create and assign work orders
- Track equipment history
- Manage parts and inventory
- Schedule routine maintenance
- Manage Assets
- Manage Work Logs
- Manage Tasks
- Create a Preventive Maintenance Plan
Source: WorkTrek
This system helps managers plan better. They can see what work is coming up and who can do it. CMMS also keeps records of all maintenance tasks. This data helps spot patterns and improve future planning.
Many CMMS tools can send alerts when it’s time for scheduled tasks. This helps ensure that jobs are not forgotten or delayed.
Maintenance Operations
Facility maintenance operations involve regular tasks to keep buildings and equipment in good working order. These activities ensure the safety, efficiency, and longevity of facilities.
Routine Inspections and Audits
Regular inspections are key to spotting issues early. Maintenance teams check buildings, systems, and equipment on set schedules. They look for wear and tear, damage, or potential safety hazards.
Inspections may cover:
- HVAC systems
- Electrical systems
- Plumbing
- Fire safety equipment
- Structural elements
Audits go deeper than routine checks. They involve detailed reviews of maintenance practices and facility conditions. These help identify areas for improvement in maintenance processes.
Repair and Corrective Actions
When inspections find problems, repairs follow. Quick fixes prevent small issues from growing into big ones. Maintenance teams address:
- Leaky pipes
- Broken fixtures
- Faulty electrical outlets
- Damaged flooring
For bigger problems, teams plan more complex repairs. They might need to:
- Replace old equipment
- Fix structural damage
- Upgrade outdated systems
Corrective actions also include steps to prevent future issues. This might mean changing maintenance schedules or updating procedures.
Maintenance PaiCles and Work Orders
Maintenance tasks cover a wide range of activities. Some are planned, while others respond to sudden needs. Common tasks include:
- Changing air filters
- Lubricating machinery
- Cleaning gutters
- Painting walls
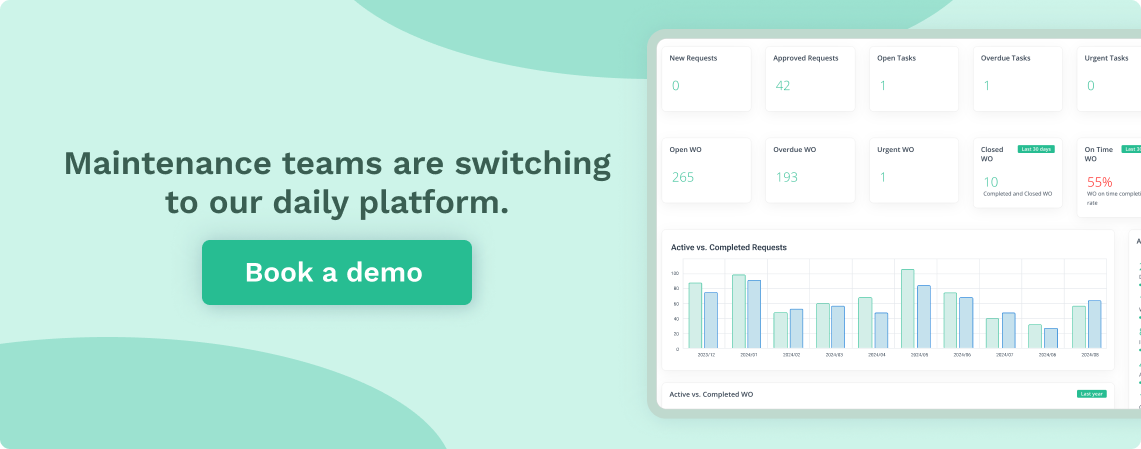
Source: WorkTrek
Work orders help organize these tasks. They detail:
- What needs to be done
- Who should do it
- When it should be completed
- What materials are needed
Teams use work order systems to track progress and manage workloads. This helps ensure all tasks are completed on time.
Maintenance Teams and Technicians
Skilled workers carry out maintenance operations. Teams often include:
- Electricians
- Plumbers
- HVAC technicians
- General maintenance workers
- Maintenance Technicians
- Facility Maintenance Workers
These professionals have specific skills for different tasks. They work together to keep facilities running smoothly.
Technicians need ongoing training to stay current with new technologies and best practices. In their daily work, they use hand tools and advanced equipment.
Teams may include in-house staff or outside contractors. The choice depends on the facility’s needs and resources.
Facility Systems and Components
Facility maintenance involves managing various interconnected systems that keep buildings running smoothly. These systems work together to create safe, comfortable, and efficient environments for occupants.
HVAC Systems and Building Systems
HVAC systems, which are generally expensive capital assets, control indoor temperature, humidity, and air quality. They include heating, cooling, and ventilation equipment. Regular HVAC maintenance ensures optimal performance and extends equipment life.
Illustration: WorkTrek / Data: FacilitiesNet
Building systems encompass electrical, plumbing, and structural components. Electrical systems power lights, equipment, and outlets. Plumbing systems manage water supply and waste removal. Structural elements like walls, floors, and roofs need periodic inspections and repairs.
Proper upkeep of these systems prevents breakdowns, improves efficiency, and maintains occupant comfort. It also helps avoid costly emergency repairs.
Energy Consumption and Sustainability
Facilities use energy for lighting, heating, cooling, and powering equipment. Energy-efficient practices can cut costs and reduce environmental impact.
LED lighting, motion detectors, and smart controls help lower electricity use.
Improved insulation and weatherization minimize heat loss, and regular equipment tune-ups keep systems running efficiently.
Illustration: WorkTrek / Data: pwc
Many facilities now use renewable energy sources like solar panels, Geothermal energy, or wind turbines. These green technologies can offset traditional energy consumption and shrink carbon footprints.
Sustainability efforts often include water conservation measures. Low-flow fixtures and rainwater harvesting systems help reduce water waste.
Fire Safety and Compliance
Fire safety is crucial for protecting lives and property. Facilities must have working smoke detectors, fire alarms, and sprinkler systems. Fire extinguishers need regular inspections and replacements.
Clear evacuation routes and emergency lighting are essential. Staff should receive fire safety training and participate in regular drills.
Facilities must comply with local fire codes and safety regulations. This includes properly storing flammable materials and maintaining fire-resistant building materials.
Regular safety audits help identify and fix potential hazards. Staying up-to-date with changing regulations ensures ongoing compliance and safety.
Facility Management Technologies
Modern technology has transformed facility maintenance. New tools and systems help managers keep buildings running smoothly and efficiently.
Facility Maintenance Software
Facility maintenance software streamlines tasks and improves communication. CMMS software like WorkTrek can provide you the ability to create and track work orders, define preventive maintenance schedules and give users mobile apps to manage their work queues.
These programs track work orders, schedule preventive maintenance, and manage inventory.
Managers can easily assign jobs to staff and monitor progress in real time.
Some software allows tenants to submit requests directly, reducing phone calls and emails. The system can also send automatic updates to keep everyone informed.
Many CMMS programs offer mobile apps. Workers can access information and update job status anywhere in the building, saving time and increasing productivity.
Smart Maintenance Management
Smart maintenance helps facility managers make smarter decisions. By collecting and analyzing information, they can spot trends and prevent issues before they happen.
Sensors placed throughout a building gather data on equipment performance. This information feeds into the maintenance system.
The software can trigger an alert when a machine shows signs of wear. Predictive maintenance uses this data to forecast when repairs will be needed.
This approach reduces downtime and extends the life of assets.
Impact of Technology on Operational Efficiency
Technology boosts operational efficiency in several ways. Automated systems handle routine tasks, freeing up staff for more complex work.
Digital tools make it easier to track key performance metrics. Managers can see how well the facility is running at a glance.
Advanced analytics help optimize resource allocation. Managers can adjust staffing and energy consumption for maximum efficiency by understanding usage patterns.
Evaluating Maintenance Effectiveness
Proper evaluation of maintenance efforts is key to ensuring facilities run smoothly and efficiently. It helps identify areas for improvement and optimize resource allocation.
Comprehensive Assessment and Audits
Regular assessments help pinpoint maintenance strengths and weaknesses. Facility managers should conduct thorough inspections of all building systems and equipment. This includes checking HVAC, electrical, plumbing, and structural components.
Audits can reveal hidden issues before they become major problems. They also help create a baseline for future comparisons. Managers should document findings in detail and use standardized checklists for consistency.
Third-party audits can provide an unbiased perspective. These external reviews often spot issues that internal teams might overlook.
Performance Metrics and KPIs
Measuring maintenance performance is crucial for improvement. Key Performance Indicators (KPIs) offer concrete data to track progress.
Common metrics include:
- Equipment uptime
- Mean time between failures
- Work order completion rates
- Energy efficiency
Managers should set clear targets for each KPI. Regular tracking helps identify trends and areas needing attention. Data visualization tools can make metrics easier to understand. Charts and graphs help teams quickly grasp performance levels.
Maintaining Asset Longevity and Reliability
Effective maintenance extends the life of facility assets.
This saves money and reduces disruptions. Strategies to boost longevity include:
- Following manufacturer recommendations
- Using high-quality replacement parts
- Training staff on proper equipment use
Predictive maintenance techniques can catch issues early, preventing unexpected breakdowns and extending equipment life. Vibration analysis and thermal imaging are useful predictive tools.
Reliability-centered maintenance focuses on critical systems. It prioritizes tasks that have the most significant impact on operations. This approach helps balance costs with equipment performance.
Sustainable Development and Green Maintenance
Sustainable practices in facility maintenance can reduce costs and environmental impact. Green maintenance focuses on energy efficiency and eco-friendly methods.
Incorporating Sustainability in Maintenance
Sustainable maintenance uses resources wisely, aims to cut waste, and saves energy. Facilities can install LED lights to use less electricity, and smart thermostats help control heating and cooling better.
Regular equipment upkeep keeps it running efficiently, saving energy and extending its life. Fixing leaks quickly stops water waste. Using green cleaning products protects the environment and worker health.
Facilities can also use renewable energy, like solar panels, which reduces reliance on fossil fuels. Rainwater collection systems also reduce water use. Green roofs help insulate buildings and manage stormwater.
Reducing Environmental Impact
Recycling programs lower waste sent to landfills. Facilities can set up bins for paper, plastic, and metal. Composting food scraps turns waste into beneficial soil.
Using eco-friendly materials for repairs helps the planet. Low-VOC paints release fewer harmful chemicals. Sustainable flooring options include bamboo and recycled materials.
Regular energy audits find ways to save power. Fixing air leaks and adding insulation cuts heating and cooling costs. Upgrading to energy-star appliances reduces electricity use. Encouraging staff to turn off lights and computers when not in use also saves energy.
Financial and Business Considerations
Proper facility maintenance impacts a company’s bottom line in many ways. It can lead to cost savings, boost productivity, and increase property value over time.
Cost Savings and Budgeting for Maintenance
Regular upkeep helps avoid costly repairs down the road.
Regular upkeep helps avoid costly repairs down the road. Setting aside money for maintenance prevents surprise expenses—a good budget plans for routine tasks and unexpected issues.
Tracking maintenance costs over time shows where money is being spent. This data helps facility managers make smart choices about repairs versus replacements and reveals which equipment needs the most attention.
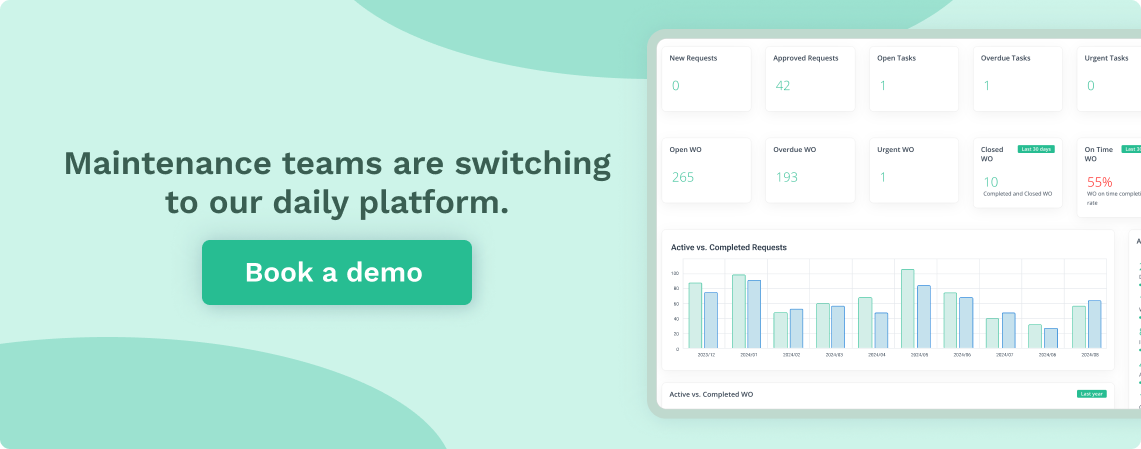
Some companies use software to manage maintenance schedules and costs. These tools can spot trends and forecast future needs, making budgeting more accurate and helping control spending.
Maximizing Productivity and Reducing Downtime
Well-maintained facilities keep operations running smoothly. When equipment works right, employees can do their jobs without delay, boosting overall productivity.
Unplanned downtime is expensive. It stops work and can lead to missed deadlines. Regular maintenance cuts the risk of sudden breakdowns, keeping production on track.
A clean, safe workplace also improves employee morale. Workers are more productive when they have the right tools and a good environment. Proper maintenance creates better working conditions for everyone.
Enhancing Property Value Through Maintenance
Good upkeep protects a company’s investment in its buildings and equipment. Well-maintained properties are worth more and last longer. This is key for businesses that own their facilities.
Regular maintenance also makes a good impression on visitors and clients. A clean, well-kept building shows that a company cares about quality. This can help attract new business and keep current customers happy.
Good maintenance can lead to better lease terms for companies that rent space. Landlords often prefer tenants who take care of the property, which can result in lower rent or other perks when it’s time to renew a lease.
Industry-Specific Facility Maintenance
Facility maintenance varies significantly across different industries. Each sector has unique needs and challenges that require specialized approaches and expertise.
Commercial Buildings Maintenance
Commercial buildings need regular upkeep to stay safe and functional. This includes offices, malls, and hotels. HVAC systems are a top priority. They keep indoor air clean and temperatures comfortable.
Elevators also need frequent checks. They move people safely between floors. Lighting systems require ongoing care, too. Good lighting helps workers stay productive and keeps shoppers happy.
Fire safety systems, including alarms, sprinklers, and extinguishers, need regular testing. Plumbing systems must also work well to prevent water damage. Parking lots also need maintenance to stay safe for cars and people.
Industrial Maintenance Essentials
Industrial sites have heavy-duty equipment that needs special care. Machines in factories and plants must run smoothly to avoid costly breakdowns. Regular oil changes and part replacements are key.
Safety is crucial in industrial settings. Guards and barriers around machines must stay in good shape, and floors need to be kept clean and dry to prevent slips and falls.
Air quality is important, too. Ventilation systems need frequent cleaning and filter changes. This keeps workers healthy and follows regulations. Waste management is another big task. Proper disposal of chemicals and materials is a must.
Residential Building Maintenance Challenges
Residential buildings face unique maintenance issues. Apartments and condos have shared spaces that need care, and hallways, lobbies, and elevators see heavy use every day.
Plumbing problems can affect multiple units. Quick fixes are important to keep tenants happy. HVAC systems in residential buildings often work overtime. They need regular tune-ups to run well.
Pest control is an ongoing challenge in homes. Regular treatments help keep bugs and rodents away. Landscaping is another key task. Well-kept grounds make residents proud of where they live. Trash removal and recycling programs need careful planning in large buildings.
Space Management and Allocation
Space management and allocation are key parts of facility maintenance. They help make the most of available areas and support the needs of building users.
Strategies for Efficient Space Utilization
Good space use starts with a clear floor plan. This shows how rooms and areas are laid out. Facility managers often use computer programs to map spaces. These tools help track where people and equipment are placed.
Flexible spaces are becoming more common.
Movable walls and modular furniture let rooms change as needed, which is useful for offices that grow or shrink their teams.
Some tricks to save space include:
- Using vertical storage systems
- Creating multi-purpose areas
- Adding hot-desking for remote workers
Regular space audits help spot unused or wasted areas.
Managers can then reassign these spaces for better use.
Maintenance’s Role in Space Allocation
The maintenance team plays a big part in space allocation. They keep areas safe and working well for their assigned uses. This includes:
- Checking that rooms meet safety codes
- Fixing issues that could limit space use
- Updating systems for new space functions
Maintenance staff also help plan for future needs. They know how building systems work and what changes might be needed, which is valuable input when deciding how to use spaces.
Good communication between maintenance and space planners is crucial. It ensures that allocated spaces can be properly maintained and supported.
Legal and Regulatory Compliance
Facility maintenance involves following many rules and laws to keep buildings safe and up to code. These regulations cover health, safety, and building standards.
Adhering to Health and Safety Regulations
Health and safety rules are key in facility upkeep. Buildings must meet air quality standards to prevent health issues. Regular checks for mold, asbestos, and other hazards are needed. Proper ventilation systems are a must.
Source: WorkTrek
Safety measures include clear emergency exits and well-lit stairways. Floors need to be slip-resistant. Facilities should have first aid kits in easy-to-reach spots. Staff training on safety rules is important too.
Keeping good records of all safety checks and fixes helps prove compliance. This can protect against legal issues if accidents happen.
Compliance with Fire and Building Codes
Fire safety is a big part of building codes. Facilities need working smoke detectors and fire alarms, and fire extinguishers must be in the right places and checked often.
Building codes set rules for things like:
- Electrical systems
- Plumbing
- Structural integrity
- Accessibility for people with disabilities
Regular inspections help catch problems early, keeping buildings safe and avoiding fines. As codes change over time, updates to old systems may be needed.
Facility managers should know local building laws and get permits for big changes or repairs. Keeping buildings up to code helps avoid legal trouble and keeps people safe.
Summary
Illustration: WorkTrek / Data: Forbes
Facility maintenance is more than fixing what’s broken—it’s about creating spaces where people can thrive and work safely.
Good maintenance touches every aspect of our daily lives, from the HVAC system keeping office workers comfortable during the summer heat to the well-maintained elevator helping elderly residents reach their apartments.
The field combines strategic planning, preventive care, and quick problem-solving to keep buildings running smoothly. Whether a facility manager schedules routine inspections, a maintenance technician responds to emergency repairs, or a sustainability expert implements green solutions, each role plays a vital part in extending building life and reducing costs.
As technology advances and sustainability becomes increasingly important, facility maintenance continues to evolve. But at its heart, it remains focused on one core purpose: ensuring that the spaces where we work, live, and gather are safe, efficient, and welcoming for everyone who uses them.