Get a Free WorkTrek Demo
Let's show you how WorkTrek can help you optimize your maintenance operation.
Try for freeSmart maintenance is the key to staying ahead while controlling maintenance costs. Integrating cutting-edge technologies, such as IoT and Artificial Intelligence (AI), smart maintenance goes beyond troubleshooting—it predicts and prevents equipment failures, ensuring smooth operation and cost savings.
As we’ve entered the age of AI, using IoT, Machine Learning, and AI can help organizations implement smart maintenance strategies to streamline maintenance.
Smart maintenance technology integrates IoT, predictive analytics, and AI to enhance asset performance and reduce maintenance costs by offering real-time data analysis, proactive maintenance scheduling, and improved decision-making.
It can also minimize unplanned downtime and optimize maintenance work allocation and supply chain management, leading to significant cost savings, increased uptime, and more efficient overall operations.
This article outlines practical smart maintenance tactics and how they are used in varied industries to extend asset life, enhance reliability, and reduce costs.
Source: WorkTrek
Exploring Smart Maintenance
At the core of modern maintenance approaches, smart predictive maintenance represents an advanced blend of methodologies and technologies that improve on traditional preventive and predictive strategies. This technique capitalizes on the synergy between people and interconnected assets by harnessing a continuous flow of real-time performance data.
It conducts thorough analysis to uncover crucial insights from extensive maintenance data. Smart predictive maintenance protocols deliver immediate visibility into equipment condition and performance, allowing organizations to detect and resolve problems quickly.
IoT Monitoring Devices
Central to the success of smart predictive maintenance is deploying cutting-edge monitoring devices, such as IoT sensors strategically placed on vital equipment. These sensory tools constantly monitor a company’s maintenance personnel, detecting subtle shifts in how assets operate and integrating seamlessly with their existing management routines.
IoT technology is pivotal to gathering the necessary information for smart maintenance strategies. Continually gathering data and interpreting signals about asset health proactively prevent minor issues from developing into more significant malfunctions that require expensive fixes.
Interpreting IoT Data
Gathering vast amounts of sensor data is insufficient—the secret lies in interpreting that data through intelligent analytics. For example, AI-driven algorithms can go beyond simple predictions and, if trained correctly, can provide recommendations for preemptive maintenance.
This approach can provide tangible business benefits, such as reducing downtime, improving the overall maintenance program, and creating efficient benefits for the maintenance team.
The Role of IoT in Real-Time Asset Monitoring
The widespread adoption of IoT devices has revolutionized the industrial internet, serving as critical elements in predictive maintenance. These intelligent sensors and sophisticated IoT monitoring tools continuously produce real-time data, vital for transitioning from a reactive to a proactive maintenance strategy.
These devices can detect early signs of failure, such as abnormal vibrations or temperature fluctuations, thus enabling maintenance organizations to schedule maintenance work before the equipment fails, thereby reducing downtime and maintenance costs.
The value of IoT lies in its ability to:
- Provide real-time visibility
- Enable rapid, informed decision-making
- Bolster process and equipment reliability through conditions-monitoring sensors and IoT technologies continuously feeding maintenance data into the system
- Helps develop modern maintenance technique
- It can be part of a more significant digital transformation step for the organization
- Reduce downtime by providing real-time data
Moreover, the data amassed by smart sensors not only informs the condition of assets but also guides optimal maintenance work allocation, ensuring that the maintenance team can operate with maximum efficiency.
Predictive Analytics: Anticipating Equipment Needs
Predictive analytics represents a significant step in the evolution of technology. It offers an impressive ability to forecast equipment maintenance requirements with remarkable precision. By analyzing vast amounts of maintenance data, these analytical tools enhance predictive maintenance strategies by providing more accurate predictions and optimizing overall maintenance protocols.
Intelligent monitoring systems can issue timely warnings about potential equipment failures through automated alerts, substantially reducing unexpected downtime.
Using Data Insights
Incorporating data insights within maintenance management allows for timeliness and specificity in preventative maintenance activities. Technologies equipped with fault detection capabilities alongside smart sensors can predict when machines will need servicing — this optimizes inventory management and avoids excessive costs associated with stocking surplus parts.
Source: WorkTrek
Analytics
By harnessing sophisticated analytics and machine learning algorithms, modern predictive maintenance solutions can identify early risks of equipment failure and recommend proactive scheduling for upkeep procedures that prevent business interruption.
The key to realizing such benefits is deploying advanced software designed for predictive repair tasks that integrate smoothly into existing systems for maximum implementation efficiency.
Artificial Intelligence: The Brain Behind Maintenance Efficiency
Artificial intelligence is the advanced processing hub of an intelligent factory’s maintenance system. It works with various sensors and predictive maintenance software to develop detailed plans that foresee and prevent equipment failures.
In 2024, there is a straightforward race to use AI to improve organizational efficiencies. However, it is essential to outline what that means and how it can benefit maintenance organizations.
Types of Generative AI
Generative AI encompasses various types, each with unique capabilities and applications.
One prominent type is large language models (LLMs), such as GPT-4, Google Gemini, and Perplexity AI. LLMs are designed to understand and generate human-like text by training on vast datasets scraped from the Internet.
These models can answer questions, create content, and even generate code. They are instrumental in applications ranging from customer service chatbots to content creation tools, enhancing productivity and user experience.
However, their use and applications regarding predictive maintenance are somewhat limited. There are use cases in which some companies have used LLMs, such as ChatGPT, to create PM lists, but that is a limited use case.
Another fascinating type of generative AI focuses on image generation. Models like DALL-E and Stable Diffusion can create detailed images from textual descriptions. This capability is revolutionizing fields such as digital art, marketing, and design, allowing for creating visuals that precisely match specific requirements.
Additionally, generative AI is being integrated with cameras and other sensors to enhance real-time data interpretation. For instance, AI-driven cameras can generate contextual information in augmented reality (AR) applications, providing users with rich, interactive experiences.
These advancements in generative AI are paving the way for more intuitive and immersive technological interactions across various industries.
Source: WorkTrek
Benefits of Using AI in Maintenance
Integrating AI into maintenance practices offers significant advantages, primarily by enhancing system reliability and reducing operational costs. AI-driven predictive maintenance can analyze vast amounts of data from sensors and historical records to predict equipment failures before they occur.
This proactive approach allows maintenance teams to address potential issues during scheduled downtimes rather than reacting to unexpected breakdowns.
As a result, AI minimizes unplanned downtime, ensuring that machinery operates smoothly and consistently. Furthermore, AI’s ability to detect patterns and anomalies that human analysts might overlook leads to more accurate diagnostics and maintenance schedules, ultimately boosting the system’s overall reliability.
Reduce Maintenance Costs with AI
In addition to improving reliability, AI significantly reduces maintenance costs. By predicting when and where maintenance is needed, AI helps optimize resource allocation, ensuring that maintenance efforts focus on critical areas. This targeted approach prevents unnecessary maintenance activities, saving time and reducing labor costs.
Moreover, AI can help extend the lifespan of equipment by identifying issues early and recommending timely interventions, which can prevent costly repairs or replacements. The efficiencies gained through AI-driven maintenance strategies translate into substantial cost savings, making it a valuable investment for organizations seeking to enhance their operational efficiency and bottom line.
AIs roles in Predictive Maintenance
AI revolutionizes predictive maintenance effectiveness by analyzing complex data sets and identifying trends that human analysts might miss. It enhances preventive efforts in several significant ways.
- It is designed for ongoing learning from an accumulation of maintenance data.
- It simplifies processes by automating routine tasks related to upkeep.
- It equips technicians with valuable insights, empowering them to take decisive and efficient action.
In an automated world, AI shines by turning what would be routine or scheduled maintenance into informed decisions. With intelligent analysis, AI guides those who maintain the machines, providing guidance that turns standard preventative to predictive and prescriptive.
It works in every part of modern machine servicing practices. AI converts patterns in the data into actions to increase output and reduce maintenance costs.
Cutting Maintenance Costs with Smart Strategies
Examining the economic impact of smart maintenance reveals that these strategies are not just about improving performance—they’re essential for reducing maintenance costs.
Smart strategies achieve significant cost savings by reducing unplanned downtime, eliminating unexpected costs, maximizing equipment availability and efficiency, and improving workplace safety conditions.
A well-implemented preventive maintenance plan, especially with new equipment, ensures continuous performance and prevents costly emergency repairs.
Statistical Benefits of Smart Maintenance
The numbers speak volumes.
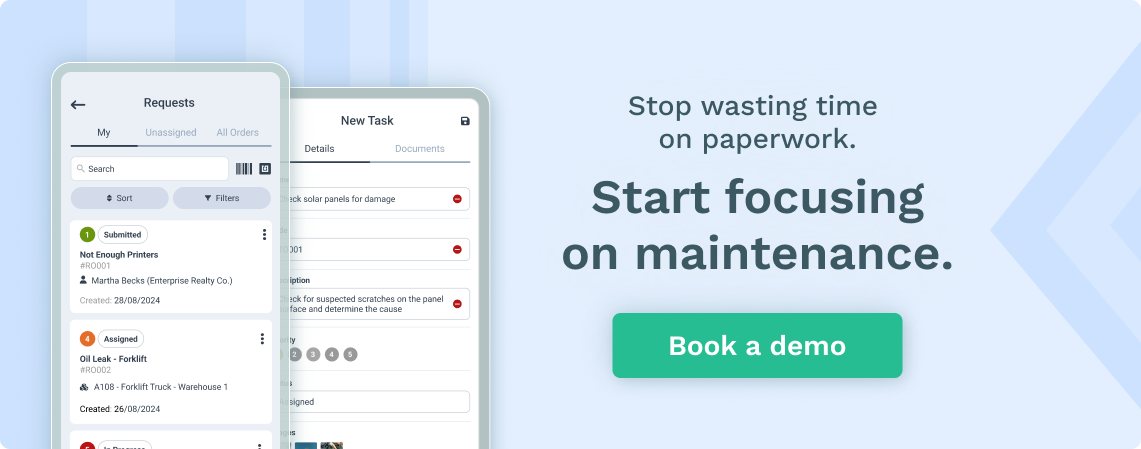
- Adopting predictive maintenance and using data analytics to drive proactive maintenance actions can lead to a 20% increase in uptime
- Predictive strategies can prevent asset failure and substantially extend the longevity of assets like HVAC systems
- This translates into fewer replacements and reduced expenses over time
- Smart maintenance practices can also result in a 10% reduction in overall maintenance costs
But how exactly do these savings materialize? The answer lies in:
- The meticulous minimization of unplanned downtime
- The strategic optimization of maintenance work allocation
- The clever integration of smart maintenance with supply chain management
Let’s peel back the layers of these strategies to understand their mechanics and the benefits they confer.
Minimizing Unplanned Downtime
Unplanned downtime is the bane of any maintenance organization, often leading to inefficiencies and lost production time. Predictive maintenance, empowered by real-time sensor data, is vital in minimizing this downtime and has been shown to enhance machine life by 20% to 40%.
Proactive maintenance strategies, which include routine checks and cleanings, are crucial for operational efficiency and ensure that maintenance tasks are prioritized for the greatest return on investment.
Moreover, analyzing maintenance data trends facilitates preventative actions against potential equipment failures and helps prioritize maintenance tasks efficiently.
Utilizing maintenance management software, which provides real-time visibility and communication, streamlines the scheduling and execution of maintenance tasks, further reducing downtime and enhancing safety and efficiency.
Optimizing Maintenance Work Allocation
A computerized maintenance management system (CMMS) is essential in contemporary maintenance strategies. Such systems bolster effectiveness by optimizing various processes, including administering work orders and scheduling preventive maintenance.
By employing CMMS, teams can efficiently organize their workload—tasks are created, delegated, and monitored automatically to ensure every technician operates as productively as possible.
These advanced systems confer more advantages than just task coordination. They serve as central hubs for all collected maintenance data, which permits the following:
- Improved interaction and teamwork within the maintenance team
- Instant access to performance metrics
- Strategic decision-making based on comprehensive analysis aligning with the overarching aims of your organization’s upkeep initiatives
- Get access to predictive and prescriptive analytics
- Accelerate digital transformation
A CMMS is a powerful tool that reduces operational disruptions and enhances procedural efficiency, essential for maintaining a competitive edge in industry standards.
Source: WorkTrek
Supply Chain Synergies: Smart Inventory Management
By integrating IoT and predictive analytics, smart inventory management aligns closely with supply chain processes to optimize maintenance schedules according to production needs. Collecting and analyzing data can anticipate potential equipment issues, allowing for proactive measures to prevent operational disruptions.
This forward-thinking approach adheres to project timelines and mitigates the ripple effects that could result from breaks in the supply chain.
Storeroom Management
Technological advancements in storeroom management align inventory planning with cutting-edge maintenance strategies. This integration allows companies to maintain just the right amount of spare parts—sufficient for their needs without excess that unnecessarily ties up capital.
Integrating smart maintenance into inventory control empowers enterprises by ensuring the timely availability of essential components, reducing downtime risks, and enhancing overall efficiency within their maintenance procedures.
Enhancing Safety and Reliability in Operations
Smart maintenance technologies are pivotal in an organization’s financial and operational well-being. These innovative methods provide advanced warning for potential failures or malfunctions, enhancing workplace safety and ensuring equipment performs reliably over time.
Predictive maintenance stands out by minimizing accidents among technicians and detecting emerging issues before they evolve into serious hazards.
Smart maintenance can prevent and predict machine failures. That’s key in maintenance – it allows you to act before downtime or significant safety incidents.
By applying smart technology to maintain machinery at optimal performance levels, manufacturing facilities can sustain smooth operations while safeguarding high-quality production standards.
Ensuring Technician Safety Through Predictive Models
Leveraging both historical and real-time data from sensors, predictive models are instrumental in ensuring the safety of maintenance technicians within a maintenance organization. These models utilize such data to predict potential hazardous conditions before they materialize, thereby playing an essential role in averting risks to personnel by alerting them about prospective equipment malfunctions early on.
As part of a strategy that prioritizes safety within maintenance operations, these forms of predictive analytics are indispensable for orchestrating the timing of maintenance tasks to prevent accidents.
Adopting predictive and prescriptive maintenance techniques has proven effective in staving off equipment failures. By harnessing technologies related to condition-monitoring sensors, these techniques extend beyond mere forecasts about when an asset might fail.
These methods also recommend optimal actions to prevent impending failure, thus significantly diminishing accident risk exposure. Consequently, this allows those responsible for routine or specialized upkeep—the maintenance technicians—to execute their roles with increased efficacy and reassurance from robust support provided by state-of-the-art predictive models designed for their protection.
Source: WorkTrek
Boosting Reliability with Data-Driven Maintenance Approaches
Leveraging advanced analytics in maintenance approaches is vital for enhancing machinery reliability. These methods promote preventive maintenance to keep machines functioning optimally by recognizing patterns indicative of looming equipment failures.
Smart maintenance uses telemetry and sensor information to synchronize upkeep schedules with production timelines, thereby reducing downtime initiated by disruptions within the supply chain.
Analyzing machine performance data is crucial for enhancing equipment reliability. It enables maintenance teams to prevent system failures before they happen. This proactive approach ensures manufacturing operations run smoothly without significant interruptions or efficiency losses.
Maintaining machinery in peak condition via such strategies supports overall equipment effectiveness—a critical indicator when evaluating a successful maintenance program’s impact on processes and tools used within an enterprise’s ecosystem.
Extending Service Life with Proactive Measures
Predictive maintenance is crucial for advancing maintenance practices. It helps identify early signs of wear and tear on manufacturing equipment. This proactive approach extends the machinery’s lifespan and efficiently schedules maintenance activities.
Organizations can maximize equipment uptime and availability by managing spare parts inventory more effectively. Field evidence from manufacturing sectors has consistently shown that predictive maintenance significantly increases asset longevity while ensuring operational reliability.
Maintenance teams utilize collected data on repairs and upkeep tasks to predict potential mechanical issues. This enables them to take timely corrective action, preventing breakdowns.
This strategy enhances the machinery’s lifespan and guarantees a streamlined execution of maintenance operations without significantly hindering production processes.
One key advantage is the creation of more durable and long-lasting assets. This leads to significant cost reductions in maintaining those assets and enhances the overall efficiency of operating heavy-duty machinery or similar equipment.
Digital Transformation: Smart Maintenance as a Catalyst
Digital transformation is revolutionizing industries, and smart maintenance has emerged as a key driver of innovation and evolution with cutting-edge technologies such as:
- Internet of Things (IoT)
- Artificial Intelligence (AI)
- Machine Learning
- Big Data Analytics
This approach collects and analyzes real-time data to enhance operational efficiency. Adopting these principles in smart predictive maintenance contributes to cost savings and strengthens the rationale for moving towards more energy-conscious strategies and intelligent solutions.
Forward-thinking companies have acknowledged that robust predictive maintenance is essential in maintaining efficient, agile operations capable of adapting to dynamic industry requirements.
Consequently, they exemplify new benchmarks for what defines a truly ‘smart factory’—one where advanced technology underpins improved facility management processes while propelling business growth.
Decision for Managers
Maintenance and Facility managers overseeing maintenance teams face an important decision: whether and how best to integrate smart techniques effectively into their operations.
Success hinges upon selecting appropriate technological tools with strategic deployment and ongoing optimization through measurement and refinement within maintenance systems to ensure smooth navigation through this pivotal change process.
Let’s explore how facility and maintenance managers can steer their businesses successfully along this transformative path toward optimized functionality.
Facility and Maintenance Managers’ Guide to Implementing Smart Systems
Facility and maintenance managers can establish a solid foundation for a smart maintenance strategy by identifying key metrics for making informed decisions. This initial step is crucial as it sets a benchmark against which managers can evaluate and improve various maintenance operations within their scope.
By focusing on the most critical KPIs, they can strategically allocate resources to enhance the efficiency and effectiveness of their maintenance practices.
Measuring Success: KPIs and Overall Equipment Effectiveness
The effectiveness of intelligent maintenance tactics can be measured using Key Performance Indicators (KPIs), which are crucial for determining the improvements in production efficiency resulting from these methods. The following are some essential maintenance KPIs:
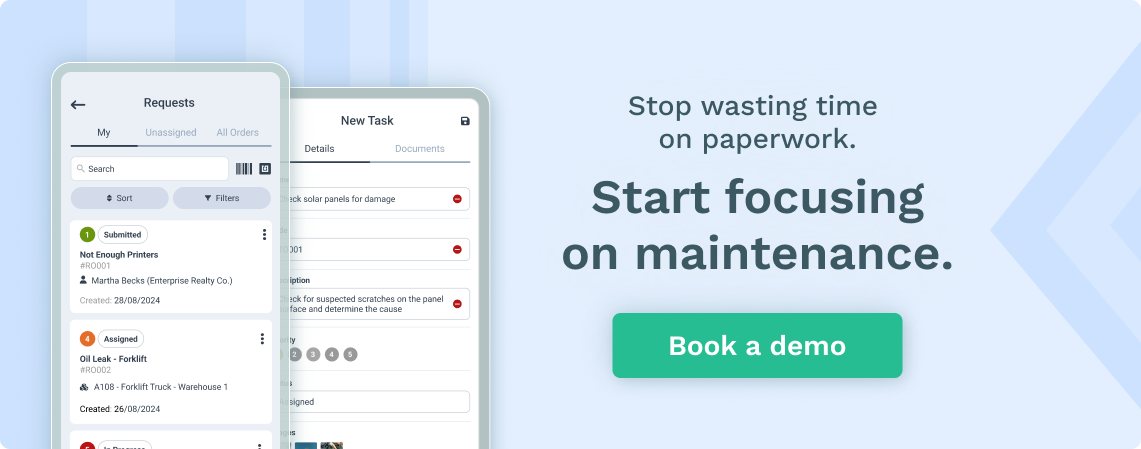
- Overall Equipment Effectiveness (OEE): This metric offers an aggregated perspective on equipment effectiveness by amalgamating several performance measures.
- Mean Time Between Failures (MTBF): This indicator tracks the reliability of equipment.
- Mean Time to Repair (MTTR): This index gauges how quickly repairs and responses are made.
Such KPIs play a pivotal role in appraising the impact of smart maintenance strategies.
Another vital KPI is Equipment Availability, which evaluates the percentage of time a device is prepared for use in production cycles. Combined with MTBF, MTTR, and OEE, this KPI becomes instrumental in facility managers’ assessing the efficacy of their existing programs within a smart maintenance framework.
Facility and maintenance managers obtain invaluable insight into their efficiency and dependability by frequently monitoring these metrics. Consequently, they can make educated adjustments that promote betterment in both areas through strategic refinement of ongoing maintenance routines at their facility.
Source: WorkTrek
Case Studies: Success Stories from the Industry
Numerous companies have emerged as beacons of success within the industry by seamlessly integrating smart maintenance strategies into their operations.
A common characteristic among these organizations is a workforce proficient in harnessing data analysis, statistical modeling, and sensor technology. These key skills are indispensable for carrying out predictive beyond-measure maintenance effectively.
By dedicating resources to cultivating these abilities within their teams, such firms unlock the immense benefits of advanced maintenance techniques and witness substantial enhancements in managing tasks.
Industry Leaders
Leaders in innovation like Bosch and Boeing exemplify this advancement through their pioneering use of augmented reality (AR) during routine upkeeping procedures.
They give technicians tools that provide real-time information and visualization, making maintenance more efficient. Digital transformation does the same for traditional asset management: it reduces downtime and increases operational efficiency and cost savings.
These successful implementations serve as strategic references and inspirational case studies for other companies considering adopting tech-enabled maintenance practices.
The Future of Maintenance: Trends and Innovations
As we look to the future, maintenance is shaped by emerging trends and innovations that promise to enhance asset management further. The integration of technologies such as machine learning, augmented reality, and big data analytics is setting the stage for a new era of maintenance where decision-making is more informed, operations are more efficient, and maintenance tasks are more strategic.
In this evolving landscape, the role of maintenance technicians will transform, with a greater emphasis on data-driven insights and advanced diagnostics.
Virtual and Augmented Reality
The adoption of Virtual Reality (VR) and Augmented Reality (AR) for maintenance diagnostics and troubleshooting is rising, revolutionizing how maintenance tasks are performed.
Additionally, robotic process automation (RPA) enhances sustainability and security measures within the facility management sector. Additive manufacturing techniques, such as 3D printing, are becoming increasingly common, enabling the on-demand production of replacement parts and minimizing equipment downtime.
These trends are not just theoretical; they signify the future trajectory of the maintenance industry. Maintenance organizations can ensure they remain industry leaders by keeping up with these advancements and adopting the innovations they introduce.
The future of maintenance is bright, and those willing to innovate and adapt will lead the way.
Source: WorkTrek
Machine Learning and Advanced Diagnostics
Machine learning technology is a crucial driver of advancements in smart predictive maintenance, enabling the creation of more sophisticated predictive models and continuously refining algorithms. In simple terms, machine learning is the underlying architecture that enables Artificial Intelligence. Systems can ingest large amounts of data and process that data based on AI models.
Data scientists utilize this technology to improve predictive capabilities, ensuring that maintenance programs become increasingly accurate and effective. Machine learning transforms maintenance data into actionable insights, allowing maintenance teams to anticipate and address equipment issues before they lead to downtime or failure.
The impact of machine learning on maintenance data analysis is profound. With the ability to learn from vast amounts of data, machine learning algorithms can:
- Identify subtle patterns and correlations that human analysts might overlook
- Enable predictive analytics to become more precise
- Help maintenance technicians to focus their efforts on the most critical maintenance tasks.
As machine learning continues to evolve, we can expect even more significant advancements in predictive maintenance, further improving the efficiency and reliability of maintenance operations.
The Integration of Big Data in Asset Management
The utilization of big data is transforming the landscape of asset management by providing in-depth insights from an extensive range of data points. By applying big data analytics, maintenance organizations are empowered with a profound comprehension of asset conditions and operational performance. The advantages derived from integrating big data into asset management include:
- Precise prediction of when equipment may fail
- Enhanced scheduling efficacy for maintenance operations
- Detection of trends and recurrent patterns that affect asset behavior
- Maximization of how assets are used while minimizing periods they’re not working
Embracing big data translates to more streamlined, effective management strategies, culminating in financial savings and bolstering efficiency across daily operations.
Leveraging insights derived from big data enhances decision-making within maintenance systems, significantly improving operational efficiency. The primary benefits of utilizing this extensive information include:
- Prolonging the useful life span of assets via accurately timed maintenance initiatives
- Enhancing overall stewardship over organizational resources using advanced analytical techniques
- Crafting tailored, intelligent programs dedicated to maintenance workloads
- Providing straightforward returns on investment and improvements for institutions
As analytical methodologies advance, the potential for improving physical asset management strategies expands significantly. This progression indicates a shift towards more calculated maintenance approaches, offering substantial benefits for organizations focused on asset preservation and efficiency.
Summary
In conclusion, the landscape of asset management is undergoing a revolution driven by the advent of smart maintenance technologies. From predictive analytics and IoT to artificial intelligence and big data, these tools enhance maintenance efficiency and transform operations’ safety, reliability, and cost management.
As we look toward the future, integrating advanced diagnostics, augmented reality, and machine learning promises to refine further and revolutionize maintenance strategies. Embracing these trends and innovations is critical for organizations seeking to maintain a competitive edge and achieve operational excellence in an increasingly complex and dynamic industry.