Get a Free WorkTrek Demo
Let's show you how WorkTrek can help you optimize your maintenance operation.
Try for freeReactive maintenance is a strategy for repairing equipment after it fails or breaks down. It’s different from other types that try to prevent problems before they happen. Some people call it “run-to-failure” maintenance. This method is standard in many industries and homes.
This type of breakdown maintenance can work well for some items.
It might be good for cheap or easy-to-replace things, but it can cause big problems for important machines.
Knowing when to use it is key to keeping costs down and operations running smoothly.
Key Takeaways
- Reactive maintenance fixes equipment only after it breaks down
- This strategy can be cost-effective for non-critical assets
- Proper implementation requires careful planning and risk assessment
Understanding Reactive Maintenance
Definition and Fundamentals
Reactive maintenance is a method in which repairs occur after equipment fails. It’s also called “run-to-failure” maintenance. Companies using this approach don’t perform regular checks or upkeep.
The main idea is to use machines until they stop working due to equipment failure.
Then, technicians step in to fix the problem. This can save money on routine maintenance costs.
However, while reactive maintenance is common in many industries, it can lead to more extended downtimes when unexpected problems occur.
Types of Reactive Maintenance
Reactive maintenance encompasses various approaches to addressing equipment failures. Understanding these types can help businesses choose the right strategy for different situations.
Emergency Maintenance
Emergency maintenance is critical to reactive maintenance.
The focus is on immediate responses to unexpected equipment failures or breakdowns. This type of maintenance is essential to prevent further damage, ensure safety, and minimize downtime.
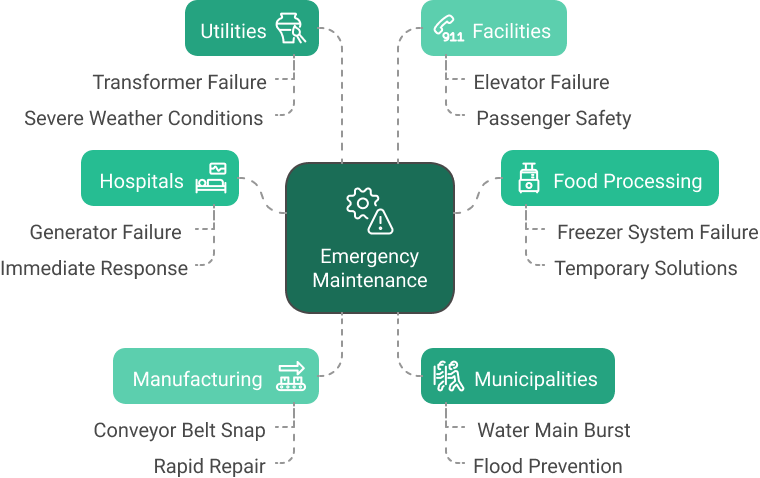
Source: WorkTrek
When an emergency occurs, the maintenance team must diagnose and fix the issue swiftly.
This often involves specialized skills, equipment, and resources, making it more costly than planned maintenance.
However, the urgency of these repairs justifies the expense, as delaying them could lead to more significant problems.
Emergency Maintenance Scenarios
Common scenarios requiring emergency maintenance include:
- Repairing a critical piece of equipment that has failed unexpectedly
- Responding to natural disasters, such as floods or earthquakes, that have damaged equipment
- Addressing safety hazards, like leaks or electrical issues, that demand immediate attention
Emergency maintenance, also known as corrective maintenance, is often performed alongside other reactive maintenance types to restore equipment to normal operating conditions as quickly and safely as possible.
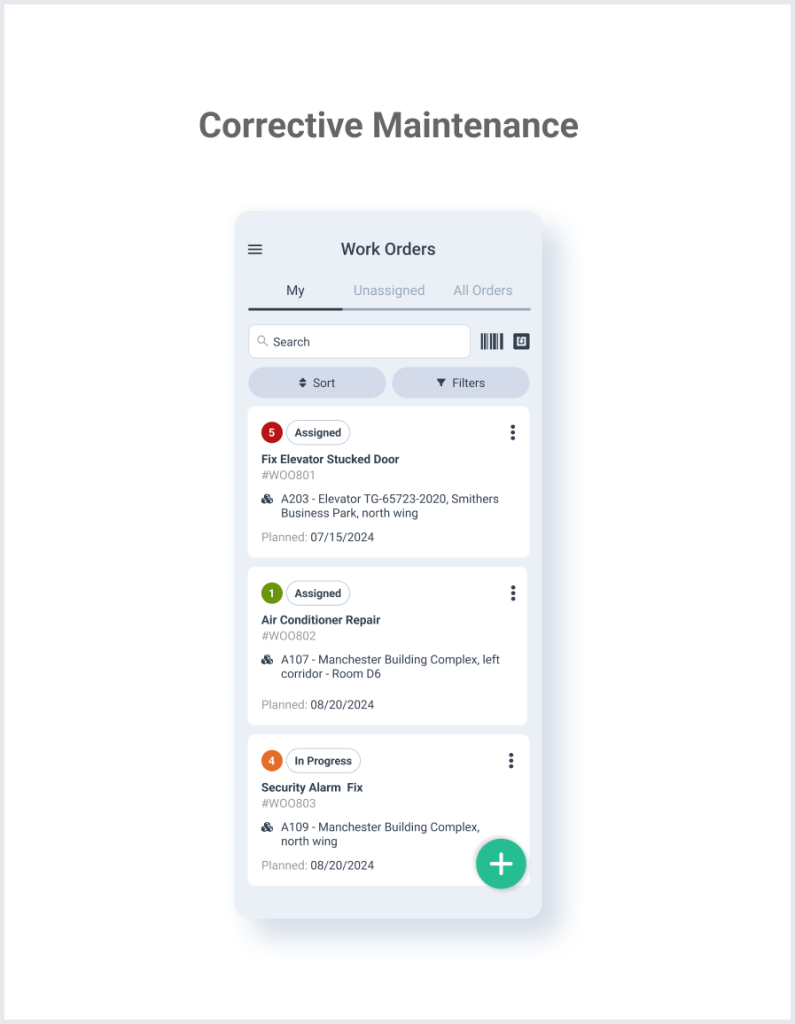
While emergency maintenance is sometimes unavoidable, restoring equipment to normal operation can be disruptive and expensive.
Is there a better way?
One solution is implementing a proactive maintenance plan that can help reduce the frequency of emergency repairs.
For instance, preventive maintenance involves routine inspections and maintenance performed tasks to identify potential issues before they escalate.
This proactive approach can significantly reduce the need for emergency maintenance and minimize associated costs and downtime.
Using Data and Analytics
Predictive maintenance takes this further by using data and analytics to forecast when equipment will likely fail.
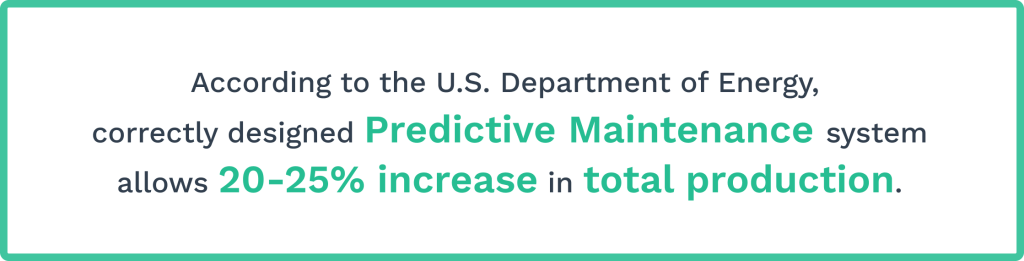
By anticipating failures, maintenance teams can perform necessary tasks before a breakdown occurs, reducing the need for emergency interventions.
In summary, emergency maintenance is a vital component of reactive maintenance, requiring quick action to address unexpected equipment failures.
By adopting proactive maintenance strategies, such as preventive and predictive maintenance, organizations can minimize the need for emergency repairs and ensure smoother, more cost-effective operations.
Comparing Maintenance Strategies
Reactive maintenance is one of several approaches to equipment care before failure occurs. Other methods include preventive and predictive maintenance.
Preventive maintenance involves regular checks and upkeep to avoid breakdowns. A preventive maintenance strategy can help extend machine life but costs more upfront.
Predictive maintenance uses data to guess when repairs might be needed. It can be very effective but requires special tools and skills.
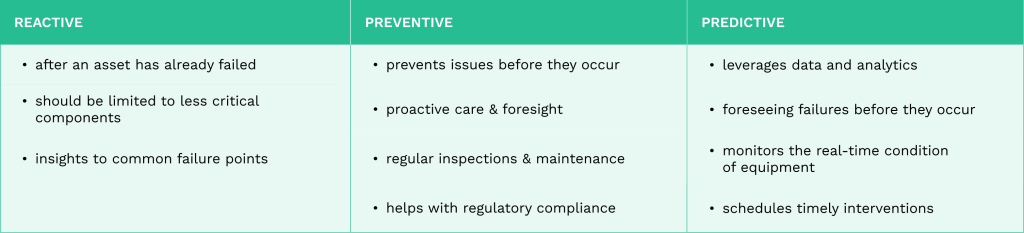
Reactive maintenance is often cheaper initially, but sudden breakdowns and emergency repairs can lead to higher costs.
When Reactive Maintenance Is Applicable
Reactive maintenance approach works best for certain situations where you want to reduce unnecessary maintenance.
It’s suitable for equipment that’s:
- Cheap to replace
- Not critical to operations
- It is unlikely to cause safety issues if it fails
Some examples include:
- Light bulbs
- Small office equipment
- Non-essential tools
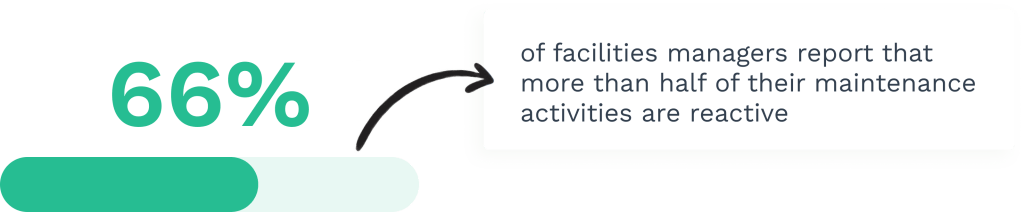
For critical machines, reactive maintenance can be risky. It may cause unexpected downtime and high repair costs.
Businesses should weigh the pros and cons carefully. The right strategy depends on the specific equipment and company needs.
Utilizing CMMS for Enhanced Reactive Maintenance
A Computerized Maintenance Management System (CMMS) like WorkTrek can significantly improve the efficiency and effectiveness of reactive maintenance strategies.
By leveraging CMMS, maintenance teams can streamline their processes, keep detailed records, and manage notifications, ultimately enhancing their ability to respond to equipment failures.
Streamlining Reactive Maintenance Processes
CMMS provides a centralized platform for logging and tracking maintenance tasks in real-time. When equipment fails, technicians can quickly input repair requests into the system, ensuring all team members know the issue.
This immediate logging helps prioritize tasks based on urgency and available resources.
Record Keeping and Historical Data
One key advantage of using a CMMS is its ability to maintain comprehensive records of all maintenance activities.
Each repair, including parts used, time taken, and technician involved, is documented within the system.
This historical data is invaluable for identifying patterns of equipment failures and can inform future maintenance strategies, potentially reducing the frequency of reactive maintenance needs.
Notifications and Alerts
CMMS systems have notification features that alert maintenance teams to new repair requests or updates on ongoing jobs.
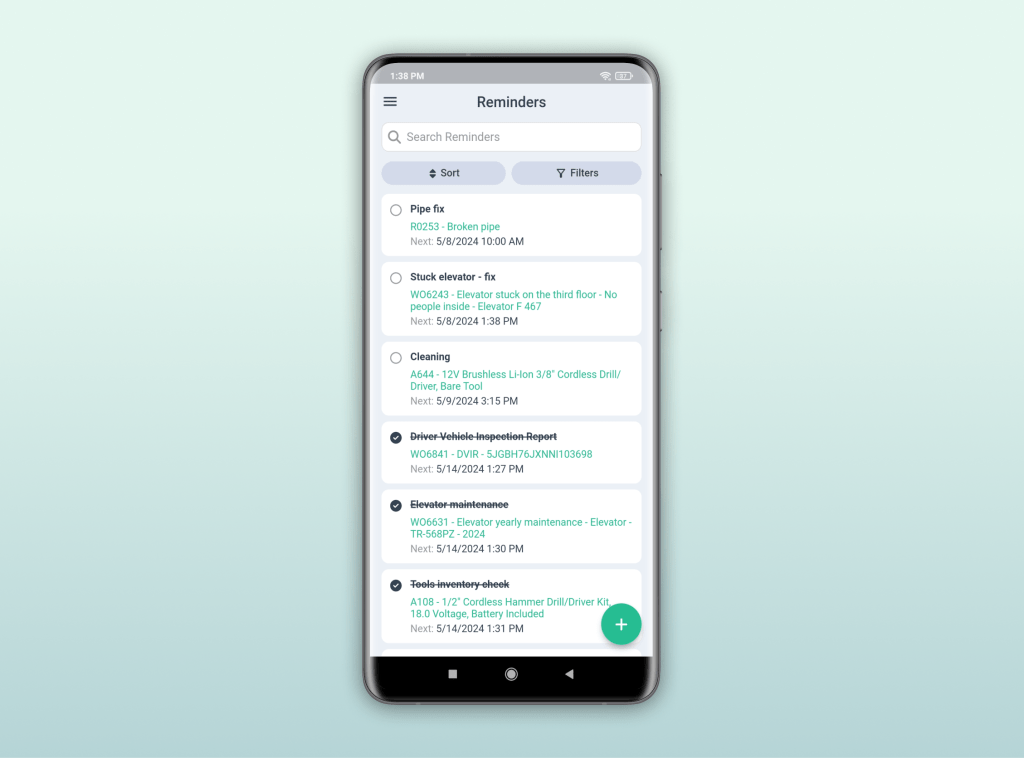
These alerts can be customized to notify relevant personnel via email or mobile apps, ensuring that no critical task goes unnoticed.
This feature is handy for managing emergency maintenance tasks, where swift response times are crucial.
Enhancing Communication and Coordination
Effective communication is vital in reactive maintenance scenarios. CMMS facilitates better coordination among team members by providing a shared platform for updates and progress reports.
This ensures everyone is informed about the status of repairs and any priority changes, minimizing downtime and improving overall response times.
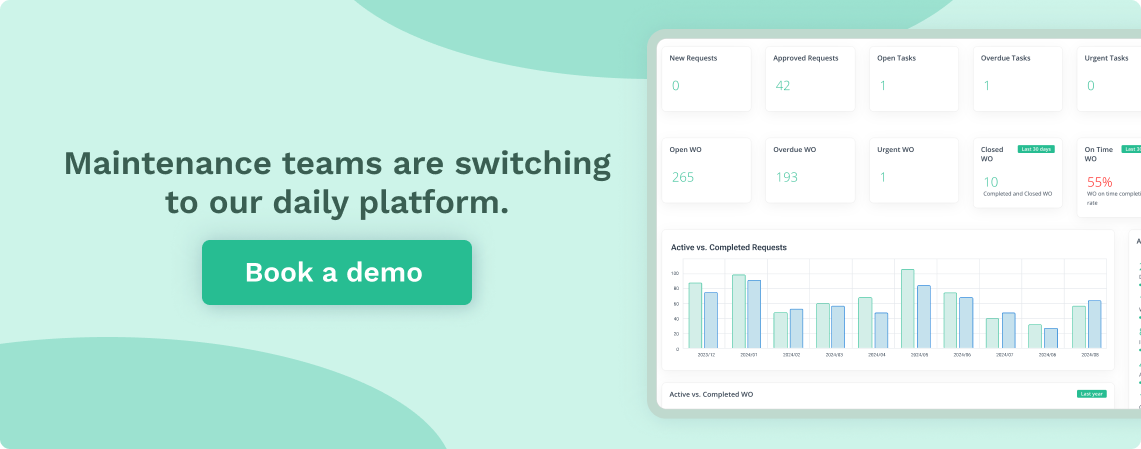
Reactive Maintenance Processes
Reactive maintenance involves specific processes to address equipment failures quickly and effectively. These processes focus on emergency repairs and routine maintenance activities.
Emergency Repairs and Procedures
Emergency maintenance refers to reacting quickly when equipment fails unexpectedly. Technicians must first assess the situation to determine the extent of the damage.
They then identify the root cause of the failure. This step is crucial for implementing the proper fix.
Next, technicians gather the necessary tools and parts. In some cases, they may need to order specialized components.
Emergency repairs often involve temporary fixes to minimize downtime. These quick solutions allow operations to resume while permanent repairs are planned.
Safety is paramount during emergency procedures. Technicians must follow strict protocols to protect themselves and others.
Clear communication is essential. Teams need to coordinate efforts and keep stakeholders informed throughout the repair process.
Maintenance Activities and Tasks
Routine maintenance tasks are a key part of reactive maintenance, with various maintenance tasks performed to restore equipment to working order.
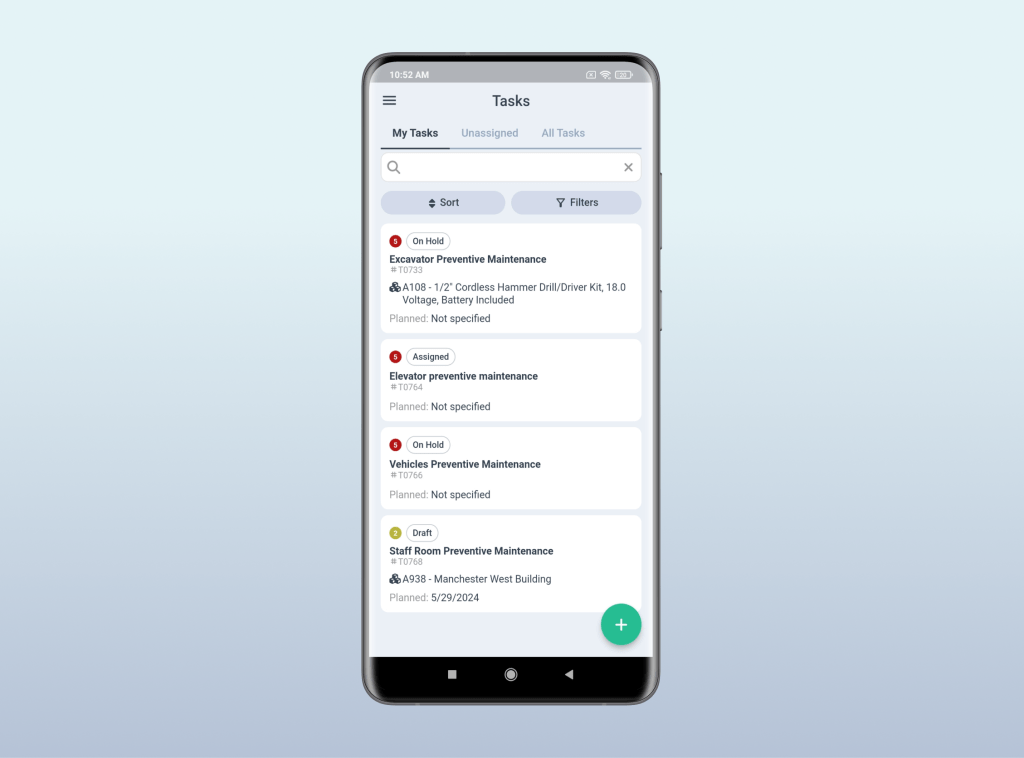
Common tasks include:
- Replacing worn or broken parts
- Cleaning and lubricating components
- Adjusting and calibrating equipment
- Updating software or firmware
Technicians often use checklists to ensure they complete all necessary steps. These lists help maintain consistency and quality in repairs.
Documentation is crucial. Technicians record details of each repair, including parts used and time spent.
This information aids in future troubleshooting and helps track maintenance costs.
Regular inspections may follow repairs to ensure the fix was successful. These checks help prevent recurring issues and extend equipment life.
Advantages and Disadvantages
Reactive maintenance has both positive and negative aspects. It offers some benefits but also comes with risks and drawbacks.
Benefits of Reactive Maintenance
Reactive maintenance can be cost-effective in the short term. Companies spend less on routine checks and part replacements, and this approach works well for non-critical equipment.
It requires less planning and fewer staff. Managers don’t need to create complex maintenance schedules; workers can focus on other tasks when machines run smoothly.
Reactive maintenance is simple to understand and implement. Small businesses with limited resources often use this method because it doesn’t need special training or tools.
Limitations and Risks
The disadvantages of reactive maintenance include unplanned downtime. Equipment failures can suddenly halt production, leading to lost time and money.
Reactive maintenance increases safety risks. Broken machines may cause accidents or injuries, and workers might not be prepared to handle sudden breakdowns safely.
Long-term costs can be higher. Repairs for severely damaged equipment are often more expensive. Machines that aren’t maintained regularly tend to break down more often.
This approach typically shortens equipment lifespan. Lack of regular care can cause parts to wear out faster, so companies must replace machines more frequently.
Impact on Business Operations
Reactive maintenance significantly affects how companies operate day-to-day. It touches many areas, from equipment performance to financial health.
Downtime and Unplanned Disruptions
Reactive maintenance often leads to unexpected downtime. When machines break without warning, work stops suddenly. This can delay production and disappoint customers.
Unplanned disruptions also stress employees. Workers must scramble to fix issues quickly. This rush can lead to mistakes or incomplete repairs.
During these surprise breakdowns, regular business processes get thrown off track. Teams may need to work overtime to catch up, which disrupts schedules and can hurt morale.
Cost Implications
The financial impact of reactive maintenance is substantial. Emergency repairs usually cost more than planned ones, and companies often pay premium prices for rush parts and labor.
Unexpected equipment failures can result in lost sales and unhappy clients. These losses increase quickly, especially for businesses that rely on continuous operations.
Long-term costs also increase. Machines that run until they break often need more extensive repairs. This can shorten their overall lifespan, leading to earlier replacement.
Equipment and Asset Management
Reactive maintenance strategies make it hard to manage assets effectively. Without regular checks, it’s tough to know the true condition of the equipment.
This approach can lead to:
- Shortened equipment lifespans
- Inefficient use of maintenance resources
- Difficulty planning for future equipment needs
Poor asset management can result in unexpected capital expenses. For example, companies might need to replace major equipment sooner than planned.
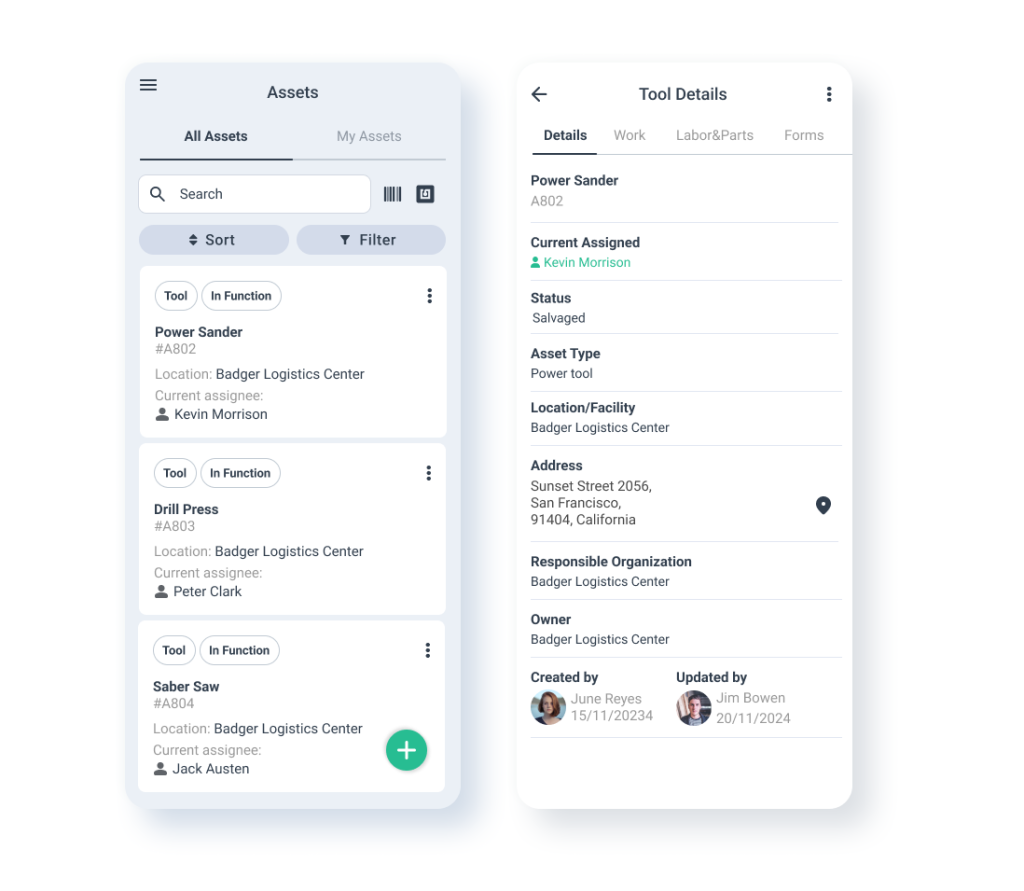
Reactive strategies also make optimizing equipment performance challenging. Machines may run below peak efficiency for long periods before issues are noticed.
Implementing Reactive Maintenance
Reactive maintenance requires a clear workflow and the right tools. Companies must plan their approach and use software to manage repairs efficiently.
Maintenance Workflow and Planning
A good reactive maintenance plan starts with setting up a clear workflow. This helps teams know what to do when equipment breaks down.
The first step is to report the problem quickly. Workers should tell managers or maintenance staff immediately when something isn’t working.
Next, the issue needs to be assessed. A skilled technician should check the equipment to determine what’s wrong. They should then decide whether it can be fixed immediately or if more work is needed.
After the assessment, repairs begin. The team should have access to common parts and tools to fix issues quickly. If special parts are needed, a plan should be implemented to get them quickly.
Streamlined response systems are key to successful reactive maintenance. Teams should practice responding to common problems to act quickly when real issues occur.
Utilizing Maintenance Management Software
Good software makes reactive maintenance much easier to handle. Computerized Maintenance Management Systems (CMMS) help teams track repairs and manage work orders. These systems can:
- Log repair requests quickly
- Assign tasks to the right technicians
- Keep track of spare parts
- Record the repair history for each piece of equipment
With a CMMS, managers can see what’s being fixed and how long it takes. This helps them make better decisions about when to replace equipment instead of repairing it.
Mobile apps for CMMS let workers report issues from anywhere. Technicians can access repair manuals and equipment data on their phones or tablets while working on fixes.
Run-to-Failure Maintenance
Run-to-failure maintenance is a planned approach where assets operate until they break down. This strategy involves deliberate non-intervention and careful asset lifespan evaluation. It can be cost-effective for certain equipment types.
Concept and Examples
Run-to-failure maintenance lets equipment operate until it stops working. It’s used when fixing or replacing after a breakdown is cheaper than ongoing upkeep.
Common examples include:
- Light bulbs
- Disposable batteries
- Printer ink cartridges
- Certain conveyor belts
This method works well for non-critical items with predictable lifespans. It’s also used for equipment where regular checks might cause more harm than good.
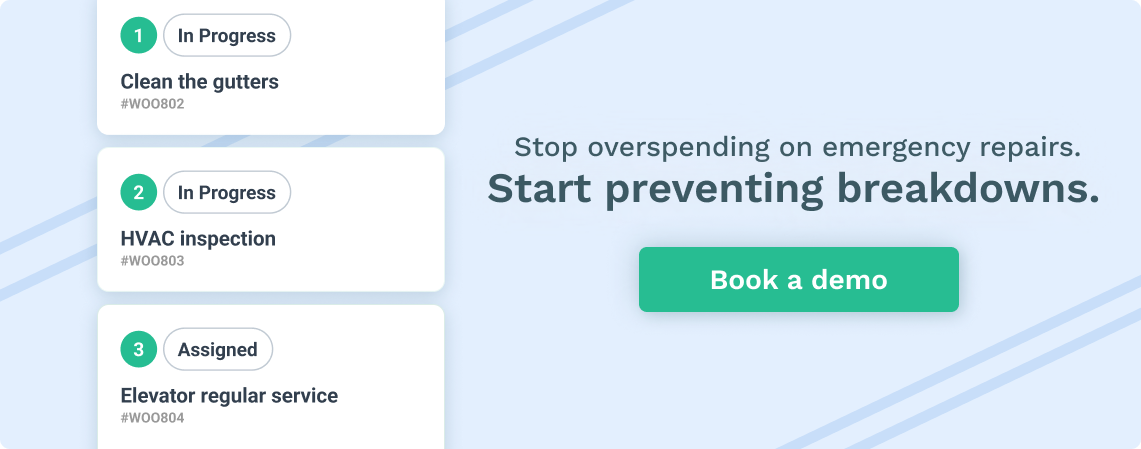
Executing a Run-to-Failure Strategy
To use run-to-failure effectively:
- Choose suitable assets
- Plan for quick replacements
- Stock spare parts
- Train staff on rapid response
Planned breakdowns can be part of this strategy. Teams prepare for eventual failures, ensuring minimal disruption when they occur.
It’s crucial to monitor asset performance. This helps predict likely failure times and plan accordingly.
Evaluating the Asset Lifespan
Understanding equipment breakdown patterns is key to run-to-failure maintenance.
Teams track:
- Average time between failures
- Typical signs of wear
- Cost of replacement vs. ongoing maintenance
- Machine breakdowns
- Productive capacity
- Equipment breakdowns
This data helps decide if run-to-failure is cost-effective. For some assets, it can save up to 50% compared to regular preventive maintenance.
Regular reviews ensure the strategy remains viable. As equipment ages or production needs change, different maintenance approaches may become necessary.
Strategic Considerations
Choosing the right maintenance approach is crucial for business success. It affects costs, safety, and operational efficiency. Let’s explore key factors to consider.
Choosing Between Maintenance Approaches
Reactive maintenance is best for non-critical systems with low downtime costs. It’s simple and requires less planning. For critical equipment, preventive or predictive maintenance may be better.
These proactive methods can reduce breakdowns and extend asset life. They often cost more upfront but save money in the long term.
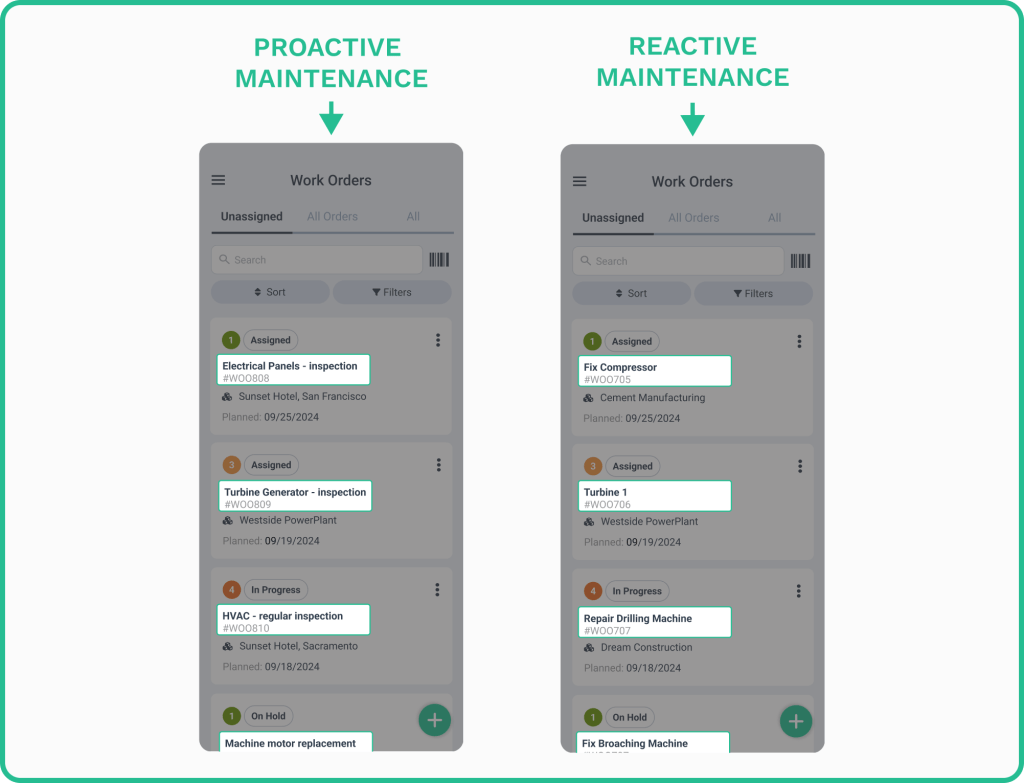
The choice depends on equipment value, failure impact, and budget. A mix of strategies often works best. Critical machines need proactive care, while less important items can use reactive maintenance.
Balancing Short-Term and Long-Term Costs
Reactive maintenance seems cheap at first, as it avoids regular upkeep costs. But it can lead to higher long-term costs.
Sudden breakdowns cause production stops. Emergency repairs are expensive. Equipment may need early replacement.
Proactive maintenance costs more initially. It includes regular checks and part replacements. But it can save money over time by:
- Reducing major breakdowns
- Extending equipment life
- Improving efficiency
- Lowering energy use
Companies must weigh immediate savings against future benefits.
Safety and Compliance Issues
Safety risks are a big concern with reactive maintenance. Sudden failures can cause accidents or injuries.
Some industries have strict maintenance rules. Reactive strategies that do not meet these standards may result in fines or legal issues.
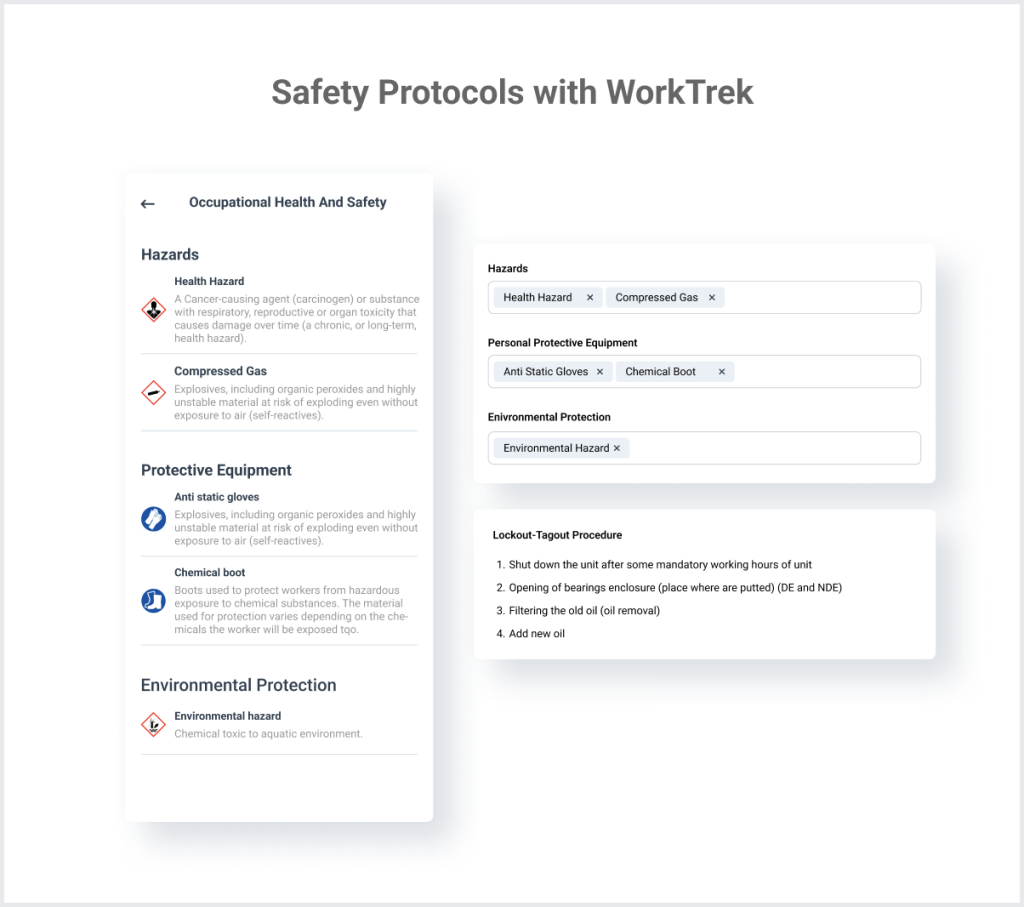
Proactive maintenance helps ensure safety. It catches problems early, reduces accident risks, and keeps operations in compliance with regulations.
Regular inspections also create a paper trail. This can be important for audits or investigations.
Safety should be a top priority in maintenance decisions. The cost of an accident often far outweighs prevention expenses.
Case Studies and Real-world Applications
Reactive maintenance plays a key role in many industries. Companies have learned important lessons from using this approach.
- Reactive maintenance can be a suitable strategy for low-cost, non-critical assets that will not interrupt normal business processes when they break down.
- Smaller organizations with limited resources may find reactive maintenance more feasible, especially when the initial costs of preventive or predictive strategies are prohibitive.
- The National Institute of Standards and Technology (NIST) research indicates that, on average, 45.7% of machinery maintenance is reactive.
- Reliability-centered maintenance (RCM) suggests that less than 10 percent of maintenance should be reactive, implying that reactive maintenance still has a place within a well-balanced maintenance strategy.
Lessons Learned from Reactive Maintenance
Many companies have found that the disadvantages of reactive maintenance include higher overall maintenance costs.
Reactive maintenance can be effective for small, cheap items but risky for critical equipment. A factory learned this when a key machine failed, stopping all work for days.
Consider using a hybrid approach, like many businesses have done, to reduce upfront costs.
Perform planned maintenance on important machines but use reactive maintenance for less crucial items.
Proper tracking of repairs is key. Implement a CMMS system to help track all your repair activities.
This helps spot patterns and decide which items need more care.
Conclusion
Reactive maintenance is a straightforward approach that addresses equipment failures as they occur. While it offers benefits such as reduced initial costs and simplicity, it also presents challenges like unplanned downtime and potential safety risks.

This maintenance strategy is best suited for non-critical assets where the cost of downtime is minimal. However, relying solely on reactive maintenance can increase long-term costs and reduce equipment lifespan.
Many businesses successfully integrate reactive maintenance with proactive preventive and predictive maintenance approaches to optimize maintenance efforts.
By doing so, companies can ensure critical equipment receives the necessary care to prevent unexpected failures while managing costs effectively for less essential assets.
Ultimately, the key to a successful maintenance program is balancing different strategies to meet specific operational needs and ensure efficiency and safety across all maintenance activities.