Get a Free WorkTrek Demo
Let's show you how WorkTrek can help you optimize your maintenance operation.
Try for freeSuccessful facility maintenance keeps buildings safe, efficient, and comfortable. It involves regular upkeep, repairs, and improvements to ensure everything runs smoothly. Setting clear goals for facility maintenance helps teams stay focused and achieve better results.
Facility managers and technicians struggle with maintenance issues that lead to costly breakdowns and unhappy occupants.
By setting smart goals, maintenance teams can prevent problems before they happen and create better spaces for everyone. Reducing equipment failures and downtime is often a top priority.
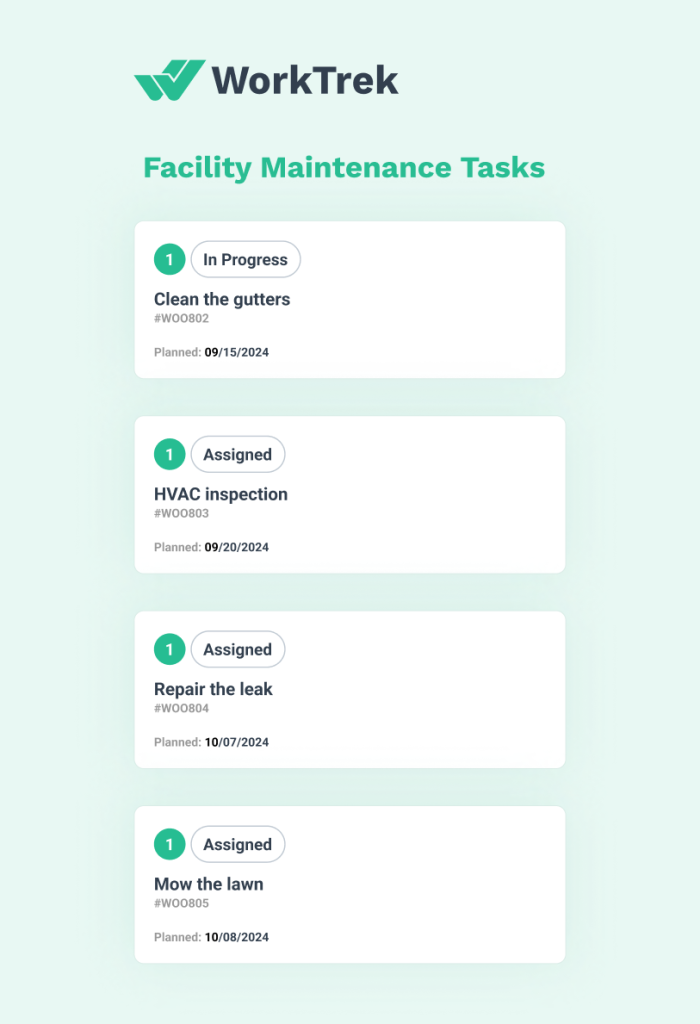
Source: WorkTrek
Facilities management goals include energy efficiency, safety, sustainability, and cost control. These goals help buildings last longer and work better.
Maintenance teams can significantly improve a facility’s performance with the right strategies and tools, such as computerized maintenance management systems (CMMS).
This article provides 8 goals for successful facility maintenance tasks.
Key Takeaways
- Clear maintenance goals help prevent costly breakdowns and improve building performance.
- Goals should address equipment reliability, energy use, safety, and sustainability.
- Regular inspections and proactive maintenance are key to meeting facility maintenance objectives .
Understanding Facility Maintenance
Facility maintenance keeps buildings and equipment in good working order. It involves different types of upkeep and repairs to ensure safety, efficiency, and longevity.
The Role of Facility Management
Facility management oversees the upkeep of buildings and equipment. It plans and carries out maintenance activities to keep everything running smoothly.
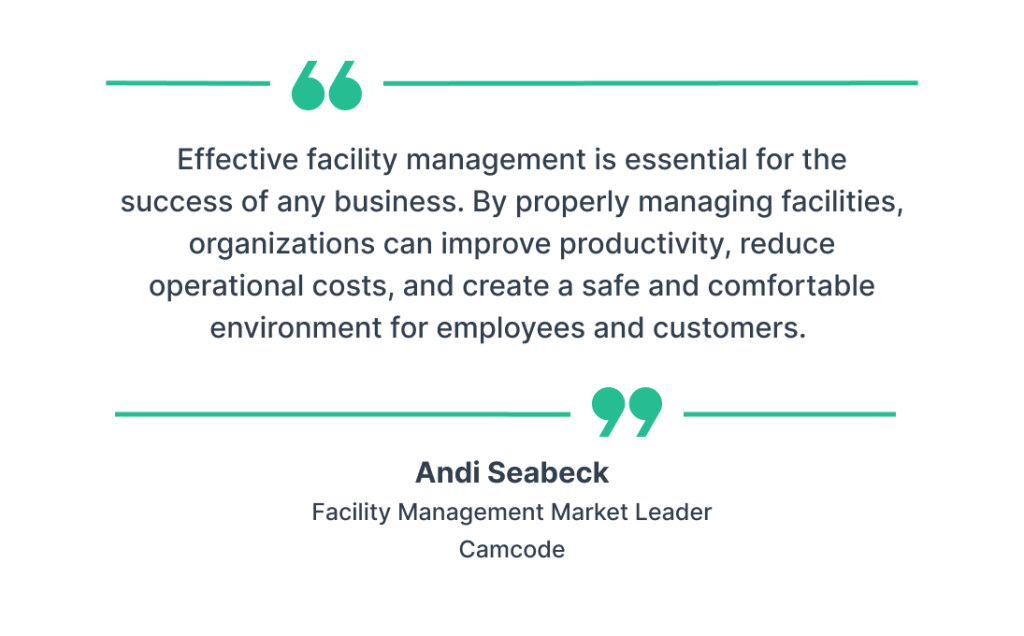
Illustration: WorkTrek / Quote: Camcode
Managers create schedules for regular checks.
Facility managers also look for ways to save money and energy. They might upgrade old systems to more efficient ones.
Types of Maintenance
There are several approaches to facility maintenance:
- Reactive maintenance: Fixing things after they break
- Preventive maintenance: Regular upkeep to avoid breakdowns
- Predictive maintenance: Using data to guess when repairs are needed
- Proactive maintenance: Fixing root causes of problems
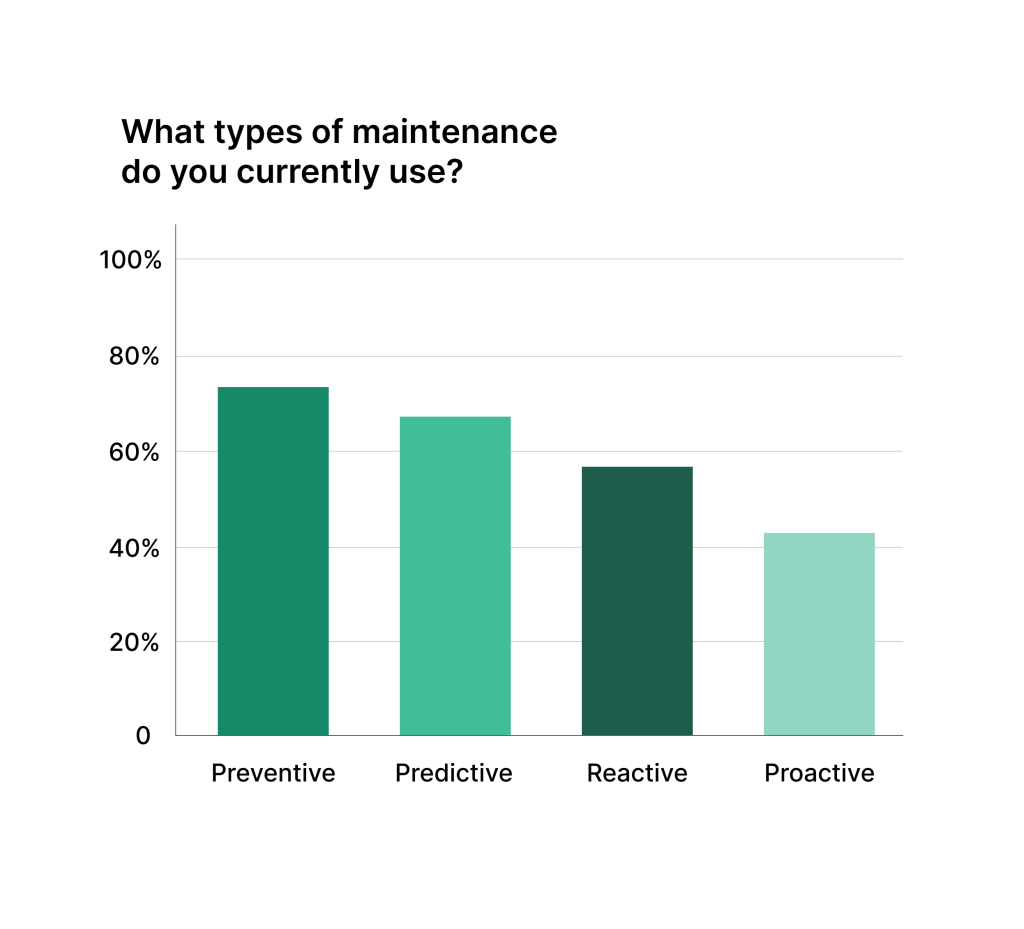
Illustration: WorkTrek / Data: ReliablePlant
Each type has its place in a good maintenance plan. Preventive maintenance helps avoid sudden breakdowns. It includes tasks like changing air filters or oiling machinery.
Predictive maintenance uses sensors and data to spot problems early. Fixing issues before they get worse can save money.
Proactive maintenance looks at why problems happen and tries to stop them for good. It might involve redesigning systems or changing how things are used.
1. Set Realistic Maintenance Goals
Setting clear goals is key for effective facility maintenance. Good goals guide teams and boost performance. They should be specific, measurable, and focused on efficiency.
Goal Setting Principles
The goals need to align with the facility’s needs. Look at past issues and plans. Pick the areas that need the most improvement.
Set both short-term and long-term goals. Short-term goals may aim to fix current problems, while long-term goals focus on preventing future issues.
Get input from maintenance staff. They know the daily challenges and their ideas can lead to more realistic and achievable goals.
Review and update goals regularly. What worked last year may not fit now. Be ready to adjust as needs change.
Specific and Measurable Goals
Measurable goals let teams track progress. Use numbers when possible. For example:
- Cut emergency repairs by 15% this year
- Complete 95% of scheduled maintenance on time
- Reduce equipment downtime by 20%
Make goals clear and simple. Everyone should understand what to do. Break big goals into smaller steps.
Use a mix of different goals. Some might focus on costs, others on safety or quality. This gives a complete picture of maintenance success.
However, safety guidelines should always be outlined, and safety standards must be followed.
Achieving Operational Efficiency
Efficiency goals help save time and money. They make the most of resources. Some ideas:
- Cut repair time by 10% through better parts inventory.
- Lower energy use by 5% with improved HVAC maintenance tasks. Even regularly cleaning filters can help improve energy efficiency.
- Increase productive work hours by reducing travel time between jobs
Track equipment histories to spot trends. This helps plan better maintenance schedules.
Train staff on new methods and tools. Skilled workers are more efficient. Set goals for training hours or certifications earned.
Use technology to boost efficiency. Set goals for adopting new software or automating tasks. This can speed up work and cut errors.
2. Develop a Maintenance Plan
A well-structured maintenance plan is key to keeping facilities running smoothly. It helps prevent issues, extends equipment life, and saves money.
Let’s explore the essential parts of a good plan.
Crafting a Maintenance Schedule
A maintenance schedule is the backbone of any good plan a facility manager creates. It lists all tasks and their due dates, including daily, weekly, monthly, and yearly jobs.
Routine Maintenance tasks might include:
- Checking HVAC filters
- Testing safety systems
- Cleaning gutters
- Inspecting roofs
- Check lighting features
- Ground Maintenance
- Test fire alarms & extinguishers
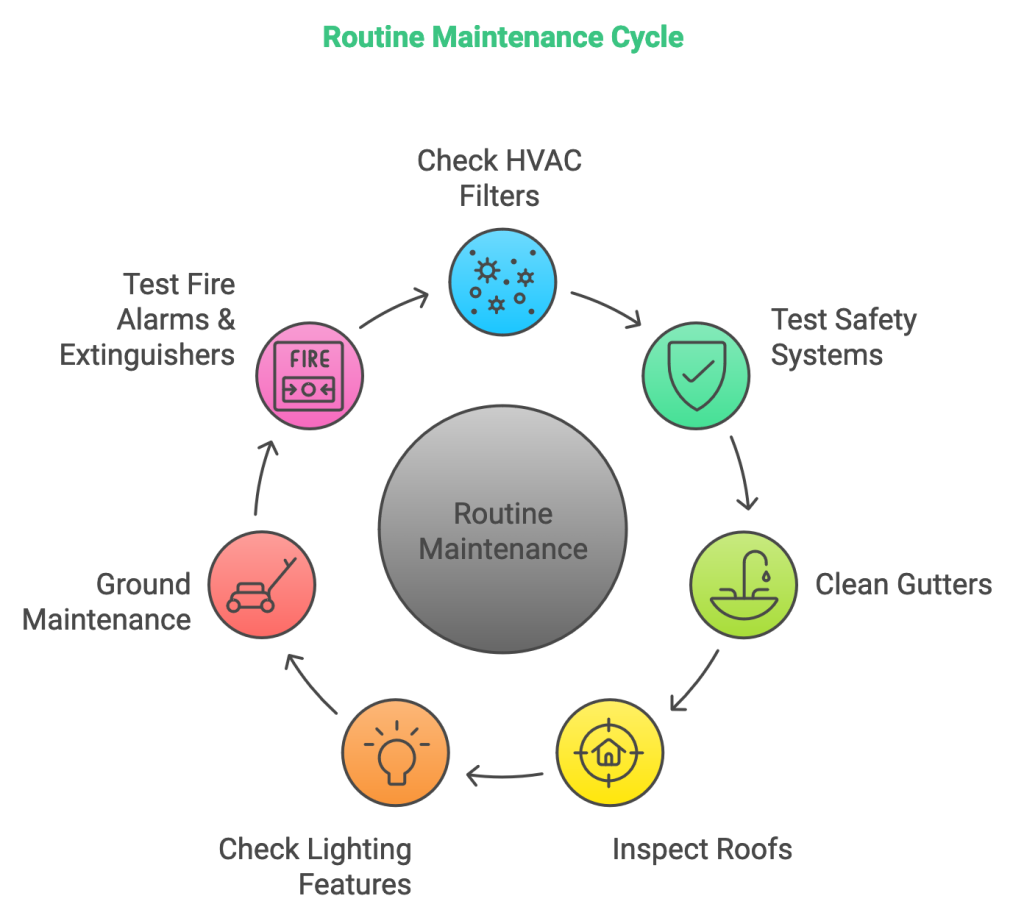
Source: WorkTrek
The schedule should be flexible and change as the facility’s needs change.
Use CMMS software to track tasks and send reminders. This helps ensure that nothing is missed.
Importance of Regular Inspections
Maintenance technicians should regularly catch small issues before they become big problems. They help keep the facility safe and working well.
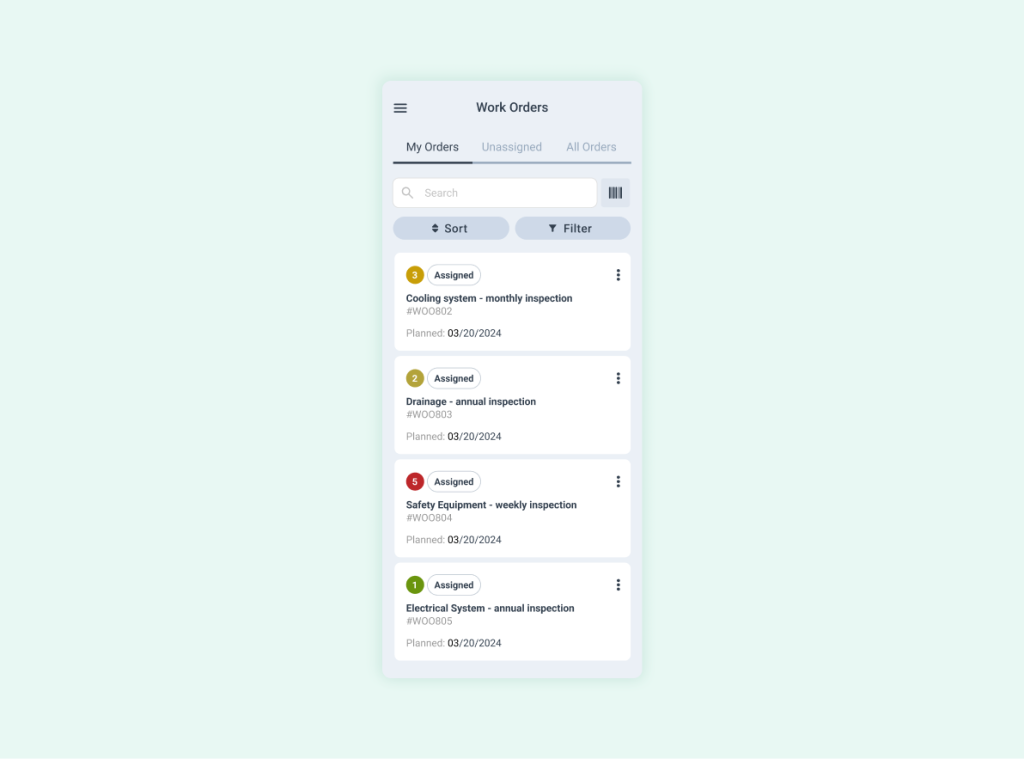
Source: WorkTrek
Inspections should cover all parts of the building.
Key areas to inspect:
- Electrical systems
- Plumbing
- Structural elements
- Safety equipment
Keep records of all inspections. Note what was checked and any problems found. This info helps plan future maintenance and spot trends. It also helps prove the facility is following safety rules.
Aligning with Best Practices
Using proven methods makes maintenance more effective and keeps operational costs low. It helps teams work smarter, not harder.
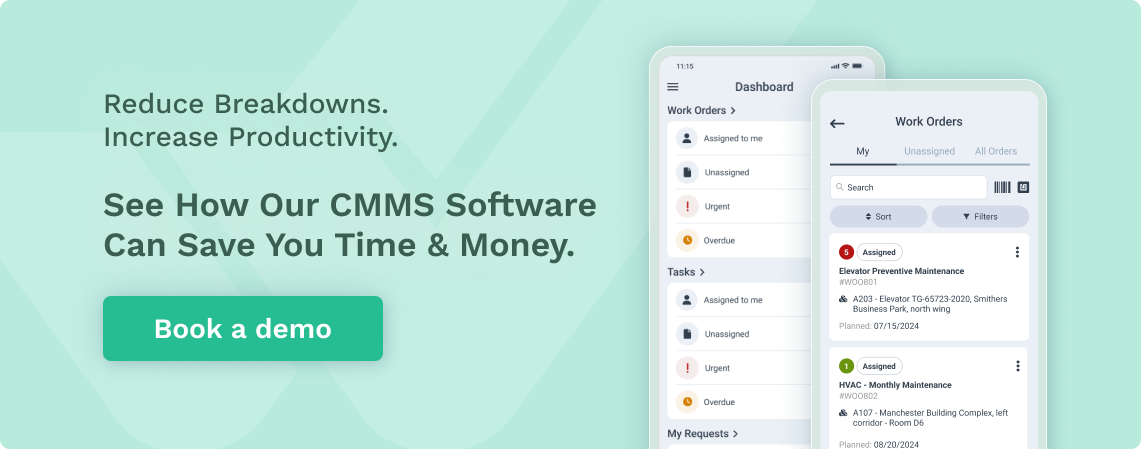
Best practices in facility maintenance are constantly changing as new technology is developed.
Some current best practices:
- Use data to make decisions
- Train staff regularly
- Adopt green maintenance methods
- Plan for emergencies
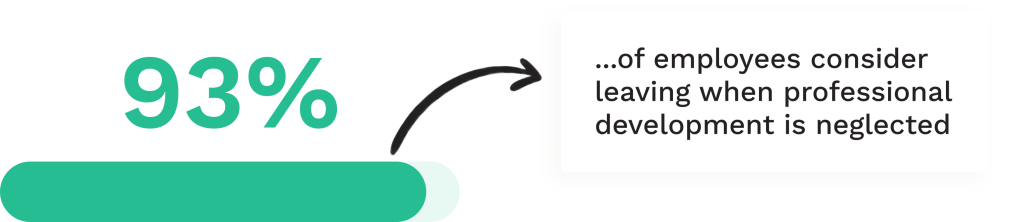
Illustration: WorkTrek / Data: Digital Adoption
Join professional groups and attend training to stay current on industry standards. This helps the team learn new skills and ideas and keeps the facility competitive and efficient.
3. Implement CMMS Software
Getting away from paperwork and using facility management software can help you meet your maintenance goals better. They help streamline operations, improve efficiency, and reduce costs.
Utilizing CMMS Software
CMMS software is a powerful tool for maintenance management. It helps track work orders, schedule preventive maintenance, and manage inventory. CMMS systems store equipment data, maintenance histories, and spare parts information in one centralized database.
Key features of CMMS software include:
- Automated work order generation
- Preventive maintenance scheduling
- Asset lifecycle tracking
- Inventory management
- Reporting and analytics
- Quickly outline Maintenance process and tasks
- Centralize all maintenance activities
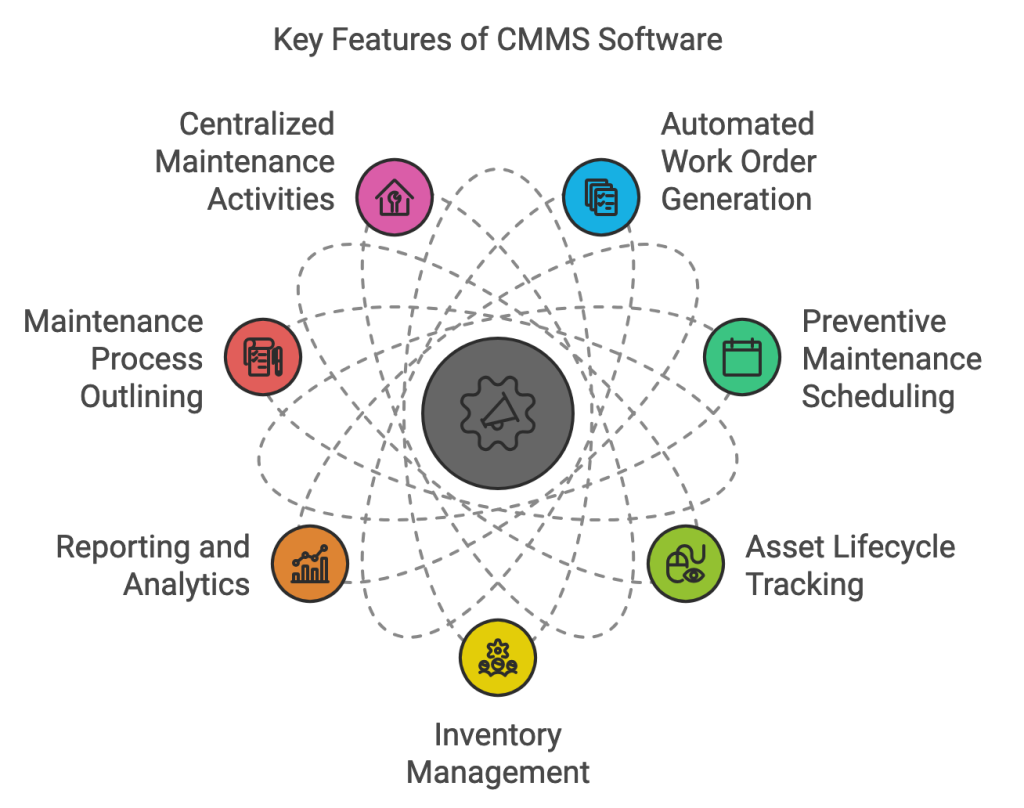
Source: WorkTrek
Computerized maintenance management systems improve communication between maintenance teams and other departments.
They also allow for better resource allocation and cost reduction and help identify recurring issues.
Benefits of Integrating IoT
The Internet of Things (IoT) is changing facility maintenance. IoT sensors collect real-time data on equipment performance and environmental conditions.
IoT integration offers several advantages:
- Predictive maintenance: Sensors detect potential issues before they cause breakdowns
- Energy optimization: Smart systems adjust heating, cooling, and lighting for efficiency
- Remote monitoring: Managers can track facility conditions from anywhere
- Data-driven decisions: Analysis of IoT data leads to better maintenance strategies
IoT devices can trigger automated work orders when they detect problems. This reduces response times and prevents minor issues from becoming major failures.
Asset Tracking and Management
Effective asset tracking and management are essential for facility maintenance. Good asset management extends equipment life and reduces replacement costs.
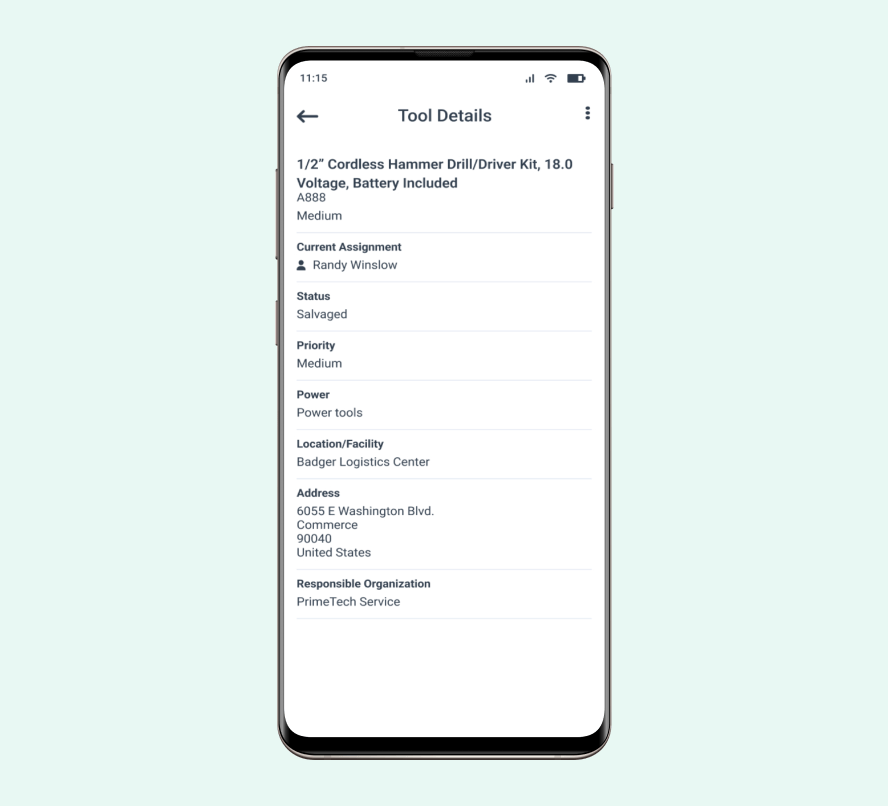
Source: WorkTrek
Key components of asset management include:
- Asset inventory: Detailed records of all equipment and systems
- Maintenance histories: Logs of all repairs and services performed
- Performance tracking: Monitoring of asset efficiency and downtime
- Lifecycle planning: Scheduling replacements and upgrades
Asset tracking systems use barcodes or RFID tags to monitor equipment location and status. This improves accountability and reduces the loss or theft of valuable assets.
Regular audits of asset data ensure accuracy and help identify opportunities for improvement. Good asset management leads to better budget planning and resource allocation.
4. Optimizing Maintenance Costs
Keeping maintenance costs low is key for any facility. Smart planning and the right tools can save money and time. Let’s look at some ways to do this.
Reducing Equipment Downtime
Downtime costs money. To reduce it, plan and create maintenance schedules for all machines, fix small issues before they become big problems, and train the maintenance team to spot trouble early.
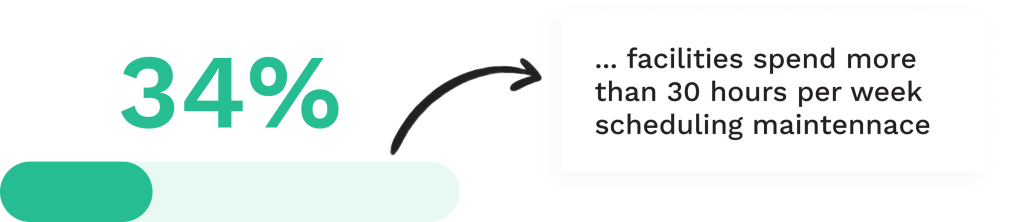
Illustration: WorkTrek / Data: FlagShip
Use tech to help. Put sensors on machines to catch issues quickly. This can stop breakdowns before they happen. Keep spare parts on hand for quick fixes.
Make sure everyone knows how to use and care for equipment. Good training means fewer mistakes and less downtime.
Cost Savings Strategies
Smart buying saves cash. Look for deals on parts and supplies. Buy in bulk when it makes sense. But don’t overstock – that ties up money.
Fix or replace? Know when each is best. Sometimes, a new machine costs less in the long run than fixing an old one.
Use energy-wise equipment. It costs more upfront but saves money over time. LED lights and smart thermostats cut power bills.
Teach your team about saving money. Every little bit helps; even small changes can add up to big savings.
Maintenance Cost Benchmarking
Compare your costs to others. This will show you where you can do better.
It would help to examine similar facilities to see how they manage costs.
Track your numbers over time. See if you’re improving—set goals based on these numbers.
Use software to gather and analyze data. It makes tracking easier and more accurate. Look at things like repair costs, energy use, and labor hours.
Share what you learn. If one area is doing well, find out why. Then, use those ideas in other places. Always look for ways to improve.
5. Focus on Safety and Compliance
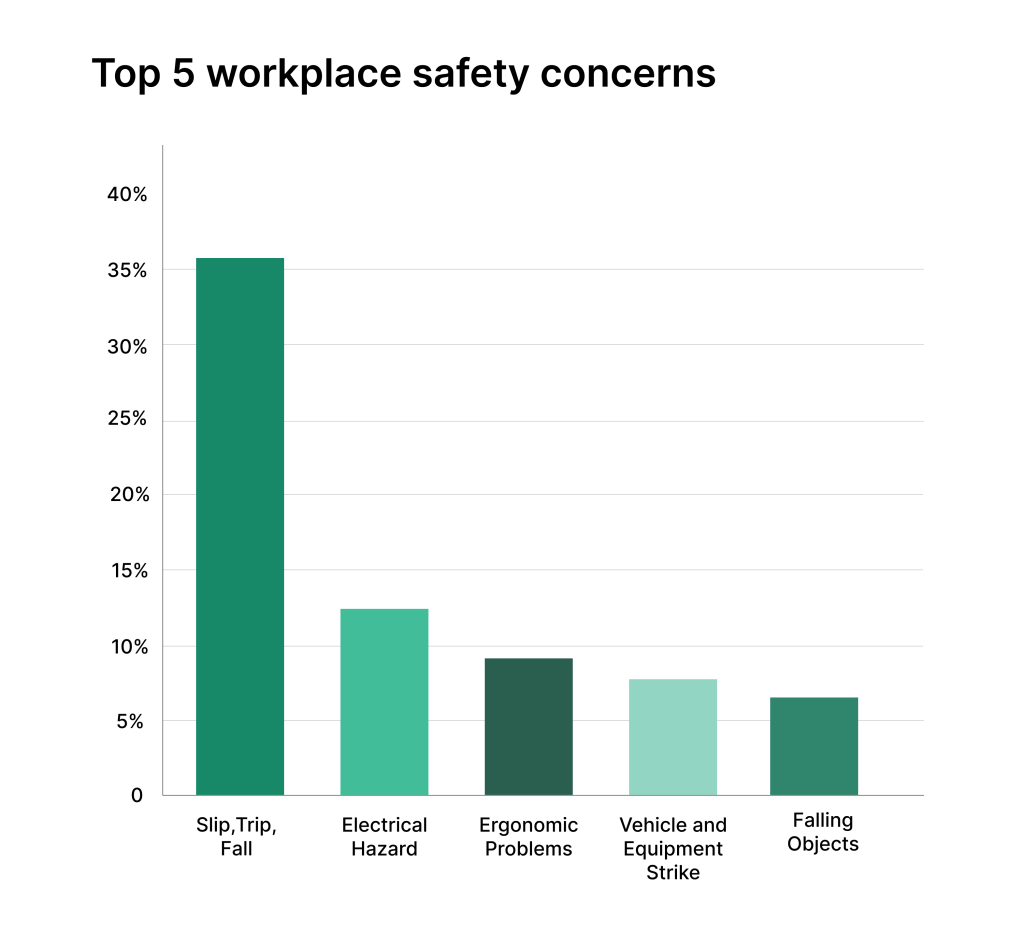
Illustration: WorkTrek / Data: 360training
Safety and compliance are key parts of facility maintenance. They keep people safe and follow important rules.
Adherence to Regulatory Standards
Facility managers must know and follow all safety rules, including building codes, fire safety, and health standards. Regular checks help catch problems early.
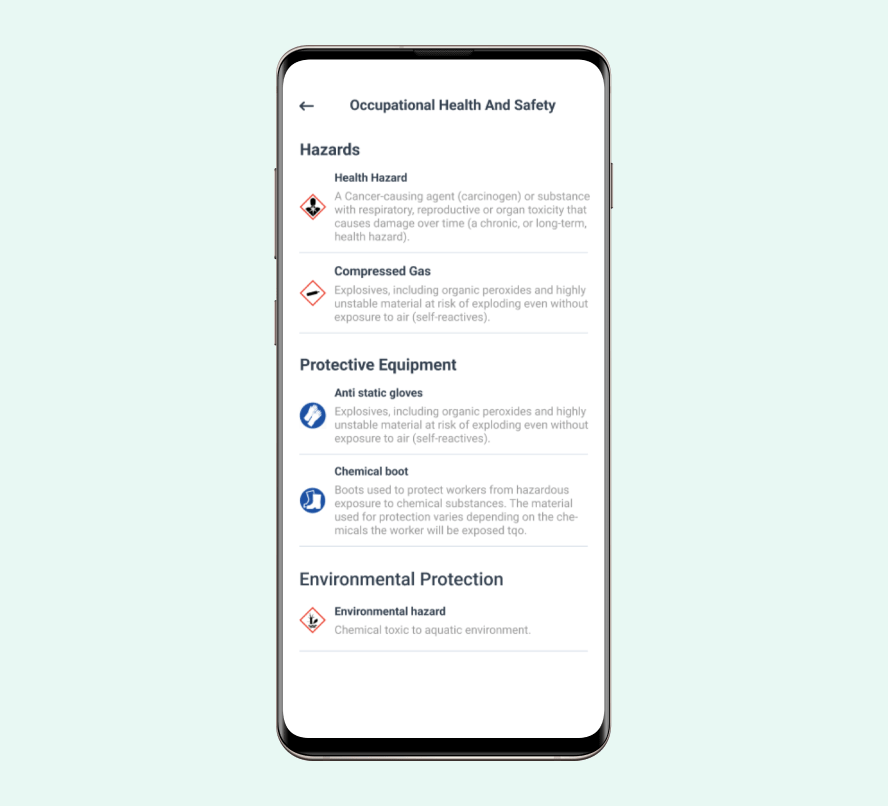
Source: WorkTrek
Regulatory compliance is a must for all facilities. It avoids legal issues and builds trust. Managers should keep good records of all safety efforts.
Facilities must meet ADA rules for access and follow environmental laws about waste and energy use.
Safety gear and emergency plans are also key.
Efficient Communication and Training
Clear safety info helps everyone stay safe. Signs, memos, and meetings can spread the word. Staff should know what to do in emergencies.
Regular training keeps safety skills sharp. This includes first aid, fire safety, and how to use safety gear. New workers need extra training on facility rules.
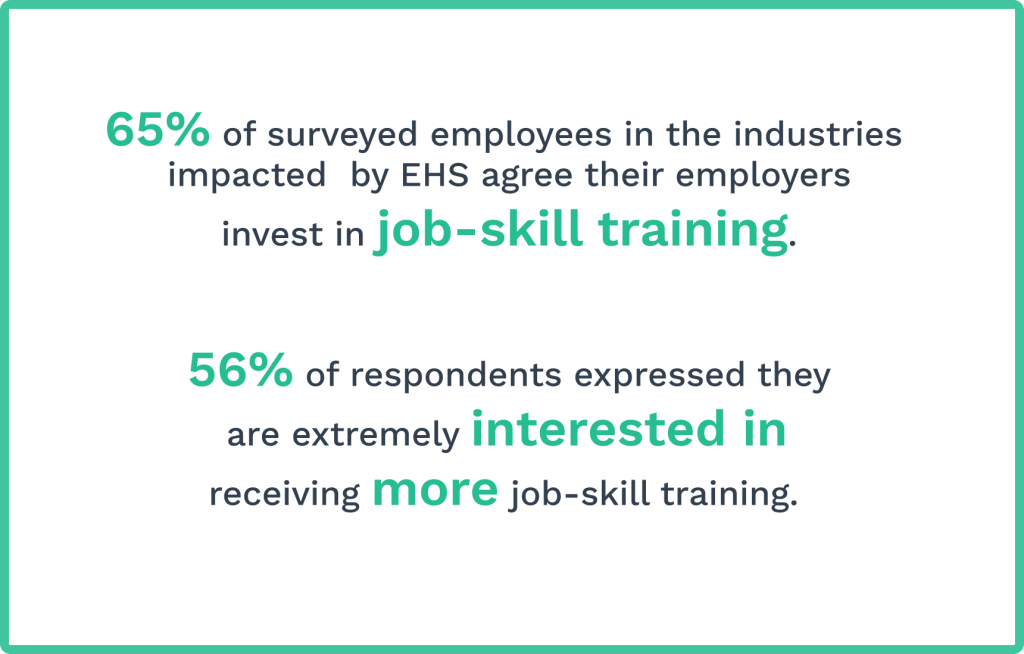
Illustration: WorkTrek / Data: 360training
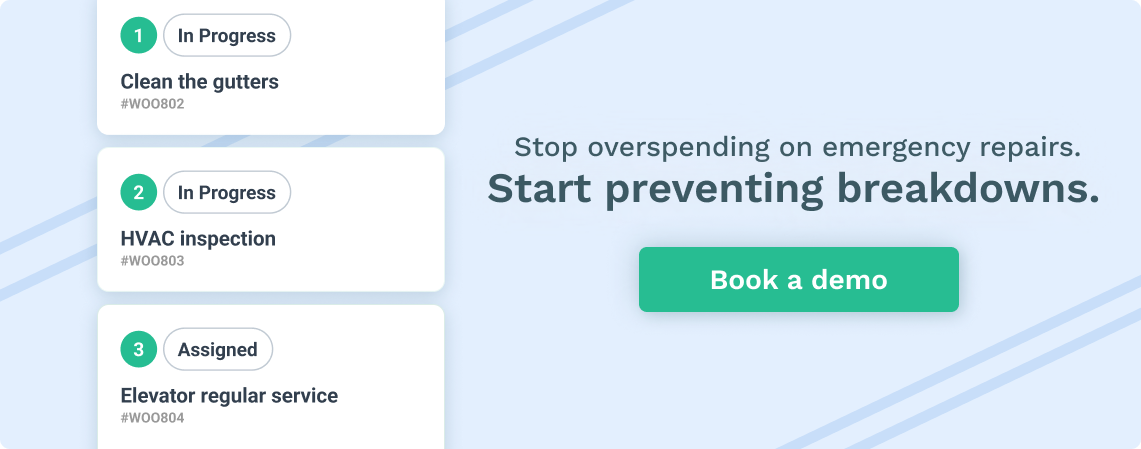
Drills help test emergency plans. They show what works and what needs fixing. After each drill, teams should discuss how to do better next time.
A good safety culture comes from the top down. Managers should lead by example and follow all safety rules.
6. Implement Sustainable Maintenance Practices
Sustainable maintenance practices focus on reducing environmental impact while improving efficiency. These approaches help facilities save money and resources over time.
Promoting Energy Efficiency
Energy efficiency is key to sustainable facility maintenance. Upgrading lighting systems to LEDs can significantly cut energy use. Regular HVAC maintenance ensures optimal performance and reduces waste.
Smart building technologies help monitor and control energy consumption. Automated systems can adjust lighting and temperature based on occupancy and time of day.
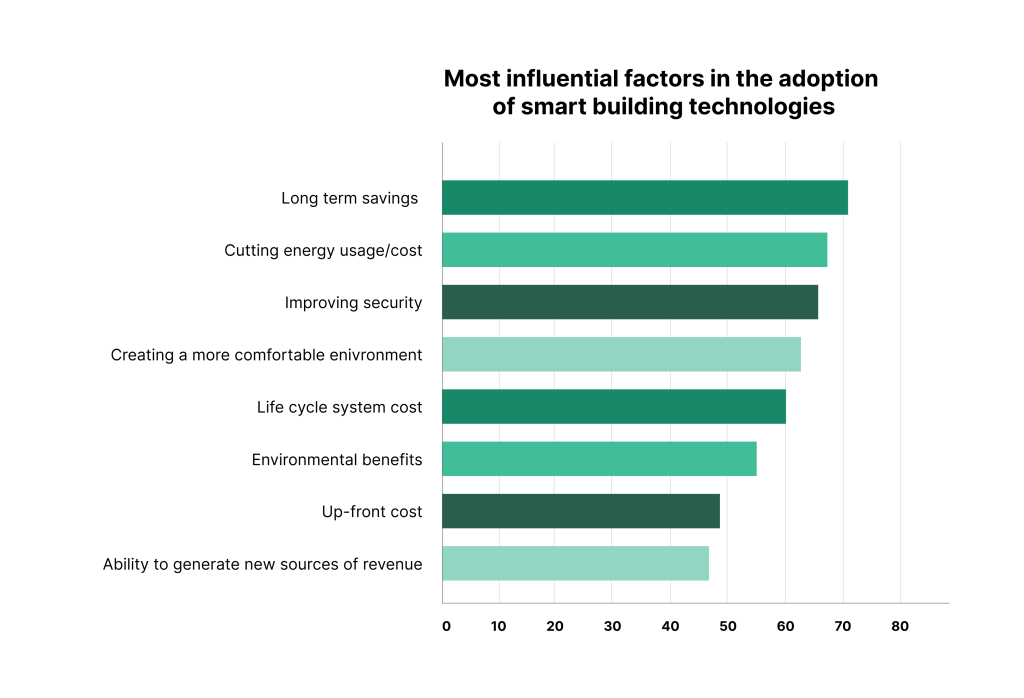
Illustration: WorkTrek / Data: Security Infowatch
Proper insulation and sealing of buildings prevent heat loss in winter and cool air escape in summer. This reduces the workload on HVAC systems and saves energy.
Train employees on energy-saving habits like you do with your family at home.
Simple actions like turning off lights and equipment add substantial savings when not in use.
Investing in Sustainable Equipment
Choosing sustainable equipment is vital for long-term facility maintenance. Energy-efficient appliances and machinery may cost more upfront but save money over time through lower energy bills.
Water-saving fixtures like low-flow toilets and faucets reduce water consumption. In some facilities, these devices can cut water usage by up to 30%.
Sustainable cleaning products and methods protect both the environment and employee health. Green cleaning solutions reduce harmful chemical exposure and minimize waste.
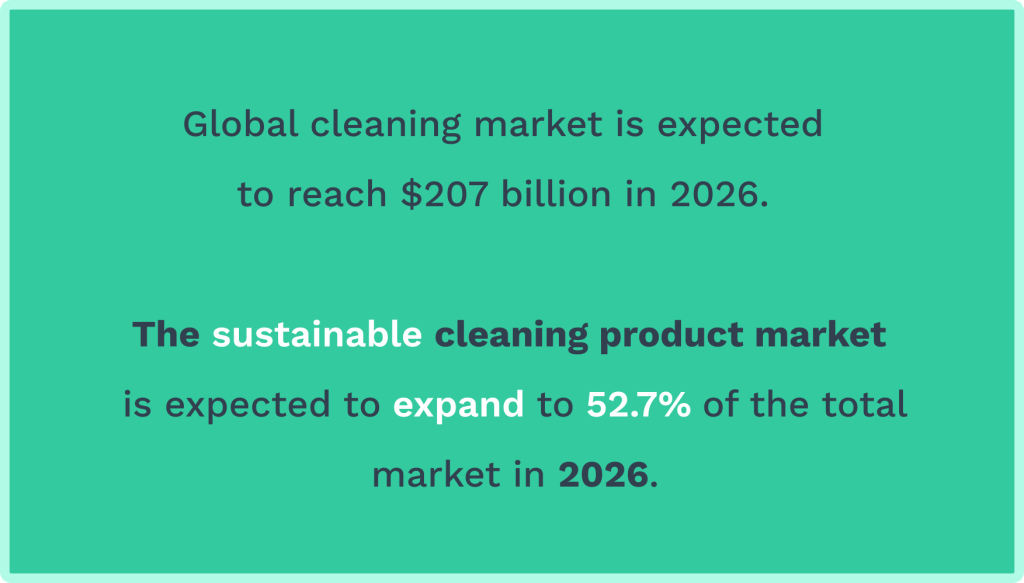
Illustration: WorkTrek / Data: Smithers
Renewable energy systems, such as solar panels or wind turbines, can power facilities partially or fully. These investments pay off through lower utility costs and reduced carbon footprint.
Regular maintenance of sustainable equipment ensures peak performance. This maximizes energy efficiency and extends the lifespan of eco-friendly installations.
7. Continuously Evaluate Maintenance Performance
Measuring and analyzing maintenance performance is key to improving facility operations. It helps identify areas for improvement and track progress over time.
Using Key Performance Indicators
Facility managers rely on key performance indicators (KPIs) to assess maintenance effectiveness. Common KPIs include equipment uptime, mean time between failures (MTBF), and maintenance backlog.
Equipment uptime measures the percentage of time assets are operational. A higher uptime indicates better maintenance practices.
MTBF tracks the average time between equipment breakdowns. Longer MTBF suggests improved reliability and maintenance.
The maintenance backlog shows the volume of pending work orders. A smaller backlog often points to more efficient workflows.
Other useful KPIs include:
- Asset lifespan
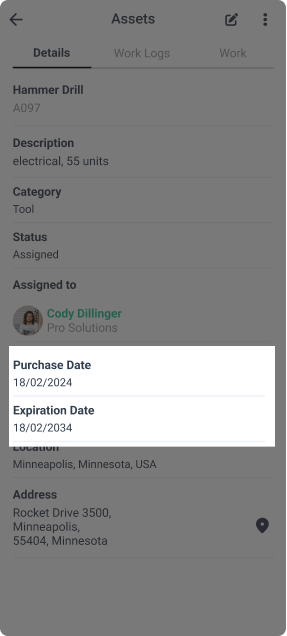
Soruce: WorkTrek
- Work order completion rate
- Energy efficiency
- Cost per maintenance task
- Safety protocols
- Space utilization
- Asset downtime
- Energy saving measures
- Centralize maintenance requests
Analyzing Maintenance Data
Regular data analysis helps optimize maintenance strategies. Managers should review KPI trends monthly or quarterly to spot issues early.
Comparing current performance to past data and industry benchmarks provides context. This helps set realistic goals for improvement.
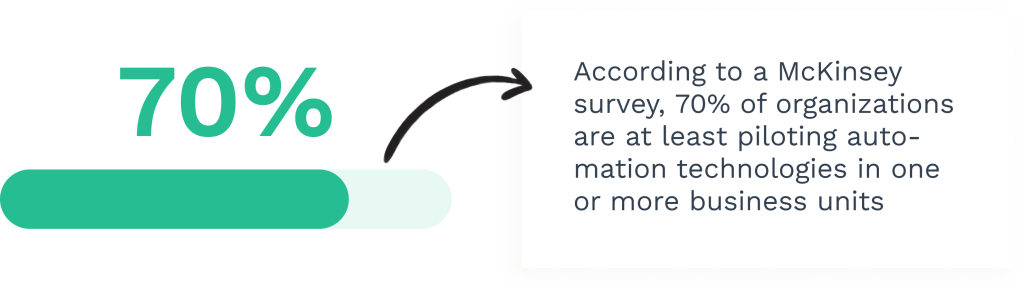
Illustration: WorkTrek / Data: pelican
Computerized maintenance management systems (CMMS) can automate data collection and analysis. These tools generate reports on key metrics, saving time and increasing accuracy.
Analyzing work order data can reveal common issues and bottlenecks in maintenance workflows. This information guides process improvements and resource allocation.
Tracking asset performance over time helps predict future maintenance needs and informs decisions about equipment replacement or upgrades.
Summary
In conclusion, achieving operational excellence in facility maintenance requires a thoughtful, proactive approach that balances reliability, efficiency, safety, and sustainability. Setting clear and measurable goals tailored to a facility’s needs is the foundation for success.
Prioritize preventive and predictive maintenance to reduce costly downtime and extend equipment’s lifespan. Implement energy-efficient upgrades and sustainable practices to reduce costs and environmental impact.
Leverage technology like CMMS and IoT to optimize processes and provide better visibility to maintenance tasks.
Equally important is fostering a skilled and informed workforce through regular training and open communication.
Regularly evaluating performance with key metrics allows facility managers to identify areas for improvement and adapt strategies as needs evolve.
Ultimately, a well-structured maintenance plan ensures smooth operations and creates safer, more efficient, and sustainable spaces for everyone involved.