Get a Free WorkTrek Demo
Let's show you how WorkTrek can help you optimize your maintenance operation.
Try for freeMany organizations struggle with inefficiencies due to poor parts maintenance and storeroom operations, leading to frequent production delays, equipment downtime, and higher costs.
Without a well-organized system, companies risk overstocking, understocking, or not having critical components when needed. This results in lost productivity, increased maintenance expenses, and staff frustration.
Implementing a streamlined Parts Maintenance Storeroom operation ensures that parts are available when needed, reduces downtime, minimizes waste, boosts productivity, and optimizes inventory control.
Illustration: WorkTrek / Data: Maintenance Innovators
Listen to this Article
Fundamentals of Maintenance Storeroom Operations
In our experience working with various customers across industries, we’ve found that a well-run maintenance storeroom can keep operations flowing smoothly. It helps prevent downtime and ensures repairs happen quickly.
Defining the Maintenance Storeroom
A maintenance storeroom is a dedicated space for storing parts and tools needed for equipment repairs. It houses items like spare parts, lubricants, and specialized tools.
The storeroom serves as a central hub for maintenance teams. It allows quick access to needed materials, and proper organization can help the team quickly find the necessary parts.
Key features of a maintenance storeroom include:
- Shelving and storage systems
- Inventory tracking tools
- Safety equipment
- Clear labeling
A well-designed storeroom layout improves workflow. It reduces search time and boosts productivity.
The Importance of Efficiency and Reliability
Efficient storeroom operations can keep equipment running smoothly. They help avoid costly downtime and production delays.
Reliable storerooms ensure parts are available when needed. This allows for faster repairs and less equipment downtime.
Implementing a CMMS system like WorkTrek, can help you improve your storeroom operations. You can view all inventory on hand and, more importantly, set automated low-stock alerts.
Benefits of an efficient storeroom:
- Reduced maintenance costs
- Improved equipment uptime
- Better inventory control
- Increased worker productivity
Using technology like barcode scanners can boost accuracy. It helps track inventory levels and usage patterns.
Regular audits keep stock levels accurate. This prevents shortages of critical parts.
Strategies for Storeroom Optimization
Illustration: WorkTrek
Effective storeroom management boosts maintenance efficiency and cuts costs. Key strategies focus on inventory control, ongoing improvements, and proven methods.
Inventory Management Essentials
Inventory accuracy can smooth storeroom operations. Tracking parts using barcoding or RFID systems helps avoid stockouts and excess inventory.
Set up a clear labeling system. Group similar items together. This makes it easier to find parts quickly.
Implement a cycle counting program. Regular checks keep inventory records up-to-date. Aim to count high-value or fast-moving items more often.
Use min/max levels for each part. This helps automate reordering and ensures you have enough stock without wasting money on inventory.
Implementing Continuous Improvement
Create a feedback loop with maintenance staff. They can spot issues and suggest fixes, helping refine processes over time.
Track key metrics, such as stock turnover and stockout rates. Use this data to spot trends and make smart changes.
Regularly train staff on best practices. This keeps everyone up-to-date and working efficiently.
Look for ways to cut waste. This might mean finding better suppliers or adjusting order quantities.
Try new ideas on a small scale first. If they work, roll them out more widely.
Employing the Best Practices
Build a strong storeroom team. Assign clear roles and responsibilities. This helps ensure smooth operations.
Use a computerized maintenance management system (CMMS). It can track inventory, schedule maintenance, and generate reports.
Optimize your storeroom layout. Put fast-moving items in easy-to-reach spots. Use vertical space with shelving and racks.
Set up a system for handling urgent parts requests. This helps avoid delays in critical repairs.
Work closely with suppliers. Good relationships can lead to better prices and faster deliveries.
Maintenance Storeroom Layout and Organization
A well-designed maintenance storeroom improves efficiency and reduces downtime. Good layout and organization make finding parts quick and easy, saving maintenance teams time and money.
Effective Layout Planning
Illustration: WorkTrek
Efficient storeroom layouts maximize space and minimize part retrieval time. Start by grouping similar items. Put frequently used parts near the entrance. Store heavy items at waist level to prevent injuries.
Use clear aisles for easy movement. Label shelves and bins. Create a map of the storeroom for quick reference.
Consider workflow when planning. Place receiving and shipping areas near doors. Set up workstations for tasks like part kitting.
Organizational Systems for Storerooms
A good system keeps parts organized and easy to find. Use a mix of methods:
- Alphabetical order for small parts
- Numerical systems for larger inventories
- Color-coding for quick visual identification
Illustration: WorkTrek
Implement 5S principles in the storeroom:
- Sort: Remove unnecessary items
- Set in order: Arrange parts logically
- Shine: Keep the area clean
- Standardize: Create consistent procedures
- Sustain: Maintain the system
Use barcode labels or RFID tags to track parts. This improves accuracy and speeds up inventory checks.
Storage Solutions and Accessibility
Choose storage options that fit your needs:
- Shelving units for small to medium parts
- Pallet racks for large or heavy items
- Drawer systems for tiny components
- Vertical lift modules for space-saving storage
Ensure good visibility of stored items. Where possible, use clear plastic bins or open shelving. Install proper lighting throughout the storeroom.
Make frequently used parts easily accessible. Use ergonomic designs to reduce strain on workers. Consider mobile storage solutions for flexibility.
Implement a check-out system to track part usage. This helps maintain accurate inventory levels and prevents stockouts.
Inventory Control and Maintenance
Good inventory control helps keep costs down and parts available. It involves tracking stock levels, checking accuracy, and managing storage costs.
Utilizing a CMMS like WorkTrek you can set triggers when spare parts run low. You can also run reports to get up-to-date status on all spare parts in the organization.
Inventory Levels and Stocking
Proper stocking ensures parts are ready when needed. Too much stock ties up money, while too little causes delays.
Set minimum and maximum levels for each item. Use past usage data and lead times to decide amounts. Keep fast-moving parts well-stocked. Order slow movers only as needed.
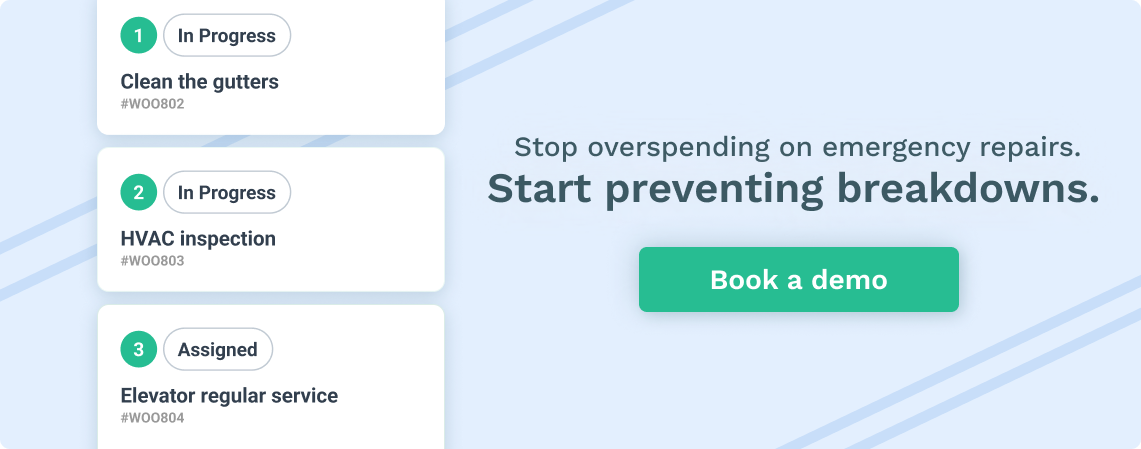
Source: WorkTrek
Consider safety stock for critical items. This extra inventory prevents stockouts during demand spikes or supply issues.
Review stock levels often. Adjust as maintenance needs change. Watch for obsolete parts and phase them out when equipment is upgraded.
Cycle Counting and Audits
Regular checks keep inventory records accurate. Cycle counting means counting a portion of stock each day or week.
Focus on high-value or critical items first. Count them more often. Use ABC analysis to group items by importance.
Compare physical counts to system records. Fix any differences right away. Look for patterns in errors to improve processes.
Do full audits yearly. This checks all inventory at once.
It takes more time but catches issues that cycle counts might miss.
Use barcodes or RFID tags to speed up counting. These reduce human error, too.
Managing Carrying Costs
Carrying costs are expenses for holding inventory. They include storage space, insurance, and lost investment chances.
Organization of the storeroom can cut storage costs. Use vertical space with proper shelving and group similar items together.
Track expiration dates to avoid waste. Rotate stock to use the oldest items first.
Consider vendor-managed inventory for some parts. The supplier keeps track and restocks as needed. This can lower your carrying costs.
Look at which parts are used the least. Can they be ordered just in time instead of stocked? This frees up space and money.
Tools and Technologies for Storeroom Management
Source: WorkTrek
Modern storeroom management relies on specialized tools and technologies. These systems help track inventory, automate processes, and improve efficiency. Let’s explore some key technologies used in maintenance parts storerooms.
Computerized Maintenance Management System (CMMS)
A CMMS is a powerful tool for managing maintenance operations. It helps track parts, schedule maintenance, and manage work orders. CMMS software can:
- Monitor inventory levels
- Generate reports on parts usage
- Create purchase orders automatically
- Track equipment maintenance history
Source: WorkTrek
This system connects different aspects of maintenance work. It allows managers to make data-driven decisions about inventory levels and part replacements.
Inventory Tracking Systems
Effective inventory tracking is crucial for storeroom management. Modern systems use barcodes or RFID tags to track parts. These technologies offer several benefits:
- Real-time inventory updates
- Reduced manual counting errors
- Easy location of parts in the storeroom
- Improved accuracy in stock levels
Source: WorkTrek
Barcode and RFID systems enhance inventory accuracy. They also speed up the process of finding and retrieving parts.
Automated Reordering and Labeling
Automation streamlines many storeroom tasks. Automated reordering systems can:
- Monitor stock levels
- Place orders when inventory is low
- Adjust order quantities based on usage patterns
Automated labeling systems print clear, consistent labels for parts. This improves organization and reduces errors in part identification.
These tools work together to create an efficient storeroom. They reduce manual work and improve accuracy in inventory management.
Maintenance and Repair Operations (MRO)
MRO helps keep facilities running smoothly. It involves managing parts, tools, and equipment to ensure efficient operations and minimize downtime.
Integrating MRO into Maintenance Strategy
MRO is essential for effective asset management. It helps organizations maintain equipment, handle repairs, and keep operations running.
A good MRO strategy includes:
- Regular equipment checks
- Timely repairs
- Proper inventory management
Companies should use MRO to reduce waste and lower costs. This can be done by organizing storerooms efficiently and tracking part usage.
Using software to manage MRO can improve results. It helps track maintenance schedules, parts inventory, and repair history.
Maintenance Budget Considerations
Setting an MRO budget requires careful planning. It’s important to balance cost control with the need for reliable equipment.
Illustration: WorkTrek / Quote: Plant Services
Key budget factors include:
- Equipment age and condition
- Replacement part costs
- Labor expenses for repairs
MRO spending typically ranges from 6% to 10% of a company’s total budget. This can vary based on industry and equipment needs.
Investing in preventive maintenance often saves money in the long term. It helps avoid costly breakdowns and extends equipment life.
Improving Equipment Reliability
Reliable equipment is key to smooth operations. MRO plays a big part in keeping machines running well.
Steps to boost reliability:
- Regular inspections
- Timely repairs
- Using quality parts
Predictive maintenance can spot issues before they cause breakdowns. This approach uses data to predict when repairs are needed.
Training staff on proper equipment use helps, too. It reduces wear and tear, leading to fewer repairs.
Keeping detailed maintenance records. It helps identify patterns and improve future maintenance plans.
Performance Metrics and Goals
Tracking the right metrics and setting clear goals is crucial for optimizing maintenance parts storeroom operations. By focusing on key indicators and targets, managers can drive continuous improvement and efficiency.
Key Performance Indicators (KPIs)
Mean Time Between Failures (MTBF) is a vital KPI for storeroom management. It measures the average time between equipment breakdowns, helping predict parts needs.
The parts turnover rate shows how quickly inventory moves. A higher rate often indicates better storeroom efficiency.
Stock-outs track how often requested parts are unavailable. Lower stock-out rates mean better parts availability and less downtime.
Inventory accuracy measures how well physical stock matches recorded levels. Higher accuracy leads to more reliable parts management.
Other useful KPIs include:
- Order fill rate
- Carrying costs
- Obsolete inventory percentage
Setting and Tracking Goals
Illustration: WorkTrek / Data: Collato
Storeroom excellence requires clear, measurable goals. Managers should set targets for each KPI based on industry benchmarks and company needs.
SMART goals work well for storerooms:
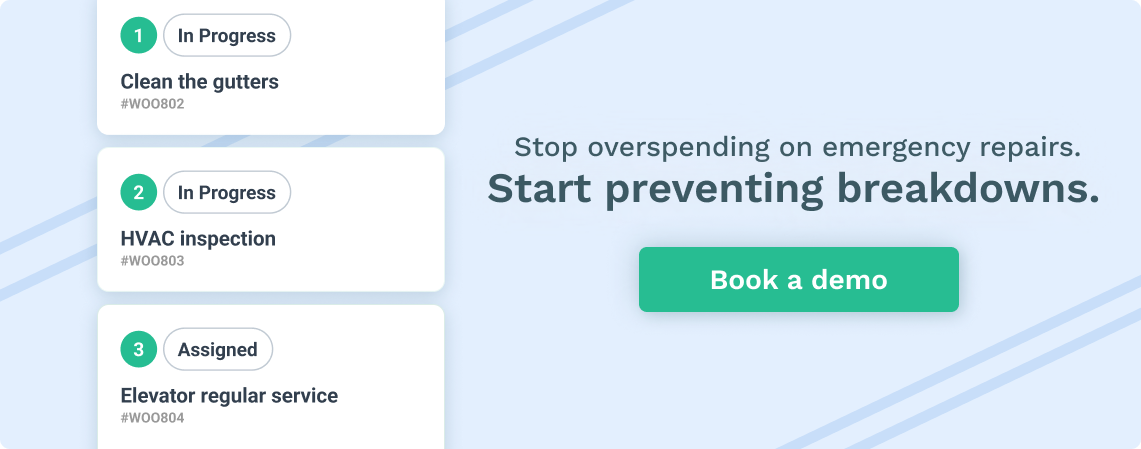
- Specific
- Measurable
- Achievable
- Relevant
- Time-bound
Example goal: “Reduce stock-outs by 25% within six months.”
Regular stick tests help track progress. These quick checks compare actual performance to goals.
Maintenance storeroom management software can automate data collection and reporting, making it easier to monitor KPIs and adjust strategies as needed.
Managers should review goals quarterly. They can then update targets based on progress and changing business needs.
Personnel and Training
Good staff and proper training are key to running a smooth parts storeroom. The right people with the right skills can make a big difference. Let’s examine the main parts of managing personnel in a maintenance storeroom.
Staffing and Job Requirements
Efficient maintenance parts storerooms need skilled workers. Jobs often include inventory managers, parts specialists, and storeroom attendants.
Inventory managers should be good with numbers and organizing. They need to know how to use inventory software.
Parts specialists must be knowledgeable about different types of parts and be able to find the right part quickly when needed.
Storeroom attendants keep the space clean and organized. They also help with receiving and organizing new parts.
All staff should be detail-oriented and able to work as a team. Good communication skills are a must for all roles.
Comprehensive Employee Training
Training can improve the productivity of the storeroom staff. It helps them do their jobs better and safer.
New workers should learn about:
- Parts identification
- Inventory systems
- Safety rules
- Storeroom layout
Ongoing training keeps skills sharp. Topics might include:
- New inventory methods
- Updates to parts catalogs
- Improved safety practices
Hands-on practice is important. Staff should get chances to use tools and systems in real situations.
Cross-training helps, too. When workers know multiple jobs, they can fill in where needed.
Standard Operating Procedures (SOPs)
SOPs are step-by-step guides for doing tasks. They help keep work consistent and safe.
Key areas for SOPs include:
- Receiving new parts
- Storing items correctly
- Picking and issuing parts
- Conducting inventory counts
- Handling hazardous materials
SOPs should be straightforward to follow. Pictures or diagrams can help explain the steps.
It’s good to review SOPs regularly. This helps keep them up to date with new practices.
Staff should help create and update SOPs. Their input makes the procedures more useful and practical.
Operational Excellence in the Storeroom
A well-run maintenance parts storeroom boosts efficiency and cuts costs. It provides timely parts access and optimizes inventory levels. Smart practices help storerooms better serve maintenance teams.
Storeroom as a Service Provider
The storeroom should operate as an internal service provider. It aims to meet maintenance needs quickly and accurately. Staff should be trained in customer service and parts knowledge.
Efficient storerooms use technology to streamline processes. Barcode scanners speed up part location and checkout, and inventory management software tracks stock levels in real time.
Clear communication is key. Storeroom staff should update technicians on the status of parts. They can suggest alternatives for out-of-stock items.
Performance metrics help measure service quality. Track metrics like order fulfillment time and accuracy. Use feedback to continuously improve processes.
Managing Parts Availability
Keeping the right parts in stock can help maintenance personnel perform their jobs quickly. Too much inventory ties up cash and too little causes delays.
A parts inventory planner should analyze usage data. They can set optimal stock levels for each item for storeroom personnel. Critical parts need higher stock levels to prevent downtime.
Source: WorkTrek
Regular cycle counts improve accuracy. Use ABC analysis to focus on high-value or fast-moving items. This ensures stock records match physical inventory and storage locations are optimized.
Build relationships with suppliers. Negotiate lead times and pricing. Consider vendor-managed inventory for some items. This can reduce carrying costs and stockouts.
Proactive Measures for Inventory Optimization
Preventive maintenance helps predict part needs. Schedule regular equipment checks. This can prevent unexpected breakdowns and emergency part orders.
Use data to spot trends in part usage. Look for patterns tied to seasons or production cycles. Adjust stock levels to match demand fluctuations.
Consider stocking kits for common repairs. This speeds up maintenance tasks and reduces the risk of forgetting needed parts.
When possible, standardize parts across equipment. This reduces the variety of items to stock and simplifies ordering and inventory management.
Review obsolete parts regularly. Phase out items for retired equipment. This frees up space and capital for needed inventory.