Get a Free WorkTrek Demo
Let's show you how WorkTrek can help you optimize your maintenance operation.
Try for freeA solid standard operating procedure will serve you well if you’re a warehouse owner or manager. We’ll teach you how to create and deploy your warehousing SOPs to improve efficiency, ensure safety, and simplify both inbound and outbound processes.
A solid standard operating procedure will serve you well if you’re a warehouse owner or manager. We’ll teach you how to create and deploy your warehousing SOPs to improve efficiency, ensure safety, and simplify both inbound and outbound processes.
Why are SOPs necessary in warehouse operations?
Standard Operating Procedures are the foundation on which organizations can improve operational efficiency. They streamline routine activities, ensuring that every action, from the receipt of goods to their shipment, is performed consistently and effectively.
SOPs act as a logical approach to performing warehouse operations and as a roadmap for operations, making supervising and mapping workflows easy.
Moreover, the profitability of any logistics and warehousing business heavily depends on optimized processes and effective SOPs.
Safety in the Warehouse
SOPs significantly improve warehouse security, visibility of inventory levels, and the increasing volume of business. These procedures contain regulations to mitigate fire hazards, hazardous chemicals, and safe equipment operation. They even call for regular inspection and maintenance of machinery like forklifts to avoid operational mishaps.
To top it all off, the dynamic nature of e-commerce demands agility, and streamlined warehouse SOP solutions play a crucial role in optimizing warehouse processes to accommodate such evolution.
Source: WorkTrek
Create your own warehouse SOP: Roadmap to Success
Formulating an SOP is similar to developing an operational recipe. It involves the process flow of critical procedures essential to your warehouse operations. These include:
- Receiving
- Picking
- Packing
- Shipping
They should be documented in consistent and easy-to-understand language, including the required tools, equipment, and step-by-step details. You can develop easy warehouse SOP solutions to enhance control operations and establish operational excellence.
It’s important to test these documented SOPs with the participation of frontline workers to ensure their practicality and effectiveness. A sample SOP template is available here.
Training
All staff must undergo comprehensive training on these standard operating procedures through diverse instructional methods. This type of training could be in person, online, or through a training agency, among other options. This ensures a thorough understanding and easy accessibility of this information throughout the warehouse premises.
Employee training sessions can include hands-on demonstrations, digital learning modules, and regular refresher courses to keep everyone up-to-date. By incorporating various training techniques, staff members can better retain and apply the information effectively in their daily tasks.
You may also provide convenient resources like print manuals, online tutorials, and visual guides placed around the warehouse to reinforce learning and for quick reminders.
Manage your work orders with a CMMS software solution and include training documentation in the
Regular Evaluations
Evaluating and updating SOPs regularly ensures they remain effective as situations change, such as new governing policies or equipment with advanced technology.
It is vital to include perspectives from different employees involved in the warehouse team, including frontline staff, management personnel, and even clients.
This captures insights on how the current operations are working to improve the process in the future.
Key Warehouse Processes
Source: WorkTrek
Fundamental procedures drive warehouse functions, such as storage, dispatch, shipment inventory, and planning layout. Pre-receiving activities prepare the warehouse for incoming workflow, establishing key factors like the number of items anticipated, specific packing requirements, and necessary document preparation.
Visualization techniques like a process map or a flow chart can help identify areas for improvement within these processes and point out possible hazards that need to be watched.
Identifying these key processes is vital in creating a Standard Operating Procedure (SOP) that covers all the essential elements for effective warehouse operations.
Define Clear Protocols
Protocols serve as essential guidelines that warehouse workers rely on to execute their daily responsibilities securely and efficiently. By establishing a well-detailed Warehouse Receiving Order (WRO) procedure, the intricacies involved in organizing incoming inventory are made straightforward through precise directions for processing.
Particularly within e-commerce settings, clearly outlined standard operating procedures (SOPs) support the adept handling of product returns, aiding in mitigating financial impacts stemming from returned goods.
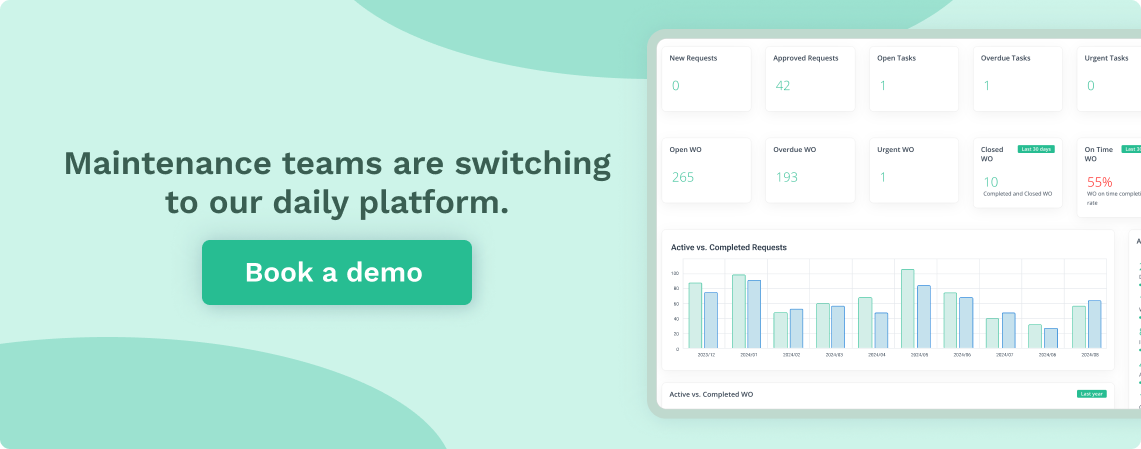
Incorporating Continuous Improvement Practices
Standard Operating Procedures (SOPs) are formulated to maintain existing processes and provide a platform for continuous improvement. Regular observation of performance and compliance allows procedures to keep pace with the latest and most efficient methods, promoting continuous improvement.
Including insights from people on the frontline greatly helps facilitate the continuous development of warehouse functions.
Digital simulation and twin technology play essential roles in designing and testing new storage strategies within an SOP before implementing them in a warehousing environment.
Create a Warehouse Layout With Efficient SOPs
Source: WorkTrek
Operational efficiency within warehouse operations is highly dependent on the configuration of the warehouse layout. By following standardized procedures, establishing warehouse operations management, and optimizing facility design, space can be utilized more effectively, ensuring a streamlined flow of operations that aligns with operational requirements.
Incorporating different floor plans such as U flow, I flow, or L flow patterns significantly improves the movement routes for goods in the facility and boosts overall efficiency.
Rack Control and Shelf Management
Reasonable rack control and appropriate zone classification are essential in creating an efficient warehouse layout. These critical factors are handled by selecting appropriate storage equipment and continuously measuring performance metrics to ensure optimal runs.
Cleanliness, including a warehouse cleaning schedule, helps maintain an orderly environment that aids productivity. With support from experienced warehouse consultants, businesses can improve their warehousing and management practices strategies.
In metropolitan areas with high rental costs, companies are pressured to maximize their available space and handle a large volume of inventory without compromising quality service levels due to lack of space.
Inventory Management SOPs: The Backbone of Warehouse Efficiency
Inventory management is the cornerstone of warehouse efficiency, with standard operating procedures (SOPs) playing a critical role in ensuring its success. Implementing inventory management systems offers numerous benefits, such as:
- Enhancing the effectiveness of supply chain operations
- Streamlining processes through automation
- Enabling access to immediate inventory counts
- Simplifying the process of establishing automatic reorder points for ideal stock levels
- Optimizing outbound operations
- Automating shipping documents
- Define material count for fulfillment centers
A systematic approach to warehouse receiving, reinforced by stringent quality control, enhances efficiency and reduces fulfillment costs.
Maintaining stock levels within the desired parameters is important. SOP policies oversee incoming and existing stock, preventing issues that could lead to increased expenses.
Regular physical inventory audits are essential to ensure that the actual on-hand merchandise matches the records in the management software. This ensures precise tracking of all items in the system.
Navigating Inbound and Outbound Warehouse Operations
Managing the intricate flow of products in and out of a warehouse requires a well-coordinated strategy. Warehouse management standard operating procedures (SOPs) for inbound operations are critical to ensure that incoming inventory is received, stored, and organized efficiently, which lays the foundation for effective eCommerce order fulfillment.
Equally important are the SOPs governing outbound processes. These rely on robust operational planning to boost customer satisfaction and improve interactions with various supply chain partners.
They assign dedicated zones within the warehouse for activities like receiving goods, storage allocation, and dispatch, which aids in establishing an efficient workflow.
Mistakes during picking can result in incorrect items being shipped, a mishap that directly affects client satisfaction. This highlights why precise SOPs are vital for such tasks.
Perfecting the Receiving Process
Perfecting the warehouse receiving process is crucial as it is the entry point for all goods into a warehouse. Conducting quality checks at this stage bars damaged, missing, or incorrect inventory from being accepted, guaranteeing that merchandise remains in a condition fit for sale.
Warehouse Receiving Orders (WROs) support precise scanning and appropriate placement of items within their designated spots. Maintaining an organized system with properly labeled documentation arranged sequentially enables meticulous examination of paperwork during the receiving operation.
Streamlining Picking, Packing, and Dispatch
Subsequent actions remain highly important after goods are received. Picking is an efficient process that collects and arranges orders from storage, a vital part of expedited shipping. The crucial packing phase involves choosing the proper packaging and ensuring products are dispatch-ready, sometimes including promotional materials as required.
This step requires humans or robots to pick items from a designated area.
Following order preparation, the courier partner guarantees prompt delivery to the customer’s address. Before shipments leave the warehouse, quality control checks ensure only top-quality items are delivered, which can help reduce return rates and meet business objectives.
Implementing Control and Improvement Measures in Warehousing
Standard Operating Procedures (SOPs) in warehouse operations are founded on fundamental principles such as Waste Control, Quality Assurance, and Continuous Improvement.
This involves establishing a safety policy and optimizing procedures to reduce the incidence of common errors and thereby minimize monetary setbacks. Strong SOPs within a warehouse setting decrease mistakes, boost efficiency, and increase customer satisfaction.
Regular audits reconcile differences in inventory and foster alterations to existing processes or policies, enhancing overall productivity while trimming down enduring operational expenses.
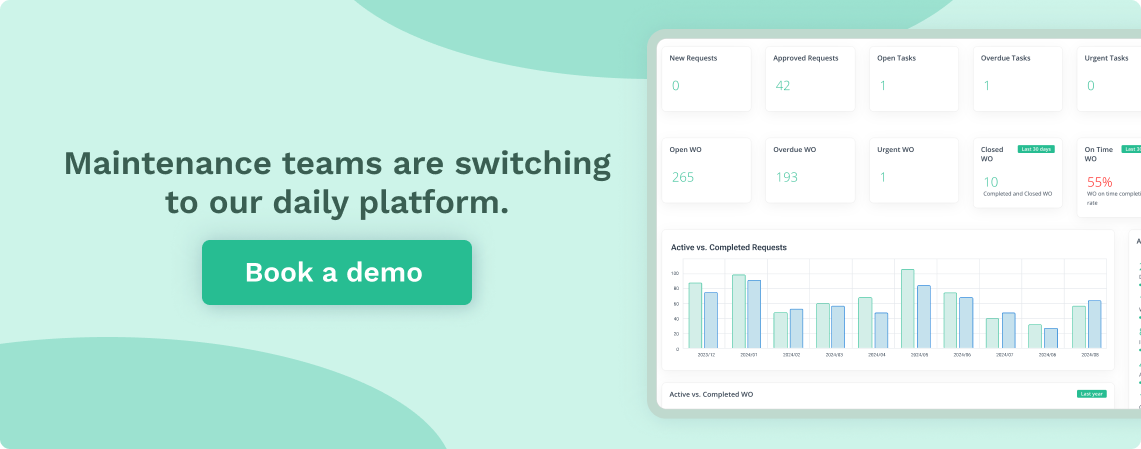
Optimizing Warehouse Healthometer Through SOPs
Operational efficiency and error rates are vital indicators of a warehouse’s health. By implementing Standard Operating Procedures (SOPs), quality control measures are reinforced, and warehouse operations experience heightened efficiency and reduced errors.
Empowering Warehouse Staff with Operational Blueprints
The backbone of successful warehouse operations lies in the hands of warehouse staff, who rely on Standard Operating Procedures (SOPs) to provide them with a definitive operational roadmap. These SOPs do more than define their responsibilities.
They boost employee confidence and speed up the integration process into company practices, which is particularly beneficial for new personnel. Ensuring staff undergo regular training on these procedures helps maintain proficiency in essential tasks such as safely operating forklifts and managing hazardous substances.
These same SOPs also act as a framework to ensure smooth transitions when substituting or reshuffling teams, thereby maintaining uninterrupted workflow during periods of change in staffing.
Actively seeking employee feedback is integral in recognizing areas where efficiency can be optimized and developing inventory management SOPs within the warehouse environment. This is a testament to an organization’s dedication to continuous improvement.
By establishing robust procedures, companies give their workers the autonomy to adeptly navigate various scenarios while upholding professional standards that reflect the firm’s values.
Source: WorkTrek
Enhancing Omnichannel Capabilities with Warehouse SOPs
In today’s multi-channel retail environment, warehouse operations must be adept at seamlessly managing different distribution channels. The development of solid warehouse standard operating procedures (SOPs) is integral to merging technology with operational processes, thus enabling faster and more accurate activities vital for the success of omnichannel commerce.
Warehouses need to evolve by incorporating automated systems, strategic relevance, and operational planning that are in tune with the requirements unique to an omnichannel strategy.
Ensuring efficient stock allocation across multiple outlets, as outlined by robust warehouse SOPs, is vital for achieving customer satisfaction. Transforming a warehouse to support omnichannel facilities effectively demands substantial modifications, such as:
- Maximizing storage space utilization
- Implementing process automation
- Enhancing logistical strategies
- Tailoring workforce management
Ensuring that warehousing procedures are up-to-date and optimized remains critical for smooth transaction execution and achieving consumer satisfaction within an omnichannel framework during order fulfillment stages.
Summary
An effective warehouse SOP includes identifying and mapping core processes, establishing clear protocols, integrating continuous improvement practices, and regularly monitoring to adapt to new regulations or equipment while factoring in stakeholder feedback.
As we’ve explored this extensive guide to developing the perfect warehousing SOP, it’s clear that SOPs are much more than simple guidelines; they are the cornerstone of warehouse efficiency and operational excellence.
SOPs play an indispensable role in warehouse management, from perfecting the receiving process to enhancing omnichannel capabilities. By implementing these SOPs, warehouses can streamline operations, empower their workforce, improve safety, and ultimately achieve a competitive edge.