Get a Free WorkTrek Demo
Let's show you how WorkTrek can help you optimize your maintenance operation.
Try for freeIntroduction
As companies become larger and more complex, managers feel pressure to keep up with trends and demands. So they try to act smarter and smarter. This means companies seek to achieve a high return on investment by improving operations through better time management, cost reduction, labor management and extending equipment life. Companies are gradually realizing that paper-and-pencil management cannot achieve their goals.
Many companies start adopting management solutions after developing computer-based management applications. A CMMS can monitor and track inventory, create work orders with accurate reporting, and most importantly, perform preventive maintenance on needed assets.
A preventive maintenance approach includes regular equipment inspections, an important aspect of a service plan. Companies prefer to use it instead of reactive methods. A reactive approach will only solve problems when they arise. This can lead to unplanned downtime and equipment failure.
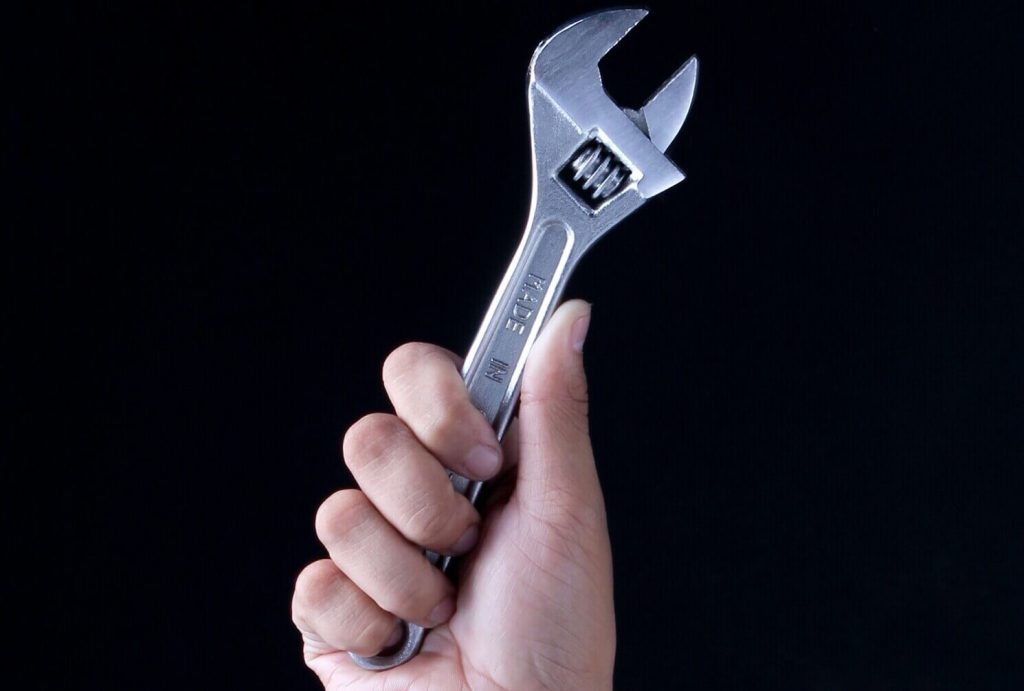
History of CMMS and Traditional Maintenance
Traditional maintenance practices have been used for centuries, relying on reactive and corrective maintenance methods where repairs are initiated in response to equipment failures or breakdowns.
Traditional maintenance involves ad-hoc repairs, routine inspections, and manual record-keeping, with limited emphasis on preventive or predictive maintenance strategies.
The emergence of computer technology in the late 20th century led to the development of CMMS, which revolutionized maintenance management by automating tasks, optimizing processes, and providing real-time visibility into maintenance activities.
CMMS originated in the 1960s and 1970s with the advent of early computer systems and mainframe-based maintenance management software.
Over time, CMMS evolved to incorporate advanced features such as preventive maintenance scheduling, asset management, inventory optimization, and data analytics, enabling organizations to adopt more proactive and efficient maintenance practices.
Today, CMMS has become an essential tool for organizations across various industries, helping them streamline maintenance operations, optimize asset performance, and improve overall operational efficiency.
While traditional maintenance practices are still prevalent in some industries, many organizations are transitioning to CMMS and other modern maintenance management systems to achieve greater reliability, efficiency, and competitiveness in their maintenance operations.
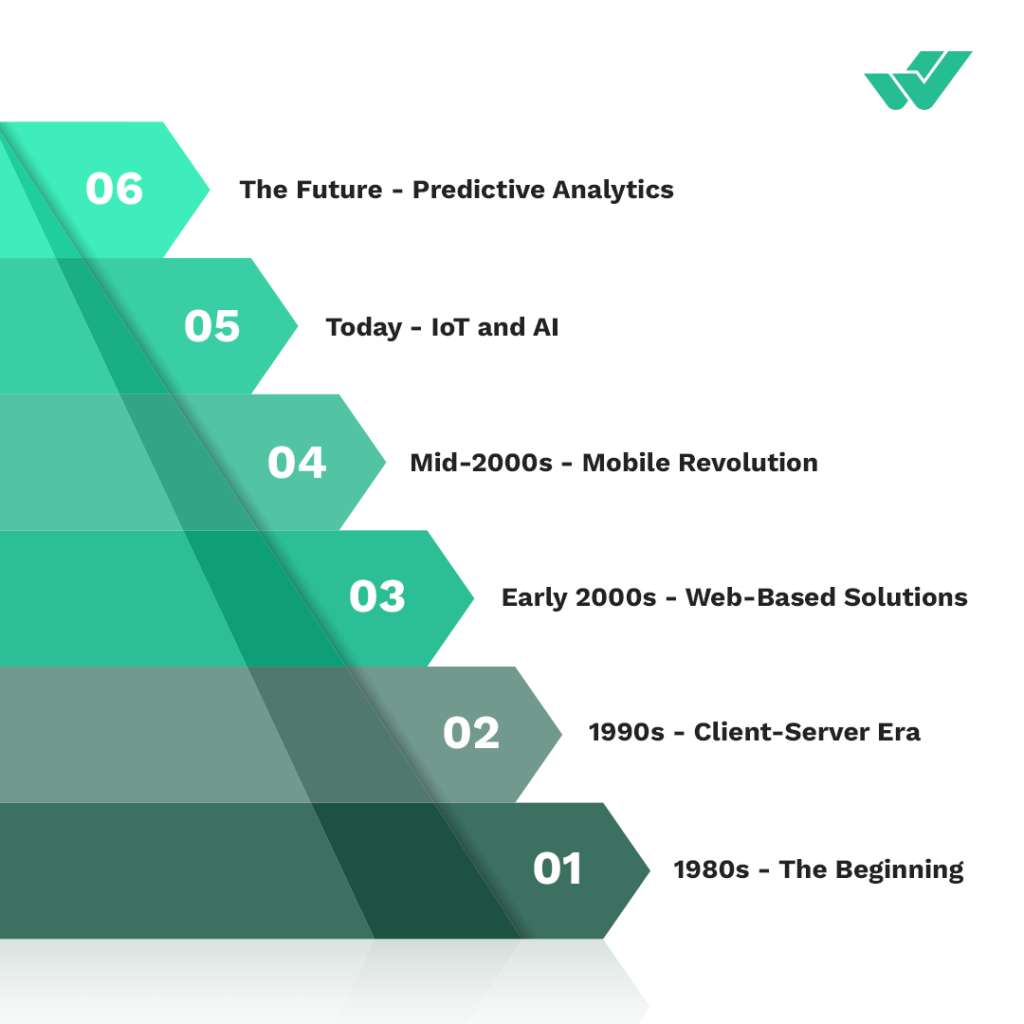
What Does CMMS Software Do and How Does it Work?
The CMMS is a software capable of containing all the maintenance information: from the technical database to the asset sheets, through maintenance plans, requests for technical intervention and work orders. It also allows you to manage all the documentation, the history of interventions and work reports, the spare parts in the warehouse, as well as of course the technicians and suppliers.
Thanks to all this information, it is able not only to help you optimize maintenance processes, but also to provide all the data necessary for a detailed analysis of them, monitoring times, costs and performance thanks to business intelligence systems that analyze the data for you, creating personalized and incredibly detailed reports.
The best CMMS software is also able to automate a large part of these processes, for example by automatically creating work orders or assigning them, always automatically, to the right personnel, based on the indications you have given to the system.
Let’s say for example that you need to plan preventive maintenance interventions based on the working time of a machine. The CMMS is able to generate a new work order every time this time is reached, inform you if spare parts are available in stock, attach the necessary documents and maintenance checklists to ensure that the interventions are carried out in the correct way and finally assign them to the personnel indicated on the basis of the machinery or its location.
This allows you to drastically reduce the costs and management times of your resources, as well as naturally machine downtime, also reducing manual actions and margins of error.
One of the most important features of modern CMMS systems is the ability to use the mobile app.
Thanks to the mobile app, technicians can take the CMMS for company maintenance with them wherever they go in the field. They will be notified via a simple notification (or an email) when they are assigned a work order, they will be able to consult the documentation, record the intervention times, take advantage of the checklists attached to the work order and add the pieces in just a few taps spare parts used on the final report.
This will allow them not only to cut intervention times, but also to automatically record all data and information relating to the work order within the CMMS system. Once the intervention is completed, they will be able to automatically generate the end of work report, create it directly on their phone and send it to the system (as well as by email to the figures involved).
At this point the CMMS system records the data and sorts them within the platform, where they will be available in real time.
Likewise, the maintenance manager will have a complete view of the progress of maintenance operations, will be able to easily monitor, without any additional action, the work orders carried out and those still to be carried out, as well as analyze the recorded data in real time.
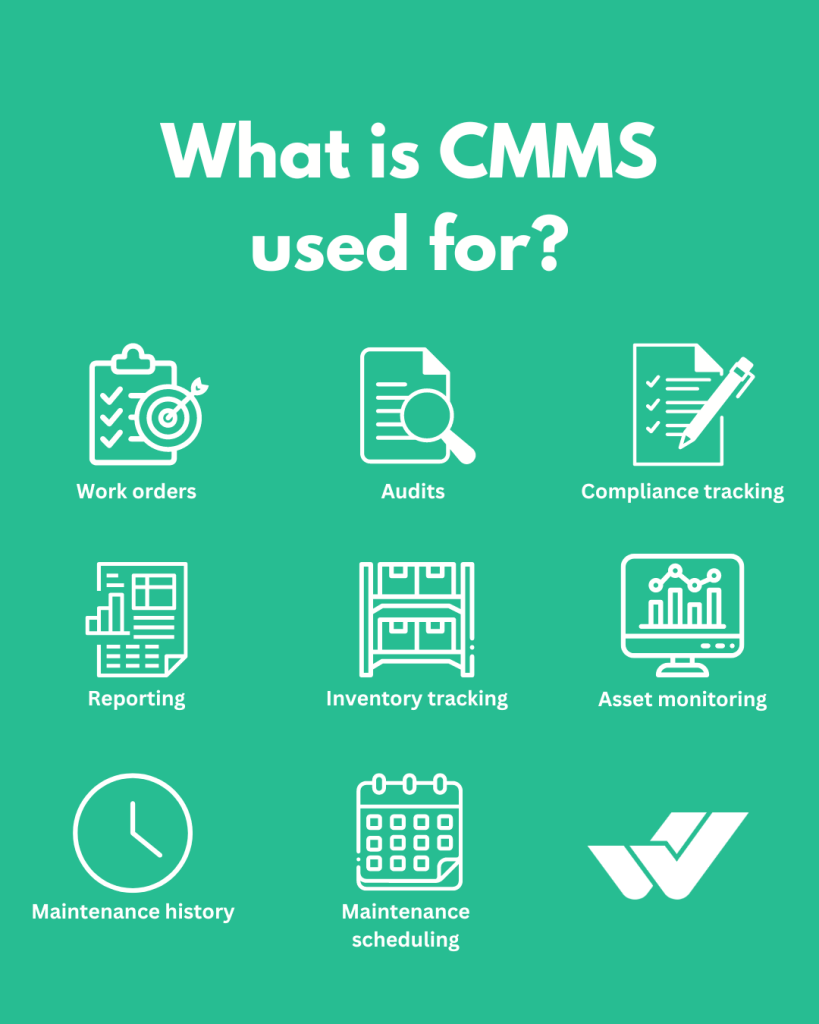
Advantages of CMMS
Implementing a computerized maintenance management system (CMMS) offers numerous benefits to companies across a variety of industries. Key benefits of a CMMS include:
Improve Maintenance Efficiency: CMMS streamlines the maintenance process by automating tasks such as work order creation, scheduling, and tracking. This increases the efficiency of managing maintenance activities, reduces administrative burden and minimizes downtime.
Improved Asset Management: A CMMS provides a centralized platform to track and manage assets, including equipment, machinery, and facilities. Companies can easily access asset information, maintenance history and performance data to optimize asset lifecycle management, improve reliability and extend asset life.
Optimize Preventive Maintenance: With a CMMS, companies can implement preventive maintenance programs based on equipment health, performance data, and manufacturer recommendations. Proactively planning maintenance tasks can help prevent equipment failure, reduce downtime and reduce maintenance costs.
Inventory Optimization: CMMS enables better management of spare parts, consumables, and inventory by tracking inventory levels, managing reorder points, and optimizing procurement processes. This ensures adequate inventory levels, reduces stock-outs and minimizes storage costs.
Data-Driven Decisions: CMMS provides valuable insights into maintenance performance, asset reliability and resource utilization through reporting and analytical tools. Companies can analyze maintenance data, identify trends and make informed decisions to optimize maintenance strategies, increase efficiency and reduce costs.
Improved Compliance and Documentation: A CMMS helps companies maintain compliance with regulatory standards and documentation requirements by storing maintenance records, inspection reports, and compliance documents in a centralized and easily accessible system. This ensures compliance with safety regulations, industry standards and audit requirements.
Reduce Downtime and Costs: By proactively managing maintenance activities, implementing preventive maintenance plans, and optimizing resource allocation, a CMMS helps reduce equipment downtime, minimize emergency repairs, and lower maintenance costs. This will lead to greater productivity, operational efficiency and profitability.
Improved Communication and Collaboration: CMMS facilitates communication and collaboration between maintenance teams, supervisors, and other stakeholders through instant messaging, notifications, and alerts. This improves coordination, teamwork and accountability, leading to better results and performance.
Overall, a CMMS provides businesses with a variety of benefits, including increased maintenance efficiency, improved asset management, preventive maintenance optimization, inventory optimization, data-driven decision-making, compliance and document management, reduced downtime and costs, and improved communication and cooperation. By effectively leveraging CMMS capabilities, companies can achieve greater operational excellence, reliability, and competitiveness in their industry.
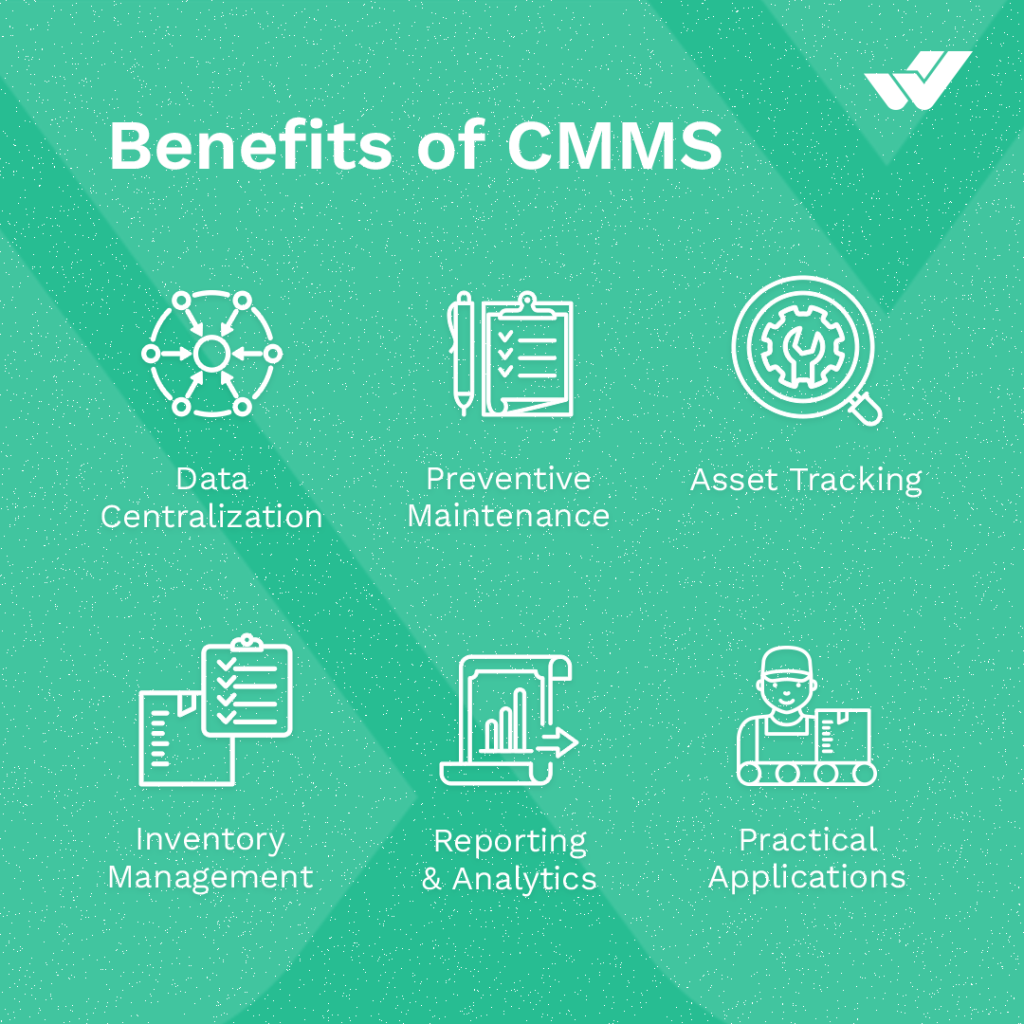
What is Traditional Maintenance?
Traditional maintenance is the traditional approach to managing maintenance activities within an organization, often characterized by reactive and corrective maintenance practices. In traditional maintenance, maintenance activities are performed in response to equipment malfunction rather than being planned or scheduled in advance.
Key features of traditional maintenance include:
Reactive Maintenance: Maintenance tasks are initiated in response to equipment failure, often resulting in unplanned downtime and production interruptions.
Fault Repair: Equipment is repaired or replaced only when it breaks down, resulting in higher repair costs, increased downtime and potential safety hazards.
Routine Inspections and Repairs: Maintenance activities such as inspections and repairs are performed on an ad hoc basis or according to a fixed schedule rather than based on equipment condition or performance data.
Limited Predictive Capabilities: The use of data and technology to predict equipment failures or maintenance needs is limited. Maintenance decisions are often based on historical experience or intuition rather than data-driven insights.
High Maintenance Costs: Reactive maintenance practices can result in higher overall maintenance costs due to emergency repairs, extended downtime, and inefficient resource utilization.
Reduced Equipment Reliability: Equipment reliability can suffer due to a lack of proactive maintenance measures to prevent failures and optimize asset performance.
Overall, compared with modern maintenance strategies such as preventive maintenance, predictive maintenance and reliability-oriented maintenance, traditional maintenance methods are often less efficient, more costly and less effective in ensuring equipment reliability and operating efficiency. Many companies are moving from traditional maintenance practices to more proactive, data-driven maintenance strategies to improve asset performance, reduce downtime and optimize maintenance costs.
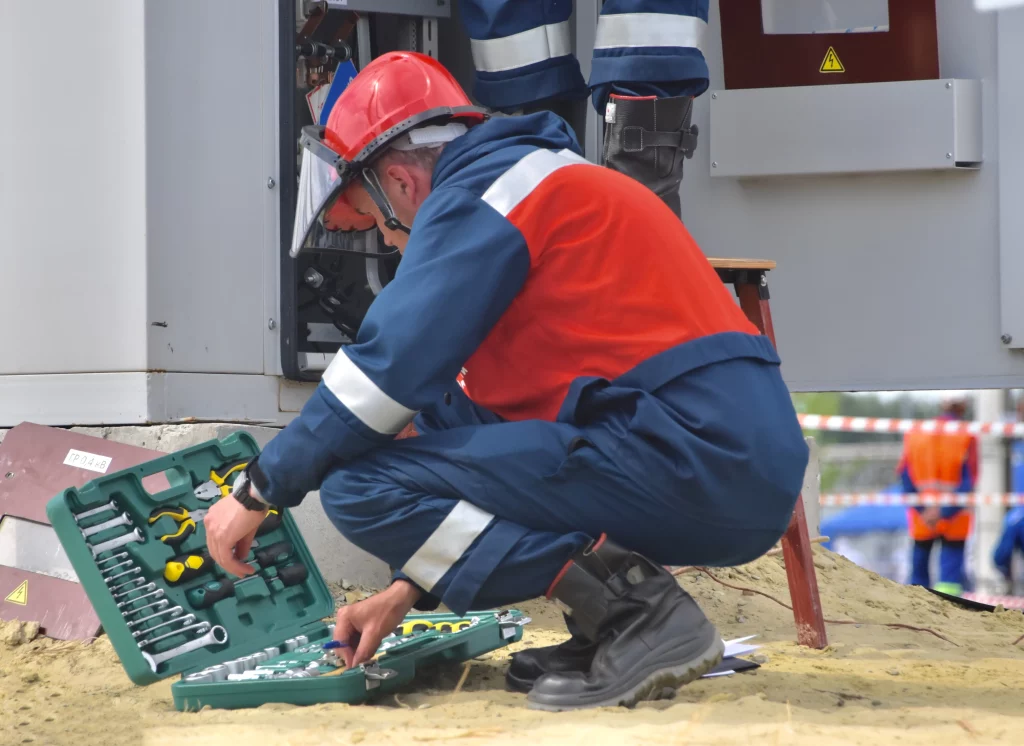
Disadvantages of Traditional Maintenance
Disadvantages of traditional maintenance include:
Higher Costs: Reactive maintenance practices often result in higher overall maintenance costs due to increased labor costs associated with emergency repairs, expedited shipping of replacement parts, and unplanned downtime.
Increased Downtime: Reactive maintenance can lead to increased equipment downtime because repairs are not initiated until an equipment failure occurs. This can disrupt production plans, reduce productivity and impact profitability.
Safety Risks: Failures caused by equipment failure and reactive maintenance operations can create safety risks for employees and lead to possible injuries, accidents and regulatory compliance issues.
Reduced Equipment Reliability: Reactive maintenance fails to address the underlying issue or root cause of equipment failure, resulting in recurring failures and reduced equipment reliability over time.
Unplanned Production Downtime: Equipment malfunctions and malfunctions can lead to unplanned production downtime, resulting in delayed order fulfillment, customer dissatisfaction and potential loss of business.
Limited Predictive Capabilities: Reactive maintenance practices cannot predict equipment failure or predict maintenance needs based on data-driven insights. This can result in missed opportunities to proactively address maintenance issues before they escalate.
Shortened Equipment Life: A lack of proactive maintenance measures can lead to premature equipment failure and shortened equipment life, requiring more frequent replacements and higher capital expenditures.
Poor Asset Management: Reactive maintenance practices often result in inadequate tracking and recording of maintenance activities, making it difficult to assess asset performance, identify trends and optimize maintenance strategies.
Overall, the shortcomings of traditional maintenance highlight the need for organizations to move to more proactive, data-driven maintenance approaches such as preventive maintenance, predictive maintenance and reliability-centered maintenance to increase equipment reliability, reduce downtime and optimize maintenance costs.
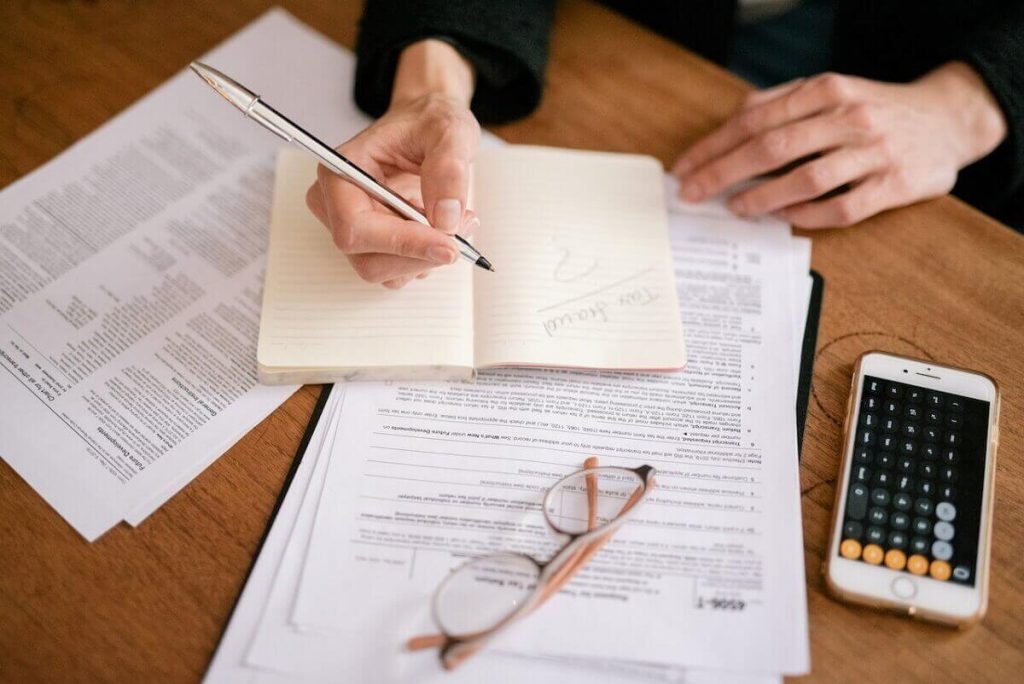
Are there Benefits to Traditional Maintenance?
While traditional maintenance practices have several disadvantages, this approach also has some potential benefits:
Simplicity: Traditional maintenance practices are often easier to implement and manage than more proactive maintenance strategies. They require less upfront investment in technology, training and infrastructure, so they can also be used by smaller organizations with limited resources.
Flexibility: Traditional maintenance practices allow companies to respond quickly to equipment malfunctions and breakdowns and resolve maintenance needs as they arise. This flexibility is useful in situations where equipment failure is rare or unpredictable.
Minimal Planning Required: Traditional maintenance requires less detailed planning and scheduling of maintenance activities in advance. Maintenance tasks can be performed on an ad hoc basis or according to a set schedule without extensive planning or preparation.
Avoid Over-Maintenance: Traditional maintenance practices only repair equipment when it breaks down, which avoids unnecessary maintenance intervention and over-maintenance. This allows companies to avoid spending resources on potentially unnecessary maintenance activities.
Lower Upfront Costs: Reactive maintenance practices typically have lower upfront costs than more proactive maintenance strategies because they do not require investments in predictive maintenance technology, condition monitoring systems, or extensive preventive maintenance programs.
Familiarity: Traditional maintenance practices may be more familiar to maintenance technicians and personnel because they are consistent with traditional maintenance management methods. This familiarity can make it easier for companies to gradually transition to a more proactive maintenance strategy.
While these benefits may apply in some situations, organizations must recognize the limitations of traditional maintenance practices and consider the long-term impact on equipment reliability, downtime, and overall operational efficiency. In many cases, moving to a more proactive and data-driven approach to maintenance ultimately results in greater cost savings, improved asset performance and increased long-term competitiveness.
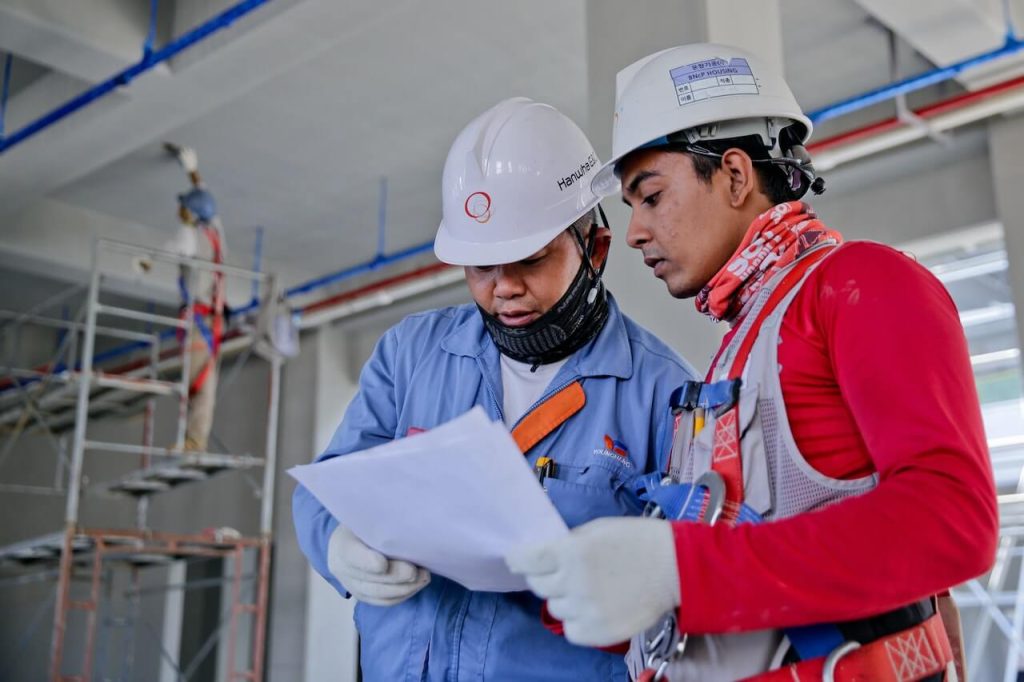
CMMS vs Traditional Maintenance
Comparing a CMMS softwares to traditional maintenance practices reveals significant differences in approach, benefits and results. Here’s how a CMMS compares to traditional maintenance:
Approach to Maintenance
· CMMS: CMMS emphasizes proactive maintenance strategies such as preventive maintenance and predictive maintenance. The focus is on planning and scheduling maintenance tasks ahead of time based on equipment health, performance data and industry best practices.
· Traditional Maintenance: Traditional maintenance practices are reactive and corrective in nature, with maintenance activities initiated in response to equipment failure. Maintenance is often ad hoc or performed on a set schedule without regard to the health or performance data of the equipment.
Maintenance Efficiency
· CMMS: A CMMS optimizes maintenance processes, automates tasks, and provides real-time visibility into maintenance activities. It improves maintenance efficiency by optimizing resource utilization, reducing downtime and increasing productivity.
· Traditional Maintenance: Traditional maintenance practices can be less efficient, resulting in increased downtime, higher repair costs and greater reliance on manual processes. Maintenance activities are often reactive and may not be optimized for efficiency.
Asset Management
· CMMS: A CMMS provides a centralized platform for tracking and managing assets, including plants, machinery, and equipment. It enables companies to maintain comprehensive asset records, track maintenance history and optimize asset lifecycle management.
· Traditional Maintenance: Traditional maintenance practices may lack robust asset management capabilities, making it difficult to track assets, monitor maintenance activities, and optimize asset performance.
Preventive maintenance
· CMMS: A CMMS helps implement preventive maintenance programs based on equipment health, performance data, and maintenance schedules. It helps prevent equipment failure, extend asset life and reduce downtime.
· Traditional maintenance: Traditional maintenance practices may rely more on reactive maintenance, resulting in more unplanned downtime, higher repair costs, and reduced equipment reliability.
Data-driven decisions
· CMMS: A CMMS provides valuable insights into maintenance performance, asset reliability and resource utilization through reporting and analysis tools. It supports data-driven decision making, allowing companies to optimize maintenance strategies and improve operational efficiency.
· Traditional Maintenance: Traditional maintenance practices may lack the data and analytics capabilities of a CMMS, making it difficult to analyze maintenance performance, identify trends, and make informed decisions.
Conclusion
While traditional maintenance practices may have been sufficient in the past, a CMMS overall offers numerous advantages in proactive maintenance, efficiency, asset management, preventive maintenance, data-driven decision making, and overall operational excellence. By switching to a CMMS, companies can achieve greater reliability, efficiency and competitiveness in their maintenance operations.