Get a Free WorkTrek Demo
Let's show you how WorkTrek can help you optimize your maintenance operation.
Try for freeHow do oil and gas maintenance safeguard operations and drive efficiency? Find methods to strengthen assets, reduce costs, and stay safe in this demanding industry. In this article, the ongoing innovation and maintenance best practices matter for oil and gas operations.
This article will cover important topics critical to the oil and gas industry. These topics include proactive preventive maintenance to avoid equipment failures, advanced predictive maintenance techniques to forecast issues, and strategic reactive maintenance to address unexpected breakdowns. These aim to enhance operational efficiency and safety for oil and gas maintenance.
We’ll also cover technological advancements like IoT, AI, CMMS, and innovative corrosion prevention methods that are revolutionizing maintenance practices, optimizing operations, extending equipment life, and ensuring maintenance is cost-effective despite the challenges posed by aging infrastructure and harsh operating conditions.
Regular maintenance is critical for operational safety and reliability in the oil and gas industry. It involves frequent inspections and timely interventions to mitigate risks and extend the equipment’s lifespan, making maintenance cost-effective in high-risk environments.
Exploring the Spectrum of Maintenance Strategies in Oil and Gas
Managing complex machinery and extensive infrastructure requires well-planned strategic measures in the oil and gas industry. This not only entails fixing what has malfunctioned but also involves proactively preventing issues before they arise and skillfully handling unforeseen events as they occur.
With the intricate nature of assets, strict regulatory standards to follow, and inherent safety hazards present, it is critical for oil and gas companies to recognize the importance of effective maintenance in upholding operational efficiency.
Maintenance within this sector balances planned inspections, regular servicing routines, and astute data analysis—all designed to improve operational efficiency and productivity.
Consistent maintenance ensures that equipment performance remains at its peak while reducing incidents that could lead to shutdowns. Proactive strategies are mainly focused on countering wear-and-tear impacts on equipment over time.
Source: WorkTrek
Proactive Preventive Maintenance
Preventive maintenance stands as a critical element in equipment maintenance, serving as the shield protecting against disruptions caused by equipment failure. Within the oil and gas sectors, this involves:
- Systematic cleansing
- Adequate lubrication
- Prompt substitution of worn parts
All these practices are based on a detailed analysis of the service durations of various components. This process involves reviewing historical data, evaluating wear and tear patterns, and employing advanced software tools to predict maintenance needs using real-time performance metrics.
Using data for preventive maintenance
By incorporating these insights, companies can refine their maintenance schedules, reducing unnecessary downtime and optimizing equipment lifecycles. Furthermore, leveraging technologies like AI and IoT enhances predictive capabilities, allowing for a dynamic and responsive maintenance strategy that adapts to the evolving conditions of both machinery and the operational environment.
This preventive approach is essential for sustaining continuous operation and robust functionality within large-scale machinery.
Safety Assessment
Organizations can dodge potential production delays while conducting exhaustive safety assessments by preemptively managing spare part inventories and synchronizing machine downtime for collective maintenance work.
Regular examinations guided by established schedules or usage statistics safeguard against malfunctions, thus significantly reducing the chance of expensive repairs. By embracing preventative methods over reactive ones, operational downtime is minimized, and production efficiency soars to greater levels.
Advanced Predictive Maintenance
Predictive maintenance is akin to having a crystal ball that predicts and prevents equipment failures before they disrupt crucial operations. This advanced technique employs:
- Systems for managing asset performance
- Analysis of vibration patterns
- Infrared thermographic inspection
- Sonic testing technologies
Leveraging these tools enables the early identification of wear and corrosion, thereby allowing for timely preventive maintenance actions. This proactive approach helps maintain the equipment’s optimal performance and significantly extends its operational life.
Early Detection of Issues
By detecting potential issues early, companies can plan and execute maintenance activities without disrupting the production schedule, maximizing uptime and productivity.
Additionally, early identification of wear and corrosion can prevent minor issues from escalating into major failures, which could be more costly and time-consuming to repair.
Industry Compliance
Furthermore, it helps to maintain compliance with industry regulations and standards, which is crucial for oil and gas companies’ reputation and operational legality.
By adopting these sophisticated practices, oil and gas establishments are equipped to:
- Anticipate breakdowns in machinery
- Drastically reduce spontaneous downtime along with its accompanying repair expenses
- Prolong the useful lifespan of essential assets
- Reinforce both safety standards and dependability
Strategic Proactive and Predictive Maintenance
While proactive preventive and predictive maintenance has introduced a new efficiency level, the traditional practice of reactive maintenance still holds its ground.
This method is often reserved for non-critical or aging gas facilities and aging equipment nearing the end of its operational life, whether through decommissioning or filter replacement.
Source: WorkTrek
Strategic Reactive Maintenance
Strategic reactive maintenance comes into play when unforeseen failures arise, swiftly tackling problems to guarantee that even antiquated machinery can conclude its service with honor.
Enhancing Safety and Reliability in Operations
In the oil and gas industry, where potential hazards and opportunities coexist, neither safety nor operational reliability must be compromised. A consistent preventive maintenance routine shields against incidents and ensures seamless operational flow. Regularly tending to maintenance enables companies to tackle issues such as:
- corrosion
- equipment failure
- leaks and spills
- overall equipment wear
Such proactive measures enhance equipment and materials safety and dependability while also providing cost-effectiveness by reducing expenses in the long term.
Culture of Safety
Building a safety culture and having suitable preventative measures in place is key to tackling the significant issues in this industry. Preventative maintenance is proactive; it prevents breakdowns and reduces unexpected downtime, essential for safe and efficient operation.
A robust safety culture is the backbone of any successful oil and gas operation. It involves implementing preventive measures and fostering an environment where safety is prioritized at every level.
This means regular training, clear communication, and a commitment to continuous improvement. Employees must feel empowered to report potential hazards and take action to mitigate risks before they escalate.
Industry Collaboration
In addition to technological advancements, collaboration and knowledge sharing among industry peers can significantly contribute to building a safety culture.
Attending industry conferences, participating in safety workshops, and engaging in professional networks can provide valuable insights and best practices that can be applied within one’s organization.
Mitigating Risks with Regular Inspections
Regular inspections are critical in the oil and gas industry. They carefully examine each component to ensure strict compliance with safety standards and promptly address any irregularities. Predictive maintenance techniques can provide insight, detecting early signs of wear and tear on equipment, thus enabling immediate repairs to maintain consistent reliability.
Such thorough checks also protect against potential hazards that could compromise worker safety and pose environmental risks. By implementing controls identified during regular assessments, these inspections are vital cogs in risk management and prevention.
Sustaining Equipment Reliability
Consistently scheduled maintenance is vital in decreasing idle time and averting mishaps. It sets the tempo for equipment availability, ensuring that it operates consistently without fail.
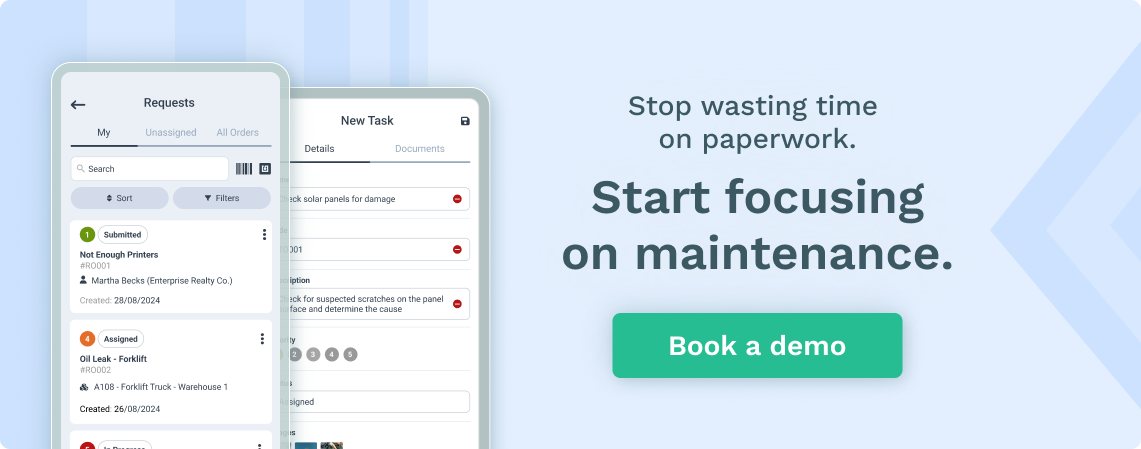
Equipment reliability and operational safety improve markedly when maintenance tasks are methodically organized.
Following established maintenance schedules is vital for keeping machinery running efficiently. This reliability is essential in the oil and gas industry, where even minor disruptions can have significant repercussions. It is the foundation of successful operations.
Cost-Effective Maintenance Approaches
The oil and gas sector’s performance is high, but the budget is low. Therefore, cost-effective and regulatory-compliant maintenance strategies are needed to ensure safety, compliance, and efficiency. A good maintenance strategy is critical as it helps manage costs while protecting people and beating benchmarks.
Technology to help control cost
Recent advancements such as intelligent machinery and cloud technology innovations, coupled with advanced methods for corrosion prevention, have revolutionized how maintenance costs can be minimized without sacrificing operation integrity.
Despite these technological strides, economic constraints pose considerable hurdles for maintenance teams who must ensure assets remain in top condition—a requirement critical to maintaining seamless operational efficacy.
Minimizing Maintenance Costs
Utilizing advanced data analytics, the oil and gas industry can enhance predictive maintenance to:
- Anticipate when equipment might fail
- Decrease both the frequency and severity of unplanned downtime
- Prevent hefty expenses that typically arise from abrupt equipment failures
- Reduce potential safety risks related to these occurrences
Being forward-thinking with maintenance brings many benefits to this industry. Companies can tune their maintenance by balancing cost with quality and safety. This balancing act gives operational efficiency in the oil and gas market, where cost control and longer equipment life are essential.
Balancing Budget and Performance
In the oil and gas industry, efficiently managing maintenance activities requires navigating several critical challenges.
- Mitigating significant safety risks inherent to operations
- Handling the complexities of maintaining older infrastructure
- Dealing with the severe environmental conditions that define operations in this sector
It’s all about balancing budget and performance. That means resource management and fund allocation. You need to have a view of the whole operational landscape, including the maintenance cost and what it does to overall performance.
Resource management prioritizes maintenance tasks that impact safety and operational performance. So, we allocate resources to the areas that will give us the highest return on investment, such as upgrading key equipment, installing monitoring systems, and training personnel to perform complex maintenance tasks. That way, we use our resources effectively, waste less, and get more out of our maintenance.
Then, you have to think forward and not just see maintenance budgets as expenses but as an investment in the life and reliability of the infrastructure.
That means being proactive with maintenance and addressing potential issues before they become big problems and lead to costly repairs.
It means using the latest technology and industry best practices to optimize maintenance schedules, downtime, and equipment performance.
Source: WorkTrek
The Role of Technology in Maintenance Optimization
In oil and gas, cutting-edge technologies have paved the way for a transformative approach to maintaining operations. Intelligent equipment, cloud computing, and advanced strategies for combating corrosion are pivotal in driving down maintenance costs. This steers the sector toward an era where thriftiness aligns with high performance.
Cutting Edge Technologies
Developments such as Artificial Intelligence and enhanced IoT communication have improved equipment maintenance procedures within these industries and can help reduce costs and enhance regular maintenance.
By strengthening preventive measures and enhancing infrastructure integrity—key elements of oil and gas operations—they extend the lifespan of assets, improve equipment performance, and reduce issues with aging equipment while achieving significant reductions in operational costs.
Harnessing Data for Maintenance Decisions
Incorporating digital technologies in the oil and gas industry marks a significant transformation, especially with adopting cloud computing and advanced data management. These innovations facilitate rapid, well-informed decision-making processes that significantly enhance operational efficiency and maintenance activity scheduling.
The integration of AI along with IoT has refined preventive maintenance practices, enabling more accurately tailored schedules for equipment service and component replacement.
Predictive Maintenance
Predictive maintenance is grounded on data analytics and cutting-edge monitoring systems to ensure that equipment remains reliable and safe for operation. Comprehensive tools like CMMS digital workflow builders are essential for creating detailed maintenance checklists while seamlessly implementing predictive maintenance tactics.
Emphasizing asset data integrity during high availability situations or disaster recovery operations Reinforces how critical robust asset management is when making decisions about maintaining an optimal state throughout the oil and gas industry infrastructure.
Integrating CMMS Solutions
Maintenance operations in the oil and gas industry are becoming more dependent on Computerized Maintenance Management Systems (CMMS). These systems, such as WorkTrek CMMS Solution, automate ordering parts and fine-tuning preventive maintenance schedules, leading to a refined workflow for precision during maintenance activities.
The analytical capabilities of CMMS tools empower stakeholders in the oil and gas field to take strategic actions regarding upkeep that bolster efficiency and reliability.
Cloud-based CMMS platforms, paired with mobile app functionality, contribute significant advantages, including:
- Greater accessibility and control over data
- More efficient procedures for inspections and routine upkeep tasks
- Driving progress within the sector towards unparalleled levels of maintaining excellence.
- Automate Preventive Maintenance Checklists
- Reduce costly repairs
- Reduce costs
- Centralize parts and materials
- Provide better visibility to equipment and repairs
Source: WorkTrek
Addressing the Challenges of Aging Infrastructure
In the oil and gas industry, a significant challenge confronting aging infrastructure is corrosion, which is exacerbated by aggressive substances like CO2 and H2S. To meet the increasing maintenance needs of these mature assets, it’s critical to adopt proactive approaches such as integrity management and condition-based maintenance.
As offshore facilities age, combating obsolescence and effectively managing to age is crucial for maintaining safety and operational integrity. This continuous fight demands relentless attention and dedication to achieving excellence in maintenance practices.
Extending Equipment Life Span
Offshore assets must be managed sustainably to remain operational and safe and extend their life. Marine environments are harsh, so it’s not just about building robust structures but also maintaining wells and controlling corrosion.
Assessments focused on present functionality, potential operational capabilities in future contexts, structural material durability, and preparedness at an administrative level play instrumental roles in prolonging the life expectancy of aging offshore structures. Firms like Keystone Energy offer specialized repair solutions that breathe new life into tools and machinery while enhancing asset longevity.
Overcoming Corrosion and Wear
The oil and gas industry is engaged in a constant battle against the damaging effects of corrosion and wear, yet these challenges are not insurmountable.
Companies like EonCoat offer advanced coatings that shield against corrosive forces. Surface modification technologies such as Physical Vapor Deposition and Chemical Vapor Deposition, which create robust barriers, can significantly enhance equipment longevity.
An array of solutions, including heat-resistant layers, corrosion-resistant linings, and detection pigments, mitigates corrosion and wear in the oil and gas sector.
Advances continue with cost-effective developments like epoxy coatings enriched with aluminum oxide particles, delivering heightened defense, especially for essential assets such as subsea cables.
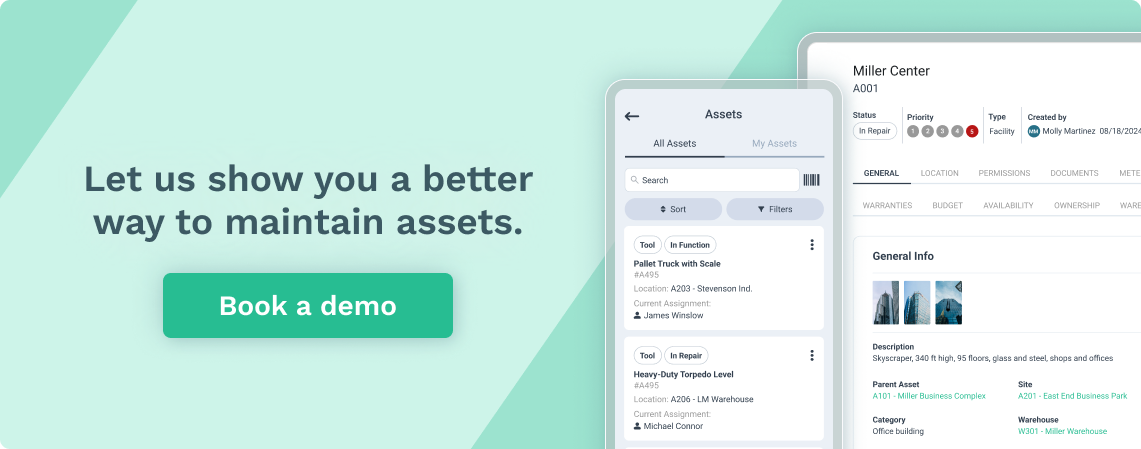
Regularly monitoring pipelines and storage containers plays an integral role in the early detection—and thus prompt correction—of potential corrosion complications. This proactive approach helps maintain the industry’s critical conduits.
Best Practices for Maintenance in Harsh Environments
Oil and gas asset maintenance professionals face some of the most extreme environments on the planet. Operating in remote areas that endure severe weather, variable temperatures, and corrosive elements presents a substantial challenge to maintaining effective operations.
Proactive measures are critical in these demanding contexts. They aren’t simply recommended procedures but essential strategies for enhancing safety protocols and ensuring assets function efficiently.
Technological advancements have revolutionized the approach to maintenance tasks in these strenuous environments. Innovative solutions like wearable devices designed for worker protection, unmanned aerial vehicles conducting pipeline inspections, and systems monitoring environmental variables in real time have vastly improved teams’ ability to foresee potential problems quickly and precisely address them.
These developments facilitate refined practices explicitly tailored for overcoming obstacles inherent in maintaining oil and gas installations under challenging circumstances.
Special Considerations for Offshore Facilities
Maintenance of offshore oil and gas can be challenging. The environment is unique and requires special attention. Sensor technology is the key to getting the information to identify faults quickly so maintenance teams can respond quickly and keep everything safe and running.
Given the harsh conditions of marine environments, consistent maintenance is crucial for ensuring smooth operations within these facilities. With significant environmental impacts at stake and the necessity for uninterrupted production, addressing maintenance with the highest level of diligence becomes increasingly essential.
Source: Rockwell Automation
Ensuring Worker Safety in Hazardous Areas
Safety is the most critical element for employees in the oil and gas industry, who confront daily hazards to guarantee ongoing energy supply. For these companies, safety has to transcend mere policy. It must become an established cultural norm within every facet of their business practices.
Ensuring high levels of safety involves a commitment to comprehensive incident documentation, thorough investigations into accidents, and solid emergency response protocols that help diminish injury risks.
In offshore operations where risks are ever-present, structured strategies and extensive training play a vital role in equipping staff for potential emergencies.
Such preparedness through emergency response plans is crucial so that if incidents arise, teams can tackle them with competence and promptness—thereby mitigating damage and keeping situations under control even in environments fraught with danger.
Summary
As we conclude our thorough examination of maintenance in the oil and gas industry, we’ve highlighted various strategies that can revolutionize operational practices. Combining proactive preventive maintenance, predictive analytics, and strategic reactive measures creates a comprehensive and essential framework for sustaining this sector.
We must acknowledge the critical lessons learned: Maintenance is not just routine work; it is a key factor in ensuring safety, improving efficiency, and extending the lifespan of assets in the oil and gas sector. By adopting these strategies, companies can elevate their operational practices and foster a more efficient and sustainable energy production environment.
Frequently Asked Questions
Why is preventive maintenance crucial in the oil and gas industry?
Preventive maintenance is essential in the oil and gas industry. It helps avert equipment breakdowns, sustain operational performance, diminish production interruptions, and boost efficiency in extracting oil and gas.
How does predictive maintenance contribute to operational efficiency?
Predictive maintenance enhances operational efficiency by proactively supervising equipment performance. This approach minimizes unexpected outages and upholds operations’ safety and dependability by detecting possible problems early and coordinating timely maintenance efforts.
What role does technology play in optimizing maintenance in the oil and gas industry?
Solutions like IIoT, AI, and CMMS enhance maintenance operations by optimizing data handling, permitting predictive analytics, and refining the coordination of maintenance activities. This progression leads to cost reductions and extends the longevity of equipment.
How can oil and gas companies maintain aging infrastructure?
Oil and gas companies can oversee the upkeep of their mature infrastructure by adopting enduring asset management strategies and proactive maintenance practices that prioritize integrity management and condition-based maintenance. These practices integrate advanced solutions designed to tackle corrosion and deterioration effectively.
This methodology allows oil and gas companies to secure their infrastructure assets’ extended lifespan and safety.
What are some best practices for maintaining equipment in harsh environments?
In extreme conditions, it is critical to embrace new technologies for monitoring safety, utilize unmanned aerial vehicles (drones) for asset inspections, conduct real-time observation of environmental conditions, and guarantee thorough incident reporting alongside robust emergency response procedures.