Get a Free WorkTrek Demo
Let's show you how WorkTrek can help you optimize your maintenance operation.
Try for freeAre you struggling with frequent downtime and soaring maintenance costs? Condition-based maintenance (CBM) might be the strategic pivot your operation needs. By monitoring the actual condition of your assets, CBM dictates maintenance only when essential, trimming excess costs and bolstering reliability.
While preventive, predictive, and schedule maintenance are essential parts of any maintenance plan, maintenance teams should strongly consider a condition-based maintenance strategy as a companion for maintenance.
This article provides a detailed outline of the techniques that make CBM effective, its real-world impact on your bottom line, and actionable steps to integrate it into your workflow.
Key Takeaways
- Condition-based Maintenance (CBM) is a proactive maintenance strategy that leverages real-time monitoring to determine the precise condition of assets. This enables maintenance teams to perform tasks only when necessary, reducing costs and extending asset lifespans.
- CBM incorporates various monitoring techniques, such as vibration, oil, and infrared analysis, with the critical use of well-calibrated sensors and predefined threshold values to ensure maintenance is done at the optimal moment, thereby avoiding unnecessary interventions and improving operational efficiency.
- Implementing CBM requires careful asset criticality assessment, strategic planning, and maintenance personnel engagement to create a continuous improvement culture. It also involves understanding the differences between CBM and other maintenance strategies, like predictive maintenance, and choosing the right tools and software for successful integration and execution.
Demystifying Condition Based Maintenance (CBM)
Source: WorkTrek
A condition-based maintenance program guides maintenance strategies, guiding teams away from guesswork and towards the solid foundation of data-driven decision-making.
At its foundation lies a proactive approach to performing maintenance that utilizes real-time data analysis to determine the actual state of equipment. This enables maintenance teams through a condition-based strategy to:
- Conduct necessary repairs immediately, eliminating unwarranted procedures and their associated expenses.
- Increase dependability in machinery.
- Drastically reduce overall costs related to upkeep
- Prolong the service life of assets
- Reduce asset failure
- Eliminate unnecessary maintenance
- Improve overall equipment maintenance
Condition Monitoring
At the heart of an effective CBM regimen are sophisticated condition monitoring techniques, which offer continuous insights into when an asset might require repair. CBM’s adaptability is remarkable—it’s designed to cater to varying operational demands, ranging from plants teeming with rotating machines to those operating on compressed gas systems.
By integrating this targeted maintenance regime, managers overseeing these processes can revolutionize workflow maintenance, achieving higher efficiency and reduced costs while ensuring smooth production cycles. This strategic integration of CBM allows for a more dynamic and responsive approach to maintenance management, where decision-making is driven by actionable insights derived from real-time data.
Such an approach streamlines maintenance operations and enhances the reliability and availability of critical equipment, thereby supporting improved productivity and operational excellence.
The Critical Role of Monitoring Techniques in CBM
A collection of condition-monitoring techniques is at the core of an effective condition-based maintenance (CBM) program. These include:
- Vibration analysis tools include accelerometers and spectrum analyzers to detect imbalances, misalignments, or bearing faults in rotating machinery.
- Oil analysis kits allow for the sampling and testing of lubricants for contaminants and metal wear particles that indicate internal wear.
- Infrared thermography cameras visually monitor and measure thermal anomalies in equipment, which can indicate issues like overheating insulation breakdowns or electrical faults.
- Ultrasonic detectors identify high-frequency sounds produced by leaks or electrical discharges that the human ear cannot detect.
- Motor circuit analysis equipment to assess the condition of motor windings and insulation in electric motors.
- Laser alignment tools ensure proper alignment of rotating shafts, which can prevent premature wear or failure.
- Corrosion probes and meters to measure material loss and corrosion rates in tanks, pipes, and other structures.
- Pressure and flow meters to monitor fluid and gas pressure and flow rates in pipelines and hydraulic systems.
- Acoustic emission detectors pick up the sound waves of cracks or faults in pressurized vessels or rotating equipment.
- Electrical signature analysis (ESA) tools analyze the electrical parameters of motors and generators to detect issues like rotor bar defects or air gap eccentricity.
These methodologies are instrumental in maintaining industrial machinery’s operational integrity and functionality. These techniques’ effectiveness and precision stem from sensors designed to continuously monitor pressure levels and other crucial variables related to equipment performance.
It’s critical for these condition monitoring sensors to be both precise and calibrated adequately so they can provide reliable data on which maintenance teams depend.
Companies must carefully determine the exact threshold values appropriate for CBM interventions based on a thorough knowledge of their machines’ behavior under different operating conditions and manufacturer recommendations.
This rigorous monitoring ensures that maintenance activities are carried out only when necessary, thus achieving an ideal equilibrium between proactive maintenance and resource conservation.
Decoding the P-F Interval for Timely Maintenance Interventions
Understanding the P-F interval is critical in condition-based maintenance (CBM). This crucial period, analogous to emergency medicine’s golden hour, can dictate an equipment’s health outcome by marking the duration from when a failure begins to manifest until it becomes a functional failure.
Source: WorkTrek
Recognizing and utilizing this window effectively allows maintenance teams to optimally plan their work before catastrophic failures occur, reducing unplanned downtime incidents.
A vital role for any maintenance manager is prolonging the P-F interval through astute condition-based maintenance practices. These practices keep the machinery running longer and protect core production processes.
CBM Intervals
Advanced CBM involves setting up monitoring points with specific warning levels that signal impending issues early on—a sort of frontline defense system for assets—prompting timely action from those in charge.
These advancements in predictive maintenance technology empower companies to shift away from reactive measures toward a proactive maintenance strategy tailored uniquely to their operational flow.
The CBM Process
Condition-based Maintenance (CBM) is a systematic blend of data collection and critical analysis that informs maintenance decisions. The steps are as follows:
- Data Collection: Details are gathered through sensors that measure variables like vibration, temperature, and pressure. This data collection is essential to identify trends that may indicate potential issues before they lead to equipment failure. By capturing this information, maintenance teams can make informed decisions about when to perform maintenance, effectively preventing downtime. The continuous data stream also provides a historical record that can be analyzed for long-term improvements and strategic planning.
- Data Analysis: This collected data is then transformed into actionable insights. By analyzing the gathered information, maintenance teams can pinpoint the early signs of wear and tear, predict potential failures, and schedule maintenance activities promptly. The analysis process helps prevent catastrophic equipment failures and supports optimizing the maintenance schedule to avoid unnecessary service interruptions. This strategic analysis is essential for making informed decisions that contribute to improved reliability and longevity of the equipment.
- Informed Decisions: These interpretations offer a clear understanding of the machinery’s condition, which aids in making knowledgeable choices. By leveraging this understanding, maintenance teams can prioritize tasks, optimize resource allocation, and avoid the pitfalls of both under-maintenance and over-maintenance.This enhanced decision-making process leads to a more efficient maintenance schedule, ensuring that machinery is maintained in a state that maximizes uptime and productivity. These informed decisions also contribute to a safer working environment by reducing the risks associated with equipment failure.
What does it include?
Subsequently, the step of condition monitoring includes:
- Constant observation of the health status of assets
- Identification for any hints pointing towards decline or forthcoming malfunction
- The generation of alerts serves as an urgent notice when specific limits are exceeded, signaling that it’s time to initiate maintenance task planning.
The process cycle encompassing Condition Based Maintenance (CBT) involves these key phases:
- Planning Stage: Develop plans and arrange for necessary upkeep activities while marshaling adequate resources.
- Implementation Phase: Execute scheduled repair operations.
- Feedback on Results: Evaluate outcome post-maintenance activity to hone future measures taken during interventions.
- Finalization Step: The CBM sequence reaches its end before recommencing from scratch.
This iterative process enhances maintenance efficiency by ensuring each phase is finely tuned to work together from initiation to completion. It forms a proactive loop of machine care based on real-time conditions rather than rigid schedules.
Developing a CBM Program: A Step-by-Step Guide
Initiating a Condition-Based Maintenance (CBM) program is comparable to planning, and systematic execution.
The structure supporting the creation of such a program steers teams through identifying appropriate assets, pinpointing possible failure modes, and navigating the complex process of analyzing gathered data.
This encompasses focusing on assets critical for production but also considers those with significant repair or replacement expenditures and those not immediately lined up for renewal.
By implementing a CBM strategy comprised of six systematic steps—starting from choosing assets and continuing to analyze collected data to steer decisions—maintenance crews can develop an enduring operation equipped to withstand future challenges.
Assessing Asset Criticality and Data Requirements
inde-Based Maintenance (CBM) program is to identify and focus on the high-value equipment that serves as the core of operations. Identifying trends and matching those to your maintenance program is also essential. All these steps help reduce overall maintenance costs, provide visibility to the maintenance team, and develop a proactive maintenance strategy.
Source: WorkTrek
Identifying the necessary types of sensors for critical assets to monitor equipment conditions continuously is an important step. The success of CBM hinges on its alignment with an organization’s unique requirements and the constraints of its maintenance budget, rendering this stage of the process pivotal. It will also be essential to match CBM with a preventive maintenance strategy.
It is essential to pinpoint critical assets whose failure would significantly disrupt operations. Therefore, it is imperative to establish systems for continuously monitoring asset performance to help improve maintenance costs and the reliability of critical assets.
Data should include auditory and digital recordings to fully capture indicators suggesting an asset is nearing a potential failure point.
Engaging Maintenance Personnel in CBM Transition
Adopting a Condition-Based Maintenance (CBM) program is not merely about changing technical procedures. It’s also about shifting the organizational culture for the maintenance team, which demands commitment and active involvement from all team members.
It is essential to involve maintenance personnel early to promote smooth integration and successful implementation of the CBM approach.
Define Gaps
Throughout this transition, gaps may emerge regarding proficiency in analyzing data and managing systems—gaps that must be addressed by providing specialized training for current employees or bringing new staff with requisite skills on board.
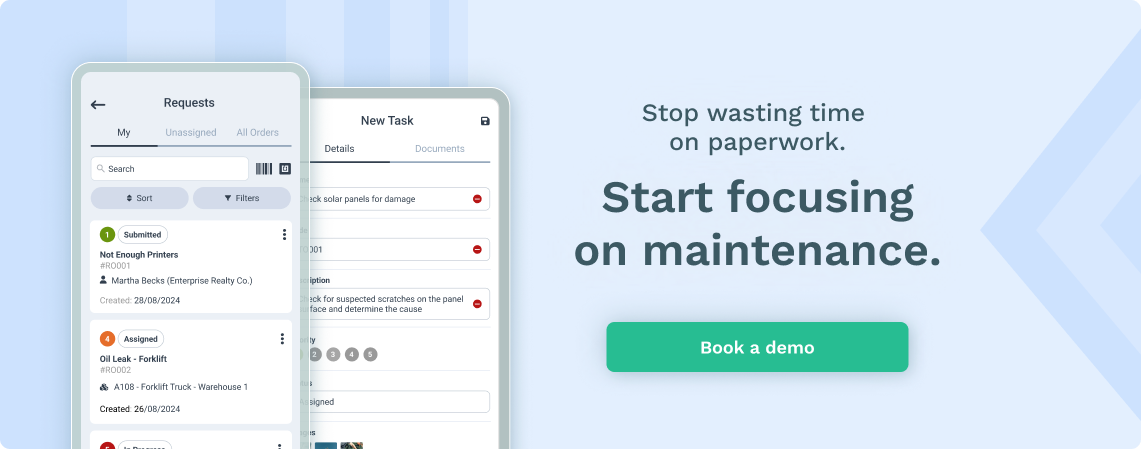
Resistance to change is often encountered, yet such challenges can be overcome by employing effective change management strategies that resonate with different maintenance teams.
These approaches should nurture a continuous improvement mindset within the organization’s culture.
Refining Your CBM Strategy with Continuous Improvement
The path to condition-based maintenance (CBM) is continuously evolving, demanding ongoing tuning and improvement to maintain the utmost precision of the strategy. Frequent tweaks informed by performance data and trend assessments can markedly refine the exactitude of maintenance choices. Such a proactive maintenance approach focuses on circumventing errors by detecting potential failure modes before they become serious issues.
With an emphasis on executing preventive maintenance predicated upon the machinery’s real-time state, CBM substantially diminishes the chances of equipment breakdowns and unexpected operational halts. This ensures uninterrupted production processes continue smoothly.
CBM Versus Predictive Maintenance: Navigating the Differences
CBM (Condition-Based Maintenance) and predictive maintenance might intersect within the maintenance sector but navigate separate trajectories. Both employ data-centric approaches.
CBH hinges on monitoring equipment either in real-time or at regular intervals to guide when to perform maintenance tasks.
Conversely, predictive maintenance utilizes intricate data analysis and forecasting algorithms to determine optimal times for upkeep procedures. Although reactive within its proactive boundary conditions, CBM relies on specific indicators or benchmarks pointing to a need for intervention due to deteriorating function.
Predictive maintenance is designed strategically to reduce unexpected interruptions by predicting forthcoming malfunctions before they occur physically. Distinct differences emerge in their workflows: CMMS integration for CBM centers around current machinery performance, prompting immediate action from maintainers whenever necessary.
Using complex analytical tools and predictive methods, potential issues can be assessed through historical insights and ongoing operational figures.
While more straightforward by nature, as it zeroes in on discerning failure modes and pinpoints precise events for activation based on past asset behaviors, CBM lays groundwork processes. Predictive practices go beyond this preliminary level by embracing extensive assessments of accumulated information—positioning itself into what lies ahead regarding preserving systems efficiently.
Source: WorkTrek
Real-world Applications: CBM in Various Industries
Condition Based Maintenance (CBM) extends far beyond the theoretical, with its practical applications spanning various industries to enhance equipment dependability. Businesses that heavily rely on the continuous operation of their physical and substantial assets greatly benefit from adopting CBM practices.
Manufacturing, oil and gas, transportation and logistics, power generation, mining, and construction are among the industries remarkably poised for improvement through CBM.
Adopting CBM methodologies within these sectors can significantly reduce unexpected downtime, prolong machinery’s life expectancy, and boost overall operational efficiency.
For instance, in specific contexts such as those in the oil industry, energy sector, or mining operations, Acoustic analysis has proven invaluable by identifying leaks in systems containing gases or liquids that might remain undetected.
Pressure analysis plays a pivotal role in condition-based maintenance strategies. It ensures systems operate at peak efficiency by maintaining the ideal flow of fluids, gases, or air. This element is crucial across a wide array of industries.
Employing electrical analysis within a condition-based maintenance framework acts as an early warning defense mechanism: It monitors circuit currents to thwart potential electric-related problems before they escalate into costly interruptions.
These instances underscore the flexibility inherent in deploying CBM approaches and how effectively they address individualized needs spanning diverse market segments.
Organizations integrating condition-based maintenance into their routine service schedules stand to capitalize significantly from real-time data paired alongside sophisticated analytics tools, which are instrumental aspects necessary for sustaining an advantageous competitive position within one’s arena.
The Intersection of Technology and CBM
The fusion of technology and Condition-Based Maintenance (CBM) is driving a new industrial revolution in which sensors and data analytics platforms become the linchpins of maintenance strategies.
Implementing IoT within CBM frameworks transforms how performance baselines are established and monitored. Deviations from these baselines prompt timely maintenance activities. This technology integration enables teams to seamlessly collect and manage the large volumes of data generated by CBM systems, facilitating advanced analytics that inform maintenance decisions.
Source: WorkTrek
Technology Challenges
However, the integration challenges are significant. Marrying different technologies, such as sensors, IoT devices, and data analytics platforms, into cohesive CBM systems requires strategic planning and execution. Infrared cameras, for instance, are utilized in CBM to detect high-temperature conditions in energized equipment, indicating potential issues before they escalate.
Moreover, IoT sensors attached to assets can initiate maintenance tasks and work orders by sending data to a CMMS through an API once predefined thresholds are crossed. This synergy of technology and maintenance strategy empowers organizations to address the health of their assets preventively, maintaining operational continuity and driving efficiency.
Using technology to reduce maintenance costs
The intersection of technology and Condition-Based Maintenance (CBM) is essential in driving down maintenance costs. By harnessing the precision of sensors and the analytical power of data platforms, CBM allows for identifying potential issues before they lead to costly repairs or replacements. This proactive approach minimizes the need for extensive maintenance work, thus reducing labor hours and material costs.
Additionally, the data collected through technology-enhanced CBM can be used to optimize maintenance schedules and resource allocation, leading to more efficient operations and further cost reductions. With technology integrated into CBM, organizations can expect a significant decrease in overall maintenance expenses, contributing to improved financial performance.
The Financial Impact of Adopting CBM
Adopting Condition-Based Maintenance (CBM) can have a profound financial impact on an organization, yielding tangible benefits such as reduced downtime and lower repair costs. By minimizing maintenance frequency, CBM helps reduce maintenance costs associated with asset failures, often leading to 15—to 30-percent cost savings.
However, it is essential to consider the ongoing maintenance costs of the CBM systems themselves, as they can affect the overall return on investment. A critical financial indicator to watch is the maintenance cost as a percent of estimated replacement value (MC/ERV), which helps determine if ongoing maintenance is more economical than replacing assets.
The initial financial hurdle when adopting CBM is the upfront investment in technology and personnel training, which must be weighed against the potential long-term savings. CBM’s impact extends beyond immediate monetary savings, enhancing operational efficiency and productivity by optimizing resource utilization.
Organizations that invest in CBM are investing in the future of their operations, positioning themselves to reap the benefits of a maintenance strategy that aligns with the evolving demands of modern industry.
Choosing the Right CBM Tools and Software
Selecting the appropriate tools and software is essential when executing a Condition-Based Maintenance (CBM) strategy. The chosen solutions need to be able to track particular failure modes while being tailored to meet an organization’s predictive requirements.
Telemetry devices and other sensors are vital components within a CBM approach. They connect with equipment to gather critical sensor data for subsequent monitoring and analytical processes. This information serves several maintenance purposes, from instigating specific actions and notifying personnel to display patterns contributing to informed maintenance planning.
A successful CBM initiative should include:
- Compatibility with existing organizational systems like ERP/CMMS for smooth integration that enables uninterrupted data circulation
- User-centric design in CBM applications allows straightforward interactions
- Functions that offer visual interpretation of complex sensor output, making it understandable and implementable
Maintenance procedures can be efficiently automated by setting up CMMS work order rules triggered by sensor data analysis. Such configuration leads directly from identified trigger events to suitable responses within the upkeep cycle, thus refining overall workflow efficiency in routine operations.
Implementing CBM: Challenges and Best Practices
Embarking to implement condition-based maintenance (CBM) can be challenging. It is essential first to grasp the core concepts of reliability-centered maintenance, as this forms the foundation for an efficient CBM program. The following steps are crucial in this process:
- Gain a deep understanding of equipment condition data and establish precise threshold levels.
- Implement IoT sensors and software solutions that facilitate seamless data collection and management.
- Ensure CMMS work order rules are configured to activate correct work orders during maintenance events.
- Consider external factors affecting maintenance, such as travel time and scheduling constraints.
Adhering to these guidelines can significantly enhance your chances of succeeding with your CBM system and boost overall upkeep productivity.
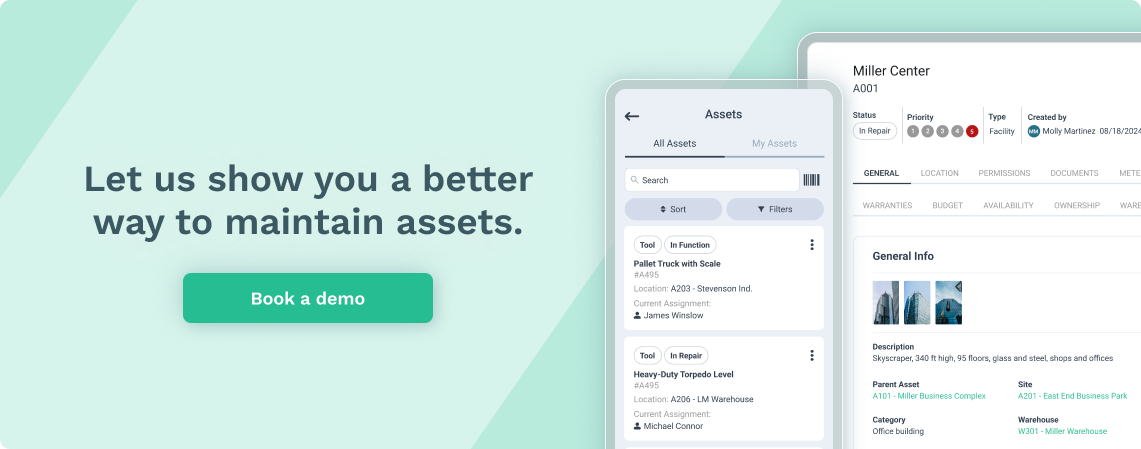
Hurdles of CBM
Implementing condition-based maintenance comes with hurdles, such as reluctance toward change, substantial initial investment requirements, and the necessity for expertise in analytics handling capabilities, which are often faced during implementation. To conquer these challenges effectively, it’s suggested that you follow several best practices, which include but aren’t limited to:
- Fostering teamwork across departments for better interpretation of collected data
- Using Reliability-Centered Maintenance evaluations to pick suitable assets for applying CBM strategies
- Carrying out thoughtful strategic planning activities
- Investing resources into comprehensive training programs
- Upholding dedication toward continual enhancements
By sticking to these recommended approaches, organizations can efficiently manage the intricacies associated with condition-based maintenance CBM application procedures and take full advantage of its possibilities to improve their day-to-day operations involving maintaining facilities or systems under their purview.
Measuring Success: KPIs for Condition-Based Maintenance
A set of crucial key performance indicators (KPIs) that reflect both maintenance actions and healthy equipment functioning can determine the success of a Condition-Based maintenance (CBM) program.
Indispensable metrics such as Mean Time Between Failures (MTBF), which shows the average time an asset runs before failing, and Mean Time to Repair (MTTR), revealing the typical duration it takes to fix an item after breakdown, are instrumental for understanding aspects like equipment availability, dependability, and upkeep productivity.
Monitoring KPIs like maintenance backlog and machinery downtime is essential in evaluating whether there’s a harmonious balance between maintenance workload and capacity. Analyzing these indicators alongside sensor data and performance statistics and identifying failure modes from various assets within their operations.
Source: WorkTrek
Maintenance Team
Maintenance teams gain valuable insight that enables them to spot trends requiring attention. Consequently, tracking these KPIs empowers organizations with actionable data to fine-tune their CBM strategies, bolstering efficiency and promoting sustained functionality across their machine inventory.
Ushering in a New Era of Maintenance with CBM
Condition Based Maintenance (CBM) is not just an evolution in maintenance practices; it represents a paradigm shift, ushering in a new era where reactive approaches give way to proactive, data-informed strategies. This shift empowers maintenance teams to:
- Detect and resolve potential failures well before they escalate into costly downtimes or catastrophic breakdowns
- Make intelligent decisions based on real-time data capture and analysis
- Align maintenance tasks precisely with equipment needs
By implementing CBM, organizations can optimize their maintenance efforts and improve overall equipment reliability and performance.
The potential of CBM to transform industrial operations is immense, offering opportunities for significant improvements in efficiency and effectiveness. By optimizing maintenance schedules and preventing downtime, CBM extends the life of assets and ensures that they operate at peak performance.
As more organizations adopt CBM, the maintenance landscape is being reshaped, enhancing reliability and productivity that will define the industry’s future.
The Role of CMMS in Condition-Based Maintenance
The significance of Computerized Maintenance Management Systems (CMMS) within Condition Based Maintenance (CBM) is crucial, as they serve as the vital processing hub that organizes and optimizes maintenance operations.
By automating work orders utilizing sensor data, CMMS equips maintenance teams with a complete perspective on machinery health and delivers an integrated platform for operation management. This automated process promotes precise and timely execution of maintenance interventions, mitigates human error risks, and increases the efficiency of overall maintenance processes.
The ability of CMMS to sync with other internal enterprise systems offers organizations several benefits.
- Thorough tracking of both labor costs and parts expenses
- Enhanced comprehension concerning total outlays on maintenance
- Informed decision-making regarding cost-efficiency measures
- Ensure that every segment, from initial condition monitoring to post-maintenance analysis in CBM initiatives, conforms meticulously to the plan.
Summary
Source: WorkTrek
Condition-based Maintenance (CBM) is critical for improving equipment dependability, operational productivity, and cost reduction. By using real-time data and sophisticated monitoring methods combined with the integration of technological advancements such as IoT and CMMS, organizations can shift their maintenance strategies from reactive to proactive stances.
Although there may be hurdles to adopting CBM, equipped with proper tools, strategic planning, and a dedication to ongoing enhancement, its advantages are significant. As industries progress dynamically, CBM emerges as an innovative lighthouse directing maintenance teams on a journey where downtime decreases significantly while efficiency soars dramatically.
Frequently Asked Questions
What is the difference between CBM and predictive maintenance?
Predictive maintenance sets itself apart from condition-based maintenance (CBM) by utilizing sophisticated data analysis and predictive modeling to project future maintenance requirements rather than relying on periodic or real-time measurements. Although both strategies are designed to guide upkeep procedures, predictive maintenance uniquely allows for predicting potential problems before they become apparent.
How do you determine which assets to include in a CBM program?
In your Condition-Based Maintenance (CBM) program, it’s essential to prioritize equipment that is highly valued and fundamental for production activities. Make decisions on prioritization considering elements like the machine’s importance to operations, costs associated with repair or replacement, and any planned schedule for replacing such assets.
What role do IoT sensors play in a CBM program?
In CBM initiatives, IoT sensors are critical as they gather data in real-time regarding variables like vibration, temperature, and pressure. This information is essential for assessing the equipment’s condition and guiding maintenance decisions.
Can CBM be integrated with existing maintenance systems?
Indeed, combining Condition-Based Maintenance (CBM) with current maintenance systems like Enterprise Resource Planning (ERP)/Computerized Maintenance Management Systems (CMMS) facilitates a continuous exchange of data and efficient synchronization of maintenance operations, rendering it an advantageous approach for enhancement.
What are some common challenges when implementing CBM?
Implementing condition-based maintenance (CBB) often involves hurdles, such as combating reluctance to alter existing processes, the need for proficiency in data interpretation, and significant initial expenses.
Careful strategic planning, adequate training opportunities, and an ethos of ongoing enhancement are crucial to successfully navigating these obstacles.