Get a Free WorkTrek Demo
Let's show you how WorkTrek can help you optimize your maintenance operation.
Try for freeAre you looking to streamline your maintenance workflow? Implementing a maintenance workflow or automation, including tracking and reviewing maintenance history, can minimize downtime and cut costs. This guide will help you discover the importance, advantages, and methods of crafting one.
A streamlined maintenance workflow is crucial for organizational efficiency, reducing downtime, extending equipment life, and ensuring operational continuity through proactive planning and execution.
The process includes continuous improvement in maintenance workflows, involving regular audits, data analysis, and monitoring, ensuring compliance, identifying inefficiencies, and driving optimization for increased reliability and cost savings.
The maintenance planner role is critical in managing a maintenance workflow process. Maintenance planners can efficiently plan resources, improve maintenance performance, and enhance reliability by having access to trigger events, parts, and resource availability through CMMS systems.
Understanding Maintenance Workflow
Rather than just a simple to-do list, maintenance workflow processes can help organize and provide visibility to the overall organization’s operations.
Essentially, these processes form a consistent and organized sequence that guides how each task involved in maintenance is handled, from initiation through approval and execution stages to vital reporting steps.
Maintenance technicians are crucial in this process. They receive work orders, complete assigned tasks, and utilize CMMS software like Worktrek for efficient maintenance workflow processes. Neglecting this step-by-step process can lead to high costs, regular equipment failures, and widespread negative impacts on productivity.
The differences between asset management and maintenance should be carefully considered. Asset management spans the entire lifespan of assets while focusing specifically on their physical preservation. This ensures that each piece of machinery operates at peak efficiency when needed. The main objectives are to reduce operational downtime, enhance output levels, and prolong the working life span of your resources.
Maintenance management acts like a reliable organizer, ensuring business operations run smoothly. It plans and coordinates all tasks related to managing facilities, ensuring that machinery works efficiently. It can also help maintenance costs, improve asset management, and provide better equipment performance.
Source: WorkTrek
Key Benefits of an Efficient Maintenance Workflow
Unlocking the full potential of your assets starts with a streamlined maintenance workflow. By following this approach, maintenance managers can squeeze every bit of productivity from their equipment. This helps extend its lifespan, and it does it all with the precision of a ballet dancer while still following strict safety and regulatory standards.
Reducing downtime equates to an uninterrupted flow of operations and better equipment performance, which can reduce the need for emergency maintenance. Coupled with preventive and proactive maintenance, creating an efficient maintenance workflow can reduce reactive maintenance instances and provide clear maintenance tasks for technicians, leading to optimal working conditions for your organization.
Steps to Design an Effective Maintenance Workflow
Initiating an effective maintenance workflow is predicated on the management team developing an asset management plan that is clear to the maintenance department and provides visibility that can track key performance indicators.
Addressing these fundamental inquiries sets the stage for a robust maintenance program. Engaging all team members, including operators, maintenance technicians, management team, and stakeholders, in this process offers valuable insights that contribute to devising operational procedures that resonate with each participant.
Creating an optimal pathway within your facility’s operations involves thoroughly understanding your assets, strategically choosing priorities, and meticulously planning specific tasks and timelines required for their upkeep. This represents the essence of an efficient maintenance workflow.
Additionally, while plans should be rigid, it is best to allow stakeholders to adjust and continuously improve the process. Proper training also enables maintenance personnel to navigate this well-organized framework confidently.
Identifying Maintenance Tasks
Start the process by initiating a complete asset inventory. If you have an existing inventory list, this is also an excellent time to update it and add either bar codes or QR Codes to each piece of equipment.
It is crucial to comprehensively understand your assets, their historical performance, and their optimal functionality requirements. Having an updated inventory list can help organize maintenance activities.
This can also help spot inefficiencies that can be addressed in your maintenance plan.
Adopting this forward-thinking strategy can revolutionize how you handle maintenance duties. It guarantees efficiency and enhances effectiveness through optimization for more significant influence.
Planning and Scheduling Maintenance Activities
Having established your maintenance priorities, developing a preventive maintenance schedule is next. This strategic timetable integrates manufacturer recommendations, proven industry practices, and previous experiences with your assets to ensure that each item receives timely care before any expensive malfunctions occur.
This approach’s primary purpose is to keep assets in their best possible condition and safeguard against financial losses by being proactive. Scheduled maintenance tasks contribute significantly to operational continuity, cost savings, and efficiency.
Your specialized planners and managers are tasked with crafting these intricate preventive maintenance plans. They balance scheduled tasks optimally timed to either usage or manufacturer recommendation to smooth out the overall operation.
This allows maintenance crews, including technicians, to proficiently manage routine duties alongside unexpected challenges proficiently, efficiently maintaining equipment at its peak performance level.
Assigning Responsibilities
A workflow cannot operate effectively without well-defined roles and responsibilities. A well-crafted plan includes clear work instructions and should highlight regular training, clear work instructions, and a detailed maintenance planner to minimize the risk of errors and maximize efficiencies.
It’s about crafting a plan that outlines the tasks and matches them to team members with the skills to execute them flawlessly. Clear work instructions and regular training ensure that each person understands their role in this well-oiled machine, minimizing the risk of errors and maximizing the efficiency of every maintenance event.
Empowering operators to take on asset care tasks can bridge the team gap, ensuring essential maintenance is carried out seamlessly. This maintains equipment reliability and promotes a culture of accountability and shared responsibility across your organization.
Utilizing Maintenance Management Software
Implementing maintenance management software (CMMS) will revolutionize the maintenance approach and process as organizations continue their digital transformation journeys.
Embracing CMMS software represents an investment in both efficiency and strategic planning. Tools such as WorkTrek bring multiple benefits:
- They enable instantaneous communication between involved parties.
- Provide advanced reporting capabilities and transparent insights into asset conditions and organizational structure.
- With data and analytics, they can help anticipate future malfunctions by using a predictive maintenance process.
- Provide extensive reporting and analytics to help organizations get better visibility
- Provide technicians that give them maintenance history, outline the maintenance program, and provide safety hazards and instructions for maintenance technicians
- Provide scheduled regular maintenance of assets
- Centralize maintenance requests
It essentially acts as an oracle within your maintenance operations.
Features of CMMS Software
Source: WorkTrek
CMMS software serves as the pivotal hub for managing your maintenance processes, meticulously recording details of work orders, inventory levels, and the entire history of maintenance. Streamlining task creation and monitoring their progress to completion guarantees that no detail is overlooked.
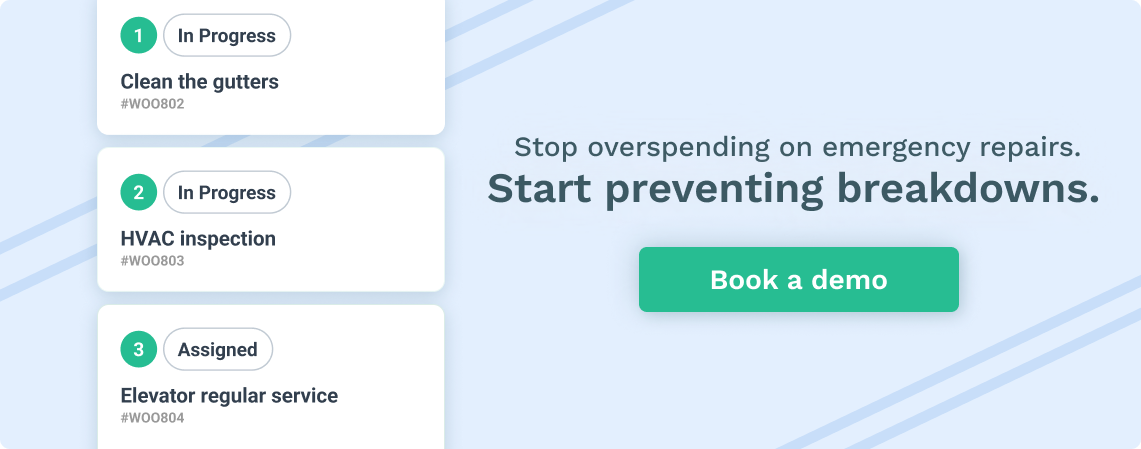
Its ability to automatically produce comprehensive reports is not merely an added benefit—it’s a crucial instrument that prevents hold-ups and discrepancies while fostering data-driven decision-making.
Through its sophisticated reporting functions, CMMS software empowers maintenance managers by allowing them to identify critical repairs and inspections swiftly, ensuring the timely execution of essential maintenance activities.
This shifts practices from predominantly reactive to proactive management, informed by robust data analysis with CMMS at its core.
Implementing CMMS in Your Organization
Adopting a CMMS system within your company can streamline communication, boost team members’ responsibility, and guarantee that maintenance tasks are carried out promptly. However, before integrating this tool, it’s crucial to establish a strategy for preventive maintenance.
Relying on CMMS does not compensate for an ineffective run-to-failure approach in handling maintenance.
One of CMMS’s many benefits is its ability to send timely reminders that prompt maintenance staff to take action, keeping the cogs of the maintenance process moving without disruption.
CMMS enables organizations to improve efficiency, quickly implement a planned maintenance process, clearly define technicians’ maintenance task, and reduce overall maintenance budgets.
A solid maintenance workflow ensures everyone is on the same page and the maintenance operations can be run smoothly.
Continuous Improvement in Maintenance Workflows
Any maintenance workflow will require continuous improvement as conditions change. One of the best ways to do that is to leverage data analysis and feedback to continuously elevate the standards of your maintenance processes.
The maintenance manager should perform a regular internal audit as part of the maintenance planning process. This will help focus the plan on quality of service, procedure efficiency, and trimming operating expenses—all with the ultimate goal of achieving unsurpassed effectiveness.
Key Performance Indicators
Utilizing key performance indicators can greatly help implement a more efficient maintenance workflow and ensure that your asset investments are well protected. This approach can shed light on areas for growth and confirm that your maintenance efforts are consistent with management’s organizational goals
By documenting metrics linked to:
- Equipment performance
- Work Order Performance
- Hours spent on labor
- Cost of Repairs
- History of equipment breakdowns
- Easy review of historical data
- View equipment health
This can pave the way to a more efficient maintenance workflow and plan.
Source: WorkTrek
Monitoring and Adjusting Workflows
Managing preventive maintenance workflows is like caring for a garden, giving each task the attention it needs to grow.
Having all the necessary resources and tools guarantees that proactive maintenance tasks are carried out effectively and accurately.
This cycle includes regular evaluations and modifications, and you must always be ready to adapt promptly to preserve the consistency of your workflow.
Fine Tune Equipment Performance
Methods such as vibration analysis, oil analysis, and temperature monitoring represent just some of the instruments available. Each contributes to a system of condition-based surveillance designed to halt asset breakdowns by perpetually checking their state of health.
This type of oversight keeps your equipment in optimal condition so it’s prepared for action whenever required.
Conducting Regular Audits
Regular evaluations are essential to the integrity of maintenance workflows, as they verify conformity with industry benchmarks and strict regulatory requirements. These assessments act as a detailed scrutiny tool that reveals potential inefficiencies in maintenance activities while pinpointing opportunities for enhancement.
A clearly outlined workflow streamlines the audit process by facilitating straightforward comparisons between actual performance and predefined protocols. This ensures process adherence and reduces the possibility of non-compliance with regulations.
These audits are influential in overseeing maintenance processes’ efficiency and steering the process toward ongoing refinement.
Best Practices for Maintenance Workflow Automation
In today’s digital environment, automation has transformed from a mere convenience to an essential element for maintaining competitiveness. To optimize your maintenance workflow through automation, establish precise and quantifiable objectives to guide every choice and procedure you undertake.
Just like performing a detailed inspection on your present machinery, it’s essential to chart your current procedures to pinpoint inefficiencies and areas ripe for improvement.
When selecting an automation tool, exercise the same diligence as when acquiring a vital piece of equipment.
Consider its scalability potential and how well it integrates and aligns with systems already in use within your organization. Continuously updating these automated processes alongside thorough training ensures that team members remain at the forefront of innovation—equipped and ready to leverage these advanced tools to their greatest capacity.
Fixed vs. Floating Preventive Maintenance Schedules
There are two options for preventive maintenance: static or adjustable maintenance schedules. The fixed maintenance schedule operates on a rigid timeline similar to railway timetables, with upkeep tasks appointed at predetermined intervals contingent upon usage or chronological benchmarks. This anticipatory strategy sets future planned activities in stone.
Conversely, floating preventive maintenance can determine subsequent tasks depending on when preceding ones were concluded and shift responsively according to your operational demands.
Such flexibility facilitates more nimble resource allocation while ensuring that each instance of scheduled maintenance is conducted punctually and pertinently.
Leveraging Technology for Automation
Maintenance errors can incur significant costs, as human error is innate but often avoidable. The reliance on manual processes introduces a vulnerability to mistakes and inefficiency since they do not provide immediate access to updated data.
Automation acts as an instrument of precision, reducing errors and facilitating the timely and correct completion of maintenance tasks.
Provisioning digital devices for those performing maintenance duties allows them to access critical information directly at the site of action, eliminating redundant movement while ensuring the utilization of up-to-date manuals and documents. In today’s data-centric environment, possessing these technological tools has transcended convenience and become essential for strategic success in maintenance operations.
Overcoming Common Challenges in Maintenance Workflows
Developing and implementing a maintenance workflow comes with its own set of obstacles.
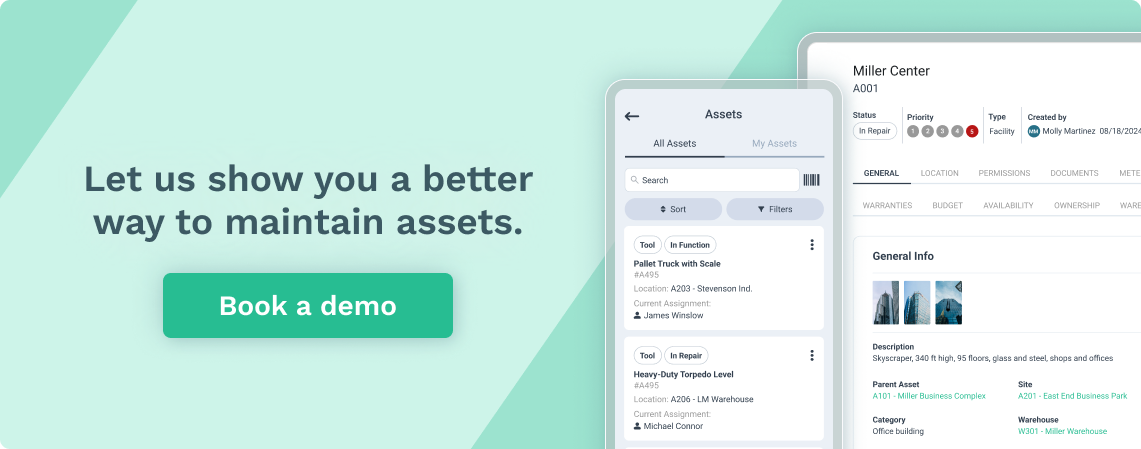
Unplanned and unscheduled maintenance, for instance, can wreck even the most well-thought-out plans, often resulting from a lack of anticipation or a failure to schedule maintenance tasks properly.
To counter this, it is imperative to establish strict preventive maintenance schedules and provide your team with the training needed to foresee and mitigate these issues.
Budget constraints and the failure to adhere to structured processes are other common roadblocks. To overcome these challenges, consider the following strategies:
- Demonstrate the long-term cost savings from a solid maintenance investment, highlighting the reduction in maintenance costs to reconcile the views of management and maintenance teams.
- Ensure that all team members are aware of and trained in established processes.
- Conduct regular audits to maintain compliance and prevent costly downtime.
By implementing these strategies, you can overcome budget constraints and improve the efficiency of your maintenance operations.
Handling Unattended Work Requests
In the dynamic environment of asset management, it is not uncommon for maintenance work requests to be overlooked, much like misplaced notes in a musical composition, resulting in equipment failures.
It’s essential to meticulously assess these submissions and decide whether to greenlight them as full-fledged tasks or reject them to better align with operational needs. Implementing a CMMS system can reduce the number of unattended work requests and provide complete visibility to all work being performed.
This system diligently monitors each maintenance work request from start to finish, guaranteeing no work order or task is ignored. The technology does more than ensure continuity. It also generates detailed reports that aid in refining your approach to maintenance duties, setting the stage for improved future undertakings.
Ensuring Timely Completion of Maintenance Tasks
Source: WorkTrek
The timely execution of maintenance tasks is the hallmark of an effectively managed maintenance operation. Work order software acts as a steady pulse, issuing regular prompts to technicians to carry out their assigned responsibilities and deliver reports on schedule.
Doing so ensures a consistent tempo for performing maintenance duties, with every action occurring at the right time.
Such a system’s elegance lies in facilitating task fulfillment and fostering an environment where adherence to safety procedures is second nature and equipment reliability remains unbreached. It promotes an ethos of ongoing enhancement, viewing each task as a chance to gain insights and refine processes for future endeavors.
Summary
In conclusion, achieving operational efficiency relies heavily on meticulous planning, structured execution, and the adoption of cutting-edge technologies. Progressing from pinpointing specific maintenance tasks to applying CMMS tools and perpetually honing these processes embodies a strategic journey towards an operation that excels in efficiency, resilience, and cost-effectiveness.
These insights can shape a well-coordinated maintenance workflow aligned with your company’s objectives. Utilize the right tools, a proactive mindset, and a commitment to continuous improvement to turn your maintenance processes into a fine-tuned machine.
Frequently Asked Questions
What is the fundamental purpose of a maintenance workflow?
The primary goal of a maintenance workflow is to optimize the execution of maintenance tasks, which minimizes downtime, cost-efficiency, and extension of asset longevity.
How does an efficient maintenance workflow benefit an organization?
By optimizing the maintenance process, a business can lessen equipment idle time and increase the longevity of its assets while enhancing safety measures, complying with regulatory standards, and curbing maintenance expenses. This approach contributes to heightened operational efficacy and generates cost reductions.
What is the role of CMMS in maintenance management?
The function of a Computerized Maintenance Management System (CMMS) within maintenance management lies in boosting effectiveness through the automation of tasks, enabling immediate communication, offering sophisticated reporting capabilities, and endorsing preventive maintenance approaches.
Such support aids in optimizing maintenance operations and elevating overall efficiency.
What are the best practices for automating maintenance workflows?
Establish specific objectives and chart current procedures to automate maintenance tasks effectively. Initiate with manageable smaller assignments, select the suitable automation instrument, deliver necessary training, and ascertain adherence to relevant industry benchmarks to streamline maintenance workflows efficiently.
How can regular audits improve maintenance workflows?
By conducting periodic reviews, maintenance workflows can be enhanced by enforcing norms and compliance with regulations, pinpointing areas that lack efficiency, and highlighting opportunities for advancement.