Get a Free WorkTrek Demo
Let's show you how WorkTrek can help you optimize your maintenance operation.
Try for freeIn today’s fast-paced and highly competitive business environment, organizations are constantly pressured to streamline operations, reduce downtime, and improve overall efficiency. One area that often goes overlooked yet plays a crucial role in achieving these goals is the management of maintenance activities.
Computerized Maintenance Management System (CMMS) software can help optimize workflow processes within your organization. By providing a centralized platform for tracking, scheduling, and managing maintenance tasks, CMMS helps ensure that equipment operates efficiently, reducing costly downtime. It also enables better resource allocation, facilitates compliance with industry regulations, and provides valuable data insights for proactive decision-making.
Implementing CMMS software enhances maintenance efficiency and drives long-term operational success, making it a vital tool for organizations aiming to stay competitive in a technology-driven landscape.
Source: WorkTrek
Understanding Maintenance Workflow
Streamlining maintenance operations requires implementing standardized maintenance workflows. By doing so, organizations can achieve a level of uniformity that enhances quality and efficiency in all maintenance activities, reducing variability and errors while promoting a culture of continuous improvement.
Workflow standardization is pivotal to cost-saving initiatives within the realm of maintenance management.
Through consistent and predefined processes, organizations can:
- Cut down on ineffective trial-and-error approaches, which often escalate operational expenses
- Follow set procedures
- Execute tasks with increased proficiency
- Boost overall efficacy in both maintenance outcomes and product integrity
- Improve equipment performance and asset management
Instituting electronic methods for managing these processes is vital. CMMS automates various aspects of routine upkeep, ensuring each task follows an established protocol. This results in fewer mistakes and heightened productivity among teams responsible for facility care.
Implementing such systems enhances transparency and accountability throughout ongoing maintenance activities. CMMS software offers clear documentation that supports defined roles at each stage, reducing misunderstandings and preventing neglectful oversights among teams responsible for repairs or improvements.
Illustration: WorkTrek / Quote: PWE
7 Key Benefits of Using CMMS for Maintenance Workflow Optimization
CMMS software is designed to help organizations manage their maintenance operations more efficiently. To achieve this goal, effective CMMS software should have the following key features:
1. Asset Management
Effective CMMS software should comprehensively view an organization’s assets, maintenance history, and associated documentation. This feature allows maintenance teams to track equipment performance, identify potential issues, and schedule preventative maintenance tasks to minimize downtime.
Source: WorkTrek
2. Work Order Management
Work order management is a critical feature of CMMS software. It allows maintenance teams to create and track work orders, assign tasks to specific team members, and monitor progress in real-time. This feature helps organizations prioritize maintenance tasks, ensure timely completion, and reduce the risk of equipment failure.
Source: WorkTrek
3. Preventative Maintenance Scheduling
Preventative maintenance scheduling is a crucial feature of CMMS software that helps organizations minimize downtime and reduce maintenance costs. This feature allows maintenance teams to schedule routine maintenance tasks, such as inspections and servicing, based on the equipment’s usage, age, and performance history.
Source: WorkTrek
4. Inventory Management
Inventory management is an essential feature of CMMS software that helps organizations manage their spare parts and supplies more efficiently. This feature allows maintenance teams to track inventory levels, reorder supplies when necessary, and avoid stockouts that can lead to equipment downtime.
Source: WorkTrek
5. Reporting and Analytics
Reporting and analytics are critical features of CMMS software that help organizations track maintenance performance, identify trends, and make data-driven decisions. This feature allows maintenance teams to generate reports on work orders, asset performance, inventory levels, and other key metrics to optimize maintenance operations.
Overall, effective CMMS software should provide organizations with the tools to manage their maintenance operations more efficiently, reduce downtime, and increase equipment reliability. Organizations can optimize their maintenance workflow and improve their bottom line by incorporating these key features into their CMMS software.
Source: WorkTrek
6. Reduce Machine Downtime
A primary benefit of deploying CMMS is its ability to significantly reduce machinery downtime. The system ensures continuous operational capability by concentrating on urgent repairs and conducting systematic inspections, reducing production delays.
CMMS software can lead to reduced maintenance costs, minimize equipment downtime, and prioritize maintenance tasks based on specific company requirements.
Source: WorkTrek
7. Manage Resources
CMMS proves invaluable for effectively managing resources. It optimizes how organizations allocate manpower and materials during repair operations, ensuring that qualified staff and necessary supplies are available at critical moments.
Adopting a strategy centered on actionable insights derived from historical data is crucial for maintaining competitiveness and achieving goals related to managing an organization’s mechanical responsibilities.
Source: WorkTrek
Improve Efficiency By Using CMMS
The introduction of CMMS software into maintenance management significantly improves the efficiency of maintenance operations by offering benefits such as:
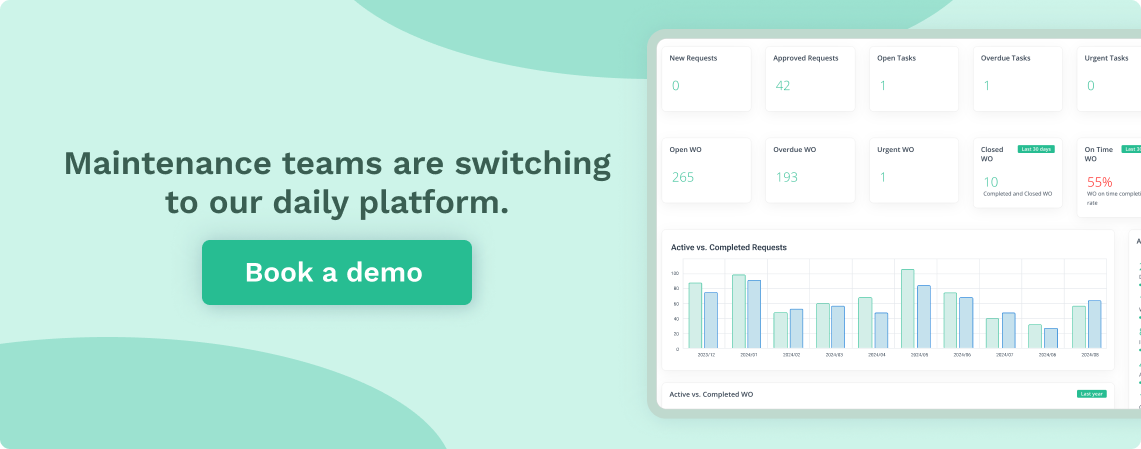
- Streamlining and automating routine maintenance workflows
- Adopting a proactive stance towards upkeep activities with preventive maintenance
- Optimize Maintenance Workflow
- Prompt execution with increased effectiveness in regular tasks
- Minimization of human errors
- Prioritizing critical jobs, ensuring essential tasks are addressed first
- Elevating the overall standard of maintenance output
- Enable maintenance managers to make data-driven decisions
- Quick access to maintenance history
Source: WorkTrek
Automating Work Order Management with CMMS
Implementing work order management through a CMMS, which streamlines maintenance tasks from start to finish, significantly enhances maintenance operations.
Automating the initiation, tracking, and completion process for work orders simplifies handling these tasks. Maintenance requesters can quickly submit their requests via digital forms.
Maintenance tasks
Automating maintenance tasks using a CMSS improves efficiency among maintenance technicians by enabling them to finalize work orders directly on-site with mobile devices.
This reduces time spent handling paperwork and allows technicians to direct their efforts toward completing maintenance tasks.
CMMS promotes better communication and accountability among maintenance team members, helping companies complete maintenance tasks faster.
Source: WorkTrek
Scheduling Preventive Maintenance Activities
Preventive maintenance should be the cornerstone of any organization. Creating effective preventive maintenance schedules (PM Schedules) can help reduce reactive maintenance cases and keep equipment running in top condition.
Having maintenance technicians address potential issues before they become significant problems can reduce overall maintenance costs.
Paired with a CMMS system, organizations can easily create and schedule PM Schedules and Task Lists and track them using Key performance indicators.
Additionally, creating detailed work orders through the CMMS system can guide technicians through each process step, including health and safety guides and equipment manuals.
Source: WorkTrek
Real-Time Asset Tracking and Inventory Management
CMMS provides organizations with indispensable tools for tracking assets in real time. Pairing equipment with RFID, QR Codes, IoT devices, and various GPS technologies can enhance overall equipment tracking:
- Accurately monitor where assets are located and their current state
- Track movement history assets
- Evaluate equipment utilization
- Get notified and detect early signs of equipment failures
- Track Key Performance Indicators
- Give the maintenance team visibility to all equipment
- Improve equipment performance
Source: WorkTrek
Equipment Transparency
As you can see, using the above tools provides several benefits, including better visibility for all equipment.
This level of transparency empowers maintenance teams to oversee asset health and properly prevent costly operational interruptions.
Pairing this with a CMMS mobile application that detects and reads these sensors can automate this approach and improve equipment visibility.
Asset and Inventory Management
One of the challenges many organizations face is inventory and spare parts management.
Maintaining stockpile levels and setting up automatic replenishment alerts ensures that essential repair parts are always on hand.
This effective supply chain management helps minimize unnecessary urgent orders or surplus inventory costs while enhancing resource allocation efficiency.
Organizations can automate this process using real-time asset management and reduce surprises during maintenance tasks.
Source: WorkTrek
Improving Communication and Collaboration
Like any organization, maintenance teams can benefit from improved communication and teamwork. CMMS can be the hub that facilitates this interaction between maintenance teams.
It can become the central hub that all parties can use to communicate status and state of work.
By centralizing all tasks, CMMS helps maintain clear responsibilities and alignment between stakeholders through task management, status updates, and information sharing.
Mobile Apps
Integrating mobile technology into CMMS enhances its utility by enabling real-time interaction capabilities.
This allows maintenance technicians to conveniently manage work orders on the go using their smartphones or tablets to approve activities, update statuses, and easily track workflows.
All of this can lead to increasing productivity levels while reducing unnecessary delays.
Centralized Document Management
CMMS can put all vital documents at your fingertips, such as equipment guidelines or health and safety instructions.
This allows maintenance technicians to access the critical information needed to complete their tasks quickly and, more importantly, correctly.
This reduces the time spent searching for documents, minimizes errors, and ensures tasks are completed correctly and efficiently.
Additionally, having up-to-date and easily accessible documentation fosters better compliance with safety and regulatory standards and streamlines training processes for new technicians.
Effective document management in CMMS improves productivity, heightened accuracy, and a more organized approach to maintenance workflows.
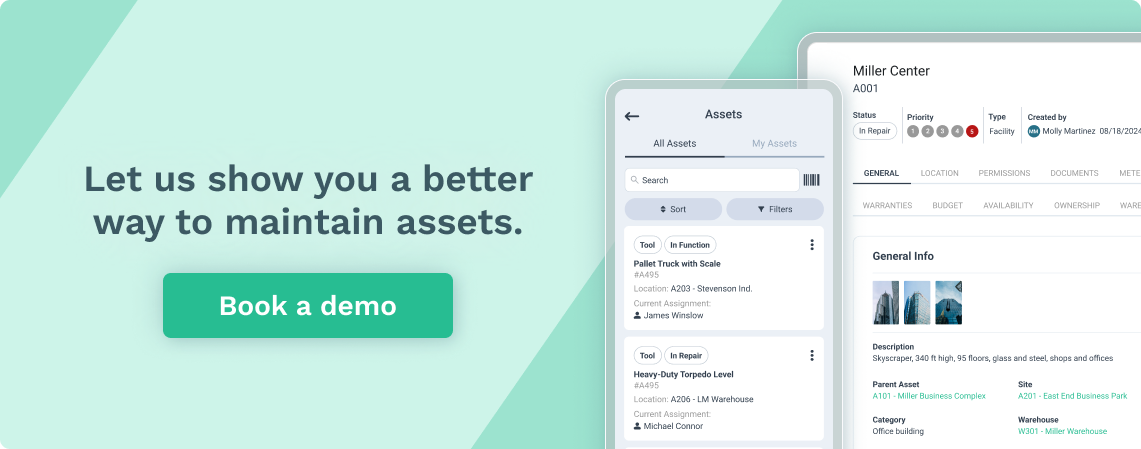
Source: WorkTrek
Leveraging Data Analytics for Continuous Improvement
Leveraging data and analytics should be the cornerstone of any successful maintenance organization. Reporting and analytics tools embedded within CMMS systems can be the foundation for this approach.
CMMS can track everything from maintenance histories to consumption trends and parts management. This data can be analyzed using the built-in reporting and analytics tools for a CMMS system to understand patterns used through a reporting and analytics system to evaluate
Organizations can use a variety of native reporting and analytics tools provided by the CMMS software or third-party tools such as Microsoft Fabric or Tableau. However, to enable those tools to work, you must ensure that the CMMS software you choose offers an Open API feature.
Data to the Rescue
Organizations can gather crucial insights that shape future maintenance strategies through CMMS by analyzing breakdown histories and parts consumption trends.
This data-driven approach empowers entities to:
- Detect recurring patterns and evolve their maintenance processes
- Refine their existing workflows
- Strengthen overall efficiency during operations
- Extract exhaustive reports for KPI evaluation
- Advance initiatives aimed at perpetual refinement
- Achieve new heights in terms lockstep with operational excellence
Predictive Maintenance
CMMS enables predictive maintenance strategies by analyzing historical maintenance records and equipment performance data.
These proactive measures allow companies to anticipate and address potential issues before they escalate, reducing downtime and repair costs.
Organizations can develop and fine-tune their predictive maintenance approach using data-driven decisions derived from repair history.
Simplify Regulatory Compliance
Most maintenance organizations must adhere to regulatory standards, such as safety management.
A CMMS assists organizations in fulfilling these objectives by consolidating asset information, streamlining the reporting process, and creating audit trails.
Documenting maintenance tasks stored in a CMMS is crucial for complying with regulations and protecting workers’ well-being.
A CMMS automates reports and audit logs, simplifying internal and external auditing and improving transparency and accountability in maintenance procedures. This software ensures that all equipment meets established safety standards by managing regulatory requirements and scheduling essential corrective actions.
This proactive approach to safety management significantly reduces accident risks, promoting a positive workplace safety culture.
CMMS can improve the overall safety posture with features such as:
- Procedures like Lockout/Tagout, which help prevent unintentional activations or hazardous releases during servicing
- Regular inspections are conducted using uniform checklists aimed at the early identification and rectification of possible risks
- Creation as maintaining safe conditions conducive for those engaged in facility upkeep
Recording incidents related to workplace safety concerns or near-misses within a CMMS allows for the rapid development of strategies to improve existing preventive measures, ultimately enhancing overall operational safety.
Source: WorkTrek
Training and Supporting Maintenance Technicians
Extensive training and consistent support for the maintenance staff are essential to ensure a smooth adoption of CMMS and its efficient utilization.
Initiating comprehensive education on the new system early can significantly enhance its utility and facilitate an easier shift in operations.
Adopting these methods will help train your maintenance personnel effectively in using the new CMNS.
- Facilitate hands-on learning through interactive workshops.
- Offer virtual classes for convenience and adaptability to remote situations.
- Implement continuous educational sessions to solidify skills while addressing queries or issues.
- Customize training programs to meet your company’s specific requirements and those of your maintenance teams.
- Stress how crucial it is to integrate everyday tasks with CMMS functionality.
Vendors typically supply online materials that act as a refresher course, enabling maintenance crews to keep up-to-date regarding progressive enhancements. Incessant instruction alongside assistance underpins efficacy, user satisfaction, and unceasing refinement across all spheres of handling upkeep functions.
Source: WorkTrek
Best Practices for Successful CMMS Implementation
Careful and strategic planning is essential to successfully deploying a CMMS. Begin by evaluating your current maintenance management processes and identifying any inefficiencies to set clear SMART objectives for improvement.
Pinpointing key issues allows companies to select an appropriate CMMS tailored to their needs.
Following these measures can facilitate an efficient CMBS deployment.
- Evaluate the existing state of maintenance operations within your organization.
- Establish SMART targets informed by the primary difficulties identified.
- Select a modern CMMS solution that meets those particular needs.
- Allocate a feasible budget for necessary customization, integration, and sustained upkeep expenses.
Stagger the Rollout
Starting with a single department, where you can potentially gain the most benefit and demonstrate value, start rolling out the CMMS system.
This approach allows you to fine-tune the overall process, define the maintenance management strategy, and create your preventive maintenance program. It also helps you prioritize maintenance activities and optimize resource allocation with a smaller group that you can quickly iterate on and fix.
Source: WorkTrek
Summary
In summary, CMMS offers many benefits for optimizing maintenance workflows, from automating work order management to enhancing communication among maintenance teams.
By leveraging data analytics and ensuring regulatory compliance, CMMS empowers organizations to achieve operational excellence and continuous improvement in their maintenance operations.
Embracing CMMS technology and following best practices for successful implementation can transform maintenance management strategies, leading to more efficient workflows, reduced downtime, and improved asset performance.
Some keys to success lie in thorough training, continuous support, and a commitment to proactive maintenance.