Get a Free WorkTrek Demo
Let's show you how WorkTrek can help you optimize your maintenance operation.
Try for freeReliability-centered maintenance (RCM) is key to keeping equipment running smoothly. It focuses on making sure machines and tools work well and stay reliable. RCM is a process where companies identify important assets and create plans to keep them working at their best.
Source: Reliabilityweb
This approach helps businesses avoid breakdowns and cut costs. RCM examines each piece of equipment independently. It determines what could go wrong and how to prevent problems before they start.
RCM is not just about fixing things when they break. It’s about smart planning to prevent issues. This method can improve performance, reduce downtime, and be more cost-effective for maintenance. Companies that use RCM often see significant improvements in how their equipment works.
Listen to a Podcast on RCM
Fundamentals of Reliability-Centered Maintenance
Reliability-centered maintenance (RCM) is a method for helping organizations keep their equipment running smoothly. It focuses on finding the best ways to prevent breakdowns and keep things working well.
Defining RCM
RCM is a process that identifies important assets and creates plans to keep them working. It examines each piece of equipment and determines the best way to maintain it. The goal is to ensure that everything keeps running without wasting time or money on unnecessary maintenance.
Source: WorkTrek
RCM asks questions like:
- What does this equipment do?
- How can it fail?
- What happens if it fails?
- How can we prevent failures?
By answering these questions, RCM helps create a smart maintenance plan.
History and Evolution in the Aviation Industry
RCM started in the aviation industry in the 1960s. United Airlines first developed it to improve airplane safety and reliability. They wanted to find better ways to maintain planes without doing unnecessary work.
The success in aviation led other industries to adopt RCM. In the 1980s, the U.S. military began using RCM. Soon after, power plants, factories, and other businesses started using it too.
As RCM grew, groups like the Society of Automotive Engineers created standards. The SAE JA1011 standard helps ensure correct RCM across different industries.
Principles of RCM
RCM follows key principles to guide maintenance decisions:
- Focus on system function, not just equipment
- Identify failure modes that matter most
- Prioritize important equipment
- Use a variety of maintenance tactics
- Accept that some failures will happen
- Use data to make decisions
- Continuously improve the process
Illustration: WorkTrek / Data: WBDG
These principles help teams make smart choices about maintaining their equipment. They focus on what’s most important and use the right tools for each job.
Process of RCM Analysis
The RCM analysis process follows these steps:
- Choose a system to analyze
- Define system functions
- Identify functional failures
- Determine failure modes
- Assess failure effects
- Select maintenance tasks
- Implement and review
Teams work through each step carefully. They examine how equipment can fail and what those failures mean. Then, they choose the best ways to prevent or deal with those failures.
RCM isn’t just about fixing things. It’s about understanding equipment deeply and making smart choices. This process helps keep systems running reliably and efficiently.
Maintenance Strategies Influenced by RCM
Reliability Centered Maintenance (RCM) shapes various maintenance approaches. These strategies aim to boost equipment reliability and reduce downtime. Each method targets specific maintenance needs and asset conditions.
Preventive Maintenance
Preventive maintenance is a key strategy in RCM. It involves regular, scheduled upkeep to prevent breakdowns. This approach helps extend equipment life and avoid unexpected failures.
Illustration: WorkTrek / Data: Reliability Centered Maintenance: Case Study
Tasks may include:
- Lubrication
- Cleaning
- Adjustments
- Parts replacement
Preventive maintenance can lower repair costs and improve safety. It works best for assets with predictable wear patterns. Companies often use software to track schedules and tasks.
Predictive Maintenance
Predictive maintenance uses data to forecast when equipment might fail. It relies on condition-monitoring tools and techniques. These may include:
- Vibration analysis
- Oil analysis
- Thermal imaging
- Ultrasonic testing
This strategy helps prevent unplanned downtime and reduce unnecessary maintenance. Predictive maintenance can save money by addressing issues before they become serious.
Companies can plan repairs at convenient times. This minimizes disruption to operations.
Proactive Maintenance
Proactive maintenance aims to prevent failures before they start. It focuses on finding and fixing the root causes of equipment problems. This strategy often involves:
- Design improvements
- Better operating procedures
- Enhanced training for operators
Proactive maintenance can extend equipment life by addressing underlying issues. It also helps reduce the frequency of breakdowns and repairs. This approach requires a deep understanding of how assets work and fail.
Proactive maintenance can lead to long-term cost savings. It also improves overall system reliability.
Reactive Maintenance
Reactive maintenance, also called run-to-failure, is a simple strategy. Equipment is fixed only when it breaks down. This approach can work for:
- Low-cost assets
- Non-critical equipment
- Items with unpredictable failure patterns
Illustration: WorkTrek / Data: Facilio
Reactive maintenance requires less planning. It can save money on unnecessary preventive tasks. But it can lead to:
- Higher repair costs
- Longer downtimes
- Unexpected failures
In some cases, RCM analysis may show reactive maintenance as the best choice for certain assets.
Condition-Based Maintenance
Condition-based maintenance relies on real-time monitoring of equipment. It uses sensors and data analysis to track asset health. Maintenance is performed when indicators show a decline in performance.
Illustration: WorkTrek / Data: ReliabilityAcademy
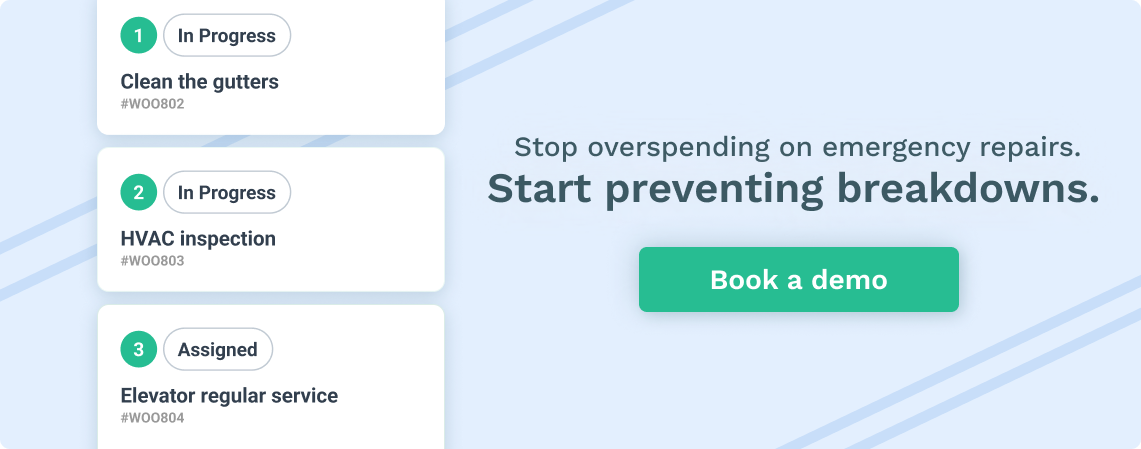
This strategy can include:
- Continuous monitoring systems
- Regular inspections
- Performance data analysis
Condition-based maintenance helps optimize maintenance timing. It can reduce unnecessary work and catch problems early. This approach works well for critical assets with variable usage patterns.
Run-to-Failure
Run-to-failure is a deliberate strategy for some equipment. It’s used when:
- Replacement is cheaper than maintenance
- Failure won’t cause safety issues
- Downtime won’t significantly impact operations
This approach can save money on maintenance costs. It works for low-cost items like light bulbs or specific electrical components. Run-to-failure requires having spare parts on hand for quick replacement.
It’s important to choose which assets to use this strategy carefully. RCM analysis helps identify where run-to-failure makes sense.
RCM Implementation and Planning
Implementing reliability-centered maintenance requires careful planning and ongoing efforts. The process involves several key steps to ensure success and maximize an organization’s benefits.
Maintenance Schedule Development
Creating effective maintenance schedules is crucial for RCM. These schedules outline when and how to perform maintenance tasks on critical assets. They should be based on equipment data, failure histories, and manufacturer recommendations.
Source: WorkTrek
Organizations need to prioritize tasks based on asset importance and failure risks. Schedules may include daily checks, monthly inspections, and yearly overhauls. The goal is to prevent breakdowns while avoiding unnecessary maintenance.
Digital tools can help track and optimize schedules. These systems alert technicians when tasks are due and log completed work. This data helps refine schedules over time for better results.
Criticality Analysis
Criticality analysis is a key part of RCM planning. It helps identify which assets are most important to operations. Teams assess each asset’s impact on safety, production, and costs if it fails.
High-criticality assets receive more attention and resources, while lower-priority items may have more straightforward maintenance plans. This focus ensures efforts go where they’re most needed.
Illustration: WorkTrek / Quote: RealiablePlant
The analysis often uses a scoring system. Factors like failure frequency, downtime costs, and safety risks are considered. The results guide maintenance strategies and resource allocation.
Regular reviews keep the analysis current as business needs change.
Cost-effectiveness and ROI
RCM aims to balance maintenance costs with equipment reliability. It seeks to find the sweet spot between too little and too much maintenance.
To measure cost-effectiveness, teams track metrics like:
- Maintenance costs per asset
- Downtime reduction
- Energy efficiency improvements
- Extended equipment life
These factors help calculate the return on investment (ROI) for RCM efforts. A successful program should show clear financial benefits over time.
It’s important to consider both short-term costs and long-term savings. While the initial RCM setup may be expensive, it often leads to significant savings later.
Aligning RCM with Business Goals
To be truly effective, RCM must support overall business objectives. This means linking maintenance strategies to key performance indicators (KPIs).
For example, if a company aims to increase production, RCM efforts should focus on boosting equipment uptime. If safety is a top priority, maintenance plans should emphasize risk reduction.
Regular meetings between maintenance teams and business leaders help ensure alignment. This keeps RCM efforts focused on what matters most to the organization.
Performance standards should be set to reflect these business goals. These standards guide maintenance decisions and help measure success.
Continuous Improvement and Feedback
RCM is not a one-time effort. It requires ongoing refinement to stay effective, and this process relies on constant feedback and data analysis.
Teams should regularly review:
- Equipment performance data
- Maintenance task effectiveness
- New technologies or methods
- Changes in business needs
This information helps identify areas for improvement. It may lead to updates in maintenance schedules, task procedures, or even equipment designs.
Employee feedback is also valuable. Technicians often have insights into better ways to maintain equipment, and it’s important to create channels for sharing this knowledge.
Regular training keeps staff up-to-date on best practices and new techniques. This supports the continuous improvement cycle.
Reliability and Performance
Reliability-centered maintenance focuses on keeping equipment running smoothly and safely. It uses data to make smart choices about upkeep and repairs.
Equipment Reliability and Uptime
Reliability-centered maintenance (RCM) aims to boost equipment reliability and uptime. It examines each machine or tool and determines the best way to keep it working well.
RCM uses a mix of different maintenance types. These include fixing things when they break, checking equipment on a set schedule, and watching for signs of wear.
Illustration: WorkTrek / Data: Pruftechnick
The goal is to stop problems before they happen. This helps avoid surprise breakdowns that can reduce work or cause safety issues.
RCM helps companies make products more consistently by keeping machines in good shape. It also saves money by reducing repairs and lost work time.
Measuring Effectiveness and KPIs
Companies need to track the right things to determine whether RCM is working. These are called key performance indicators (KPIs).
Some important KPIs for RCM include:
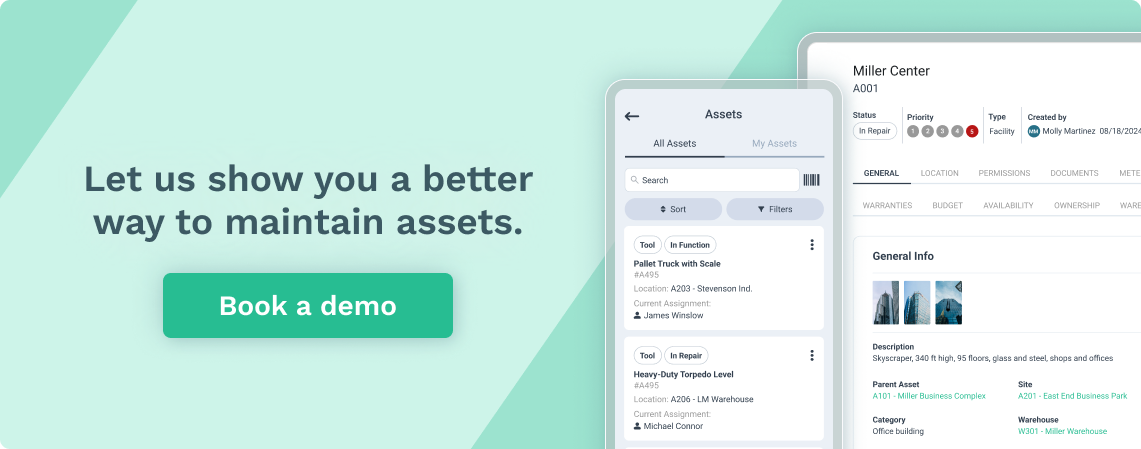
- Equipment uptime percentage
- Mean time between failures
- Repair costs
- Production output
Companies can use these numbers to spot trends and make better choices. They can see which machines need more attention and which maintenance tasks work best.
By watching these KPIs, managers can fine-tune their maintenance plans. This helps them get the most out of their equipment while keeping costs down.
Impact on Safety and Risk Management
RCM plays a big role in keeping workers safe and managing risks. Keeping equipment in good shape helps prevent accidents and failures that could hurt people.
Illustration: WorkTrek / Data: 360training
RCM considers the possible ways each piece of equipment could fail. It then plans how to prevent these failures or deal with them safely if they do happen.
This careful planning helps companies:
- Spot safety risks before they cause problems
- Create better training for workers
- Make smarter choices about when to replace old equipment
RCM also helps companies meet safety rules and standards. By showing that they take care of their equipment, companies can avoid fines and legal issues.
Analytical Techniques in RCM
RCM uses several methods to analyze and prevent equipment failures. These techniques help identify potential issues and determine the best maintenance strategies.
Failure Modes and Effects Analysis (FMEA)
FMEA is a core technique in RCM. It examines how equipment might fail and what effects those failures could have.
Illustration: WorkTrek / Data: Reliability Centered Maintenance – Implementation and Benefits
The process involves:
- Listing potential failure modes
- Identifying the causes of each failure
- Evaluating the effects of failures
- Ranking the severity of effects
FMEA helps prioritize maintenance tasks. It focuses on critical failures impacting safety, operations, or costs.
Teams use FMEA to create detailed failure scenarios. This allows them to develop targeted prevention strategies.
Condition Monitoring
Condition monitoring tracks equipment health in real time. It uses sensors and data analysis to detect early signs of problems.
Common monitoring methods include:
- Vibration analysis
- Oil analysis
- Thermography
- Ultrasonic testing
Illustration: WorkTrek / Source: Icon
These techniques can spot issues before they cause functional failures. This allows for timely repairs and prevents unexpected breakdowns.
Condition monitoring supports predictive maintenance. It helps schedule repairs based on actual equipment conditions rather than fixed time intervals.
Failure Finding and Detective Maintenance
Failure-finding tasks check for hidden problems in standby equipment. Since these items don’t run constantly, failures may go unnoticed.
Examples include:
- Testing backup generators
- Checking emergency systems
- Inspecting fire suppression equipment
Detective maintenance aims to find and fix issues before they’re needed in an emergency. It’s crucial for safety-critical systems.
Regular checks ensure standby equipment will work when required. This improves overall system reliability.
Time-Based Maintenance
Time-based maintenance involves regular, scheduled tasks. It’s used when wear is predictable or when regulations require fixed intervals.
Examples include:
- Oil changes every 5,000 miles
- Annual safety inspections
- Monthly lubrication of bearings
This approach works well for simple, non-critical components. It’s less effective for complex systems with multiple failure modes.
Time-based tasks are often combined with other RCM techniques to create a comprehensive maintenance strategy tailored to each asset’s needs.
Summary
In summary, Reliability-Centered Maintenance (RCM) is a powerful tool to get the most out of your equipment.
Based on a deep understanding of how each asset works and what causes it to fail, RCM enables you to make data-driven decisions that extend equipment life and safety. RCM improves operational efficiency and aligns with your business goals for long-term success when implemented correctly.
Whether in aviation, manufacturing, or energy, RCM is a must-have tool for companies that want to optimize their maintenance and continuous improvement.