Get a Free WorkTrek Demo
Let's show you how WorkTrek can help you optimize your maintenance operation.
Try for freeWith the latest technologies, mobile CMMS facilitates the work of stakeholders in the field as well as real-time monitoring by their management and their customers.
They make it possible to have the right information in real-time, to locate the faulty equipment on a map or a plan, to take instructions on the intervention, to have the necessary authorizations for the sites at risk, to have the history of the equipment, diagrams or instructions for use.
Combined with a system for managing rounds and the geolocation of workers, this makes it possible to know who is the nearest qualified worker and how quickly he can get there. This therefore provides more responsiveness, but also clarity towards customers or the internal customer.
The recording of information by the worker himself in the field enhances the quality of the data contained in the CMMS. In fact, this avoids re-entry, with all the misunderstandings that this brings. It is the employee who carried out an intervention who has the best information, not to mention the time that it costs the company.
Mobility is becoming essential and makes it possible to provide traceability and transparency of interventions, optimize travel, and increase the quality of service.
Click here to learn more about CMMS.
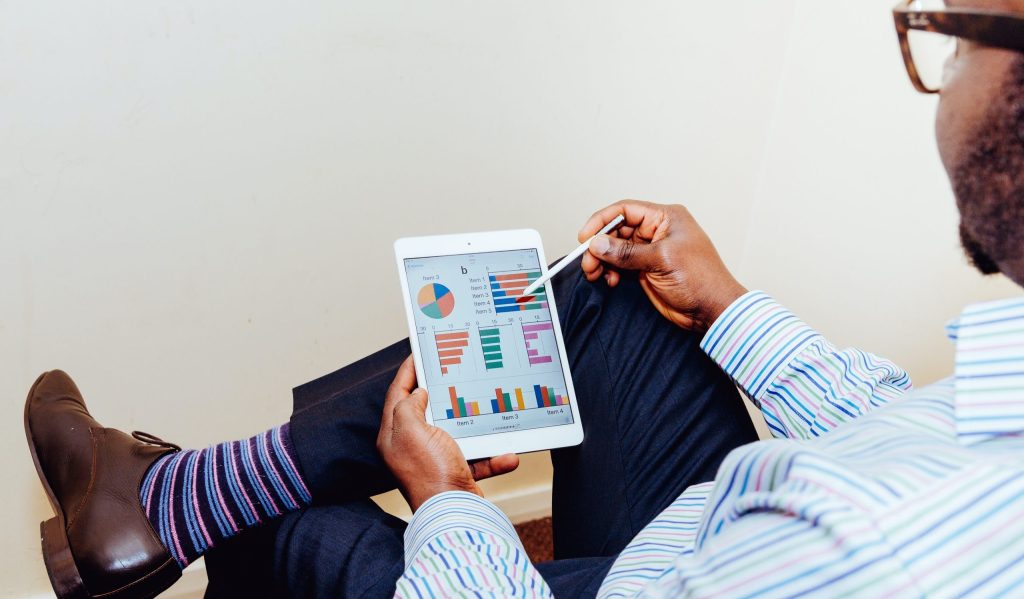
Mobile CMMS, a Small Revolution
By using a CMMS mobile app, maintenance teams are more likely to leverage the full potential of a CMMS.
What is a mobile CMMS?
Mobile CMMS software is an application that can be used on a smartphone or tablet. Essentially, it is this possibility of “on-the-go” deployment that distinguishes it from traditional software, and it also takes over the maintenance management functions.
However, some applications integrate many additional features inspired by recent advances in new technologies and their new uses in daily life.
The application uses big data logic to provide its users with analytical tools based on data collected from thousands of anonymous and professional users working on the same machine.
Community operations inspired by social networks allow maintenance technicians and machine operators to exchange information and share their problems. This applies both to communities within the company or group and to users from other organizations.
Finally, the ergonomic design makes it as easy to use as everyday applications, even for inexperienced users.
How does a mobile CMMS work?
Specifically, a mobile CMMS is an application that can be used on a tablet or smartphone. Some of the solutions are very similar to everyday apps available on Android and IOS.
More specifically, CMMS publishers that offer a mobile version typically offer two versions of the solution, all of which work online. The main version is the most complete, accessible via an internet browser, and therefore designed for use on a computer. The mobile version takes the form of an Android or IOS CMMS application that provides some of the functionality of the desktop version. Of course, the data available for both versions is the same.
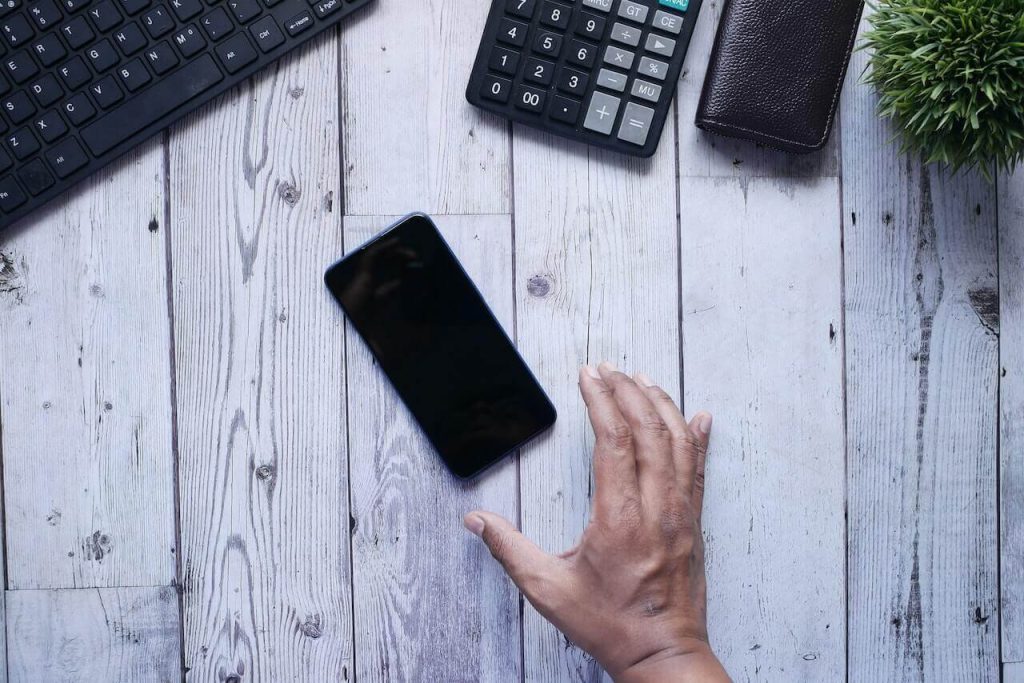
Advantages of Mobile CMMS
The main advantage of a mobile CMMS is obviously…mobility – This is a big advantage, especially for building maintenance software, the fact that maintenance technicians using a mobile CMMS can enter their intervention reports immediately after the fact rather than having to write the information down in a notebook and then return to the office to copy or memory, which often results in loss of information. In addition, they have access to information they need for their work, such as technical data sheets for equipment or safety instructions to follow.
Job Satisfaction
A mobile CMMS provides you with a wealth of useful resources that can improve your performance. Mobile access enables technicians to complete tasks faster and more efficiently. Faster access and dissemination of information about tasks improves overall performance. You can also stay up-to-date on important developments while you’re at work, so you can respond quickly in emergencies.
Communicate instantly from any location
When a critical component fails, technicians must repair it immediately and make necessary repairs with minimal disruption to maintenance schedules. To avoid such unexpected failures and avoid huge costs, technicians must be able to react in real-time. A mobile CMMS provides the ability to remain flexible and adaptable by sending immediate notification of any outages along with complete records of previously performed repairs and maintenance. With real-time visibility into serviceability and equipment health, facility managers can also prevent workplace hazards and ensure a safer working environment.
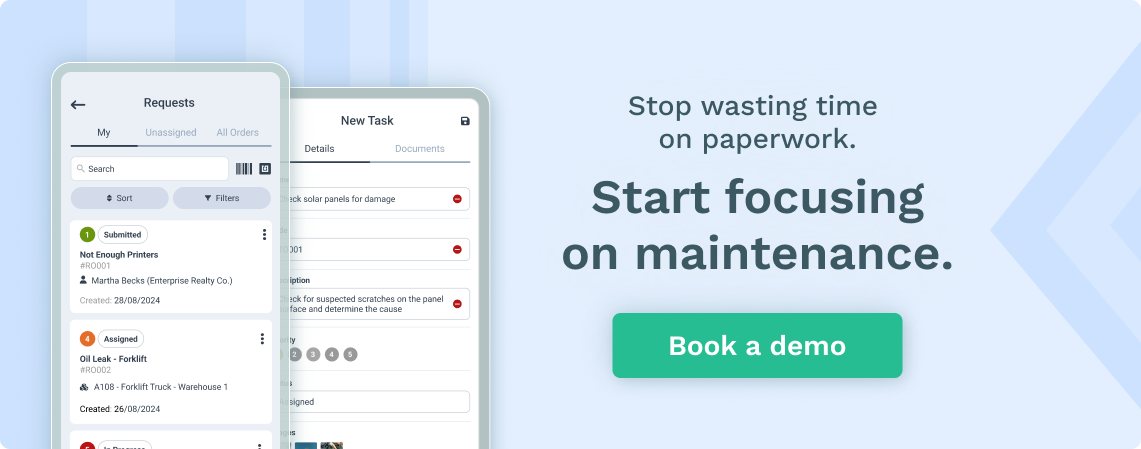
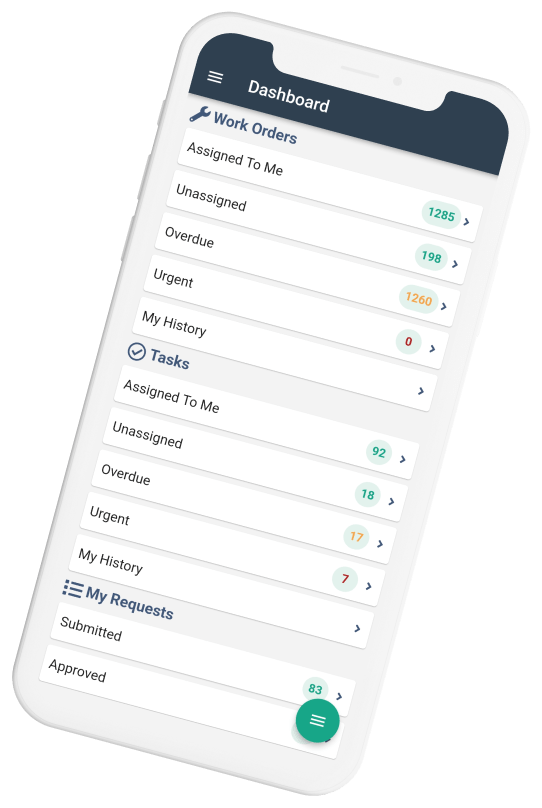
Promote a paperless work environment
A mobile CMMS can effectively manage an organization’s maintenance and repair activities. It includes features and functionality that eliminate the need for paper copies of work orders, thereby saving significant office supply costs. Additionally, this paperless approach significantly reduces the harmful environmental impact associated with printing and processing paperwork. Implementing a CMMS eliminates the risk of important maintenance records being lost or damaged due to paper documentation.
All data is stored securely within the software, so no data can be lost or accidentally corrupted. This seamless organization of information greatly facilitates efficient and smooth workflow. In addition, the use of mobile CMMS also leads to significant improvements in productivity. With access to work orders, schedules, and maintenance history at the touch of a button, employees can respond quickly to maintenance requests and perform tasks more efficiently. This streamlined process saves valuable time and allows maintenance teams to focus on their core tasks rather than wrangling paperwork.
Companies can demonstrate their commitment to modern technology and efficient processes rather than relying on manual records and outdated systems. This enhances the reputation of the organization and gives employees a sense of professionalism and reliability.
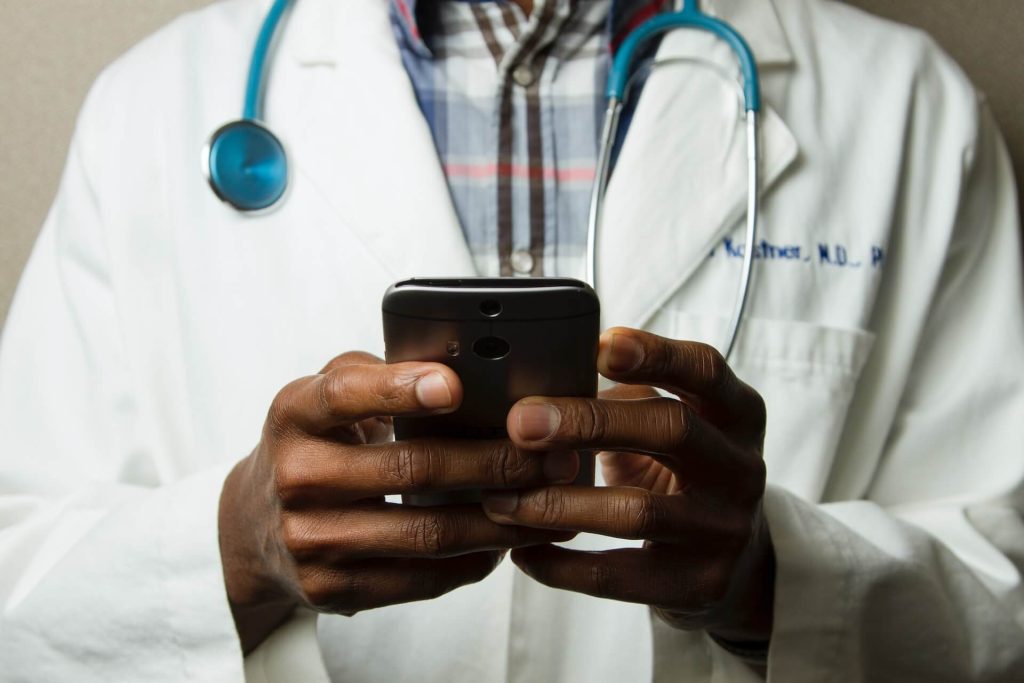
Greater accuracy
An important reason why many manufacturing companies commonly choose to implement maintenance management software is the improvement in work order accuracy. A mobile CMMS only improves this. Instead of writing down or remembering work order instructions when leaving the shop floor, technicians can use a mobile app to view the information when they arrive on site. You no longer have to worry about missing notes or hearing something wrong. Just use the app to enter your details.
See which key metrics you should keep track of inside CMMS.
Reduce downtime
Production facilities, drilling rigs, and power plants are productive assets, and if these assets experience a loss of capacity or downtime during maintenance, troubleshooting should occur quickly. In order to be able to use the system efficiently again in a timely and efficient manner, fast communication is necessary. A mobile CMMS keeps technicians informed, eliminating the need to report and check dispatch to headquarters. It can significantly reduce downtime by notifying technicians which parts need urgent replacement, which parts are currently available, and which equipment needs repair as soon as possible. This increases work efficiency and instantly returns the machine to peak performance. When managing complex assets with multiple dependencies, downtime affects all concurrent activities. With a mobile CMMS, facility managers can prevent unplanned outages and minimize the impact of planned outages by recording work in real-time, making immediate corrections, and forwarding information to field engineers.
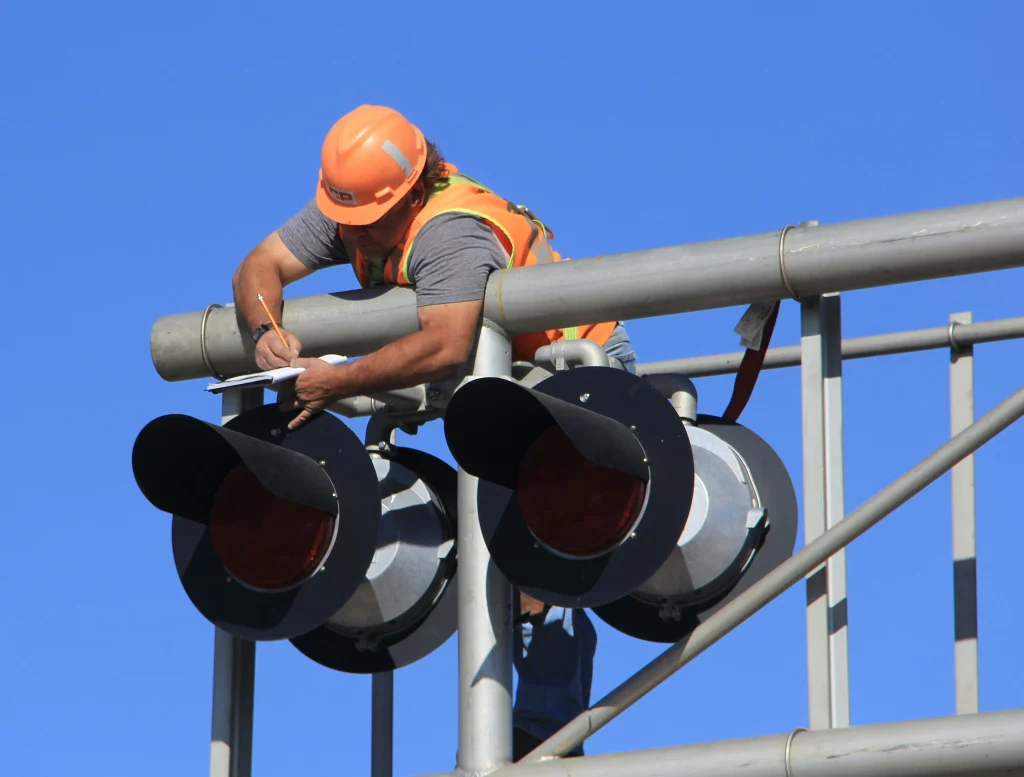
Ability to work online and offline
One of the biggest benefits of using mobile CMMS software is the ability to open, create, manage, and close work orders even from a remote location. Equipment failures often occur in inopportune places. With a mobile CMMS, companies can solve this problem by allowing employees to access the system even when they are offline.
Cut costs
A mobile CMMS can help companies reduce costs by streamlining maintenance operations and improving asset utilization. This means businesses can save on repair and replacement costs as well as labor costs. As costs are reduced, companies can allocate their newfound budget to other areas of the business, such as investments, marketing, and research and development.
Check out our blog about How can CMMS save you money.
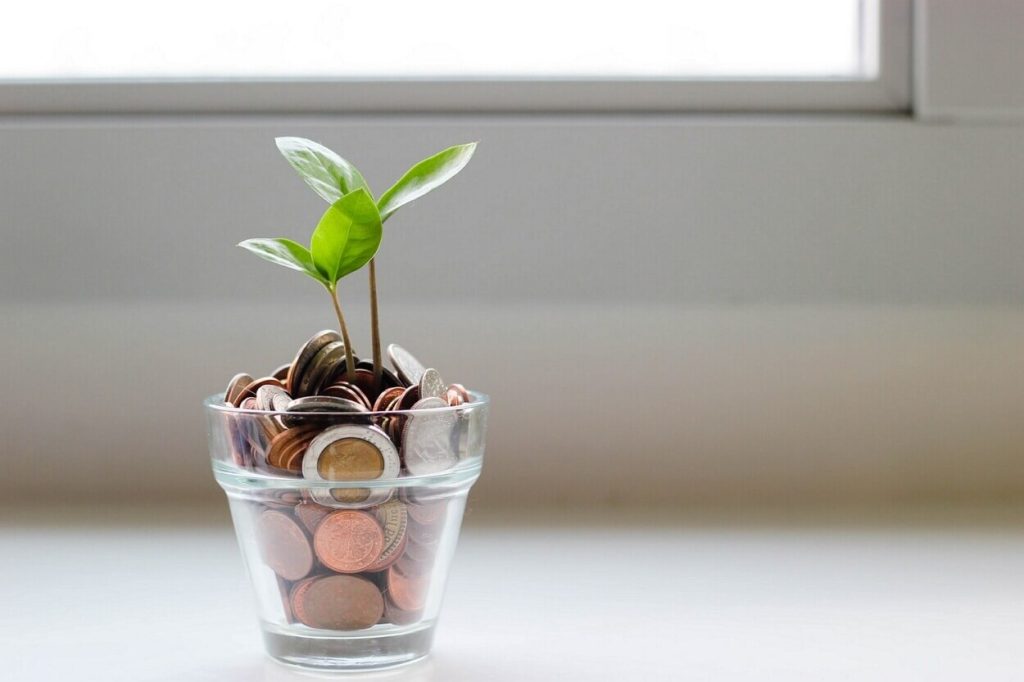
Key Features of CMMS Mobile Software
The ideal mobile CMMS software helps maintenance teams by providing key features that make their lives easier and get the job done as quickly as possible. Therefore, mobile CMMS software should have the following main functions:
- Manage and create work orders: Maintenance technicians can issue parts to work orders, add notes, and complete work orders to verify job completion.
- Create a work request: Workers can enter issues with specific equipment and submit them as work requests.
- Schedule and manage maintenance: The software should give you a comprehensive overview of all maintenance activities and allow you to easily create and manage schedules.
- Asset Tracking: This should also allow you to track your assets in real-time. This includes location, status, and repair history.
Next, read the Top 5 CMMS Features you need in your work life.
Increase your employee productivity with mobile CMMS!
Book a WorkTrek demo to see how a CMMS can help your business.
Try for freeNo Maintenance Restrictions With Mobile CMMS Software
Industrial maintenance can be managed in many ways without specialized software, but its limitations always reduce a company’s activity and profitability. These limitations are:
Industrial Maintenance Level 0
Some businesses still manage equipment maintenance in a “piecemeal” manner. If a machine was found to be defective, parts were replaced, but this activity was not monitored, a spare parts warehouse was not organized, and no tasks were planned.
This approach—or rather, the lack of it—has two major drawbacks. On the one hand, this results in a significant loss of productivity, since the machine is idle when parts arrive. Monitoring maintenance work is impossible and not simplified at all. It is therefore impossible to foresee or plan interventions, nor to have a complete picture of the wear and maintenance needs of the machine.
Maintain “paper talk”
Monitoring machine maintenance operations using paper documents is the first step in the organized management of industrial maintenance. Written documentation of each intervention allows for minimal monitoring and traceability.
See also, how can CMMS help you reduce machine downtime.
However, access to the intervention booklet or intervention sheet (which is only available as a single copy stored in a single location) and its readability is limited. This does not allow for good traceability of interventions or smooth transfer of information between affected teams. Finding a description of a specific task is an obstacle.
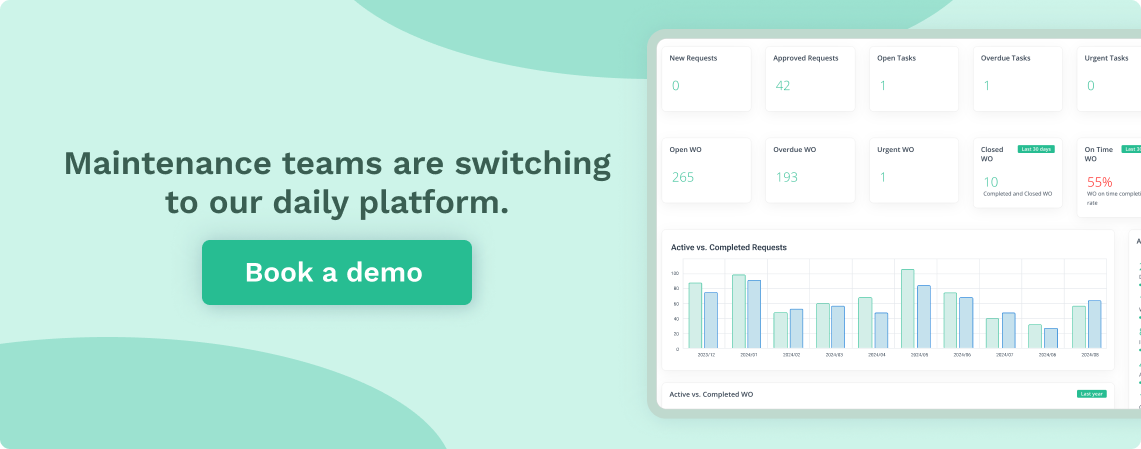
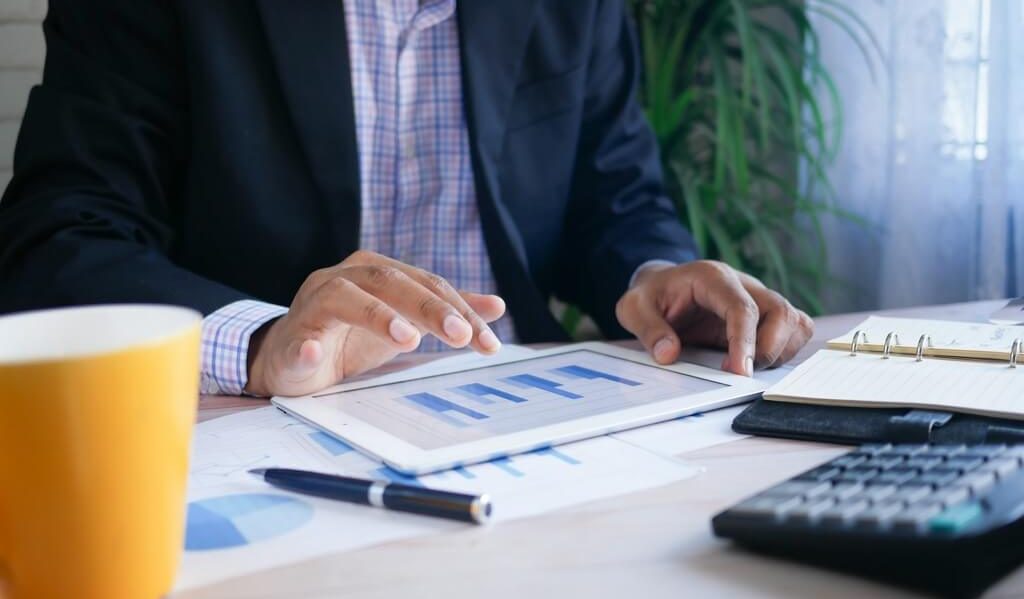
CMMS Excel or Access
The spread of IT and the emergence of Excel software enabled some companies to introduce the first forms of computerized maintenance management. They use spreadsheets to record all maintenance work performed.
Although this approach significantly improves the monitoring of interventions and in particular the consultation on implemented measures, it is still limited in terms of information acquisition and planning of measures.
The use of Access software represents a definite advance on this last point, enabling calendar planning of both preventive and formal maintenance work.
Regardless of whether you choose Excel or Access, the exchange of information is limited by the characteristics of the software and cannot be viewed and used through the network.
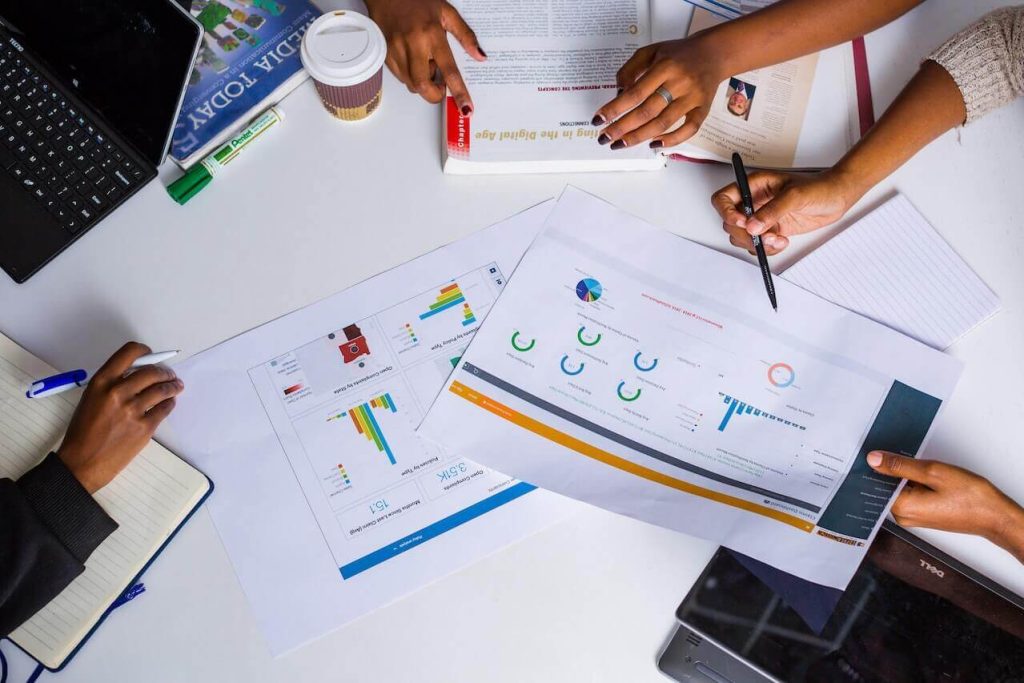
Mobile CMMS: 4 Reasons to Equip Your Maintenance Worker With a Smartphone/Tablet
You have decided to take a CMMS solution to equip your teams, but you are afraid that the tool will be more restrictive than anything else? It is not so! The objective of a CMMS application is to be mobile. Indeed, it is supposed to be suitable for maintenance workers. They have many missions to carry out and must travel to complete them. A mobile CMMS tool will help him a lot and save him time in his organization. But wasting the time saved by going back and forth to a fixed computer is a shame… Fortunately, there is a perfect alternative: the digital tablet.
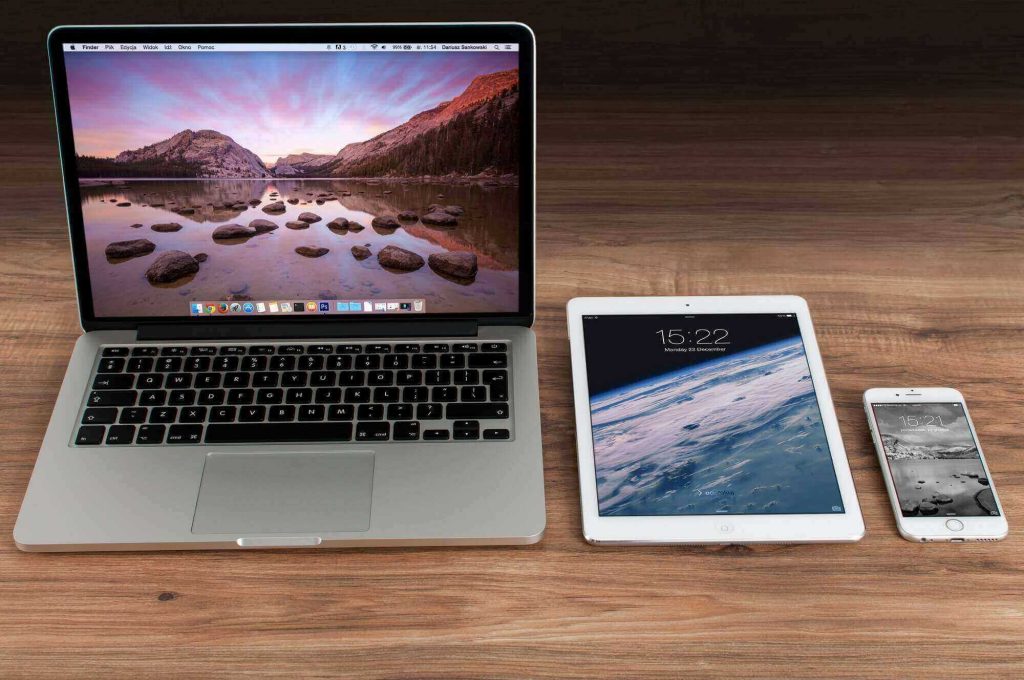
1. Be more mobile and save time
First of all, the format of the tablet is super practical, It allows you to go everywhere without asking questions, without a small notebook, and without thinking about writing down notes for later… What a relief! And yes, equipping your maintenance agent with a tablet makes data entry easier. For example, the tablet simplifies data entry on its CMMS software and optimizes its mobility. Small and light, the tablet can stay with its agent at any time of the day.
2. Capture data in real-time, more easily
Second, the tablet makes it super easy to enter data in real-time. Using a digital tablet also means being able to enter data in real-time. And for good reason, it is really useful for maintenance agents who need to regularly enter information into their CMMS tool. Keeping your maintenance up to date is very important and much easier with a touchscreen tablet! Thanks to it, the maintenance agent does not need to wait until the end of the day to enter all the information in one go. He can therefore enter them as his day progresses, in real time. Temperature readings to take? The tablet is ideal and much more practical for their input. No need to write everything down on a piece of paper that can easily be lost. No need to type everything again. Everything happens on the tablet and everything is recorded directly on your CMMS.
3. Consult information in real-time
Using a tablet with a CMMS also makes it possible to consult maintenance information in real-time. A doubt about the info on the equipment or the last date of maintenance? With his tablet, the maintenance agent obtains the necessary information in an instant. No more trips to the computer or worse: uncertainty and questioning… This saves time, and energy, and limits the risk of errors.
4. Gain responsiveness with the camera and QR code reader
The advantage of a tablet is also to have an integrated camera. Need to illustrate a breakdown? To show the results of the work? Describe the room. From a serial number? A photo in one click and presto, the file can be directly loaded onto the CMMS tool.
Without forgetting that with a tablet equipped with a CMMS tool, if your equipment is equipped with QR codes, you can directly scan the code and save considerable time. The function is not possible from a computer.
Next, read how much CMMS software costs.
What Benefits Can a Mobile CMMS Bring to a Company?
Efficiency is a top priority. Just think of the time you would save if you no longer had to go to your desk to get more information, or to the parts room only to find a part was out of stock. Imagine being notified instantly of an urgent work task via a notification tone on your device instead of seeing a note on your desk hours later.
Mobile CMMS improves communication between maintenance personnel, managers, and citizens. Essentially, the efficiency we experience when using mobile devices in our daily lives can directly impact the efficiency of our workflow:
A lean and efficient team allows you to do more with less, save overtime, use that time for preventive maintenance, other more efficient projects, and more.
Quick access to a CMMS helps our operations run smoother, reduce downtime, reduce waste, and improve the quality of our work.
Ultimately, a mobile CMMS saves us money by reducing labor costs and creating longer-lasting assets and facilities.
See more benefits of CMMS software.
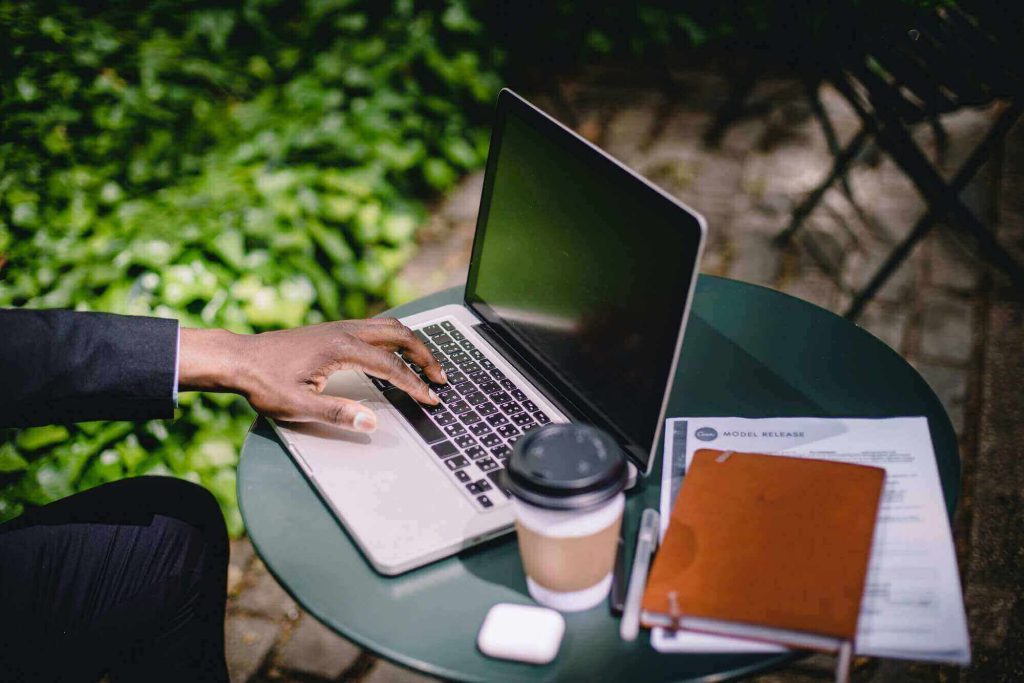
Conclusion
CMMS tools greatly facilitate the management of your daily maintenance. However, the experience can be further simplified by using a tablet and be a huge time and efficiency saver. The difference between a classic CMMS and a mobile CMMS may seem small at first glance. Simply being able to use the software on a tablet or smartphone, the practical direct and indirect impacts of the advantages of a mobile CMMS are actually numerous.