Get a Free WorkTrek Demo
Let's show you how WorkTrek can help you optimize your maintenance operation.
Try for freeThis article offers valuable guidance on managing operation and maintenance (O&M) to ensure your facilities and equipment function efficiently. By implementing these strategies, you can diminish expenses, avert breakdowns, and prolong the durability of your assets for effective O&M administration.
What does O&M management involve? Effective operation and maintenance (O&M) management involves strategic tasks, such as preventive maintenance and adherence to standard operating procedures, to reduce costs and extend asset lifespan.
Additionally, leveraging technology, like Computerized Maintenance Management Systems (CMMS), enhances O&M efficiency by centralizing information, optimizing asset use, and enabling predictive maintenance for improved reliability and minimized downtime.
Understanding Operation and Maintenance
Immersed in operations and maintenance, we engage in a complex environment where continual care for physical assets is essential. At its heart, O&M involves several critical components:
- Proactively tackling preventive maintenance tasks to address minor concerns before they become expensive repairs.
- Guaranteeing the uninterrupted operation of machines.
- Strategically coordinating upkeep schedules to ensure that properties remain in prime condition.
- Improving maintenance operations and asset management
O&M extends beyond mere mechanical adjustments or ticking items off a list. It represents a sophisticated integration of regular minor and routine maintenance efforts backed by profound technical know-how, which, if implemented effectively, can markedly reduce overall costs associated with maintaining equipment while prolonging asset longevity.
Maintenance workers keep detailed records and adhere to established operating procedures. They play a crucial role in ensuring facilities run smoothly and safely while aligning with the organization’s broader goals.
Importance of an Operation and Maintenance Manual
The operation and maintenance manual is a fundamental component of effective maintenance management. It is an indispensable guide for maintenance personnel, organizational managers, and third-party contractors. It outlines the intricate details of preventive maintenance tasks and other vital operational procedures to ensure adherence to quality standards.
Without a detailed and thorough operation and maintenance manual, companies risk falling into disarray due to unclear directives. This can lead to avoidable accidents, substandard quality control measures, and inconsistent practices across different departments or locations.
This document is critical in maintaining clarity among all stakeholders involved in upkeep processes by synchronizing their efforts towards safe and efficient facility operations.
Components of an O&M Manual
An operation and maintenance manual achieves its full potential by encompassing essential elements that transform it from simple text to a vital instrument.
Emergency procedures are among the most critical components, which offer precise guidelines for managing crises and ensuring coordinated actions during urgent situations. Equally important are the detailed descriptions of routine and corrective maintenance procedures designed to maintain machinery’s consistent operational integrity.
Incorporating standard operating protocols alongside robust safety guidelines enhances the effectiveness of this resource, which is the foundation upon which daily tasks rest securely.
Troubleshooting guidance equips maintenance technicians with the knowledge to resolve technical problems promptly, reducing operational disruptions while promoting a secure workplace setting. Careful compilation of these core components yields an O&M manual that informs and safeguards operations and refines the overall approach to equipment upkeep.
Source: WorkTrek
Types of O&M Manuals
Companies have different O&M manuals for different needs, just like surgeons have different tools for different procedures. Many maintenance manuals are often for different departments and areas in larger companies. These are tailored to the specific needs of each area. Here are some common types of operation and maintenance manuals:
- Manuals for product installation
- Comprehensive guides on operation and maintenance
- Instructions on troubleshooting and repair work
- Directives concerning safety protocols
- Handbooks for training purposes
Such resources act as exhaustive repositories in the maintenance world, delivering detailed guidance across various tasks through structured programs centered around maintenance manuals.
HR and Help Desk
Stepping outside technical boundaries, O&M manual content can extend into areas such as human resources management, customer or help desk support services, and emergency response procedures.
Each variant provides targeted navigational assistance pertinent to its sphere—whether managing software updates or conducting vehicle fleet inspections—to facilitate accuracy and efficiency in carrying out designated responsibilities.
Goals of Effective Operation and Maintenance Programs
The goals of O&M’s strategic domain are clear and ambitious. An effective O&M program aims to improve asset management, ensure operational efficiency, and prolong the lifespan of equipment.
It’s about achieving a harmonious balance between cost and performance, where reducing maintenance expenses aligns perfectly with preserving asset value.
One cannot overstate the importance of maintaining or improving product quality directly linked to the proper care of production equipment. These goals extend beyond the immediate to support broader outcomes such as realizing energy and water efficiency, improving resilience, and contributing to the organization’s overall operational success.
Effective O&M is thus a linchpin in an organization’s strategy to thrive in today’s competitive market.
Source: WorkTrek
Enhancing Asset Performance
Regular maintenance and comprehensive evaluations are crucial for consistently enhancing an asset’s performance. Understanding the intricacies of the asset’s operation ensures that equipment functions efficiently.
This extends the asset’s service life and improves its efficiency and reliability, significantly contributing to the company’s financial success through meticulous upkeep.
The alignment of scheduled maintenance tasks with precise data acts as a navigational tool, steering toward improved asset performance. When preventive care supersedes corrective action, outcomes undergo a marked transformation.
Consistent peak performance of physical assets, fewer breakdowns, and reduced repair costs are hallmarks of organizations that excel in strategic asset management practices.
Reducing Downtime and Failures
Imagine a scenario where machinery breakdown is an exception, not the norm. Proactive maintenance aims to establish such a scene. Conducting consistent examinations allows establishments to perform routine maintenance ahead of time, intercept serious malfunctions, and certify the dependable operation of equipment.
Preventative actions like applying lubricants or replacing filters defend against unscheduled operation halts, thus promoting seamless productivity. On the other hand, corrective or reactive maintenance steps occur only after problems emerge and often result in more regular operational interruptions.
This all comes down to striking an equilibrium between preventive measures and necessary interventions.
This is key for any organization’s upkeep plan. The Planned Maintenance Percentage (PMP) offers valuable insight into how much upkeep is executed proactively versus reactively. With the objective that planned procedures should ideally make up 90% while leaving just 10% for unplanned emergencies, the PMP shows commitment to efficient Operations and maintenance management.
Achieving a high PMP is not just about setting targets; it requires a systematic approach to planning and executing maintenance tasks. This includes leveraging advanced tools like CMMS to schedule regular inspections, track equipment performance, and ensure timely interventions before issues escalate. By consistently monitoring and adjusting maintenance strategies based on data-driven insights, organizations can optimize their PMP, leading to fewer unexpected breakdowns and a more reliable operational environment.
PMP and Organizational Culture
Furthermore, a high PMP reflects an organization’s proactive maintenance culture, prioritizing long-term asset health over short-term fixes. This cultural shift can significantly impact operational efficiency, employee morale, and customer satisfaction. Employees working in a well-maintained environment are likely to be more productive and engaged, while customers benefit from the reliability and quality of the services or products offered.
A high PMP can improve operational efficiency and contribute to sustainability goals. Proactive maintenance often involves energy-efficient practices and the timely replacement of worn-out components, which can reduce energy consumption and minimize waste. This aligns with broader environmental objectives and can enhance the organization’s reputation as a responsible and forward-thinking entity.
This approach minimizes downtime and prolongs asset lifetimes, ultimately enhancing investment returns.
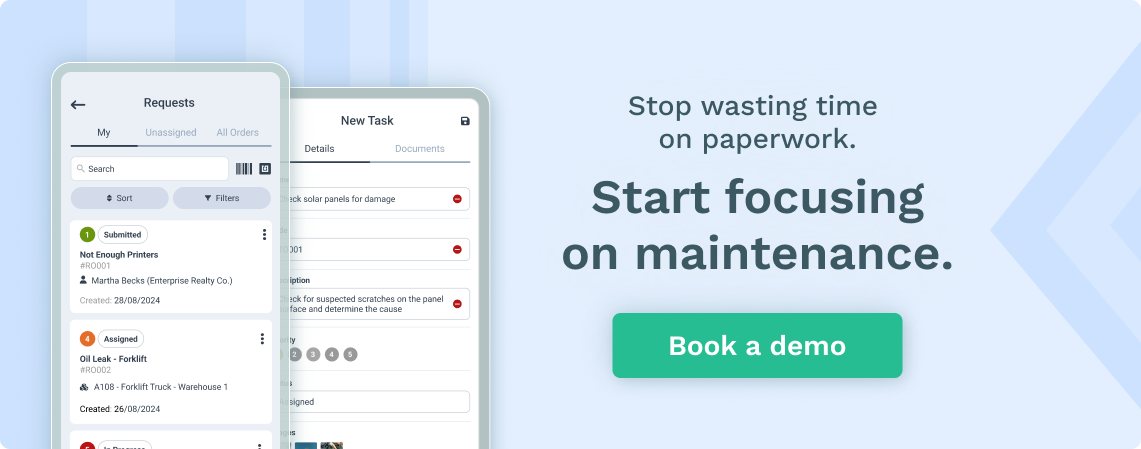
Promoting Safety Standards
Safety goes beyond mere regulatory compliance; it is a core principle in operations and maintenance. Inspecting equipment and maintaining high safety standards are essential to prevent accidents and ensure a secure workplace.
Implementing protective measures and routines within machinery highlights an organization’s commitment to safeguarding its workforce.
This is done by following the rules and continuously improving our quality control. This reduces risks and creates a culture of accountability and awareness. By having robust protocols, we protect our most valuable asset—our people.
Leveraging Technology for O&M Efficiency
In an age where technology reigns supreme, it’s no surprise that digital tools have become integral to operations and maintenance management. Enter the Computerized Maintenance Management System (CMMS), a game-changer that:
- Centralizes maintenance information
- Streamlines asset management
- Optimizes asset use and reduces excess costs
- Enhances the visibility of maintenance workflows
- Improve asset life cycles
- Provides invaluable tools for condition monitoring and predictive maintenance
- Centrally define maintenance schedule
- Get complete visibility of all maintenance work
- Define and communicate a central maintenance plan
Integrating advanced functionalities provides a comprehensive solution for managing maintenance activities efficiently and effectively. The CMMS enables organizations to track the lifecycle of their assets meticulously, ensuring that every piece of equipment receives the attention it requires at the right time.
Reporting and Analytics
Moreover, the system’s ability to generate detailed reports and analytics offers invaluable insights into asset performance and condition, allowing for data-driven decision-making. This proactive approach minimizes downtime, extends asset lifespans, and significantly reduces maintenance costs.
Additionally, the CMMS supports compliance with industry standards and regulations by maintaining accurate records of maintenance activities and inspections. This ensures that organizations can easily demonstrate adherence to safety and quality protocols during audits.
In short, CMMS is not just a tool for scheduling and tracking maintenance tasks; it is a strategic asset that empowers organizations to optimize their operations, enhance asset performance, and achieve long-term sustainability goals.
Source: WorkTrek
Work Order Management Process
A correctly implemented work order management system is the backbone of an effective Computerized Maintenance Management System (CMMS). This system enables preventive maintenance, boosts asset availability, and efficiently organizes essential data such as warranties and owner’s manuals.
It enhances maintenance operations by automatically creating work orders, assigning personnel, monitoring downtime periods, and appending relevant documentation.
As a subset of CMMS systems, the capabilities of a Work Order Management System include:
- Recording key performance indicators (KPIs) for maintenance activities
- Documenting extensive history logs for maintenance performed
- Facilitating managerial decisions through rich data analytics
- Fostering cost reduction alongside enhanced planning processes for upkeep tasks
- Optimizing task efficiency to ensure longevity in asset function
These advanced features provide managers with critical insights that foster informed decision-making. Such strategic advantages result in financial savings while refining the procedures around maintaining equipment—ultimately revolutionizing how organizations approach their maintenance management process.
Inventory Management Solutions
In operations and maintenance management, inventory management is essential. Most modern CMMS solutions, such as WorkTrek, offer full inventory functionality, including low-stock alerts. It also provides:
- Management of vendors
- Tracking costs associated with inventory
- Automatic replenishing of supplies
- Creating barcodes
- Monitoring spare parts
- Keeping tabs on stockroom levels
CMMS ensures materials are on hand when needed, offering a detailed picture of the material flow of MRO (Maintenance, Repair, and Operations).
The goal of these inventory management functions extends beyond just maintaining well-stocked inventories. They also ensure seamless operations without interruptions.
By efficiently managing their stocks through a capable CMMS system that handles diverse MRO materials and the complexities of maintenance tasks, organizations can avoid unnecessary expenses from overstocking and delays caused by stock shortages—all vital for achieving cost efficiency.
Predictive Maintenance Tools
Predictive maintenance tools provide a forward-looking perspective on equipment health, acting as a predictive crystal ball.
Distinct from preventive maintenance, which operates on a fixed schedule, predictive maintenance harnesses sensors and analytical data to foresee when components might be close to breaking down.
This intelligent approach extends component life and avoids breakdowns before they happen, redefining standards for executing maintenance operations.
Incorporating predictive maintenance into a Computerized Maintenance Management System (CMMS) takes advantage of regular activities, sensor outputs, and Internet of Things (IoT) technology to produce practical recommendations.
Advance alerts are provided if assets are nearing failure or not performing at their best, allowing maintenance teams to act quickly and efficiently. This proactive approach boosts asset dependability and ensures peak operational performance.
Source: WorkTrek
Creating an Effective Operation and Maintenance Manual
Creating a practical O&M manual is an intricate endeavor. It involves meticulous planning, thorough research, and the cooperative input of stakeholders to ensure that it is not only exhaustive but also intuitive for users.
Starting with a thoughtfully designed template that promotes easy navigation and includes visuals such as diagrams and illustrations can significantly enhance comprehension.
Updating Manuals
All of this hinges on keeping the manual current. Regular updates are crucial for maintaining relevance and ensuring safety. This dynamic document updates continuously to include new assets, accounts for changes within the facility, and integrates insights from everyday users.
As this process recurs over time, the O&M manual solidifies as an essential resource in guiding maintenance and operations staff by offering precise instructions they can depend upon.
Planning and Research
Establishing a robust O&M manual is essential during the planning and research stage. Initiating actions include:
- Determining the main objective of the manual.
- Recognizing who will be using the document.
- Conduct thorough discussions with engineers, technicians, and users to obtain specific technical information and valuable insights.
These key actions are instrumental in creating an accurate and relevant manual.
Incorporating primary research methods such as interviews with front-line personnel helps solidify content that accurately reflects daily procedures and best practices.
The input from a varied group, including management personnel, suppliers, and service engineers, is crucial to compiling an extensive body of knowledge within the manual that proficiently facilitates maintenance operations.
Source: WorkTrek
Designing a Clear Layout
A practical O&M manual excels in clarity and user-friendliness. It is structured to guide the reader from a broad overview to detailed procedures. Maintaining a uniform format that includes headers, subheaders, and bullet lists throughout the document transcends mere visual tidiness.
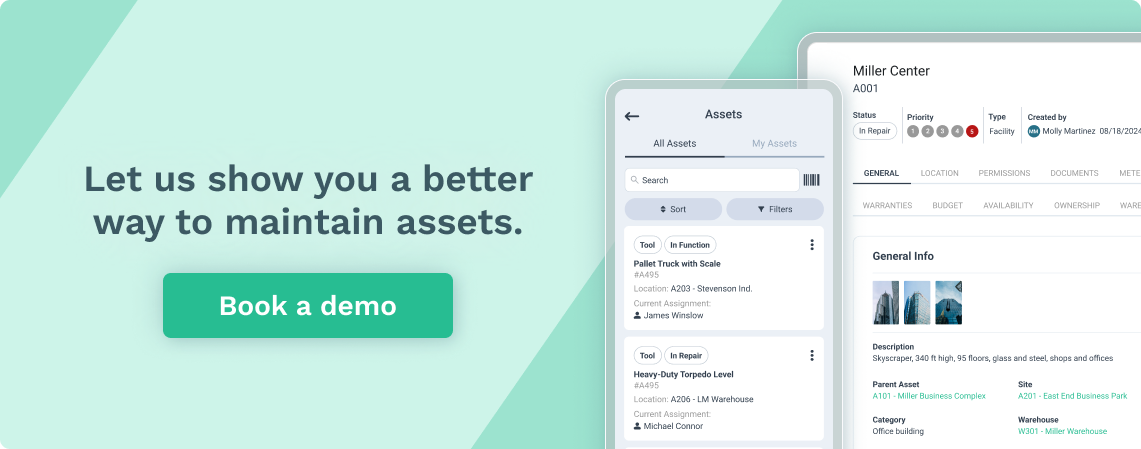
This consistency is crucial in minimizing confusion and efficiently retrieving essential information.
Several design components have been incorporated to augment the manual’s usability for navigation purposes.
- An exhaustive table of contents
- A thorough index
- Sections distinguished by color coding
- Important details accentuated with bold typeface
- Symbolic representation via icons
- Informational side panels
Incorporating these features transforms the manual into an intuitive reference that becomes critical for those involved in maintenance and operational roles.
Collaboration and Feedback
A guide that fails to connect with its audience is useless, much like a directionless map. It’s essential to engage those who use the equipment daily to craft a manual that informs and enables users.
The feedback gathered from these individuals is essential as it illuminates the practical aspects that need polishing. By integrating this input, the manual constantly adapts, becoming an active document always attuned to its organization’s needs.
Ongoing Communication
Ongoing communication should underscore the review process—a concerted effort to ensure contemporary workplace realities are mirrored in the manual’s contents. Keeping pace with new experiences and user insights ensures regular updates so that operational methods and safety protocols remain current within its pages.
This cycle of cooperation and perpetual refinement keeps an O&M (Operations & Maintenance) manual pertinent and instrumental for efficient practice.
Real-World Applications of O&M Programs
Seeing O&M in action is the best way to see the benefits. Building maintenance can mean anything from changing light bulbs to ensuring the heating and cooling systems run.
These programs are designed considering each facility’s specific requirements, including elements like the size of the building, its intended purpose, and the complexity of its systems.
Initiatives like the 50001 Ready program, which provides facilities with the resources needed to create an energy management system, clearly demonstrate a structured O&M strategy. This initiative highlights how integral O&D is to reaching sustainability targets by optimizing energy consumption and cutting operating expenses.
The positive outcomes of these operations across various sectors underscore the transformative power and robustness of O&M practices in enhancing different business functions.
Summary
The practice of operations and maintenance management is an essential field that ensures any institution’s sustained functionality and effectiveness. This involves carefully developing a maintenance manual and using advanced tools such as CMMS to embed O&M principles at the core, ensuring physical assets’ durability and optimal functioning.
Proper implementation helps preserve machinery and significantly minimizes expenses while upholding employee safety and health.
As we conclude our thorough review of operations and maintenance, let it serve as a stimulus for advancement within your enterprise. Take advantage of the knowledge imparted here to reinforce your approach to maintaining these systems.
Remember, achieving excellence in operations and maintenance is a continuous journey. Each proactive step enhances resilience, optimizes processes, and increases productivity, paving the way for your organization’s brighter and more prosperous future.
Frequently Asked Questions
What is the primary purpose of an operation and maintenance manual?
An operation and maintenance manual is designed to offer detailed, sequential guidance for carrying out preventive maintenance tasks, conducting safety inspections, and executing routine maintenance operations. Its core function is to establish uniform procedures and minimize the likelihood of accidents in the workplace.
How often should an operation and maintenance manual be updated?
An operation and maintenance manual must be periodically revised to incorporate information on new assets, modifications in facility operations, and the latest safety protocol and procedure updates to maintain relevance and accuracy.
What role does technology play in operations and maintenance management?
Computerized maintenance management systems (CMMS) harness technology to consolidate maintenance information, improve asset utilization, equip users with condition monitoring tools, and facilitate predictive maintenance. This integration boosts the efficiency and effectiveness of operations and maintenance (O&M) procedures.
What is the Planned Maintenance Percentage (PMP), and why is it important?
The Planned Maintenance Percentage (PMP) indicates the proportion of scheduled maintenance activities versus reactive activities. This metric is vital, as an increased PMP typically reduces downtime and maintenance costs while enhancing asset reliability and longevity.
Can predictive maintenance tools replace preventive maintenance tasks?
Certainly not. Predictive maintenance instruments complement preventive maintenance tasks rather than substitutes. They forecast possible breakdowns and facilitate opportune corrective actions that optimize component longevity and prevent malfunctions.
Maintaining regular preventive maintenance chores is crucial even when incorporating predictive technologies.