Get a Free WorkTrek Demo
Let's show you how WorkTrek can help you optimize your maintenance operation.
Try for freeCMMS Reporting: Maintenance metrics and KPIs are essential elements to be able to monitor the performance of our assets and maintenance team. In this article, we offer a complete overview of the main metrics and KPIs, explaining how to choose them in relation to our goals and how to calculate them in the simplest way.
Stop Driving In The Dark
Imagine driving a car that doesn’t have a fuel gauge. Or that it lacks a speedometer. To know the speed at which you are going, you would be forced to count the kilometers covered one by one and divide the total by the time it took you to cover them. And even so, it would be an extremely approximate finding.
Now imagine driving this same car every day for eight hours. It would be total chaos, wouldn’t it? Continuously dry tank and speeding tickets would become the norm and all this because you are driving in the dark.
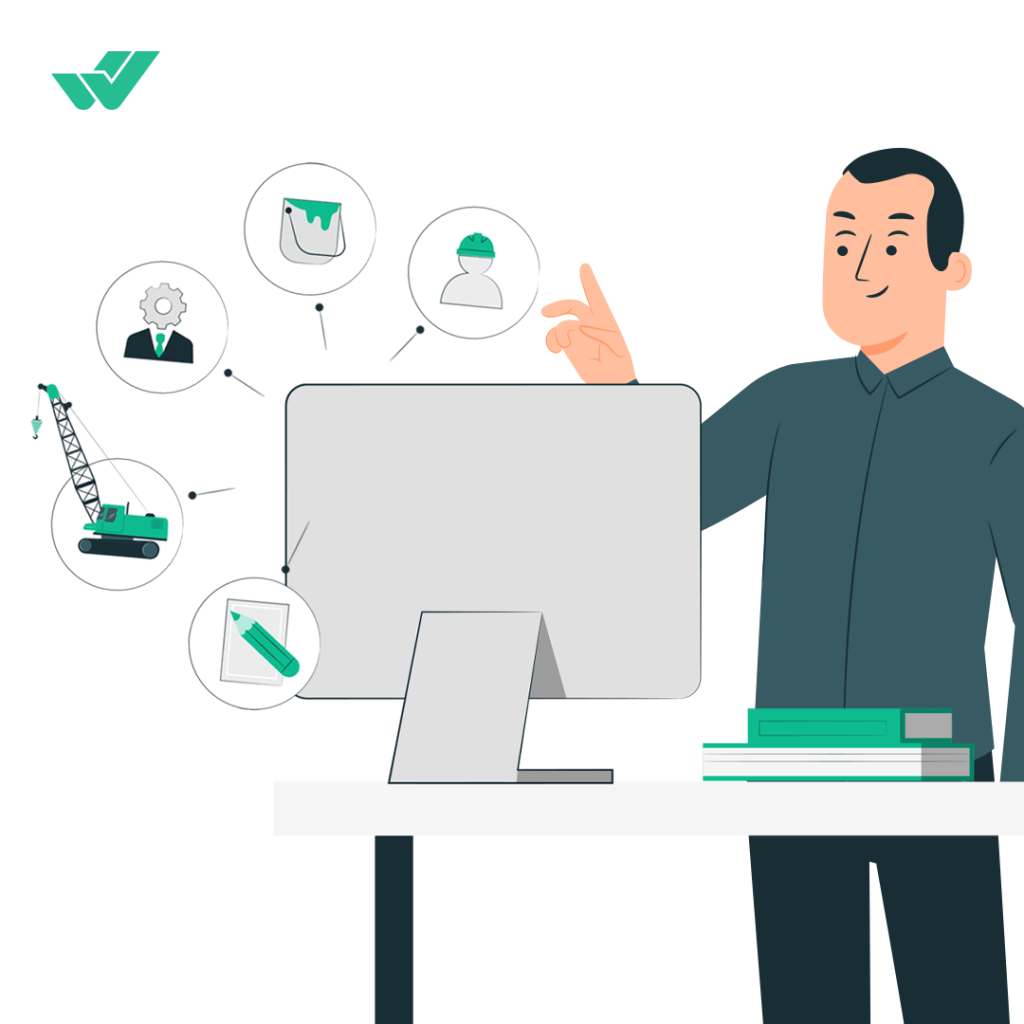
Here, now try to think of managing your plants, or even an entire facility in this way.
In short, it’s impossible to improve what you can’t measure.
Luckily, however, there are some metrics and KPIs that can help you, just like your car’s speedometer or fuel gauge, help you achieve success.
Maintenance metrics and KPIs allow you to shed light on every process and operation that takes place within your facility. The best part is that these metrics aren’t that complicated to calculate and track, at least if you have the right tool at your disposal, at the right time. However, is that – despite everything – today there are still many companies that do not bother to carry out this type of analysis seriously and constantly, often limiting themselves to acquiring approximate data and processing them inefficiently. This represents an excellent possibility to be able to acquire a competitive advantage over the competition.
What Is A Maintenance KPI: Data Anatomy
KPIs (key performance indicators) are performance indicators, i.e. measurements which, through their monitoring, give us a precise indication of our work with respect to the objectives we have set ourselves. We can thus measure the performance of a person, an asset, a process, or an entire company and how efficient they are in achieving the established objectives.
Maintenance, can for example be used to establish new strategies that minimize downtime, identify bottlenecks and inefficiencies, build better preventive maintenance plans, and optimize costs.
In other words, KPIs serve to show you the way to turn on the lights of your car, shedding light on the processes and helping you to design the fastest way to achieve the objectives you have chosen.
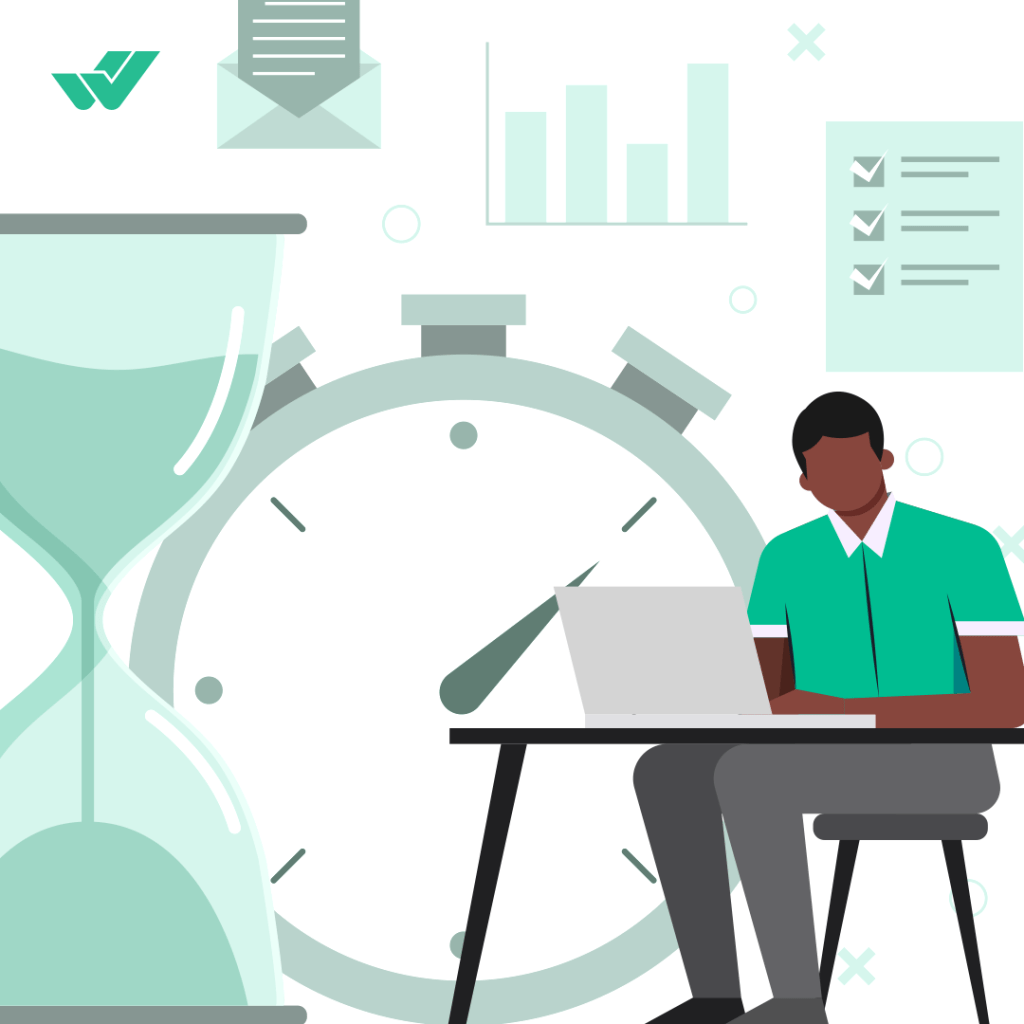
KPI vs. Maintenance Metrics: What Is The Difference?
Metrics and KPI maintenance are two terms often used interchangeably. In any case, there is a subtle difference between them.
Specifically, KPIs are numbers that we need to give a dimension to our progress in relation to the goals we have set. We need them to set a goal we want to strive for.
On the other hand, Metrics, are the building blocks with which we build KPIs and are used to connect our actions to the performance we want to monitor.
Example KPIs:
Let’s say your goal is to increase revenue at the end of the year. To achieve this, you will want to increase the volume of merchandise produced and sold.
However, production capacity is strictly influenced by the number of machine downtimes encountered. Therefore, one of the KPIs that you will be interested in monitoring will be the total number of machine downtimes or, even better, the total downtime for a specific plant.
All actions that are linked to this KPI and can be quantified, from the number of corrective maintenance interventions to the operational time between two failures, represent maintenance metrics to be monitored.
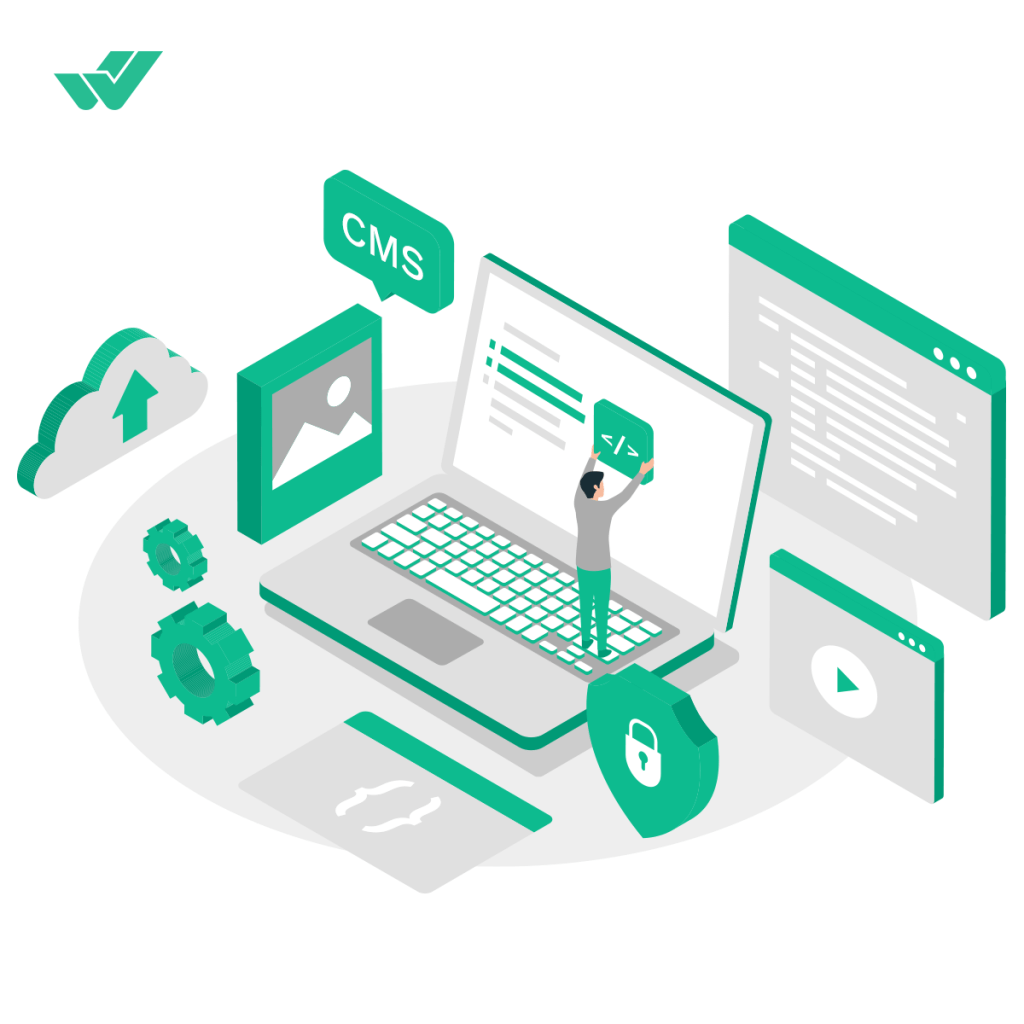
Adopt a logic of continuous improvement
You’ve no doubt heard of TPM – Total Productive Maintenance. But what does TPM have to do with monitoring business KPIs and maintenance metrics?
Like all active maintenance policies, the TPM tries to solve the problems related to the decrease in the performance of machines and plants and make the processes related to asset management more efficient. The ultimate goal of TPM is therefore to increase overall productivity by optimizing these processes.
How can you improve a process if you are not able to monitor it? Any action you take, without tangible feedback, does not allow you to clearly and precisely identify and separate what works from what does not.
Our approach to maintenance metrics and KPIs
Metrics and KPIs tell you a lot about the how and why behind each event, providing you with a valuable diagnostic tool aimed at improving your operations and the results of the entire company. But being able to monitor these performance indicators comes at a cost if only in terms of time and resources to devote to them. This is why it is important to be able to choose the KPIs that interest us and focus on them.
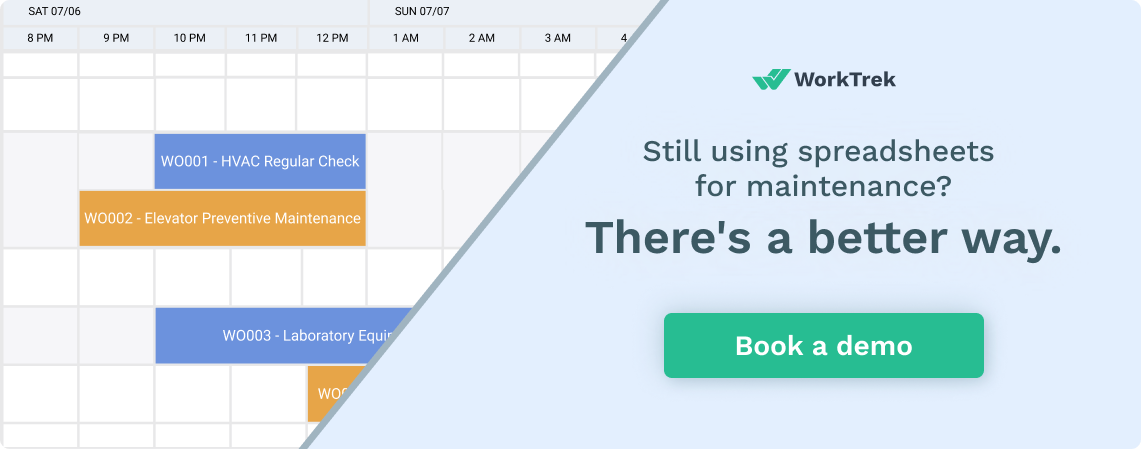
To choose which metrics and KPIs are right for you, you need to start with the final goals you intend to achieve.
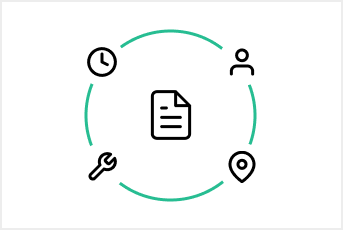
KPIs And Metrics To Track
Only you and your maintenance department can determine which KPIs are right for your organization and aligned with its strategic goals. But first, let’s look at a few common maintenance performance KPIs.
Maintenance Backlog and Overtime
A maintenance backlog is the accumulation of maintenance work that needs to be performed for safety reasons or to avoid failures. This KPI is critical because the more unfinished work, the greater the chance of severe and costly downtime.
The goal is to control the backlog both in day-to-day operations and in times of crisis.
If there are too many work orders pending, it is an indication that more employees need to be hired. On the other hand, having no backlog may indicate that you can reduce headcount too much.
Managers can track overtime to see if their department is overly reliant on reactive maintenance. This can lead to technician burnout, high maintenance costs, costly downtime, and reduced productivity.
Equipment downtime
Equipment downtime is any period of time when equipment is not operating. Because of preventive maintenance, is sometimes planned as part of an overall maintenance plan.
In other cases, however, unplanned downtime may occur and production may stop due to equipment failure or inoperability. While this scenario is more likely for companies that rely on reactive rather than preventive maintenance, in either case, the costs can add up quickly, with industry estimates at around $50 billion a year due to downtime.
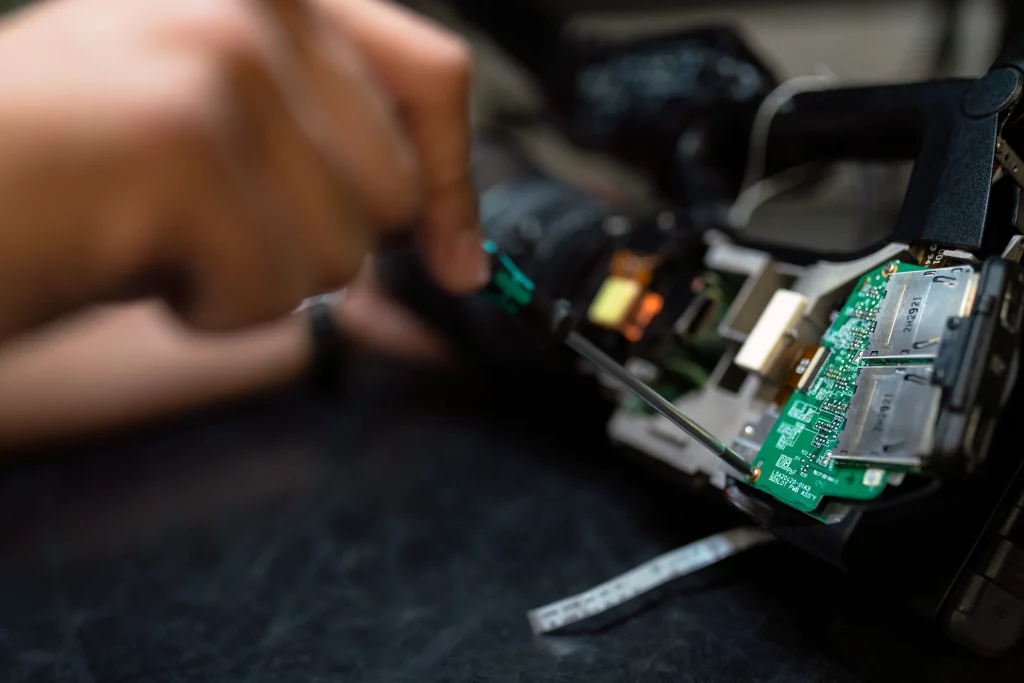
Mean Time To Repair (MTTR)
MTTR is the mean time it takes for failed equipment to recover and return to production. Accessing this metric gives you insight into how your organization needs to respond to planned repairs or unplanned equipment issues. EAM software can help you accurately calculate this metric.
Mean Time Between Failures (MTBF)
MTBF is the mean time between equipment failures. Measure this KPI for individual devices using CMMS software. It is one of the most effective ways to analyze asset reliability and predict its future performance.
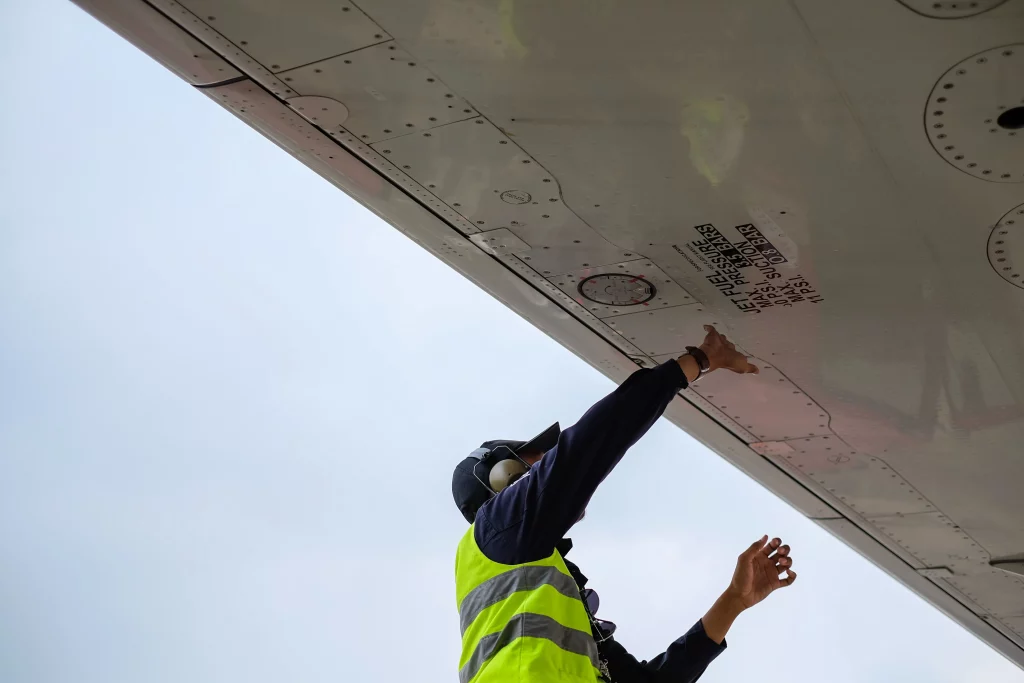
Overall Equipment Effectiveness (OEE)
This KPI looks at the overall performance of the facility. OEE is based on the availability of equipment, the efficiency of its overall performance, and the quality level of the final product. Other key figures often have to play a role in this measurement.
Percentage of Planned Maintenance (PMP)
The planned maintenance percentage is the percentage of hours spent on planned maintenance activities to the number of hours spent on unplanned maintenance activities. This metric is calculated by dividing the planned maintenance work hours by the total maintenance hours for a given maintenance period.
Completed work order
Work Orders Completed is a CMMS KPI that measures the number of work orders completed on time. This KPI is also used to calculate Preventive Maintenance Compliance (PMC). Completed work orders are typically measured daily, and this information is readily available in most CMMS systems.
Supercharge your business with WorkTrek CMMS
Book a WorkTrek demo to see how a CMMS can help your asset management.
Try for freeMetrics And KPIs Related To Service Management
KPIs and Service-related metrics are particularly suitable indicators for the Facility Management and Global Service sector, but not only.
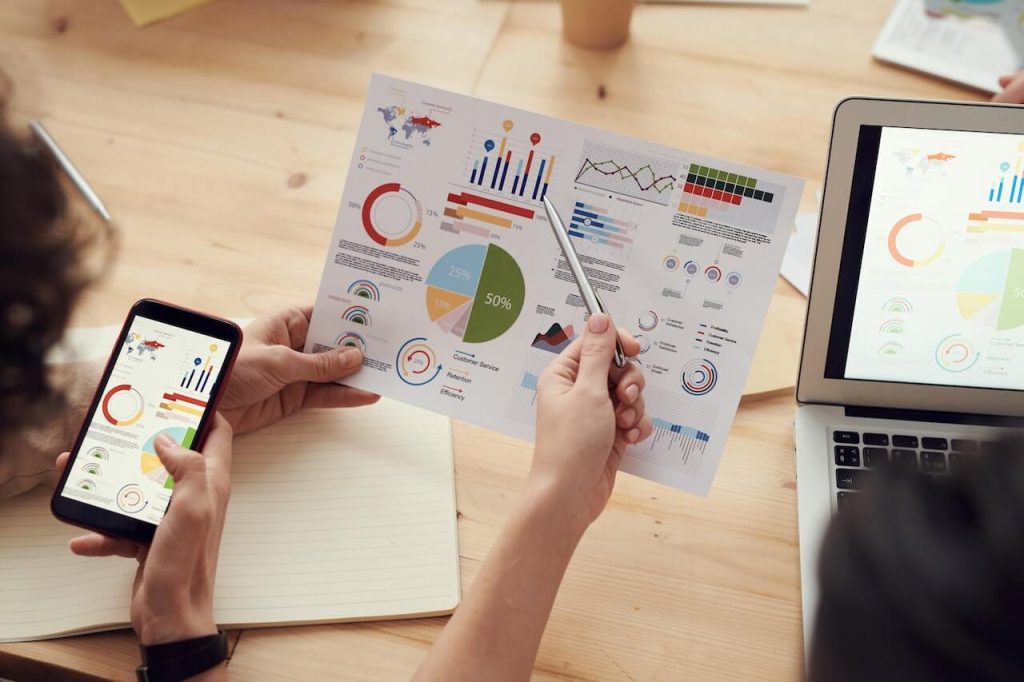
Through this group of KPIs, the maintenance manager will be able to answer questions such as:
- How efficient is the intervention request management system?
- How efficient is the management process of planned interventions?
- How many/which work orders are left unfinished?
- How much time elapses between the actual moment of the failure and its reporting?
- Does the management process have bottlenecks?
What are the maintenance KPIs related to Service Management?
- % of corrective Work Orders closed within a defined period
- % planned work orders closed within a defined period
- Maintenance backlog (number of work orders arrears)
- Work Order trends created: corrective maintenance vs. planned maintenance
- Work orders divided by group
- Work orders divided by category
Maintenance Metrics And KPIs Related To Asset Management
The second group, Asset Management, refers to metrics and KPIs whose main objective is to monitor a series of values that are typical of maintenance engineering. They are indicators that allow maintenance to be brought to a level of greater knowledge and professionalism, often used in industry and manufacturing environments where there are machinery and plants to monitor.
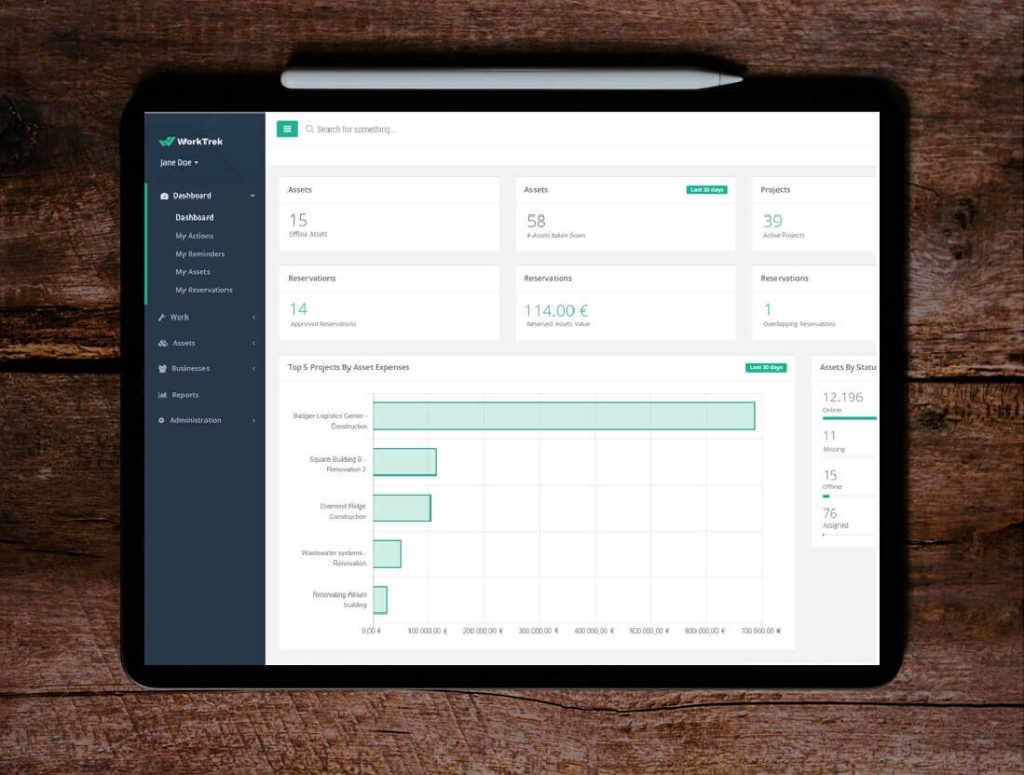
Through these indicators, you will be able to respond to surveys such as:
- How much time elapses between two consecutive anomalies on the same asset (MTBF)?
- How much time is required on average to resolve an anomaly on a specific asset (MTTR)?
- What are the assets that presented the most anomalies (Top Worst Asset)?
- What is the time of each single repair (MRT – Wrench Time)
What are the maintenance KPIs related to Asset Management?
- Mean Time Between Failures (MTBF)
- Mean Time To Repair (MTTR)
- Mean Time To Failure (MTTF)
- Mean Repair Time (MRT)
- Mean Time Between Maintenance (MTBM)
- Total number of machine stops
- Top Worst Assets
Maintenance Metrics And KPIs Related To Cost Control
The third group, Cost Control, refers to metrics and KPIs that aim to define the costs that affect maintenance. Costs can be dictated by the type of maintenance performed, the use of internal or external resources (suppliers, service companies), and the materials used.
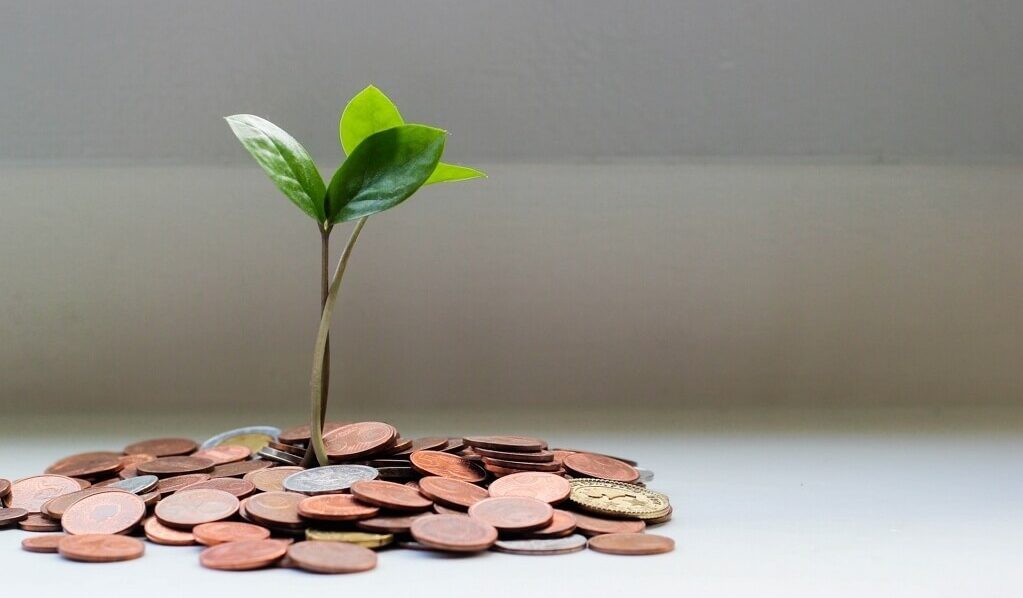
By analyzing these KPIs, it is possible to answer the following questions:
- How much did maintenance cost, during a given period, for a specific asset?
- How much labor has affected the total cost of maintenance?
- How much did the cost of spare materials affect the total cost?
These KPIs represent the final objective of carrying out maintenance but naturally require a certain accuracy in identifying the cost items associated with the interventions.
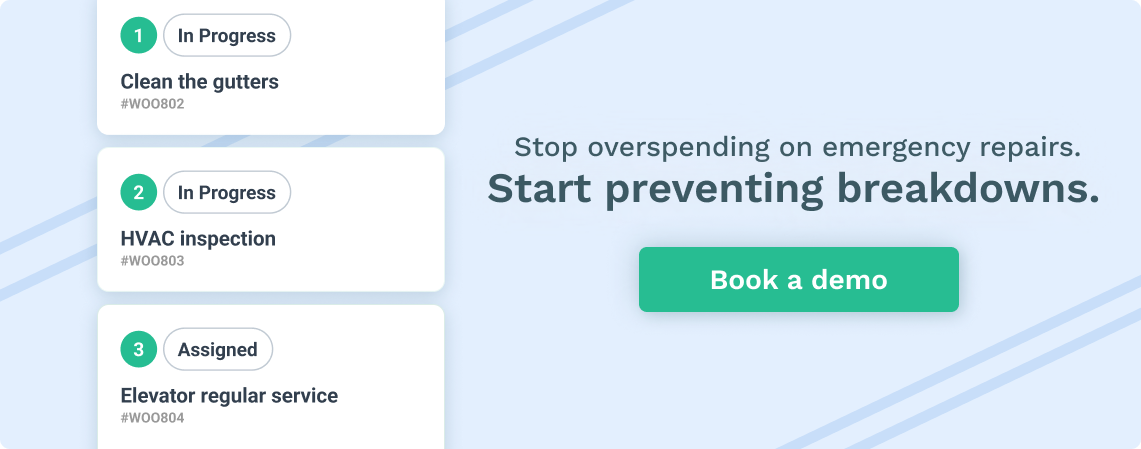
What are the maintenance KPIs related to cost control?
- Total cost of corrective maintenance
- Total cost of planned maintenance
- Weight in % of the corrective maintenance on the planned one
- Weight in % of the use of external resources on internal resources
How Can Tracking KPIs And Metrics Help A Business?
Making online business decisions based on assumptions is no better than walking a maze blindfolded. You can’t control where you’re going, but you know you’re going somewhere. The same goes for tracking KPIs and metrics.
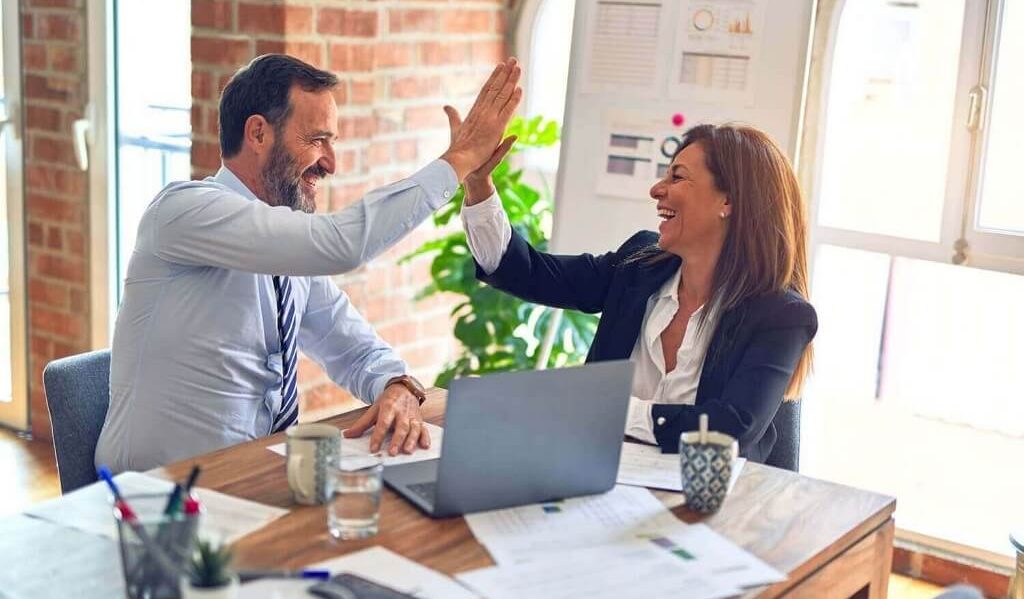
Tracking KPIs and metrics can go a long way in helping you maintain control of your business while making better data-driven decisions.
In a nutshell, here’s how they help:
Monitor the health of your company
Even if you think it’s a time-consuming process, you just need a few KPIs to monitor the health of your business, such as:
Financial Metrics: Measure and compare historical and current financial metrics to drive revenue growth
Employee KPIs: measure employee productivity and satisfaction to assess a company’s work environment
Customer Success KPIs: Measure how your service impacts customers and identify opportunities for improvement
These KPIs are metrics like customer retention, net profit margin, and similar metrics. Plus, they make it easy to assess the health of your business over time.
Measure progress
KPIs can greatly help you measure your organization’s progress against predetermined goals.
All you have to do is set the right KPIs and track key metrics like revenue and gross margin, as well as compare past and current performance to measure progress.
Metrics enable organizations to gain detailed insight into the performance of specific campaigns, strategies, and campaigns.
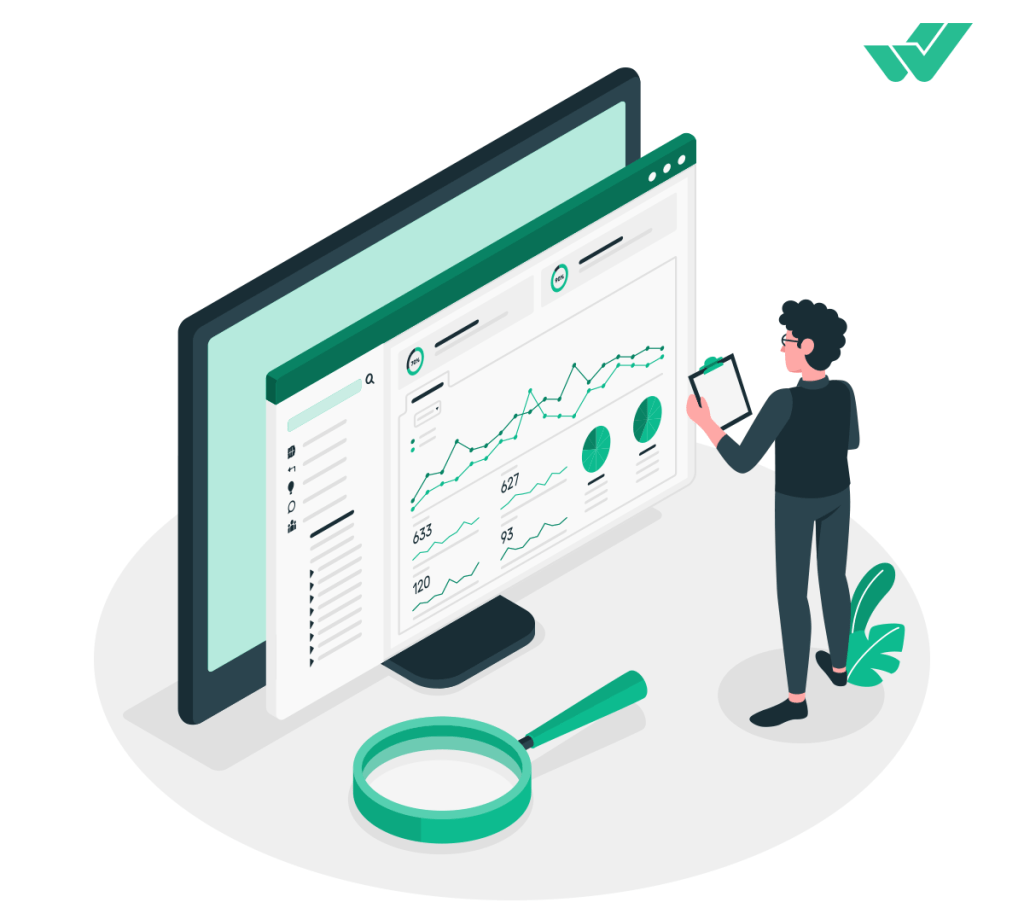
Make adjustments
One wrong decision can cause your business to fail. But by tracking KPIs and performance metrics, you can control what works for you and what doesn’t.
Tracking key performance indicators and indicators such as leading and lagging indicators at specific time intervals can help you identify pain points and determine future courses of action for better business growth.
How Does a CMMS Help Maintain KPIs?
Help centralize your maintenance information – The KPIs listed above are just some of the available KPIs. Teams can measure the success of their maintenance programs in a number of ways. Also, it can be a challenge to remember the various numerical formulas used to calculate each KPI on the fly.
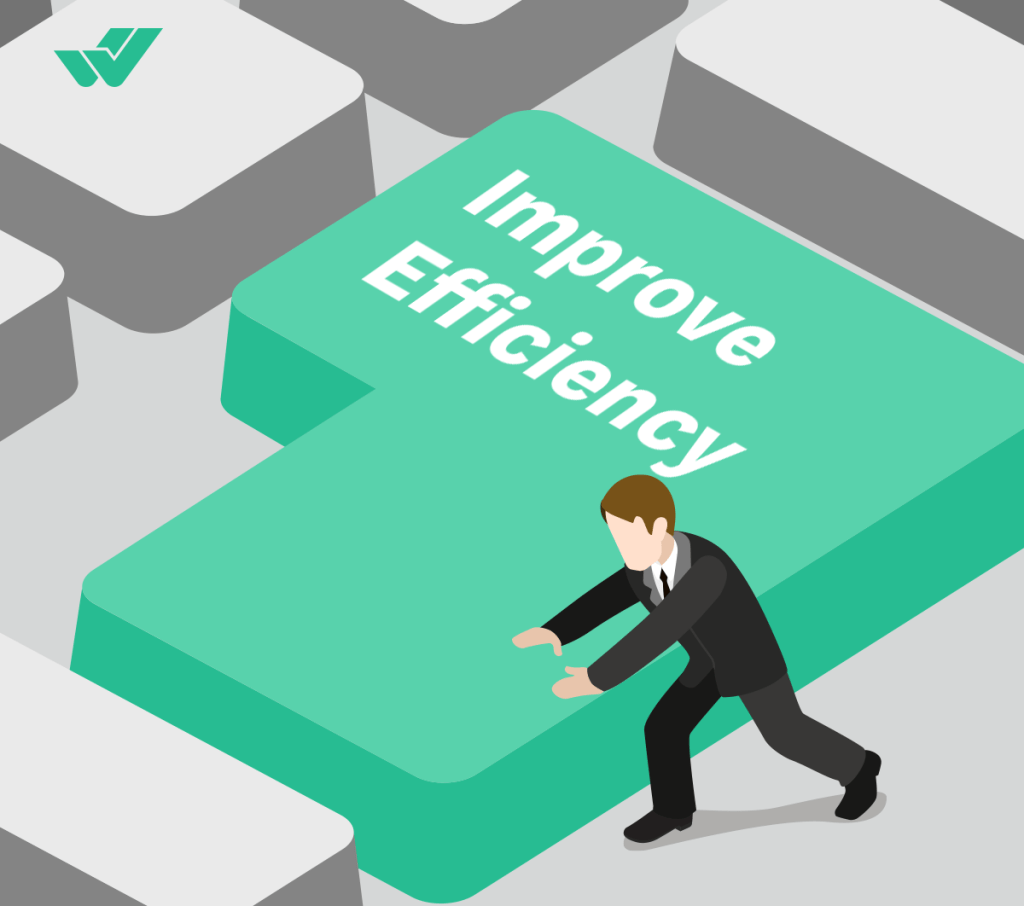
A good CMMS can provide simplified data and asset management, eliminating the need to memorize these formulas or remember exactly which maintenance KPIs you are tracking and why. Everything is in your hands.
Facilitates real-time data reporting – Powerful CMMS software stores your data in the cloud. CMMS has intuitive reporting capabilities that allow team members to comprehensively record maintenance performance indicators and KPI data in real-time.
This allows you to immediately see what is happening and really understand how your maintenance process is running.
Help you delegate work – Getting information is one thing. Knowing who should do what is another. The best CMMS will help you assign maintenance responsibilities quickly and easily, and may even eliminate the need to perform these tasks manually.
Conclusion
KPIs are key metrics that help keep your facility up and running efficiently. By selecting a few key metrics, your management team can make changes and measure their effectiveness.
Focusing on your most important assets and processes can have a huge positive impact on your bottom line. That’s what every company wants.