Get a Free WorkTrek Demo
Let's show you how WorkTrek can help you optimize your maintenance operation.
Try for freeUnexpected equipment failures drain your budget, halt production, and create chaos. Without a proper maintenance strategy, you’re constantly fighting fires instead of preventing them.
The cost of poor maintenance extends far beyond repair bills. Every minute of downtime erodes your bottom line, damages customer relationships, and stresses your team unnecessarily. Can your business afford to keep gambling with reactive maintenance?
Implementing these eight proven maintenance management practices and maintenance management software can transform equipment reliability, extend asset lifecycles, reduce potential equipment failures, and significantly reduce operational costs.
Discover how leading organizations save 20-30% on maintenance expenses while boosting production capacity by up to 25%.
Key Takeaways
- A well-structured maintenance plan with prioritized assets helps organizations maximize equipment reliability, reduce costs, and add overall operational efficiency.
- Implementing a CMMS solution like WorkTrek centralizes maintenance data, improves maintenance processes, and leads to operational excellence.
- Making employees accountable and setting specific goals ensures continuous improvement in maintenance operations and leads to cost efficiency.
Understanding Maintenance Management
Maintenance management and proactive maintenance strategies systematically coordinate activities to keep equipment, facilities, and infrastructure operating efficiently.
It encompasses planning, scheduling, and tracking maintenance tasks to prevent breakdowns and extend asset lifecycles.
Defining Maintenance Management
Maintenance management is the process of organizing, planning, and controlling maintenance activities to ensure optimal equipment performance and facility functionality.
It includes various preventive, predictive, and reactive maintenance approaches to improve asset performance.
A good maintenance management system helps track work orders, manage inventory, and document maintenance history.
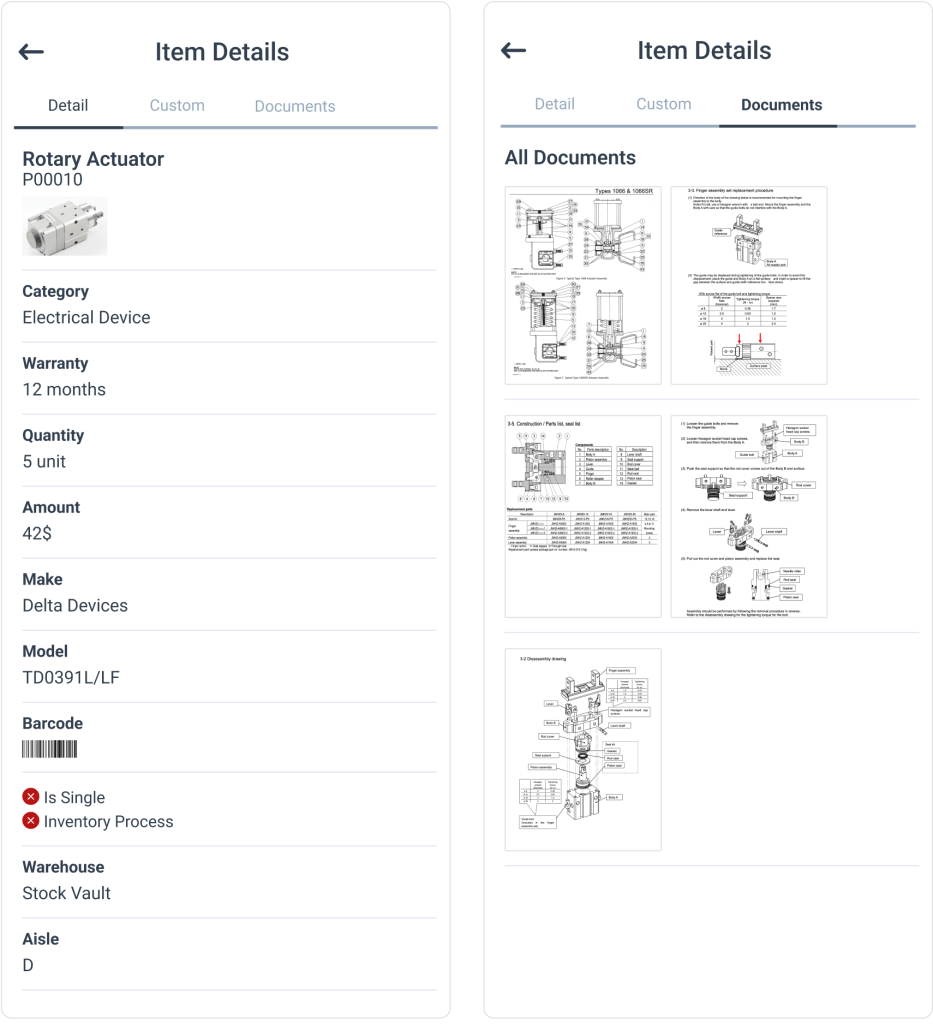
Computerized Maintenance Management Systems (CMMSs) are commonly used to streamline these processes and minimize downtime.
Effective maintenance strategies and management require:
- Clear documentation of procedures
- Proper resource allocation
- Strategic maintenance schedules
- Continuous monitoring of equipment performance
- Preventive maintenance program
- Preventive maintenance schedule
Maintenance management creates a structured approach that minimizes disruptions and maximizes operational efficiency when implemented correctly.
Importance of Maintenance in Operations
Proper maintenance impacts an organization’s bottom line by reducing costly emergency repairs and extending asset lifespans.
Equipment failure can halt production, creating expensive downtime that affects customer satisfaction and revenue.
Maintenance also plays a crucial role in safety compliance and risk management. Well-maintained equipment poses fewer hazards to workers and the environment.
According to industry experts, organizations that implement effective maintenance practices typically experience:
- 20-30% reduction in maintenance costs
- 35-45% decrease in downtime
- 20-25% increase in production capacity
Maintenance affects quality control as well. Equipment operating at optimal performance produces more consistent output with fewer defects and less waste.
This quality consistency builds customer trust and strengthens market position.
Developing a Maintenance Strategy
A well-crafted maintenance strategy serves as the foundation for effective maintenance management. It provides a clear direction for maintenance activities and helps organizations allocate resources efficiently.
Aligning Maintenance with Business Goals
Maintenance strategies must directly support the organization’s business objectives.
Start by identifying key performance indicators (KPIs) that matter most to your operation, such as equipment uptime, production output, or quality metrics.
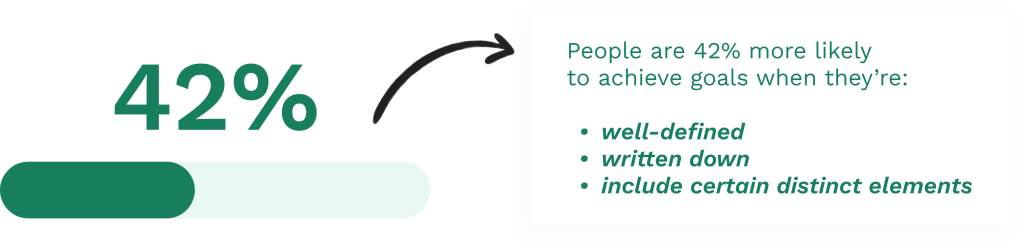
Critical alignment factors:
- Financial targets (cost reduction, ROI)
- Production requirements
- Safety and compliance standards
- Asset lifecycle management
- Asset reliability
- Improving equipment efficiency
One suggestion we’ve seen succeed is if department leaders meet quarterly to ensure maintenance priorities reflect changing business needs.
This alignment prevents maintenance from operating in isolation and transforms it into a strategic business function.
Don’t forget to communicate these goals clearly to maintenance teams so they understand how their work contributes to organizational success. Regular performance reviews against these metrics help identify gaps and improvement opportunities.
Predictive vs. Preventive Maintenance
Organizations must determine the right balance between predictive and preventive maintenance approaches for different assets.
Preventive maintenance strategies follow fixed schedules based on time or usage intervals. It works well for:
- Equipment with predictable wear patterns
- Assets with clear manufacturer guidelines
- Systems where failures create safety hazards
Predictive maintenance strategies use condition monitoring to perform maintenance only when needed. It excels with:
- Critical equipment where downtime is costly
- Assets with variable usage patterns
- Systems with detectable failure indicators
Predictive maintenance requires access to a lot of repair and equipment data and potentially specialized software.

Implementing both approaches typically yields the best results. Use data analysis to determine which assets benefit most from each strategy.
Modern CMMS solutions offer a good balance so that you can track effectiveness and optimize your maintenance mix.
Incorporating Reliability-Centered Maintenance
Reliability-Centered Maintenance (RCM) focuses on identifying and addressing the most critical failure modes that impact system functions.
The RCM process involves:
- Identifying system functions
- Determining potential functional failures
- Analyzing failure modes and effects
- Selecting optimal maintenance tasks
This systematic approach ensures maintenance efforts focus on failure prevention rather than just equipment repair. RCM helps maintenance teams move beyond reactive practices by targeting the root causes of equipment failures.
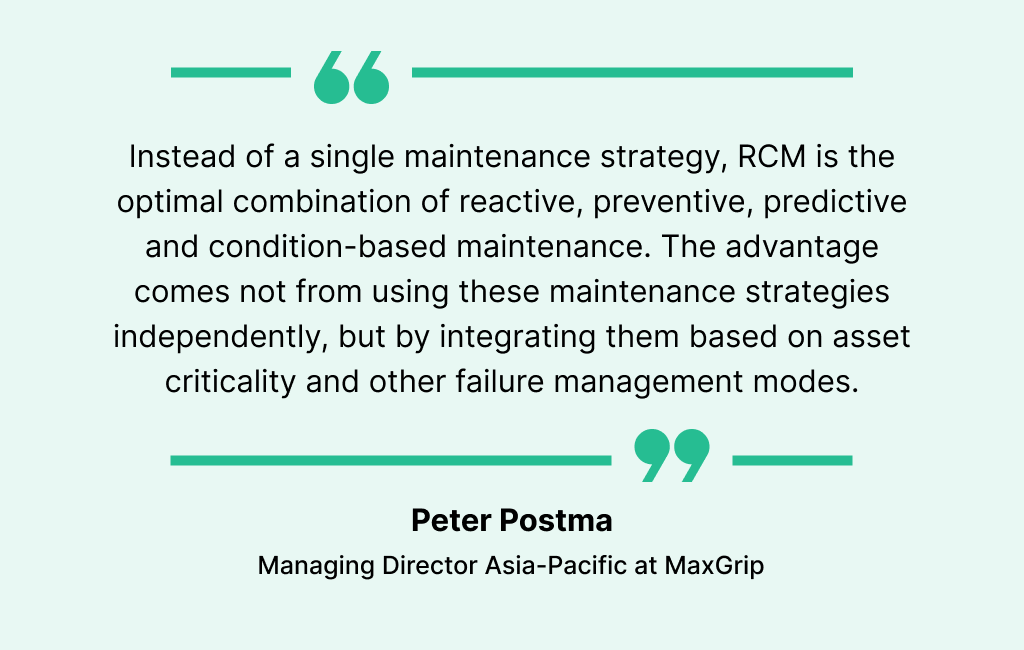
To implement RCM effectively, create cross-functional teams including operators, maintenance technicians, and engineers.
Their combined expertise helps identify critical failure modes that might otherwise be overlooked.
RCM implementation typically results in fewer catastrophic failures, extended equipment life, and more efficient resource allocation.
Implementing Maintenance Best Practices
Use and implement proven practices before implementing a maintenance management process. Organizations that systematically apply these methods consistently achieve better equipment reliability and operational efficiency.
Standardizing Processes
Start with standardizing your processes. Standardization serves as the foundation for effective maintenance operations.
Implementing a Computerized Maintenance Management System CMMS solution helps centralize maintenance data and standardize department workflows. This technology ensures the consistent execution of maintenance tasks.
Standard Operating Procedures (SOPs) eliminate guesswork and reduce errors. Maintenance teams should document each critical process with step-by-step instructions, including safety protocols and required tools.

Key elements of standardization include:
- Detailed maintenance checklists
- Clear documentation formats
- Consistent naming conventions for equipment
- Standardized work order procedures
- Maintenance workflows
Review these standards regularly. Consider all of the practices and evaluate their effectiveness regularly.
One good guideline is to evaluate these processes every quarter with the team and measure their effectiveness.
Routinely Training Maintenance Staff
Continuous skill development directly impacts maintenance quality.
Investing in training ensures technicians can effectively maintain increasingly complex equipment and systems.
Training should address both technical skills and procedural knowledge. New staff require comprehensive onboarding that covers system operations, documentation protocols, and safety requirements.
Effective training approaches include:
- Hands-on demonstrations with experienced technicians
- Equipment-specific certifications
- Regular refresher courses on critical systems
- Cross-training to build versatile skill sets
Maintenance departments should maintain training records to track skill development and identify knowledge gaps. Using a CMMS system like WorkTrek will simplify document tracking.
This documentation helps create personalized development plans for each team member.
Optimizing Workflow and Schedules
Strategic scheduling maximizes productivity while ensuring all assets receive appropriate attention. Developing a maintenance plan with clear priorities prevents resource conflicts and reduces emergency repairs.
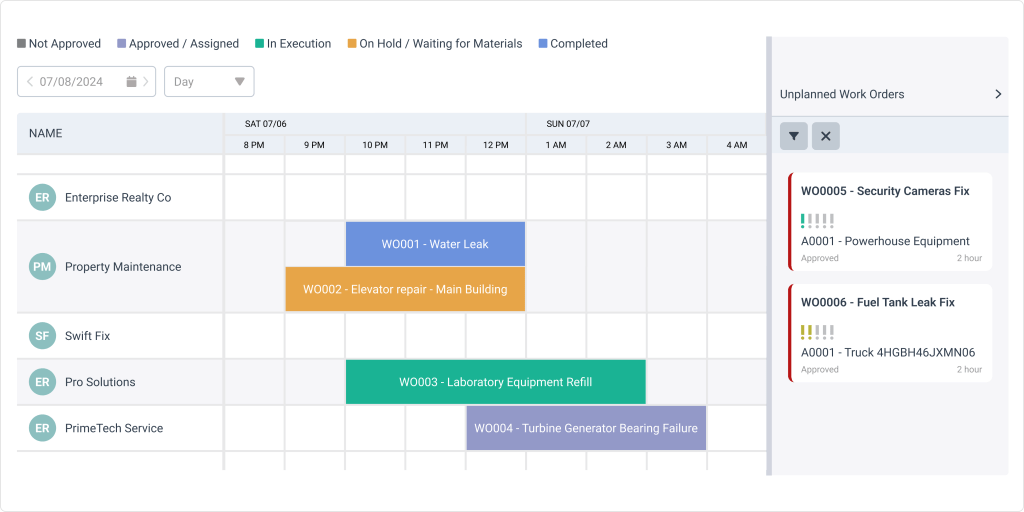
To start, prioritize your assets. Critical equipment directly impacting production should receive the highest maintenance priority, with appropriate frequency and thoroughness.
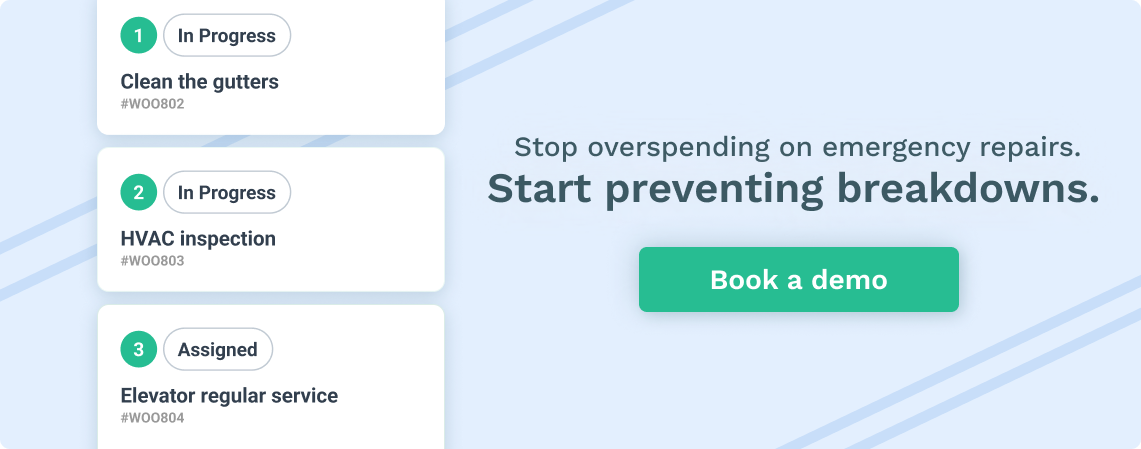
Maintenance managers should analyze work order completion times to identify inefficiencies. This data highlights opportunities to reallocate resources, adjust schedules, or modify procedures for better outcomes.
Workflow optimization strategies include:
- Grouping similar maintenance tasks
- Scheduling preventive work during planned downtime
- Balancing workloads across all technicians
- Centralizing vendor management to streamline external support
Regular schedule reviews are crucial for continuous improvement.
Monthly assessments help identify recurring issues and refine the maintenance calendar.
Leveraging Maintenance Software
Modern maintenance management depends heavily on software solutions that streamline operations and provide valuable data insights.
The right software tools can transform maintenance from reactive to proactive while reducing costs and equipment downtime.
Choosing the Right Maintenance Software
When selecting maintenance software, focus on your organization’s needs rather than the most popular options.
Implement a CMMS solution that matches your facility size, asset complexity, and team capabilities.
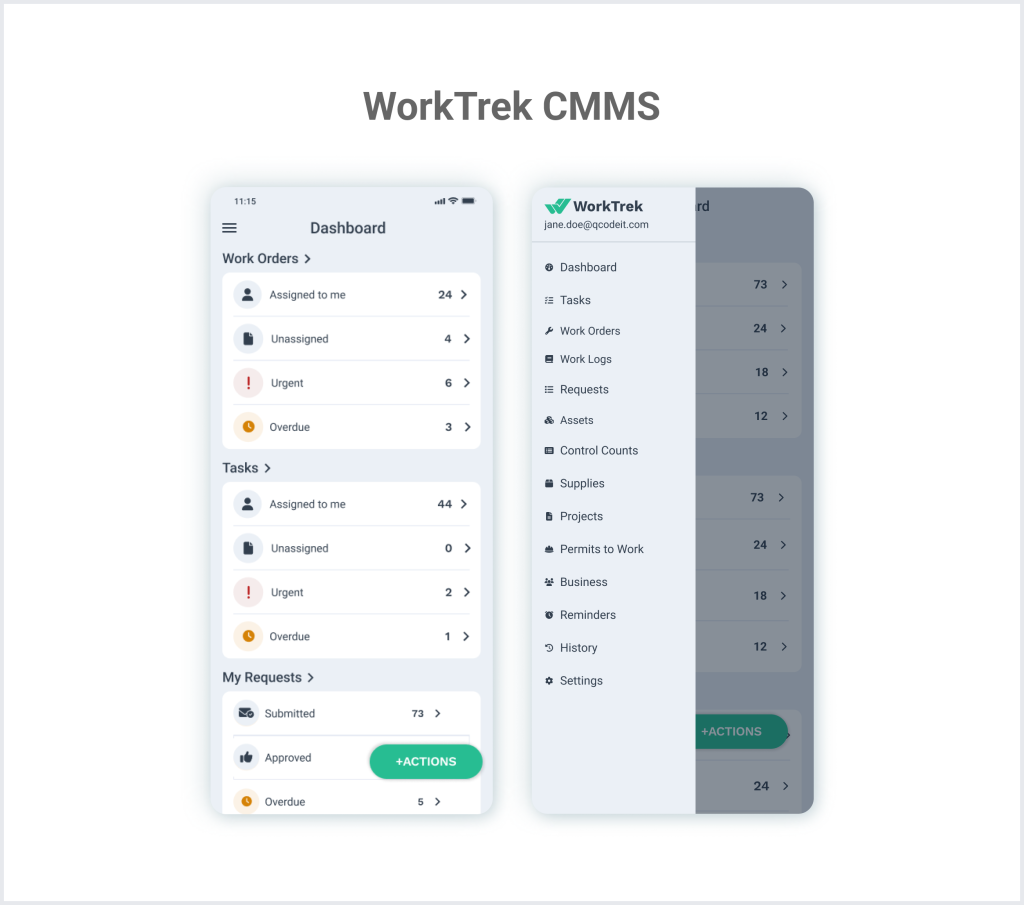
Consider these key factors:
- User-friendliness – Software should be intuitive for your maintenance team
- Scalability – Can it grow with your organization?
- Mobile accessibility – Field technicians need on-the-go access
- Technical support – Reliable vendor assistance is crucial
Demo several options before deciding. Check if the software offers customizable reporting features that align with your KPIs. Ensure the solution provides adequate security for your operational data.
Maximizing the Use of CMMS
A CMMS delivers value only when properly utilized. When implementing your system, gather input from various departments, including maintenance teams, IT, and management.
Effective CMMS usage requires:
- Comprehensive asset and equipment inventories
- Regular data updates and maintenance
- Proper staff training on all features
- Setting up automated preventive maintenance schedules
To encourage consistent use, make data entry simple for technicians and use the reporting functions to identify maintenance trends and problem areas.
Embrace preventive maintenance schedules through your CMMS to reduce emergency repairs.
Set up automated alerts for critical maintenance tasks to ensure nothing is overlooked.
Integrating with Other Systems
Maintenance software delivers maximum value when it communicates with other business systems. Integration eliminates data silos and provides a more complete operational picture.
Key integration points include:
- Inventory management – Automatic parts ordering when stocks run low
- Purchasing systems – Streamlined procurement processes
- Energy management systems – Correlate maintenance with energy efficiency
- Asset management software – Complete lifecycle tracking
- Enterprise Resource Planning Software – Manage financials
APIs (Application Programming Interfaces) facilitate these connections between systems. Ask software vendors about pre-built integrations or open APIs with your existing systems.
Foster a culture of continuous improvement by regularly reviewing how well your integrated systems function together.
Schedule periodic reviews to identify new integration opportunities that enhance maintenance operations.
Managing Maintenance Data
Data forms the backbone of effective maintenance management. Properly collected and analyzed information enables better decision-making, resource allocation, and performance tracking across maintenance operations.
Tracking Key Performance Indicators
Maintenance KPIs provide measurable values that show how effectively a facility meets its maintenance objectives. The eight essential maintenance management indicators include equipment availability, mean time between failures, and maintenance costs.

Key maintenance KPIs to track:
- Equipment downtime percentage
- Preventive maintenance compliance
- Work order completion rate
- Maintenance backlog
- Mean time to repair (MTTR)
Most modern CMMS systems make KPI tracking more efficient. These systems automatically collect and organize maintenance data, generating reports highlighting improvement areas.
Regular KPI reviews help maintenance teams identify emerging issues before they escalate into costly problems.
Analyzing Maintenance Records
Maintenance records provide valuable insights into equipment performance trends and maintenance effectiveness. These records should include repair histories, part replacements, and technician notes.
When analyzing maintenance records, look for:
- Recurring failures on specific equipment
- Patterns in breakdown timing or conditions
- Variations in repair times among technicians
- Parts that frequently need replacement
Standardizing record formats ensures consistent data collection. Effective maintenance management requires detailed records that go beyond simple work order completion.
Digital record systems allow faster searching and better pattern recognition than paper-based systems. They also facilitate information sharing across departments and shifts.
Using Data for Continuous Improvement
Maintenance data drives continuous improvement by identifying inefficiencies and opportunities. Creating a culture of continuous improvement starts with using data to establish baseline performance.
Data-driven improvement strategies:
- Set up regular performance review meetings
- Create action plans based on KPI trends
- Test and measure results of maintenance strategy changes
- Share success stories to motivate the team
Predictive maintenance relies heavily on quality data. Maintenance teams can predict when equipment might fail by analyzing performance patterns and scheduling interventions before breakdowns occur.
Data visualization tools help communicate complex information to stakeholders. Simple charts and graphs can reveal trends that might be missed in spreadsheets or text reports.
Remember that data quality matters more than quantity. Focus on collecting accurate, relevant information rather than overwhelming the team with excessive metrics.
Ensuring Regulatory Compliance
Regulatory compliance forms the backbone of effective maintenance management. Clear documentation and standardized procedures help organizations avoid penalties while maintaining safe and efficient operations.
Staying Informed on Regulations
Maintenance departments must actively track industry regulations that affect their operations. This requires:
- Designating compliance officers responsible for monitoring regulatory changes
- Subscribing to industry newsletters from governing bodies
- Joining professional associations that provide regulatory updates
- Attending regular training sessions on compliance requirements
Create a regulatory tracking system that categorizes requirements by department, equipment type, and deadline. This helps prioritize which regulations need immediate attention.
Regular team meetings to discuss regulatory changes ensure everyone stays informed. These meetings should cover potential impacts on current procedures and necessary adjustments.
Maintaining Compliance Records
Document management is the cornerstone of adhering to regulatory standards. Well-defined policies and procedures help ensure compliance with regulations and standards.
Essential documentation includes:
- Equipment maintenance logs
- Training certifications
- Inspection reports
- Safety incident records
- Corrective action documentation
A CMMS solution can centralize and automate documentation. This technology reduces manual record-keeping and minimizes human error.
Establish standardized formats for all compliance documents. This consistency makes information easier to locate during audits or inspections.
Store records according to retention requirements vary by industry and document type. Always maintain backups of critical compliance documentation.
Regular Audits and Inspections
Proactive auditing prevents compliance issues before they become serious problems.
Setting up a calendar to track inspection dates helps avoid missed checks and keeps facilities compliant. This can also be easily managed in a CMMS system.
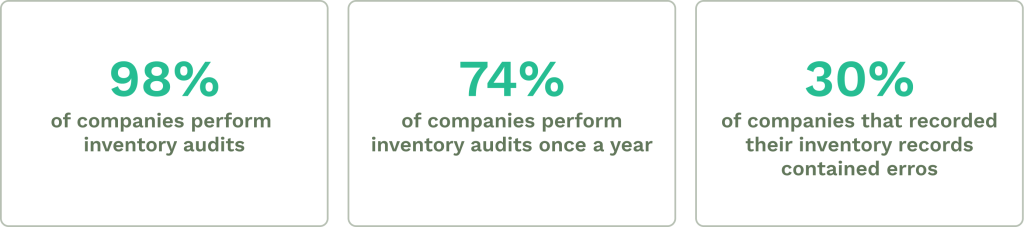
Develop a structured audit schedule that includes:
- Daily visual inspections of critical equipment
- Weekly safety checks of high-risk areas
- Monthly compliance reviews of documentation
- Quarterly comprehensive audits of all maintenance systems
Train auditors to identify both technical violations and procedural shortcomings. Their findings should be documented in standardized reports.
After each audit, create action plans with specific tasks, responsible parties, and completion deadlines. Follow up consistently to ensure issues are resolved promptly.
Consider using third-party auditors periodically to provide unbiased assessments of compliance status. External perspectives often identify blind spots internal teams might miss.
Budgeting for Maintenance
Creating a realistic maintenance budget helps organizations control costs while keeping equipment running smoothly.
Estimating Maintenance Costs
Accurate cost estimation forms the foundation of any maintenance budget. Start by analyzing historical maintenance data to identify spending patterns and trends for each asset.
Many maintenance professionals follow the asset-based budgeting approach, which allocates funds based on equipment importance and condition. This method ensures that critical assets receive appropriate financial attention.
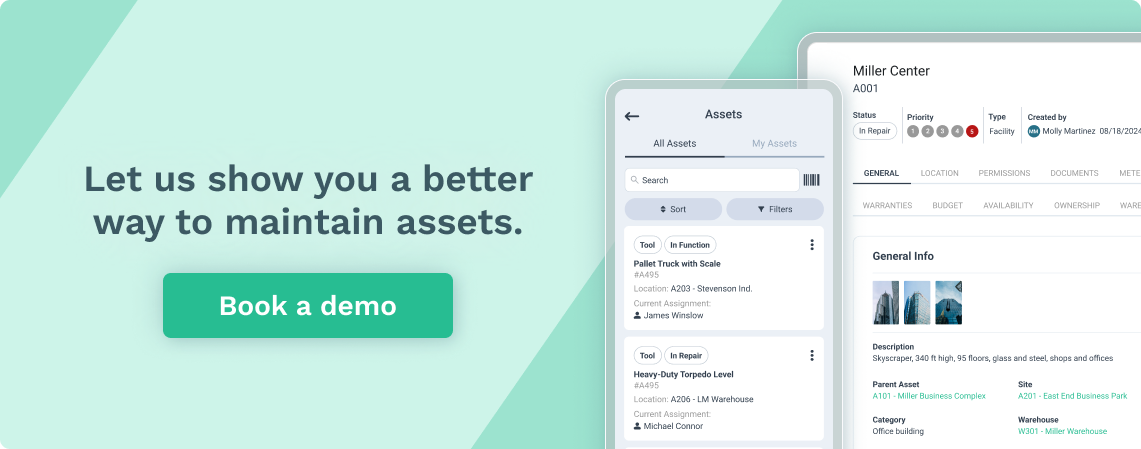
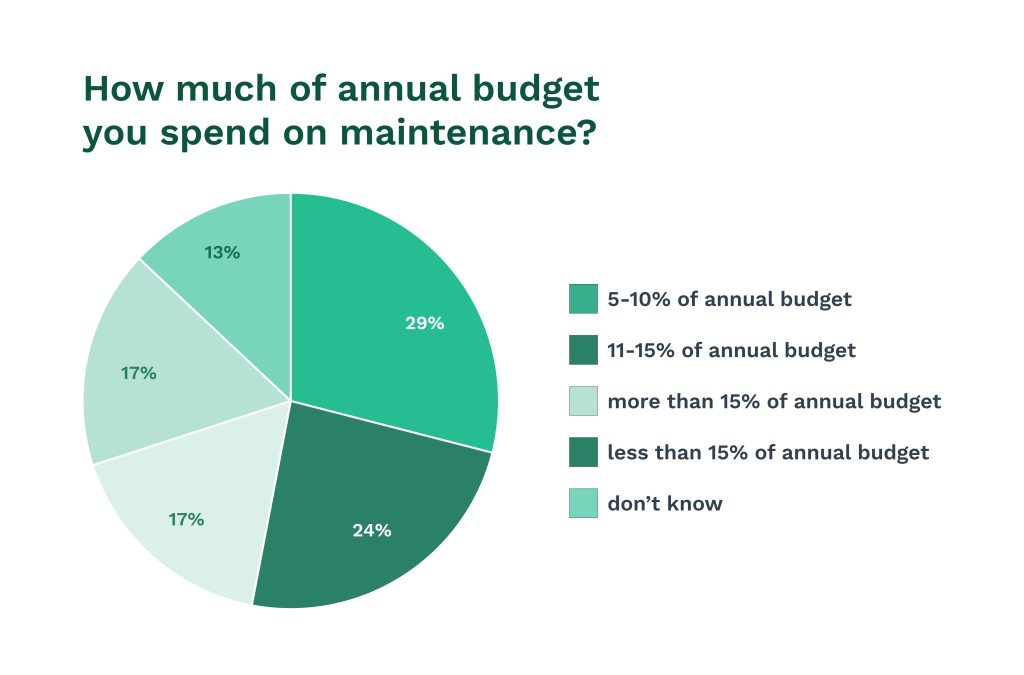
Manufacturers’ recommendations provide initial maintenance cost estimates for new equipment. When projecting total expenses, factor in labor costs, spare parts inventory, and contractor services.
A good rule of thumb for building maintenance is to budget 1-3% of the facility’s replacement value annually. Equipment-heavy industries often require higher percentages.
CMMS systems can help track actual costs against projections, enabling more accurate future budgeting.
Allocating Resources Effectively
Prioritization is essential when allocating maintenance resources. Categorize assets based on criticality to operations and potential failure impact.
Resource Allocation Priority Matrix:

Standardizing maintenance processes across departments eliminates redundancy and reduces waste. To lower long-term costs, consider shifting from reactive to preventive maintenance.
Training maintenance staff on budget awareness encourages cost-conscious decisions. Empower technicians to identify potential savings without compromising quality.
Regular budget reviews (quarterly at minimum) allow for adjustments based on changing conditions and maintenance needs.
Planning for Unexpected Repairs
Even the best maintenance programs face unexpected breakdowns. A contingency fund is essential for handling these situations without derailing the entire budget.
Financial experts recommend setting aside 10-15% of your total maintenance budget for emergency repairs. This creates a financial buffer that prevents funds from being pulled from other critical maintenance activities.
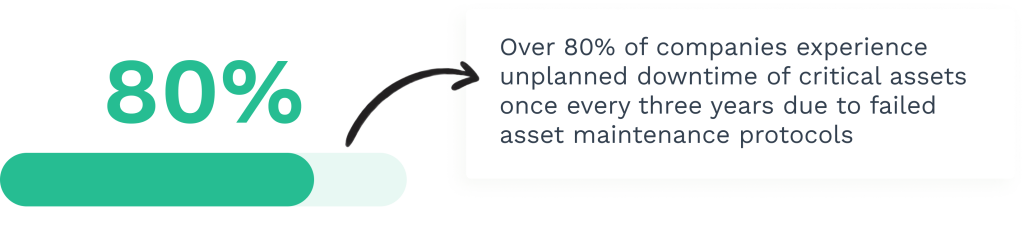
CMMS software helps stretch maintenance budgets during unexpected situations by identifying the most cost-effective repair options. It also tracks repair histories to help prevent similar failures.
Consider maintenance insurance or service contracts for highly specialized equipment where emergency repairs could be exceptionally costly.
Develop clear approval processes for accessing emergency funds to ensure they’re used appropriately. Quick response times to failures often minimize total repair costs and operational disruptions.
Continuous Improvement in Maintenance
Like all other activities, don’t forget to focus on continuous improvement in your maintenance management program.
This can lead to better efficiency, reduced costs, and extended asset lifespans.
Implementing structured feedback loops and suggestion boxes and staying current with industry developments ensures maintenance practices evolve with organizational needs.
Soliciting Staff Feedback
Maintenance technicians do the work and know the equipment well. They often have valuable insights about equipment issues and process inefficiencies.
Creating formal channels for this feedback can uncover improvement opportunities that management might miss.
A simple feedback system might include:
- Daily huddles (5-10 minutes) to address immediate concerns
- Monthly review sessions to analyze recurring issues
- Digital suggestion platforms where ideas can be submitted anytime
Rewarding valuable contributions encourages ongoing participation. This might involve recognition programs or incentives for implemented ideas that yield measurable improvements.
Track which suggestions lead to improvements and share these successes with the team. This reinforces the value of their input and encourages continued engagement.
Adapting to Technological Advances
Maintenance technology evolves rapidly, with new tools and systems offering significant efficiency gains. Organizations must regularly evaluate new technologies against current maintenance needs.
CMMS forms the backbone of modern maintenance operations.
Implementing a CMMS solution helps track work orders, schedule preventive maintenance, and analyze performance data.
Emerging technologies worth monitoring include:
- IoT sensors for real-time equipment monitoring
- AI-powered predictive analytics to forecast failures
- Mobile applications for field technicians
- Augmented reality for remote troubleshooting
Budget for regular technology training. Even the best maintenance technologies fail without proper user adoption. Develop a systematic approach to evaluate new tools against specific maintenance challenges.
Create a technology roadmap that plans implementations over 1-3 years rather than attempting wholesale changes simultaneously.
Benchmarking Against Industry Standards
Comparing maintenance performance against industry benchmarks reveals improvement opportunities and validates current practices.
Key performance indicators (KPIs) provide objective measures for this assessment.
Essential maintenance KPIs to track include:

Join industry associations to access benchmark data specific to your sector. These organizations often publish reports with average performance metrics.
Prioritize maintenance assets based on criticality to focus improvement efforts where they’ll have the most significant impact.
This targeted approach yields better results than trying to improve everything simultaneously.
Conduct regular audits comparing your organization’s performance against established benchmarks. Document findings and create specific action plans to address gaps.
Conclusion
Effective maintenance management is not just about fixing equipment—it’s about creating a sustainable system that protects business assets while controlling costs. Organizations can move from reactive firefighting to proactive maintenance excellence by implementing the strategies outlined in this article.
The most successful maintenance programs combine standardized processes, well-trained staff, appropriate technology solutions, and data-driven decision-making.
Remember that maintenance management is an ongoing journey rather than a destination. Continuous improvement should remain your north star, and regular performance evaluations should guide adjustments to your maintenance strategy.

Implement a CMMS solution to centralize information and strengthen work order management. Finally, foster a culture where maintenance is viewed as a value-adding business function rather than just a necessary expense.
With these practices in place, your organization will experience fewer disruptions, longer equipment lifespans, and a stronger bottom line.