Get a Free WorkTrek Demo
Let's show you how WorkTrek can help you optimize your maintenance operation.
Try for freeAre you struggling to enhance productivity in manufacturing? How can you improve manufacturing productivity? This article will guide you through essential tactics, including optimizing workflows, effectively training employees, and implementing cutting-edge technologies. Learn the steps to refine your processes efficiently and boost output.
Key Takeaways
- Conducted comprehensive workflow analyses and identified bottlenecks to improve manufacturing processes and boost productivity.
- Invest in employee training, cross-training, and performance incentives to create a skilled and motivated workforce.
- Implement automation and advanced technologies such as Robotic Process Automation (RPA) and IoT devices to enhance efficiency and reduce downtime.
Introduction
Productivity serves as a key indicator of competitive edge. Boosting productivity drives higher profits, unlocks the potential for reduced product pricing, and underpins the reduction of production costs—all crucial for elevating a manufacturing firm’s global stature.
Embracing an all-encompassing strategy that considers aspects beyond the manufacturing process—including personnel, technology, and production costs—can fundamentally transform business operations and help improve productivity.
Assess Current Manufacturing Processes
At this stage, it’s essential to thoroughly evaluate your manufacturing processes and pinpoint key areas ripe for improvement. This endeavor goes beyond mere minor adjustments. It involves a complete overhaul of workflows and systems to boost manufacturing productivity significantly.
The process starts with realizing that productivity is vital for financial success and creating more efficient production lines. To realize these goals, a carefully devised strategy to improve manufacturing productivity must be documented and implemented.
Conduct a Comprehensive Workflow Analysis
Source: WorkTrek
An in-depth review of your manufacturing process involves a comprehensive workflow analysis, providing insight into every aspect of your operations.
By carefully breaking down each phase, starting with the raw materials and moving through to the finished product, you reveal opportunities to enhance productivity and rapidly respond to changing market needs. As a manufacturing company, this can help your organization remain competitive.
The focus is on leveraging techniques such as value stream mapping and machine learning technologies—not just aiming for efficiency within manufacturing but positioning yourself at the cutting edge of productivity enhancement.
This step will also help establish best practices that can improve manufacturing productivity.
Identify Bottlenecks and Pain Points
Bottlenecks can significantly hinder productivity, acting as a barrier that can reduce production efficiency. For manufacturing companies, pinpointing these obstacles is critical to maximizing efficiency, improving employee productivity, and expediting a lucrative manufacturing process.
This involves analyzing the workflow to eliminate inefficiencies and implementing specific solutions to optimize your production lines, increase productivity, and eliminate waste for maximum efficiency and operational excellence.
Engage Employee Feedback
Listening to your employees’ valuable opinions is the key to enhancing manufacturing productivity. Their daily interaction with equipment and supplies gives them an unparalleled view into areas where efficiency could be improved and resources better utilized.
Inviting their input isn’t just about fostering a better workplace environment; it’s a strategic move that can lead to significant productivity gains and ultimately result in higher customer satisfaction.
Invest in Employee Training and Development
Investing in your team goes beyond mere altruism. It’s an essential tactic integral to boosting manufacturing productivity. Creating a workplace environment with growth opportunities ensures each staff member is prepared and confident in facing the complexities of today’s manufacturing floor.
This training serves more than just honing abilities. It aims to nurture a committed, effective, and constantly poised workforce to drive your manufacturing operations toward unprecedented success.
Source: Money
Implement Regular Training Programs
A vigorous training program serves as the core of a high-performing workforce, injecting vital skills and expertise that ensure your manufacturing procedures remain at the forefront of innovation.
It empowers your workers to spot areas for efficiency improvements and handle machinery with the expertise gained from continuous education and adaptation.
Cross-Train Employees
Cross-training enhances your production lines by creating a safety net that keeps the entire system functional if one component fails. It makes a versatile and proficient team capable of handling various roles and maintaining production levels even during unexpected disruptions.
Incentivize Performance
Incentives act as a catalyst that can improve productivity among your workforce. Offering recognition and rewards goes beyond merely expressing gratitude. It cultivates an environment where the quest for excellence is encouraged and achievements are commemorated—effectively enhancing manufacturing productivity.
Optimize Equipment and Maintenance
For any manufacturer, the harmonious hum of a smoothly running machine is akin to a musical masterpiece, with regular maintenance conducting this orchestral production.
Ensuring that machinery remains pristine is an essential element of the manufacturing process, as it guarantees each piece operates without fault and at peak efficiency.
Regular Maintenance Schedules
By sticking to a consistent maintenance routine, you ensure the durability of your manufacturing equipment and prevent unexpected failures that could hinder your operational efficiency. This proactive approach not only prevents complications but also creates an environment where interruptions in manufacturing are infrequent rather than commonplace.
Upgrade Outdated Machinery
Outdated equipment can become a significant bottleneck in your efforts to enhance productivity. On the other hand, investing in state-of-the-art machinery can drive progress by delivering greater speed, reliability, and efficiency. Such an upgrade is crucial for unlocking the full potential of your manufacturing process.
Monitor Equipment Performance
By tracking the performance metrics of your manufacturing equipment, you can unlock insights to enhance productivity. This monitoring system acts as a predictive tool, identifying and preventing issues before they arise. Such proactive maintenance strategies ensure that the machinery vital to production runs smoothly, thereby avoiding any disruptions in workflow.
Streamline Inventory Management and Boost Productivity
In manufacturing, inventory management is all about striking the right balance. Excessive inventory can lead to high costs, while insufficient inventory can cause production delays. Optimizing this crucial aspect involves maintaining the precise stock levels needed strictly when required to support your operational needs efficiently.
Implement Just-In-Time (JIT) Inventory
The Just-In-Time (JIT) inventory system, a technique that Toyota perfected, improves timing and precision, providing materials to the production line at the precise moment they are required without any premature delivery. This approach reduces excess inventory, cutting down on storage expenses, and cultivates a streamlined and flexible manufacturing process that can swiftly adapt to fluctuations in demand.
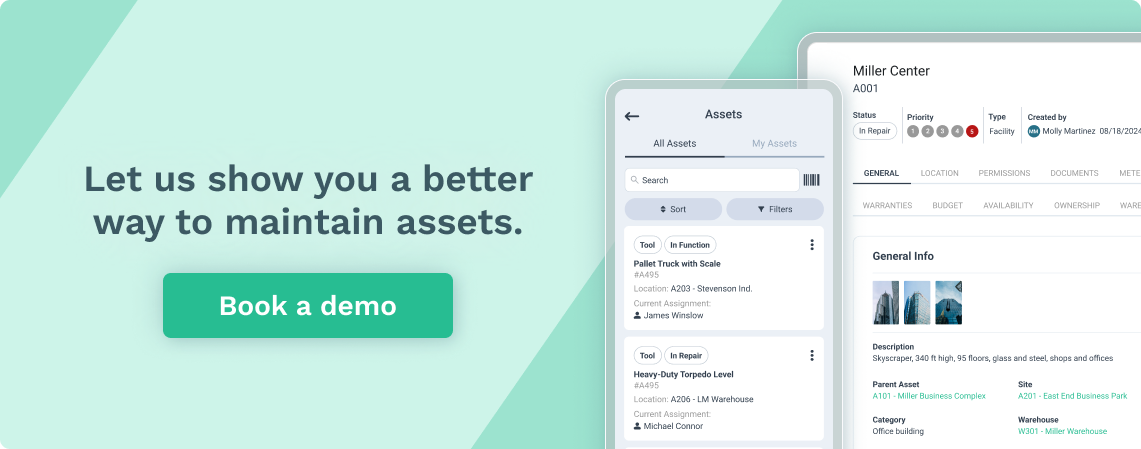
Use CMMS Systems
Computerized Maintenance Management Systems (CMMS) are pivotal in enhancing manufacturing productivity by streamlining maintenance operations and ensuring optimal equipment performance. By automating the scheduling and tracking of maintenance activities, CMMS software minimizes downtime and prevents unexpected breakdowns, leading to a more reliable production process.
The system’s ability to store detailed maintenance records and generate real-time reports enables manufacturers to identify recurring issues and implement preventive measures, thereby extending the lifespan of machinery and reducing repair costs.
This proactive maintenance approach boosts operational efficiency and ensures that production lines run smoothly with minimal interruptions.
Moreover, CMMS software facilitates better resource management by providing insights into inventory levels, parts availability, and labor allocation. This comprehensive visibility allows manufacturers to plan maintenance activities more effectively, ensuring that the necessary tools and spare parts are always on hand when needed.
Additionally, the system’s ability to track and analyze maintenance costs helps in budgeting and financial planning, allowing manufacturers to allocate resources more strategically.
By optimizing maintenance workflows and enhancing resource utilization, CMMS software significantly contributes to increased productivity, reduced operational expenses, and improved overall performance in the manufacturing sector.
Source: WorkTrek
Improve Supplier Relationships
Establishing strong partnerships with your suppliers involves more than just transactional exchanges. It’s a crucial step toward achieving manufacturing excellence.
Fostering these relationships can ensure a resilient and efficient supply chain, minimize disruptions, and maintain smooth production operations. Collaborating with reliable manufacturing partners is essential to upholding the consistency and reliability of your production processes.
Enhance Communication and Collaboration
A thriving manufacturing venture relies heavily on effective communication and teamwork, transforming isolated efforts into shared accomplishments. This includes tapping into the workforce’s collective intelligence, synchronizing plans, and ensuring that every component within the system operates in harmony.
Utilize Digital Communication Tools
In today’s digital age, technologies that facilitate rapid, transparent, and efficient communication significantly enhance manufacturing productivity. For instance, standardized messaging tools like Slack, MS Teams, or WhatsApp within the organization can streamline team communication.
Adopting applications and systems that unify teams, streamline processes, and promote clear communication will equip your operations with powerful tools designed to drive efficiency and success.
Foster a Collaborative Environment
Creating a work environment that encourages the exchange and growth of ideas builds a cohesive team and fosters a culture where innovation thrives and productivity soars. The true strength of collaboration lies not just in dividing tasks but in amplifying the creative energy within your workforce.
Streamline Supplier Communication
Maintaining clear and constant dialogue with suppliers is like having a well-drawn supply chain map—essential for managing manufacturing complexities without errors. The goal is to establish communication as reliable as the materials supplied, ensuring every order and delivery is timely, thereby enhancing a production process that operates with increased efficiency.
Implement Automation and Technology
Additionally, employing automation and technology can act as potent catalysts, improving the efficiency of your processes. These tools are valuable partners in freeing your workforce from repetitive tasks, thus enabling a harmonious collaboration where machines contribute accuracy and humans provide creativity—each leveraging their unique strengths within manufacturing.
Adopt Robotic Process Automation (RPA)
While this can be costly, implementing Robotic Process Automation (RPA) can improve efficiency for repetitive tasks. This approach can also help improve accuracy and steadiness, which are unique to machines. This technology is instrumental in relieving employees from monotonous tasks, thus enabling them to dedicate their efforts to creative problem-solving that propels productivity within the manufacturing sector.
For example, RPA can streamline inventory management by automatically updating stock levels and generating purchase orders when supplies run low, thus preventing production delays. Additionally, RPA can automate quality control processes by inspecting products for defects with high precision and consistency, reducing the likelihood of human error.
It can also handle data entry and reporting tasks, ensuring accurate and timely information flow across departments. By taking over these routine activities, RPA frees human workers to focus on more complex and value-added tasks, ultimately boosting overall productivity and operational efficiency.
Source: WorkTrek
Integrate IoT Devices
Incorporating the Internet of Things (IoT) into your manufacturing operations instills a layer of intelligent connectivity among equipment, granting them capabilities to:
- Engage in real-time communication and refinement
- Gather and scrutinize data using digital tools
- Oversee and manage procedures and improve manufacturing productivity
- Elevate efficiency and production rates
- Diminish instances of downtime as well as expenses related to maintenance
This advancement propels us towards an era where each sensor and piece of data unite to orchestrate a harmonious display of streamlined productivity.
Explore AI and Machine Learning
Artificial intelligence (AI) and machine learning are revolutionizing the manufacturing industry by transforming it into an arena where:
- Predictive analytics and intelligent automation have become standard practices
- Proactive measures can foresee and mitigate problems before they occur
- Managing processes and enhancing the process can lead to increased productivity
Leveraging these cutting-edge technologies empowers your business to scale production, continuously improve efficiency, stay at the forefront of innovation, and optimize overall performance.
Focus on Continuous Improvement
In manufacturing, the relentless pursuit of productivity is driven by a commitment to continuous improvement, focusing on improving efficiency. This process nurtures an environment where exceptional performance becomes the norm, and every incremental improvement signifies progress toward attaining peak operational excellence.
Lean Manufacturing Principles
Lean manufacturing is more than just a methodology; it’s a philosophy aimed at eradicating waste to uncover actual efficiency. By embracing its core principles, you can systematically eliminate all seven types of waste from your manufacturing process, creating an operation that is not only streamlined and adaptable but also steadfastly focused on delivering value to your customers.
Lean manufacturing originated from the Toyota Production System (TPS), which revolutionized the automotive industry by emphasizing the importance of continuous improvement and respect for people. The seven types of waste, known as “muda,” include overproduction, waiting, transportation, extra processing, inventory, motion, and defects. By identifying and eliminating these wastes, manufacturers can save significantly, improve lead times, and enhance product quality.
Furthermore, lean manufacturing encourages a culture of continuous improvement, known as “kaizen,” where employees at all levels are empowered to suggest and implement process enhancements. This collaborative approach boosts morale and drives innovation and efficiency throughout the organization.
Implementing lean principles requires ongoing training and development, ensuring the workforce is well-versed in lean tools and techniques such as 5S, value stream mapping, and Kanban Systems.
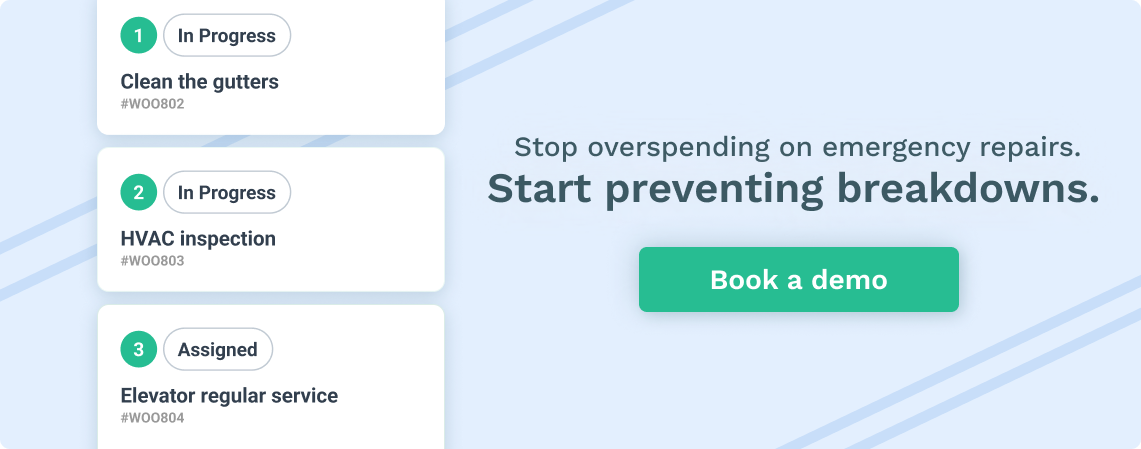
Ultimately, lean manufacturing is about creating more value for customers with fewer resources, fostering a sustainable and competitive manufacturing environment.
Six Sigma Techniques
Six Sigma represents the pursuit of excellence, embodying a systematic method to minimize errors and boost product quality. Employing its stringent DMAIC (Define, Measure, Analyze, Improve, and Control) methodology, it equips you with analytical tools to meticulously scrutinize and refine your manufacturing processes into exemplars of accuracy and dependability.
Six Sigma ensures that your manufacturing operations are consistently optimized by rigorously defining problems, measuring critical aspects of the process, analyzing data to identify root causes of issues, implementing improvements, and controlling future process performance. This methodology reduces variability and defects and enhances customer satisfaction by delivering products that meet or exceed expectations.
Furthermore, Six Sigma projects often lead to significant cost savings by identifying inefficiencies and eliminating waste within the manufacturing process. The data-driven approach of Six Sigma provides a clear roadmap for making informed decisions, ensuring that resources are allocated effectively and improvements are long-term sustainable.
By integrating Six Sigma principles into your manufacturing strategy, you can achieve higher efficiency, reduced production costs, and a competitive edge in the market.
Establish KPIs and Metrics
Tracking Key Performance Indicators (KPIs) provides quantifiable benchmarks that serve as navigational aids for enhancing productivity. These metrics do more than quantify success. They leverage live data to drive ongoing refinement within your manufacturing processes, thus laying the groundwork for perpetual advancement in manufacturing efficiency.
KPIs can encompass various aspects of manufacturing, including production output, machine utilization rates, defect rates, and on-time delivery performance. By setting measurable goals, manufacturers can monitor progress and identify improvement areas.
Regularly reviewing these indicators ensures that the entire team remains aligned with the company’s objectives, fostering a culture of accountability and continuous improvement.
Moreover, KPIs facilitate better decision-making by providing a data-driven foundation for strategic planning. For example, analyzing trends in machine downtime can highlight the need for maintenance or equipment upgrades, while tracking labor productivity can reveal opportunities for additional training or process adjustments. This proactive approach minimizes disruptions and maximizes operational efficiency.
A robust KPI tracking system also enables benchmarking against industry standards, helping manufacturers stay competitive. By comparing performance metrics with those of leading companies, organizations can adopt best practices and innovate to maintain a competitive edge.
Summary
As we navigate through the strategies for boosting manufacturing productivity, it’s clear that the path to excellence is paved with deliberate actions, targeted improvements, and an unwavering commitment to progress. From scrutinizing processes and investing in your workforce to embracing cutting-edge technologies and fostering a culture of continuous improvement, each step is a step towards a future where efficiency, quality, and innovation are not just goals but realities. Let this guide be the catalyst for transformation, inspiring you to implement these strategies and witness the flourishing of your manufacturing operations.
Frequently Asked Questions
How can we increase productivity in the manufacturing industry?
Enhancing productivity can be achieved in the manufacturing sector by boosting operational efficiency. This can involve examining and optimizing workflows, streamlining the process of ordering materials, pinpointing and addressing bottlenecks, educating workers, adopting automated systems to aid in tasks, ensuring a safe workplace for staff members, and keeping equipment adequately maintained.
How does investing in employee training contribute to manufacturing productivity?
Putting resources into employee training bolsters productivity in manufacturing by upgrading skills, minimizing mistakes, and fostering a better work environment. This advancement leads to heightened efficiency and sparks innovation.
Such an investment is closely linked with the uptick in productivity since employees who have received comprehensive training are more capable of refining tasks and confidently offering innovative contributions.
What is the significance of regular maintenance schedules?
Maintaining regular maintenance schedules is crucial for ensuring machinery remains in prime working order, thus avoiding unforeseen malfunctions and prolonging the equipment’s service life. Adhering to consistent upkeep reduces idle time and preserves operational efficiency, playing a pivotal role in enhancing productivity and minimizing costs associated with production.
How can Just-In-Time (JIT) inventory management impact manufacturing?
In manufacturing, JIT (Just-In-Time) inventory management enhances the production process by coordinating the timing of material orders with production timelines. This approach reduces storage burdens and lowers costs associated with holding inventory. Receiving materials precisely when necessary allows for a streamlined production that responds to demand fluctuations and efficiently minimizes waste.
Why is it essential to adopt automation and technology in manufacturing?
Incorporating automation and technology within the manufacturing sector is crucial as it decreases the time spent on manual labor, reduces the incidence of mistakes, and frees up human workers to concentrate on more complex tasks. This adoption boosts production efficiency while simultaneously cutting down on operational expenses.