Get a Free WorkTrek Demo
Let's show you how WorkTrek can help you optimize your maintenance operation.
Try for freeMaintenance best practices are the cornerstone for achieving peak operational performance. This article directly answers your pressing maintenance questions, laying out the tenets of preventive, predictive, and reactive care that will keep your operations running smoothly while cutting down on expenses and emergency fixes.
Effective maintenance strategies encompass preventive, predictive, and reactive maintenance, each critical for ensuring efficient operations, preventing asset failures, and optimizing lifecycle costs. Additionally, integrating CMMS software for task scheduling, enhanced team collaboration, and better decision-making facilitated by data insights and automation can streamline maintenance workflows.
Unlocking the Pillars of Maintenance Excellence
Three fundamental pillars underpin maintenance excellence:
- Preventive maintenance
- Predictive maintenance
- Reactive maintenance
These components are essential to an effective overall maintenance strategy as they significantly enhance efficiency, forestall asset failure, prolong their useful life, and diminish expenses and operational downtime.
So, what exactly are these pillars comprised of? It’s time for a closer examination.
Embracing Preventive Maintenance
Envision the capability to avert issues before they manifest. This is the essence of preventive maintenance.
Implementing regular inspections and adhering to a scheduled regimen within a preventive maintenance program enables us to diminish equipment malfunctions, prolong the life of assets, and enhance their energy efficiency.
Adopting this proactive stance also yields significant savings on spare parts and tools, reduces expensive repair occurrences, and provides better visibility for maintenance managers.
Nevertheless, challenges do exist. Excessive maintenance might trigger potential failures requiring ongoing optimization of PM activities.
When proper Computerized Maintenance Management Systems (CMMS) are utilized effectively, we can craft a consistent and efficient preventive maintenance routine that benefits operations in the long run.
Prioritizing Predictive Maintenance for Maintenance Tasks
Predictive maintenance enhances the process of preventive maintenance by foreseeing possible equipment failure in advance.
Leveraging data and machine learning, this advanced form of maintenance allows for better-informed decisions through constant surveillance and analytical insights. This can lead to a dramatic reduction—potentially up to 90%—in unanticipated equipment failures.
The Significance of Data in Predictive Maintenance
The role of data in predictive maintenance cannot be overstated. By gathering and analyzing data from various sensors and systems within the equipment, organizations can gain critical insights into the condition and performance of their assets.
This data-driven approach allows for identifying patterns and anomalies that may indicate impending equipment failure. With such predictive capabilities, maintenance can be scheduled at the optimal time to prevent downtime rather than reacting to unexpected breakdowns.
Furthermore, accumulating historical data over time enriches the predictive models, enhancing their accuracy and reliability in forecasting potential issues.
Source: WorkTrek
Machine Learning: A Game-Changer in Predictive Maintenance
Machine learning takes predictive maintenance to a new level by enabling the automated discovery of insights within the data. This advanced technology can learn from the data to identify complex correlations that human analysis might miss.
By employing machine learning algorithms, predictive maintenance systems can adapt and improve continuously, becoming more adept at forecasting failures with greater precision.
As a result, organizations can anticipate problems before they occur, optimize maintenance schedules, and reduce the frequency and severity of equipment downtime.
Integrating machine learning into predictive maintenance represents a significant leap forward in pursuing operational efficiency and asset management excellence.
This approach is instrumental in minimizing downtime significantly.
Mastering Reactive Maintenance
Even with thorough preventive and predictive maintenance efforts, equipment can fail without warning. In such instances, reactive maintenance and corrective maintenance are essential.
These methods focus on handling sudden malfunctions effectively to reduce downtime. They rely on competent technicians and ensure a well-stocked supply of crucial spare parts through reliability-centered maintenance practices.
Streamlining Your Maintenance Workflow
We must integrate CMMS software into the system to enhance maintenance workflow and achieve top-tier efficiency. This technology will automate work orders, optimize scheduling, and guarantee that essential parts and resources are readily available.
Maintenance managers can monitor task progress by proactively managing maintenance plans with this software. They’ll be able to ensure everything is in sync with broader strategic goals and make any adjustments required to improve maintenance operations, processes, and individual tasks.
Integrating Maintenance Management Systems
Examining CMMS reveals that this digital maintenance platform accomplishes several vital functions.
- It organizes and schedules maintenance tasks
- Timelines for inspections are established
- Distribution of work orders is handled efficiently
- Encourages teamwork among staff members
It bolsters decision-making by providing up-to-date data, thereby streamlining the execution of maintenance duties. This includes arranging preventive maintenance and identifying equipment problems at an early stage.
One of its most significant advantages is optimizing maintenance cost management. It achieves this through meticulous record keeping, close monitoring of expenses, and precise administration of the spare parts inventory.
Optimizing Resource Allocation
Optimizing resource allocation is a critical element in refining maintenance procedures. It’s crucial to assign tasks according to their urgency and complexity to reduce equipment downtime and enhance the efficiency of maintenance activities. This ensures that appropriate materials, staff, and equipment are designated for particular maintenance tasks, crucial for executing projects effectively and managing expenses judiciously.
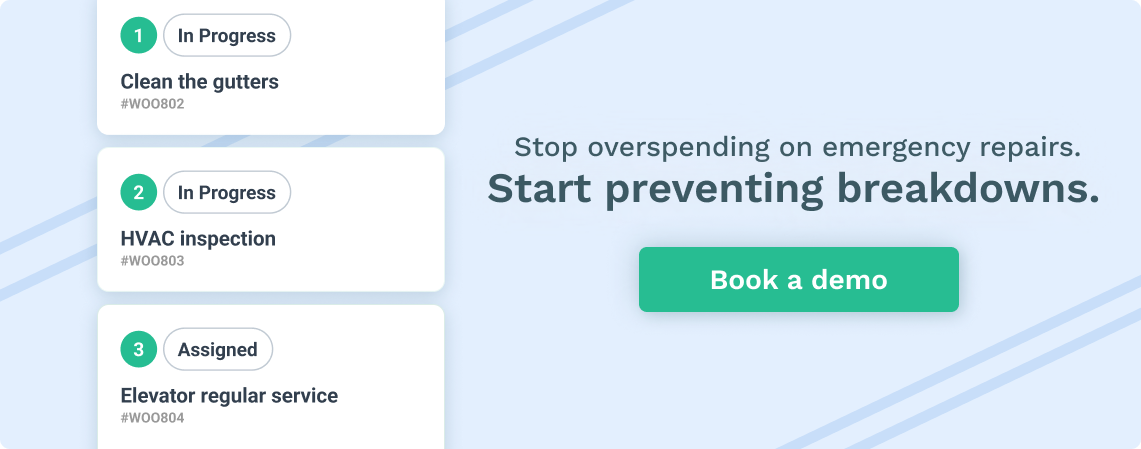
Maintenance Managers
Maintenance managers can optimize resources and better maintain equipment by implementing a strategic resource allocation plan. This involves thoroughly assessing maintenance tasks and prioritizing them based on criticality and urgency.
By doing so, managers ensure that high-priority equipment receives the necessary attention, preventing potential breakdowns that could lead to costly downtime.
Additionally, they can leverage CMMS software to track asset usage and performance, enabling informed decisions about when to allocate resources for maintenance, repairs, or replacements.
Optimizing resources also includes efficient inventory management of spare parts, ensuring that the correct parts are available when needed without overstocking, which ties up capital.
Training maintenance personnel to be multi-skilled can also increase flexibility in task assignments, allowing for a more dynamic response to maintenance needs.
By smartly managing time, personnel, and materials, maintenance managers can enhance the reliability and longevity of equipment while controlling costs.
Source: WorkTrek
Advancing with Automation
Recognizing the significance of automation is crucial to optimizing workflows. Fusing building automation systems with Computerized Maintenance Management Systems (CMMS) facilitates smoother inspections and enhances maintenance procedures.
Such integration instantaneously facilitates data exchange and supports a better-informed process for making decisions.
Cultivating a Skilled Maintenance Team
In developing an effective maintenance strategy, it is imperative to focus on creating a highly competent maintenance team. Essential attributes for such a team include experience, technical know-how, problem-solving abilities, varied backgrounds and experiences, independence in decision-making, and decisive leadership.
Fostering this type of team requires a relentless commitment to comprehensive training programs that combine theoretical knowledge with practical hands-on applications and structured onboarding processes designed to integrate new members smoothly.
Continuous Training and Development
Ongoing education and skill enhancement are essential for fostering a maintenance team with high expertise. By combining practical application with academic learning, we can ensure that the group is versatile and proficient.
This approach streamlines processes and enhances workplace safety by minimizing operational interruptions and incidents arising from personnel mistakes.
Empowering Maintenance Technicians
Empowering every member of the maintenance team is essential for nurturing them. Engaging management and staff in carrying out maintenance tasks can harness a variety of viewpoints, leading to enhanced outcomes.
Adopting this collaborative strategy has the potential to positively transform an organization’s culture by aligning it more closely with its mission and promoting a favorable shift within the organizational ethos.
Implementing Cost-Effective Maintenance Strategies
With the team assembled, it’s time to concentrate on the execution of maintenance strategies that are both economical and efficient. This includes:
- Ensuring a harmonious relationship between the costs of maintenance and the performance levels of assets
- Putting into action plans for preventive upkeep
- Carrying out tactical planning
- Managing inventory for spare components
Balancing Maintenance Costs and Asset Performance
Utilizing key performance indicators (KPIs) such as MC/ERV, MTBF, and MTTR is crucial in balancing maintenance costs with asset performance. These metrics are instrumental in assessing asset reliability, availability, and cost-efficiency.
Source: WorkTrek
Strategic Spare Parts Management
It’s essential to remember the vital importance spare parts play in maintenance strategy. Ensuring correct categorization, effective inventory management, and fostering strong supplier relationships can help us keep inventory levels at their best while minimizing carrying costs.
Measuring Success with Key Performance Indicators
We gauge the effectiveness of the maintenance strategy by utilizing Key Performance Indicators (KPIs). These essential tools assist in evaluating routines, procedures, and equipment to ensure that the organization is on track with maintenance objectives.
Defining Relevant KPIs
To accurately gauge the effectiveness of maintenance endeavors, it is imperative to establish pertinent Key Performance Indicators (KPIs). These should encompass a variety of metrics that are concentrated on multiple aspects, including:
- Proficiency
- Financial Expenditure
- Health and Safety Compliance
- Performance of Assets
- Operational Interruption Time
- Management of Work Orders
- Regulation and Control of Inventory
Tracking and Analyzing Data
Organizations can guarantee effective decision-making and maintenance planning through data tracking and analysis by gathering comprehensive records, scrutinizing long-term maintenance data, and acquiring consistent feedback once KPIs are established.
Aligning Maintenance Goals with Business Objectives
Source: Velosi
The maintenance KPIs and objectives must support overall business goals by establishing clear deliverables, prioritizing effectively, and fostering communication across various departments. This alignment is critical to evaluating the success of maintenance efforts in a way that contributes meaningfully to broader business ambitions.
Setting Clear Maintenance Objectives
Organizations must establish distinct maintenance targets to synchronize business objectives with maintenance aims. We should employ the SMART criteria to ensure these objectives are:
- Clearly defined
- Quantifiable
- Achievable
- Appropriate
- Restricted by time limits
Communicating Across Departments
Maintaining open lines of communication is crucial to aligning business objectives with maintenance goals. Successfully navigating the hurdles of interdepartmental teamwork can foster a more cohesive and affirmative company culture.
Enhancing Lifecycle Management of Assets
Now, we shall focus on the lifecycle management of assets. The process encompasses:
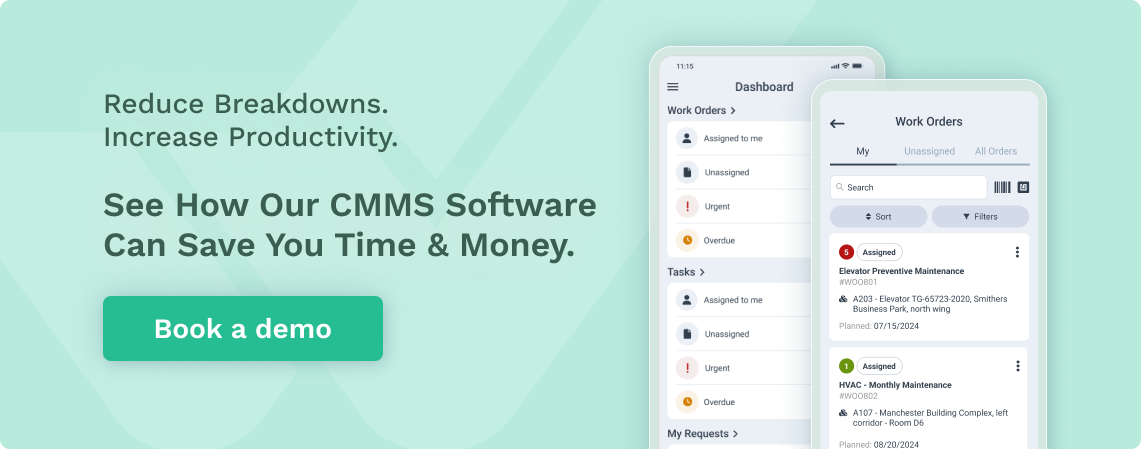
- Enhancing operational efficiency and return on investment across the lifespans of assets
- Performing analysis over asset lifecycles
- Developing strategies for managing asset lifecycles
- Recognizing critical assets
Lifecycle Analysis and Planning
Analyzing and planning activities throughout assets’ lifespans is essential to oversee their lifecycle proficiently. This requires consistently monitoring how these assets perform, examining past data, and strategizing for eventual asset disposal to facilitate informed decisions regarding maintenance scheduling.
Identifying Critical Assets
Recognizing which assets are critical is essential for managing them throughout their lifecycle and tracking the progress of repairs. Determining their significance in everyday activities allows us to concentrate maintenance work on these critical assets.
Proactive Approach to Decrease Downtime
Recognizing assets requires adopting a proactive strategy to reduce downtime. This calls for applying preventive and predictive maintenance tactics aimed at curtailing idle periods, cutting expenses, and enhancing the overall efficiency of the equipment.
Regular Inspections and Predictive Analytics
Adopting a proactive approach involves using regular inspections and predictive analytics. This strategy is instrumental in identifying early indications of deterioration, which aids in averting unforeseen breakdowns and minimizes periods of inactivity.
Emergency Response Planning
It’s crucial to have a carefully devised response strategy in place during an emergency. This should include established channels for clear communication, designated roles for team members, and consistent training exercises to tackle unforeseen equipment malfunctions promptly.
Crafting a Robust Maintenance Plan
We are now prepared to develop a comprehensive maintenance plan, including cataloging every piece of machinery and equipment, ranking them based on their importance, and formulating precise plans for their upkeep.
Assessing Maintenance Needs
To develop a robust plan for asset maintenance, we must evaluate maintenance requirements. This evaluation process includes assigning priority levels to every asset by considering variables like:
- The significance of the asset
- The specific needs related to its upkeep
- How often repairs are necessary
- Specifications about its operation
- Costs linked with maintaining each asset
Documenting and Reviewing the Maintenance Plan
After assessing maintenance requirements, we must document and scrutinize the maintenance strategy. This process includes logging all maintenance operations and consistently evaluating the plan to ensure its effectiveness while striving for continuous enhancement in upkeep activities.
Summary
In this article, we’ve explored the importance of preventive, predictive, and reactive maintenance, the role of CMMS software in streamlining workflows, the importance of a skilled maintenance team, and the significance of aligning maintenance goals with business objectives.
We’ve also delved into the lifecycle management of assets, taken a proactive approach to decrease downtime, and crafted a robust maintenance plan. As we conclude, remember this – every step taken towards maintenance excellence is a step towards cost efficiency, increased performance, and overall business growth.
A successful maintenance approach requires setting clear, measurable objectives that align with business goals, investing in continuous personnel training, and employing cost-effective practices, including strategic spare parts management and utilization of KPIs for performance measurement.
Frequently Asked Questions
What are the pillars of maintenance excellence?
Preventive, predictive, and reactive maintenance stands as the fundamental pillars of outstanding maintenance performance, collectively shaping an all-inclusive strategy for upkeep.
How can I streamline my maintenance workflow?
Consider adopting CMMS software to enhance your maintenance workflow. This technology can automate the generation of work orders, guarantee optimal scheduling, and maintain access to necessary parts and resources.
Such a move could markedly boost the effectiveness of your maintenance processes and increase overall operational efficiency.
What is the importance of a skilled maintenance team?
A skilled maintenance team is crucial for optimal asset management and maintenance success, achieved through continuous training and hands-on experience.
How can I balance maintenance costs and asset performance?
Implementing preventive maintenance, strategic planning for spare parts management, and utilizing key performance indicators such as Maintenance Cost to Estimated Replacement Value (MC/ERV), Mean Time Between Failures (MTBF), and Mean Time To Repair (MTTR) can help maintain harmony between asset performance and the costs of maintaining those assets. These strategies aid in assessing the availability, reliability, and cost-efficiency of your assets.
What is a proactive approach to decreasing downtime?
Adopting predictive and preventive maintenance strategies can enhance equipment efficiency, reduce downtime, and diminish overall maintenance costs.