Get a Free WorkTrek Demo
Let's show you how WorkTrek can help you optimize your maintenance operation.
Try for freeMachines break down, equipment fails—these are facts of life in any industry. However, a good maintenance plan can reduce problems and keep things running smoothly. This article covers 10 tips for an effective maintenance plan and approach.
A smart approach to maintenance and upkeep saves time and money in the long run.
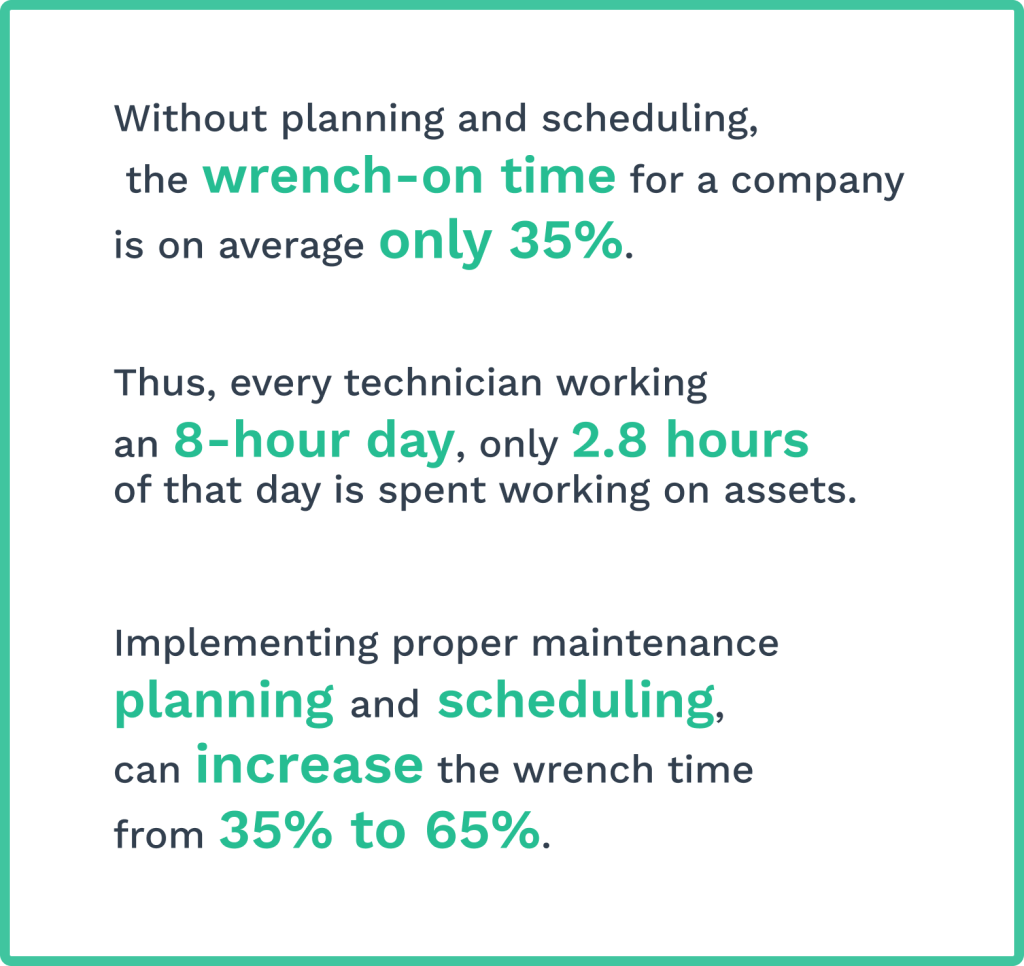
Illustration: WorkTrek / Data: Inspectione
An effective maintenance plan includes regular checks, timely repairs, and smart resource use. It helps prevent unexpected breakdowns that can halt work and cost a lot of cash. With the right plan, businesses can keep their gear in top shape and avoid big headaches.
This post will share 10 key tips for creating a strong maintenance strategy. These ideas can help any company improve how it cares for its equipment and facilities. These tips cover all the bases for better maintenance, from setting clear goals to using new tech.
Understanding Maintenance Planning
Maintenance planning is key to keeping equipment running smoothly. It helps prevent breakdowns and saves money. Good planning makes work easier and more efficient.
Benefits of Preventive Maintenance
Preventive maintenance stops problems before they start. It makes machines last longer and work better. This type of care cuts down on sudden breakdowns that can halt work.
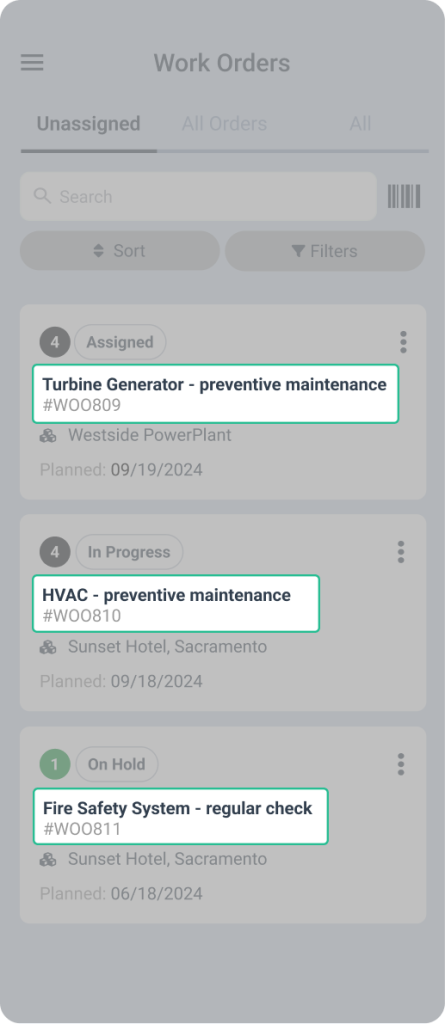
Source: WorkTrek
Regular check-ups catch small issues early. Fixing these small problems costs less than big repairs later and means less machine downtime.
Preventive maintenance helps plan work better. Teams can schedule fixes when it’s best for the business. This means less rush and stress.
Preventive care also improves safety. Well-kept machines are less likely to cause accidents, keeping workers safe and happy.
Differentiating Maintenance Strategies
Different maintenance plans fit various needs. Some focus on fixing things only when they break, while others try to prevent breaks before they happen.
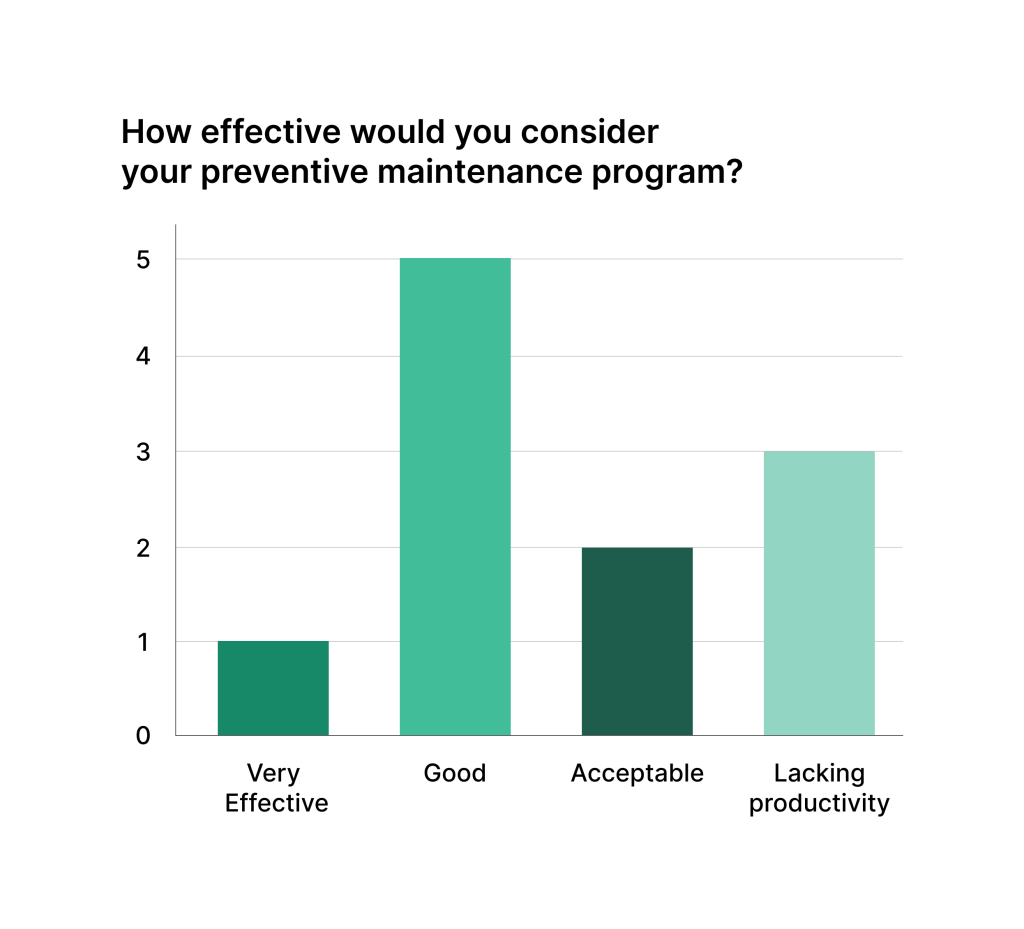
Illustration: WorkTrek / Data: Present Status and Future Growth of Advanced Maintenance Technology and Strategy in US
Reactive maintenance waits for problems to occur. It’s simple but can lead to big, costly fixes. This works for small, cheap parts but not for essential machines.
Predictive and preventive maintenance tasks use data to guess when things might break. They also check machine health often, which helps fix issues at just the right time.
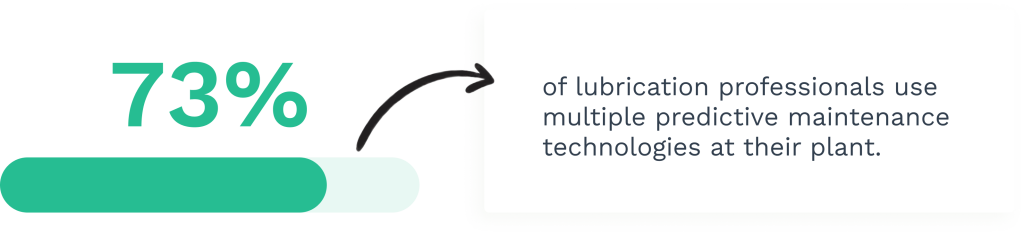
Illustration: WorkTrek / Data: Machinery Lubrication
Condition-based maintenance watches how machines work. It fixes them when signs show they need help, saving time and money by not fixing things that don’t need it.
Setting Maintenance Goals
Effective maintenance goals drive performance and align with business needs. They provide clear targets for teams to work towards and measure progress.
Defining SMART Objectives
SMART goals—specific, measurable, achievable, relevant, and time-bound—are key to maintenance success.
For example, a SMART maintenance goal could be: “Reduce equipment downtime by 10% within 4 months through scheduled maintenance and staff training.”
This goal is:
- Specific: Focuses on equipment downtime
- Measurable: 10% reduction
- Achievable: Through defined actions
- Relevant: Improves operational efficiency
- Time-bound: 4-month timeframe
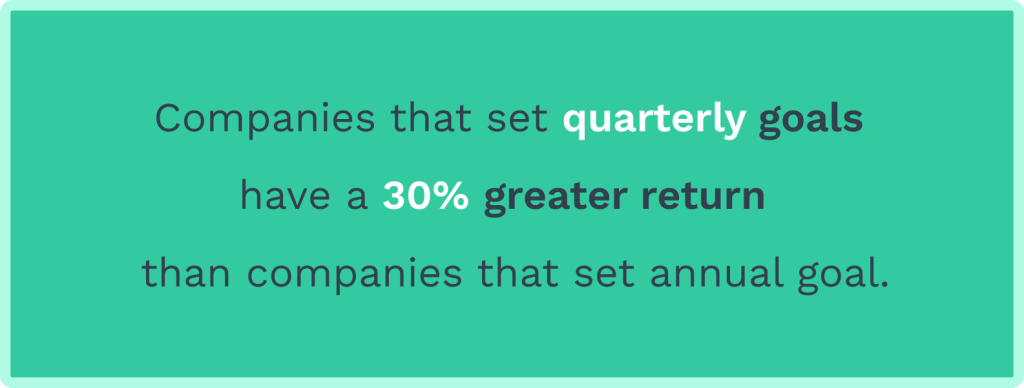
Illustration: WorkTrek / Data: Healthy Happy Impactful
Teams should set 3-5 SMART goals to focus efforts without overwhelming staff.
Aligning with Business Outcomes
Maintenance goals must support broader company objectives to improve asset performance. This ensures maintenance efforts contribute to organizational success.
Key business outcomes to consider:
- Cost reduction
- Productivity improvement
- Quality enhancement
- Safety improvement
- Regulatory compliance
For instance, if a company aims to cut costs, a maintenance goal might be to extend equipment lifespan through preventive care. This reduces replacement expenses and downtime.
Regular meetings between maintenance leaders and executives help keep goals aligned. Goals should be reviewed quarterly and adjusted as business needs change.
Assessing Your Current Maintenance Operations
A thorough assessment of your maintenance operations is key to developing an effective plan. This involves examining your equipment and procedures and pinpointing areas needing improvement.
Audit Current Equipment and Processes
Start by taking stock of all your equipment. Make a list of each machine, its age, condition, and maintenance history. This inventory will help you spot patterns and potential problem areas to help reduce equipment failures.
Next, review your current maintenance processes and set specific maintenance tasks. Look at how often you perform maintenance tasks and who carries them out. Check if you use a computerized maintenance management system (CMMS) to track work orders and schedules.
Analyze your maintenance data, including repair frequency, downtime, and costs. These numbers can reveal which machines need the most attention and where you spend the most money.
Identify Areas for Improvement
With your audit complete, it’s time to find ways to enhance your maintenance operations. Look for equipment that breaks down often or costs a lot to repair. These might need more frequent check-ups or replacements.
Examine your maintenance schedules. Are you performing too much reactive maintenance?
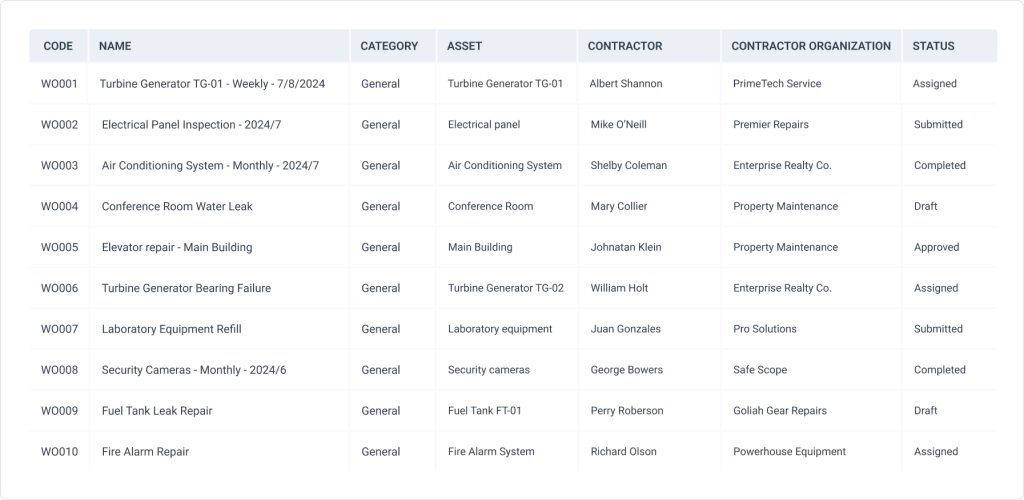
Source: WorkTrek
Shifting towards preventive maintenance could reduce unexpected breakdowns and costs.
Consider your staff’s skills. Do they have the right training for your maintenance technicians to handle all maintenance tasks? Identifying skill gaps can guide future training plans.
Lastly, review your parts inventory. Ensure you have the right parts on hand to avoid delays in repairs. An organized inventory system can save time and money.
Developing a Maintenance Strategy
A good maintenance strategy helps keep equipment running smoothly and prevents costly breakdowns. In the long run, it saves money and time.
Selecting the Right Maintenance Model
Proactive preventive maintenance is key to an effective strategy. This approach aims to fix issues before they cause problems, which is better than maintenance team members constantly reacting to breakdowns.
Different models work for different needs:
- Preventive Maintenance:
- Preventive maintenance is about regular checks and servicing to avoid breakdowns. It follows a schedule based on time or usage. This approach reduces downtime, improves reliability, and extends equipment life. For managers and technicians, it ensures tasks are planned, cuts emergency repairs, and keeps operations running smoothly.
- Predictive Maintenance:
- Predictive maintenance uses data and sensors to spot problems early. It tracks performance to predict failures before they happen. This approach reduces downtime, lowers costs, and improves reliability. For managers and technicians, it means fixing issues at the right time and keeping equipment running smoothly.
- Condition-based:
- Condition-based maintenance monitors equipment in real time to decide when maintenance is needed. It targets issues only when signs of wear appear. This approach cuts unnecessary work, saves resources, and improves reliability. It helps managers and technicians fix problems quickly and prevents breakdowns.
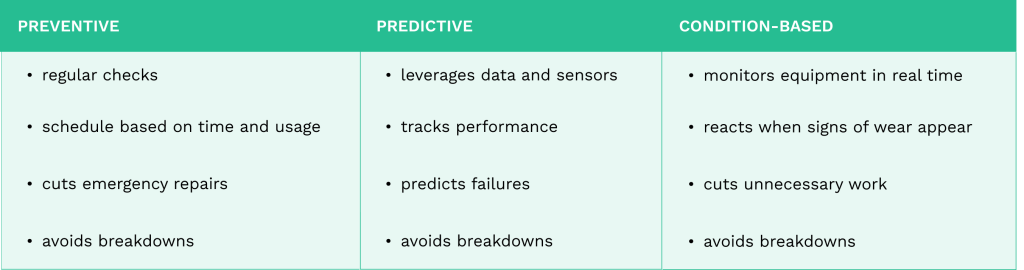
Source: WorkTrek
Choose a model that fits your resources and goals. Mix and create hybrid models for best results.
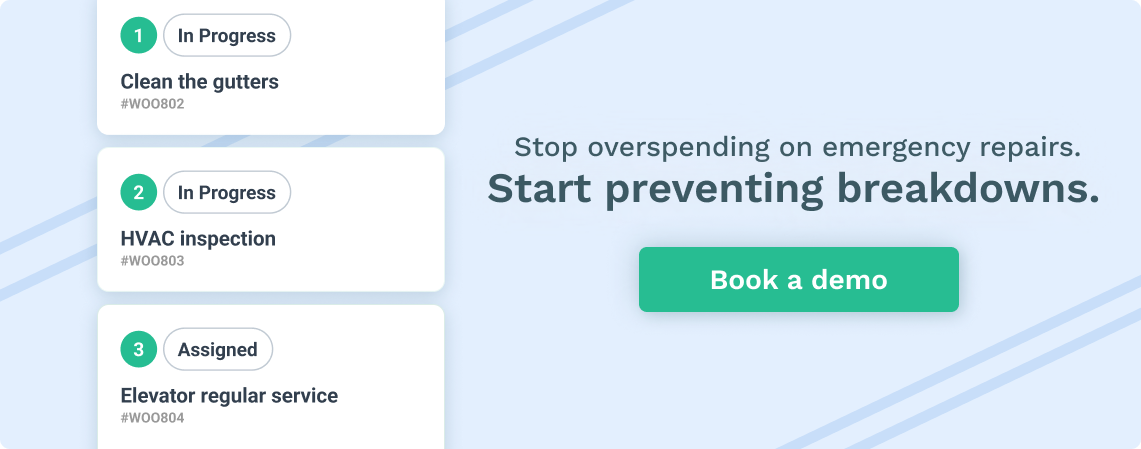
For example, preventive measures can be used for simple tasks and predictive measures for critical machinery.
Balancing In-House and Outsourced Tasks
Decide which tasks to do in-house and which to outsource. This balance affects maintenance costs and quality.
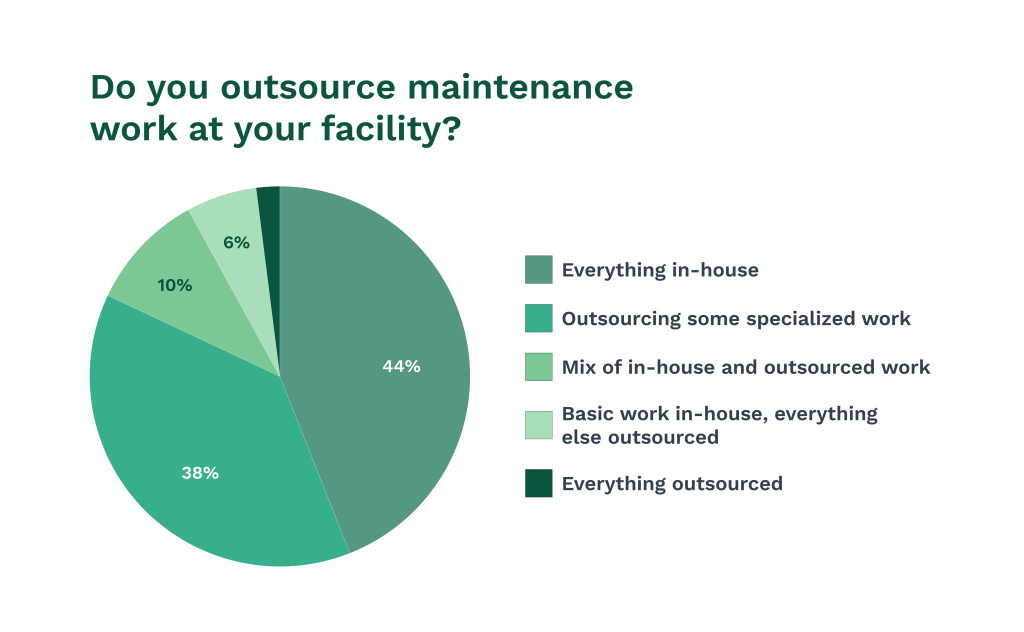
Illustration: WorkTrek / Data: Limble
In-house pros:
- Better control
- Faster response times
- Deep knowledge of equipment
- Dedicated team members
Outsourcing pros:
- Access to specialists
- Reduced labor costs
- Focus on core business
- Cost savings
- Smaller maintenance team
Hire a maintenance planner to manage this balance and help with strategic planning. This would help the maintenance manager assign tasks based on skill and cost, allowing other staff to focus on their primary jobs and improve operational performance.
Train your team on new tech and methods. This keeps skills sharp for in-house work. Pick partners with a good track record and clear communication for outsourced tasks.
Creating a Maintenance Schedule
A well-planned maintenance schedule keeps equipment running smoothly and prevents unexpected breakdowns. It helps businesses save time and money by organizing tasks efficiently.
Prioritizing Maintenance Activities
To make a good maintenance schedule, list all equipment that needs upkeep and define routine maintenance. Rank tasks by importance, focusing on critical machines for daily operations. Look at how often each item breaks down and how much it costs to fix.
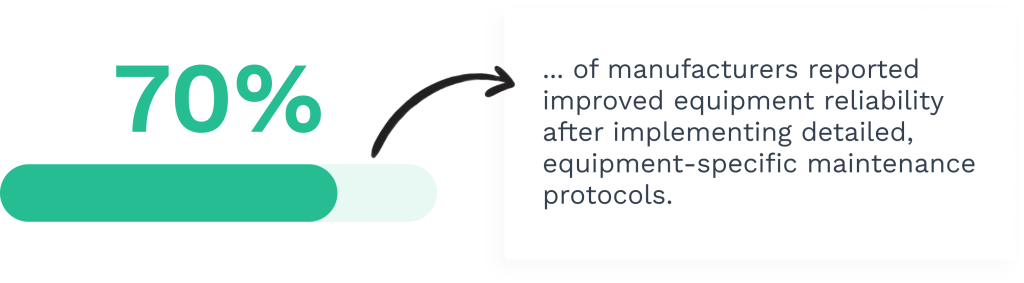
Illustration: WorkTrek / Data: Machinery Lubrication
Consider the impact of equipment failure on production and safety. Machines that could cause accidents or stop work should be a top priority.
Use data from past maintenance records to spot patterns. This helps predict when things might break and schedule fixes before problems happen.
Frequency of Maintenance Tasks
Decide how often each task needs to be done. Some equipment might need daily checks, while others only need yearly service.
Follow manufacturer guidelines for maintenance intervals. But adjust based on your actual usage and conditions. Machines used more often or in harsh environments may need more frequent care.
Make a calendar showing when each task is due. Use different colors or symbols for daily, weekly, monthly, and yearly tasks. This makes the schedule easy to read at a glance.
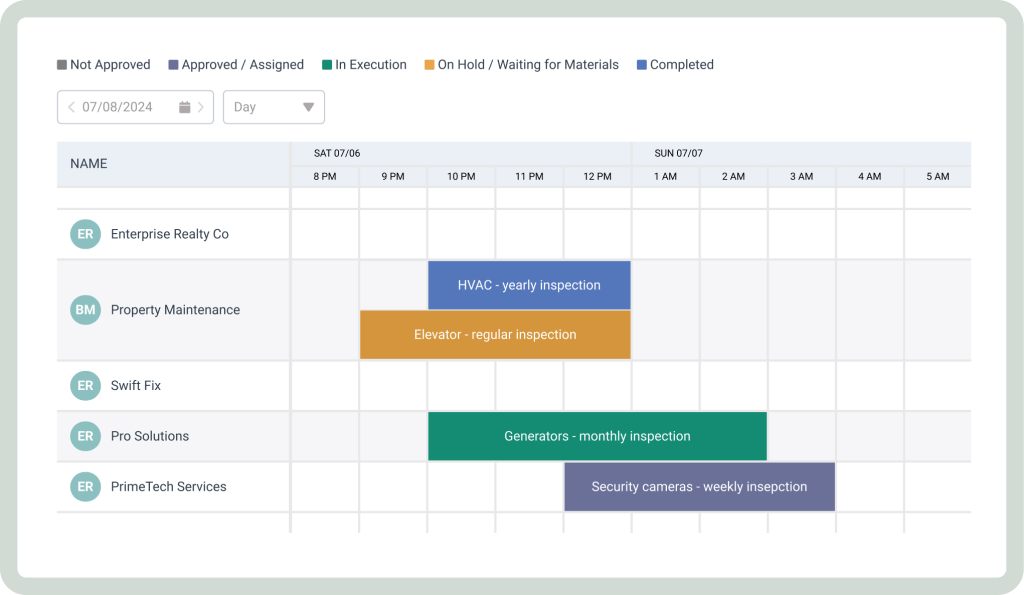
Source: WorkTrek
Be flexible with your schedule. Leave some open slots for unexpected repairs or changes in production needs.
Implementing a Preventive Maintenance Program
A preventive maintenance program helps keep equipment running smoothly and avoids costly breakdowns. It involves creating a schedule, defining regular inspections, and maintaining equipment to catch issues early.
Establishing Preventive Maintenance Routines
Start by making a list of all equipment that needs maintenance. Note how often each item should be checked or serviced. Create a schedule that spreads out the work over time.
Use a computerized maintenance management system to track tasks and send reminders. This will help ensure that nothing is missed.
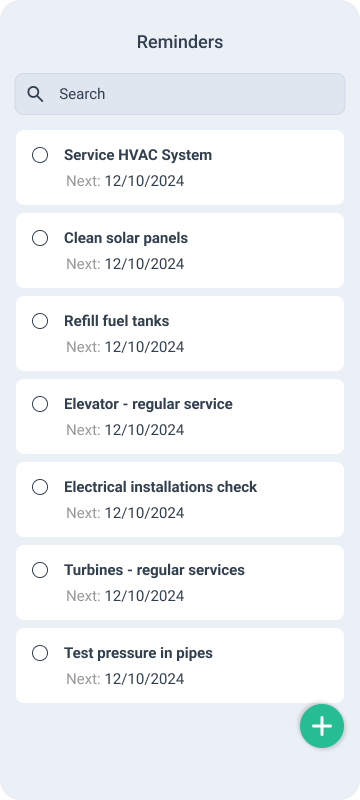
Set up checklists for each piece of equipment and scheduled maintenance tasks. Include steps like checking oil levels, tightening bolts, or cleaning filters. Make the checklists easy to follow.
Keep good records of all maintenance done. This helps spot patterns and plan future work.
Training for Maintenance Staff
Proper training is key for an effective preventive maintenance program. Teach staff how to use the maintenance tracking system and follow checklists.
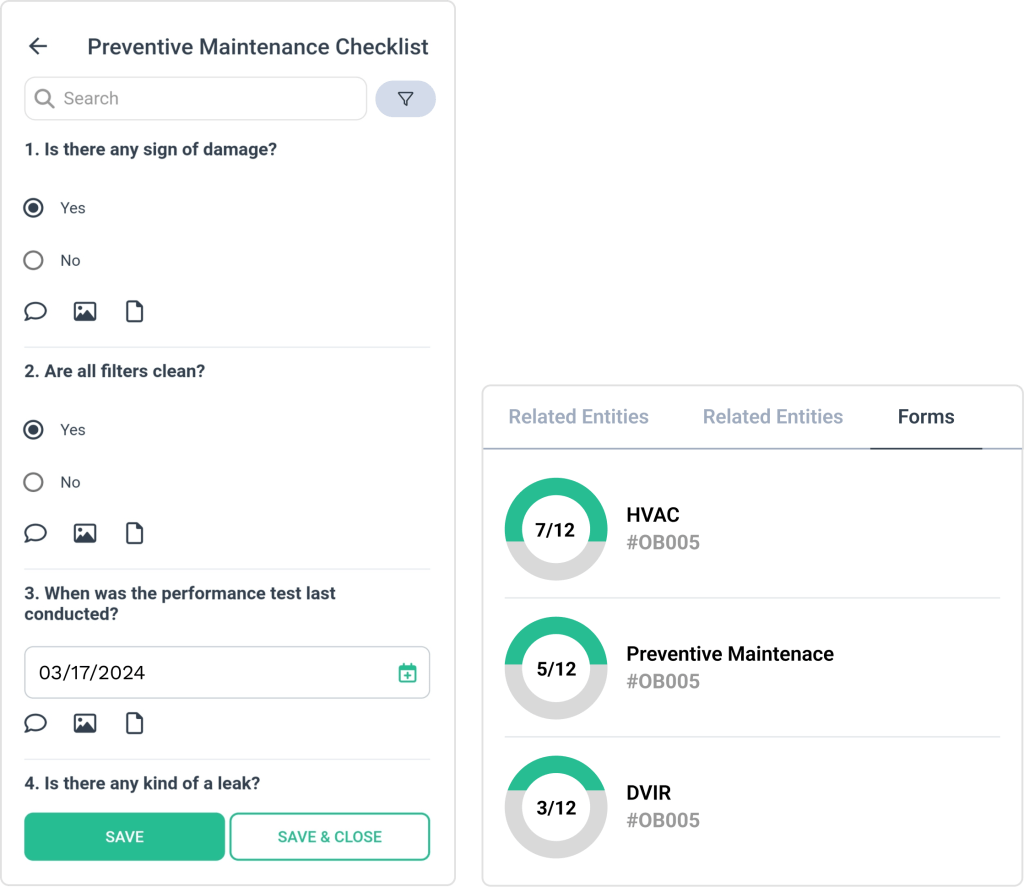
Give hands-on training for different types of equipment. Show how to spot early signs of wear or damage. Practice proper repair techniques.
Offer ongoing education to keep skills up to date. This could include classes on new technology or safety procedures.
Encourage staff to share knowledge. Set up a system for reporting and fixing problems quickly.
Regular training helps staff work more efficiently and safely. It also leads to better equipment care and fewer breakdowns.
Utilizing Maintenance Software
Maintenance software is key for effective upkeep. It streamlines processes and boosts efficiency.
Features of CMMS
Computerized Maintenance Management Systems (CMMS) offer many helpful tools. They track assets, schedule tasks, and manage work orders.
Asset tracking lets teams know where equipment is and its condition. This helps plan repairs and replacements.
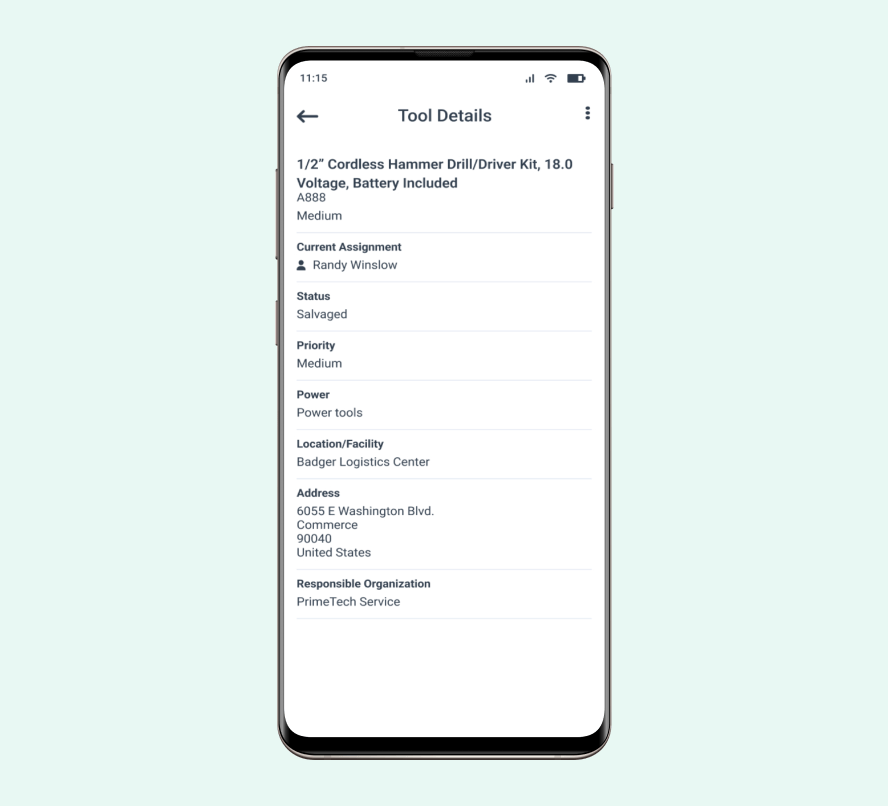
Scheduling features automate maintenance tasks. This ensures regular upkeep and prevents breakdowns.
Work order management tracks repairs from start to finish. It shows who did what and when, improving accountability.
CMMS also stores equipment manuals and repair histories. This info helps techs fix issues faster.
Reports and analytics show trends in equipment performance. Teams can spot problem areas and make smart decisions.
Integrating with Other Systems
CMMS works best when linked to other business systems. This creates a smooth flow of data across departments.
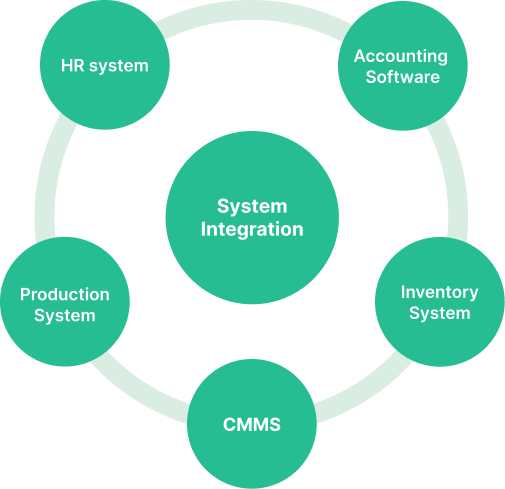
Source: WorkTrek
Connecting to inventory systems ensures parts are always in stock. When stock runs low, the CMMS can trigger automatic orders.
Linking to accounting software simplifies cost tracking. It’s easy to see how much is spent on each asset or repair.
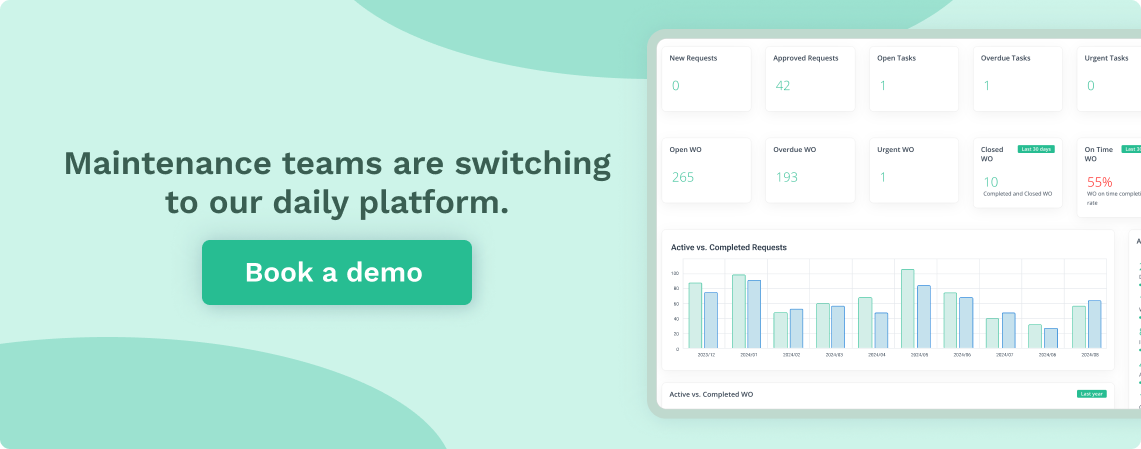
Integration with HR systems helps manage technician schedules. It ensures the right people are assigned to each job.
Tying into production systems allows for better planning and improved preventive maintenance activities. Maintenance can be scheduled during downtimes to minimize disruptions.
Mobile apps let technicians access the CMMS in the field. They can update work orders and check manuals on the go.
Monitoring and Improving Maintenance Processes
Tracking key metrics and constantly refining processes are crucial for an effective maintenance plan. These practices help identify areas for improvement and boost overall efficiency.
Key Performance Indicators (KPIs)
KPIs are vital tools for measuring maintenance effectiveness. Common maintenance KPIs include:
- Equipment uptime
- Mean Time Between Failures (MTBF)
- Mean Time To Repair (MTTR)
- Planned Maintenance Percentage (PMP)
- Overall Equipment Effectiveness (OEE)
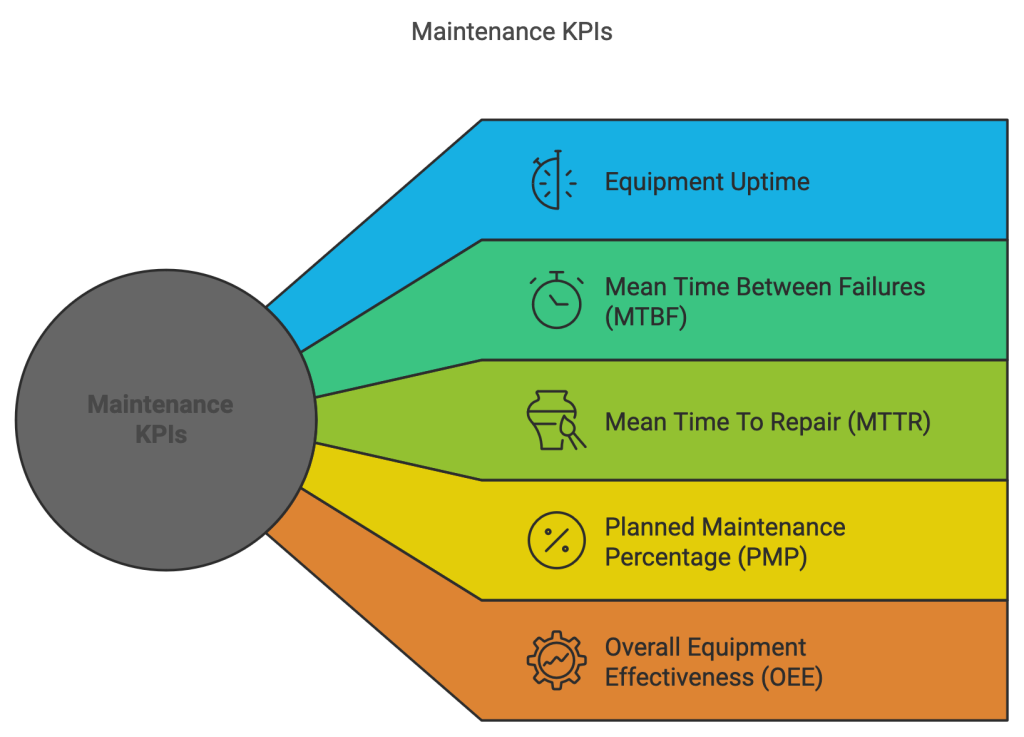
Source: WorkTrek
Tracking these metrics helps maintenance teams spot trends and make data-driven decisions. For example, a low MTBF may indicate the need for more frequent preventive maintenance.
Regular review of KPIs allows teams to set realistic goals and measure progress over time. This data-driven approach leads to more efficient resource allocation and improved equipment reliability.
Continuous Process Improvement
Maintenance processes should evolve to meet changing needs. Regularly reviewing and improving processes is key to maintaining effectiveness.
Steps for continuous improvement include:
- Gather feedback from maintenance staff
- Analyze maintenance data and KPIs
- Identify bottlenecks or inefficiencies
- Develop and test improvement strategies
- Implement successful changes
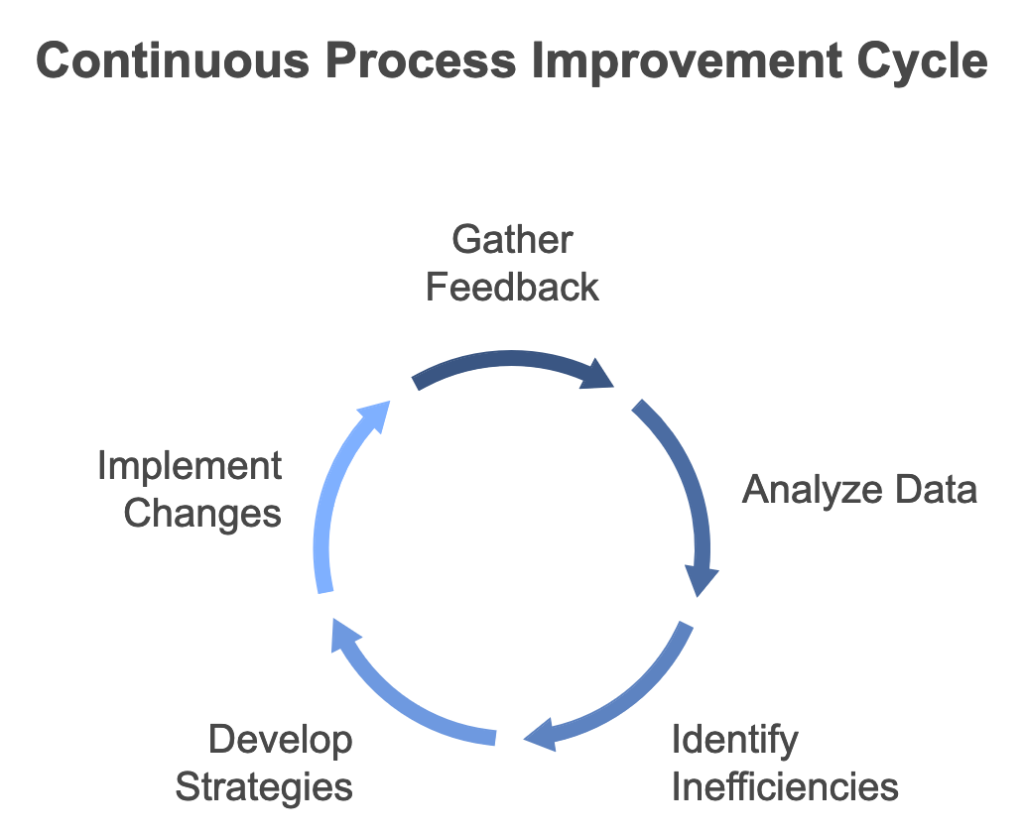
Source: WorkTrek
Encourage a culture of innovation where staff can suggest improvements. This approach helps identify practical solutions to everyday challenges.
Adopting new technologies, like predictive maintenance tools, can also enhance processes. These tools use real-time data to predict potential failures, reducing reactive maintenance tasks.
Ensuring Safety and Compliance
A good maintenance plan keeps workers safe and follows the rules. It helps avoid accidents and legal problems. Regular checks and fixes make equipment safer to use.
Adhering to Safety Standards
Safety rules are key for maintenance work. Develop clear safety policies for all tasks. Train workers on proper tool use and protective gear.
Set up safety checks before each job. Look for hazards like loose parts or electrical issues, and fix problems immediately.
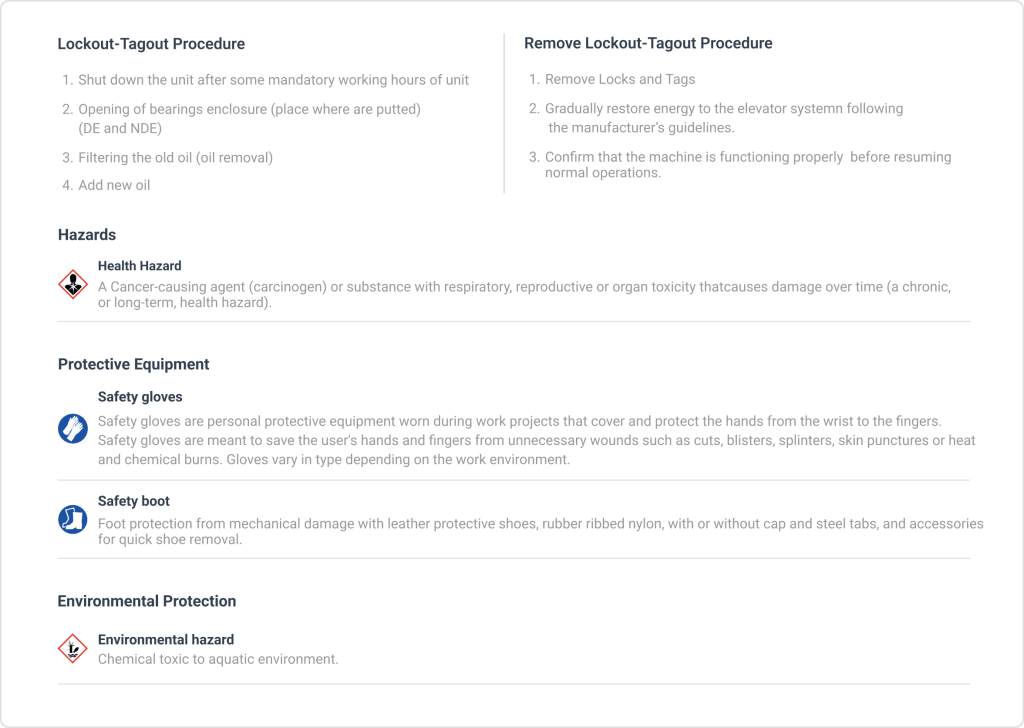
Source: WorkTrek
Use safety signs and labels on equipment. Mark danger zones.
Keep work areas clean and well-lit to prevent trips and falls.
Hold regular safety meetings. Discuss near-misses and ways to improve. Reward workers who follow safety rules well.
Environmental Regulations and Compliance
Maintenance must follow environmental laws. Employees must know the rules for handling chemicals and waste and use eco-friendly cleaning products when possible.
Set up proper disposal for oils, coolants, and other fluids. Don’t let these leak into drains or soil. Keep good records of all waste disposal.
Check air filters and emissions regularly. Fix leaks in air or fluid systems quickly. This will reduce pollution and save energy.
Stay current on changing laws. Join industry groups to learn about new rules. Train staff on environmental best practices often.
Create a plan to deal with spills or accidents. Have cleanup kits ready. Know who to call if there’s a big problem.
Reviewing and Adjusting the Maintenance Plan
Regular reviews of your maintenance plan are crucial for its success. Set up quarterly or annual review meetings to assess the plan’s effectiveness.
These reviews examine key performance indicators (KPIs) like equipment uptime, repair costs, and maintenance response times. Compare actual results to your goals.
Look for patterns in equipment breakdowns and failures. This can reveal areas where preventive maintenance needs improvement.
Get feedback from maintenance staff and equipment operators. They often have valuable insights into what’s working and what isn’t.
Use data from your computerized maintenance management system (CMMS) to inform decisions. This tool can provide detailed reports on maintenance activities and costs.
Be prepared to make adjustments based on your findings. This might include:
- Changing maintenance frequencies
- Updating maintenance procedures
- Investing in new equipment or tools
- Providing additional staff training
Remember, an effective maintenance plan is never static. It should evolve with your organization’s needs and technological advancements.
Continuously monitor the results of your adjustments. This ongoing process ensures your maintenance plan remains effective and efficient over time.
Conclusion
A solid maintenance plan is necessary for any business that uses equipment or facilities. The tips in this article can help you create a plan that works. Set clear goals, check how things are running now, and use preventive maintenance and software to stay on top.
Keep safety and compliance in mind, too. Review and adjust your plan often so it stays up to date. It might seem like a lot of work upfront, but it’s worth it. A good maintenance strategy saves you time and money in the long run. It means less downtime and fewer surprise costs.
Plus, it keeps your business running smoothly, allowing you to stay competitive. Ultimately, taking good care of your equipment and facilities is just business sense.