Get a Free WorkTrek Demo
Let's show you how WorkTrek can help you optimize your maintenance operation.
Try for freeLearn about the integral MRO strategies—preventive, corrective, and predictive maintenance—and their roles in averting downtime and boosting equipment longevity. By unpacking these maintenance pillars, you’ll learn to craft an MRO routine that keeps your operations seamless and economically sound.
MRO is critical for industrial operations’ efficiency, safety, and sustainability. Though often categorized as indirect spending, it is essential for keeping the production process active without becoming a direct part of the final product. An effective strategy includes reactive preventive, corrective, and data-driven predictive maintenance. Hybrid approaches are common to ensure optimal infrastructure repair and maintenance activities.
Understanding Maintenance, Repair, and Overhaul
Maintenance, Repair, and Operations (MRO) is the foundational support for facilities and equipment. It includes regular maintenance work, precision repairs, and comprehensive refurbishments of machinery systems – a spectrum of tasks necessary to ensure constant operation within the industry.
The role that MRO plays is critical. It upholds operational efficiency, adheres to safety regulations, and keeps pace with technological innovation while embracing environmentally sustainable practices.
In terms of financial allocation, expenses related to MRO are frequently deemed indirect costs. These investments cover essential items that aid production and are generally considered maintenance supplies but do not become part of the end product. Such expenditures include purchasing.
- Spare parts
- Lubricants
- Repair tools
- Glues
It can also include other items vital for production equipment repair, such as safety equipment, cleaning supplies, power tools, hand tools, and even pest control—this encompasses safety gear crucial for preserving safe working conditions.
Office supplies are another vital component of MRO spending. They play an indispensable role in daily corporate operations by supporting administrative tasks and maintaining overall company efficiency.
Source: WorkTrek
Foundation of MRO: Preventive, Corrective, and Predictive Maintenance
Examining the strategies that bolster Maintenance, Repair, and Operations (MRO), we find a comprehensive approach. At its core are three essential components: preventive, corrective, and predictive maintenance. These strategies each serve unique functions, but when combined, they work harmoniously to deliver the best outcome: reducing equipment downtime.
The objectives of these strategies include:
- Preventive maintenance aims to preempt equipment breakdowns.
- Corrective maintenance addresses identified issues to reinstate functionality.
- Predictive operation leverages data analysis tools for foreseeing impending malfunctions.
Many organizations integrate corrective actions and preventive measures into their comprehensive strategy for ongoing facility management activities to guarantee robust infrastructure repair and the upkeep of their equipment systems.
This dual approach ensures that immediate issues are addressed promptly while preventing future problems.
By combining these two maintenance strategies, organizations can create a balanced and effective MRO program and improve customer satisfaction. This integrated approach enhances equipment reliability and performance, improving operational efficiency and cost savings.
Source: WorkTrek
Preventive Maintenance
Preventive maintenance is a systematic and scheduled approach to equipment upkeep that prevents unexpected failures. It goes beyond routine tasks and represents a proactive effort to enhance the longevity and reliability of vital machinery within the production process.
The primary goal of preventive maintenance is to ensure continuous operations by avoiding unplanned stoppages due to equipment breakdowns.
A variety of methods are utilized by those specialized in maintenance as part of their preventive efforts. Such practices include:
- Conducting consistent examinations
- Applying lubricants where necessary
- Making precise adjustments
- Executing comprehensive cleaning regimes for machines
- Replacing components before they fail
- Carrying out exhaustive inspections biannually or annually
Regular preventive maintenance helps identify potential issues before they become critical. In contrast, corrective maintenance ensures that problems are swiftly dealt with, maintaining a smooth and continuous production process.
Corrective Maintenance
Corrective maintenance is initiated after a malfunction is identified and designed to quickly and effectively restore equipment operation. This approach helps minimize the occurrence of emergency maintenance situations and promotes enhanced safety measures.
While inherently reactive, this type of maintenance may occur during routine preventive checks or via specific work orders dedicated to fixing and inspecting for potential issues that might lead to future operational disruptions if ignored.
Can Corrective Maintenance Lower Costs?
Though it responds reactively to problems as they arise, corrective maintenance typically incurs lower initial costs because it occurs on an as-needed basis. In terms of effective cost management within MRO (maintenance, repair, and operations), such a practice can be economical over shorter periods.
It plays a vital role in preemptively tackling complications before they worsen, thereby maintaining equilibrium within MRO management strategies.
Predictive Maintenance
Predictive maintenance, which leverages the convergence of data analysis, artificial intelligence, and the Internet of Things (IoT), represents a sophisticated MRO strategy designed to prevent equipment malfunctions before they occur.
This forward-thinking method aims to refine maintenance tasks by focusing on condition-based monitoring over traditional time-interval schedules in preventive maintenance practices. This approach can improve asset uptime, scheduled maintenance, and smooth operations.
The intent is to mitigate chances for unforeseen downtime through calculated scheduling and help improve routine inspections.
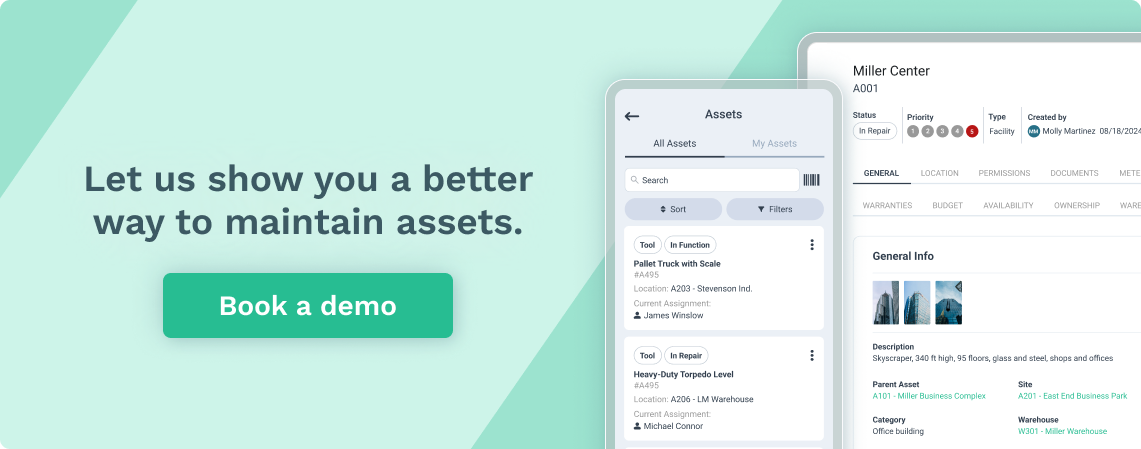
Source: WorkTrek
Industry Examples
The effectiveness of predictive maintenance can be seen at Cathay Pacific’s Hong Kong MRO facility, where such approaches have substantially lowered incidences of unscheduled repair work and reduced unscheduled downtime, leading to cost efficiencies and heightened aircraft readiness.
By identifying potential failures before they manifest, this form of proactive upkeep plays a crucial role in increasing availability, prolonging uptime, and overall reliability across various types of equipment.
Managing MRO Inventory: A Balancing Act
Managing MRO inventory is like walking a tightrope. Too much and too little can be the difference between production and downtime. If you can forecast demand and avoid stock imbalances, you’ll keep your lines running without surprises.
RFID Tags
The introduction of digital tracking systems, such as RFID tags, has revolutionized this process, providing real-time visibility and automating inventory management, which is essential for meeting the unpredictable demands of MRO.
KPIs
Key performance indicators, including stockout rates and inventory turnover, reveal the efficiency of MRO inventory management. By measuring these indicators, businesses can identify cost-saving opportunities and improve their management systems while keeping inventory costs in check.
Streamlining MRO Procurement for Efficiency
Proper MRO management and improved communication can significantly refine the process of procuring MRO materials and services. Organizations can procure the appropriate materials at competitive rates by promoting enhanced collaboration between procurement teams and maintenance personnel, thus making acquiring MRO items more efficient.
When an organization reduces its list of suppliers for these goods, it often benefits from better pricing structures and volume discounts that contribute to a leaner procurement procedure.
Entering into long-term agreements with Miro suppliers is beneficial in establishing a reliable supply chain that diminishes potential disruptions while facilitating more effective operational planning. Advantages gained from such partnerships include:
- Achieving superior prices and conditions on products through collective purchasing.
- Diminishing risks associated with supply chain interruptions via strengthened relationships with suppliers.
- Concentrating on saving costs and maximizing supply chain efficacy as part series methods for managing expenses related to Maintenance, Repair, and Operations (MRO) supplies.
Given the unpredictable nature of industry commodity costs, among other factors, implementing these tactics becomes crucial for proficiently handling MRO management activities.
Navigating MRO Management Challenges
Managing MRO is a complex endeavor, with many hurdles to clear. When mismanagement occurs, it can culminate in unexpected downtime, which spells trouble for operations by causing delayed deliveries to customers, unproductive employee time, and missed goals – all contributing to an onerous responsibility within many companies.
Emirates Engineering has illustrated through its initiatives in training its personnel that having a skilled maintenance team is critical to tackling these obstacles effectively. Such teams are more competent at delivering premium MRO services and can skillfully address problems.
The efficiency of Mro workflows must be prioritized for asset management excellence. Any setbacks or communication breakdowns must be avoided since they obstruct this process. Making well-informed decisions regarding repair timelines or when replacements and regular maintenance should occur will help conquer such impediments.
The optimization of these processes allows organizations to achieve several objectives: averting unplanned downtimes that lead to operational deficits while elevating productivity levels alongside diminishing expenses, boosting asset reliability and longevity, and ensuring better adherence to safety standards and regulatory compliance measures.
Ensuring Safety Through MRO Practices
Safety is crucial to MRO inventory management, involving essential items such as fire extinguishers, gas detectors, and protective gear. Regular maintenance of these items is vital to prevent safety hazards and ensure a secure environment for the workforce. Neglecting proper upkeep can lead to project delays and increase risks to employee safety.
Integrating virtual testing and simulations into MRO strategies not only enhances efficiency within operations, resulting in financial benefits but also markedly improves safety benchmarks across the sector. Such technological adoption enables companies to forecast potential risks regarding equipment-related dangers before their manifestation proactively.
Advanced Tools for MRO: From CMMS to AI
The adoption of cutting-edge tools and software has transformed the management of MRO. Using a Computerized Maintenance Management System (CMMS) optimizes planning and scheduling for corrective maintenance activities, mitigating the likelihood of unscheduled repair work.
Digital twins—virtual models that mirror physical assets—enrich the capability to devise better maintenance and repair protocols by gaining insights into asset functioning and identifying possible complications.
Leveraging technologies such as:
- Augmented Reality/Virtual Reality (AR/VR)
- Robotics
- Unmanned Aerial Vehicles (UAVs or drones)
- Knowledge management systems
Integrating MRO Processes
Proper integration of these technologies within MRO processes amplifies operational efficiency while enabling maintenance crews to execute tasks with increased accuracy and productivity.
These innovations and specialized maintenance management applications significantly contribute to effectively managing numerous assets, thus delivering substantial time efficiencies and cost reductions through improved communication flows and procedures.
The Role of MRO in Production Process Continuity
Maintaining and repairing equipment through an effective MRO (maintenance, repair, and operations) strategy is essential to seamless industrial processes and constant production flows. These practices are vital in enhancing output rates while bolstering profitability margins by preventing malfunctions and unforeseen operational interruptions.
Strategic asset management supported by MRO enables manufacturing entities to schedule maintenance work appropriately or decide whether to repair or replace machinery for uninterrupted service.
Consistent execution of quality products is ensured via various advantages proffered by thoroughgoing MRO procedures:
- Curtailment of unexpected downtime due to prevention of breakdowns
- Assurance that production installations operate with maximal efficiency
- Extension of the usable lifespan for factory apparatus
- Enhancement of plant-wide reliability and performance
Routine checks on the health status of industrial tools are at the heart of any sound MRA framework as they mitigate potential periods when equipment may be out of action. Such proactive measures ascertain ready availability should there be a need for items pertinent to material handling equipment upkeep or patch-up jobs on operational gears integral to the setting-up line’s toolkit.
Vendor Managed Inventory: A Strategic Approach to MRO
Vendor-managed inventory (VMI) marks a strategic shift in Maintenance, Repair, and Operations (MRO). It involves suppliers or vendors directly in the inventory management process. When companies share their inventory information with vendors, these suppliers can place orders more effectively, enhancing efficiency and streamlining operations.
Implementing VMI often leads to automatic ordering systems that help maintain optimal stock levels while diminishing the chances of running out of stock.
With VIM’s ability to allow instantaneous adjustments based on changes in demand, sellers also benefit from lowered costs related to managing inventories. Keeping stocks at an ideal level means organizations can cut back on storage space requirements and associated expenses, which brings financial and operational benefits.
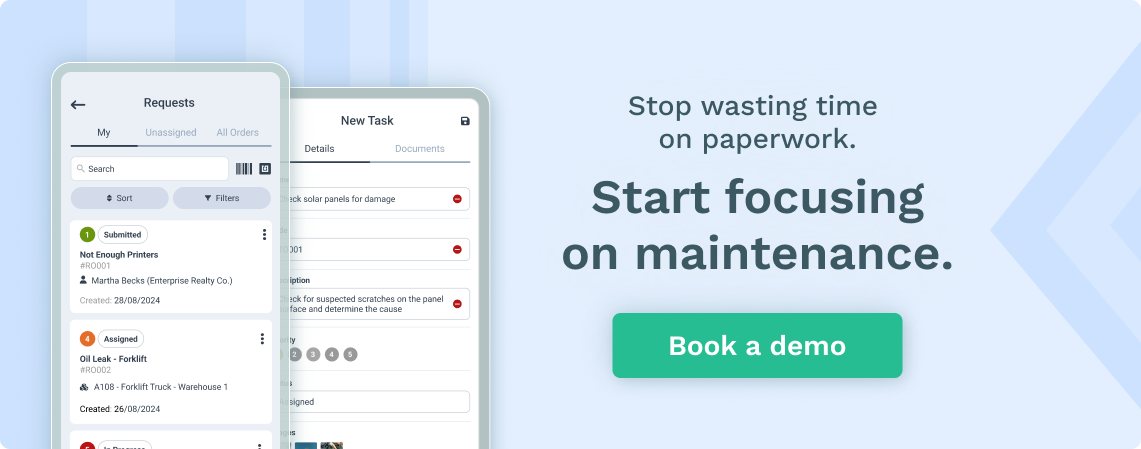
Source: WorkTrek
Case Studies: Successful MRO Strategies in Action
Examining real-world applications of successful MRO strategies offers valuable insights into their potential impacts on operations. Companies such as Southwest Airlines, Lufthansa Technik, and the joint venture Elbe Flugzeugwerke have all implemented MRO strategies that have significantly improved their business performance.
For instance, Southwest Airlines leveraged Lean Six Sigma principles in its Dallas MRO facility, which yielded optimized maintenance processes, cost reductions, and improved turnaround times.
Similarly, Lufthansa Technik’s component maintenance and repair facility in the Philippines has enhanced the company’s profitability by servicing a wide range of clients, including military operators.
The collaboration between ST Engineering Aerospace and Airbus in their joint venture, Elbe Flugzeugwerke, has resulted in a specialized service converting passenger aircraft into freighters, demonstrating how strategic MRO practices can lead to profitable outcomes.
Summary
As we conclude our exploration of MRO, it becomes clear that the strategies and techniques we’ve covered are essential for routine operations and achieving commercial success. Effective MRO management ensures seamless industrial processes, prolongs equipment life, improves raw materials handling, and upholds safety standards. This proactive maintenance approach helps avert potential breakdowns, providing continuous and efficient production workflows.
In this extensive examination of MRO—from grasping its core principles to exploring advanced tools that enhance its application—we hope these insights inspire you to refine your MRO management systems, leading to an era of minimal downtime and increased productivity.
Frequently Asked Questions
What is the role of MRO in industrial settings?
The significance of MRO in sustaining productivity, ensuring safety measures, and preserving ecological sustainability within industrial settings is profound. It includes a variety of processes, including maintenance, corrective repairs, and thorough system overhauls—all vital for facilitating uninterrupted operations within facilities.
How does preventive maintenance differ from predictive maintenance?
Scheduled tasks are the cornerstone of preventive maintenance, aiming to prevent equipment malfunctions. On the other hand, predictive maintenance employs data analytics to anticipate possible defects before they occur.
While preventive maintenance is orchestrated according to a timed schedule, predictive maintenance is governed by the equipment condition and predicts when maintenance should be performed.
Why is proper MRO inventory management important?
Efficient management of MRO inventory is crucial, as it guarantees the availability of essential components and supplies when required. This prevents halts in production that can result from discrepancies in stock levels.
It includes predicting future parts needs and implementing digital systems to monitor inventory instantly, giving a clear view of current stock.
How can MRO contribute to a company’s profitability?
Maintenance, Repair, and Overhaul (MRO) is pivotal in bolstering a company’s profit margins by preventing unexpected halts in production and guaranteeing steady manufacturing processes. This is achieved by preserving uniform product quality, increasing output levels, and prolonging asset service life.
Such proficient MRO strategies are instrumental in boosting businesses’ profitability.
What are the benefits of implementing Vendor Managed Inventory (VMI) in MRO?
Adopting Vendor-Managed Inventory (VMI) within MRO operations can facilitate automatic stock replenishment, enhance inventory level optimization, and decrease inventory management costs. This shift contributes to more effective fulfillment processes and yields financial and operational benefits.